齿轮动态啮合有限元分析
齿轮有限元分析

2 ANSYS 准备工作.................................................................................................................- 4 2.1 ANSYS 安装与启动........................................................................................................- 4 2.1.1 许可证服务器安装............................................................................................ - 4 2.1.2 主程序安装.......................................................................................................- 5 2.1.3 启动许可证服务器............................................................................................ - 7 2.1.4 ANSYS 启动与配置............................................................................................. - 8 2.2 设置工作目录............................................................................................................ - 10 2.3 指定作业名与分析标题.............................................................................................. - 10 2.3.1 指定作业名..................................................................................................... - 10 2.3.2 指定分析标题..................................................................................................- 11 2.4 定义图形界面过滤参数....................................................................................... - 11 2.5 ANSYS 单位制...................................................................................................... - 12 2.6 选取和定义单元................................................................................................. - 13 -
基于有限元法的齿轮齿条动态应力分析
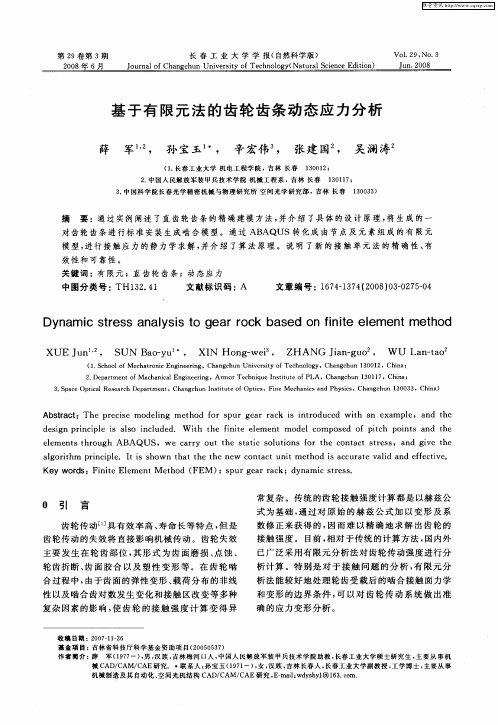
模型, 进行接 触 应力 的静力 学求 解 , 并介绍 了算法 原 理 。说 明 了新 的接 触 单元 法 的精确 性 、 有
效性和 可 靠性 。 关 键 词 : 限 元 ;直 齿 轮 齿 条 ;动 态 应 力 有
中图分 类号 : TH1 2 4 3. 1
文献标 识 码 : A
文章编 号 : 6 41 7 ( 0 8 0 —2 50 1 7— 3 4 2 0 )30 7 —4
』 :
基 于 有 限 元 法 的 齿 轮 齿 条 动 态 应 力分 析
薛 军 , 孙 宝 玉H , 辛宏 伟 。 张建 国 , 吴 澜 涛 ,
( . 春 工业 大 学 机 电 工 程 学 院 , 林 长 春 1长 吉 101 ; 3 0 2 101 ; 3 1 7 10 3) 30 3 2 中 国 人 民解 放 军装 甲兵 技 术 学 院 机 械 工 程 系 , 林 长 春 . 吉
ee e t h o g A QUS, we c r y o t t e sa i ou in o h o t c te s n ie t e lm n st r u h AB a r u h t t s l t s f r t e c n a t sr s ,a d gv h c o
a g rt l o ihm i cpl. I s s own t tt h w on a t un tm e h sa c r t a i d e f c i . prn i e ti h ha he t e ne c t c i t od i c u a e v ld an f e tve
齿轮系统的有限元分析

西京学院毕业设计(论文)}题目:齿轮系统的有限元分析系(院): 机电工程系专业: 数控技术班级: 数控0902姓名: 方荣稳!学号: 05指导老师: 李少海日期: 2011年11月—摘要齿轮啮合过程作为一种接触行为, 因涉及接触状态的改变而成为一个复杂的非线性问题。
传统的齿轮理论分析是建立在弹性力学基础上的, 对于齿轮的接触强度计算均以两平行圆柱体对压的赫兹公式为基础,在计算过程中存在许多假设,不能准确反映齿轮啮合过程中的应力以及应变分布与变化。
相对于理论分析,有限元法则具有直观、准确、快速方便等优点。
本论文对齿轮系统同利用有限元法进行实验分析实现对齿轮的有限元模态分析。
利用有限元理论和数值分析方法, 对齿轮系统在加载和离心力共同作用下的变形和强度进行了分析, 研究了离心力对该系统的影响和动态响应。
利用三维啮合弹塑性接触有限元方法对齿轮进行了接触强度分析, 并基于热弹耦合进行了轮齿的修形计算, 得到轮齿的理想修形曲线, 为齿轮动态设计提供了一种非常有效的方法。
将齿轮系统划分为传统系统和结构系统两部分, 通过轴承把两者耦合起来。
采用有限元方法, 建立了实际单级齿轮减速器的有限元动力学模型, 在工作站上用I- DEA S 软件研究了该齿轮系统的固有特性, 所得结果既后映了系统的动力学性能, 又为齿轮系统的动态响应计算和分析奠定了基础。
关键词:齿轮;有限元法; 模态分析;接触; 修形;、目录第一章绪论 (3)有限元的概念 (3)概述 (4)第二章齿轮系统有限元模型的建立 (6)第三章I2DEA S 固有特性的计算方法 (8)第四章齿轮系统有限元模态分析结果 (10)结论 (12)致谢 (14)参考文献 (15)^`第一章绪论有限元的概念有限元分析(FEA,Finite Element Analysis)的基本概念是用较简单的问题代替复杂问题后再求解。
它将求解域看成是由许多称为有限元的小的互连子域组成,对每一单元假定一个合适的(较简单的)近似解,然后推导求解这个域总的满足条件(如结构的平衡条件),从而得到问题的解。
有限元分析齿轮轴

Abaqus分析报告(齿轮轴)名称:Abaqus齿轮轴姓名:班级:学号:指导教师:一、简介所分析齿轮轴来自一种齿轮泵,通过用abaqus软件对齿轮轴进行有限元分析和优化。
齿轮轴装配结构图如图1,分析图1中较长的齿轮轴。
图1.齿轮轴装配结构图二、模型建立与分析通过part、property、Assembly、step、Load、Mesh、Job等步骤建立齿轮轴模型,并对其进行分析。
1.part针对该齿轮轴,拟定使用可变型的3D实体单元,挤压成型方式。
2.材料属性材料为钢材,弹性模量210Gpa,泊松比0.3。
3.截面属性截面类型定义为solid,homogeneous。
4.组装组装时选择dependent方式。
5.建立分析步本例用通用分析中的静态通用分析(Static,General)。
6.施加边界条件与载荷对于齿轮轴,因为采用静力学分析,考虑到前端盖、轴套约束,而且根据理论,对受力部分和轴径突变的部分进行重点分析。
边界条件:分别在三个轴径突变处采用固定约束,如图2。
载荷:在Abaqus中约束类型为pressure,载荷类型为均布载荷,分别施加到齿轮接触面和键槽面,根据实际平衡情况,两力所产生的绕轴线的力矩方向相反,大小按比例分配。
均布载荷比计算:矩形键槽数据:长度:8mm、宽度:5mm、高度:3mm、键槽所在轴半径:7mm键槽压力面积:S1 = 8x3=24mm2 平均受力半径:R1=6.5mm齿轮数据:=齿轮分度圆半径:R2 =14.7mm、压力角:20°、单个齿轮受力面积:S2 ≈72mm2通过理论计算分析,S1xR1xP1=S2xR2xP2,其中,P1为键槽均布载荷幅值,P2为齿轮均布载荷幅值。
键槽均布载荷幅值和齿轮均布载荷幅值之比约为P1:P2≈6.3 。
取键槽均布载荷幅值为1260,齿轮载荷幅值为200.由于键槽不是平面,所以需要切割,再施加均布载荷。
图3 键槽载荷施加比较保守考虑,此处齿轮载荷只施加到一个齿轮上。
齿轮强度的有限元分析
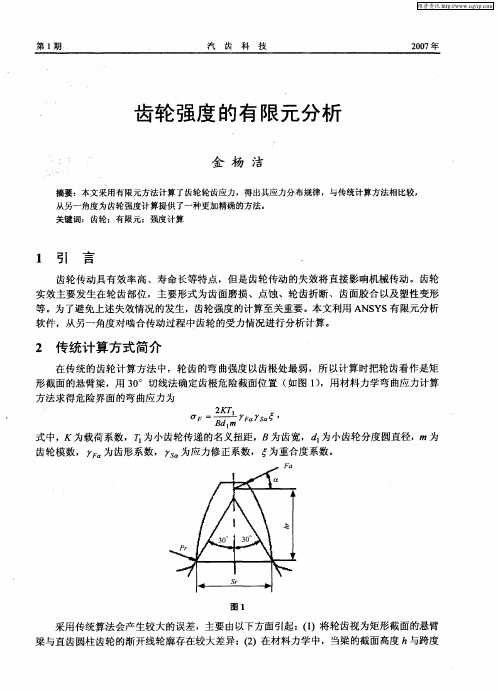
Sc pe o
S o i be G o e r e cin c p gMeh d n e m ty l t S e o
Ge me r o ty
…
iE g d e
XCo r ia e 0. o dn t m YCo r ia e 0 o dn t .m ZCo r ia e 0 o dn t .m Lc t n o ai o Ci oC an e lkt h g c
结 构 ,从 而控 制离 合泵 的行 程 输 出 ,达 到控 制 离合 器 的分离 与结 合 ,其 结构 简 图见 图 2 。
1电机 2,齿轮 . .、 J 3大齿轮 4螺母 . .
5 丝 杆 6杠 杆 . . 7推 杆 8离合器 . .
油泵
图2
31 模型 的建 立 .
根据实测所得的需用空间计算出这对齿轮副的中心距为 7 . 5 4 3 ,由电机特性可以确定齿 2 数 比约为 4 ,其 他初 选 齿轮 参 数见 表 1 。
维普资讯
第 1期
汽
齿
科
技
20 0 7钜
齿轮 强度 的有 限元分析
金 杨 洁
摘要 :本文采 用有限元方法计算 了齿轮轮齿应力 ,得 出其应力 分布规律 ,与传统计算方法相 比较, 从另 一角度 为齿轮强度 计算提供 了一种更加精确 的方法 。 关键词 :齿轮 ;有 限元;强度计算
参数名称 数值 参数名称 数值
齿 数
压力角
螺旋角 模数 m 齿 项高 精度等级
Z l 1 。 9
Z J 2 7 9
齿 高 根
齿根 圆角半径
变位系数 分度 圆直径
齿轮箱有限元模态分析及试验研究报告

齿轮箱有限元模态分析及试验研究报告齿轮箱是现代机械设备中重要的组成部分,它广泛用于各种机械传动系统中,如车辆、工程机械等。
因此研究齿轮箱的动力学特性对于机械传动系统的设计、优化和性能提升具有重要意义。
本文通过有限元模态分析和试验研究,对齿轮箱的动力学特性进行了分析和研究。
首先进行有限元模态分析,使用ANSYS软件建立了三维齿轮箱模型,并对其进行了固有频率和模态分析。
在分析过程中,设定了模型的约束和加载条件,确保模型模拟的真实性与可靠性。
通过模态分析,得到了齿轮箱的固有频率和模态形态,并且确定出了前几个重要频率的数值。
结果表明,齿轮箱的固有频率主要集中在数百Hz的高频段。
为了验证有限元模态分析结果的准确性,本文设计了试验验证方案。
首先,使用激光精密测量仪对齿轮箱的位移进行测量,并将测试数据存储为动态位移序列。
然后,基于FFT算法对动态位移序列进行频谱分析,得到齿轮箱的频响函数。
最后,通过对比有限元模态分析结果与试验结果,验证模型的准确性和可靠性。
试验结果表明,模型的预测结果与试验结果相符,二者的误差在可接受范围内。
综上所述,本文采用有限元模态分析和试验验证两种方法,对齿轮箱的动力学特性进行了研究。
结果表明,齿轮箱具有较高的固有频率,且主要分布在数百Hz的高频段。
通过试验验证,证明了有限元模态分析方法的准确性和可靠性。
这些结果对于齿轮箱的优化设计、结构改进和性能提升具有重要参考价值。
齿轮箱的有限元模态分析和试验研究,采用了多项相关数据。
在本文中,我们主要关注以下数据:1. 齿轮箱模型的材料性质2. 模型的约束和加载条件3. 模型的固有频率和模态形态4. 齿轮箱的位移测试数据5. 齿轮箱的频响函数6. 模型预测结果与试验结果的误差对于第一项数据,齿轮箱的材料性质是有限元模型分析的关键。
正确的材料参数可以确保分析结果的准确性和可靠性。
在本文中,我们将齿轮箱的材料定义为铸铁,其杨氏模量为169 GPa,泊松比为0.27。
准双曲面齿轮动态啮合性能的有限元分析研究_唐进元
id164 实体单元, 单元积分形式为单点高斯积分。
第7 期
唐进元等: 准双曲面齿轮动态啮合性能的有限元分析研究
103
大轮底面和小轮内圈采用刚体材料, 弹性模量为 2. 1 × 10 5 MPa, 泊松比为 0. 3 , 采用 shell163 壳单元, 壳 单元属性默认。 定义大轮和小轮之间为自动面面接触, 约束大、 小 轮除了沿其各自轴线的旋转自由度以外的所有自由 对小轮内圈施加恒定转速 1 200 r / min, 同时对大轮 度, 底面施加恒定负载扭矩 200 N· m。 计算时间为 0. 015 s, 满足 1 个啮合周期。
· · · · · · ·
有限元网格划分 有限元网格划分
( 2)
x ) 为单元应力场等效节点矢量组集而成 , H 其中,F ( x, [13 ] 为总体结构沙漏阻尼力 。 由以上运动方程及动力学理论可知, 惯性载荷是 使结构产生动力响应的本质因素, 而惯性载荷的产生 又是由结构的质量引起的。 因此, 对准双曲面齿轮的 质量位置及其运动的准确描述成为了动态啮合分析的 关键。 总结已有模型所存在的问题, 本文建立了合理的 准双曲面齿轮动态啮合有限元分析模型, 该模型的建 模方法也可用于其他齿轮的动态啮合有限元分析模 型中。 准双 曲 面 齿 轮 有限 元 模 型 的 建 立 主要 包 括 几 何 模 型 的构建, 合理的网格 合理的边界载 划分, 荷施加, 以及定义单 元和材料模型, 定义 现分别予以 接触等, 介绍。
[12 ] 作者在已有研究基础上 , 应用非线性动力学相 关理论及商用软件 LS_DYNA 对准双曲面齿轮的动态 啮合过程进行进一步有限元分析研究, 研究动态啮合
1. 1
几何模型的建立
文章通过数值计算得到齿面离散数据点 ( 主要几 由离散数据点拟合成精确的准双曲面 何参数见表 1 ) , 齿轮展成曲面, 并依此构建出准双曲面齿轮三维实体 模型, 如图 1 所示。 详细建模方法与模型精度参照文 献
基于APDL与UIDL的齿轮啮合动态有限元分析系统
・
1 8・
价 值 工程
基于 A D P L与 U D 的齿 轮 啮合 动态 有 限元分 析 系统 IL
Th a e h Dy a i i ie E e e tAn l ss S se s d o e Ge r M s n m c F n t l m n a y i y t m Ba e n APDL n DL a d UI
朱春雨①Z uC u y ; h h n u 陈宏丽②C e n l; h nHo gi佟海龙③T n i n o gHal g o
( ①沈阳铁路机械学校, 沈阳 10 3 ; 沈阳中瑞机械有限公司 , 1 6② 沈阳 10 1 ; 1 1③三一重型装备有限公司, 沈阳 10 2 ) 10 7 ( hnag aw yM cai colSeyn 0 6 C ia ̄) eyn hnri cai l o pn ,hnag10 1 ,h a @Seyn i a ehn a Sho,hnag103 ,h ; S nag ogu Mehnc m aySey C i R l c l 1 n h Z aC n 1 1 n ③ Sn ev q i et o p ySeyn 1 2 ,hn ) ay ayE up n C m a hnag10 7C ia H m n I
齿轮有限元分析
齿轮有限元分析引言有限元分析(Finite Element Analysis,简称FEA)是一种工程分析方法,用于通过将复杂的结构分割为简单的有限元,利用力学原理进行计算和分析。
它在工程领域得到了广泛的应用,齿轮有限元分析便是其中之一。
齿轮是一种常见的传动装置,广泛应用于机械、汽车、冶金等领域。
传统的齿轮设计方法主要依赖于经验和试错,效果难以保证。
而有限元分析能够通过数值计算对齿轮进行全面的力学分析,为齿轮的设计与优化提供有力支持。
齿轮有限元分析原理齿轮有限元分析的基本原理是将齿轮进行离散化,将其分解为多个小块,每个小块称为一个有限元。
然后根据有限元理论,建立有限元模型。
将齿轮的物理性质、边界条件等输入有限元模型,并进行求解,得到齿轮的应力、变形等相关结果。
在齿轮有限元分析中,需要考虑的因素包括载荷、齿轮的几何形状、材料参数等。
其中载荷可以分为静态载荷和动态载荷,可以通过实际工况和使用要求确定。
几何形状是指齿轮的轮齿形状、齿顶高度、齿距等。
材料参数包括齿轮的弹性模量、泊松比等。
齿轮有限元分析采用有限元软件进行计算,常见的有ABAQUS、ANSYS、Nastran等。
通过建立合理的有限元模型和适当的边界条件,可以得到齿轮的应力分布、变形情况等结果,从而评估齿轮在工作过程中的可靠性。
齿轮有限元分析的应用齿轮有限元分析在齿轮设计与优化中扮演着重要的角色。
它能够帮助工程师更全面地了解齿轮在工作条件下的应力分布、变形情况,从而为设计提供指导。
具体应用包括以下几个方面:齿轮受力分析通过齿轮有限元分析,可以得到齿轮在受到静态或动态载荷作用时的应力分布情况。
这可以帮助工程师判断齿轮在工作过程中是否存在应力集中现象,以及是否满足材料的强度要求。
在设计中,可以根据这些分析结果调整齿轮的几何形状或材料参数,以提高齿轮的可靠性和寿命。
齿轮变形分析齿轮在受到载荷作用时,会发生一定的变形。
通过齿轮有限元分析,可以计算齿轮的变形情况,包括齿轮的轴向变形、径向变形等。
变速器齿轮轴有限元及动力仿真分析
∀ 工艺与装备 ∀
变速器齿轮轴有限元及动力仿真分析
胡祝田, 宋守许, 刘志峰
( 合肥工业大学 机械与汽车工程学院, 合肥 230009)
*
摘要: 联合仿真法预估疲劳寿命包括获取载荷历程 、 应力应变场和材料参量三个方面内容 。文章在此基 础上依据企业提供的二维图纸, 在三维造型软件 P ro /Eng ineer中建立某型号变速器的第一齿轮轴实体模 型 。根据有限元基本理论, 建立该轴的有限元模型 。最后在有限元分析系统 M SC. N astran中进行该轴的 应力分析, 得出应力应变。 采用 P ro /E 和 ADAM S /V iew 的专用接口模块 M echan ism /P ro 实现两者之间的 数据转换, 最后仿真得出齿轮轴与从动齿轮的载荷曲线 , 其与理论计算值十分接近 。有限元分析及动力 仿真结果对进行齿轮轴的疲劳寿命预估提供了必须的数据, 为进一步来预测服役齿轮轴的剩余寿命有 着重要的作用。 关键词 : 齿轮轴; 有限元分析 ; 仿真; 疲劳分析 中图分类号 : TH 16 文献标识码: A
n∃ =
( 6)
2010年第 8 期 式中: n! n∃ !- 1 ∃- 1 K !, K ∃ ∀ !a ∃a % ∃ !m , ∃ m 弯矩时的安全系数 ; 扭矩时的安全系数 ; 剪切疲劳极限; 弯曲疲劳极限; 有效应力集中系数 ; 尺寸系数 ; 表面系数 ; 弯曲应力; 扭转应力 ; 扭应力不对称循环系数 ; 应力幅。
结束语通过有限元分析及虚拟仿真与理论计算结果相比较可以看出该变速器齿轮轴的刚度和强度在设计时满足要求且有一定的裕度能保证工作中的正常使最为重要的是文中有限元分析结果及动力学仿真对进行产品的疲劳寿命分析提供了必须的数据于名义应力法预估第一齿轮轴工作寿命有着重要作用
- 1、下载文档前请自行甄别文档内容的完整性,平台不提供额外的编辑、内容补充、找答案等附加服务。
- 2、"仅部分预览"的文档,不可在线预览部分如存在完整性等问题,可反馈申请退款(可完整预览的文档不适用该条件!)。
- 3、如文档侵犯您的权益,请联系客服反馈,我们会尽快为您处理(人工客服工作时间:9:00-18:30)。
齿轮动态啮合有限元分析
作者:陕西法士特齿轮有限公司孙春艳郭君宝
齿轮传动是机械传动中最重要、应用最广泛的一种传动。
通常齿轮安装于轴上并通过键连接,转矩从驱动轴经键、齿轮体和轮齿最终传递到从动轮的齿轮。
在这一过程中,齿轮承受应力作用。
另外,为了润滑齿轮传动与减少齿轮传动时产生的热量,通常在齿轮轮体上开设润滑油孔(图1)。
油孔的开设位置将影响齿轮的应力及其分布,进而影响齿轮疲劳寿命。
图1中的齿轮A在实际使用过程中,经常发生油孔附近轮齿断裂的现象。
本文的目的在于计算齿轮动态啮合过程的应力分布,得到齿轮轮齿根部应力及接触应力的分布情况,从而为齿轮的结构优化提供理论依据。
传动齿轮在工作中速度高,所受载荷大,引起的应力情况复杂。
传统的齿轮强度分析是建立在经验公式基础上的,其局限性和不确定性日益突出。
有限元方法在齿轮仿真分析中的应用,提高了齿轮设计计算精度。
目前,轮齿接触有限元分析多建立在静力分析基础上,未考虑动力因素的影响。
而在齿轮轮齿啮合过程中,动力因素对轮齿的受力和变形状态会产生较大的影响,尤其在轮齿啮入和啮出时,由于轮齿受力变形,会产生较大的啮合冲击。
本文应用参数化方法首先建立齿轮轮齿的精确几何模型,然后采用动力接触有限元方法,对齿轮轮齿啮合过程中的应力变化情况进行仿真分析,得到轮齿应力在啮合过程中随时间的变化情况。
本文主要针对图1中的齿轮A和与其配对齿轮在运转过程中的应力变化情况进行有限元分析。
其主要参数为:主动齿轮齿数20,从动齿轮齿数19,模数4.5,压力角为20°,齿宽为23mm,从动齿轮上所受扭矩为400N·m。
如图2 所示,首先利用Pro/ENGINEER软件建立四齿对啮合的齿轮轮齿几何模型。
这是因为,对于重合度大于1的齿轮副,需要考虑几对轮齿同时啮合的情况,建立多对轮齿的几何模型,在此基础上划分有限元网格,如图3所示。
由于轮齿接触区域很小,需要对接触齿面的有限元网格加密。
边界条件为约束齿轮内圈表面节点的径向和轴向位移,只保留沿轴向的转动自由度。
在主动齿轮上施加轴向的角速度载荷,在从动齿轮上施加扭矩负载,然后应用显式非线性动力有限元方法进行求解。
对于动力接触这种非线性问题,可采用拉格朗日增量描述法。
设质点在初始时刻的坐标为Xi,任意时刻t,该质点坐标为xi,质点运动方程为:xi=xi(Xi,t), i=1,2,3。
结合动量方程、质量守恒方程和能量方程,并考虑沙漏效应和阻尼影响,得到总体运动方程:
其中M为集中质量矩阵;P为总体载荷矢量;F为单元应力场的等效节点力矢量组集而成; H 为总体结构沙漏粘性阻尼矩阵;为总体节点加速度矢量; C为阻尼矩阵。
对总体运动方程采用显式时间积分法求解。
本文采用ABAQUS 有限元分析软件对上述模型进行有限元分析,得到该对齿轮的一对轮齿啮合全过程,及Von Mises应力变化,如图4 所示。
由图4中可以看出,在一对轮齿啮合过程中,齿轮轮齿啮合状态在单齿对啮合和双齿对啮合间交替变化。
主动齿轮的轮齿在从啮入到啮出过程中,齿根应力随着啮合点向齿顶移动而逐渐增大,并伴随着单齿对和双齿对啮合状态的交替变化产生波动,最后在轮齿退出啮合过程后,齿根应力迅速降低。
同时,我们还可以观察到轮齿啮合时接触应力的变化情况,从图中可以看出:在双齿对啮合状态下应力值较低,而在单齿对啮合状态下应力值明显升高,两
种状态转换时应力值发生明显的突变。
这是因为,当一对轮齿啮合后进入双齿啮合状态时,由于两齿对之间载荷分配的变化,中间轮齿逐渐变为主要承载轮齿,其啮合处的应力随之升高。
在前一对轮齿退出啮合后,进入中间轮齿单独啮合状态,啮合处的应力比双齿啮合状态明显增加。
而当后一对轮齿进入啮合后,中间轮齿啮合处的应力又随之降低。
在轮齿啮入和啮出时,由于弹性变形使轮齿基节发生变化,引起啮合干涉,产生啮合冲击,所以中间轮齿在啮合处会产生较大应力。
本文从实际应用问题入手,利用通用有限元分析软件ABAQUS 对齿轮轮齿动态啮合进行仿真与计算分析,使我们对轮齿啮合过程中弯曲应力及接触应力的分布与变化有了更加清晰和深入的认识。
通过对该传动齿轮啮合过程中轮齿的应力分析不难看出,在单齿对啮合和双齿对啮合过程中轮齿的应力值是起伏变化的,并且由于啮合冲击,使得轮齿产生较大冲击应力,这说明在轮齿啮合过程中动力因素会对轮齿的应力状态产生较大影响,而这是我们采用静态分析所无法得到的。
另外,采用这种动态有限元分析齿轮轮齿啮合过程,可以得到轮齿应力随时间的变化情况,更加接近轮齿啮合的真实情况,为齿轮强度分析提供了一种更加精确有效的分析方法,从而为齿轮变速箱及相关行业的可靠性分析奠定了有力的理论根基。
(end)。