油管振动导致断裂原因分析及处理方式
高压油管开裂原因分析及改进建议
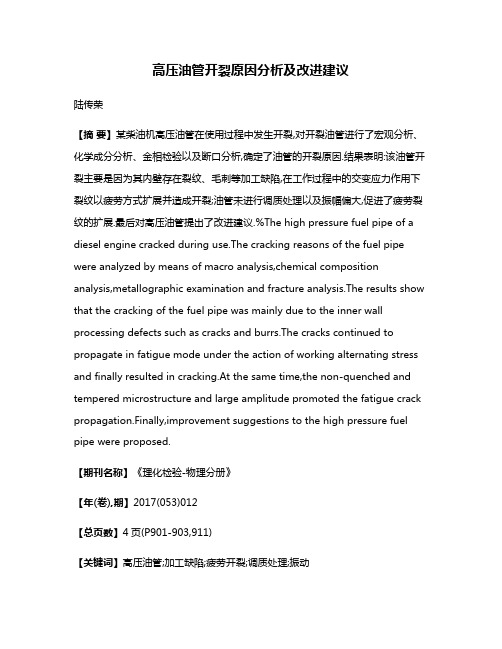
高压油管开裂原因分析及改进建议陆传荣【摘要】某柴油机高压油管在使用过程中发生开裂,对开裂油管进行了宏观分析、化学成分分析、金相检验以及断口分析,确定了油管的开裂原因.结果表明:该油管开裂主要是因为其内壁存在裂纹、毛刺等加工缺陷,在工作过程中的交变应力作用下裂纹以疲劳方式扩展并造成开裂;油管未进行调质处理以及振幅偏大,促进了疲劳裂纹的扩展.最后对高压油管提出了改进建议.%The high pressure fuel pipe of a diesel engine cracked during use.The cracking reasons of the fuel pipe were analyzed by means of macro analysis,chemical composition analysis,metallographic examination and fracture analysis.The results show that the cracking of the fuel pipe was mainly due to the inner wall processing defects such as cracks and burrs.The cracks continued to propagate in fatigue mode under the action of working alternating stress and finally resulted in cracking.At the same time,the non-quenched and tempered microstructure and large amplitude promoted the fatigue crack propagation.Finally,improvement suggestions to the high pressure fuel pipe were proposed.【期刊名称】《理化检验-物理分册》【年(卷),期】2017(053)012【总页数】4页(P901-903,911)【关键词】高压油管;加工缺陷;疲劳开裂;调质处理;振动【作者】陆传荣【作者单位】海军驻上海711所军事代表室,上海 201108【正文语种】中文【中图分类】TK428;TG115某柴油机高压油管在使用过程中发生开裂。
压缩机润滑油管断裂失效原因分析

第42卷第1期2021年2月化工装备技术49失效分析压缩机润滑油管断裂失效原因分析吕华亭*薛利杰任发才司俊(上海市特种设备监督检验技术研究院)摘要通过化学成分、金相分析、断口分析等手段对某压缩机润滑油管断裂原因进行了分析。
结果表明:润滑油管接管处存在加工缺陷,在流体诱导的双向振动下,使管道疲劳断裂。
关键词润滑油管失效分析疲劳断裂中图分类号TG115DOI:10.16759/ki.issn.1007-7251.2021.02.013Failure Analysis of Compressor Lubricating Oil Pipe FractureLYU Huating XUE Lijie REN Facai SI JunAbstract:By means of chemical composition,metallographic analysis and fracture analysis,failure analysis of lubricating oil pipe of a compressor was carried out.The results showed that there were machining defects at the connecting pipe of lubricating oil pipe,which made the pipe fatigue fracture under the bidirectional vibration induced by fluid.Key words:Lubricating oil pipe;Failure analysis;Fatigue fractureC-XX---1—0刖s在压力传输系统中,由于压缩机工作过程具有往复性,导致系统中产生了机械振动与噪声。
系统中管道的原始缺陷或制造缺陷在循环载荷的作用下容易发生疲劳断裂失效,轻则导致传输物质泄漏、污染环境,重则造成系统损坏和人员伤亡。
顶轴油管开裂事件原因分析与处理

顶轴油管开裂事件原因分析与处理摘要:某新建东汽350MW机组投运初期连续出现3起顶轴油管开裂事件,对造成开裂的共性与非共性问题进行了分析,判断其制造过程中的结构缺陷,安装过程工艺不当以及应力集中区的存在是造成开裂的主要原因,针对性的提出了整改与防范措施。
关键词:应力集中;金属疲劳;失效开裂;顶轴油管1概述某新建350MW热电联产机组汽轮机为东方汽轮机有限公司生产,2020年12月投运。
顶轴油系统主要用于汽轮发电机组开机之前及停机后需要投入盘车时,顶起转子,降低转子转动所需力矩,避免轴颈与轴直接接触造成磨损等。
顶轴油系统设置3台柱塞泵,向汽轮机与发电机3至6号轴承供油,油源取至润滑油母管。
顶轴油泵入口设置有一台前置泵和一组双联滤油器,出口为母管制系统,顶轴油经油泵出口、滤网引至轴承,在顶轴油泵出口设置有恒压阀,调节油泵出口压力为18MPa,顶轴油母管设置有溢油阀,整定母管压力为16MPa,顶轴油系统运行时1台油泵运行,2台油泵备用。
机组于2021年3月26日首次停机检修,停机投运顶轴油系统盘车期间,相继出现了1号顶轴油泵入口法兰角焊缝开裂,出口滤网后母管管接头开裂,2号顶轴油泵入口法兰处压力取样管管接头开裂事件,由于发现及时且处理得当,所幸未造成严重后果。
2原因分析金属构件的断裂失效是金属部件最为常见的失效形式之一,也是最为危险的失效形式。
造成金属部件断裂失效主要有以下几方面原因:过载断裂、材料致脆断裂、环境致脆断裂、疲劳断裂、混合断裂等,在实际案例当中,往往是由其中一种或者多种因素共同作用导致金属失效的发生。
火电厂中金属材料使用工况复杂,往往工作在高温、高压、腐蚀性介质、高流速介质等环境中,还要受到交变应力和冲击应力的影响,易发生金属构件失效情况。
本案例三起事件虽然最终表现结果均为金属的开裂失效,但开裂部位的结构形式及所处工况不尽相同,为了准确判断三起事件中金属部件失效的原因,分别从不同的角度进行分析。
EH油管的裂纹成因分析

2 ( ) 46~4 7 3 4 :8 8
64 m管 中的环 向应 力 较小 , 向力或 振动 造成 的 1m 轴 弯 曲应力成为导 致应力腐蚀 的重要应力来源 。
() 管 材 料 化 学 成 分 和 金 相 组 织 正 常 , 纹 是 3油 裂 从 外 表 面 形成 的 , 此 裂 纹 的 产 生 与 材 料 和 管 内 输 因
氯 和硫 。 内外 表 面 酸 洗 腐 蚀 的 特 征 相 同 , 明 管 内 说
工 作 环 向 应 力 远 大 于 +4 m 管 。这 可 以 解 释 为 何 1m +5 2mm管 中 主要 形 成 4 5度 角 方 向 的 裂 纹 和 纵 方 向 裂 纹 , +4 m 管 中 裂 纹 趋 向 于 横 方 向 ,因 为 而 1m
抗燃油没有对 内表面产生腐蚀 作用 。
裂 纹 的 剖 面 形 态 如 图 4, 纹 是 由 外 表 面 向 内 裂
维普资讯
电子显 微学 报 J hn Eet. c s . o .C i . lc Mi c S c r o r
20 04年 47 8
从 工 作 压 力 估 算 ,2mm 油 管 中 内压 产 生 的 环 向 应 +5
力 约 7 M a 而  ̄ 4 m 油 管 约 为 5 a  ̄5 3 P, 1m 1 MP , 2 mm 管
物, 腐蚀产 物 中铬 明显 富 集 。说 明这 类裂 纹应 该 与 氯离子 的腐蚀 作用 有关 。钢 管 的 内、 外表 面 有 表面 酸洗 留下 的均 匀深腐 蚀 痕迹 , 分析 出局部 有 残存 的
生应力腐蚀 开裂 的典型断 口特征 。局部断面可 以看 见有腐蚀残 留物形 成 的泥状 花样 ( 6 , x射线 图 )用 能谱仪分析 出腐 蚀残 留物 中有 很 高含量 的氯 , 一 进 步证 明开裂过 程受到环境 中含氯腐蚀 介质 的作 用。
分析管道震动与裂缝的原因及其消除措施

分析管道震动与裂缝的原因及其消除措施摘要:管道振动与裂缝的存在严重干扰正常生产,造成安全隐患,积极解决这类问题对实现安全生产有重要意义。
本文介绍了管道振动与裂缝产生的原因,并结合原因分析探讨了如何实现减震消震的举措,希望能够改善管道振动与裂缝现象,促使压缩机安全运行。
关键词:管道振动减震消震管架石油化工领域往复式压缩机应用较为普遍,这类机械常见问题为管道振动与裂缝,尤其是压缩器工作时,缓冲罐等容器刚性连接的地方经常出血裂纹,不仅影响正常生产应用,还存在较大的安全隐患,所以积极分析压缩及管道振动和裂缝出现原因,并积极探讨消除措施,是实现安全生产的重要举措。
一、管道振动与裂缝产生原因管道振动与裂缝的产生主要以气流脉动、共振和内部机械原因为主。
往复式压缩机工作时需要通过活塞在气缸内的往复运动实现气体的吸入、压缩和排出,这种周期性运动决定了管道进出口内流体呈现脉动状态,一旦气流遭遇管件产生激振力,即可产生管道振动现象。
管道内容纳的气体可称为气柱,压缩机工作时促使气柱不断压缩、膨胀,以激发频率工作,管道内部管件与支架组成弹性系统以固有频率运作,当激发频率与固有频率接近或相等时导致压力脉动异常从而产生管道内的机械共振现象[1]。
内部机械原因主要为管道设计不合理、内部机械动平衡性能差、基础与支撑不当等,导致压缩机工作时出现管道振动现象甚至造成裂缝。
二、管道振动与裂缝消除举措分析1.管道减震目前,管道减震措施主要以三种为主,分别是通过控制气流脉动、合理设计管道来减少谐振发生,通过调整激发频率和固有频率避免其相近或固定,通过合理设计管道装配结构、调整牢固压缩机组实现减震目的。
往复式压缩机内决定压力脉动和振动发生的二因素主要包括压缩机参数、系统噢诶之与压缩介质的物理参数,三种因素在振动的发生中有着重要影响[2]。
减震举措中,减少气流脉动是常见方法,可通过设置缓冲器实现减震目的,缓冲器内部的芯子元件可有效减弱压力脉动,效果理想。
连续油管振动的分析和研究

连续油管套管开窗振动分析引言连续油管钻井(CTD)技术作为一种新型且快速发展的钻井作业手段,以其良好的现场作业效果和众多的作业优势越来越受到油田作业者的关注。
进入20世纪80年代以来,世界范围内各大油田相继进入开发后期,油藏开发难度逐渐增加,油藏开发形势、油藏地质条件等因素对钻井的要求越来越苛刻。
连续油管开窗侧钻为解决上述问题提供了了一个很好的途径。
套管开窗的好坏直接影响后续侧钻井下钻具组合能否顺利下入井中以及钻井的质量。
影响开窗质量的因素主要有造斜器的性能,钻头的类型,钻压的施加,钻井液的使用及控制及操作人员的操作等。
其中,上述原因都涉及到振动的影响,振动常常也会导致开窗作业过程中常常出现井底钻具的严重破坏、随钻测量设备的频繁失效等,所以研究振动对开窗质量的影响具有重要意义。
造斜器振动的影响连续油管过油管开窗侧钻技术包括水泥塞开窗侧钻技术、水泥环内置造斜器开窗侧钻技术和过油管造斜器开窗侧钻技术。
三种技术的主要差别在于开窗和出老井眼的导向方式上。
目前,水泥塞开窗侧钻技术比较成熟,应用广泛,是三种技术中最可靠、经济的一种。
但是,水泥塞开窗侧钻和水泥环内置造斜器开窗侧钻所需的工序多,需要多次起下钻,加速了连续油管的疲劳磨损,而连续油管造斜器开窗侧钻可实现“单程”下造斜器和开窗作业,延长了连续油管使用寿命。
所以,造斜器开窗侧钻越来越受到油田作业者的关注。
常用的造斜器还有滑块定位式、撑块卡固式、偏斜定位套式等。
造斜器的类型和锚固方式对振动的产生具有重要影响。
传统的与弹性元件配合使用的造斜器由于使用弹性元件,往往会导致封隔器存在不利的微小位移,而产生振动影响开窗铣锥齿的切削深度,从而产生更大的振动,加速了铣锥的破坏和窗口质量的下降。
此外,由于连续油管开窗侧钻常常需要过直径小于套管的油管,所以造斜器直径往往比油管要小,当座封或锚固好造斜器下入开窗钻具组合后,造斜器导斜面由于受到钻具的作用和自身刚度的限制会产生快速的小变形(如图所示),这将导致不规则的切入深度,随机的大切入深度会瞬时消耗马达大量能量并随之产生振动。
液力偶合器油管断裂故障的技术分析及改进
液力偶合器油管断裂故障的技术分析及改进陆传荣;何柳;李唐;顾智超;杜言峰;李建军【摘要】针对某液力偶合器在考核试验中油泵油管在管接头处断裂的故障,从管接头加工缺陷、管接头受力过载、油泵振动过大等因素进行分析,分析表明:油管断裂主要原因是油泵振动偏大,在改进了油泵支承结构后,油泵的振动情况得到了明显改善,解决了油管断裂的故障.【期刊名称】《传动技术》【年(卷),期】2015(029)001【总页数】6页(P43-48)【关键词】液力偶合器;油管断裂;结构改进【作者】陆传荣;何柳;李唐;顾智超;杜言峰;李建军【作者单位】驻七一一研究所代表室,上海 200090;七一一研究所,上海 200090;七一一研究所,上海 200090;七一一研究所,上海 200090;七一一研究所,上海 200090;七一一研究所,上海 200090【正文语种】中文【中图分类】U463.2121 前言液力偶合器作为一种液力传动机械,通过液体在旋转的叶轮中流动,完成机械能→液体能→机械能的转换,实现动力传递[1]。
某型液力偶合器油泵的作用是为系统提供控制油及润滑油,在油泵的供油油管断裂后,将无法为系统提供控制油及润滑油,导致液力偶合器无法实现接合功能,不能正常传递扭矩。
本文就某型液力偶合器在试验过程中出现的油泵油管断裂故障进行分析,并提出相关的解决方案。
2 故障现象某液力偶合器在进行试验时,滑油压力由0.18 MPa突降为0.04MPa,液力偶合器由接合状态变为脱开。
将液力偶合器油底壳拆除后,发现油泵的供油油管在管接头处断裂,如图1所示:图1 油管断裂部位Fig.1 crack position of the fracture oil pipe断裂油管在油泵上的安装位置如图2所示:图2 断裂油管安装位置Fig.2 settlement position of the fracture oil pipe3 故障原因分析由于油管在管接头处发生断裂,所以从管接头加工缺陷[2]、管接头受力过载、油泵振动过大等因素进行分析:3.1 管接头加工缺陷将断裂的管接头沿径向剖开,管接头内腔加工比较粗糙,有明显的加工刀痕,如图3所示:图3 管接头内腔加工刀痕Fig.3 machining cuts on the pipe joint为了验证管接头加工缺陷是否是油管断裂的主要原因,加工了新的管接头,表面粗糙度达到图纸要求,装配后重新进行试验,该油管在同样部位再次发生断裂。
船用主机高压油管开裂分析及措施
主机燃油高压油管是主机燃油系统中的重要组成部分,主机运行时高压油管持续承受脉冲高压冲击,其质量的好坏直接关系到主机运转[1]。
为了保证主机正常运转,主机燃油高压油管在管材一般要求的基础之上,主机专利商MDT 还有以下相关要求:1)管材需要能承受90 MPa 的压力在200 ℃条件下;2)管子内表面的总脱碳层深度不得超过0.03 mm;3)管子内壁缺陷的深度不能超过0.3 mm;4)离内表面0.3 mm范围内的珠光体减少不得超过50%。
某船主机型号为6S50ME-B9.3,功率为8 130 kW,高压油管材质为490 I,规格为φ25×8.5 mm(外径×壁厚),高压油管原材料采用多道冷拔及调质处理工艺加工而成,整个生产、加工过程中无酸洗、磷化工序,主机运行时高压油管所受到的冲击频率约为50 次/分钟。
该主机在运行102 h 左右就发生高压油管开裂,见图1。
图1 失效高压油管本文通过对断裂油管断口分析、金相分析、化学成份、力学性能分析,确定了其开裂失效原因及后续的改进措施。
一、检测分析结果1、检测方案制定该主机相继出现开裂的油管总共有 3 根,对其中1 根进行磁粉检测发现共有 4 处裂纹,所处位置大约在距离 A 端弯管处300 mm~550 mm 之间,裂纹长度大约在30 mm~50 mm,高压油管的 A 端是联接喷油器,B 端连接高压油泵,开裂部位在图1 中 C 处。
为了准确查找失效原因,制定从以下几个方面查找原因:1)在C 处开裂口进行宏观、微观分析,查找开裂原因;2)在D、E、F、G 位置做横截面内表面微裂纹深度检测;3)做化学成份与力学性能分析。
2、断口及表面缺陷观察将开裂位置C 处的管段剖开,见图2(a),可见2个贯穿整个油管壁厚的裂纹面。
裂纹面宏观形貌见图2(b),开裂面较为平整,无明显塑性变形,裂纹源区位于内壁,开裂面上清晰可见贝壳纹,符合疲劳开裂的宏观形貌特征。
基于振动测试的发动机高压油管断裂问题分析
基于振动测试的发动机高压油管断裂问题分析白书战 1 ,贾迎军 2 ,张海龙3 ,李国祥 1 ,张锡朝1(1 . 山东大学能源与动力工程学院 ,济南 250061 ;2 . 山东英才职业技术学院 ,济南 250104 ;3 . 山东省交通运输集团 ,济南 250031)摘要 :本文通过振动测试 ,分析了某车用发动机高压油管断裂的原因 。
根据振动测试的结果 ,提出了两项改进措施 :一是改变支架刚度来改变其固有频率 ,使共振转速出现在发动机不 常用的转速范围内 ;二是将喷油泵与驱动齿轮间的连接方式改用法兰来连接 ,避免了由于轴的 加工误差和安装同轴度的影响 。
经过试验测试 ,改变连接方式后有效缓解了高压油管的振动 。
关键词 :车用发动机 ; 高压油管 ; 振动测试中图分类号 : T K 402 文献标识码 :A 文章编号 :1673 - 6397 (2007) 03 - 0049 - 04Analysis of Da mage of E ngine Fuel I njection Pipe B a s e d on V ibrat ion TestB A I Shu - zhan 1,J I A Y ing - jun 2,ZH AN G Hai - l ong 3,L I G uo - xiang 1,ZH AN G X ichao1(1 . School of E nergy and P ower Engineering , Shandong University ,J i nan 250061 ;2 . Shandong Y ingcai V ocati onal T echnol ogy C ollege , J inan 250104 ;3 . Shandong Province C omm unicati on & T ransportati on G roup , J inan 250031)Abstract : F or dam age of high pressure oil pipe in som e vehicle engines , this paper analyses the rea 2 sons by vibrati on test . T w o m ethods are presented in the paper . One is to keep the resonant speed within the range of speed , which is not used in comm on , by changing the rigidity of bracket . Another one is t o connect the injecti on pum p to the driving gear with flange to avoid the influence from m achining error of shaft and coax ial degree while installing. It is shown that vibrati on is lighten efficiently when connecti on is changed.K ey Wor d s :Vehicle E ngine ; Fuel Injecti on Pipe ; Vibrati on T est予以消除的 。
原油管道输油泵出口管线振动原因分析及对策
原油管道输油泵出口管线振动原因分析及对策摘要:随着全球需求的增长,原油管道输油系统受到了越来越多的关注。
然而,输油泵出口管线振动问题仍然存在,给系统的安全和稳定性带来了挑战。
本论文旨在分析引起振动的主要原因,并提出相应的对策。
通过对现有文献和实际案例的综合分析,发现振动主要是由于管线与周围环境的不合适耦合、流体的压力脉动和管线结构的失稳性等因素引起的。
为防止振动对系统产生负面影响,我们建议采取减振措施,如使用减振器、加装阻尼材料和改进管线设计等。
这些对策有助于提高输油系统的可靠性和稳定性,从而确保原油输送过程的顺利进行。
关键词:原油管道;振动原因;减振措施引言随着全球需求的增长,原油管道输油系统面临着振动问题的挑战。
其中,输油泵出口管线振动对系统的安全和稳定性产生重要影响。
为了解决这一问题,本论文旨在分析振动的主要原因,并提出相应的对策。
通过对现有文献和实际案例的综合分析,振动主要受到管线环境耦合、流体压力脉动和管线结构失稳性等因素的影响。
针对这些原因,采取减振措施如使用减振器、加装阻尼材料和改进管线设计等,可以提高系统的可靠性和稳定性。
本研究对于确保原油输送过程的顺利进行具有重要意义。
1.振动原因分析1.1管线与周围环境的不合适耦合管线与周围环境的不合适耦合是导致输油泵出口管线振动的主要原因之一。
由于管线布置、支撑等方面的不合理设计,管线与周围环境之间存在过大的接触面积和摩擦力,从而引发振动。
此外,环境中的地震、土壤沉降等因素也对管线的稳定性产生影响。
针对这一问题,可以采取相应的措施,如增加管线的支撑点数和刚度,改善管道与地基的接触方式等,以减少管线与周围环境之间的摩擦和不稳定因素,降低振动风险。
1.2流体压力脉动流体压力脉动是导致输油泵出口管线振动的另一个重要原因。
在输油过程中,由于泵的工作方式和流体的运动特性,会引起流体压力的脉动现象。
这种脉动压力通过管道传播,导致管线产生振动。
流体压力脉动的频率、幅值和相位都会对管线振动产生影响。
- 1、下载文档前请自行甄别文档内容的完整性,平台不提供额外的编辑、内容补充、找答案等附加服务。
- 2、"仅部分预览"的文档,不可在线预览部分如存在完整性等问题,可反馈申请退款(可完整预览的文档不适用该条件!)。
- 3、如文档侵犯您的权益,请联系客服反馈,我们会尽快为您处理(人工客服工作时间:9:00-18:30)。
#2机EHM管振动导致断裂原因分析及处理方式
《科技与企业》杂志2011年12月(下)大唐莱阳发电厂(湖南省末阳市)王班瑛【摘要】大唐耒阳发电,广’一期丁1987-,年-投产两台200MW气轮发电机
组,采用哈尔滨汽轮机厂制连的55型第7台和第ZION200-- 130/5j5 一次中问再热
凝气式汽轮机,在投产时两台机组均没有采用高压抗燃油EH液压控制系统。
后
#1、#2机分别丁2001年、2005年在大修期间进行改造米用了高压抗燃油EH液
压控制系统,EH油系统设备是由上海新华公司提供的配套设备。
而#2机的EH油
管是在2005
年69大修期间进行安装的,管道分别是q)25 X 2. 5与(1)14x2的不锈钢管,
由新华公司提供,管道与所有三通、接头、大小头均采用是插入式焊接,EH油泵出口压力为14. 5Mpa EH油温:40” 55。
G
【关键词】#2机EH油管;断裂;分析及处理
一.现状分析
我厂#1、2机组EHM系统管道安装后运行超过8年,自设备安装运行以来,#2 机
组丁2008年、2011年7月29K 2011年8月4B共发生了3次中压调门管道焊缝
处裂纹或断裂事故,造成停机。
特别是#2机最近一次管道断裂是发生在大修后,
大修期间金相人员对管道三通焊缝进行了检查,未发现异常,但是在大修
后一个多月,中压调门油动机的EH油管道就发生了2次断裂现象。
造成了EH 油
的大量泄漏,而导致停机。
这对机组的安全运行造成了重大的影响,同时也造
成了严重的经济损失。
因为EH油的造价非常贵,每次机组因EHM管道泄漏而造成
的异停,至少造成EH油泄漏1桶以上,丽且开停机有大量的损耗,造成f不必要
的经济损失,同时也加强了运行人员和检修人员的劳动强度。
=.原因分析
引起油管振动的原因主要有以卜几个方面:
1、机组、调门振动。
汽轮机本体与汽门阀组相连,油动机与阀门本体相连,EH油管与油动机相连接,当调门振动加大时,油管道肯定会随之增大振动,200MvM组的4个中压调门、油动机在汽缶工的侧面和最上部,当机组振动增大时,振动会直接或间接的传递到EH 油系统管道,造成EH油管道振动增大。
2、管夹固定不到位。
由一I : EH油管道的管线较长,按照《EH系统安装调试手册》中规定管夹必须可靠固定,如果管道管夹固定不好,布置不合理,不但不能对发生振动的管道起到约束和消振的作用,反而可能会造成管系的共振,加大油管的振动,油管道还必须有相应的固定支架,固定支架必须到位,否则容易造成油管无良好支撑,增大振动量。
3、伺服阀故障。
EH油中电液伺服阀出现故障时,如:伺服阀
卡涩,紧同件松动、卸荷阀内阻尼孔松脱、弹簧管疲劳等等因素
都可以导致EH油系统无法正常运行,产生振荡信号,引起油管振
动。
4、抗燃油油质劣化的因素。
EH油外观透明均匀,无沉淀物,其密度很大,因而有可麓使得管道中的污染物悬
浮在液面而在系统内循环,造成零部件的堵塞和磨损。
从而造成管道的振动。
而导
致EH油油质劣化。
5、油管道运行时间过长,已运行8年,焊缝周围易产生疲劳断裂,有条件nr 采用更换管道的方式保证机组运行安全。
6、油管材质和焊接问题
通过对EH油管道断裂处进行检查,发现裂纹一般发生在离焊1]3mm母材处。
该活接设计成套管形式,这种形式在施工时能保持内部干净,管道对接时容易对
中。
但是也存在很大的缺点:套管加工时由丁车肖II等原因,管套内部存在直角台阶,这样形成了明显的应力集中区,特别是由14管套的加工比较困难,加工过程中退刀时极易造成明显的槽或刀痕,加大了应力集中。
系统存运行时,调门各油管的温度在500C左右,由丁管道的热膨胀,使套管内部台阶处的挤压应力增大,加上外部振动的影响,使套管在台阶处很容易产生内部裂纹。
在改造EH 油管道时,我们发现不锈钢管插入到管套内部直接顶到台阶,未留间隙,这样在焊接后由丁管套受热不均,使插入管套内的部分对管套台阶处产生挤压应力。
7、中压调门弹簧操作座螺检松动,放大了振动量。
三. 解决问题的方案。
措施
通过现场检查,找出振动的源头,采取相应的措施来消除振动或者减小振动带来的影响。
1、解决机组振动的影llf帆经过检查,发现汽机本体的振动偏大,在机组下次检修过程中。
解决机组本体振动偏大的缺陷,用以减小振动。
2、提高管道材料的质量。
将#2机4个中压调门EHM管@14x 2的不锈钢管用锯弓锯断,为了防止杂物进入EH油系统,接头拆除封好,将J目的由14 x2的不锈钢管更换成为由新华公司提供的书16X 2. 8的不锈钢管(新的管道全部由金相人员进行材料检查)增强了其管道的强度,重新进行弯管处理,改变管道的弯度,增强其扰度,提高补偿能力,达到减振的效果。
3、改变焊接方式严格焊接工艺。
人员使用高级焊工,必须严格按照焊接工艺规程,将不锈钢管插入式焊接更换为对接焊接,减少其应力,管道焊接时采用全氯弧焊且连续完成。
在管道焊接好后,对#2机EHM管所有焊II进行金相着色、射线检查,有焊缝不合格的,重新进行打磨焊接。
4、保证EH油的活洁度。
在检修过程中要注意检修工艺,新安装的EH油管道要
用无水洒精冲洗内部,用绸布反复擦拭管道内壁,直至没有污点为止,用绸布和塑料布双重包扎好.在焊接前再用氮气吹扫,保证管内干净。
12个油动机的卸荷阀进行检查,发现#3高压调门和#3中压
调门的卸荷阀阻尼孔松脱,固定好;炉侧中压主汽门的换向电磁阀活洗以及部分单向蛹阻尼孔活洗。
把#2机4个中压商门的伺服阀更换成冲洗板,进行油循环,优化油质,待油质合格,把4个中压调门冲洗板更换成伺服阀,同时更换了进门滤网和回油管道滤芯及油动机滤芯。
将EH油系统的杂质过滤干净。
检查了油箱上的呼吸器的十燥器,让干燥器保持良好状态,有效的防止了外部水分进入油箱。
通过这一系歹灯的工作来保证EH油的活洁度。
四、结束语
#2机EHM管道经过改造后,机组投入运行经过了多次的管道振动须IJ量,管
道振动明显减小。
不但避免了因油管裂纹而引起的停机,同时大大提高_r机组的运行可靠性,还可以节约EH油的使用量和开机时的耗油,另一方面可以降低运行人员及检修人员的劳动强度。
为我厂节能降耗、机组安全运行提供有力保障。
参考文献
【1】陶本勇,电液调节系统(EH)油管道断裂原因分析与处理【J】,安徽电力科技信息,2006(6) ; 25〜Z7
[21 « 200wM气机检修工艺规程。