发动机振动特性分析与试验(精)
发动机的特性曲线分析
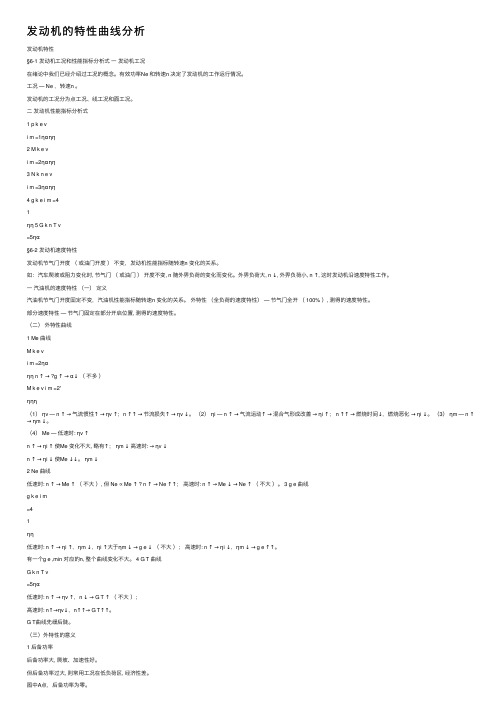
发动机的特性曲线分析发动机特性§6-1 发动机⼯况和性能指标分析式⼀发动机⼯况在绪论中我们已经介绍过⼯况的概念。
有效功率Ne 和转速n 决定了发动机的⼯作运⾏情况。
⼯况 — Ne ,转速n 。
发动机的⼯况分为点⼯况、线⼯况和⾯⼯况。
⼆发动机性能指标分析式1 p k e vi m =1ηαηη2 M k e vi m =2ηαηη3 N k n e vi m =3ηαηη4 g k e i m =41ηη 5 G k n T v=5ηα§6-2 发动机速度特性发动机节⽓门开度(或油门开度)不变,发动机性能指标随转速n 变化的关系。
如:汽车爬坡或阻⼒变化时, 节⽓门(或油门)开度不变, n 随外界负荷的变化⽽变化。
外界负荷⼤, n ↓, 外界负荷⼩, n ↑, 这时发动机沿速度特性⼯作。
⼀汽油机的速度特性(⼀)定义汽油机节⽓门开度固定不变,汽油机性能指标随转速n 变化的关系。
外特性(全负荷的速度特性) — 节⽓门全开( 100% ), 测得的速度特性。
部分速度特性 — 节⽓门固定在部分开启位置, 测得的速度特性。
(⼆)外特性曲线1 Me 曲线M k e vi m =2ηαηη n ↑→ ?g ↑→α↓(不多)M k e v i m =2'ηηη(1)ηv — n ↑→⽓流惯性↑→ηv ↑;n ↑↑→节流损失↑→ηv ↓。
(2)ηi — n ↑→⽓流运动↑→混合⽓形成改善→ηi ↑; n ↑↑→燃烧时间↓,燃烧恶化→ηi ↓。
(3)ηm — n ↑→ηm ↓。
(4) Me — 低速时: ηv ↑n ↑→ηi ↑使Me 变化不⼤, 略有↑;ηm ↓⾼速时: →ηv ↓n ↑→ηi ↓使Me ↓↓。
ηm ↓2 Ne 曲线低速时: n ↑→ Me ↑(不⼤), 但 Ne ∝ Me ↑ ? n ↑→ Ne ↑↑;⾼速时: n ↑→ Me ↓→ Ne ↑(不⼤)。
3 g e 曲线g k e i m=41ηη低速时: n ↑→ηi ↑,ηm ↓,ηi ↑⼤于ηm ↓→ g e ↓(不⼤);⾼速时: n ↑→ηi ↓,ηm ↓→ g e ↑↑。
DO-160E 第八章 振动

RTCA, Inc1828 L Street, NW, Suite 805华盛顿,哥伦比亚特区20036RTCA/DO-160E机载设备的环境条件和试验方法第八章振动重要提示本章中所包含的信息对于所有的试验方法都是适用的,包括在其他章节中所描述的试验方法。
附录A适用于既定环境试验的实施。
批准日期2004年12月9日替代RTCA/DO-160D提出:SC-1358.0 振动8.1试验目的本试验目的为验证待试设备在适当的安装位置上经受规定类别的振动量值时是否符合相关设备性能标准(包括耐久性要求)。
8.2 适用范围以下振动试验适用于螺旋桨推进的固定翼飞机、涡轮喷气飞机、使用涡桨发动机的固定翼飞机、使用桨扇发动机的固定翼飞机和直升机。
本节定义的振动试验是为了验证待试设备是否符合其性能标准。
试验内容的选择取决于以三因素:(1) 飞机类型;(2)试验类别;(3)设备在飞机上的安装位置。
具体要求和步骤在以下章节叙述。
8.2.1 振动试验分类适用类别(类别系列)的选择于设备符合其性能标准的要求程度。
固定翼飞机上的机载设备需进行标准试验和鲁棒试验。
是否进行高量值短时振动试验取决于设备性能的要求。
安装于直升机的机载设备,只需进行鲁棒振动试验。
8.2.1.1标准振动试验( S类)本试验验证固定翼飞机上机载设备在飞机正常飞行时遇到的振动环境中是否能够满足其功能要求。
8.2.1.2健壮振动试验( R类、U类和U2 类)本试验目的为验证设备在经受振动环境时能正常工作,且在经受相当强度的振动环境后仍能正常工作。
鲁棒振动试验同时验证了设备的功能和结构完整性。
所有需要承受长时间振动环境的机载设备都需进行鲁棒振动试验,以验证其对振动环境的承受能力。
设备技术要求需明确该设备是否需进行鲁棒振动试验。
对于安装在未知旋翼频率的直升机上的设备要进行U类和U2类试验。
8.2.1.3高量值短时振动试验( H类、Z 类)高量值瞬间振动环境发生在固定翼飞机的发动机叶片折断时,此为固定翼飞机的异常状态。
航空发动机喘振故障分析

航空发动机喘振故障分析摘要:本文简要介绍了航空发动机喘振的概念和原理,分析了发动机喘振的机理和诱发因素。
通过介绍发动机喘振的主要特征,在分析压气机喘振因素的基础上,提出了中间级放气是一种结构简单、可操作性强的防喘振措施。
同时,多转子发动机具有工作范围广、效率高、不易喘振、适应性好、启动方便等优点,在航空发动机中得到了广泛应用。
总之,要有效地预防和控制发动机喘振问题,必须认真分析原因并采取相应的解决措施。
只有这样才能可靠地保证发动机组的长期稳定运行。
关键词:发动机;喘振;损伤;故障分析;措施1、前言发动机喘振会对航空发动机的运行造成严重危害,是其运行过程中的一种异常状态。
为了保障发动机稳定工作,本文详细论述了发动机喘振的机理和现象。
并就如何控制和预防发动机喘振故障提出了一系列措施和建议,以保证发动机的正常运行。
同时为了提高发动机的效率,保证人员的安全,提高设备操作性,必须采取必要的防喘振措施,以保障发动机的稳定运行。
2、基本概念2.1发动机简介发动机叶轮叶片的前部大多是弯曲的,称为导向轮。
利用快速旋转的叶片增加空气压力,它将气体导入工作叶轮,以减少气流的冲击损失。
小型增压器的发动机叶轮一般由导向轮和工作叶轮组成,在发动机叶轮出口设置扩散器,将叶轮内气体的动能转化为压力。
发动机壳体上一般设有进气口和出气口,进气口一般沿轴向布置,通流部分略有减小,以减小进口阻力,排气口一般设计成蜗杆形状的圆周扩张流道,使高速气流不断扩张,提高了增压器的整体效率。
发动机由涡轮驱动,其主要性能参数为:转速、流量、空气流量、增压比。
2.2喘振现象及判断发动机一旦发生喘振,音调会变低而沉闷,导致设备振动增大,主要表现为压力高、流量波动大。
发动机出口压力和流量波动大,转速不稳定,气压突然下降。
发动机排气温度升高,导致温度过高。
喘振严重时,气流阻断,发动机会熄火停机。
发动机一旦进入喘振状态,首先会引起发动机强烈的机械振动和端部过热,在很短的时间内会对设备部件造成严重损坏。
汽车动力总成悬置系统振动分析及优化设计

上海交通大学硕士学位论文
摘 要
汽车动力总成悬置系统振动分析及优化设计
摘 要
汽车动力总成振动是汽车振动的主要激振源之一,对汽车的舒适性 和 NVH 特性有很大的影响。 设计合理的动力总成悬置系统可以减少振动 传递,提高乘坐舒适性。本文以国产某轿车为研究对象,对动力总成悬 置系统隔振性能进行了分析研究。本文的研究工作包括以下几个方面: 首先,运用拉格朗日方程,建立了动力总成悬置系统动力学方程。 根据试验所获得的模型参数,在 Matlab 和 ADAMS 软件环境中建立了六 自由度仿真模型。 其次,结合实车试验,验证了所建模型准确性,并从系统固有频率 配置及振动解耦角度分析了悬置系统的振动特性;根据实际条件,以提 高系统振动解耦率为目标,应用优化算法对动力总成悬置刚度参数进行 优化设计,通过仿真分析比较了优化前后的固有特性,结果表明优化有 效提高了系统固有频率配置合理性和系统振动解耦率。 最后,建立了动力总成-整车十三自由度动力学模型,其仿真结果表 明优化后悬置刚度参数能改善怠速隔振特性,所建立的模型可以作为悬 置系统优化设计的虚拟样机。 本文的研究结果表明优化设计后的悬置系统其隔振特性有了较大的 改进,所运用的研究方法对悬置系统的优化设计具有一定的指导意义。
k sf k sr csf csr
ϕ
xi yi zi i′ j ′ k ′ PjI q
C
广义坐标方向单位矢量 往复惯性力 ( N ) 二阶往复惯性力 ( N ) 六自由度系统质量矩阵 六自由度系统刚度矩阵 位置转移矩阵 十三自由度系统质量矩阵
T F
第
发动机速度、负荷特性实验项目报告

项目报告—发动机特性曲线学院:车辆与能源学院班级:11车辆工程2班姓名:连伟波学号:110113030036指导教师:王文峰目录一、试验目的二、试验原理三、数据处理四、数据分析五、试验心得一、试验目的1.了解发动机台架性能试验系统的基本结构。
2.了解发动机台架试验设备,仪器和仪表的正确使用方法。
3.掌握汽油机速度特性台架试验的试验方法。
4.掌握汽油发动机速度特性试验数据的处理,能够绘制汽油机速度特性曲线图,并能对特性曲线进行分析。
二、试验原理汽油机速度特性:在汽油机节气门开度一定(部分开度或全开)的情况下,研究其功率Pe 、转矩Ttq、耗油量B及燃油消耗率be与转速n之间的关系。
三、数据处理发动机台架试验所用的是摩托车发动机为单缸机部分试验数据节气门开度分别为18%、38%、58%、78%时的转矩,功率,油耗及燃油消耗率,转速的部分数据(发动机台架试验所用的是摩托车发动机为单缸机,转速为变速器一档时的转速)转矩功率油耗量油耗率36.84 1.08 0.714 535.535.54 1.07 0.721 535.535.87 1.1 0.709 535.536.09 1.16 0.699 535.535.81 1.12 0.685 535.535.71 1.1 0.683 535.536.63 1.16 0.683 535.535.98 1.15 0.683 535.536.36 1.15 0.708 535.536.3 1.14 0.688 535.536.68 1.14 0.678 535.536.52 1.17 0.683 535.536.79 1.15 0.672 535.536.47 1.13 0.657 535.536.34 1.123 0.657 585.236.14 1.12 0.657 585.236.09 1.15 0.627 585.236.63 1.17 0.607 585.236.68 1.15 0.581 585.236.03 1.11 0.546 585.235.43 1.18 0.526 585.235.38 1.27 0.511 585.235.54 1.3 0.511 585.235.33 1.24 0.516 585.235.05 1.3 0.495 585.235.11 1.29 0.49 585.235.27 1.29 0.49 585.235.22 1.29 0.48 585.235.05 1.27 0.475 585.235.16 1.3 0.47 585.235.05 1.3 0.465 585.235.61 1.227 0.465 379.034.84 1.27 0.465 37935 1.28 0.475 37934.89 1.29 0.475 37935.11 1.31 0.47 37934.73 1.29 0.47 37934.19 1.3 0.506 37933.64 1.28 0.475 37933.32 1.33 0.49 37933.21 1.36 0.485 37933.26 1.39 0.475 379根据记录的实验数据运用Excel作出发动机在各个节气门开度时的速度特性曲线。
JIS D 汽车零部件振动试验方法 中文版
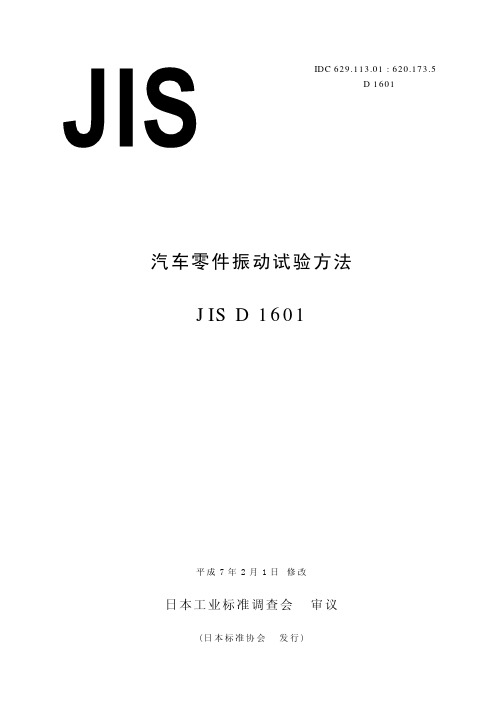
IDC 629.113.01 : 620.173.5D 1601汽车零件振动试验方法JIS D 1601平成7年2月1日修改日本工业标准调查会审议(日本标准协会发行)日本工业标准JIS汽车零件振动试验方法D1601-19951.适用范围 本标准规定了汽车零件(以下称零件)的振动试验方法。
2.试验种类 试验种类分以下几类。
⑴ 共振点检测试验 求零件共振振动频率的试验⑵ 振动性能试验 研究施振时零件性能的试验⑶ 振动耐久试验 研究以一定的振动频率激振,相对于振动的零件耐久性的试验⑷ 扫描振动耐久试验 研究按同样的比例连续增减振动频率激振,相对于振动的零件耐久性的试验3.振动条件分类 振动性能试验及振动耐久试验的振动条件分以下几种。
⑴ 零件的振动条件,按被安装的汽车的种类分:1种 主要指轿车系列2种 主要指公共汽车系列3种 主要指货车系列4种 主要指二轮汽车系列⑵ 零件振动条件按,被安装的状态分:A种 安装在车体或悬架装置的弹簧上,振动较小时B种 安装在车体或悬架装置的弹簧上,振动较大时C种 安装在发动机上,振动较小时D种 安装在悬架装置的弹簧下和安装在发动机上,振动较大时,振动条件分类及相应产品示例如参考表1。
4.试验条件4.1试验顺序 试验按共振点检测试验,振动性能试验,振动耐久试验或扫描振动耐久试验的顺序 进行。
不过,共振点检测试验和振动性能试验,或共振点检测试验和振动性能试验及扫描振动耐久试验同时进行也可以。
4.2 零件的安装 零件安装在振动试验台上的状态原则上应接近于零件的使用状态。
4.3 零件的动作 试验原则上要按零件的动作状态进行。
4.4 施振方法 相对于零件的安装状态,按顺序施加上下、左右、前后垂直的简谐振动。
但是,简谐振动的高次谐波含有率⑴,原则上在振动加速度的25%以内。
注⑴:简谐振动的高次谐波含有率的计算如下:⑴以正弦波振动的振动加速度±a(m/s2),按下式计算:a=Kf2A×10-3其中,K=2π2≈19.74f:振动频率(Hz)A:全振幅(mm)24附图2 振动频率67Hz时的振幅7D 1601 1995附图3 振动频率133Hz时的振幅8附图4 振动频率167Hz时的振幅9附图5 振动频率200Hz时的振幅10附图6 振动频率400Hz时的振幅1112。
发动机特性
项目六发动机特性学习目标:重点掌握发动机的负荷特性、速度特性、万有特性及柴油机调速特性的定义。
理解各个特性曲线的变化趋势及原因;各个曲线的正式成立和位置对发动机的性能有何影响;柴油机安装调速器的原因。
了解柴油机和汽油机特性曲线的异同点及形成原因;万有特性的应用;两级式调速器和全程式调速器对柴油机性能的影响及各自的特点。
本项目是本课程的重点之一。
发动机经常在较大的负荷和转速范围内工作,仅了解某点或几点的性能指标和参数,往往是不够的,而需要了解在整个工作范围内的变化规律和发展趋势。
任务一发动机工况、性能指标与工作过程参数的关系一、工况发动机的运行情况,简称工况。
工况以功率Pe和转速n来表示。
根据发动机的用途,其工况可分为以下几类:(1)恒速工况 n=常数,如发电机组中的发动机,其转速基本保挂持不变,功率Pe随负荷而变化,称为线工况。
(2)螺旋桨工况作为船舶主机的柴油机按推进特性工作,柴油机功率与转速的立主成正比Pe=kn3,k为比例常数,见图中的曲线2。
(3)面工况汽车在运输作业时,发动机的功率Pe和转速n都在很大的范围内变化。
如图中阴影所示,曲线3中发动机在各种转速下所能发出的最大功率。
(4)点工况内燃机的转速n及功率P e均近似不变,如内燃机作为排灌动力。
二、发动机特性发动机性指标随着调整情况及运转工况变化而变化的关系称为发动特性,特性用曲线表示称为特性曲线。
其中随着调整情况而变化又称为调整特性。
发动机的性能特性包括负荷特性、速度特性、万有特性、空转特性等,速度特性又包括外特性和部分速度特性。
三、发动机性能指标与工作过程参数的关系发动机的有效指标P me、T tq、Pe、be、B与工作过程参数的关系如下列诸式:平均有效压力有效功率有效转矩燃油消耗率小时耗油量要了解上述指标随工况变化的情况,就必须分析ηv、ηi、ηm、α随工况的变化。
四、发动机功率标定根据国家标准CB1105.1─1987《内燃机台架性能试验方法》的规定,内燃机标定功率依不同用途分类如下:(1)15min功率适用于汽车、军用车辆、摩托车的发动机功率的标定。
内部标准_振动测试标准
该试验是模拟控制器部件在汽车行驶工作期间的振动负荷。
测试部件的振动耐受能力,以评估部件抗振性能和稳定性。
1.1 说明本标准适合车载控制器产品的振动测试,也适合本公司生产的或采购的其它车载电子产品。
本标准适用于产品SOP定型评判,以及外购车载电子产品的采纳评判。
1.2 相关定义2.0 试验振动试验根据车载安装部位的不同进行选择,并叠加温度循环。
2.1用于安装在发动机上的控制器2.1.1正弦振动试验依照IEC 60068-2-6 标准执行激励,按照以下参数进行试验:图1:用于发动机安装件的正弦振动曲线2.1.2宽带噪声振动试验依照IEC 60068-2-64 标准执行激励,按照以下参数进行试验:图2:用于发动机安装件的宽带噪声振动曲线2.2 用于安装在车身上(簧上质量)的控制器2.2.1 宽带噪声振动试验依照IEC 60068-2-64 标准执行激励,按照以下参数进行试验:图3:用于车身安装件的宽带噪声振动试验曲线2.3 用于安装在底盘上(簧下质量)的控制器依照IEC 60068-2-64 标准执行激励,按照以下参数进行试验:图4 :用于底盘安装件的宽带噪声振动试验曲线2.4 温度叠加循环在上述试验中叠加温度变化。
以模拟真实车辆运行情况下的振动和温度环境。
温度曲线如下图:图5:温度叠加曲线温度循环周期为480分钟,其中135分钟至420分钟为振动叠加区间,每480分钟循环一次,直到累计振动时间大于振动试验要求的时长。
2.4.1 不同安装部位的温度要求对于不同安装部位,温度叠加参数如下:2.5 要求试验期间和试验后,控制器均须达到功能状态A级。
3.0本标准的阶段性实施由于目前公司量产的产品均未进行该试验,且实验室装备水平尚未达到要求,以及预留整改时间等原因,拟分阶段实施本标准。
3.1振动评判级别为了更好地逐步实施本标准,过度阶段引入振动评判级别的概念,不同阶段实施不同的振动评判级别,逐步达到标准要求。
基于ADAMS的微型摆式内燃机振动特性分析
( 煤炭科 学研究 总院 太原 研究 院 , 太原 0 00 ) 3 06
An lss o i r t n c a a t r t s o c o fe it n ay i n v b a i h r c e i i fmir r e ps o o Sc
●
-
一
~
、
J
O
Fe un yHz rq e c( )
图 3运动学激振器
2 建立微 型摆式 内燃机 的振动模 型
Tme sc i (e )
2. 建 立微型摆 式 内燃 机的输入 通道 1
图 1微型摆式内燃机在工作过程中受到在水平方向上的激励
-
将图 1 2中的力作为边彳 振动分析的激振力 ,将激振力施 和 亍
Ke y wor : br to c r c e itc ; ir r es ng p s o e i ; ds Vi a i n ha a t r si s M c o f e wi it n ng ne ADAM S
中 图分 类 号 iH1 文 献标 识码 : T 6 A
1 引言
ctn cai hc aaeorm cai , hc 0 pe eth rcse suei , u i m h s w i i a r l l a m h s w i C1i l n epoess对 qezn t ge n m hs p l g e n m h "m m t t g saig dctn tte Ol m .h uapoesdb eo7rs oolgo p aac .u 一 hpn a utga h let e e gr rcse t f, tny odi a er ebt n i Sz i T s y h 7e in np n
动力总成刚体模态名称
动力总成刚体模态名称简介动力总成是指汽车中负责提供动力的部分,包括发动机、变速器、传动轴和差速器等组成的系统。
而刚体模态则是指刚体在振动过程中产生的模态,即固有频率和振型。
动力总成刚体模态名称就是指动力总成在振动过程中的固有频率和振型的名称。
动力总成刚体模态名称对于汽车工程师来说非常重要,它可以帮助工程师了解动力总成的振动特性,从而优化设计和改进性能。
在汽车设计和制造过程中,动力总成的振动问题会直接影响到汽车的舒适性、稳定性和耐久性。
动力总成刚体模态名称的确定需要进行实验和分析,通过测量和计算动力总成在不同频率下的振动响应,可以确定其固有频率和振型。
这些固有频率和振型的名称可以帮助工程师更好地理解动力总成的振动特性,并制定相应的改进措施。
动力总成振动分析动力总成的振动分析可以通过试验和数值模拟两种方法进行。
试验方法通常使用振动传感器和数据采集系统进行振动测量,可以直接获取动力总成在不同频率下的振动响应。
数值模拟方法则是通过建立动力总成的数学模型,使用有限元分析等方法进行计算,得到动力总成的振动特性。
试验方法的优点是直观、准确,可以真实地反映动力总成的振动情况。
但是试验方法需要耗费大量的时间和资源,并且受到环境条件的限制。
数值模拟方法则可以在计算机上进行,可以快速得到动力总成的振动特性,并且可以进行参数优化和设计改进。
但是数值模拟方法的准确性受到模型的精度和输入数据的影响。
无论使用哪种方法,动力总成的振动分析都需要考虑以下几个方面:1. 动力总成的结构和材料动力总成的结构和材料对其振动特性有着重要影响。
不同的结构形式和材料特性会导致不同的固有频率和振型。
因此,在振动分析中需要准确描述动力总成的结构和材料特性。
2. 动力总成的边界条件动力总成在振动分析中需要考虑其边界条件,即与其他部件的连接方式和约束情况。
边界条件的不同会导致动力总成的振动特性发生变化。
因此,在振动分析中需要准确描述动力总成的边界条件。
- 1、下载文档前请自行甄别文档内容的完整性,平台不提供额外的编辑、内容补充、找答案等附加服务。
- 2、"仅部分预览"的文档,不可在线预览部分如存在完整性等问题,可反馈申请退款(可完整预览的文档不适用该条件!)。
- 3、如文档侵犯您的权益,请联系客服反馈,我们会尽快为您处理(人工客服工作时间:9:00-18:30)。
发动机振动特性分析与试验(精)
发动机振动特性分析与试验
作者:长安汽车工程研究院来源:AI汽车制造业
完善的项目前期工作
预示着更少的项目后期风险,这也是CAE工作的重要意义之一。
在整机开发的前期(概念设计和布置设计阶段),由于没有成熟样机进行NVH试验,很难通过试验的方法预测产品的NVH水平。
因此,通过仿真的方法对整机NVH 性能进行分析甚至优化显得十分重要。
众所周知,发动机NVH是个复杂的概念,包括发动机的振动、噪声以及个体对振动和噪声的主观评价等。
客观地说,噪声与振动也相互联系,因为发动机一部分噪声由结构表面振动直接辐射,另一部分由发动机燃烧和进排气通过空气传播。
除此之外,发动机附件(如风扇)也存在噪声贡献。
本文仅考虑发动机结构振动问题,即在主轴承载荷、燃烧爆发压力和运动件惯性力的作用下,对发动机结构振动进行分析以及与试验的对比。
发动机结构噪声的激励源主要包括燃烧爆发压力、气门冲击、活塞敲击、主轴承冲击、前端齿轮/链驱动和变速器激2. 动力总成模态压缩
缩减有限元模型,得到动力总成的刚度、质量、几何以及自由度信息,用于多体动力学分析。
3. 运动件简化模型建立
发动机中的部分动件不用进行有限元建模,可作简化处理,形成梁-质量点模型,用于多体动力学分析。
其中包括:活塞组、连杆组和曲轴及其前后端。
4. 动力总成多体动力学分析
在定义了动力总成各零部件间连接并且已知各种载荷的情况下,对动力总成进行时域下的多体动力学分析,并对得到的发动机时域和频域下的动态特性进行评判,同时,其输出用于结构振动分析。
5. 动力总成结构振动分析
基于多体动力学分析结果,对整个动力总成有限元模型进行强迫振动分析,得到发动机本体、
变速器以及各种外围件的表面振动特性,进行评判和结构优化。
实例分析
1. 分析对象
以一款成熟的直列四缸1.5L发动机为平台,针对其结构振动问题,对其进行结构振动CAE分析,并与其台架试验结果相比较。
发动机的部分参数如下:缸径75mm,冲程85mm,缸间距84mm,最大缸压6MPa。
2. 坐标定义
为了便于以后叙述,对动力总成进行了坐标定义(见图2)。
图2 动力总成坐标系
3. 动力总成有限元建模及模态校核
整个动力总成包括42万节点和54万单元。
其中,缸体、缸盖和缸盖罩为六面体单元;油底壳、进排气歧管为四边形壳单元;变速器及支架为二阶四面体单元;其他外围零件则简化为质量点,并通过梁单元与机体相连。
图3为其有限元模型,模态分析结果和试验结果如表所示。
图3 动力总成有限元模型
动力总成固有频率结果
通过上表可以看出,CAE分析和模态试验得到的动力总成主要模态结果比较接近,在允许的误差以内。
所以,此模型具有可信性,可以用于强迫响应计算。
当然,从分析和试验的结果也可以看出,本款发动机的整体弯曲模态偏低,有必要进行结构优化。
动力总成动力学分析
1. 整机台架振动试验
在半消声室中进行整机振动测试(见图4),其中,对多处重要的发动机及其外围部件表面位
置安装了传感器。
本实例选择了3处传感器位置进行分析,包括变速器支架端(三向传感器)、差速器底部(三向传感器)以及缸体群部中部(单向传感器)。
传感器输出为速度信号。
试验中测试了发动机在2 000r/min、4500r/min
和5 500r/min共3个转速下的振动特性,其中,每个转速下分别对空载、半载和满载进行了测试。
图4 台架及部分传感安装
2. 动力学仿真分析
通过EXCITE Power Unit建立的动力学模型主要包括发动机零部件、零部件间连接和加载载荷信息。
动力学模型为非线性系统,其中包括所有的线性零部件和部分非线性的零部件连接。
由于客观条件的限制,加载载荷只考虑了燃烧压力、主轴承载荷,而配气机构载荷、变速器载荷和活塞敲击没有考虑在内。
另外,分析得到的结果为动力总成的表面速度,用于与试验结果进行对比。
主轴承载荷和气缸爆发压力见图5、图6。
图5 主轴承载荷
图6 气缸爆发压力
计算工况选择发动机满载工况,转速从2
000r/min到5500r/min,每500r/min 计算一次。
3.仿真结果与试验结果的比较
(1)变速器支架端振动结果比较
仿真和试验的1/3倍频程结果和Campbell如图7~9所示。
图7 变速器支架端振动结果比较(2 000r/mim)
图8 变速器支架端振动结果比较(5 500 r/mim)
图9 变速器支架端振动结果比较-Campbell
从结果可以看出,X方向上:计算与试验结果都在4 000r/min以上出现宽频带的响应;500Hz 以下的频率范围中,计算与试验同时反映出3.5和5.5谐次的振动响应,幅值接近105dB;250~500Hz范围内,计算和试验的幅值状态也一致;高速下,高频带700~800Hz反映出另一共振区域,但频率稍有差异。
Y 方向上:计算与试验结果都明确反映了2.5
谐次的振动响应;4 500r/mim以上,计算与试验结果都明确反映出200~700Hz的宽频带响应,幅值大小也基本一致。
Z方向上:计算与试验结果都明确反映了2谐次和3.5谐次的振动响应;计算与试验结果都明确反映出,Z向振动以300以下的谐频响应为主,在220Hz附近受动力总成弯曲模态的影响,但无明显的共振现象发生。
(2)差速器底部振动结果比较
类似于变速器支架端振动结果的比较,进行差
速器底部仿真和试验结果的比较,得到以下结论:各个转速下,除低频外,两者在整个分析频域下都比较接近;低频处的不协调可能是由于悬置橡胶参数的不准确造成的,需要对橡胶参数进行进一步测试。
(3)缸体群部中部振动结果比较
类似于变速器支架端振动结果的比较,进行缸体群部中部仿真和试验结果的比较可以看出:大部分分析频率范围内,试验和仿真结果比较接近。
结语
基于有限元及系统动力学耦合方法进行发动机振动分析,在一定程度上能够有效地、准确地预测发动机(包括变速器)本身的振动特性。
在没有试验样机的情况下,能够使用该方法结合AVL-EXCITE和相应的有限元分析软件,对发动机的振动特性进行正确地预测和合理的优化工作。
该方法可用于整机振级的判定、悬置
位置选择及特性校验、振源及传递特性分析等。