环锭纺各工序主要任务和工艺流程
布料制造流程简述
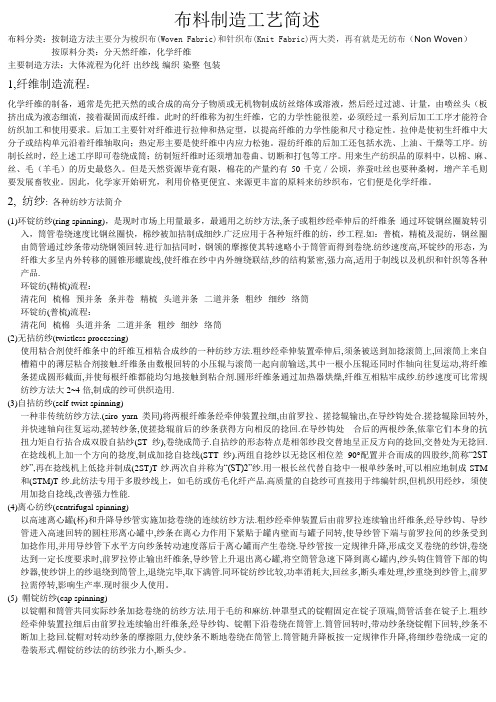
布料制造工艺简述布料分类:按制造方法主要分为梭织布(Woven Fabric)和针织布(Knit Fabric)两大类,再有就是无纺布(Non Woven)按原料分类:分天然纤维,化学纤维主要制造方法:大体流程为化纤-出纱线-编织-染整-包装1,纤维制造流程:化学纤维的制备,通常是先把天然的或合成的高分子物质或无机物制成纺丝熔体或溶液,然后经过过滤、计量,由喷丝头(板挤出成为液态细流,接着凝固而成纤维。
此时的纤维称为初生纤维,它的力学性能很差,必须经过一系列后加工工序才能符合纺织加工和使用要求。
后加工主要针对纤维进行拉伸和热定型,以提高纤维的力学性能和尺寸稳定性。
拉伸是使初生纤维中大分子或结构单元沿着纤维轴取向;热定形主要是使纤维中内应力松弛。
湿纺纤维的后加工还包括水洗、上油、干燥等工序。
纺制长丝时,经上述工序即可卷绕成筒;纺制短纤维时还须增加卷曲、切断和打包等工序。
用来生产纺织品的原料中,以棉、麻、丝、毛(羊毛)的历史最悠久。
但是天然资源毕竟有限,棉花的产量约有50千克/公顷,养蚕吐丝也要种桑树,增产羊毛则要发展畜牧业。
因此,化学家开始研究,利用价格更便宜、来源更丰富的原料来纺纱织布,它们便是化学纤维。
2, 纺纱: 各种纺纱方法简介(1)环锭纺纱(ring spinning),是现时市场上用量最多,最通用之纺纱方法,条子或粗纱经牵伸后的纤维条通过环锭钢丝圈旋转引入,筒管卷绕速度比钢丝圈快,棉纱被加拈制成细纱.广泛应用于各种短纤维的纺,纱工程.如:普梳,精梳及混纺,钢丝圈由筒管通过纱条带动绕钢领回转.进行加拈同时,钢领的摩擦使其转速略小于筒管而得到卷绕.纺纱速度高,环锭纱的形态,为纤维大多呈内外转移的圆锥形螺旋线,使纤维在纱中内外缠绕联结,纱的结构紧密,强力高,适用于制线以及机织和针织等各种产品.环锭纺(精梳)流程:清花间--梳棉--预并条--条并卷--精梳--头道并条--二道并条--粗纱--细纱--络筒环锭纺(普梳)流程:清花间--梳棉--头道并条--二道并条--粗纱--细纱--络筒(2)无拈纺纱(twistless processing)使用粘合剂使纤维条中的纤维互相粘合成纱的一种纺纱方法.粗纱经牵伸装置牵伸后,须条被送到加捻滚筒上,回滚筒上来自槽箱中的薄层粘合剂接触.纤维条由数根回转的小压辊与滚筒一起向前输送,其中一根小压辊还同时作轴向往复运动,将纤维条搓成圆形截面,并使每根纤维都能均匀地接触到粘合剂.圆形纤维条通过加热器烘燥,纤维互相粘牢成纱.纺纱速度可比常规纺纱方法大2~4倍,制成的纱可供织造用.(3)自拈纺纱(self-twist spinning)一种非传统纺纱方法.(siro yarn类同)将两根纤维条经牵伸装置拉细,由前罗拉、搓捻辊输出,在导纱钩处合.搓捻辊除回转外,并快速轴向往复运动,搓转纱条,使搓捻辊前后的纱条获得方向相反的捻回.在导纱钩处合后的两根纱条,依靠它们本身的抗扭力矩自行拈合成双股自拈纱(ST纱),卷绕成筒子.自拈纱的形态特点是相邻纱段交替地呈正反方向的捻回,交替处为无捻回.在捻线机上加一个方向的捻度,制成加捻自捻线(STT纱).两组自捻纱以无捻区相位差90°配置并合而成的四股纱,简称“2ST 纱”,再在捻线机上低捻并制成(2ST)T纱.两次自并称为“(ST)2”纱.用一根长丝代替自捻中一根单纱条时,可以相应地制成STM 和(STM)T纱.此纺法专用于多股纱线上,如毛纺或仿毛化纤产品.高质量的自捻纱可直接用于纬编针织,但机织用经纱,须使用加捻自捻线,改善强力性能.(4)离心纺纱(centrifugal spinning)以高速离心罐(杯)和升降导纱管实施加捻卷绕的连续纺纱方法.粗纱经牵伸装置后由前罗拉连续输出纤维条,经导纱钩、导纱管进入高速回转的圆柱形离心罐中,纱条在离心力作用下紧贴于罐内壁而与罐子同转,使导纱管下端与前罗拉间的纱条受到加捻作用,并用导纱管下水平方向纱条转动速度落后于离心罐而产生卷绕.导纱管按一定规律升降,形成交叉卷绕的纱饼,卷绕达到一定长度要求时,前罗拉停止输出纤维条,导纱管上升退出离心罐,将空筒管急速下降到离心罐内,纱头钩住筒管下部的钩纱器,使纱饼上的纱退绕到筒管上,退绕完毕,取下满管.同环锭纺纱比较,功率消耗大,回丝多,断头难处理,纱重绕到纱管上,前罗拉需停转,影响生产率.现时很少人使用。
环锭纺纱——精选推荐

环锭纺纱新技术——紧密纺(上)秦贞俊教授级高级工程师中国纺织工程学会棉纺织专业委员会当代环锭纺纱在短纤维纺纱体系中占有十分主要的地位,即使在20世纪后20年许多新型纺纱技术已有了很大发展,像转杯纺、喷气枋等新型纺纱体系统具有速度高,产量高及生产费用少的特点。
比环锭纱好,如毛羽、纱疵及条干均匀度等,但所生产纱线的特性在一些方面远不如环锭纱如单纱强力,手感等方面。
一、近期紧密纱环锭纱的研究与开发,使纱线质量得到很大改进,紧密环锭纱的毛羽显著减少,细纱强力进一步提高,断裂伸长率也得到改进,十分有利於生态环境的改进(飞花少),耐磨度提高,手感好及具有理想的纱线结构等。
紧密纺环锭纺纱技术展示了许多优势。
在传统的环锭纺中,从前罗拉钳口线引出的纤维受到加捻,加捻点与前罗拉钳口之间形成纺纱加捻三角区,加捻三角区的外侧纤维承受较大的张力,中间的纤维承受的张力较小。
大部分纤维会加捻成纱,而部分纤维会形成纱线毛羽及飞花。
新型紧密纺环锭纺纱体系,使处於罗拉钳口与加捻点之间三角区的纤维受到控制,从前罗拉钳口引出的纤维束在牵伸区完成牵伸后,受到设在三角区负压的凝聚,在负压凝聚力的作用下,使纤维受控到达加捻点进行加捻,因此,纺纱三角区基本不存在,使所有纺纱三角区中的纤维被凝聚全部被纺成纱。
在普通环锭细纱机中,如图1所示,在离开前罗拉钳口线之前,牵伸区中的纤维束宽度为B,它取决许多因素如纺纱支数,粗纱捻度及牵伸状况。
假如纤维须条离开前罗拉钳口线即开始加捻,对於特定的纱线即一定的纱支并伸直的纤维束,纺纱三角区宽度大小主要取决於卷绕张力P,纺纱三角区b与卷绕张力P成反比,这个关系表明:纺纱三角区的宽度小於喂入须条的宽度,三角区边缘的纤维与纱体连接差的纤维,一端伸在纱体外而另一端被捻入纱体中或者出现不被捻入纱体的情况,由此会产生飞花及纱线毛羽。
与普通环锭纺相反,在紧密环锭纺中,纤维受负压气流的作用,在离开主牵伸区前罗拉钳口的会出现凝聚现象。
精梳环锭纺的纺纱工艺流程及半制品名称

精梳环锭纺的纺纱工艺流程及半制品名称1. 引言1.1 精梳环锭纺简介精梳环锭纺是一种先进的纺纱技术,采用先进的环锭纺纱机进行生产。
该技术在纺纱过程中能够有效剔除纤维中的短纤维和杂质,使纺出的纱线质量更加优秀。
精梳环锭纺具有纤维长度长、纱线强力高、表面光滑等优点,是高档纺织品生产的关键工艺之一。
精梳环锭纺具有高度自动化生产线,生产效率高,可采用多种类型的纤维原料进行生产。
这种技术在纺织行业中得到了广泛应用,生产出的纱线被广泛用于高档纺织品的生产中。
2. 正文2.1 纺纱工艺流程纺纱工艺流程是整个精梳环锭纺生产过程中至关重要的一部分,可以分为精梳纺前处理、精梳纺和精梳纺半制品名称三部分。
首先是精梳纺前处理,这一步骤主要包括原料的准备和清洗工作。
在精梳环锭纺生产过程中,纺纱的原料通常为棉花,而在进行纺纱之前,需要将棉花进行开松、除杂、除尘等处理,以确保纱线的质量和稳定性。
接下来是精梳纺的过程,这一步骤主要包括梳理、拉幅、精梳和牵伸等工序。
在梳理过程中,通过梳理机将棉花进行细分和剥离,去除短纤维和杂质,使纤维平行排列;而在拉幅和精梳过程中,通过拉伸和精梳机的作用,进一步提高纤维的纯度和平行度,使得纱线更加细长和均匀。
最后是精梳纺半制品名称,经过精梳纺的工艺处理,原料棉花被加工成了半成品纱线,常见的精梳纺半制品名称包括精梳棉纱、精梳纱等,这些半成品纱线可以进一步加工成成品纺织品,如衬衫、床上用品等。
通过以上的纺纱工艺流程,精梳环锭纺的生产过程能够保证纱线的质量和稳定性,为纺织品的生产提供了坚实的基础。
2.2 精梳纺前处理精梳纺前处理是精梳环锭纺纱工艺中非常重要的一部分,它主要包括纱线预处理和原料准备两个环节。
纱线预处理是指对原料进行检查、质量分级、控制纤维长度和漂白等工序,以确保纤维质量达到要求。
原料准备则是指对原料进行均匀混合、开松和精梳等处理,使纤维在进入纺纱机之前达到最佳状态。
在纱线预处理阶段,工人首先会对原料进行检查,检查原料是否存在破损、杂质等问题,确保其质量良好。
环锭纺、气流纺、喷气纺、涡流纺、赛络纺、紧密纺简介

环锭纺、气流纺、喷气纺、涡流纺、赛络纺、严密纺简介环锭纺环锭纺纱是现时市场上用量最多,最通用之纺纱方法,条子或粗纱经牵伸后的纤维条通过环锭钢丝圈旋转引入,筒管卷绕速度比钢丝圈快,棉纱被加捻制成细纱.广泛应用于各种短纤维的纺纱工程.如普梳,精梳及混纺,钢丝圈由筒管通过纱条带动绕钢领回转.进展加捻,同时,钢领的摩擦使其转速略小于筒管而得到卷绕.纺纱速度高,环锭纱的形态,为纤维大多呈外转移的圆锥形螺旋线,使纤维在纱中外缠绕联结,纱的结构严密,强力高,适用于制线以及机织和针织等各种产品。
环锭纺(精梳)流程:清花间--梳棉--预并条--条并卷--精梳--头道并条--二道并条--粗纱--细纱--络筒环锭纺(普梳)流程:清花间--梳棉--头道并条--二道并条--粗纱--细纱--络筒气流纺气流纺不用锭子,主要靠分梳辊、纺杯、假捻装置等多个部件。
分梳辊用来抓取和分梳喂入的棉条纤维,同过他的高速回转所产生的离心力可把抓取的纤维甩出。
纺杯是个小小的金属杯子,他的旋转速度比分梳辊高出10倍以上,由此产生的离心作用,把杯子里的空气向外排;根据流体压强的原理,使棉纤维进入气流杯,并形成纤维流,沿着杯的壁不断运动。
这时,杯子外有一根纱头,把杯子壁的纤维引出来,并连接起来,再加上杯子带着纱尾高速旋转所产生的钻作用,就好似一边“喂〞棉纤维,一边加纱线搓捏,使纱线与杯子壁的纤维连接,在纱筒的旋绕拉力下进展牵伸,连续不断的输出纱线,完成气流纺纱的过程。
气流纺的特征气流纺纱有速度大、纱卷大、适应性广、机构简单和不用锭子、钢领、钢丝圈的优点,可成倍的提高细纱的产量。
气流纺与环锭纺的区别气流纺与环锭纺一个是新型纺织技术,一个是老式纺纱技术。
气流纺是气流纺纱,而环锭纺那么是机械纺,就是由锭子和钢铃、钢丝圈进展加捻,由罗拉进展牵伸。
而气流纺那么是由气流方式输送纤维,由一端握持加捻。
一般来说,环锭纱毛羽较少,强度较高,品质较好。
气流纺工序短,原料短绒较多,纱线毛,支数和拈度不能很高,价格也较低。
环锭纺——精选推荐

环锭纺(精梳)清花间——梳棉——预并条——条并卷——精梳——头道并条——二道并条——粗纱——环锭纺纱——络筒环锭纺(普梳)清花间——梳棉——头道并条——二道并条——粗纱——环锭纺纱——络筒气流纺清花间——梳棉——头道并条——二道并条——气流纺纱喷气纺清花间——梳棉——预并条——条并卷——精梳——头道并条——二道并条——喷气纺纱竹节纱是由细纱各粗纱组成,你可测出细纱长度和粗纱长度(细节与粗节间的过渡期不算)用克重量的方法算出细支和粗支(倍数是细支除以粗支),再用平均纱支的方法算综合纱支纱线纺织庇点一. 紗源上的疵點:紗線所帶來的疵點.1. 死棉<1> 特點: 細小針狀白點;中深色易發現.<2> 成因: 紡成紗線的棉纖維(棉花)在成長過程中,發育不良,部分坏死的纖維混在正常纖維中被紡成紗,織成布.由于坏死的纖維無法吸收染料,染不上色,故顯白色針狀,分布于布疋中.<3> 如何處理/避免: 此類現象發生頻率高,一般不可返修,排染時最好排淺色.2. 棉子殼<1> 特點:帶灰色的細小點,一般在花灰布類中較易見.<2> 成因:紡紗時把棉花的細小殼一起紡成紗,織成布<不上色><3> 如何處理:一般用手工挑或用剪毛机來吸改善.3. 粗幼紗<1> 特點:相對正常紡紗而言的,在布疋呈現緯向線圈的粗幼.<2> 成因:在同一條紗中,某一段或几段紗較細或較粗.使織出的布面出現橫的線圈的疏密,此情況可能是一段,可能整疋,嚴重的粗幼紗將聯成橫狀,稱之粗幼紗起橫.<3> 處理:一般無法返修,若作抓毛或磨毛則應該可接受.4. 起橫(包括緊紗起橫/机橫/余紋起橫)<1> 特點:緯向橫紋狀態,有一定循環間距,一定是与緯紋一致.<2> 成因:由于織胚所用的同一棚紗中有一支或一支以上与其它紗支不同,其包括:A.紗線的產期不一致,稱之紗橫.以錯紗起橫為突出. B.由于校机不當或紗線張力不統一,使布面出現一行与上下不同形狀的線圈,稱作机橫.<3> 處理:應与染整剪毛痕,磨毛痕區別分開.注: 因起橫是有規律的橫紋,用肉眼看時側面看較清楚或更換不同角度.5. 橫間:它是起橫的一种,具有起橫之特點,有粗紗橫間,幼紗橫間,色紗橫間等多种.其應區別于"橫漏"."橫漏"指斷紗.6. 污紗<1> 特點:布面有污點或橫向污紗,一定是跟紗走向.<2> 成因:A由于織布的紗筒外層沾上了油污或箱頭筆.B由于織布時該條紗沾上了机油(油紗).<3> 處理:打油槍或落缸除油.7. 紗源的問題除了以上主要6點外,另有黃白紗,雜紗,等等.二. 紡織上的疵點1. 針路<1> 特點:A. 沿經線直上,不會左右移動,除非旁邊的紗也出現針路.B .一般具有透光性,(布身厚的不完全透光)C .在布疋任何地方均可出現,原則上是統疋性<2> 成因:在織造時,由于織針所行走的針坑受損或坑內有積塵,導致織針上落受阻使紗線張力不平均或織針變形(彎曲,歪斜,甚至倒勾)針舌開閉不正常,使該針所織出的線圈形狀有异于其它正常工作的織針所織出的線圈,使布面出現一條連貫的直向白條紋.<3> 處理對策及判斷手法:A 停机不易見或雙層不見,不開底燈不見,則屬輕微.B 驗布机運行与停止都有明顯症狀,屬明顯針路.C 此類情況一般在平紋布与位衣布易產生及發現,且無法返修,應加強對織机及織針的管理.2. 葉路<1> 特點:除了染色后呈線白色特點外,其它与針路相似,且比針路粗一些.<2> 成因:在織造時針舌受損,使該針所織出的線圈被磨損后,在布面出現一條連貫直向條紋.<3> 處理對策与判別手法同針路3. 油針(油路)(1) 短油針(污油針)<1> 特點:沿紗直上,不透光,短短的色路,其位置不固定.<2> 成因:在織造時,有油污沾在一條或几條紗上.少則2-3行,多則8-9行沿紗而上.<3> 處理對策:在未上樹脂漿料時打油槍或落缸除油.(2) 長油針<1> 特點:沿紗而上,不透光長長的色路,其位置不固定.<2> 成因:因織机故障,織机內的潤滑油或油壓過大漏出,在或加潤滑油時過多便會沿著針流到紗上,造成油針.胚布查驗時不易見,染色后布面會出現1-几條沿紗而上,不透光的色路.<3> 處理對策及判斷手法:打油槍/落缸除油;開底燈查看,寬度由寬到窄乃至消失.記錄所在位置及條數4花針<1> 特點:沿紗而上的含針線圈,可能通疋或段落,一條或多條.<2> 成因:由于織針損坏,造成在同一條針路上出現非布身結构需要的含針線圈.嚴重時會有几條紗線含在線圈內.<3> 處理方式:中檢查較難發現,成品檢布易發現.以碼數計.5.斷針<1> 特點:沿紗直上抽針條紋<2> 成因;在織造時由于織針針勾折斷所引起.6.漏針(直漏)<1> 易分辨/其有全疋性/段落性,也有短小及反布漏針等多种.<2>成因:指織造時,織針未能勾起應該進行織造的紗線,從而使原套在織針上等待被下一行紗穿起的線圈.在脫离織針后懸空,隨著織造時本身受力,該線圈往下逐行松脫,從而產生一定長度的漏針.(也稱直漏)附: 漏針是沿紗線直上的(經線方向)而斷紗形狀類似漏針,只是斷紗是橫向(緯線方向),切不可把所謂的橫漏即斷紗當成漏針看待.7.斷紗<1> 特點:橫向順緯線之破洞<2> 成因:由于織布時突然某條紗斷開,而織机之停机裝置未能及時制停,從而在布面出現數支針的破洞.<3> 處理對策;一般不可返修,較小的可縫補.8.爆孔<1> 由于織造時,線用完未能及時駁上<2> 由于紗線張力較弱,在織造時被織針拉斷或染色后整過程中,受各种机台拉力而斷紗.<3> 由于紗線結頭過大或粗妨礙紗線成圈被拉斷.9百足:由于斷紗形成的破洞,用縫紉線將其縫合稱之為百足,染整一般稱作破洞.10.斜間<1> 特點:布面傾斜橫紋,注意并不是斜紋.<2> 成因:由于織机取紗輪的轉速低于合理要求,使織針所勾的紗的張力不平均,從而使布身線圈疏密不一,一經染色,布面便出現斜向橫紋.11.飛花<1> 特點:布面中非布身的外來纖維,以淺色布為多,飛花包括紅色,藍色白色灰色等多种顏色,尤以紅藍為多,又稱紅藍點.<2> 成因,在織造過程中,非織物本身的外來纖維粘附在紗線上,被帶入織物內,這些外來纖維可能是紡紗時混入,亦可能是翻紗或織布時由其它紗帶入.<3> 處理對策:用手工挑,紅藍點用做R/C,高溫處理.一般此類紗應作中深色.12.尼龍草它是飛花的一种,只不過產生飛花外來纖維是尼龍.此類飛花也只能用手工挑.13.紗結即紗線的結頭,一般底多于面,珠地布(尤其是雙珠地)易出現.其成因,原則上織厂要求值机員將紗線打結后剪掉紗尾,所以一般較少紗結,而珠地布多紗結的原因是珠地布其布身結构的特殊性,織厂一般用不經翻紗的紗進行織造,如果紗質不好,結頭多,且紗尾未經修剪,便极容易在布身出現紗結,加上雙珠地是以織机之布底作為成衣之布面.而在織造過程中,紗織于布底出現率大于布面,所以雙珠地又特別易發生紗結.可用手工挑.14.粗結是長度小于一寸的粗紗,一般抓毛布可通過.15.錯紗<1> 即駁錯紗,其特點是顯現的紗圈顏色明顯异于其它部分,是橫狀紗線.<2> 成因:主要由于同棚紗中有一支紗的紗質不同,織造后胚布不易發現,染色后由于該支紗吸附染料的能力与其它部分不同造成該線圈的顏色明顯异于其它部分. 處理方法同起橫.16.胚布刮痕<1> 特點A.一條直上(經向)的連貫直紋端面的圓筒布遍均受磨損.B.有時則為一條直上的間斷直紋,其間距呈一定的遞增或遞減關系(証明成卷的圓筒胚布一端某部分受到意外的磨擦而纖維受擦,可能是一條,可能是兩條,如果兩條則對稱存在.<2> 成因:圓筒胚布儲存過程中,時間太長,積壓太久,或沒有用布頭蓋著全疋布,布邊受到意外的磨損即產生.<3> 一般不可回修,松反布可減少產生的數量.17.胚布中間痕<1> 特點:開邊布的抽針位對面即為布幅中間的一條直上的折痕,但如果圓筒布邊抽針不在布邊則可見兩條.間距為1/2布幅,同樣是平衡直上的折痕.<2> 成因:圓筒胚布長期存倉,布邊長期受壓之下,在染色的染液中無法松馳,而在布面形成一條直上的折痕.其折痕一般不能回修.18.胚布折痕<1>特點:在開幅布的中央或兩邊,一般較為細小,不規則,如果是圓筒布則在兩布邊上.<2>成因;胚布卷得不平整,有折皺,在長期積壓下產生,一般不可返修.19風痕<1> 特點:染不上色,嚴重的布底布面都呈白色,具透光性,輕微的布底呈白色,布面不會.較寬,直向,沿著線方向,一般不會通疋都有,間斷性.<2> 成因:在存放過程中未包好布頭或由于較長時間的存放,胚布圓筒布邊由于長期光照,空气,水分,還原气体的作用,纖維組織受損退化.<3> 一般不可返修,可染淺色.20.織机壓痕沿腺直上,有時會左右移動,布面呈深色,布底淺白色,若一條則是織机導布輪撐布輪仔一邊有力一邊無力造成的,若兩條則是兩邊壓得太緊而造成,不可返修.(2)高捻:此类高捻为棉纱中,有一小段之捻度过大,在织物未染色时,较难发现,但在深色布面上很明显,形成疵点,此类疵点在染色布上以视觉查检,再将数量平均码数记录。
环锭纺纱工艺流程
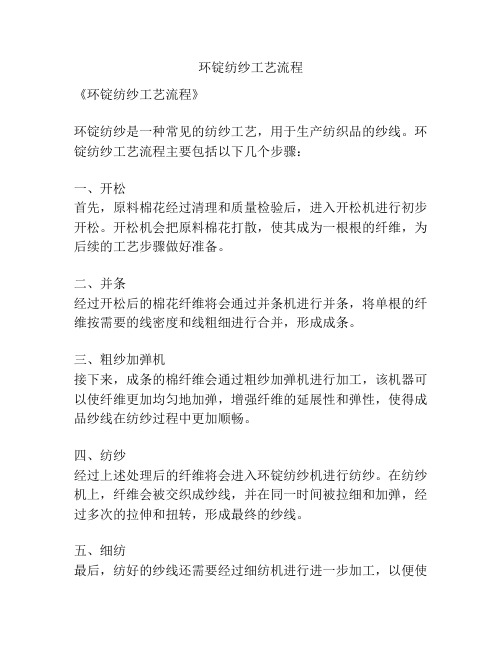
环锭纺纱工艺流程
《环锭纺纱工艺流程》
环锭纺纱是一种常见的纺纱工艺,用于生产纺织品的纱线。
环锭纺纱工艺流程主要包括以下几个步骤:
一、开松
首先,原料棉花经过清理和质量检验后,进入开松机进行初步开松。
开松机会把原料棉花打散,使其成为一根根的纤维,为后续的工艺步骤做好准备。
二、并条
经过开松后的棉花纤维将会通过并条机进行并条,将单根的纤维按需要的线密度和线粗细进行合并,形成成条。
三、粗纱加弹机
接下来,成条的棉纤维会通过粗纱加弹机进行加工,该机器可以使纤维更加均匀地加弹,增强纤维的延展性和弹性,使得成品纱线在纺纱过程中更加顺畅。
四、纺纱
经过上述处理后的纤维将会进入环锭纺纱机进行纺纱。
在纺纱机上,纤维会被交织成纱线,并在同一时间被拉细和加弹,经过多次的拉伸和扭转,形成最终的纱线。
五、细纺
最后,纺好的纱线还需要经过细纺机进行进一步加工,以便使
得纱线更加均匀和细致,以符合纺织品的要求。
以上就是环锭纺纱的工艺流程,经过这些步骤的处理,原料棉花最终会转变成高质量的纱线,为纺织工业提供了坚实的基础。
环锭纺、气流纺、喷气纺、涡流纺、赛络纺、紧密纺简介
环锭纺、气流纺、喷气纺、涡流纺、赛络纺、紧密纺简介环锭纺环锭纺纱是现时市场上用量最多,最通用之纺纱方法,条子或粗纱经牵伸后的纤维条通过环锭钢丝圈旋转引入,筒管卷绕速度比钢丝圈快,棉纱被加捻制成细纱.广泛应用于各种短纤维的纺纱工程.如普梳,精梳及混纺,钢丝圈由筒管通过纱条带动绕钢领回转.进行加捻,同时,钢领的摩擦使其转速略小于筒管而得到卷绕.纺纱速度高,环锭纱的形态,为纤维大多呈内外转移的圆锥形螺旋线,使纤维在纱中内外缠绕联结,纱的结构紧密,强力高,适用于制线以及机织和针织等各种产品。
环锭纺(精梳)流程:清花间--梳棉--预并条--条并卷--精梳--头道并条--二道并条--粗纱--细纱--络筒环锭纺(普梳)流程:清花间--梳棉--头道并条--二道并条--粗纱--细纱--络筒气流纺气流纺不用锭子,主要靠分梳辊、纺杯、假捻装置等多个部件。
分梳辊用来抓取和分梳喂入的棉条纤维,同过他的高速回转所产生的离心力可把抓取的纤维甩出。
纺杯是个小小的金属杯子,他的旋转速度比分梳辊高出10倍以上,由此产生的离心作用,把杯子里的空气向外排;根据流体压强的原理,使棉纤维进入气流杯,并形成纤维流,沿着杯的内壁不断运动。
这时,杯子外有一根纱头,把杯子内壁的纤维引出来,并连接起来,再加上杯子带着纱尾高速旋转所产生的钻作用,就好像一边“喂”棉纤维,一边加纱线搓捏,使纱线与杯子内壁的纤维连接,在纱筒的旋绕拉力下进行牵伸,连续不断的输出纱线,完成气流纺纱的过程。
气流纺的特征气流纺纱有速度大、纱卷大、适应性广、机构简单和不用锭子、钢领、钢丝圈的优点,可成倍的提高细纱的产量。
气流纺与环锭纺的区别气流纺与环锭纺一个是新型纺织技术,一个是老式纺纱技术。
气流纺是气流纺纱,而环锭纺则是机械纺,就是由锭子和钢铃、钢丝圈进行加捻,由罗拉进行牵伸。
而气流纺则是由气流方式输送纤维,由一端握持加捻。
一般来说,环锭纱毛羽较少,强度较高,品质较好。
气流纺工序短,原料短绒较多,纱线毛,支数和拈度不能很高,价格也较低。
环锭纺各工序主要任务和工艺流程
环锭纺各工序主要任务和工艺流程一、环锭前纺1、清花(1)主要任务:开松、除杂、混和。
(2)工艺流程:抓棉机BOA→多功能分离机SP-MF→预清棉机CL-P→TV425风机→10仓混棉机MX-I→强力除尘机SP-DX 2、梳棉(1)主要任务:除杂、梳理、牵伸、成条。
(2)工艺流程:二路分棉→均棉箱→给棉罗拉→剌辊部分→锡林及盖板工作区→道夫→剥棉罗拉大压辊→喇叭口→圈条器→棉桶(生条)3、并条(1)主要任务:并合、混和、牵伸、成条。
(2)工艺流程:导条圈→导条架(压辊)→断头感应器→导条栅→四导轮→自调匀装置→给棉板→牵伸系统(皮辊、罗拉)→集束口→喇叭口→紧压罗拉→圈条器→棉桶(熟条)4、条并卷(1)主要任务:除杂、梳理、牵伸、成卷。
(2)工艺流程:棉条桶→棉条架→棉条喂入装置→牵伸部分→紧压罗拉→卷绕头→有齿成卷罗拉→棉卷夹盘→棉卷筒成卷5、精梳(1)主要任务:梳理、除杂、牵伸、成条。
(2)工艺流程:棉卷→承卷罗拉→过棉板→偏心轮→上下钳板→顶梳→锡林→毛刷→分离皮辊→分离罗拉→输出皮辊→输出罗拉→压辊→导条柱→合面板→后区牵伸罗拉→前区牵伸罗拉→牵伸皮辊→伸头吹管→喇叭口→压辊→输送带→喇叭口→凹罗拉→凸罗拉→卷条器→棉条筒6、粗纱(1)主要任务:牵伸、加捻、卷绕与成形。
(2)工艺流程:棉桶→葡萄架→牵伸部分→集束器→假捻器→锭翼→压掌→筒管二、环锭后纺1、细纱(1)主要任务:除杂、牵伸、加捻、成纱。
(2)工艺流程:a正常纱机台:粗纱→导纱杆→横动装置→牵伸装置→前罗拉(紧密纺机台才有)→纱钩→钢丝圈→钢领→管纱b氨纶包芯纱机台:粗纱→导纱杆→氨纶丝→托辊→导丝轮→前皮辊→前罗拉(紧密纺机台才有)→纱钩→钢丝圈→钢领→管纱2、络筒(1)主要任务:按成纱要求将前道工序送来的细纱管纱络成筒子纱,并圈绕成一定的规格形状的筒子,供后道工序使用,同时,通过清纱装置的作用,进一步清除管纱一定长度、粗、细的纱疵,提高成纱质量。
立达全流程
标题: 立达全流程纺纱系统第1楼 方志同 发表于 2007/12/19 12:25立达是全球唯一一家提供整套从纤维到纱线的环锭纺纱系统和转杯纺纱系统的供应商,因此能为客户提供最优化的产品解决方案。
只有从抓棉机到最终纺纱工序的工艺优化组合,才能确保所需纱线品质能够实现,使之具有最大的灵活性和经济性。
立达环锭纺系统工序流程:立达转杯纺系统工序流程:第2楼 方志同 发表于 2007/12/19 12:26立达紧凑型短流程开清系统立达开清棉生产线完全保证您的系统在高效除杂和高产量条件下极其温和处理并充分混和原棉。
设备在减少清洁作用点的同时却可以保证其更加有效的除杂,所需能耗更低。
随着开松和除杂一步一步地深入,所有的棉,化纤和混纺纤维得到了充分的混合梳理。
现代化的立达开清棉系统是基于以下两个主要设计思想:两步开清通过VarioSet简便地设定机器的工艺参数立达开清棉设备具有极其多样化的功能:相同的操作原理和标准化的零部件使今后的维修保养十分简便,以及技术领先的控制系统。
两者紧密的结合保证了最大生产效率下所需空间的最小。
独立的开清棉改装件设计保证了最优的灵活配置,系统的高效率同时赋予了最快的投资回报承诺。
立达拥有开清棉系统每一个环节的机器:全自动抓棉机UNIFLOC A 11抓棉机-开清时,温和开松成细小纤维束,为最大清洁特性提供了理想的前提条件更大的纤维束表面积可以获得更高的清洁效率第3楼方志同发表于2007/12/19 12:37 两级清棉和VARIOSETUNIclean B 12预清棉机,温和而彻底的清洁原料;CLEANfeed集成了精细清棉的梳棉箱,配合梳棉机,始终在生产中保持纤维供给。
VarioSet控制系统确保在使用不同的原棉时,高产量且保持高度的灵活性。
所有的设定可以重复利用。
彻底混棉的最佳选择UNIBLEND A 81可对多达8种不同的原料进行定量的混棉,生产色纱当中最热销的产品,提高了下游工序的质量。
C29.5 K环锭纺普梳纯棉针织纱工艺设计
C29.5 K环锭纺普梳纯棉针织纱工艺设计目录第一章概述 (1)1.1纱线产品设计的目的与基本要求 (1)1.2纱线产品设计的方法与要点 (1)1.3纱线产品设计的方案与产品质量要求 (1)1.4纺纱工艺流程与设备选型 (2)第二章纺纱原料的选配 (3)2.1原棉选配的基本原则 (3)2.2原棉选配的方法 (3)2.3原棉选配方案及分类排队表 (3)第三章开清工艺流程、设备选型与主要工艺 (4)3.1开清工艺流程选择的基本原则 (4)3.2开清工艺流程与设备选型 (4)3.3开清工序主要工艺 (5)3.4开清工序质量控制 (5)第四章梳棉工艺参数的选择与工艺计算 (6)4.1设计要点 (6)4.2工艺参数设计 (6)4.3生条质量控制 (10)第五章并粗细捻工艺参数的选择与工艺计算 (11)5.1并条 (11)5.2精梳 (13)5.3粗纱 (16)5.4细纱 (19)第六章总结 (23)参考文献 (23)附录1 配棉排队表 (24)附录2 各道工序工艺计算汇总表.......................... 错误!未定义书签。
第一章概述1.1 纱线产品设计的目的与基本要求1.纱线产品设计的目的:《纱线产品设计》是与《纺纱学》课程相配套的实践教学内容。
学生通过纺纱工艺设计,加深对理论教学内容的理解,同时也初步掌握棉纺工艺设计的基本原理和方法。
2.纱线产品设计基本要求:(1)原棉选配及配棉:主要根据所给定的纱线品种选择原棉、配棉和配棉等级计算。
(2)清花工艺流程:根据给定的纱线品种选择适当的工艺流程。
工艺流程包括:清花工艺流程、梳棉、并条、(精梳)、粗纱、细纱等。
选择工艺流程时应选择最近几年的纺机产品和较为成熟的工艺流程。
(3)棉卷定量设计、清花工艺参数:对于清梳不联的工艺流程,棉卷定量要求设计计算;清梳联工艺流程则不要求进行设计。
根据给定的细纱品种,设计棉卷定量。
清花工艺参数主要是棉卷定量设计。
- 1、下载文档前请自行甄别文档内容的完整性,平台不提供额外的编辑、内容补充、找答案等附加服务。
- 2、"仅部分预览"的文档,不可在线预览部分如存在完整性等问题,可反馈申请退款(可完整预览的文档不适用该条件!)。
- 3、如文档侵犯您的权益,请联系客服反馈,我们会尽快为您处理(人工客服工作时间:9:00-18:30)。
环锭纺各工序主要任务和工艺流程
一、环锭前纺
1、清花
(1)主要任务:开松、除杂、混和。
(2)工艺流程:抓棉机BOA→多功能分离机SP-MF→预清棉机CL-P→
TV425风机→10仓混棉机MX-I→强力除尘机SP-DX 2、梳棉
(1)主要任务:除杂、梳理、牵伸、成条。
(2)工艺流程:二路分棉→均棉箱→给棉罗拉→剌辊部分→锡林及盖
板工作区→道夫→剥棉罗拉大压辊→喇叭口→圈条
器→棉桶(生条)
3、并条
(1)主要任务:并合、混和、牵伸、成条。
(2)工艺流程:导条圈→导条架(压辊)→断头感应器→导条栅→四
导轮→自调匀装置→给棉板→牵伸系统(皮辊、罗拉)
→集束口→喇叭口→紧压罗拉→圈条器→棉桶(熟
条)
4、条并卷
(1)主要任务:除杂、梳理、牵伸、成卷。
(2)工艺流程:棉条桶→棉条架→棉条喂入装置→牵伸部分→紧压罗
拉→卷绕头→有齿成卷罗拉→棉卷夹盘→棉卷筒成
卷
5、精梳
(1)主要任务:梳理、除杂、牵伸、成条。
(2)工艺流程:棉卷→承卷罗拉→过棉板→偏心轮→上下钳板→顶梳
→锡林→毛刷→分离皮辊→分离罗拉→输出皮辊→
输出罗拉→压辊→导条柱→合面板→后区牵伸罗拉
→前区牵伸罗拉→牵伸皮辊→伸头吹管→喇叭口→
压辊→输送带→喇叭口→凹罗拉→凸罗拉→卷条器
→棉条筒
6、粗纱
(1)主要任务:牵伸、加捻、卷绕与成形。
(2)工艺流程:棉桶→葡萄架→牵伸部分→集束器→假捻器→锭翼→
压掌→筒管
二、环锭后纺
1、细纱
(1)主要任务:除杂、牵伸、加捻、成纱。
(2)工艺流程:
a正常纱机台:
粗纱→导纱杆→横动装置→牵伸装置→前罗拉(紧密纺机台才有)→纱钩→钢丝圈→钢领→管纱
b氨纶包芯纱机台:
粗纱→导纱杆→氨纶丝→托辊→导丝轮→前皮辊→前罗拉(紧密纺机台才有)→纱钩→钢丝圈→钢领→管纱
2、络筒
(1)主要任务:按成纱要求将前道工序送来的细纱管纱络成筒子纱,并圈绕成一定的规格形状的筒子,供后道工序使用,
同时,通过清纱装置的作用,进一步清除管纱一定长
度、粗、细的纱疵,提高成纱质量。
(2)工艺流程:菊花盘→锭脚→气圈破裂器→断头感应器→机械清
纱器→张力盘→捻接器→电子清纱器→张力传感器
→捕纱器→槽筒→夹纱夹→筒子。