裂解汽油加氢
汽油加氢工艺原理
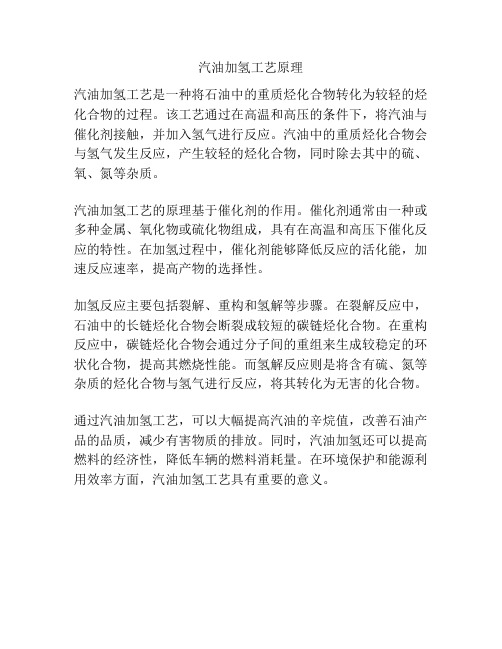
汽油加氢工艺原理
汽油加氢工艺是一种将石油中的重质烃化合物转化为较轻的烃化合物的过程。
该工艺通过在高温和高压的条件下,将汽油与催化剂接触,并加入氢气进行反应。
汽油中的重质烃化合物会与氢气发生反应,产生较轻的烃化合物,同时除去其中的硫、氧、氮等杂质。
汽油加氢工艺的原理基于催化剂的作用。
催化剂通常由一种或多种金属、氧化物或硫化物组成,具有在高温和高压下催化反应的特性。
在加氢过程中,催化剂能够降低反应的活化能,加速反应速率,提高产物的选择性。
加氢反应主要包括裂解、重构和氢解等步骤。
在裂解反应中,石油中的长链烃化合物会断裂成较短的碳链烃化合物。
在重构反应中,碳链烃化合物会通过分子间的重组来生成较稳定的环状化合物,提高其燃烧性能。
而氢解反应则是将含有硫、氮等杂质的烃化合物与氢气进行反应,将其转化为无害的化合物。
通过汽油加氢工艺,可以大幅提高汽油的辛烷值,改善石油产品的品质,减少有害物质的排放。
同时,汽油加氢还可以提高燃料的经济性,降低车辆的燃料消耗量。
在环境保护和能源利用效率方面,汽油加氢工艺具有重要的意义。
裂解汽油加氢二段催化剂使用效果分析
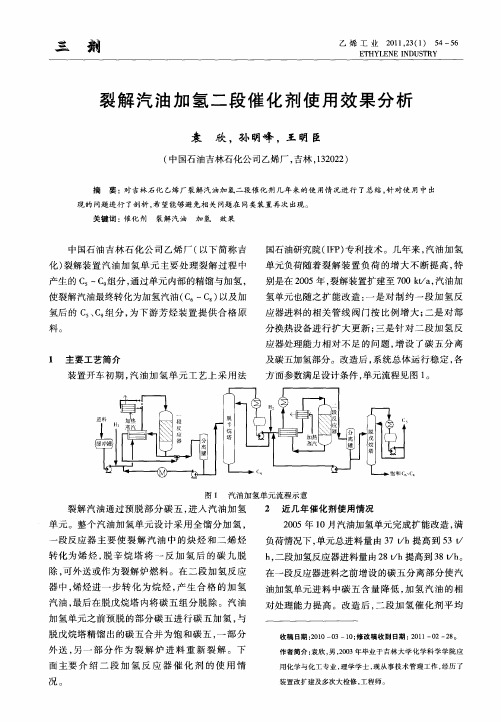
应器进 料 的相 关 管 线 阀 门按 比例 增 大 ; 二是 对 部 分换 热设备 进 行 扩 大 更 新 ; 是 针 对 二段 加 氢反 三 应器处 理 能力 相 对 不 足 的 问题 , 设 了碳 五 分 离 增
1 主要 工艺简 介
及碳五 加氢 部分 。改 造后 , 系统 总 体运 行 稳定 , 各 方面参 数满 足设 计条件 , 单元 流程 见 图 1 。
差是 造成 产 品超标 的主要 原 因 。
20 07年 6月加 氢 汽 油 产 品 出现 超标 , 过 对 经
一
段、 二段 加 氢 反应 器 床 层 温 度 进 行 最 大 限 度 调
整, 同时对 相关点 进行 取样 分析 , 结果 发 现 :1 单 () 元 进料 组分 , 初馏 点 7 . 终 馏 点 186℃ , 4 6o C, 7. 密 度 0 823gm 这 些 基 本 参 数 与催 化 剂 使 用 之 .6 / L, 初 无 大 幅 变 化 ; 2) 段 反 应 器 人 口双 烯 值 为 ( 一 1.O 10g出 1双 烯 值 为 14 10g 已满 65 0 , : 3 .7 0 , 足 设计要 求 ( / 0 ) 说 明一 反 运 行 状 态正 ≤3g 10g ,
段反应器 主要 使裂解 汽油 中的炔 烃 和二 烯烃
负荷情况下 , 单元总进料量由 3 h提高到 5 / 7t / 3t /
h二 段加 氢反应 器进料 量 由 2 h提高 到 3 h , 8t / 8t 。 / 在一段 反应 器进 料之前 增 设 的碳 五 分 离部 分 使 汽
转化为烯烃 , 辛烷 塔将 一 反加 氢后 的碳九 脱 脱 除 , 外 送 或作 为 裂解 炉 燃 料 。在 二 段 加 氢 反 应 可
加氢裂化工艺流程介绍

加氢裂化工艺流程介绍加氢裂化是一种重要的石油加工工艺,可以将高沸点石油馏分转化为低沸点馏分,同时提高汽油和润滑油基础油的数量和质量。
本文将介绍加氢裂化的工艺流程。
1. 原料引入原料通常是经过预处理的石油馏分或重油,经过加热后进入加氢裂化反应器。
通常预处理过程包括脱蜡、脱硫、脱氮、脱水等步骤,以保证原料质量达到反应器的要求。
2. 加氢在反应器中,原料与氢气混合,压力一般在20到70大气压之间。
加氢操作是为了提供反应所需的氢气,并将部分反应产物中产生的芳烃和不饱和化合物氢化,达到减少积碳和减少杂质的目的。
3. 热解在反应器中,加热的原料和氢气混合物进入热解区域,受热后发生热解反应。
热解反应是原料中分子裂解成较小分子的过程,该过程有利于提高汽油和基础油的数量和质量。
裂解反应产生的芳烃、烯烃、脂肪烃等不饱和物质,进一步参与裂解反应。
4. 转化原料中分子的热解不仅分解了大分子化合物,而且还通过转化产生了新的分子,这是加氢裂化的重要特点。
转化反应相当于将一种化合物转化成另一种化合物。
该过程对于提高工艺效率和提高产品质量有重要意义。
5. 冷凝加氢裂化的反应产物中包含大量的不同碳数的烃烃类化合物。
从反应器中出来的气体混合物在经过冷却后,其中的液态混合物进入分离器进行进一步的分离。
尤其是汽油和润滑油基础油在冷凝后可以直接由分离器分离出来,经过蒸馏后得到最终产品。
6. 氢气回收由于反应过程需要大量的氢气,因此需要对反应后剩余的氢气进行回收。
在回收前,需要将氢气先进行压缩,进而进行氢气的回收和再利用。
7. 产品储存和输送从分离器中分离出来的产品由输送系统输送到储罐中进行储存。
对于汽油和润滑油基础油需要进行进一步的精制,以提高其纯度和质量,最终得到优质的成品。
总之,加氢裂化工艺流程具有较高的生产效率和制品质量,可以为石油化工行业提供具有重要价值的产品。
裂解汽油加氢装置的节能降耗技术措施
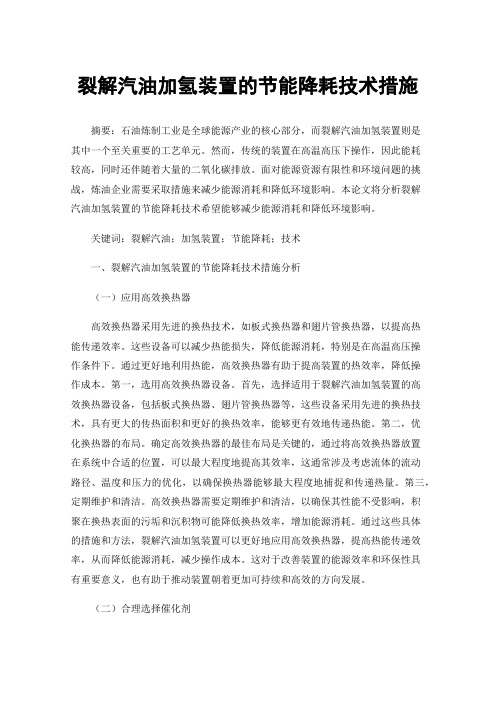
裂解汽油加氢装置的节能降耗技术措施摘要:石油炼制工业是全球能源产业的核心部分,而裂解汽油加氢装置则是其中一个至关重要的工艺单元。
然而,传统的装置在高温高压下操作,因此能耗较高,同时还伴随着大量的二氧化碳排放。
面对能源资源有限性和环境问题的挑战,炼油企业需要采取措施来减少能源消耗和降低环境影响。
本论文将分析裂解汽油加氢装置的节能降耗技术希望能够减少能源消耗和降低环境影响。
关键词:裂解汽油;加氢装置;节能降耗;技术一、裂解汽油加氢装置的节能降耗技术措施分析(一)应用高效换热器高效换热器采用先进的换热技术,如板式换热器和翅片管换热器,以提高热能传递效率。
这些设备可以减少热能损失,降低能源消耗,特别是在高温高压操作条件下。
通过更好地利用热能,高效换热器有助于提高装置的热效率,降低操作成本。
第一,选用高效换热器设备。
首先,选择适用于裂解汽油加氢装置的高效换热器设备,包括板式换热器、翅片管换热器等,这些设备采用先进的换热技术,具有更大的传热面积和更好的换热效率,能够更有效地传递热能。
第二,优化换热器的布局。
确定高效换热器的最佳布局是关键的,通过将高效换热器放置在系统中合适的位置,可以最大程度地提高其效率,这通常涉及考虑流体的流动路径、温度和压力的优化,以确保换热器能够最大程度地捕捉和传递热量。
第三,定期维护和清洁。
高效换热器需要定期维护和清洁,以确保其性能不受影响,积聚在换热表面的污垢和沉积物可能降低换热效率,增加能源消耗。
通过这些具体的措施和方法,裂解汽油加氢装置可以更好地应用高效换热器,提高热能传递效率,从而降低能源消耗,减少操作成本。
这对于改善装置的能源效率和环保性具有重要意义,也有助于推动装置朝着更加可持续和高效的方向发展。
(二)合理选择催化剂催化剂在裂解汽油加氢过程中起到关键作用,正确选择催化剂可以改善反应条件,包括降低反应温度和压力,从而减少热耗散。
此外,催化剂还可以提高反应速率,减少能源消耗,并减少副产物的生成,提高了装置的效率。
加氢裂化工艺流程
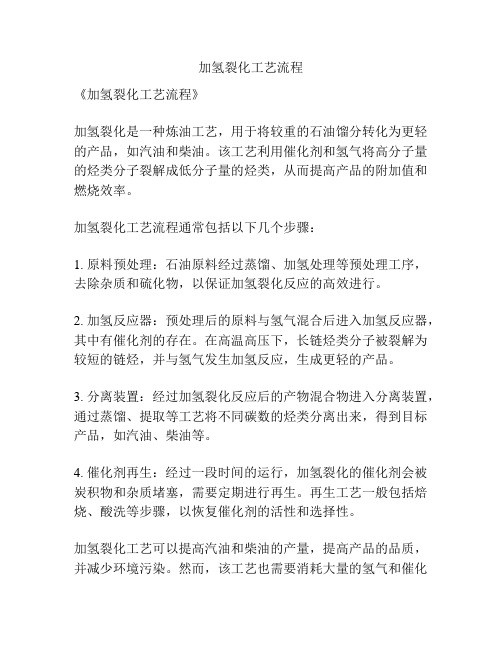
加氢裂化工艺流程
《加氢裂化工艺流程》
加氢裂化是一种炼油工艺,用于将较重的石油馏分转化为更轻的产品,如汽油和柴油。
该工艺利用催化剂和氢气将高分子量的烃类分子裂解成低分子量的烃类,从而提高产品的附加值和燃烧效率。
加氢裂化工艺流程通常包括以下几个步骤:
1. 原料预处理:石油原料经过蒸馏、加氢处理等预处理工序,去除杂质和硫化物,以保证加氢裂化反应的高效进行。
2. 加氢反应器:预处理后的原料与氢气混合后进入加氢反应器,其中有催化剂的存在。
在高温高压下,长链烃类分子被裂解为较短的链烃,并与氢气发生加氢反应,生成更轻的产品。
3. 分离装置:经过加氢裂化反应后的产物混合物进入分离装置,通过蒸馏、提取等工艺将不同碳数的烃类分离出来,得到目标产品,如汽油、柴油等。
4. 催化剂再生:经过一段时间的运行,加氢裂化的催化剂会被炭积物和杂质堵塞,需要定期进行再生。
再生工艺一般包括焙烧、酸洗等步骤,以恢复催化剂的活性和选择性。
加氢裂化工艺可以提高汽油和柴油的产量,提高产品的品质,并减少环境污染。
然而,该工艺也需要消耗大量的氢气和催化
剂,并且对原料的要求较高,因此需要精细的工艺控制和运行管理。
随着石油工业的不断发展,加氢裂化工艺也在不断完善和优化,以适应市场的需求和环保的要求。
裂解汽油加氢催化剂的影响因素及应对措施

裂解汽油加氢催化剂的影响因素及应对措施摘要:作为乙烯生产过程中的副产物,裂解汽油随着乙烯工业的快速发展和乙烯加工能力地提高其产量也不断增加。
裂解汽油中含有丰富的芳烃类及其他如硫、氮、氧、氯等多种化合物,需要进行加氢催化剂操作。
本文通过围绕裂解汽油氢催化剂应用的实际经验,对加氢催化剂的寿命影响因素进行分析,并提出相关应对措施,以供参考。
关键词:裂解汽油;加氢催化剂;影响因素;应对措施当前乙烯加工能力地提高促进了其副产品裂解汽油产量的增加,裂解汽油芳烃含量的高达60%-80%。
目前裂解汽油加氢催化剂的工艺主要是部分馏分二段加氢工艺。
第一段主要是饱和二烯烃,其次是单烯烃和少量苯乙烯。
第二段主要饱和一段没有饱和的大部分单烯烃,其次是少量的二烯烃和硫、氮等杂质。
下文主要围绕于裂解汽油加氢催化剂的影响因素与应对措施展开分析,以促进加氢催化剂的使用寿命的有效延长。
1裂解汽油加氢催化剂影响因素分析1.1二段催化剂的影响1.1.1催化剂活性的影响二段加氢催化剂一般具有加氢选择性好、脱硫活性高、热稳定性高等优点,但如果加氢催化剂的初始活性反应温度较高,会导致加氢催化剂在催化剂床层中未加氢饱和的二烯烃发生结焦聚合反应,催化剂的失活率加快,从而降低加氢催化剂的使用寿命,同时产品质量也会随之下降。
其次裂解汽油或裂解装置中所带有的毒物如砷化物也会对催化剂的活性造成影响。
由于加氢之前需要对裂解汽油进行液相脱砷,在进行重质化脱身反应过程中砷容易滞留装置,这种砷化物的积压对非贵金属催化剂属性的二段催化剂造成活性无法恢复的影响。
1.1.2催化剂上积炭的影响催化剂上的积炭形成主要有两种途径,一是原料油在进行加热、蒸馏等预处理过程中形成的胶质沉积在催化剂表面;二是在催化剂孔道中吸附的不饱和烃分子和相邻的不饱和烃分析产生聚合反应或者缩合反应形成积炭大分子。
积炭的形成也影响加氢催化剂的使用期限。
1.2原料油性质对催化剂的影响一是原料油水分的影响。
加氢裂化原理

加氢裂化原理
加氢裂化原理是一种石油加工技术,用于将较重的石油烃转化为较轻的烃类。
它主要通过加入氢气使得重质石油烃发生裂解反应,产生较轻的烃类化合物。
加氢裂化是一种催化裂化过程,需要催化剂的参与。
通常使用铂、钴、镍等金属作为催化剂,以保证反应的高效性和选择性。
裂化过程中,加入的氢气在催化剂的作用下与重质石油烃发生反应,生成较轻的烃类化合物和水。
这种化学反应被称为加氢裂化。
加氢裂化的原理是基于分子结构的裂变。
重质石油烃在催化剂的作用下,通常发生饱和、断裂和重排等反应,从而生成较轻的烃类化合物。
这个过程中,氢气提供了所需的氢原子,帮助重质石油烃发生裂解和转化。
同时,氢气的参与还可以防止催化剂中毒,延长其使用寿命。
加氢裂化广泛应用于石油炼制和石化工业。
通过加氢裂化,可以将重质石油烃转化为轻质烃类,如石脑油、汽油等。
这不仅有助于提高石油产品的产量和质量,还有利于满足市场需求和提高能源利用率。
总之,加氢裂化通过加入氢气和催化剂,将重质石油烃裂解为较轻的烃类化合物。
这种技术在石油加工和石化工业中具有重要作用,为提高能源利用效率和产物质量提供了可行途径。
FH-40A型催化剂在裂解汽油二段加氢中的应用

大连理工大学化学工程专业 , 现从事 裂解汽油加 氢工艺技 术
管理 及 半 再 生 催 化 重 整 工 艺 技 术 管 理 工 作 , 整 车 间 工 艺 技 重
术管理高级工程师 , 师。 工程
・
5 ・ 6
乙 烯 工 业
表 7 一 、 段 原 料 数 据 二
第2 2卷
从 图 3可 看 出 , 化 剂 加 氢 饱 和双 键 及 脱 硫 催
效果 均较 好 , 经过初 期 几个 月 的 运行 来看 , 应 且 反
器 压差 变化不 大 ( 图 4 。 见 )
ห้องสมุดไป่ตู้
裂解汽油分析数据( 一段进料 ) 一段加氢油分析数据( 二段进料)
相对密度 总 硫/ m k ) ( g・ g
MA / mg・ 。 ) V ( g 。 Ir( 10g ) B! g・ 0
填数 据 。
表 1 催化剂装填数据
项目 高度/ u nn体积/ m。 重量/ 堆积密度/ t mI ) t ( ・ 3
德希尼布公司引进, 采用法 国石油研究院(F ) IP 专
利 。装置 以裂 解 装 置 副 产 的 裂 解 汽 油 和 炼 油 厂 P A氢气 为 原 料 , 过 第 一 段加 氢 将 原 料 中 的二 S 通
收稿 日期 :0 0—0 0 。 21 2— 9 作者 简 介 : 成 威 ( 9 1一) 男 , 宁 海 城 人 ,0 1年 毕 业 于 王 17 , 辽 20
严重 , 旧剂粉化较严重 , 颜色变为深 灰或纯黑 色。
对 旧剂 进行 卸 除 , 换 新 的 F 一4 A 型催 化 剂 , 更 H 0 K 0 反 应 器 内径 为 10 0 m 21 0 m。表 1为新 剂 的装
- 1、下载文档前请自行甄别文档内容的完整性,平台不提供额外的编辑、内容补充、找答案等附加服务。
- 2、"仅部分预览"的文档,不可在线预览部分如存在完整性等问题,可反馈申请退款(可完整预览的文档不适用该条件!)。
- 3、如文档侵犯您的权益,请联系客服反馈,我们会尽快为您处理(人工客服工作时间:9:00-18:30)。
1 第二节 裂解汽油加氢 一、裂解汽油的组成 裂解汽油含有C6~C9芳烃,因而它是石油芳烃的重要来源之一。裂解汽油的产量、组成以及芳烃的含量,随裂解原料和裂解条件的不同而异。例如,以石脑油为裂解原料生产乙烯时能得到大约20%(质、下同)的裂解汽油,其中芳烃含量为40~80%; 用煤柴油为裂解原料时,裂解汽油产率约为24%,其中芳烃含量达45%左右。 裂解汽油除富含芳烃外,还含有相当数量的二烯烃、单烯烃、少量直链烷烃和环烷烃以及微量的硫、氧、氮、氯及重金属等组分。 裂解汽油中的芳烃与重整生成油中的芳烃在组成上有较大差别。首先裂解汽油中所含的苯约占 C6~C8芳烃的 5 0%,比重整产物中的苯高出约5~8%,其次裂解汽油中含有苯乙烯,含量为裂解汽油的3~5 %,此外裂解汽油中不饱和烃的含量远比重整生成油高。 二、裂解汽油加氢精制过程 由于裂解汽油中含有大量的二烯烃、单烯烃。因此裂解汽油的稳定性极差,在受热和光的作用下很易氧化并聚合生成称为胶质的胶粘状物质,在加热条件下,二烯烃更易聚合。这些胶质在生产芳烃的后加工过程中极易结焦和析碳,既影响过程的操作,又影响最终所得芳烃的质量。硫、氮、氧、重金属等化合物对后序生产芳烃工序的催化剂、吸附剂均构成毒物。所以,裂解汽油在芳烃抽提前必须进行预处理,为后加工过程提供合格的原料。目前普遍采用催化加氢精制法。 1.反应原理 裂解汽油与氢气在一定条件下,通过加氢反应器催化剂层时,主要发生两类反应。首先是二烯烃、烯烃不饱和烃加氢生成饱和烃,苯乙烯加氢生成乙苯。其次是含硫、氮、氧有机化合物的加氢分解(又称氢解反应),C—S、C—N、C—O键分别发生断裂,生成气态的H2S、N H3、H2O以及饱和烃。例如:
金属化合物也能发生氢解或被催化剂吸附而除去。加氢精制是一种催化选择加氢,在 2
340℃反应温度以下,芳烃加氢生成环烷烃甚微。但是,条件控制不当,不仅会发生芳烃的加氢造成芳烃损失,还能发生不饱和烃的聚合、烃的加氢裂解以及结焦等副反应。 2.操作条件 (1)反应温度 反应温度是加氢反应的主要控制指标。加氢是放热反应,降低温度对反应有利,但是反应速度太慢,对工业生产是不利的。提高温度,可提高反应速度,缩短平衡时间。但是温度过高,既会使芳烃加氢又易产生裂解与结焦,从而降低催化剂的使用周期。所以,在确保催化剂活性和选择加氢前提下,尽可能把反应温度控制到最低温度为宜。由于一段加氢采用了高活性催化剂,二烯烃的脱除在中等温度下即可顺利进行,所以反应温度一般为60~110℃。二段加氢主要是脱除单烯烃以及氧、硫、氮等杂质,一般反应在320℃下进行最快。当采用钴一钼催化剂时,反应温度一般为320~360℃。 (2)反应压力 加氢反应是体积缩小的反应,提高压力有利于反应的进行。高的氢分压能有效地抑制脱氢和裂解等副反应的发生,从而减少焦炭的生成,延长催化剂的寿命,同时还可加快反应速度,将部分反应热随过剩氢气移出。但是压力过高,不仅会使芳烃加氢,而且对设备要求高、能耗也增大。 (3)氢油比 加氢反应是在氢存在下进行的。提高氢油比,从平衡观点看,反应可进行得更完全,并对抑制烯烃聚合结焦和控制反应温升过快都有一定效果。然而,提高氢油比会增加氢的循环量,能耗大大增加。 (4)空速 空速越小,所需催化剂的装填量越大,物料在反应器内停留时间较长,相应给加氢反应带来不少麻烦,如结焦、析碳、需增大设备等。但空速过大,转化率降低。 3.工艺流程 以生产芳烃原料为目的的裂解汽油加氢工艺普遍采用两段加氢法,其工艺流程如图 4-10所示。 3
第一段加氢目的是将易于聚合的二烯烃转化为单烯烃,包括烯基芳烃转化为芳烃。催化剂多采用贵重金属钯为主要活性组分,并以氧化铝为载体。其特点是加氢活性高、寿命长,在较低反应温度(60℃)下即可进行液相选择加氢,避免了二烯烃在高温条件下的聚合和结焦。 第二段加氢目的是使单烯烃进一步饱和,而氧、硫、氮等杂质被破坏而除去,从而得到高质量的芳烃原料。催化剂普遍采用非贵重金属钴-钼系列,具有加氢和脱硫性能,并以氧化铝为载体。该段加氢是在300℃以上的气相条件下进行的。两个加氢反应器一般都采用固定床反应器。 裂解汽油首先进行预分馏,先进入脱C5塔(1)将其中的C5及C5以下馏分从塔顶分出,然后进入脱C9塔(2)将C9及C9以上馏分从塔釜除去。分离所得的C6~C8中心馏分送入一段加氢反应器(3),同时通入加压氢气进行液相加氢反应。反应条件是温度60~110℃、反应压力2.60MPa,加氢后的双烯烃接近零,其聚合物可抑制在允许限度内。反应放热引起的温升是用反应器底部液体产品冷却循环来控制的。 由一段加氢反应器来的液相产品,经泵加压在预热器内,与二段加氢反应器流出的液相物料换热到控制温度后,送入二段加氢反应器混合喷嘴,在此与热的氢气均匀混合。已气化的进料、补充氢与循环气在二段加氢反应器附设的加热炉(4)内,加热后进入二段反应器(5),在此进行烯烃与硫、氧、氮等杂质的脱除。反应温度为329~358℃,反应压力为2.97MPa。反应器的温度用循环气以及两段不同位置的炉管温度予以控制。 二段加氢反应器的流出物经过一系列换热后,在高压闪蒸罐(8)中分离。该罐分离出的大部分气体同补充氢气一起经循环压缩机回流罐(6)进入循环压缩机(7),返回加热炉,剩余的气体循环回乙烯装置或送至燃料气系统。从高压闪蒸罐分出的液体,换热后进入硫化氢汽提塔(9),含有微量硫化氢的溶解性气体从塔顶除去,返回乙烯装置或送至燃料气系统。汽提塔釜产品则为加氢裂解汽油,可直接送芳烃抽提装置。(见本章第二节 催化重整 (四)芳烃抽提过程)。经芳烃抽提和芳烃精馏后,得到符合要求的芳烃产品。 第三节 对二甲苯的生产 无论是催化重整还是裂解汽油加氢得到的石油芳烃,即苯、甲苯、二甲苯、乙苯等,都在品种与数量上与实际需求不一致。随着苯和对二甲苯需求量日益猛增,尚供不应求。在石
图4-10 两段加氢法的典型流程示意图 1-脱C5塔;2-脱C9塔;3-一段加氢反应器;4-加热炉;5-二段加氢反应器; 6-循环压缩机回流罐;7-循环压缩机;8-高压闪蒸罐;9-HS汽提塔 4 油芳烃中约占40~50%的甲苯、间二甲苯和C9芳烃还未充分利用而供过于求,造成石油芳烃品种及其数量上供需不平衡。因此,开发了一系列芳烃的转化技术,旨在将芳烃的品种与数量进行调整。 图4—11表示以甲苯与C9芳烃为原料,通过歧化和烷基转移生产苯和二甲苯的物料平衡情况。 从图4-11可以看出,通过芳烃歧化和烷基转移工艺可将甲苯和C9芳烃有效地转化为苯和二甲苯,若再配以二甲苯异构化装置,则由100份甲苯和80份C9芳烃可制得36份苯和102份对二甲苯。因此,芳烃的歧化和烷基转移是一种能最大限度生产对二甲苯的方法。 从图4-11还可以看出,芳烃歧化和烷基转移、混合二甲苯异构化、吸附分离等过程必须联合生产,才能最大限度地生产苯、对二甲苯等紧缺品种。
100甲苯C9芳烃歧化和烷基转移
歧化和烷基转移异构化
对二甲苯乙苯
14080
6012040
苯16
20苯
混合二甲苯
20100吸附分离
1884
102烷基化其它各过程
芳 烃 系 产 品 一、歧化或烷基转移生产苯与二甲苯 1.反应原理 甲苯歧化和甲苯与C9芳烃的烷基转移工艺是增产苯与二甲苯的有效手段。芳烃的歧化反应一般是指两个相同芳烃分子在催化剂作用下, 一个芳烃分子的侧链烷基转移到另一个
图 4—11 甲苯、C9芳烃生产苯和对二甲苯的 物料平衡以及其它结构调整的关系 5
CH3 ——CH3
CH3
CH3
芳烃分子上去的过程。而烷基转移反应是指两个不同芳烃分子间发生烷基转移的过程。 主反应: (1)歧化
(2)烷基转移
副反应: (1)在临氢条件下发生加氢脱烷基反应,生成甲烷、乙烷、丙烷、苯、甲苯、乙苯等; (2)歧化反应,由二甲苯生成甲苯、三甲苯等,即主反应中烷基转移的逆过程; (3)烷基转移,如苯和三甲苯生成甲苯和四甲苯等; (4)芳烃加氢、烃类裂解、苯烃缩聚等。 2、操作条件 (1)原料中三甲苯的浓度 投入原料C9混合芳烃馏分中只有三甲苯是生成二甲苯的有效成分,所以原料C9芳烃馏分中三甲苯的浓度高低,将直接影响反应的结果。当原料中三甲苯浓度50%左右时,生成物中C8芳烃的浓度为最大。为此应采用三甲苯浓度高的C9芳烃作原料。 (2)反应温度 歧化和烷基转移反应都是可逆反应。由于热效应较小,温度对化学平衡影响不大,而催化剂的活性一般随反应温度的提高而升高。温度升高,反应速度加快,转化率升高,但苯环裂解等副反应增加,目的产物收率降低。温度低,虽然副反应少、原料损失少,但转化率低,造成循环量大、运转费用高。在生产中主要选择能确保转化率的温度,当
CH3 ——(CH3)2
CH3 ——CH3
CH3 ——(CH3)3
CH3 ——(CH3)2
CH3
——CH3