不同红土镍矿的处理工艺简述
红土镍矿火法RKEF及湿法HPAL工艺对比

中间品为M S P ( 混合硫化镍钴)或M H P ( 氢氧化镍钴)。M S P 进一步精炼可得到纯镍,不锈钢厂的冶炼项目倾向于生产M S P ; 而MHP制电池用硫酸镍更容易,前驱体厂布局镍冶炼集中于生产MHP。
• 工艺难度:对设备、操作上的要求较高,需要控制合适的反应温度、压强、 酸度等。生产中对生产指标的控制不当不仅会拉低镍回收率,酸度过低会导 致高压釜和管道发生结垢堵塞,酸度过高会发生管道腐蚀,这也是过去相关 湿法冶炼项目达产周期长的原因之一。
除杂后使用的工艺不同,会产出不同的产物,主要有氢氧化物沉淀(MHP) 及硫化物沉淀(MSP),碳酸盐沉淀应用较少。中合反应后进行的不同工 艺可产出不同的中间产物。1)加H₂S制得高镍硫MSP,可以进一步还原为 精炼镍/钴,在过去动力电池市场未上量时,需求高于MHP,因而过去投建 的湿法冶炼项目产物主要为M S P ;2)加碱制得氢氧化镍钴M H P ,后续制 硫酸镍的生产成本更低,适用于三元前驱体的生产,因而近年新投的湿法冶 炼项目集中于此路线。
图:高压酸浸工艺流程图
红土镍矿
蒸汽、硫酸
矿浆处理
预热
加压酸浸
矿浆闪蒸和 矿浆中和
尾渣 CCD洗涤
中和除杂、 镍钴沉淀
硫 化 物 沉 淀
氢 氧 化 物 沉 淀
碳 酸 盐 沉 淀
深海填埋/ 尾矿坝
不同工艺可得到三 种不同的镍中间品 沉淀物
3
火法RKEF工艺:回转窑还原镍铁氧化物,矿热炉熔融精炼
红土镍矿火法冶炼工艺现状
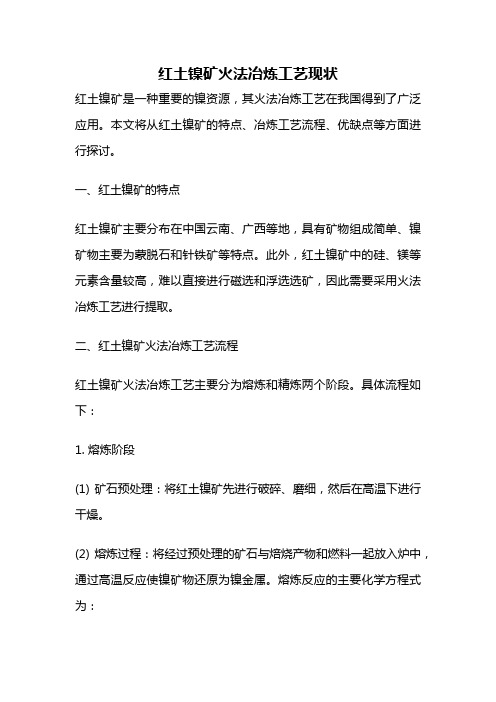
红土镍矿火法冶炼工艺现状红土镍矿是一种重要的镍资源,其火法冶炼工艺在我国得到了广泛应用。
本文将从红土镍矿的特点、冶炼工艺流程、优缺点等方面进行探讨。
一、红土镍矿的特点红土镍矿主要分布在中国云南、广西等地,具有矿物组成简单、镍矿物主要为蒙脱石和针铁矿等特点。
此外,红土镍矿中的硅、镁等元素含量较高,难以直接进行磁选和浮选选矿,因此需要采用火法冶炼工艺进行提取。
二、红土镍矿火法冶炼工艺流程红土镍矿火法冶炼工艺主要分为熔炼和精炼两个阶段。
具体流程如下:1. 熔炼阶段(1) 矿石预处理:将红土镍矿先进行破碎、磨细,然后在高温下进行干燥。
(2) 熔炼过程:将经过预处理的矿石与焙烧产物和燃料一起放入炉中,通过高温反应使镍矿物还原为镍金属。
熔炼反应的主要化学方程式为:NiO+CO=Ni+CO2(3) 炉渣处理:熔炼产生的炉渣中含有一定量的铁、硅、镁等杂质,需要通过浸出、氧化等方法进行处理。
2. 精炼阶段(1) 精炼过程:将熔炼后的镍合金放入铸造坩埚中,加入一定量的铝、铜等金属,通过化学反应使杂质逐渐被还原掉,从而提高镍的纯度。
(2) 精炼产品加工:将精炼后的镍合金进行锻造、轧制等加工工艺,制成各种形状的金属制品。
三、红土镍矿火法冶炼工艺的优缺点红土镍矿火法冶炼工艺具有以下优点:1. 可以处理含硅、镁等难选元素较高的红土镍矿。
2. 熔炼反应速度快,冶炼周期短,生产效率高。
3. 通过添加金属等元素,可以进行精炼,提高镍的纯度。
但是,红土镍矿火法冶炼工艺也存在一些缺点:1. 需要大量的燃料,炉温高,能耗较大。
2. 熔炼过程中产生大量的炉渣,处理难度较大。
3. 精炼过程中需要添加大量的金属,成本较高。
四、结语红土镍矿火法冶炼工艺是一种比较成熟的提取红土镍矿中镍的方法。
随着科技的不断发展,人们对其进行了不断的改进和优化,使其在生产实践中得到了广泛应用。
未来,随着资源的日益稀缺和环境保护意识的不断增强,红土镍矿火法冶炼工艺将会得到更为广泛的应用和发展。
红土镍矿湿法冶炼工艺
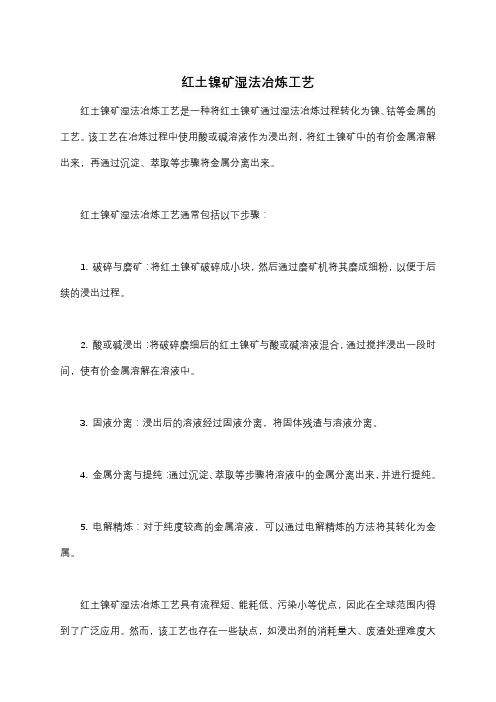
红土镍矿湿法冶炼工艺
红土镍矿湿法冶炼工艺是一种将红土镍矿通过湿法冶炼过程转化为镍、钴等金属的工艺。
该工艺在冶炼过程中使用酸或碱溶液作为浸出剂,将红土镍矿中的有价金属溶解出来,再通过沉淀、萃取等步骤将金属分离出来。
红土镍矿湿法冶炼工艺通常包括以下步骤:
1. 破碎与磨矿:将红土镍矿破碎成小块,然后通过磨矿机将其磨成细粉,以便于后续的浸出过程。
2. 酸或碱浸出:将破碎磨细后的红土镍矿与酸或碱溶液混合,通过搅拌浸出一段时间,使有价金属溶解在溶液中。
3. 固液分离:浸出后的溶液经过固液分离,将固体残渣与溶液分离。
4. 金属分离与提纯:通过沉淀、萃取等步骤将溶液中的金属分离出来,并进行提纯。
5. 电解精炼:对于纯度较高的金属溶液,可以通过电解精炼的方法将其转化为金属。
红土镍矿湿法冶炼工艺具有流程短、能耗低、污染小等优点,因此在全球范围内得到了广泛应用。
然而,该工艺也存在一些缺点,如浸出剂的消耗量大、废渣处理难度大
等。
为了提高红土镍矿湿法冶炼工艺的经济效益和环保性能,需要不断改进和优化工艺流程,如开发高效低耗的破碎磨矿设备、优化浸出剂配方、提高金属回收率等。
同时,也需要加强废渣处理和资源综合利用的研究,以实现红土镍矿湿法冶炼工艺的可持续发展。
红土镍矿处理工艺综述
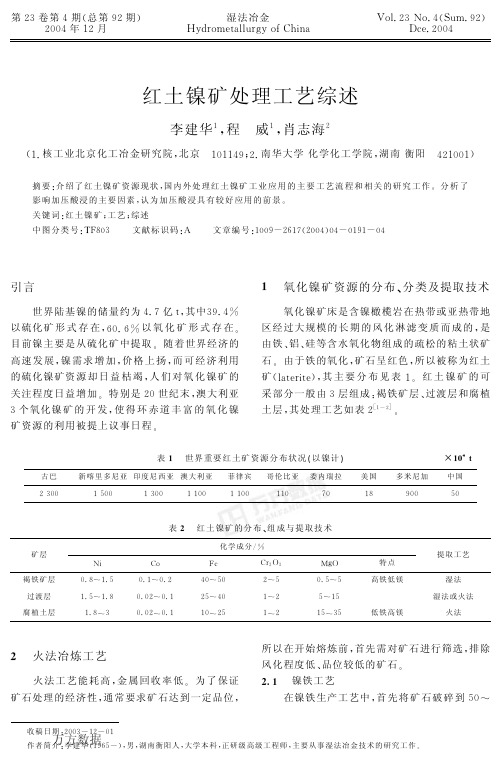
第!"卷第#期!总第$!期"!%%#年&!月湿法冶金C 8DEFG :H 9I IJ EK 8F L’A M 19N F I O !"<F O #!2J GO $!"+P :O !%%#红土镍矿处理工艺综述李建华&!程威&!肖志海!!&O 核工业北京化工冶金研究院#北京!&%&&#$$!O 南华大学化学化工学院#湖南衡阳!#!&%%&"摘要!介绍了红土镍矿资源现状#国内外处理红土镍矿工业应用的主要工艺流程和相关的研究工作%分析了影响加压酸浸的主要因素#认为加压酸浸具有较好应用的前景%关键词!红土镍矿$工艺$综述中图分类号!6>.%"!!文献标识码!(!!文章编号!&%%$=!,&-!!%%#"%#=%&$&=%#收稿日期!!%%"=&!=%&作者简介!李建华!&$,/="#男#湖南衡阳人#大学本科#正研级高级工程师#主要从事湿法冶金技术的研究工作%引言世界陆基镍的储量约为#O -亿H #其中"$O #U 以硫化矿形式存在#,%O ,U 以氧化矿形式存在%目前镍主要是从硫化矿中提取%随着世界经济的高速发展#镍需求增加#价格上扬#而可经济利用的硫化镍矿资源却日益枯竭#人们对氧化镍矿的关注程度日益增加%特别是!%世纪末#澳大利亚"个氧化镍矿的开发#使得环赤道丰富的氧化镍矿资源的利用被提上议事日程%!氧化镍矿资源的分布"分类及提取技术氧化镍矿床是含镍橄榄岩在热带或亚热带地区经过大规模的长期的风化淋滤变质而成的#是由铁&铝&硅等含水氧化物组成的疏松的粘土状矿石%由于铁的氧化#矿石呈红色#所以被称为红土矿!I 9H :E M H :"#其主要分布见表&%红土镍矿的可采部分一般由"层组成’褐铁矿层&过渡层和腐植土层#其处理工艺如表!(&=!)%表!世界重要红土矿资源分布状况#以镍计$T !%"0!!古巴新喀里多尼亚印度尼西亚澳大利亚菲律宾哥伦比亚委内瑞拉美国多米尼加中国!"%%&/%%&"%%&&%%&&%%&&%-%&.$%%/%表#红土镍矿的分布"组成与提取技术矿层化学成分*U <M’F >:’E !7"5K 7特点提取工艺褐铁矿层%O ."&O /%O &"%O !#%"/%!"/%O /"/高铁低镁湿法过渡层&O /"&O .%O %!"%O &!/"#%&"!/"&/湿法或火法腐植土层&O .""%O %!"%O &&%"!/&"!&/""/低铁高镁火法#火法冶炼工艺!!火法工艺能耗高#金属回收率低%为了保证矿石处理的经济性#通常要求矿石达到一定品位#所以在开始熔炼前#首先需对矿石进行筛选#排除风化程度低&品位较低的矿石%#E !镍铁工艺在镍铁生产工艺中#首先将矿石破碎到/%"万方数据!!!!!!!!!!!!!!!!!!!!湿法冶金!!!!!!!!!!!!!!!%%#年&!月&/%G G !然后送干燥窑干燥到矿石既不黏结又不太粉化!再送煅烧回转窑!在-%%f 温度下!干燥"预热和煅烧!产出焙砂#在焙砂加入电炉后!再加入&%""%G G 的挥发性煤!经过&%%%f 的还原熔炼!产出粗镍铁合金#粗镍铁合金再经过吹炼产出成品镍铁合金$其生产工艺流程如图&所示$图&!镍铁合金工艺流程采用该法生产镍铁合金的工厂主要有法国镍公司的新喀里多尼亚多尼安博冶炼厂"哥伦比亚塞罗马托莎厂"日本住友公司的八户冶炼厂$产出的产品中镍质量分数为!%U ""%U !镍回收率为$%U "$/U !钴不能回收$#E #镍硫工艺镍硫生产工艺是在生产镍铁工艺的&/%%"&,%%f 熔炼过程中!加入硫磺!产出低镍硫!再通过转炉吹炼生产高镍硫!其原则工艺流程如图!所示$生产高镍硫的主要工厂有法国镍公司的新喀里多尼亚多尼安博冶炼厂"印度尼西亚的苏拉威西%梭罗阿科冶炼厂$高镍硫产品一般镍质量分数为-$U !硫质量分数为&$O /U $全流程镍回收率约-%U &"=#’$图!!红土矿生产镍硫的原则工艺流程&湿法冶炼工艺&E !氨浸工艺氨浸工艺最早在古巴尼加罗冶炼厂得到应用!其原则工艺流程如图"所示$图"红土矿的氨浸工艺流程%!$&%万方数据第!"卷第#期!!!!!!!!!李建华!等"红土镍矿处理工艺综述!!!!!将红土矿干燥#磨碎!在,%%"-%%f温度下还原焙烧!使镍#钴和部分铁还原成合金!然后再#级逆流氨浸!利用镍和钴可与氨形成配和物的特性!使镍#钴等有价金属进入浸出液$浸出液经硫化沉淀!沉淀母液再除铁#蒸氨!产出碱式硫酸镍!碱式硫酸镍再经煅烧转化成氧化镍!也可以经还原生产镍粉$到目前为止!世界上采用该工艺处理红土矿的仅有澳大利亚R<3公司的雅布鲁精炼厂和古巴的尼加罗冶炼厂$一般生产的镍块中镍质量分数达$%U!全流程镍的回收率达到-/U".%U$与火法冶炼流程相比!钴可以部分回收!回收率约#%U"/%U%/&$&E#加压酸浸工艺&E#E!工艺流程在!/%"!-%f!#"/549的高温高压条件下!用稀硫酸将镍#钴等有价金属与铁#铝矿物一起溶解!在随后的反应中!控制一定的T C值等条件!使铁#铝和硅等杂质元素水解进入渣中!镍#钴选择性进入溶液$浸出液用硫化氢还原中和#沉淀!产出高质量的镍钴硫化物$镍钴硫化物通过传统的精炼工艺配套产出最终产品$其原则工艺流程如图#所示$图#加压酸浸原则工艺流程最早的加压酸浸冶炼厂是古巴的毛阿冶炼厂!其设计年处理矿石!%%万H!产品为镍钴硫化物!镍钴产量分别为!O!-万H和!%%%H!镍#钴回收率分别达到$%U"$/U和.%U"$%U!高于氨浸流程和火法流程$加压酸浸的金属回收率高’见表"(!所以近年来投产的和即将投产的工程均采用加压酸浸工艺%,&$表&不同提取工艺的金属回收率提取工艺回收率)U<M’F镍铁工艺$%"$/=镍硫工艺-%=氨浸工艺-/".%#%"/%加压酸浸$%"$/.%"$%&E#E#加压酸浸工艺的主要影响因素9O矿石品位$矿石品位直接影响加压酸浸工艺的经济性和后续溶液处理的难度$只有镍达到一定的品位!才能保证一定的经济指标$对于部分矿石!可以通过湿筛分离!提高矿石中镍与钴的品位$c O镁与铝的含量$镁与铝是主要的耗酸元素!在镍#钴品位一定的情况下!矿石中镁#铝的含量直接影响矿石的硫酸消耗量!从而影响工艺的技术经济指标$P O矿物学特征$不同的矿物组成!对加压酸浸工艺金属的回收率影响很大$加压酸浸工艺适合处理以针铁矿为主的矿石!不太适合处理泥质较多的矿石$D O结垢程度$加压酸浸过程中!溶液中含有大量的铝#铁和硅!随着反应的进行!铝#铁和硅都会沉降!粘附在高压釜胆和管道内壁!从而减少高压釜的有效容积!堵塞管道$在古巴的毛阿厂!高压釜的结垢速率为"%%G G)9!平均每月需要/D 时间除垢$在西澳的连续试验过程中!采用高盐度水!在温度!/%"!,/f条件下!其结垢速率大约为&/%G G)9$因此!减少结垢速率是提高高压釜处理能力的重要手段$!!:O工业用水$在加压浸出过程中!高盐度水的使用有可能有利于有价金属的浸出$但是高盐度水在浸出过程中产出酸!从而导致设备#管道及阀门的腐蚀$"有关红土矿处理工艺的其它研究工作!!还原焙烧*酸浸或亚硫酸浸出工艺$此工艺可在常压下进行!并尽可能少地溶解铁$试验证*"$&*万方数据!!!!!!!!!!!!!!!!!!!!湿法冶金!!!!!!!!!!!!!!!%%#年&!月明!在-&%"-"%f 温度下还原焙烧的矿石!用&UC !27#浸出!<M 浸出率为.%U "./U !>:浸出率为&%U "如用/U C !27#浸出!<M 浸出率可达$/U !>:浸出率为&/U "!%U "矿石还原焙烧后!用亚硫酸或吹入27!的水浸出!也可取得较好的效果"硫化焙烧"将矿石加入硫化剂!于-%%f 下硫化焙烧!>:!#27#$"分解!铁不生成硫酸盐!而镍生成硫酸盐!可用水浸出!镍转入溶液"水热法"在矿石中加入适量的硫磺!制备成含硫矿浆"含硫矿浆先在硫化反应器中硫化#!"%"!#%f !!O -""O #549!蒸汽加热"A $!然后在氧化反应器中氧化#!%%f !!O .549!空气氧化$!A !镍溶于矿浆中!可用铁粉置换镍"此外!日本采用离析’选矿法处理红土矿*硅酸镍矿"红土矿还原后!用’7羰化!镍的提取率达.%U !铁的浸出率仅为&U %-&"(结束语!!随着世界镍需求量的增长以及镍资源的短缺!红土型镍矿资源的开发将成为未来几年世界镍工业发展的主要趋势"其中!从环保’金属回收率及镍矿资源状况等几方面考虑!加压酸浸工艺在工业上都会具有较好的应用前景"参考文献!%&&V J P A 9191+O <M P h :I %(&O 31((’F J 11M D M H 8b:‘M :a %’&O S F 1*D F 1(31Y H M H J H :F L5M 1M 1K 91D 5:H 9I I J E K 8!&$.!O %!&b F F E D 9C)!C :E G 91Y )5(O \1:E K 8’F 1Y H E 9M 1Y M 1H A :\;*L E 9P H M F 1F L<M P h :I L E FG 7;M D :Y7E :Y %)&O \E @G :H 9I !&$.&!"##"$(..!=..-O%"&伍鸿九!王立川O 有色金属提取手册#铜镍卷$%5&O北京(冶金工业出版社!!%%%O /&!=/&#O%#&黄其兴!王立川!朱鼎之!等O 镍冶金学%5&O北京(科学技术出版社O &$$%O !!#=!!/%/&陈家镛!杨守志!柯家骏!等O 湿法冶金的研究与发展%5&O北京(冶金工业出版社!&$$.O !-=/#O%,&兰兴华O 镍的高压湿法冶金%)&O 世界有色金属!!%%!!#&$(/=!-O%-&刘大星O 从镍红土矿中回收镍’钴的技术的展%)&O有色金属!!%%!!#"$(,=&%O7.81.@,634,4.//Q .2L 6,H 51./,9J ;0.410.F 612U .HO 4.S 3)M 91*A J 9&!’C \<]Z :M &!_3(70A M *A 9M!#&>0($1$",2(3(*%456"3)$)7)(&8-5(’$4*+!",$"((%$",*"9:()*++7%,/!-;;-!0($1$",&%&&#$!-5$"*)!>@45&&+&8-5(’$3)%/*"9-5(’$4*+!",$"((%$",!;*"57*?"$#(%3$)/!F (",/*",!F 7k *"!#!&%%&!-5$"*$A B /04;20(4E :Y :1HY H 9H J YF L I 9H :E M H :*1M P h :IE :Y F J E P :Y9E :M 1H E F D J P :D O6A :G 9M 1H :P A 1M P Y91DE :I 9H :D Y H J D M :Y 9E :D :Y P E M c :D O 6A :G 9M 1L E 9P H F E Y F La F E h M 1K F 19P M D M P I :9P A M 1K J 1D :E T E :Y Y J E :9E :919I 8@:D O 3H M Yc :I M :‘:D H A 9H 9P M D M P I :9P A M 1K J 1D :E T E :Y Y J E :T E F P :Y Y M YG F Y H I 89T T I M P 9H M F 1T E F Y T:P H M ‘:O C .D @,4</(I 9H :E M H :*1M P h :I E :Y F J E P :)T E F P :Y Y ),,,,,,,,,,,,,,,,,,,,,,,,,,,,,,,,,,,,,,,,,,,,,,,E :‘M :a 硫化银沉淀物的硝酸浸出4O ’O C F I I F a 98等研究了用硝酸浸出硫化银沉淀物!在&/%f "&&%%h 49"$O ,U 固体质量分数及硝酸用量为理论量的!倍条件下#获得了$,O &U 的最大浸出率!在最佳浸出条件下#银浸出率还可进一步提高!此工艺可用于从沉淀于感光溶液的硫化银中回收银!对硝酸浸出液#在&/%f 和氢气压力#%%%h 49条件下#银近乎完全沉淀$$$O .U %!在银浓度超过硫化银在室温下的溶解度极限时#氢气的还原效率也较高!所得高纯银的粒度为&%,’G 占$,O !U !&张丽霞译自’C 8D E F G :H 9I I J E K 8(!%%##-#$"=#%)!&"=!!%**#$&*万方数据。
国外红土镍矿冶炼处理工艺

常见的红土镍矿冶炼处理工艺主要有湿法工艺和火法工艺。
湿法工艺是使用硫酸、盐酸或者氨水溶液作为浸出剂,浸出红土镍矿中的镍和钴金属离子。
常见的湿法处理工艺有高压酸浸工艺(HPAL)、常压酸浸工艺(PAL)和氨浸工艺(Caron)。
硅镁质型红土镍矿中镁含量高,浸出过程酸耗大,目前较多采用火法工艺处理。
常用的红土镍矿火法处理工艺有:电炉溶炼、高炉镍铁工艺、硫化熔炼等。
目前国外大部分采用湿法工艺冶炼红土镍矿。
美国:新型还原焙烧-氨浸法回收率提高还原焙烧-氨浸工艺又称为Caron流程,属于湿法冶炼工艺。
其主要流程为:矿石经破碎、筛分后在多膛炉或回转窑中进行选择性还原焙烧,还原焙砂用氨-碳酸铵溶液进行逆流浸出,经浓密机处理后得到的浸出液经净化、蒸氨后产出碳酸镍浆料,再经回转窑干燥和煅烧后,得到氧化镍产品,并用磁选法从浸出渣中选出铁精矿。
焙烧过程采用的还原剂主要是煤或还原性气体,其主要目的是将矿石中的镍和钴还原,而三价铁大部分被还原为磁性的Fe3O4,少数被还原成金属铁。
氨浸的主要目的是将焙砂中的镍和钴以络氨离子的形式进入溶液,而铁、镁等主要杂质仍以单质或氧化物的形式留在浸出渣中,从而实现镍、钴与铁等杂质的初步分离。
该工艺的优点是常压操作,浸出液杂质含量较少,浸出剂中的氨可回收;主要缺点是镍、钴回收率较低,镍的回收率为75%~80%,钴的回收率低于50%。
截止到目前,全球只有少数几家工厂采用该法处理红土镍矿。
为提高镍、钴回收率,美国矿物局最近发展了还原焙烧-氨浸法处理红土矿回收镍的新流程,简称USBM法。
该法的要点在于还原焙烧前加入了黄铁矿(FeS2)进行制粒,还原时用的是纯CO。
浸出液用LIX64-N作为萃取剂实现钴、镍分离,整个系统为闭路循环,有效地利用了资源。
据报道,用该法处理含镍1%、钴0.2%的红土矿时,镍、钴的回收率分别为90%和85%。
若处理含镍0.53%、钴0.06%的低品位红土矿时,钴的回收率亦能达到76%。
红土镍矿湿法冶金 工艺流程
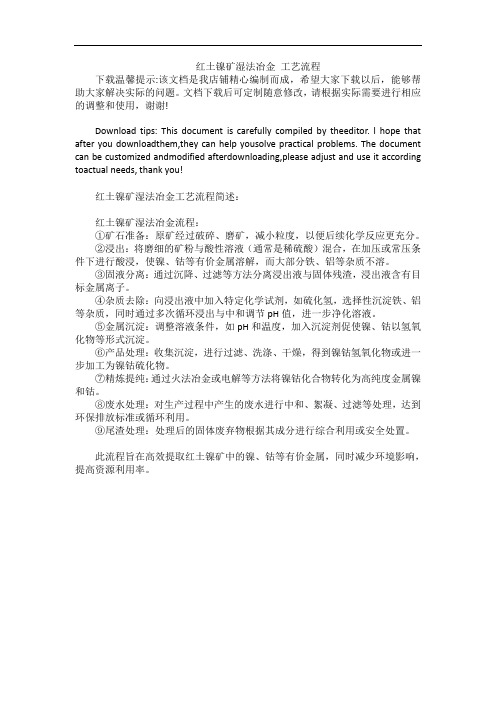
红土镍矿湿法冶金工艺流程下载温馨提示:该文档是我店铺精心编制而成,希望大家下载以后,能够帮助大家解决实际的问题。
文档下载后可定制随意修改,请根据实际需要进行相应的调整和使用,谢谢!Download tips: This document is carefully compiled by theeditor. l hope that after you downloadthem,they can help yousolve practical problems. The document can be customized andmodified afterdownloading,please adjust and use it according toactual needs, thank you!红土镍矿湿法冶金工艺流程简述:红土镍矿湿法冶金流程:①矿石准备:原矿经过破碎、磨矿,减小粒度,以便后续化学反应更充分。
②浸出:将磨细的矿粉与酸性溶液(通常是稀硫酸)混合,在加压或常压条件下进行酸浸,使镍、钴等有价金属溶解,而大部分铁、铝等杂质不溶。
③固液分离:通过沉降、过滤等方法分离浸出液与固体残渣,浸出液含有目标金属离子。
④杂质去除:向浸出液中加入特定化学试剂,如硫化氢,选择性沉淀铁、铝等杂质,同时通过多次循环浸出与中和调节pH值,进一步净化溶液。
⑤金属沉淀:调整溶液条件,如pH和温度,加入沉淀剂促使镍、钴以氢氧化物等形式沉淀。
⑥产品处理:收集沉淀,进行过滤、洗涤、干燥,得到镍钴氢氧化物或进一步加工为镍钴硫化物。
⑦精炼提纯:通过火法冶金或电解等方法将镍钴化合物转化为高纯度金属镍和钴。
⑧废水处理:对生产过程中产生的废水进行中和、絮凝、过滤等处理,达到环保排放标准或循环利用。
⑨尾渣处理:处理后的固体废弃物根据其成分进行综合利用或安全处置。
此流程旨在高效提取红土镍矿中的镍、钴等有价金属,同时减少环境影响,提高资源利用率。
红土镍矿处理方法综述
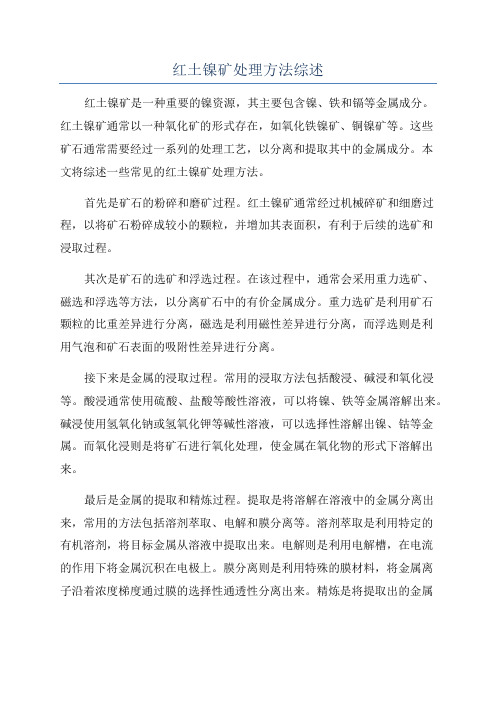
红土镍矿处理方法综述红土镍矿是一种重要的镍资源,其主要包含镍、铁和镉等金属成分。
红土镍矿通常以一种氧化矿的形式存在,如氧化铁镍矿、铜镍矿等。
这些矿石通常需要经过一系列的处理工艺,以分离和提取其中的金属成分。
本文将综述一些常见的红土镍矿处理方法。
首先是矿石的粉碎和磨矿过程。
红土镍矿通常经过机械碎矿和细磨过程,以将矿石粉碎成较小的颗粒,并增加其表面积,有利于后续的选矿和浸取过程。
其次是矿石的选矿和浮选过程。
在该过程中,通常会采用重力选矿、磁选和浮选等方法,以分离矿石中的有价金属成分。
重力选矿是利用矿石颗粒的比重差异进行分离,磁选是利用磁性差异进行分离,而浮选则是利用气泡和矿石表面的吸附性差异进行分离。
接下来是金属的浸取过程。
常用的浸取方法包括酸浸、碱浸和氧化浸等。
酸浸通常使用硫酸、盐酸等酸性溶液,可以将镍、铁等金属溶解出来。
碱浸使用氢氧化钠或氢氧化钾等碱性溶液,可以选择性溶解出镍、钴等金属。
而氧化浸则是将矿石进行氧化处理,使金属在氧化物的形式下溶解出来。
最后是金属的提取和精炼过程。
提取是将溶解在溶液中的金属分离出来,常用的方法包括溶剂萃取、电解和膜分离等。
溶剂萃取是利用特定的有机溶剂,将目标金属从溶液中提取出来。
电解则是利用电解槽,在电流的作用下将金属沉积在电极上。
膜分离则是利用特殊的膜材料,将金属离子沿着浓度梯度通过膜的选择性通透性分离出来。
精炼是将提取出的金属进行纯化和精细化处理。
常用的精炼方法包括化学精炼、电解精炼和熔炼等。
总而言之,红土镍矿的处理方法涉及到矿石的粉碎、选矿、浸取、提取和精炼等多个步骤。
不同的方法适用于不同的矿石成分和金属含量。
综合应用这些方法,可以高效地提取和精炼红土镍矿中的有价金属。
红土镍矿湿法冶金工艺综述及进展
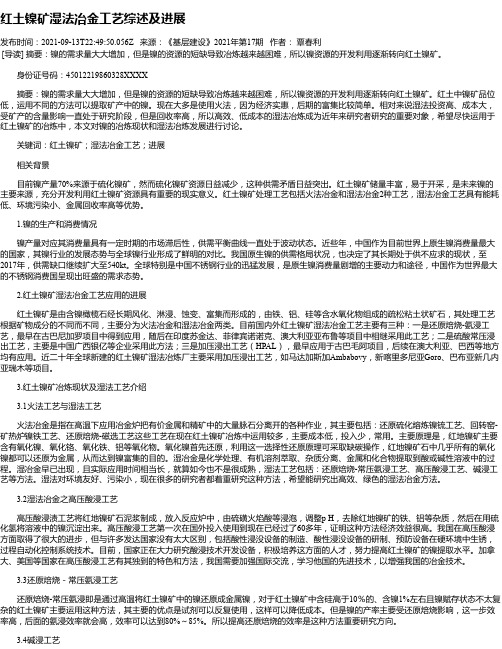
红土镍矿湿法冶金工艺综述及进展发布时间:2021-09-13T22:49:50.056Z 来源:《基层建设》2021年第17期作者:覃春利[导读] 摘要:镍的需求量大大增加,但是镍的资源的短缺导致冶炼越来越困难,所以镍资源的开发利用逐渐转向红土镍矿。
身份证号码:45012219860328XXXX摘要:镍的需求量大大增加,但是镍的资源的短缺导致冶炼越来越困难,所以镍资源的开发利用逐渐转向红土镍矿。
红土中镍矿品位低,运用不同的方法可以提取矿产中的镍。
现在大多是使用火法,因为经济实惠,后期的富集比较简单。
相对来说湿法投资高、成本大,受矿产的含量影响一直处于研究阶段,但是回收率高,所以高效、低成本的湿法冶炼成为近年来研究者研究的重要对象,希望尽快运用于红土镍矿的冶炼中,本文对镍的冶炼现状和湿法冶炼发展进行讨论。
关键词:红土镍矿;湿法冶金工艺;进展相关背景目前镍产量70%来源于硫化镍矿,然而硫化镍矿资源日益减少,这种供需矛盾日益突出。
红土镍矿储量丰富,易于开采,是未来镍的主要来源,充分开发利用红土镍矿资源具有重要的现实意义。
红土镍矿处理工艺包括火法冶金和湿法冶金2种工艺,湿法冶金工艺具有能耗低、环境污染小、金属回收率高等优势。
1.镍的生产和消费情况镍产量对应其消费量具有一定时期的市场滞后性,供需平衡曲线一直处于波动状态。
近些年,中国作为目前世界上原生镍消费量最大的国家,其镍行业的发展态势与全球镍行业形成了鲜明的对比。
我国原生镍的供需格局状况,也决定了其长期处于供不应求的现状,至2017年,供需缺口继续扩大至540kt。
全球特别是中国不锈钢行业的迅猛发展,是原生镍消费量剧增的主要动力和途径,中国作为世界最大的不锈钢消费国呈现出旺盛的需求态势。
2.红土镍矿湿法冶金工艺应用的进展红土镍矿是由含镍橄榄石经长期风化、淋浸、蚀变、富集而形成的,由铁、铝、硅等含水氧化物组成的疏松粘土状矿石,其处理工艺根据矿物成分的不同而不同,主要分为火法冶金和湿法冶金两类。
- 1、下载文档前请自行甄别文档内容的完整性,平台不提供额外的编辑、内容补充、找答案等附加服务。
- 2、"仅部分预览"的文档,不可在线预览部分如存在完整性等问题,可反馈申请退款(可完整预览的文档不适用该条件!)。
- 3、如文档侵犯您的权益,请联系客服反馈,我们会尽快为您处理(人工客服工作时间:9:00-18:30)。
不同红土镍矿的处理工艺简述氧化镍矿是含镍橄榄石经长期风化淋滤变质而形成的矿物,由于矿床风化后铁的氧化,矿石呈红色,因而通称为红土矿(Laterite)。
根据矿石中铁和镁含量的不同,含镍红土矿可以简单地分为褐铁矿类型和残积矿类型。
一般残积矿类型氧化镍矿含镁较高,而褐铁矿类型镍红土矿含铁较高而含镁较低。
一、现有红土镍矿处理技术概况在红土镍矿的处理方面,比较成熟的冶炼方法包括:①回转窑干燥预还原-电炉熔炼法(RKEF)、②烧结-鼓风炉硫化熔炼法、③烧结-高炉还原熔炼法、④回转窑(或隧道窑、或转底炉)半熔融还原焙烧-磁选法、⑤还原焙烧(回转窑或沸腾炉)-氨浸法、⑥高压酸浸法、⑦常压酸浸法以及⑧硫酸堆浸法等。
上述处理方法均有各自的适应性,需要根据矿石镍、钴、铁含量和矿石类型的差异,以及当地燃料、水、电和化学试剂的供应状况等的不同,选用适宜的冶炼工艺。
从总体上说,红土镍矿的处理主要分为火法冶金和湿法冶金二大类。
1.1 火法冶金火法冶金主要处理含镍 1.5~3%、Fe10~40%、MgO5~35%、Cr2O31~2%的含镍品位较高的变质橄榄岩。
冶炼工艺主要包括回转窑干燥预还原-电炉熔炼法(RKEF)和鼓风炉硫化熔炼及烧结-高炉还原熔炼法,产品主要为镍铁合金和镍锍产品,镍铁合金主要供生产不锈钢,镍锍则须经转炉进一步吹炼生产高冰镍产品。
日本大江山冶炼厂则采用回转窑高温半熔融还原焙烧(~1350℃)产出粒铁,经破碎、跳汰富集产出含镍大于20%的镍铁合金供生产不锈钢,并被公认为是目前最为经济的处理镍红土矿的方法。
回转窑干燥预还原-还原熔炼工艺生产镍铁,镍的回收率可以达到90%以上,但生产镍铁时由于进入镍铁中的钴不计价,因此对钴含量较高的氧化镍矿并不适用。
由于红土镍矿含水高,加之投资大,从经济角度考虑,电炉还原熔炼工艺适宜于处理镍含量大于 1.8%、钴含量小于0.05%的矿石,且要求当地要有充沛的电力供应。
鼓风炉硫化熔炼也是经典工艺,红土镍矿在配入适量的CaO和SiO2后,在约1100℃下烧结成块,再配入20%左右的黄铁矿和约15~25%的焦炭,在鼓风炉内约1350℃的温度下熔炼,产出含镍8~15%的低冰镍产品。
根据矿石中镍含量的高低,镍回收率通常可以达到90%以上,并可以回收80%以上的钴。
因此,对于含钴较高(如>0.2%)的镁质红土镍矿,选用鼓风炉硫化熔炼是较为适宜的方法。
由于鼓风炉必须使用昂贵的冶金焦,在目前冶金焦价格较高的状况下,鼓风炉硫化熔炼的经济效果较差。
近年来,随着国家产业政策的调整,大量500m3以下的炼铁高炉被淘汰。
但由于国内不锈钢用镍紧张,镍价高涨,许多小高炉被用来处理含铁40%左右、含镍大于1%的红土镍矿,生产含镍大于2%的含镍生铁或不锈钢基料。
但由于红土镍矿铁品位低、氧化铝含量较高,高炉体积利用率低、焦炭消耗量大、烧结污染严重、镍生铁所含铁不计价等,和鼓风炉硫化熔炼类似,烧结-高炉还原熔炼法的的经济效果也比较差。
1.2 湿法冶金世界范围内大规模工业应用的氧化镍矿湿法冶金生产工艺主要有三种:还原焙烧-氨浸法、加压酸浸法、常压酸浸法和堆浸法。
1.2.1 还原焙烧-氨浸法对于含镍1%左右且镍赋存状态不太复杂的红土镍矿,通常采用还原焙烧-氨浸工艺处理,其主要优点是试剂可循环使用,消耗量小,能综合回收镍和钴,缺点是浸出率偏低,镍、钴金属回收率分别为75%~85%和40%~60%。
采用氨浸法的生产厂有古巴的尼卡罗冶炼厂、印度苏金达厂、阿尔巴尼亚的爱尔巴桑钢铁联合企业、斯洛伐克的谢列德冶炼厂、澳大利亚雅布鲁精炼厂及加拿大INCO的铜崖铁矿回收厂等。
国内,由北京矿冶研究总院设计的青海元石山镍铁矿也采用了还原焙烧-氨浸工艺,建成了年处理30万吨镍铁矿的冶炼厂,并于2009年建成投产,处理平均含镍0.7%、铁28%的铁质/硅质/镁质复杂混合矿,取得了渣含镍<0.25%(国外同类冶炼厂的渣含镍~0.35%),镍、铁回收率大于70%和60%,铁精矿含铁大于58%,氨耗15kg/t-矿、煤耗130kg/t-矿的生产指标。
由于矿石费用只有50元/t,因此每生产1吨精制硫酸镍的税后成本接近2.3万元,使呆滞了40多年的元石山镍矿得以经济开发。
2011年10月,元石山项目通过了青海省科技厅的专家鉴定,鉴定意见为:首次以煤替代天然气/煤气/重油作为热源和还原剂,实现了镍铁矿的选择性还原焙烧;首次从低浓度镍的氨浸液采用选择性萃取/反萃技术直接生产精制硫酸镍产品,氨介质循环利用、蒸汽消耗量少;该工艺流程短、能耗和生产成本低、资源综合利用率高,在处理低品位红土镍矿的工艺方面达到了国际领先水平。
“低品位镍铁矿高效绿色提取关键技术研究及示范”获得了国家“十一五”科技支撑计划(2007BAB19B00)支持,已通过科技部验收。
成果获得2012年中国资源综合利用协会科学技术奖一等奖和青海省科技进步二等奖。
图1 青海元石山工程全景原则工艺流程见图2。
吨硫酸镍生产成本见表1。
图2 还原焙烧-氨浸-磁选原则工艺流程图具体于菲律宾或印尼的褐铁型红土镍矿,由于其本身的粒度就较细(-200目>60%),采用回转窑还原焙烧,粉尘量会很大,建议采用成熟多膛炉还原焙烧技术,只是需要使用煤气来还原-需要建煤气发生炉。
若处理规模较大,反萃得到的高纯硫酸镍可以进一步生产电解镍。
表1 吨硫酸镍生产成本计算表1.2.2 加压酸浸法对于含镁小于10%,特别是小于5%的褐铁型红土镍矿,比较适合采用硫酸加压酸浸(HPAL)的全湿法流程。
红土镍矿在高温(230~260℃)和高压(4~5MPa)下用硫酸浸出,可以获得95%以上的镍、钴浸出率。
加压酸浸工艺经济指标主要受硫酸消耗量的影响,因而镁、铝含量和硫酸成本的高低直接影响该工艺的应用,另外,废水中镁、锰重金属的污染也是一个一直困扰该工艺应用的问题。
通常加压酸浸工艺可以经济地处理含镍1.3%以上的低品位矿石。
加压酸浸工艺自上世纪50年开始,在古巴毛阿(MOA)开始应用,经过40多年的运营,证明该工艺是经济可行的。
目前该厂年生产镍量约32000t,产品为混合镍钴硫化物精矿,为加拿大一家镍精炼厂提供原料,采用帕丘卡槽作为加压浸出设备,被认为是镍红土矿加压酸浸工艺的鼻祖。
上世纪90年代,随着硫化镍资源和高品位镍红土矿资源的逐渐减少,人们对大量存在的、品位在1%~1.5%之间的镍红土矿冶炼技术进行了更深入的研究开发。
自上世纪90年代以来,新的卧式加压浸出釜在黄金冶炼企业普遍应用,以加压酸浸为主的湿法冶炼镍红土矿技术,也相应地在更多的新建镍红土矿冶炼厂使用。
并于1997到1999年之间,相继在西澳大利亚建设了三家采用该技术的工厂:穆林穆林(Murrin Murrin)厂、布隆(Bu Long)厂和考斯(Cawse)厂。
目前,菲律宾的柯拉尔湾(Coral Bay)厂、新喀里多尼亚的戈罗(Goro)厂、巴布亚新几内亚的拉姆冶炼厂以及澳大利亚的拉温索普(Raven Sthorpe)厂正在采用加压酸浸法建设。
西澳大利亚的三个镍红土矿加压酸浸厂自建成投产以来并未取得预想的效果,使得镍红土矿加压酸浸的投资热度有所降低。
考斯镍冶炼厂1999年投产,是成功地从含镍红土矿中直接生产出电积镍的冶炼厂,但正是因为处理流程过于繁长,试生产期间就发生了资金链断裂问题而停产,后被OMG公司收购。
和考斯厂同时投产的布隆镍冶炼厂的设计能力为9000t/a阴极镍,加压浸出液经石灰中和除杂后直接采用萃取-电积技术生产阴极镍,由于硫酸钙问题导致萃取设备无法正常运转,萃取三相多、镍阳极板变形、腐蚀,最终因经营不善而破产。
穆林穆林厂设计能力为4.5万吨/a氢还原镍粉(镍块)和3000t/a 电解钴。
投产后的前三年仅达到设计能力的65%,主要是为了节省投资,在施工过程中使用了较多的替代材料。
后经改进,目前已达到设计能力的80%以上。
上述三个镍红土矿加压酸浸厂的主体工艺是成功的,但由于局部问题而影响了整个工艺的贯通。
正是基于这一看法,加之具有金属回收率高的优点,镍红土矿加压酸浸法越来越受到重视和应用。
但需要关注的是,西澳大利亚的三个镍红土矿加压酸浸厂处理的均是较为特殊的硅质型红土镍矿。
其典型成分为:含镍~1.5%、铁~20%、SiO2~40%、MgO<2%。
由于MgO和Al2O3的含量较低,加压酸浸时的耗酸量较低,因此采用加压酸浸法是比较适宜的。
而中冶集团在巴布亚新几内亚投资建设的RAMU红土镍矿项目采用加压酸浸就显得不那么合适了。
RAMU红土镍矿是典型的褐铁型红土镍矿,含铁~45%、含镍~1.2%、含钴0.8%。
按目前的金属价格,该矿主要有价元素的价值组成如下(1t):表2 RAMU红土镍矿的价值组成(1t)镍仅占原矿价值的46%,铁的价值则超过了镍。
目前采用的硫酸加压浸出工艺仅仅考虑了镍、钴的回收,富含铁的浸出渣则被用于填海,不仅浪费了铁资源,而且带来了环境污染。
1.2.3 常压酸浸法最近几年,世界镍的价格飙升,国内的硫酸价格则由1600元/t 的高位持续下跌至约100元/t的低位,至目前稳定在650元/t左右。
和镍的价格相比较,硫酸的消耗量和由此带来的生产成本已不再成为红土镍矿处理的制约性因素。
以橄榄岩为主的镁质红土镍矿,由于可以在常压下得到较好的浸出结果(大于85%),因而在国内也得到了较快的发展。
通常常压硫酸浸出工艺可以经济地处理含镍1.5%以上的镁质红土镍矿(MgO含量10~20%)。
1.2.4 堆浸法氧化铜矿的堆浸-萃取-电积技术是上世纪六十年代开发的一项新技术,主要用以处理常规选冶工艺无法经济回收的、以往被视为难处理矿或呆矿而未被开发利用的低品位铜资源。
由于具有工艺简单、投资低、生产成本低、对环境友好等诸多优点,该项技术在北美、南美、非洲、澳大利亚等地很快得到推广应用。
目前全世界采用这项技术生产的电解铜每年超过了200万t。
2001年,我国有关单位借鉴低品位铀矿和低品位氧化铜矿堆浸的成功经验,针对云南元江镍矿开展了低品位氧化镍矿的堆浸实践,虽然存在镍、钴浸出率低(Ni~60%、Co~40%,渣含镍~0.4%)、硫酸消耗量大(70t-H2SO4/t-Ni)、硫酸镁溶液直接排放等一系列的问题,但受国内镍资源短缺和世界镍价的影响,加之生产规模较小,对资源破坏和环境影响尚不严重,该工艺目前尚能维持。
但若考虑大规模的工业开发,该工艺对资源的破坏和环境的影响显然非常严重,即便考虑对硫酸镁进行回收,硫酸镁的销售也存在很大的问题,若按年产5000t-Ni、镍回收率50%、镁浸出率60%计算,年产结晶硫酸镁将达到100万t。
近年来,国外也开展了褐铁矿类红土镍矿的堆浸研究和实践,但受矿物特性的影响,褐铁矿类红土镍矿的堆浸浸出效果并不理想,加之红土镍矿的渗水性较差,堆浸时的沟流严重,镍、钴的浸出率通常在50~60%;同时由于浸出渣中残留着大量的硫酸根,也很不利于后续铁的综合利用。