热塑性片状模塑料及其制品冲压成型工艺
热塑性复合材料成型工艺介绍

热塑性复合材料成型工艺介绍热塑性复合材料是以玻璃纤维、碳纤维、芳纶纤维等增强各种热塑性树脂的总称,国外称FRTP(Fiber Rinforced Thermo Plastics)。
由于热塑性树脂和增强材料种类不同,其生产工艺和制成的复合材料性能差别很大。
从生产工艺角度分析,塑性复合材料分为短纤维增强复合材料和连续纤维增强复合材料两大类:(1)短纤维增强复合材料①注射成型工艺;②挤出成型工艺;③离心成型工艺。
(2)连续纤维增强及长纤维增强复合材料①预浸料模压成型;②片状模塑料冲压成型;③片状模塑料真空成型;④预浸纱缠绕成型;⑤拉挤成型。
热塑性复合材料的特殊性能如下:(1)密度小、强度高热塑性复合材料的密度为1.1~1.6g/cm3,仅为钢材的1/5~1/7,比热固性玻璃钢轻1/3~1/4。
它能够以较小的单位质量获得更高的机械强度。
一般来讲,不论是通用塑料还是工程塑料,用玻璃纤维增强后,都会获得较高的增强效果,提高强度应用档次。
(2)性能可设计性的自由度大热塑性复合材料的物理性能、化学性能、力学性能,都是通过合理选择原材料种类、配比、加工方法、纤维含量和铺层方式进行设计。
由于热塑性复合材料的基体材料种类比热固性复合材料多很多,因此,其选材设计的自由度也就大得多。
(3)热性能一般塑料的使用温度为50~100℃,用玻璃纤维增强后,可提高到100℃以上。
尼龙6的热变形温度为65℃,用30%玻纤增强后,热形温度可提高到190℃。
聚醚醚酮树脂的耐热性达220℃,用30%玻纤增强后,使用温度可提高到310℃,这样高的耐热性,热固性复合材料是达不到的。
热塑性复合材料的线膨胀系数比未增强的塑料低1/4~1/2,能够降低制品成型过程中的收缩率,提高制品尺寸精度。
其导热系数为0.3~0.36W(㎡·K),与热固性复合材料相似。
(4)耐化学腐蚀性复合材料的耐化学腐蚀性,主要由基体材料的性能决定,热塑性树脂的种类很多,每种树脂都有自己的防腐特点,因此,可以根据复合材料的使用环境和介质条件,对基体树脂进行优选,一般都能满足使用要求。
模压成型工艺
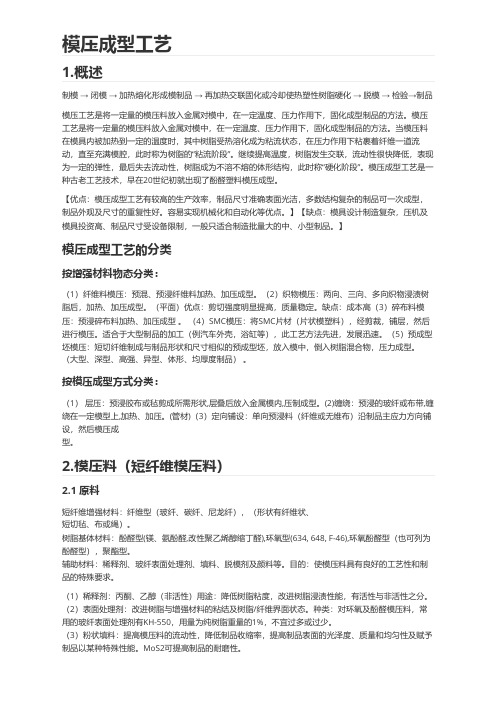
模压成型工艺1.概述制模→闭模→加热熔化形成模制品→再加热交联固化或冷却使热塑性树脂硬化→脱模→检验→制品模压工艺是将一定量的模压料放入金属对模中,在一定温度、压力作用下,固化成型制品的方法。
模压工艺是将一定量的模压料放入金属对模中,在一定温度、压力作用下,固化成型制品的方法。
当模压料在模具内被加热到一定的温度时,其中树脂受热溶化成为粘流状态,在压力作用下粘裹着纤维一道流动,直至充满模腔,此时称为树脂的“粘流阶段”。
继续提高温度,树脂发生交联,流动性很快降低,表现为一定的弹性,最后失去流动性,树脂成为不溶不熔的体形结构,此时称“硬化阶段”。
模压成型工艺是一种古老工艺技术,早在20世纪初就出现了酚醛塑料模压成型。
【优点:模压成型工艺有较高的生产效率,制品尺寸准确表面光洁,多数结构复杂的制品可一次成型,制品外观及尺寸的重复性好。
容易实现机械化和自动化等优点。
】【缺点:模具设计制造复杂,压机及模具投资高、制品尺寸受设备限制,一般只适合制造批量大的中、小型制品。
】模压成型工艺的分类按增强材料物态分类:(1)纤维料模压:预混、预浸纤维料加热、加压成型。
(2)织物模压:两向、三向、多向织物浸渍树脂后,加热、加压成型。
(平面)优点:剪切强度明显提高,质量稳定。
缺点:成本高(3)碎布料模压:预浸碎布料加热、加压成型。
(4)SMC模压:将SMC片材(片状模塑料),经剪裁,铺层,然后进行模压。
适合于大型制品的加工(例汽车外壳,浴缸等),此工艺方法先进,发展迅速。
(5)预成型坯模压:短切纤维制成与制品形状和尺寸相似的预成型坯,放入模中,倒入树脂混合物,压力成型。
(大型、深型、高强、异型、体形、均厚度制品)。
按模压成型方式分类:(1)层压:预浸胶布或毡剪成所需形状,层叠后放入金属模内,压制成型。
(2)缠绕:预浸的玻纤或布带,缠绕在一定模型上,加热、加压。
(管材)(3)定向铺设:单向预浸料(纤维或无维布)沿制品主应力方向铺设,然后模压成型。
塑料成型模具设计热成型
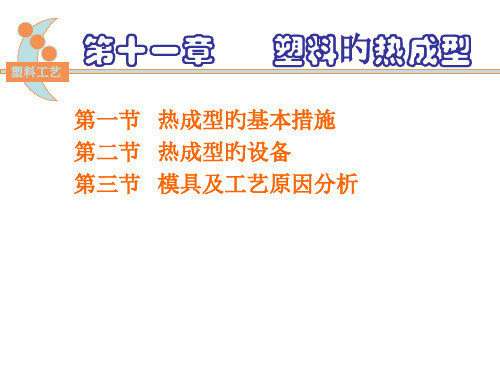
7.其他成型 板材旳弯曲,法兰旳弯制,管材旳弯制等,另外,有板材
卷成筒,容器旳口部或底部旳卷边和管材旳扩口等,都属于热 成型旳范围。
第二节 热成型旳设备
塑料工艺
热成型旳基本工序: 片材夹持、加热、成型、冷却、脱模
一.模具
1.工作压力不高时,可采用强度底旳材料制造模具。材料旳选择 要根据成型旳数量和质量要求而定,如木制模具合承受500次成型, 石膏模具可承受50次,型砂模具和树脂砂模可承受500次以上。 2.模具上旳通风孔制作也是在浇注型砂前插上表面涂有隔离剂旳 钢丝,浇注14小时后抽出钢丝。 3.外形简朴旳制品用阴模成型。因制品收缩,易取出,若构造复 杂,要施加顶出力;对用阳模成型小型拉伸制品时,阳模旳高度尤 为主要。阳模侧圆半径不应不大于板厚旳3-5倍。
品。
2) 应用范围广;日常生活中器皿,食品和药物包装, 汽车部件等。
3) 设备投资少;热成型压力不高,对设备要求不高。 4) 模具制造以便;∵压力低,除金属外,木材,塑料, 石膏等∴热成型在近十年才有较大旳发展。
塑料工艺
3.成型基本过程 1) 先将裁诚一定尺寸和固定形样旳片材夹在框架上; 2) 加热到热高弹态; 3) 成型 凭借施加压力使其贴近模具旳形面,从而得
定压强)→片材包住(模具反压力)封死→打开底模具部抽气孔抽 气→回吸而贴合→成型→冷却脱模→修整→制品 3)推气真空成型 如图 13-11
塑料工艺
塑料工艺
5.模压成型 单阳模法、 单阴模法、 对模成型
多和模压成型 使用也全部热塑性塑料
6.双片成型 这是成型中空制品旳一种措施 如图13-13 两块已加热到足够温度塑料片材,放在半合模具模框上夹
热成型工艺pptx
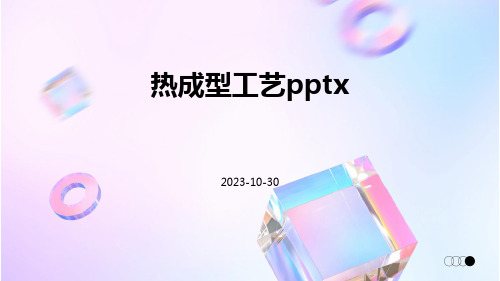
近年来,随着环保意识的不断提高,热成型工艺逐渐向绿色制造方向发展,例如采用回收塑料材料作为原料, 以及开发新的加工技术以提高生产效率和降低成本。
热成型工艺的应用范围
汽车行业
热成型工艺被广泛应用于制造汽车车身覆 盖件、仪表板、保险杠等大型塑料制品。
建筑行业
热成型工艺可制造各种类型的塑料门窗、 幕墙、扣板等建筑装饰材料。
冷却温度
冷却温度也是热成型工艺中需要严格控制的参数,冷却不当可能导致材料变形、内应力增大或者出现 气泡等缺陷。
时间控制
成型时间
成型时间太长可能导致材料变形或产生内应力,而时间太短则可能导致成型不充分或者出现缺陷。
冷却时间
冷却时间太长可能导致材料变脆或者产生内应力,而时间太短则可能导致材料未充分冷却而影响性能 。
特点
热成型工艺具有生产效率高、制造成本低、材料利用率高、 可制造大型制品等优点,但同时也存在制品精度不高、材料 性能有所损失等缺点。
热成型工艺的历史与发展
历史
热成型工艺最初起源于20世纪40年代,当时主要用于制造玻璃纤维增强塑料制品。随着材料和技术的不断发 展,热成型工艺逐渐应用于制造各种类型的塑料制品。
热成型弯曲变形
• 弯曲变形:热成型制品形状与设计不符,原因可能是材料流 动性差、模具设计不合理、冷却不均匀等。防止方法包括改 善材料流动性、优化模具设计、控制冷却速度等。
表面粗糙与橘皮状
表面粗糙
热成型制品表面不平整,原因可能是材料流 动性差、模具表面质量差等。防止方法包括 改善材料流动性、提高模具表面质量等。
热成型工艺pptx
2023-10-30
目录
• 热成型工艺简介 • 热成型工艺流程 • 热成型工艺参数控制 • 热成型工艺缺陷及防止方法 • 热成型工艺优化与发展趋势 • 热成型工艺案例展示
复合材料成型工艺与设备(11.热塑性片状模塑料及其制品)

9
2 干法生产工艺及设备 (1)层合法生产热塑性片状模塑料 是将连续玻璃纤维毡和聚丙烯(或其它热塑性塑料) 薄片叠合后,经过加热、加压、浸渍、冷却定型和切 断等工序制造片状模塑料的方法。 优点 塑料挤板机“可有可无”,粉末状树脂直接撒 入毡内,容易浸透纤维。
10
2
1
3
4
6
7 8 9
5
图13-2 干法生产热塑性片状模塑料工艺及设备
3
Байду номын сангаас
6)比热固性玻璃钢具有较高的耐化学腐蚀性、耐水性 和气密性 7)原材料充足、价格便宜、成本低(与手糊比低20%左右) 8)机械化程度高 热塑性CM必须采用机械化生产,质量稳定。 9)设备一次性投资大 热塑性SMC与注射成型热塑性CM的比较: (1)、具有较高的强度和刚度; (2)、抗冲击性能好; (3)、产品精度高; (4)、产品尺寸较小时一般采用注射成型(属短纤维增强) 对于较大型制品,可采用冲压成型(属连续纤维增强)
是以碳纤维、芳纶纤维及高强度玻璃纤维增强聚醚醚酮 (PEEK)、聚醚酮(PEK)、聚苯硫醚(PPS)等高性能树脂等。 特点 1、使用温度高(260℃),热固性CM使用温度低于200℃ 2、碳纤维增强的热塑性复合材料密度小
6
2.2 通用型热塑性复合材料 是指以玻璃纤维增强聚丙烯、聚乙烯、尼龙等 一般的FRTP
3.1冲压成型工艺 根据坯料在模具内的成型过程及温度 流动态冲压成型 (1)成型特点: 成型周期短,生产效率高 表13-7 无储存期,可回收利用 模具费用低 一次能成型形状复杂或大型制品 可与金属等其它材料复合制成复合结构制品
15
固态冲压成型
(2)固态冲压成型 类似于金属冲压工艺,按样板将片状模塑料剪切成坯料, 然后在加热器内将料片加热到低于粘流态温度10~20℃,装 入模具,快速合模加压,在70℃模具内冷却脱模,修边成 制品。 特点:制品形状简单,周期短,成型压力小(一般小于 1.0MPa)。 (3)流动态冲压成型 适于制备成型厚度和密度变化大、带凸台或加强肋等形 状复杂的或带金属预埋件的制品。 按样板将片状模塑料剪切成坯料,然后在加热器内将 料片加热到高于粘流态温度10~20℃,装入模具,快速合模 加压,迫使融态坯料流动并填满模腔(成型压力较大,约 10~20MPa),冷却定型后脱模成制品。
塑料热压成型工艺
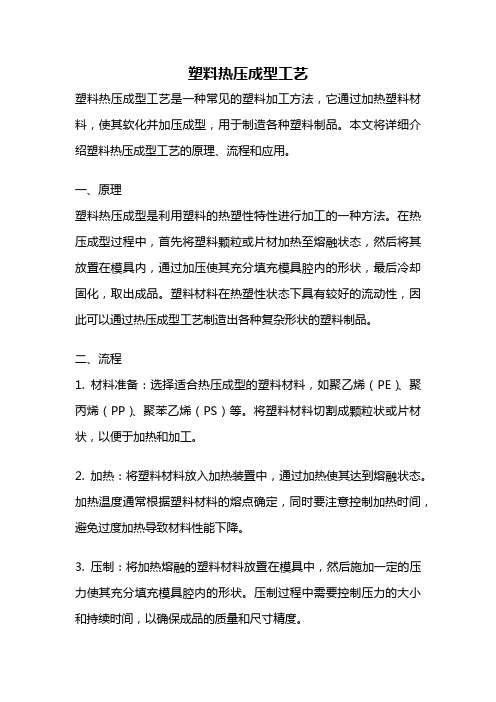
塑料热压成型工艺塑料热压成型工艺是一种常见的塑料加工方法,它通过加热塑料材料,使其软化并加压成型,用于制造各种塑料制品。
本文将详细介绍塑料热压成型工艺的原理、流程和应用。
一、原理塑料热压成型是利用塑料的热塑性特性进行加工的一种方法。
在热压成型过程中,首先将塑料颗粒或片材加热至熔融状态,然后将其放置在模具内,通过加压使其充分填充模具腔内的形状,最后冷却固化,取出成品。
塑料材料在热塑性状态下具有较好的流动性,因此可以通过热压成型工艺制造出各种复杂形状的塑料制品。
二、流程1. 材料准备:选择适合热压成型的塑料材料,如聚乙烯(PE)、聚丙烯(PP)、聚苯乙烯(PS)等。
将塑料材料切割成颗粒状或片材状,以便于加热和加工。
2. 加热:将塑料材料放入加热装置中,通过加热使其达到熔融状态。
加热温度通常根据塑料材料的熔点确定,同时要注意控制加热时间,避免过度加热导致材料性能下降。
3. 压制:将加热熔融的塑料材料放置在模具中,然后施加一定的压力使其充分填充模具腔内的形状。
压制过程中需要控制压力的大小和持续时间,以确保成品的质量和尺寸精度。
4. 冷却:在压制完成后,需要将模具中的塑料制品进行冷却固化。
冷却时间通常根据塑料材料的特性和成型件的厚度来确定,以确保成品具有足够的强度和稳定性。
5. 取出成品:冷却固化后,打开模具,取出成品。
这时,成品已经具备了所需的形状和性能特点。
三、应用塑料热压成型工艺广泛应用于各个领域,包括日常生活用品、工业制品、电子产品等。
例如,塑料热压成型可以用于制造塑料碗、塑料杯等日常生活用品,具有成本低、生产效率高的优点;在工业制品中,塑料热压成型可以用于制造塑料托盘、塑料箱等,具有轻质、坚固、耐用的特点;在电子产品领域,塑料热压成型可以用于制造手机壳、键盘等,具有外观精美、绝缘性能好的特点。
总结:塑料热压成型工艺是一种常见且重要的塑料加工方法,通过加热、压制、冷却等步骤,将塑料材料加工成各种形状的塑料制品。
高分子材料加工技术--压制成型

1.2工艺过程
高分子材料成型加工
高分子材料成型加工
2.片状模塑料模压成型
(Sheet Molding Compound. SMC)
2.1 配比:
不饱和聚酯 约20~30%
增稠剂
约 5%
无机填料 40~50%
引发剂
2~3%
脱模剂
0.5~1%
短切玻璃纤维或毡片 适量
2.2 工艺过程
高分子材料成型加工
高分子材料成型加工
三. 模型硫化工艺及硫化条件
工艺过程
混炼胶和橡胶半成品→ 计量→ 加料→ 闭 模→排气 →保压(硫化)→ 脱模→ 制品
这一过程基本上与热固性塑料的模压成型 相同,硫化工艺条件是硫化压力、硫化温 度和硫化时间。
高分子材料成型加工
1.硫化压力 大多数的橡胶制品的硫化是在一定压力下 进行的 一般模压制品的硫化压力为2~4 MPa 胶料流动性差,制品形状复杂,制品表面 花纹细致,结构复杂,厚制品,硫化温度 高,则硫化压力高一些。 太高的硫化压力会加速橡胶分子链的热降 解
高分子材料成型加工
一. 热固性模塑料的成型工艺性能:
1.流动性:热固性模塑料的流动性是指其在受热和受 压情况下充满整个模具型腔的能力。 影响流动性的因素:
压模塑料的性能和组成(分子量、颗粒形状、小分 子物质)
模具与成型条件(光洁度、流道形状、预热)
流动性要适中:
太大:溢出模外,塑料在型腔内填塞不紧,或树脂 与填料分头聚集。
高分子材料成型加工
根据实践经验,在选择模压成型的工艺条 件时,可以从模压压力、温度和时间三者 中先固定一个条件,如按经验选定成型压 力,然后再变化成型的温度和时间,从实 验中找出合理的条件来。
热塑性塑料常用的加工工艺
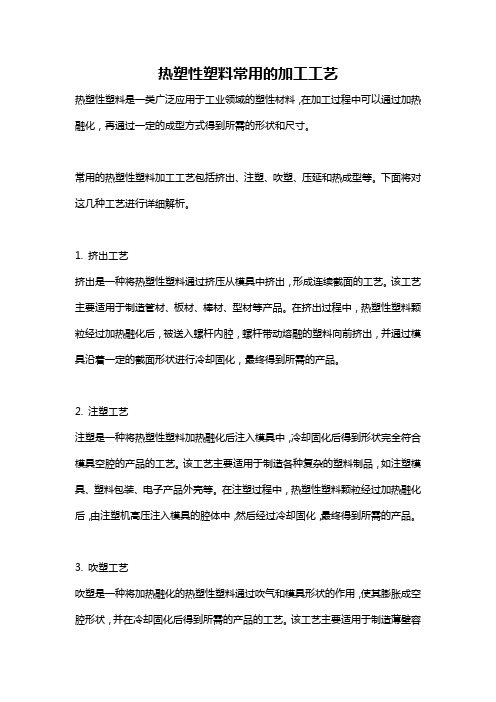
热塑性塑料常用的加工工艺热塑性塑料是一类广泛应用于工业领域的塑性材料,在加工过程中可以通过加热融化,再通过一定的成型方式得到所需的形状和尺寸。
常用的热塑性塑料加工工艺包括挤出、注塑、吹塑、压延和热成型等。
下面将对这几种工艺进行详细解析。
1. 挤出工艺挤出是一种将热塑性塑料通过挤压从模具中挤出,形成连续截面的工艺。
该工艺主要适用于制造管材、板材、棒材、型材等产品。
在挤出过程中,热塑性塑料颗粒经过加热融化后,被送入螺杆内腔,螺杆带动熔融的塑料向前挤出,并通过模具沿着一定的截面形状进行冷却固化,最终得到所需的产品。
2. 注塑工艺注塑是一种将热塑性塑料加热融化后注入模具中,冷却固化后得到形状完全符合模具空腔的产品的工艺。
该工艺主要适用于制造各种复杂的塑料制品,如注塑模具、塑料包装、电子产品外壳等。
在注塑过程中,热塑性塑料颗粒经过加热融化后,由注塑机高压注入模具的腔体中,然后经过冷却固化,最终得到所需的产品。
3. 吹塑工艺吹塑是一种将加热融化的热塑性塑料通过吹气和模具形状的作用,使其膨胀成空腔形状,并在冷却固化后得到所需的产品的工艺。
该工艺主要适用于制造薄壁容器,如瓶子、罐子等。
在吹塑过程中,热塑性塑料颗粒经过加热融化后,通过模具内的吹气,使其膨胀成空腔形状,然后经过冷却固化,最终得到所需的产品。
4. 压延工艺压延是一种将热塑性塑料加热融化后,通过压力作用使其均匀地挤出成一定厚度和宽度的连续膜或板的工艺。
该工艺主要适用于制造塑料膜、塑料板等产品。
在压延过程中,热塑性塑料颗粒经过加热融化后,被挤出成一定厚度和宽度的连续膜或板,然后通过冷却固化,最终得到所需的产品。
5. 热成型工艺热成型是一种将热塑性塑料加热融化后,通过模具形状的作用,将其成型成所需的产品的工艺。
该工艺主要适用于制造各种形状复杂的塑料制品,如塑料容器、塑料包装等。
在热成型过程中,热塑性塑料颗粒经过加热融化后,被加压使其进入模具中,然后通过冷却固化,最终得到所需的产品。
- 1、下载文档前请自行甄别文档内容的完整性,平台不提供额外的编辑、内容补充、找答案等附加服务。
- 2、"仅部分预览"的文档,不可在线预览部分如存在完整性等问题,可反馈申请退款(可完整预览的文档不适用该条件!)。
- 3、如文档侵犯您的权益,请联系客服反馈,我们会尽快为您处理(人工客服工作时间:9:00-18:30)。
产
1-塑料挤板机;2-玻璃纤维毡;3-塑料片材;4-无端
工
加压带;5-加热、挤压装置;6-冷却设施;7-复合片
艺
材;8-切断器;9-成品
及
设
备
第13章 热塑性片状模塑料
课件
13.2.3
(2)分散法生产片状模塑料工艺
将短切玻璃纤维与聚丙烯或尼龙等树脂粉末在特 殊的搅拌机内混合均匀,然后按设计厚度铺撒均匀, 再经加热,加压制成片状模塑料。
第13章 热塑性片状模塑料
课件
13.3.1
作业:
与热固性片状模塑料相比,热塑性片状模塑料制品有哪些 特性?
片 状 模 塑 料 湿 法 生 产 工 艺
第13章 热塑性片状模塑料
2.2 通用型热塑性复合材料 是指以玻璃纤维增强聚丙烯、聚乙烯、尼龙等
一般的FRTP
通 用 型 热 塑 性 复 合 材 料
课件
第13章 热塑性片状模塑料
课件
13.2.1
13.2 热塑性片状模塑料的生产工艺及设备
层合法
干法
通
生产方法
分散法
用 型
湿法 水分散法
热 塑
WT法(泡沫分散法)
4)成型压力低 热塑性片状模塑料冲压成型压力 3~8MPa
概 热固性片状模塑料热压成型压力 3~15MPa 述 5)贮存期长
热塑性片状模塑料可贮存几年以上; 热固性片状模塑料可贮存3个月(常温)
第13章 热塑性片状模塑料
课件
6)比热固性玻璃钢具有较高的耐化学腐蚀性、耐水 性
和气密性 7)原材料充足、价格便宜、成本低(与手糊比低20%左右)
8)机械化程度高 热塑性CM必须采用机械化生产,质量稳定。
9)设备一次性投资大
13.1.1
热塑性SMC与注射成型热塑性CM的比较:
概 (1)、具有较高的强度和刚度; 述 (2)、抗冲击性能好;
(3)、产品精度高; (4)、产品尺寸较小时一般采用注射成型(属短纤维增强) 对于较大型制品,可采用冲压成型(属连续纤维增强)
是将连续玻璃纤维毡和聚丙烯(或其它热塑性塑料)
干 法
薄片叠合后,经过加热、加压、浸渍、冷却定型和切 断等工序制造片状模塑料的方法。
生 优点 挤板机“可有可无”,粉末状树脂直接撒入毡
产
内,容易浸透纤维。
工
艺
及
设
备
第13章 热塑性片状模塑料
课件
2
1
3
4
67
8
9
13.2.3
干
5
法 生
图13-2 干法生产热塑性片状模塑料工艺及设备
第13章 热塑性片状模塑料
课件
13 热塑性片状模塑料及其制品 冲压成型工艺
1.1 定义
它是以连续玻璃纤维毡、短切玻璃纤维
毡、布、无捻粗纱和热塑性树脂复合而成的
一种片状模塑料。
13.1.1
热塑性片状模塑料加工制品工艺——料片预热冲压成型;
热固性片状模塑料加工制品工艺——热压成型。
热塑性片状模塑料制品与热固性制品特性比较:
干 优点: 1)增强材料范围广 法
生
2)纤维含量控制在20一40%
产 工
3)纤维铺层方向可任意选择
艺
及
设
备
第13章 热塑性片状模塑料
课件
13.3.1
3 热塑性片状模塑料湿法生产工艺
将 玻 璃 纤 维 无 捻 粗 纱 切 成 长 7 ~ 50mm( 最 佳 长 度 为
13mm左右)的短纤维,在搅拌器内与粉末状树脂加水搅拌
性
复
图13.1 热塑性片状模塑料制造方法
合
材
料
第13章 热塑性片状模塑料
课件
1 原材料
(1)树脂 尼龙、聚乙烯、聚氯乙烯和聚丙烯等。目前 用于生产的只有聚丙烯和改性聚丙烯树脂。
13.2.2
聚丙烯的优点:(1)密度小;(2)抗冲击性好;(3)
使用温度范围较宽-40~100℃;(4)工艺性好,在熔
融条件下的流动性好,对玻纤的浸渍性好,冷却后固
片 成均匀的悬浮料浆,用泵将其输送到传送网带上,经减压 状 脱水,形成湿毡,再经干燥、切断、收卷成中间产品。
模
塑 料 湿
特点 1、用短切纤维、粉末状树脂和水或泡沫 悬浮液混合料浆
法 生
2、纤维含量可达20~70%
产
3、产品厚度为1.27~6.35mm
工
艺
第13章 热塑性片状模塑料
课件
13.3.1
片
高性能复合材料 通用型复合材料
高 2.1 高性能复合材料
性 能 复
是以碳纤维、芳纶纤维及高强度玻璃纤维增强聚醚醚酮 (PEEK)、聚醚酮(PEK)、聚苯硫醚(PPS)等高性能树脂等。
合 特点 1、使用温度高(260℃),热固性CM使用温度低于200℃
材
料
2、碳纤维增强的热塑性复合材料密度小
13.1.3
状
模
塑
料
湿
法
生 产
图13-3 湿法生产热塑性SMC示意图
工 1-玻纤纱;2-切断器;3-沉降室;4-输送带;5-树脂、填料;6-水;7-拌
艺
浆槽;8-泵;9-浆槽;10-浆料;11-真空脱水;12-运输带;13-胶粘剂; 14-烘干;15-切断;16-坯料;17-无端钢带;18-加热、加压区;19-成品
化迅速,由此生产效率 玻璃纤维无捻粗纱,玻璃纤维短切毡、 连续玻璃纤维毡和针刺连续玻璃纤维
毡等 。只是浸润剂有所区别,(使玻
纤能与聚丙烯牢固结合) 。
第13章 热塑性片状模塑料
课件
13.2.3
2 干法生产工艺及设备 (1)层合法生产热塑性片状模塑料
概 述
1)比强度高 热塑性片状模塑料强度与手糊玻璃钢相似,见表13-2
密度(1.1~1.6 g/cm3)
热固性制品强度见表13-2,与热塑性相当,密度1.6~
2.0 g/cm3
第13章 热塑性片状模塑料
课件
13.1.1
2)能重复加工成型 边角余料、废品等可重复加工,节省材料,降低成本。
3)成型周期短 热固性SMC成型周期6~15min 热塑性SMC成型周期20~60s 生产效率高,易于实现自动化、机械化生产。
13.1.1
第13章 热塑性片状模塑料
(5)、成型压力较小 对模具和压机的要求比注射成型低。
与钢材相比:
(1)重量轻,密度小;
(2)耐腐蚀;
(3)形状设计性好,可一次成型较复杂制品
概
(4)比钢材的生产投资少
述
课件
第13章 热塑性片状模塑料
课件
1.2 纤维增强热塑性复合材料的基本性能
13.1.2
纤维增强热塑性复合材料