萘酚工艺操作规程最新

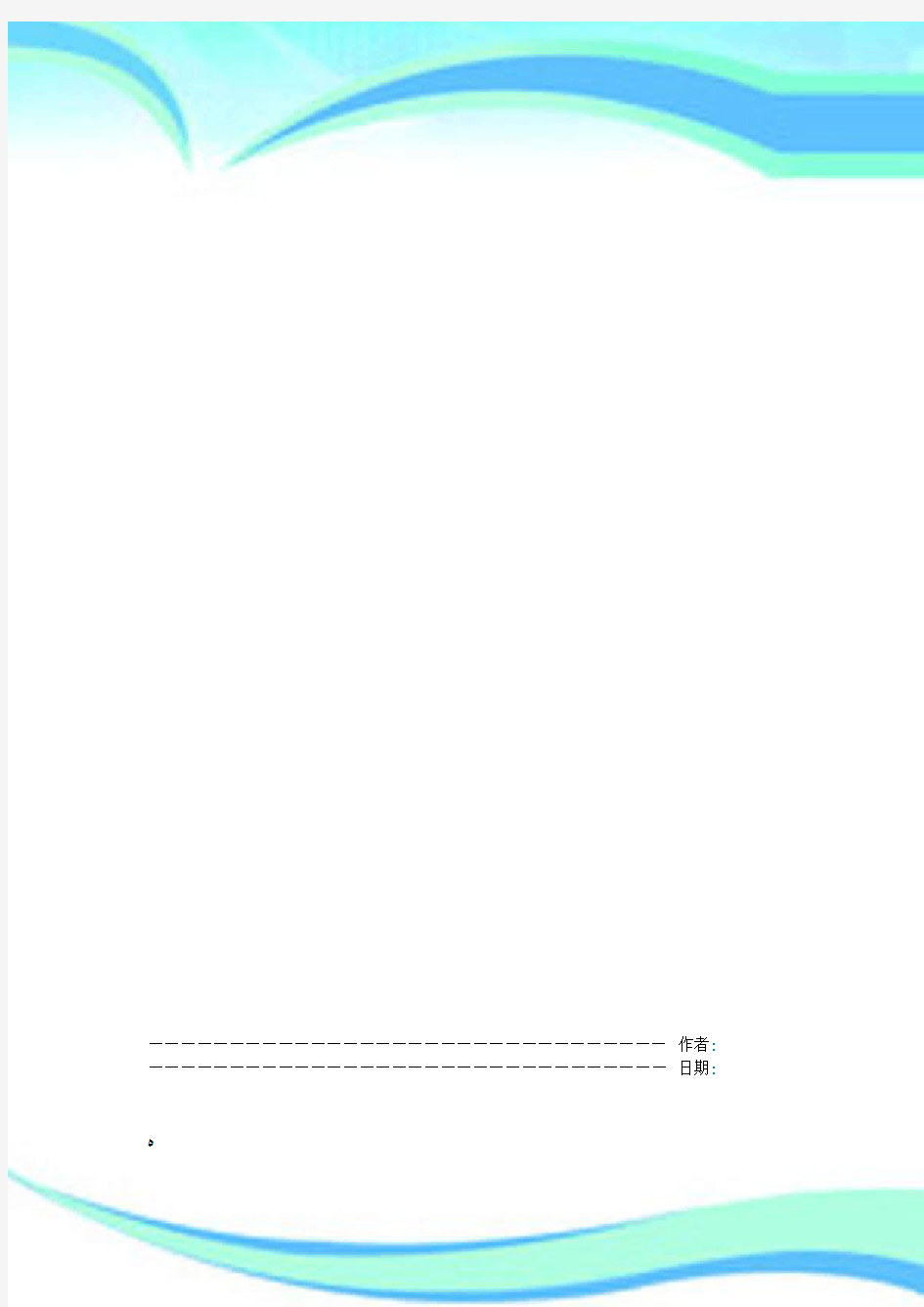
-萘酚工艺操作规程(最新)
————————————————————————————————作者: ————————————————————————————————日期:
?
2-萘酚工艺操作规程
(A版)
批准:惠晓新
审核:周宏钧
编写:孙金毛金兴官
王玉明
2012年1月3日批准 2012年1月4日实施宿迁思睿屹新材料有限公司
目录
1.产品概述 (3)
2.产品原料 (3)
3.生产工艺流程图 (4)
4.生产操作过程控制 (6)
5.异常现象及处理方法 (18)
6.主要设备一览表.......................................23 7.主要工艺参数控制一览表 (25)
2—萘酚工艺操作规程
1 产品概述
1.1产品名称
1.1.1中文名称:β—萘酚(或2—羟基萘, 2—萘酚)
1.1.2 英文名称:β—Naphthol
1.2 产品物理、化学性质
2—萘酚为灰白色薄片或均匀粉末,易溶于乙醇、乙醚、氯仿、苯等及苛性钠的水溶液中。
1.3 产品的主要用途
2—萘酚用来制造苯胺染料工业中的各种中间体,制造橡胶工业的防老剂,制造晒盐工业用的蒸发促进剂,以及作颜料、油漆和棉织品的冰染染料等。
1.4产品化学结构式
1.5 产品分子式: C10H8O
产品分子量:144.16
2 产品、原料规格
2.1 原料规格
本工艺中使用的原料规格见LT/QG SJ0500《主要原料及其控
制指标》。
2.2 产品规格
见相应的国家标准。
2.3 包装
2—萘酚装于内衬塑料袋的编织袋中,净重25Kg/袋。袋口用线扎紧,防止散落及雨水浸入。
3 化学反应过程和生产工艺流程图 3.1 化学反应过程 3.1.1 磺化
+H 2SO 4
+H2O
3.1.2 水解
+H 2O
+H 2S O4
3.1.3吹萘
加30%的NaO H于水解后的物料中 3.1.3.1 与水解物中的游离酸起中和反应
2N aO H+H2SO4 Na 2S O4+2H2O 3.1.3.2 与部分2—萘磺酸生成2—萘磺酸钠盐结晶种子 NaOH+
+H2O
3.1.4 中和
用Na 2S O3溶液中和萘物
+Na 2SO 3
+H 2O +SO 2
3.1.5 2—萘磺酸钠盐的碱熔
+2Na OH
330-340℃
+Na 2SO 3 +H2O
3.1.6 2—萘酚钠盐的酸化
+SO 2+H 2
O +N a2SO 3
2NaOH+SO 2 Na 2SO 3+H 2O 3.2 生产工艺流程简图
精萘 H 2SO 4
H 2O
H 2O NaOH Na 2SO 3
SO 2
90%NaOH
H2O
H 2O
H 2O
4 生产过程控制
4.1 磺化 (岗位编号:β-OH —01) 4.1.1 操作目的
二 煮 06
磺 化 01
水 解 02
吹 萘 02 中 和 03
冷却、压滤 04
碱 熔 05 稀 释 05 酸 化 03 一 煮 06
三 煮 06 干 燥 07
蒸 馏 07
切 片 07 包 装 07
压 滤
冷 凝 液
残液
残渣油
根据工艺规程,用98%硫酸与萘反应生成符合质量要求的2-萘磺酸,供水解、吹萘岗位用。
4.1.2 操作指标
加料表(一次作业投入量)
名称
浓度
( )
折百重
(kg)
工业重
(kg)
体积
(L)
千摩尔
(Kmol)
备注
精萘 99 1568 1584 1650 12.25
浓度以结晶点
≥79.5℃计
硫酸98 1244 1270 690 12.70
中控指标
总酸度(%) 24.0~28.0 游离酸(%) 6.0~8.0
4.1.3 操作步骤
4.1.3.1 开车前准备工作
①检查清理所有设备、管道、阀件无滴渗漏现象。
②仪表、电器设备、传动装置等保持正常使用要求,备好岗位专用工具。
③开硫酸液下泵进酸于计量槽。
④磺化锅应无杂物,投料前应先开夹套导热油,预热烘干水份。
⑤调整磺化锅的各种阀门于正确位置。
4.1.3.2正常操作方法
①开启精萘打料泵,将熔融的萘打入萘计量槽,待回流时停泵,回流结束后开磺化进萘阀,全部加入磺化锅后,量体积至1650L。
②调整夹套导热油,使萘温升至138~145℃,在搅拌下加酸10~30
分钟。再调整夹套导热油,使物料温度升至160~165℃,常压维持2小时以上。
③维持结束,关闭夹套导热油,停搅拌后测体积约2200~2400L,取样分析。
④调整阀门,用蒸汽吹扫管道。应先通知水解岗位工得到同意方可出料。锅内压力应≤0.12MPa,出料完毕调整阀门,检查锅内应无余料。
⑤操作台时、异常情况、分析数据应及时填入记录本。
4.1.4 停工方法
按车间停工指令,停止投料,锅内不应存放物料。
如需洗锅,先向锅内加少量水,搅拌下洗锅,洗锅水通过出料管压入水解锅,再按车间规定程序操作,最后套用于生产。
如若长时间停工,酸、萘计量槽不允许存放原料。
4.1.5 “三停”情况处理方法
若突然停导热油炉,应先关闭导热油阀,停止加酸,待导热油正常后继续操作;已维持的物料则继续维持至终点。
突然停电,关闭夹套导热油阀,停止所有操作,来电后再恢复操作,如维持的物料再继续维持至终点。
磺化出料时遇停电、停导热油,应停止出料,用余压或余汽把物料吹扫干净,防止堵管而影响下一次操作。
4.2 水解、吹萘(岗位编号:β-OH -02)
4.2.1 操作目的
将磺化副反应生成的1—萘磺酸经水解后含量降低,加少量稀碱产生晶种,用直接蒸汽将游离萘吹净并回收,供磺化套用。
4.2.2 水解、吹萘岗位操作指标
加料表(一次作业投入量)
名称浓度(%)体积(L)
磺化物 2200~2400
烧碱30~3
220~280
2
水 200~400
中控指标
游离硫酸%8.5~15
水解总酸度(%) 25~
32
吹萘总酸度(%) 16~23 游离萘无或微量(目测)
4.2.3 操作步骤
4.2.3.1 水解操作
①开启母液泵,调节控制阀向塔内进行喷洒,开两塔联通阀及母液溢流阀。
②打开水解锅排气阀和进料阀,通知磺化进料,进料完毕后待吹扫管道结束关闭进料阀。
③开启搅拌向锅内加50L水,结束后关阀并开蒸汽阀,在0.02~0.06M Pa压力下进行水解,时间1.5~2.5小时。经冷凝器后温度≥90℃后,打开弯管冷却水阀喷淋。水解时塔温控制为 100℃。
④遇有特殊情况等料2小时,水解时可不加50L水,据实际情况决定。
⑤水解结束后,关闭冷却水,停止搅拌。关闭直接蒸汽待锅内无余压时开手孔取样,并送至分析室。
⑥操作台时及生产异常情况应及时填写在记录本上。
4.2.3.2 吹萘操作
①在搅拌情况下向水解物中加水200~400L(蒸汽带水可酌情减少)、液碱220~280L,结束后关闭阀。
②开蒸汽阀,保持压力0.02~0.06MPa条件下吹萘,时间1~1.5小时,同时开盘管冷却喷淋,进行萘回收。
③吹萘结束后,缓慢停蒸汽、停搅拌,关闭水阀停止冷却喷淋,待锅内无余压时取样分析,吹萘分析合格可终止操作,否则应继续延迟吹萘时间直至合格。
④总酸度偏高可在搅拌情况下补加适量液碱后重新取样分析,合格后,方可出料。
⑤得到中和岗位允许,调整阀门,用压缩空气将物料全部出至中和锅,结束后放空余压,用蒸汽冲扫出料管。
⑥水解、吹萘操作时应经常观察回收系统母液回流保持正常状态,塔温控制正常,防止塔带压操作,杜绝跑萘。
⑦操作台时及异常情况应及时记录和交班。
⑧定期检查水解锅、吹萘锅搅拌叶、鼓泡器、出料管,应符合正常使用条件,否则应通知洗锅检修。
4.2.3.3 回收萘处理方法
①由白班对三组塔进行轮换处理,拾伍锅以内可暂不处理。
②将要处理的回收萘塔升温至100℃,维持、静置30分钟,使萘全部熔化,升温前必须关闭母液溢流阀。
③开塔顶放萘阀和塔底进母液阀,当塔内液位升至放萘管高度时,萘流入回收萘干燥器内,根据观察视镜流量调节进母液量,防止溢萘。
④观察并鉴别萘及母液分流情况,先流为萘,后流为母液;放萘终止后须知蒸汽吹扫管道并关闭进母液阀,量干燥器萘体积并填入交班记录。
⑤按规定进行干燥器保温静置,打开底部分水阀分水,如混层不清,必须重新补加母液或Na2SO3,升温静置后重新分水,通知磺化备用。
⑥回收萘剩余体积应控制不大于800L,否则应通知磺化继续使用,便于白班处理塔。
⑦回收萘大母液沉淀池应认真交接,萘沉积多时安排处理,将萘加入熔萘锅升温分水后,压入干燥罐备用。
4.2.4 停工方法
①按停工通知要求做好停车工作,做好回收萘的处理及设备清洗工作等。
②如遇“三停”,在正常水解、吹萘时停止操作,关闭水、汽阀,停止加碱、母液喷淋及冷却水,待正常后再恢复生产。
4.3 中和、酸化 (岗位编号:β-OH -03)
4.3.1 操作目的
将吹萘后物料,用Na2SO3溶液中和,生成符合规定质量要求的 —萘磺酸钠盐,供吸滤岗位使用。用中和产生的SO2酸化稀释物生成粗萘酚和亚硫酸钠供煮沸用。
4.3.2 操作指标
中和加料表
中和
名称浓度(g/L) 体积(L)
一次操作吹萘物2800
Na
2
SO
3
170~220 5800~6500
酸化加料表
酸化
名称体积(L)稀释物一次操作量6500~7500 中和来的SO
2
一锅对一锅
中控指标
名称指标 (%)
中和终点pH值5~6
中和物中亚硫酸氢钠2~5
酸化物中亚硫酸氢钠 1~5
酸化物中亚硫酸钠13~28
4.3.3 中和正常操作方法
①开启加Na2SO3阀门向中和锅内加预热后的Na2SO3,并控制加料速度保持锅内负压,加Na2SO3,时间控制在0:30~1:00,如中和物料泡沫大时,可开压缩空气鼓泡,待正常后恢复操作。
②当中和锅内泡沫没有时,应停止加Na2SO3,取样用PH试纸测定PH=5~6,继续带真空并用压缩空气鼓泡赶SO25~10分钟。
③吹扫SO2结束后补加1~3分钟Na2SO3。
④得到吸滤岗位同意后,用蒸汽吹扫管道畅通后方可用压缩空气将中和物出至冷却槽,开冷却水冷却,并经常观察出料情况,出料完毕后,用蒸汽吹扫管道并放空锅内余压。
⑤若车间废水来不及处理时,加Na2SO3后期及补加Na2SO3时可用少量30%液碱20L~50L来代替,使其减少车间废水量。
4.3.4酸化正常操作方法
①调整酸化锅阀门,通知稀释岗位工进料。酸化锅进料完毕,开水环真空泵,并打开锅上真空阀,然后打开通往中和的SO2管道阀,开搅拌,进行酸化,通SO2时间0:30~1:00。
②当中和操作结束后,关闭中和排SO2阀,开酸化锅废气阀,停真空,在常压下停搅拌,取样用PH试纸测PH6~6.5并送分析至终点合格。
③如分析不合格,必须补通下一锅中和之SO2。
4.3.5 正常停工方法
较长时间停车,中和锅内严禁存料,Na2SO3贮罐停止加热,水流泵应停止使用。
临时“三停”应停止操作,待正常后再恢复操作。
4.4 冷却、压滤(岗位编号:β-OH -04)
4.4.1 操作目的
根据工艺规程,完成β-萘磺酸钠盐结晶过程,进行过滤,使之符合质量要求,供碱熔岗位用。
4.4.2 操作指标
加料表(一次作业投入量)
β—萘磺酸钠悬浮液8000—85
00L
中控指标
名称指
标
冷却槽放料温度≤60℃
4.4.3 操作步骤
①调整冷却槽阀门, 开启搅拌,通知中和岗位进料后,打开冷却水阀及回水阀,开始冷却。
②物料冷至规定温度,停止冷却,开进泵冷却水,用泵将冷却槽物料进入预选准备好的β盐压滤机,但压滤机物料全部进满,未满要待下一锅冷却槽物料继续进料,直至压滤机料框全部进满物料,一锅冷却槽进完后要用β盐沉降池液冲洗冷却槽和进料管,冲洗结束关冷却槽底阀。进压结束关泵冷却水。
③β盐压滤机进满物料后,关进料阀门,开挤压泵,观察挤压
压力在0.4-0.8MPa,并在视镜里观察母液流出情况,大约挤压半
小时,待视镜中无大量母液流出,视为挤压完成,关挤压泵及阀
门,打开挤压回水阀门。
④开动β盐压滤机物料输送带,松开β盐压滤机,将压滤机内
的β盐卸至物料输送带,将物料送入β盐料仓。
⑤卸料结束后检查滤布,滤布滤水慢时应考虑清洗滤布,滤布
破损时要更换。在卸料过程中,要把滤板四周粘着的物料清理干
净。
⑥母液沉淀池中钠盐定期用泵打至冷却槽重新压滤。
4.5 蒸碱、碱熔、稀释(岗位编号:β-OH -05)
4.5.1 操作目的
将≥30%碱经蒸浓后压至碱熔锅与2-萘磺酸钠盐在高温条件下反应,生成2-萘酚钠盐和亚硫酸钠,经稀释后供酸化用。
4.5.2 操作指标
加料表(一次作业投入量)
序号名称原
料
体积(L)备注
1 碱熔90%浓缩
碱
450
β-钠盐2200~24
00Kg
一锅冷却的合格β-钠盐
2 稀释
洗水 3000~4000
碱熔物 1800~2000
中控指标
名称指标名称指标
游离碱 1~6%酚钠≥40%
亚硫酸钠28~38%维持温度325~345℃
4.5.3 操作步骤
4.5.3.1 开车前的准备工作
检查液碱贮罐是否有碱,输送泵能否正常运转。
②检查设备管道、阀门、阀件无滴漏、渗漏现象。碱熔锅底阀应检查是否漏
碱。
③蒸碱、碱熔锅内无积水、无杂物。
④仪表、电器设备、传动装置、加料器、引射泵、碱输送泵、碱雾系统保持正常使用要求。
⑤备齐岗位专用工具,备高温牛油3公斤以上。
4.5.3.2 蒸碱正常操作方法
①首次开车,开启液碱离心泵向液碱计量槽进碱至回流,停泵。
②调整计量槽放碱阀,分别向蒸碱锅锅内加2500~3500L液碱。
③通知司炉工点火,在4~6小时升温至260~280℃时,向锅内加细流液碱,控制230~300℃范围内,根据碱熔需求,调蒸碱速度。
④碱熔用碱时,由碱熔工用蒸汽引射泵打碱,连续用碱时应加大蒸碱速度,保持锅内有较大的体积,以利蒸碱。
⑤停蒸时间长,碱表面凝固时,蒸碱应小火,待表面熔化后在沸腾情况下可细流加入液碱。
⑥碱熔停工,蒸碱应继续加液碱,停火后碱不沸腾,降低碱液浓度而减少凝固,便于蒸碱恢复操作。
⑦蒸碱锅蒸碱时应严禁进水,防止冲料。
液体烧碱沸点与浓度关系对照表
浓度%60 7080 85.389.9 95.
2
99.5 100
沸点℃161 5 275310 314
4.5.3.3 碱熔操作法
①首次开车先加水洗锅,试搅拌及放料阀,升温预热锅体后放热水稀释锅。
②连续投料时,待放完上一锅物料后,等稀释工通知已关闭放料阀,方可进碱,体积达规定量,升温,开搅拌。
③升温至290℃以上,可试加第一批β-钠盐,观察物料反应情况,控制温度均匀上升,在300~340℃范围内,温差±10℃,每锅批次不少于10批。接近终点前要提前勤观察锅内物料反应情况,并提前1~2批停火,继续观察
至终点。
④停止加料后,关闭加料器,开蒸汽维持,根据温度情况也可加适量细流水,在325~345℃维持0:45~1:15,仍应观察物料变化并根据物料情况补加碱或钠盐,并适当延长维持时间。
⑤维持结束,停蒸汽,取样分析,通知稀释工放料,填写好记录。
⑥检查锅内料已放干净,待稀释工关闭锅底阀,用引射泵进碱。进碱结束放空引射泵余汽,打开放空阀防止堵管。
4.5.3.4 稀释正常操作法
①稀释锅进料前应加3000~4000L洗水或清水作为底水,然后打开放空管阀门,再关好人孔盖,接着装好放料接管,关闭稀释锅手孔,与碱熔联系,做好接料准备工作。
②开搅拌,带好面罩,缓慢开碱熔锅放料阀,将物料放入稀释锅内。放料速度不宜太快,防止物料及稀释蒸汽灼伤,终了可开大阀门放料。
③进完料关闭手孔,加水调整稀释物体积6500~7500L,调整阀门,通知酸化岗位准备出料。
④用压缩将物料出至酸化锅,出料前后,用蒸汽吹扫管道,料出完后缓慢放空余压。
⑤稀释物中有蒸馏进来的1.3镏份或稀释体积遇酸化对料等情况,必须在原始记录注明,便于酸化操作。
⑥如遇“三停”,根据“三停”时间安排停车。停电应通知司炉停火,加料未达到终点可根据加料及锅内物料反应情况,决定是否把物料留在锅内,如停电超过二小时,加料超过三分之二则可通知稀释工放料。如停汽可改用加水调节维持温度。
4.6 煮沸、压滤 (岗位编号:β-OH-06)
4.6.1 操作目的
完成酸化物料的后处理工作,得到合格的粗萘酚和亚硫酸钠溶液,供蒸馏与中和岗位用。
4.6.2操作指标
加料表(一次作业投入量)
序号工序原料名称体积(L)
酸化物 6500~7500
1 一煮沸
洗涤水 3000~3500
一煮沸后粗酚一锅
2二煮沸
二次洗涤水 3000
水 3000
3三煮沸
二煮沸后粗酚一锅
中间控制表
名称指标备注
亚硫酸钠浓度160~230克/升该指标仅供参查
(早班抽查)
亚钠中含粗酚量≤6克/升
4.6.3 操作步骤
4.6.3.1 一煮沸操作方法
①接到酸化通知问清物料情况,开进料阀向一煮锅进料。
②开搅拌酌情加水,从视镜中观察分层情况,粗酚应在最上层,如若分层不好应重新调比重,煮沸后静置直至分层良好。开蒸汽升温至沸腾,然后关闭蒸汽,停搅拌、静置15分钟以上。
③得到压滤工允许后,调整阀门,将合格的亚硫酸钠通过板式冷凝器及夹套管进冷却槽后压往压滤机过滤,从出料管视镜观察分层情况或从出料管旁路小阀放料观察,时间0:20~0:40。
④亚硫酸钠分层结束后,调整阀门,将上层粗酚压入二煮沸锅。
4.6.3.2二煮沸操作方法
①将三煮沸洗水全部压入二煮沸锅中,用蒸汽加热至沸腾。
②在搅拌下接受一煮沸来的粗萘酚,搅拌5~15分钟后停搅拌,静置15分钟让其分层。如分层不清应补加热水,重新搅拌、静置分层。
③将粗酚用压缩空气压入三煮沸锅,洗水压入一煮沸锅中。
4.6.3.3 三煮沸操作方法
①由热水罐向锅内加一定量的热水用蒸汽加热至沸腾。
②在开搅拌下进二煮沸一次作业量的粗萘酚后搅拌5~15分钟后,静置15分钟。
③静置后将粗萘酚压入干燥器,洗水压入二煮沸锅。
4.6.3.4 压滤操作方法
①将一煮沸一次作业亚硫酸钠溶液通过冷却槽冷却后进行压滤。
②滤液应不混浊,如滤液混浊应关机,重新洗机后再行压滤。
③压滤过程中应勤观察滤液情况,如若滤液混浊、流量小,可能是机内粗酚已满,应停止压滤,重新洗机。
④开小蒸汽洗机30~40分钟,压力不允许超过0.1MPa。
⑤洗机过程中,如滤液阀堵可以通通,并经常观察管道是否堵塞,防止压滤机带压损坏滤布。
⑥刚开始进压滤,流出的混浊液体不能流入受液槽中。
4.6.3.5 正常停工方法
①如遇“三停”根据时间,二、三煮沸锅内不宜存放粗酚。
②每次洗压滤机时,滤框中的粗萘酚必须洗干净,滤布必须检查,定期更换。
4.7 干燥、蒸馏(岗位编号:β-OH-07)
4.7.1 操作目的
将三煮沸后粗萘酚通过干燥、蒸馏精制成符合国家标准的2-萘酚工业产品。
4.7.2 操作指标
加料表(一次作业投入量)
序号设备原料名称浓度(%)体积(L)
1干燥器煮沸后粗
酚4000~4700
中控指标:干燥粗酚含量≥89%
4.7.3 操作步骤
4.7.3.1 粗酚干燥操作方法
①通知煮沸工进料,一般粗酚4000~4700L为一锅投入量,连续干燥至合格(约需3~4锅碱熔料)。
②每锅粗酚进料完毕,开启夹套导热油和水环真空泵阀门进行
脱水干燥,真空度一般控制为0.02~0.05MPa。
③粗酚干燥后水蒸汽经冷凝后积集在冷凝液贮罐中,将其升温沸腾后压往稀释锅套用。
④干燥器内温度升至120℃左右,停真空、取样分析合格,停干燥,将物料用压缩空气送至蒸馏锅内。
4.7.3.2蒸馏操作方法
①调整阀门,用压缩空气将干燥内的粗酚压入蒸馏锅内。
②进料完毕后,用蒸汽吹扫管道,通知司炉点火升温。
③通过1.3馏份受槽及真空捕集器,让蒸馏物料常压升温排水。
④当夹套金属浴温度达到220~270℃,液相温度180~205℃时,开真空泵,通过1.3馏份受槽抽真空,蒸一馏份。
⑤蒸一馏份时间20~40分钟,过后即可转二馏份。
⑥转二馏份后,蒸二馏份时,金属浴温250~285℃、液温
185~220℃、汽温180~230℃、真空度≥0.09MPa,时间3:00~
5:30,蒸出了全部二馏份。
⑦ 2.3馏份分割依据是:a.蒸出成品数量为投料量的90%以上;b.观察物料在视镜中颜色从无色透明转为浅棕色;c.锅内物料减少,视镜中流量少;d.液相温度上升5~10℃以上,流量减少。符合上述四条件即可转三馏份。
⑧三馏份时间约为1:00~1:45分,当锅内物料温度升到330~
360℃、汽相温度310~360℃、铅锑温度380~420℃、真空
≥0.09MPa,视镜中基本无流量,就可以认为此锅蒸馏结束。调整
阀门,用蒸汽将渣排至配油锅。
⑨在蒸馏锅排渣之前,用泵打入2000L蒽油,并打开搅拌。当蒸
馏需要排渣时,打开进料阀,废气阀。待排渣结束关进料阀,继续
搅拌。
一锅蒽油(2000L)配3锅渣。结束后,用压缩空气把锅内的
油压入配制油储罐中。
⑩蒸馏锅内残渣排不干净,需洗锅时,必须先用蒸汽降温,使导热油温度降至220℃以下,然后加液碱或清水洗锅。实在困难时采取扒渣。
⑾蒸馏途中如遇停电,关闭夹套冷却水和真空总阀,使锅内无真空,通过1.3馏份受槽,让其自然蒸馏。
4.7.3.3 切片操作方法
①开启除尘风机,调整放料夹套管和切片机料盘夹套保温。开动切片机,调整切片机旋塞,均匀将液体成品放入料盘中,调整转鼓冷却水,控制好切片速度和切片厚度。
②从转鼓表面刮下来的片状成品,采用内衬塑料袋的编织袋包装,袋口用塑料扎线打双结扎紧,防止散落及雨水浸入。
③一台切片机每小时可切850~900Kg。
④切片机刀片松动应及时紧固,否则转鼓表面料刮不干净,影响传热,导致物料不凝固而造成漫料。切片机漏出来的料,每班下班前应送入干燥重新回收。
⑤若2,3酸车间、2,6酸车间需要2-萘酚时还可以采取2-萘酚液体输送。
⑥乙萘酚切片的片子装于袋中,扎口叠堆,挂上标识牌。
⑦成品乙萘酚不可浸入雨水,在敞口散热时不可放于室外。叠堆后,雨天或夜里在室外堆放,要及时用蓬布盖起来;日班尽快同仓库联系,铲至仓库内存放。
5异常现象及处理的方法
5.1磺化异常现象及处理方法
异常现象可能原因处理办法