大型复杂不锈钢叶轮熔模_砂型复合铸造工艺_杨兵兵 (1)
大型水轮机叶片铸造工艺研究
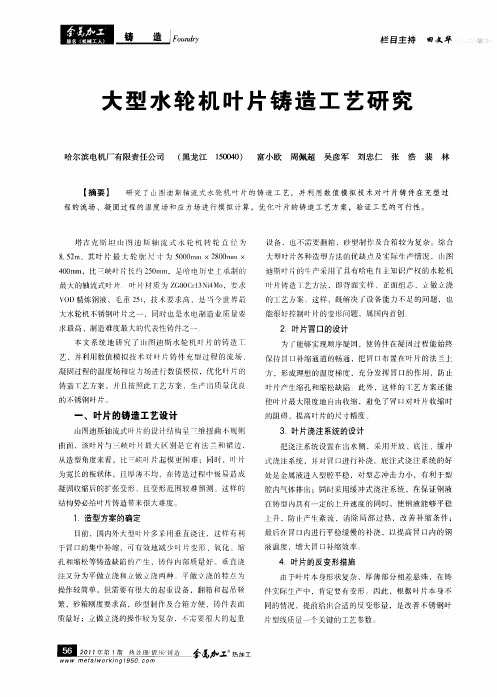
i
图 3 叶片凝 同结果 X射线 显示
三 、生产过程及结果
图 1 叶片铸造丁艺示 意
1 .生产过 程
水轮机叶片的生产 流程 如罔 4所示 ,铸 件及成品实
物 照 片 如 图 5、图 6所 示 。
繁 ,砂箱 刚度要求 高,砂型制作及合箱方便 ,铸件表 面 质量好;立做立浇的操作较为复杂 ,小需 要很火 的起重
同的情况 ,提 前给 合适 的反变形 量 ,是改善不锈钢 叶
片 型 线 质 量一 个关 键 的 工 艺 参数 .
盈 2 年第 1 _ 01 7 期 熟 处理/ 锋造 缎,
2 .叶片 冒 口的设 计
为 r能够实现顺序凝同 ,使铸 件在凝 过程能始终
保持 胃 口补 缩 通 道 的 畅通 ,把 胃 口布 置 在 叶 片 的法 兰 J -
艺 ,并利用数值模 拟技术 对叶片铸 件 危型过徉 的流场 、 凝固过程的温度场和应力场进 仃数值模拟 ,优 化叶片的
铸 造 T艺 方 案 , 且按 照此 T 方 案 .生 产 ¨质 星 良 ; 的不 锈 钢 叶 片 。
程 的流场 、凝 固过 程的温度场和 应力场进 行模拟 计算 ,优化 叶片 的铸造 工 艺方案 ,验 证工 艺的可行 性。
塔 吉 克 斯 坦 山 迪 斯 轴 流 式 水 轮 机 转 轮 径 为
设 备 ,也 不需 要 醐箱 ,砂 型 制 作 及 合 箱 较 为 复杂 。综 合
85 m,其叶 片最 大 轮 脚 尺 寸 为 5 0 m ×20 nn× .2 00 m 8 0n
上升 ,防 f产牛紊流 ,消除局部 过热 ,改 善补缩 条件 ; 最后存 胃1 3内进行平稳缓慢的补浇 ,以提高 冒口内的钢 液温度 ,增大 冒口补缩效率 .
casting1

1.5 m 不锈钢船用螺旋推进器
熔模铸造
熔模铸造
砂铸(形状复杂,铸件表面粗糙)
拉模铸造
第一节 合金的铸造性能
流动性和收缩性是合金的主要铸造工艺特性。 一、基本概念 ①合金—两种或两种以上的金属元素、或金属与非 金属元素(碳)熔和在一起,所构成具有 金属特性的物质。 特点:
[硬度、强度]合金 > [硬度、强度]纯金属
②充型— 液态合金填充铸型的过程。
二、液态合金的充型
1. 合金的流动性
熔融金属的流动能力。
衡量方法:
“螺旋形流动性试样”法。
螺旋形流动性试样示意图
液态合金的充型
影响流动性的因素:
①合金的种类和化学成分
不同种类的合金其流动性不同,同一种
类不同成分的合金其流动性也不相同。 流动性最好 灰口铸铁 → 硅黄铜 → 铝硅合金 最差 → 铸钢
合 金 收 缩 的 三 个 阶 段:
(1)液态收缩
合金从 T浇注→ T凝固开始 间的收缩。 (2)凝固收缩 合金从 T凝固开始→ T凝固终止 间的收缩。 (3)固态收缩(易产生铸造应力、变形、裂纹等。)
合金从 T凝固终止→ T室 间的收缩。
浇 注 温 度 (1) 凝 固 温 度 室 温
开始
凝固收缩
(2)浇注条件 a. 浇注温度(T) T 越高(有界限),充型能力越好。 b. 充型压力
流动方向上所受压力越大, 充型能力越好。 (3)铸件结构 结构越复杂,充型越困难。
三、铸件的凝固与收缩
1. 铸件的凝固及影响因素
(1)逐层凝固方式
特点:
① 铸件组织致密、紧实; ② 充型能力强,不易产生 铸造缺陷; ③ 流动性较好,铸件轮廓 清晰; ④ 断面固、液分界线清晰。
不锈钢压铸工艺流程

不锈钢压铸工艺流程
要想完成一件精密铸造产品所需的工序很复杂,首先制模+熔炼(温度1600°C) →浇注→振壳+切割(切割浇口)→粗磨(磨去浇口)→酸洗(目的:去除铸造氧化皮酸洗液:硝酸50%、氢氟酸50%温度: 50-60°C 时间20 30分钟冲洗水温:50°C) - +吊抛(目的:去除铸造表面氧
化皮合金钢丸:直径0.2-0.4mm 时间: 20-30分钟)精喷目的:局部小
孔抛光不方便的地方使用喷砂处理。
→固溶化的目的是获得单相奥氏体组织:工艺:加热温度到1080°C;时间:壁厚25mm/n;冷却:常温水。
时间: > 30s→吊抛的目的是去除热处理时产生的氧化皮合金钢丸:
直径0.2-0.4mm时间: 10-1 5分钟- +整形- +钝化目的是使不锈钢
表面生成保护膜酸洗液:酸洗液:硝酸50%、氢氟酸50%温度: 50-60°C 时间3-5分钟冲洗水温: 90°C →然后就不锈钢铸件的工序就完成了终检入库。
XX有限公司精密铸造、丕锈钢铸件、不锈钢铸造、硅溶胶精密
铸造为主,其产品包括缝制配件、纺织配件、门窗配件、家具配件、管件阀门、快速接头、船用五金、机械五金、五金工具等精铸件、产品广泛应用于机械、建筑、船舶、汽车、缝纫机、家居、医疗等领域。
熔模铸件生产工艺规程完整
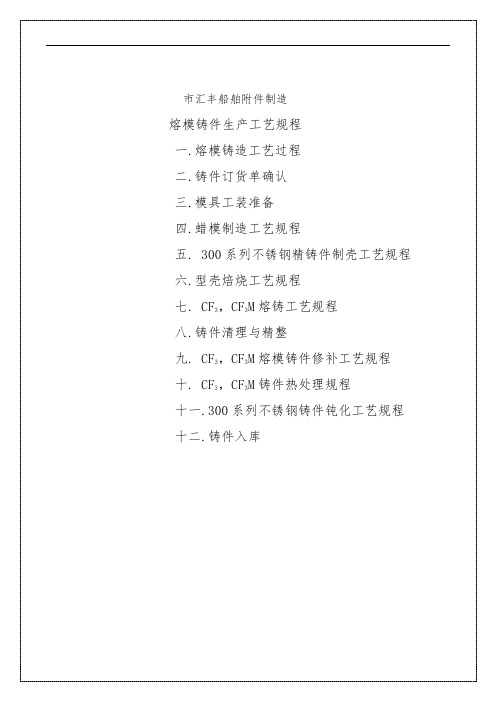
⑷浇注时钢水要对准浇口杯,既要快,又要稳,钢水浇至离浇口杯上部以下10mm即可,8大件铸件浇口杯浇浇后下沉后需要进行补浇,再后浇口杯上覆盖保温发热剂
⑸浇注后的模壳中铸件经冷却1小时后移出浇注场地准备下一炉的工作;
⑹做好过程记录。
(八).铸件清理与精整
⑴清砂、用震动脱壳机去除铸件表面型壳;
1室温度控制在15℃~30℃;
2焊接时,浇口棒下端流出15~20mm再焊接蜡形,上部蜡形距浇口杯顶端保持80mm~100mm。蜡形与蜡形之间间距15~30mm,视工件大小决定;
3焊接可用电烙铁,电炉加热焊刀等;
4焊刀温度不宜过高,一般为300℃左右;
5焊接时选用的浇口棒、冒口、浇口排列顺序均按焊接工艺卡执行;
⑻氩弧焊后进一步修磨,保证铸件表面无缺陷;
⑼经清理精整后逐只检收合格送下道热处理
(九).CF3,CF3M铸件热处理规程
1.恶劣工作条件用耐蚀铸钢的化学成分(%)[ASTM A744/A744M-2000]
钢号/元素
C≤
Si≤
Mn≤
P≤
S≤
Cr
Ni
Mo
相当于
CF3
0.03
2.0
1.5
0.04
0.04
17.0~21.0
6、成品的保管
经质检员按图纸要求检验合格的产品,又车间负责人填好入库单,入库单上必须写明产品的名称及数量交成品保管员,成品保管员接到入库单后必须认真负责进行清点核对,确认无误后才能入库、登帐,并放在指定位置,堆放整齐,不准乱堆。发货时,成品保管员要认真核对发货单位的产品名称、规格型号、发货数量,确认无误后才能发货并登帐。成品保管员每月要对库成品核对清查每个成品的库存量,并造册向厂部报告。
- 1、下载文档前请自行甄别文档内容的完整性,平台不提供额外的编辑、内容补充、找答案等附加服务。
- 2、"仅部分预览"的文档,不可在线预览部分如存在完整性等问题,可反馈申请退款(可完整预览的文档不适用该条件!)。
- 3、如文档侵犯您的权益,请联系客服反馈,我们会尽快为您处理(人工客服工作时间:9:00-18:30)。
收稿日期:2007-01-21; 修订日期:2007-01-23作者简介:杨兵兵(1967- ),陕西咸阳人,讲师.研究方向:精密铸造工艺.Email :yangbingbing661218@V ol.28N o.4A pr.2007铸造技术F O UN D RY T ECH NO LOG Y铸造技术 Foundry Technology大型复杂不锈钢叶轮熔模-砂型复合铸造工艺杨兵兵1,2,范志康1,陈淑惠2(1.西安理工大学材料科学与工程学院,陕西西安710048;2.陕西工业职业技术学院,陕西咸阳712000)摘要:研究了大型复杂不锈钢叶轮熔模-砂型复合铸造工艺。
借助设计的工装,利用熔模铸造涂制出复杂叶片部分的硅酸乙酯-水玻璃复合型壳;利用砂型造型得到简单轮毂轮辐及熔模型壳部分的铸型;将熔模型壳与水玻璃砂型组合后得到了该叶轮的熔模-砂型复合铸型;通过熔炼、浇注、切割、清理、热处理得到了ZG 1Cr18N i9T i 叶轮铸件。
结果表明:采用该复合工艺生产的叶轮铸件表面粗糙度达到Ra 3.2~1.6、尺寸精度达到CT 4~C T5、力学性能等都满足技术要求,且工艺稳定,生产成本低。
关键词:不锈钢叶轮;复合铸型;熔模铸造;砂型铸造中图分类号:TG269 文献标识码:A 文章编号:1000-8365(2007)04-0457-04Study on the Compound Precision Casting and Sand Casting Technologyof a Large Complicated Stainless Steel ImpellerYANG Bing -bing 1,2,FAN Zhi -kang 1,CHEN Su -hui 2(1.Institute of Materials Science and Engineering Xi ’an University of Technology ,Xi ’an 710048,China ;2.Shaanxi Polytechnic Institute ,Xianyang 712000,China )Abstra ct :The compou nd castin g techn ology of a large complicated stain less steel impeller was studied th rou gh precision castin g and sand castin g.Parts of complicated blade were made in to the silicon e -water glass composite shell by precision castin g ;simple h ubs an d spokes ,an d the precisionshell were m ade by san d castin g meth od ,then all of them were com bin ed together to obtain an impeller compo und mould with precision castin g shell an d sand mo uld.ZG1Cr18Ni9Ti impeller castin g is produ ced by melting ,pourin g ,cu ttin g an d heat treatment.The results show that the surface ro ughn ess and precision of the castin g can reach R a 3.2~1.6an d CT4~CT5respectively.Its mechanical properties can m eet the specification requirem en ts.The combined technolo gy is stable an d has low cost.Key words :Stainless steel impeller ;Compoun d mould ;Precesion casting ;Sand castin g 大型复杂不锈钢叶轮(见图1)是某进口制药设备上的关键、易耗铸件,工作环境处于强腐蚀性介质中,不仅结构复杂,叶片数量多,尺寸精度要求高,还需要进行超速(转速为额定转速的110%,持续2min )和动平衡检测,而且要求叶片表面光洁,任意3个相邻叶片外圆的两弦长之差不超过3m m ,叶片的扭曲角偏差在1°以内,不允许存在夹渣、疏松、气孔、裂纹等铸造缺陷,否则会出现断裂事故。
叶轮尺寸如图2所示,外径ø700m m 、高度130mm 、单件净重202kg ,辐板厚30m m 、轮辐部分为一较大的平面,叶片间距小,层层错叠,形状复杂,呈图1 大型复杂不锈钢叶轮Fig.1 L arg e -scale co mplex stainless steel impeller流线型,壁厚仅为5mm ,数量多达54个,给制模和造型都带来困难,目前,采用单一的熔模铸造、砂型铸造方法生产还存在着一定难度。
为了降低成本,实现叶轮铸件生产国产化,满足制药企业需要,有必要对其铸造工艺进行研究。
1 铸造方法选择一方面,由于该叶轮外径尺寸较大,且材质为457F O UN D RY T ECH NO LOG Y V ol.28N o.4A pr.2007图2 叶轮尺寸Fig.2 Dimension of impellerZG1Cr18Ni9Ti ,体收缩率较大,因而叶轮轮毂、轮辐部分的热节必须采用较大的冒口进行补缩。
另一方面,该叶轮不仅结构复杂,叶片数量多,间距小,而且对表面粗糙度、叶片位置、尺寸精度要求较高。
因此,生产小型复杂叶轮常用的熔模铸造,或者生产大型简单叶轮的组芯或抽芯砂型铸造的单一工艺方法,很难同时满足此类大型复杂叶轮内在质量、尺寸精度及表面质量的严格要求。
生产过程中,通过对此类叶轮铸件结构特点以及熔模铸造和砂型铸造工艺优缺点的分析,我们将此类叶轮由轮缘内侧(直径为ø416mm )划分为形状简单的轮毂轮辐部分和形状复杂的叶片部分。
对于形状复杂的叶片部分,采用熔模铸造涂制出叶片部分的型壳;对于形状简单的轮毂轮辐部分,通过砂型铸造方法造出相应部分的砂型,最后将熔模型壳与砂型组合,得到了满足技术要求的熔模-砂型复合铸型,解决了此类叶轮难于造型和不易补缩的难题。
2 工艺方案确定及浇冒口设计通过综合分析与工艺验证,实际生产中,选用了水平分型,轮缘设置3个补缩冒口、轮毂设置1个冒口代浇口的顶注式熔模-砂型复合铸造工艺方案,见图3。
图3 叶轮铸造工艺方案Fig.3 Casting scheme of impeller2.1 工艺方案确定由于选择了熔模-砂型复合造型,为了使模样制作简单、造型简便、降低对操作工人操作技艺的要求,确保合箱时模壳与铸型配合精确度,决定采用水平分型、两箱造型方案。
由于轮毂、轮缘与轮辐相交部分为热节,而轮辐部分厚度只有30mm ,先于热节部位凝固,补缩通道严重不足。
同时由于叶轮材质为ZG1Cr18Ni9Ti 奥氏体不锈钢,体收缩率大,该钢含C r 高,在浇注过程中易生成氧化铬夹杂物而使流动性降低,氧化铬膜还使铸件易产生冷隔和表面皱皮等缺陷,并且钢液温度越低、浇注时间越长,氧化现象越严重。
为了保证ZG1Cr18Ni9Ti 钢液的快速充型,有利于对热节的补缩,避免轮毂、轮缘热节处缩孔、缩松的产生,采用了轮缘部位设明顶冒口进行补缩,轮毂部位冒口代浇口的顶注工艺方案。
虽然顶注工艺易产生夹砂、气孔等缺陷,但考虑到叶轮高度仅为130mm ,飞溅较小,可通过选择合理的浇注方法、轮缘上安放冒口补缩带排气、叶片上型部位扎气眼、熔炼优质钢液等工艺措施克服该工艺的不足。
考虑到模壳与铸型的合型误差以及上型的浇冒口加工因素,叶轮上、下水平面加工余量分别取5mm 、3m m ,型芯单面加工余量取5mm 。
2.2 浇冒口设计轮毂部位选用标准腰圆型明冒口。
利用模数法计算得M 毂冒=2.48cm ,查标准腰圆型明冒口资料得:冒口宽度为120m m 、长度为180m m 、高度为150mm 。
冒口颈高度取20mm ,考虑到轮毂宽度,与轮毂接触处宽度取50mm 。
冒口重量约为25kg ,当ε=6%时,最大补缩铸件的体积V C =4.3×103cm 3。
经冒口补缩能力核算及补缩长度校核,仅需设置1个标准腰圆型明冒口。
轮缘部位同样选用标准腰圆型明冒口。
利用模数法计算得M 缘冒=2.27cm ,查标准腰圆型明冒口资料得:a =110mm ,b =165m m ,h =138m m (取150mm 与轮毂冒口高度相同)。
取冒口颈高度为20mm ,考虑到轮缘宽度,与轮缘接触处宽度取40m m 。
冒口重量为21kg ,当ε=6%时,最大能补缩铸件的体积V C =3.0×103cm 3。
经冒口补缩能力核算及补缩长度校核,需设置同样尺寸的3个标准腰圆型明冒口。
3 叶轮熔模-砂型复合造型3.1 叶轮叶片部分熔模型壳工艺3.1.1 熔模组焊由于叶轮有54个叶片,层层错叠的分布在ø700mm 的圆周上,故叶片间距很小,加上形状复杂,所以叶片部分的熔模型壳是铸造叶轮的关键。
模料选择具有良好综合性能的松香-蜡基模料,收缩率为0.75%,其热稳定性较高。
压型选用了45#钢,铸件的综合收缩率选取2.6%,型腔表面粗糙度为Ra 0.8~0.2,采用机械加工。
为了保证叶片部分熔模组焊尺寸的精确性以及涂料工序的正常进行,设计了如图4所示的组焊工装。
其由上盖板、下盖板、定位458《铸造技术》04/2007 杨兵兵等:大型复杂不锈钢叶轮熔模-砂型复合铸造工艺图4 叶轮组焊工装Fig.4 So lder mount technolog y o f impelle r圈、紧固轴4部分组成。
利用叶片上的圆弧与定位圈进行配合,并利用样板进行检验来确保叶片熔模的尺寸符合要求。
3.1.2 模壳涂料由于叶轮尺寸较大、形状复杂,尺寸精度、表面粗糙度技术要求高,为了确保叶片表面质量、模壳强度以及叶片模壳与砂型很好的接合并降低成本,采用了硅酸乙酯-水玻璃复合型壳,具体工艺参见参考文献[1]。
3.1.3 型壳的加固、脱蜡、焙烧叶片部分模壳涂制完成以后,由于叶片部分熔模型壳体积较大,如果立即卸去涂制工装,在搬运、脱蜡、焙烧过程中,会发生变形,严重时可导致模壳报废。