砂型铸造工艺设计概述
砂型铸造工艺与工装设计

铸造 工艺 图
在零件图上,用标准(JB2435-78)规 定的红、蓝色符号表示出;浇注位 置和分型பைடு நூலகம்,加工余量,铸造收缩 率(说明)。起模斜度,模样的反 变形量,分型负数,工艺补正量, 浇注系统和冒口,内外冷铁,铸肋, 砂芯形状,数量和芯头大小等
铸件 图
反映铸件实际形状、尺寸和技术 是铸件检验和验收、 要求。用标准规定符号和文字标注, 机械加工夹具设计 反映内容:加工余量,工艺余量, ⑦在完成铸造工艺图的基 的依据。 础上,画出铸件图 不铸出的孔槽,铸件尺寸公差,加 适用于成批、大量 工基准,铸件金属牌号,热处理规 生产或重要的铸件。 范,铸件验收技术条件等 表示出浇注位置,分型面、砂芯数 目,固定和下芯顺序,浇注系统、 冒口和冷铁布置,砂箱结构和尺寸 等 是生产准备、合箱、 检验、工艺调整的 依据。 ⑧通常在完成砂箱设计后 适用于成批、大量 画出 生产的重要件,单 件生产的重型件。 用于生产管理和经 济核算。依批量大 小,填写必要内容 ⑨综合整个设计内容
按 JB2435—78 《铸造工艺符号及其表示方法》 绘制
在确定了上述各项目后,编制铸造工艺卡。 其格式见 JB/Z 234.10—85《铸造工艺卡》。
铸造工装图
支架的铸造工艺设计过程
零 件 图
工 艺 图 芯 盒
模
样
铸 件
第二节 铸造工艺设计与经济指标 和环境保护的关系
铸造工艺设计时,采用不同的工艺, 对铸造 车间或工厂的金属成本,熔炼金属的质量,能量 消耗,铸件工艺出品率和成品率的优劣,工时费 用的大小,铸件成本和利润率的高低等,都有显 著的影响。
一. 概念 铸造工艺设计:就是根据铸造零件的特 点,技术要求,生产批量和生产条件等,确 定铸造方案和工艺参数,绘制工艺卡等技术 文件的过程。
砂型铸造及铸造工艺设计

砂型铸造及铸造工艺设计砂型铸造是一种常见的铸造工艺,它通过制作砂型并在其中注入熔化金属,使金属在砂型中凝固成型。
砂型铸造具有成本低、生产周期短、适用于各种金属材料等优点,因此在工业生产中得到广泛应用。
砂型铸造的工艺设计主要包括以下几个方面:模型制作、砂型制备、浇注系统设计、砂型充填与密实、凝固与固化、砂型剥离与修整等。
首先是模型制作。
模型是铸造过程中的主要参照物,它决定了最终铸件的形状和尺寸。
模型可以采用实物模型、木模、塑料模等材料制作。
在模型制作过程中,需要考虑到模型的缩短率,即模型尺寸与最终铸件尺寸之间的比例关系。
其次是砂型制备。
砂型是砂型铸造的核心部分,它承担着承载和固定熔化金属的功能。
砂型制备的关键在于砂型材料的选择和配比。
常用的砂型材料有硅砂、水玻璃、氯化钠等。
在制备砂型的过程中,需要考虑到砂型的强度、耐火性以及砂型表面的光洁度等因素。
浇注系统设计是保证铸件质量的重要环节。
浇注系统包括浇注口、浇注道和浇注杯等部分。
浇注系统的设计应考虑到金属液体的流动和凝固过程,以确保金属能够充分填充砂型,并且避免气体和杂质的混入。
砂型充填与密实是决定铸件质量的关键步骤。
在砂型充填过程中,需要确保熔化金属能够均匀地填充砂型,并且避免产生气孔和缩孔等缺陷。
砂型密实的方法包括振动、压实等。
振动可以提高砂型的密实度,压实则可以增加砂型的抗压强度。
凝固与固化是铸造过程中不可或缺的环节。
在凝固过程中,金属由液态逐渐转变为固态,并在这个过程中释放出大量的热量。
凝固过程的控制将直接影响到铸件的组织结构和性能。
固化过程的目的是使砂型的结构稳定,以便后续的剥离和修整。
最后是砂型剥离与修整。
在铸件凝固后,需要将砂型从铸件上剥离,并对铸件进行修整和清理。
砂型剥离的方法包括机械剥离、化学剥离等。
修整的目的是去除铸件上的毛刺、气孔等缺陷,使铸件达到设计要求的形状和尺寸。
总之,砂型铸造工艺设计的关键在于模型制作、砂型制备、浇注系统设计、砂型充填与密实、凝固与固化、砂型剥离与修整等方面的考虑。
砂型铸造
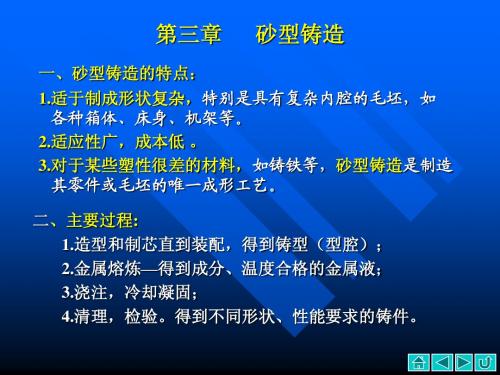
第四节
砂型铸造工艺设计举例
砂型铸造工艺设计内容: 铸件成形工艺分析; 选择铸件浇注位置和分型面; 确定工艺参数; 绘制铸造工艺图、铸件图。 一. 铸件成形工艺分析 ①依据给定零件图纸,了解铸件名称、使用功能、材料牌 号及技术要求; ②分析零件主要轮廓尺寸、壁厚大小及分布、主体结构及 形状复杂程度。
灰铸铁件 铸钢件
30~50 50
大量生产 成批生产 单件、小批生产
12~15 15~30 30~50
二.起模斜度
起模斜度-为便于起模,平 行起模方向的模样表面上所 增加的斜度。
三.收缩率 合金线收缩造成铸件各部分尺寸缩小。 为了保证铸件应有的尺寸,模样尺寸必须比铸件放大一个该 合金的收缩量。
四.型芯及芯头 型芯——形成铸造内腔或局部外型;
型芯设计主要包括型芯的划分和芯头的设计两部分。
依照型芯在铸型中的安放位置不同,常分为垂直型芯和水 平型芯两类。 L、H、S的值详见JB/T5106-1991标准。
五、浇注系统
组成: 浇口杯─接纳金属液;直浇道—其高度决定金属液 流入的静压力; 横浇道—引入金属液流,撇渣; 内浇道—引入金属液流,调节温度场分布; 浇注系统在工艺图上用红线表示。
上 2 下C 例:轴承座分型方案
Ø5 0
(一)工艺分析: 铸件为小型铸件,ø 50孔应铸出。 (二)方案分析:
下 1 200 B
方案1可用整模造型,但因A处凸 起,将阻碍起模,
方案2采用分模造型,取对称面为 上 分型面,B处阻碍起模, 3 方案3采用整模造型,型芯垂直设 下 置。图中C处将阻碍起模,但因C 处部分是一较小的局部,可采用活 A 块造型,
上
80
第三节
工艺参数的选择
砂型铸造工艺及工装设计

砂型铸造工艺及工装设计一、工艺流程设计砂型铸造的工艺流程设计是整个工艺的基础,包括以下步骤:设计铸造模具:根据产品需求和工艺要求,设计铸造模具的结构和尺寸。
制作砂型:根据模具和产品需求,制作符合要求的砂型。
浇注:将熔融的金属液体注入砂型,填充模具的型腔。
冷却:让金属液体冷却凝固,形成铸件。
脱模:将凝固的铸件从砂型中脱出,完成整个铸造过程。
二、铸造模具设计铸造模具的设计是整个工艺的核心,直接影响产品的质量和工艺的效率。
设计时需考虑以下几点:模具材料选择:根据产品需求和工艺要求,选择合适的模具材料。
模具结构确定:根据产品形状和尺寸,设计模具的结构和形状。
模具尺寸精度:根据产品要求和工艺条件,确定模具的尺寸精度。
浇口设计:浇口是金属液体注入模具的通道,设计时需考虑浇口的尺寸、位置和形式。
排气口设计:排气口是排除模具内的空气和挥发物的通道,设计时需考虑排气口的位置和大小。
三、砂型制作工艺设计砂型制作是整个工艺的重要环节,其质量直接影响产品的质量和工艺的效率。
设计时需考虑以下几点:砂型材料选择:选择符合要求的砂型材料,如黄沙、石英砂等。
砂型紧实度控制:控制砂型的紧实度,以保证砂型的强度和稳定性。
砂型透气性控制:控制砂型的透气性,以保证浇注过程中金属液体能够顺利填充模具的型腔。
砂型表面处理:对砂型的表面进行处理,以提高产品的表面质量。
四、浇注系统设计浇注系统是金属液体注入模具的通道,其设计直接影响到金属液体的流动和填充效果。
设计时需考虑以下几点:浇注系统结构形式:根据产品要求和工艺条件,选择合适的浇注系统结构形式。
浇注系统尺寸精度:根据产品要求和工艺条件,确定浇注系统的尺寸精度。
浇注速度控制:控制浇注速度,以保证金属液体能够平稳、充足地填充模具的型腔。
浇口位置选择:根据产品形状和模具结构,选择合适的浇口位置。
溢流槽设计:溢流槽是收集多余金属液体的结构,设计时需考虑溢流槽的位置和大小。
过滤网设置:过滤网是过滤金属液体中的杂质和气泡的结构,设计时需考虑过滤网的形式和材料。
砂型铸造工艺流程简介

砂型铸造工艺流程简介
砂型铸造工艺是一种广泛应用于金属加工领域的铸造工艺,其工艺流程一般包括以下几个步骤:
1. 设计和制作模具:根据产品的几何形状和尺寸要求,设计和制作相应的铸模,通常采用木模或金属模。
2. 准备砂型材料:将粘结剂、砂粒等材料混合均匀,形成砂型材料,通常采用粘土砂、树脂砂等。
3. 制作砂型:将砂型材料按照产品的形状和尺寸要求制作成铸型,通常采用手工或机械加工等方式。
4. 浇注和冷却:将熔融金属液体倒入砂型中,待冷却后取出铸件,然后进行后续加工处理。
5. 清理和修整:对铸件进行清理和修整,以去除表面的砂型残留物和毛边等,提高铸件的表面质量和精度。
6. 后处理:对铸件进行必要的后处理,如热处理、表面处理等,以满足后续使用要求。
需要注意的是,不同的产品和工艺要求可能会有所不同,因此在实际应用中,还需要根据具体情况进行调整和优化。
砂型铸造工艺具有生产效率高、成本低等优点,被广泛应用于机械、汽车、航空航天、电子等领域。
砂型铸造工艺与工装设计

详细描述
针对大型船用柴油机缸盖的工装设计,采用了高强度和刚性的材料,确保了工装的稳定性和精度。同 时,加强筋和支撑结构的设计提高了工装的耐久性和使用寿命,减少了维修和更换的频率。
实例四:复杂阀体的工装设计
总结词
结构紧凑、定位准确、操作简便
VS
详细描述
复杂阀体的工装设计采用了紧凑的结构布 局,减少了占地面积和制造成本。准确定 位和夹紧系统保证了阀体的加工精度和一 致性,提高了产品质量。同时,人性化的 操作界面和便捷的调整方式使得操作过程 简单易懂,降低了操作难度和培训成本。
砂型铸造工艺的应用范围
机械制造
砂型铸造广泛应用于机械制造领域,如汽车、船舶、 航空航天等。
农业机械
在农业机械领域,砂型铸造工艺用于生产各种农机具 和零部件。
五金工具
五金工具制造中,砂型铸造工艺用于生产各种刀具、 量具等。
砂型铸造工艺的历史与发展
历史
砂型铸造工艺起源于古代中国,随着技术的发展和进步,逐渐传播到世界各地 。
发展
现代砂型铸造工艺不断改进和创新,采用新型材料和工艺技术,提高了铸件质 量和生产效率。
02
CATALOGUE
砂型铸造工装设计基础
砂型铸造工装设计的原则
功能性原则
工装设计应满足铸造生产的功 能需求,确保能够实现预定的
铸造工艺过程。
标准化原则
工装设计应遵循标准化原则, 尽量采用标准化的零部件和材 料,以提高互换性和降低成本 。
实例二:汽车发动机缸体的工装设计
总结词
模块化、柔性、高精度
详细描述
汽车发动机缸体的工装设计采用了模块化结构,便于后期维护和升级。同时,柔性化的设计使得工装能够适应不 同型号的缸体生产,提高了设备的利用率。高精度的定位和测量系统确保了缸体的加工精度和产品质量。
砂型铸造的造型工艺
浇注系统的计算与选择
计算浇注系统的流量和压力 选择合适的浇注系统类型 考虑浇注系统的尺寸和布局
计算浇注系统的冷却时间和冷却速度 考虑浇注系统的安全性和可靠性 计算浇注系统的成本和效率
砂型铸造的常见 缺陷及防止措施
气孔的产生及防止措施
气孔产生的原因:砂型铸造过程中由于气体的侵入导致铸件内部形成气孔 防止措施:在铸造过程中采用真空铸造技术减少气体的侵入 防止措施:在铸造过程中采用压力铸造技术提高铸件的致密度 防止措施:在铸造过程中采用热处理技术消除铸件内部的气孔
陶瓷型铸造:使用陶瓷型作为造型材 料具有耐高温、耐磨损等优点
塑料型铸造:使用塑料型作为造型材 料具有重量轻、易于加工等优点
金属型铸造:使用金属型作为造型材 料具有强度高、耐磨损等优点
复合型铸造:使用多种材料复合作为 造型材料具有综合性能优良等优点
造型材料的选择
石英砂:具有较高的耐火性 和稳定性适用于高温铸造
砂型铸造常用的造型材料有: 石英砂、粘土、水玻璃等
粘土:具有良好的可塑性和 粘结性适用于复杂形状的铸
造
水玻璃:具有较好的流动性 和粘结性适用于大型铸造件
的制造
造型材料的制备
原材料选择:选择合适的砂、粘结剂、附加剂等 混合搅拌:将原材料混合均匀形成砂型铸造所需的造型材料 造型材料性能测试:测试材料的流动性、强度、透气性等性能指标 造型材料储存:将制备好的造型材料储存在适宜的环境中以保持其性能稳定
感谢您的观看
汇报人:
模型制作包括手工制作、机 械制作、3D打印等方法
模型修整包括打磨、切割、 焊接等操作
模样制作是砂型铸造造型工 艺中的重要环节
模型检验包括尺寸检验、表 面质量检验、结构检验等
砂箱准备
砂型铸造及铸造工艺设计
砂型铸造及铸造工艺设计砂型铸造是一种常用的铸造工艺,通过在砂型中,将液态金属倒入砂型中,待金属凝固后,即可获得所需铸件。
砂型铸造工艺设计是指在进行砂型铸造时,根据铸件的形状、尺寸和要求,设计出适合的砂型铸造工艺流程,确保铸件质量和生产效率。
砂型铸造工艺设计的具体步骤如下:第一步,确定铸件的形状和尺寸。
根据铸件的图纸和要求,确定铸件的形状和尺寸。
铸件的形状和尺寸直接影响到砂型的设计和制造,因此在确定铸件形状和尺寸时,需要考虑到铸件的可铸性和制造工艺。
第二步,选择适当的砂型材料。
常用的砂型材料有石英砂、石膏砂、黏土砂等。
选择适当的砂型材料需要考虑到砂型的耐火性、流动性和可塑性等方面的要求。
第三步,设计砂型结构。
根据铸件的形状和尺寸,设计出适合的砂型结构。
砂型结构包括上下模板、芯子和样板等。
上下模板用于固定砂型,芯子用于制造中空铸件,样板用于制造固定模板。
砂型结构的设计需要保证砂型的密实性和刚度,以确保铸件的精度和强度。
第四步,制造砂型。
根据砂型结构的设计,制造适合的砂型。
制造砂型的过程包括准备砂型材料、混合砂型材料、充填砂型、震动砂型、刮平砂型等。
制造砂型时需要注意砂型的密实性和表面平整度,以确保铸件的质量。
第五步,准备铸造设备和材料。
在进行砂型铸造之前,需要准备好铸造设备和材料。
铸造设备包括炉子、浇注设备、除渣设备等。
铸造材料包括金属液体和砂型材料。
第六步,进行砂型铸造。
在准备好铸造设备和材料之后,进行砂型铸造。
砂型铸造的过程包括熔炼金属、倒入砂型、待金属凝固、冷却铸件、取出铸件等。
在进行砂型铸造时,需要控制铸造温度、倒铸速度和铸造压力,以确保铸件的质量。
第七步,进行铸件的后处理。
在进行砂型铸造之后,需要对铸件进行后处理,包括去除砂型、修整表面、热处理等。
后处理的目的是提高铸件的机械性能和表面质量。
砂型铸造工艺设计需要综合考虑铸件的形状、尺寸和要求,选择适当的砂型材料和制造过程,并进行铸造和后处理。
砂型铸造工艺设计概述
铸造工艺图实例2
作业:P80 (1) 补充作业:定性画出图示支座的铸造工艺
图、模型图及铸件图
材料:灰铁 铸造工艺:砂型铸造 生产量:单件小批
(1)外浇口
其作用是容纳注入的金属液并缓解液态金属对砂型的冲击。 小型铸件通常为漏斗状(称浇口杯),较大型铸件为盆状(称 浇口盆)。
(2)直浇道
是连接外浇口与横浇道的垂直通道,改变直浇道的高度可以 改变型腔内金属液的静压力从而改善液态金属的充型能力。
(3)横浇道
横浇道是将直浇道的金属液引入内浇道的水平通道,一般 开在砂型的分型面上。横浇道的主要作用是分配金属液入内 浇道和隔渣。
四、收缩率
铸件由于凝固、冷却后的体积收缩,其各部分尺寸均小 于模样尺寸。为保证铸件尺寸要求,需在模样(芯盒)上加大 一个收缩的尺寸。加大的这部分尺寸称收缩量,一般根据铸 造收缩率来定。铸造收缩率定义如下:
K=[(L模-L件)/L件]×100% 式中: K为铸造收缩率;L模为模样尺寸;L件为铸件尺寸。
铸造收缩率主要取决于合金的种类,同时与铸件的结构 、大小、壁厚及收缩时受阻碍情况有关。对于一些要求较高 的铸件,如果收缩率选择不当,将影响铸件尺寸精度,使某 些部位偏移,影响切削加工和装配。
通常灰铸铁为0.7~1.0%,铸造碳钢为1.3~2.0%,铝硅
合金为0.8~1.2%,锡青铜为1.2~1.4%。
四、铸造工艺方案
概括说明铸造生产的基本过程和方法的工艺 文献,包括造型和造芯方法、铸型种类、浇注位 置和分型面的确定等。
第一节 浇注位置与分型面的选择
浇注位置:浇注时铸件在砂型中所处的空间位置。 分型面:铸型组元间的结合面
一、浇注位置的选择原则
原则:主要考虑铸件质量 1.铸件的重要加工面或主要工作面应朝下或位于侧面
2.4砂型铸造
参见表2-12
有色金属:表面光洁,加工余量少。
生产批量 大批量生产,机器造型
单件、小批生产,手工造型
最小铸出孔直径 铸铁件 铸钢件
Ф 15~30
<Ф25 <Ф35
3.工艺参数的选择
2)起模斜度 :便于模样从砂型中取出。
取决于起模高度、造型方法、模样材料、等。
机器造型比手工造型斜度小; 木模比金属模斜度大; 立壁越高,斜度越小; 内斜度比外斜度大。
造型材料应具备以下性能:
可塑性:砂和芯砂在外力作用下要易于成形。 足够的强度:型砂和芯砂在外力作用下要不易破坏。 耐火性:型砂和芯砂在高温下要不易软化、烧结、粘附。 透气性:型砂和芯砂紧实后要易于通气。
退让性:型砂和芯砂在冷却时其体积可以被压缩。
2)造型方法
用造型混合料及模样等工艺装备制造铸型的过程称为造型,是 砂型铸造的最基本工序。
单面模板
是模板底面一面有模样的模板。 上模板→上型
下模板→下型
合型两块模板。用两台造型机。
(a)铸件
(b)上模板(有浇注系统)
(c)下模板
特点:结构简单,应用较多。
双面模板
上半个模样和浇注系统固定在模底板一侧,下半个模样固定在该 模底板另一侧对应位臵,在同一台造型机上造出上、下型。
双面模板
造下型 1-模底板;
2.铸型分型面的选择 4.铸造工艺图的绘制
作用:制模(模样、 芯盒)、造型(芯)、 准备生产设备、铸件 检验的依据。
定义:在零件图上用各 种工艺符号及参数表示 出铸造工艺方案的图形。
1. 浇注位置的选择
① 铸件重要加工面、主要工作面、大平面、基准面应朝下 (或侧面), 以防产生气孔等,使其组织致密、质量好。
- 1、下载文档前请自行甄别文档内容的完整性,平台不提供额外的编辑、内容补充、找答案等附加服务。
- 2、"仅部分预览"的文档,不可在线预览部分如存在完整性等问题,可反馈申请退款(可完整预览的文档不适用该条件!)。
- 3、如文档侵犯您的权益,请联系客服反馈,我们会尽快为您处理(人工客服工作时间:9:00-18:30)。
这些技术文件必须结合工厂的具体条件,是 在总结先进经验的基础上,以图形、文字和表格 的形式对铸件的生产工艺过程加以科学地规定。 它是生产的直接指导性文件,也是技术准备和生 产管理、制定进度计划的依据。
大量生产,上限用于单件小批生产
生产批量
大量生产 成批生产 单件、小批生产
最小铸孔
最小铸出孔直径
灰口铸铁件
12~15 15~30 30~50
铸钢件
- 30~50
50
注:对于零件上不要求加工的孔槽,无论大小均应铸出
二、起模斜度 为了起模方便又不损坏砂型,凡垂直于分型面的壁上须 留有斜度。
起模斜度的形式
三、铸造圆角
铸件上相邻两壁之间的交角,应做出 铸造圆角,防止在尖角处产生冲砂及裂纹 等缺陷。圆角半径一般为相交两壁平均厚 度的1/3~1/2
四、收缩率
铸件由于凝固、冷却后的体积收缩,其各部分尺寸均小 于模样尺寸。为保证铸件尺寸要求,需在模样(芯盒)上加大 一个收缩的尺寸。加大的这部分尺寸称收缩量,一般根据铸 造收缩率来定。铸造收缩率定义如下:
500~800
顶面 5.0~7.0 底、侧面 4.0~5.0
800~1250
顶面 底、侧面
6.0~7.0 4.0~5.5
50~120
4.0~4.5 3.0~3.5
4.5~5.0 3.5~4.0
5.0~6.0 4.0~4.5
6.0~7.0 4.5~5.0
6.5~7.5 5.0~5.5
加工面与基准面的距离(mm) 120~260 260~500 500~800
对于要求比较高的单件生产的重要铸件和大量生产的铸件,除要 详细绘制铸造工艺图,填写工艺卡以外,还应绘制铸件图、铸型装配 图以及大量的工装图,如模样图、模板图、砂箱图、芯合图、下芯夹 具图,检验样板及量具图等。
三、铸造工艺设计的一般步骤
1.对零件图纸进行审核和进行铸造工艺性分析 2.选择铸造方法 3.确定铸造工艺方案 4.绘制铸造工艺图 5.绘制铸件图 6.填写铸造工艺卡和绘制铸型装配图 7.绘制各种铸造工艺装备图纸
上
下
上
②
下
①
第二节 铸造工艺参数的确定
一、机械加工余量和最小铸孔
灰铸铁的机械加工余量
铸件最大 尺寸 (㎜)
浇注时 位置
<50
<120
顶面 3.5~4.5 底、侧面 2.5~3.5
120~260
顶面 4.0~5.0 底、侧面 3.0~4.0
260~500
顶面 4.5~6.0 底、侧面 3.5~4.5
K=[(L模-L件)/L件]×100% 式中: K为铸造收缩率;L模为模样尺寸;L件为铸件尺寸。
铸造收缩率主要取决于合金的种类,同时与铸件的结构、 大小、壁厚及收缩时受阻碍情况有关。对于一些要求较高的 铸件,如果收缩率选择不当,将影响铸件尺寸精度,使某些 部位偏移,影响切削加工和装配。
通常灰铸铁为0.7~1.0%,铸造碳钢为1.3~2.0%,铝硅
铸造工艺设计包括以下几种主要技术文件:
1.铸造工艺图
5.模样图
2.铸造工艺卡
6.芯合图
3.铸型装配图
7.砂箱图
4.铸件图
8.模板图
由于每个铸件的生产任务和要求不同,生产条件不同,因此,铸
造工艺设计的内容也不同。
对于不太重要的单件小批量生产的铸件,铸造工艺设计比较简单。 一般选用手工造型,只限于绘制铸造工艺图和填写有关工艺卡,即可 投入生产
3. 铸件大面积的薄壁部分放在铸型的下部或垂直、倾斜。 原因:这样能增加薄壁处金属液的压强,提高金属液
的流动性,防止薄壁部分产生浇不足或冷隔缺陷。
4.易产生缩孔的构件,应使厚截面位于分型面附近的上部或侧面
原因:便于安放冒口,实现定向凝固,进行补缩。
二、铸型分型面的选择 原则:在保证质量的前提下,尽量简化工艺
5.0~5.5 4.0~4.5
6.0~7.0 4.5~5.0
6.5~7.0 4.5~5.5
7.0~8.0 5.0~6.0
6.5~7.0 5.0~6.0
7.0~8.0 5.0~6.0
7.5~8.0 5.5~6.0
7.5~9.0 6.5~7.0
8.0~9.0 5.5~7.0
800~1250
8.5~10 6.5~7.5
1.分型面应设在铸件最大截面处,以保证模样从型腔中顺利取出
2.应使造型工艺简化 ★应尽量使分型面平直,以简化模具制造及造型工艺,避免挖砂造型
★尽可能减少铸件的分型面,尽量做到只有一个分型面
★应使型芯和活块数量尽量减少。
3.应使铸件全部或大部放在同一砂箱。
4.应尽量使型腔及主要型芯位于下型,以便于造型、下芯、 合型及检验。
第四章 砂型铸造工艺
教学目的
1.了解砂型铸造工艺设计有关知识。 2.掌握浇注位置、分型面选择;铸造工艺参数确定;型
芯设计;浇冒系统等有关知识。 3.学会绘制简单铸件的铸造工艺图。
教学重点
1.浇注位置、分型面选择。 2.铸造工艺参数确定。
教学难点: 型芯及浇冒系统设计 计划学时:1学时
概述
一、铸造工艺设计的概念
合金为0.8~1.2%,锡青铜为1.2~1.4%。
第三节 砂芯设计
一、型芯的作用 形成铸件的内腔、孔洞和形状复杂阻碍起 模部分的外形。
二.型芯的数量及分块 ★型芯的数量取决于铸件的形状 ★大型复杂型芯根据需要分块制作
三.型芯的形式 常用的型芯有水平型芯、垂直型芯、
四、铸造工艺方案
概括说明铸造生产的基本过程和方法的工艺 文献,包括造型和造芯方法、铸型种类、浇注位 置和分型面的确定等。
第一节 浇注位置与分型面的选择
浇注位置:浇注时铸件在砂型中所处的空间位置。 分型面:铸型组元间的结合面
一、浇注位置的选择原则
原则:主要考虑铸件质量 1.铸件的重要加工面或主要工作面应朝下或位于侧面
原因:铸件的上表面容易产生砂眼、气孔、夹渣等 缺陷,组织也不如下表面致密。
2.铸件的大平面尽可能朝下或采用倾斜浇注
原因:铸型的上表面除了容易产生砂眼、气孔、 夹渣外,大平面还极易产生夹砂缺陷。这是由于在 浇注过程中,高温的液态金属对型腔上表面有强烈 的热辐射,型砂因急剧膨胀和强度下降而拱起或开 裂。拱起处或裂口浸入金属液中,形成夹砂缺陷。 同时铸件的大平面朝下,也有利于排气,减小金属 液对铸型的冲刷力。