第四章砂型铸造工艺设计(1)
砂型铸造工艺设计共36页文档

46、我们若已接受最坏的,就再没有什么损失。——卡耐基 47、书到用时方恨少、事非经过不知难。——陆游 48、书籍把我们引入最美好的社会,使我们认识各个时代的伟大智者。——史美尔斯 49、熟读唐诗三百首,不会作诗也会吟。——孙洙 50、谁和我一样用功,谁就会和我一样成功。——战斗,就像为 了城墙 而战斗 一样。 ——赫 拉克利 特 17、人类对于不公正的行为加以指责 ,并非 因为他 们愿意 做出这 种行为 ,而是 惟恐自 己会成 为这种 行为的 牺牲者 。—— 柏拉图 18、制定法律法令,就是为了不让强 者做什 么事都 横行霸 道。— —奥维 德 19、法律是社会的习惯和思想的结晶 。—— 托·伍·威尔逊 20、人们嘴上挂着的法律,其真实含 义是财 富。— —爱献 生
铸造工艺设计概论
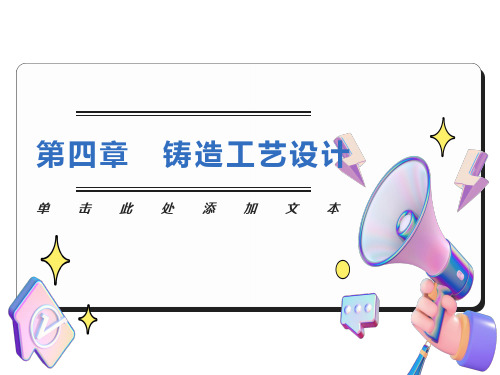
对于粗而矮的砂芯,常可不用上芯头,这可使造型、合箱方便
02
对于等截面的或上下对称的砂芯,为下芯方便,上下芯头可用相同的高度合斜度。
03
决定芯头高度有以下几点值得注意:
芯头斜度 对垂直芯头,上下芯头都应设有斜度。
芯头间隙
压环、防压环和积砂槽
(二)芯头承压面积计算 芯头的承压面积应足够大,以保证在金属液最大浮力的作用下不超过铸型的许用压应力。 由于砂芯的强度通常都大于铸型的强度,故只核算铸型的许用压力即可。 芯头的承压面积S应满足下式
对于大平板类铸件,可采用倾斜浇注,以便增大金属液上升速度。
H值=200-400毫米
应保证铸件能充满
具有大面积的薄壁铸件,应将薄壁部分放在铸型的下部,同时要尽量使薄壁部分处于垂直位置或倾斜位置。见图3-2-23。
应有利于铸件的补缩 对于易产生收缩缺陷的铸件因优先考虑实现顺序凝固的条件
避免用吊砂、吊芯或悬臂式砂芯,便于下芯合箱及检查
02
注意减轻铸件清理和机械加工量
01
为什么要设分型面?怎样选择分型面
02
浇注位置的选择或确定为何受到铸造工艺人员的重视?应遵循哪些原则?
03
怎样审查铸造零件图样?其意义何在?
思考题
砂芯的功用是形成铸件的内腔、孔和铸件外形不能出砂的部位,砂型局部要求特殊性能的部分,有时也用砂芯。
砂芯应满足以下要求:砂芯的形状、尺寸以及在砂型中的位置应符合铸件要求,具有足够的强度和刚度,在铸件形成过程中砂芯所产生的气体能及时排除型外,铸件收缩时阻力小和容易清砂
砂芯形状适应造型、制芯方法
高速造型线限制下芯时间,常把若干个小砂芯组合成一个砂芯,以便节约下芯时间。
芯头:是指深出铸件以外不与金属液接触的砂芯部分。
金属工艺学第五版课后习题解答修图版

铸造:第四章 砂型铸件的结构设计
2.什么是铸件的结构斜度?它与起模斜度有何不同? 图示铸件的结构是否合理?应如何改正? p81
在零件设计中所确定的非加 工表面斜度为结构斜度。而 在绘制铸造工艺图中加在垂 直分型面的侧面所具有的斜 度称为起模斜度,以使工艺 简化和保证铸件质量。
铸造:第四章 砂型铸件的结构设计
6.为什么铸件要有结构圆角?图示铸件上哪些圆角不 够合理?应如何修改? p81
铸造:第四章 砂型铸件的结构设计
7.下图所示的支架件在大批量生产中该如何改进其设 计才能使铸造工艺得以简化? p81
尽量避免铸件起模方 向存有外部侧凹,以 便于起模。
铸造:第四章 砂型铸件的结构设计
p73
I方案存在错箱可能。 该零件不算太高,故 方案II稍好,从冒口
II
安放来看,II方案容 易安放。
I
铸造:第三章 砂型铸造
5.图示铸件在单件生产条件下该选用哪种造型方法?
方案I: 分型面为
大截面处,且为平面,
方案可行。
铸造:第三章 砂型铸造
5.图示铸件在单件生产条件下该选用哪种造型方法?
4 确定焊缝位置,选择焊接方法,制定 装配焊接次序。
筋 板
5000
600
6
10
3600
上翼板 300
腹板 8 800
下翼板
焊接:第四章 焊接结构设计
4 确定焊缝位置,选择焊接方法,制定装配焊接次序。
焊接方法: 手工电弧焊、二氧化碳气体保护焊
试制样机时该连杆宜采用砂型铸造方法p93当年产量为1万件时宜采用金属型铸造方法当年产量超过10万件时宜采用压力铸造方法
砂型铸造工艺设计..
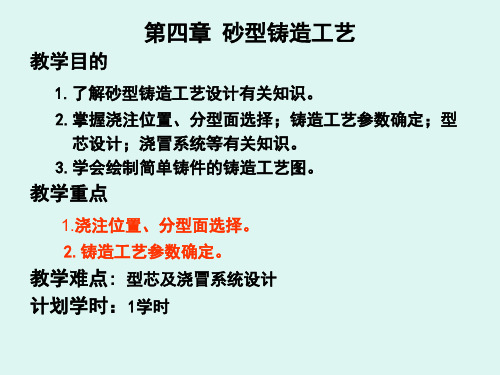
(3)中间注入式浇注系统
62
中注式浇注系统
这是一种介于顶注和底注之间的注 入方法,既降低了液流落下的高度,又 使温度的分布较为均匀,内浇道处在分 型面上,便于开设和选择部位。因此, 这种浇注系统的应用很广。
63
(4)阶梯注入式浇注系统
阶梯注入式浇注系统
阶梯注入式浇注系统亦称阶梯式浇注 系统,是在铸件高度上设二层或二层以 上的内浇道,它兼备了顶注式、底注式 和中间注入式浇注系统的优点。
对于要求比较高的单件生产的重要铸件和大量生产的铸件,除要 详细绘制铸造工艺图,填写工艺卡以外,还应绘制铸件图、铸型装配 图以及大量的工装图,如模样图、模板图、砂箱图、芯合图、下芯夹 具图,检验样板及量具图等。
三、铸造工艺设计的一般步骤
1.对零件图纸进行审核和进行铸造工艺性分析 2.选择铸造方法 3.确定铸造工艺方案 4.绘制铸造工艺图 5.绘制铸件图 6.填写铸造工艺卡和绘制铸型装配图 7.绘制各种铸造工艺装备图纸
1.分型面应设在铸件最大截面处,以保证模样从型腔中顺利取出
2.应使造型工艺简化 ★应尽量使分型面平直,以简化模具制造及造型工艺,避免挖砂造型
★尽可能减少铸件的分型面,尽量做到只有一个分型面
★应使型芯和活块数量尽量减少。
3.应使铸件全部或大部放在同一砂箱。
4.应尽量使型腔及主要型芯位于下型,以便于造型、下芯、 合型及检验。
<50 3.5~4.5 2.5~3.5 4.0~5.0 3.0~4.0 4.5~6.0 3.5~4.5 5.0~7.0 4.0~5.0 6.0~7.0 4.0~5.5 50~120 4.0~4.5 3.0~3.5 4.5~5.0 3.5~4.0 5.0~6.0 4.0~4.5 6.0~7.0 4.5~5.0 6.5~7.5 5.0~5.5 5.0~5.5 4.0~4.5 6.0~7.0 4.5~5.0 6.5~7.0 4.5~5.5 7.0~8.0 5.0~6.0 6.5~7.0 5.0~6.0 7.0~8.0 5.0~6.0 7.5~8.0 5.5~6.0 7.5~9.0 6.5~7.0 8.0~9.0 5.5~7.0 8.5~10 6.5~7.5 120~260 260~500 500~800 800~1250ຫໍສະໝຸດ 60顶注式浇注系统
砂型铸造工艺设计

2020年7月22日星期三
2-6 砂型铸造工艺设计基础
确定铸件的分型方案
•分型面的选择是在确定浇注位置之后进行的。应当 根据一定的基本原则来确定合理的分型方案
分型面应当尽量少 分型面应当尽量采用平直分型面 分型面应当取在铸件的最大截面处,并使模型的高度不致过高 ,以便于取模 铸件的全部或大部应当位于同一砂箱,加工面与加工基准面应 当位于同一砂箱 尽量减少活块及型芯的数目,以简化造型、制模、合箱的工序
2020年7月22日星期三
2-6 砂型铸造工艺设计基础
2020年7月22日星期三
2-6 砂型铸造工艺设计基础
铸造工艺设计的基本方法
铸造工艺设计有两大基本任务
1.根据零件图绘制铸造工艺图 • 确定铸件的浇注位置 • 确定铸件的分型方案 • 选择相应的造型方法 • 绘制铸造工艺图
2.根据铸造工艺图设计铸件图、模型图、芯盒图、合箱图
2020年7月22日星期三
2020年7月22日星期三
2-6 砂型铸造工艺设计基础
绘制芯盒图
•芯盒图是制造型芯盒的依据,在芯盒图上 同样要考虑线收缩量、拔模斜度、铸造圆 角、活块设置以及型芯头的设置。
2020年7月22日星期三
2-6 砂型铸造工艺设计基础
绘制合箱图(砂型装配图)
•在合箱图上标示浇注系统,包括浇注系统的 结构形式、浇注系统引入铸件的位置、冒口 的位置和形式、冷铁的设置位置和形式以及 型芯的位置、设置方式和通气方式等。
2020年7月22日星期三
2-6 砂型铸造工艺设计基础
铸造工艺设计的内容
•铸造工艺设计的先期工作时审查无误的、 结构设计合理的零件图。 •铸造工艺设计的内容
用不同的颜色、各种工艺符号及相应的数据,将铸造 工艺设计的各项内容描绘到零件图上,从而将零件图 制成铸造工艺图。铸造工艺图是绘制模型图、芯盒图 、合箱图、铸件图及编制铸造工艺卡片的主要依据。
1砂型铸造PPT课件

案
上 不合理
下
上 合理
下
4
确定分型面
★ 分型面应避免曲折,数量应少,最好是一个,且为平面
不合理
合理
5
确定分型面
★ 分型面应避免曲折, 数量应少,最好是一个, 且为平面
√
6
确定分型面
★ 应尽量使型腔全
部或大部分置于同一 个砂型内,最好使型 腔或使加工面与基准 面位于下型中。
不合理
合理
7
确定分型面
铸件位置选择
★ 铸件的重要工作面或主要 加工面应朝下或呈侧立状态
27
绘制铸件工艺图 铸件位置选择
★ 铸件上
的大平面结 构或薄壁结 构应朝下或 呈侧立状态
不合理
合理
28
绘制铸件工艺图 铸件位置选择
★ 铸件上的
大平面结构或 薄壁结构应朝 下或呈侧立状 态
不合理
合理
29
绘制铸件工艺图 选择浇注位置
选择浇注位置
整模造型
16
刮板造型
17
假箱造型
18
挖砂造型
19
三箱造型
20
活块造型
21
砂型铸造
22
2、机器造型
填砂、紧实、起 模等实现机械化,生 产率高,投资大,主 要用于批量生产。
机器造型
压实式造型 震机压实式造型 微震压实式造型 高压式造型 空气冲击式造型 射压式造型 抛砂式造型
23
2 铸造工艺规程制定
★ 选择浇注位
置应有利于补缩, 防止在铸件中产 生缩孔。
不合理
合理
卷扬机筒
30
绘制铸件工艺图 浇注系统
标准的浇注系统(外浇口、直浇道、横浇道、 内浇口及冒口)应放在分型面处,并朝向上箱。
材料成型第4章_铸造工艺设计1.答案
(2)尽量使铸件重要加工面或大部分加 工面、加工基准面放在一个砂型内,减少 错箱、披缝和毛刺,提高铸件精度。
床身铸件,其顶部平面为加工基准面。 图中方案a在妨碍起模的凸台处增加了外部型芯,因采用整模造型使加工 面和基准面在同一砂箱内,铸件精度高,是大批量生产时的合理方案。 若采用方案b,铸件若产生错型将影响铸件精度,但在单件、小批生产条 件下,铸件的尺寸偏差在一定范围内可用划线来矫正,故在相应条件下方 案b仍可采用。
25
方案1要考虑采用活块造型或加外型芯才能铸造; 方案2则省去了活块造型或加外型芯。
26
使铸件全部或大部分放在同一砂型
尽量使加工基准面与大部分 加工面在同一砂型内
不合理
合理
尽量使加工基准面与大部分 加工面在同一砂型内
27
(3)使型腔和主要型芯位于下箱,以便于造型、下 芯、合型和检查型腔尺寸。
于垂直或倾斜位置。图为油盘铸件的合理浇注位 置。
图4-2b 大面积薄壁铸件浇注位置
(4)对于容易产生缩孔的铸件,应使厚的 部分放在铸型的上部或侧面,以便在铸件 厚壁处直接安置冒口,使之实现自下而上 的定向凝固
铸钢卷扬筒,浇注时厚端放在上部是合理的; 反之,若厚端放在下部,则难以补缩。
23 图4-2-1 有热节的浇注位置
铸件的造型位置由分型面决定,而铸件的浇注位 置与造型位置通常是一致的。
浇注位置和分型面对铸件质量及铸造工艺都有很 大影响。
选择原则:着眼于控制铸件的凝固顺序
估计到铸件发生缺陷的可能
1.浇注位置的选择原则
(1) 铸件的重要加工面或主要工作面应朝下或位于 侧面,避免砂眼、气孔和夹渣
因为铸件的上表面容易产生砂眼、气孔、夹渣等缺陷,组 织也不如下表面致密。如果这些加工面难以朝下,则应尽 力使其位于侧面。当铸件的重要加工面有数个时,则应将 较大的平面朝下。
第四章 铸件结构与工艺设计
铸件结构设计 砂型铸造工艺设计 铸造工艺设计实例
第一节 铸件结构设计
铸件结构不仅会直接影响到铸件的力学性 能、尺寸精度、重量要求和其它使用性能, 同时,对铸造生产过程也有很大影响。 所谓铸造工艺性良好的铸件结构,应该是 铸件的使用性能容易保证,生产过程及所 使用的工艺装备简单,生产成本低。 铸件结构要素与铸造合金的种类、铸件的 大小、铸造方法及生产条件密切相关。
(压铸)便于取出铸件的设计
熔模铸件平面上的工艺孔和工艺肋
2.铸件的组合设计 2.铸件的组合设计
因工艺的局限而无法整铸的结构,应采用组合设计。
铸钢底座的铸焊
组合床身铸件
a)砂型铸件改为b)组合压铸件 a)砂型铸件改为b)组合压铸件
第二节 砂型铸造工艺设计
1) 2) 3) 4)
砂型铸造工艺具体设计内容包括: 选择铸件的浇注位置和分型面; 确定工艺参数(机械加工余量、起模斜度、铸造圆 角、收缩量等); 确定型芯的数量、芯头形状及尺寸; 确定浇冒口、冷铁等的形状、尺寸及在铸型中的 布置等。 然后将工艺设计的内容(工艺方案)用工艺符号或文 字在零件图上表示出来,即构成了铸造工艺图。
冒口 上 中 上 下
中 下 放收缩率1% 放收缩率1% 余量:上面>侧面> 余量:上面>侧面>下面 单件小批 手工三箱造型 大批量
外 型 芯 块
两箱机器造型
第三节 铸造工艺设计实例
例1:支架零件铸造工艺设计
材料为HT200,单件、小批量生产工作时承受中等 静载荷,试进行铸造工艺设计。
1.零件结构分析: 零件结构分析: 零件结构分析 筒壁过厚,转角处未采用圆角。修改后的结 构如图b)所示。 选择铸造方法及造型方法: 2.选择铸造方法及造型方法: 3.选择浇注位置和分型面
铸造工艺总汇-砂型铸造工艺设计
铸造工艺总汇-砂型铸造工艺设计图1 流涂装置示意图1一泄流阀, 2一涂料罐, 3一电动机, 4一搅拌杆, 5一滤网, 6一回收槽7一砂型, 8一流涂杆头, 9一控制开关, 10一软管, 11一泵5)静电喷涂法采用粉末涂料,借高压直流电形成强大静电场使粉末涂料微粒在喷枪头部的电晕放电区带电,在电场力和风力作用下向异极性砂芯(型)表面迅速集积成涂层,然后加热使涂料中粘结剂软化重熔建立涂层强度。
此法适用于尺寸较狭小的凹坑或狭缝不易徐敷上涂料的场合。
3.6 工艺分析与设计(工艺分析与参数查询)3.6.1浇注位置的确定根据对合金凝固理论的研究和生产经验,确定浇注位置时应考虑以下原则:1.铸件的重要部分应尽量置于下部。
2.重要加工面应朝下或呈直立状态。
3. 使铸件的大平面朝下,避免夹砂结疤类缺陷。
对于大的平板类铸件,可采用倾斜浇注,以便增大金属液面的上升速度,防止夹砂结疤类缺陷(见图1、2)。
倾斜浇注时,依砂箱大小,H值一般控制在200~400mm范围内。
图1具有大平面的铸件正确的浇注位置图2 大平板类铸件的倾斜浇注4.应保证铸件能充满。
对具有薄壁部分的铸件,应把薄壁部分放在下半部或置于内浇道以下,以免出现浇不到、冷却等缺陷。
图3为曲轴箱的浇注位置。
5.应有利于铸件的补缩。
6. 避免用吊砂、吊芯或悬臂式砂芯,便于下芯、合箱及检验。
7. 应使合箱位置、浇注位置和铸件冷却位置相一致这样可避免变合箱后或于浇注后再次翻转铸型。
此外,应注意浇注位置、冷却位置与生产批量密切相关。
图 3 曲轴箱的浇注位置a)不正确b)正确3.6.2 分型面的选择分型面是指两半铸型相互接触的表面。
除了地面软床造型、明浇的小件和实型铸造法以外,都要选择分型面。
分型面一般在确定浇注位置后再选择。
但分析各种分型面方案的优劣之后,可能需重新调整浇注位置。
生产中,浇注位置和分型面有时是同时确定的。
分型面的优劣,在很大程度上影响铸件的尺寸精度、成本和生产率。
砂型铸造工艺设计
砂型铸造工艺设计砂型铸造是一种常用的金属铸造工艺,适用于生产各种大中小型铸件。
砂型铸造工艺设计的主要目的是确保铸件形状、尺寸和质量的准确性,同时提高生产效率和降低生产成本。
下面是一个砂型铸造工艺设计的示例。
首先,确定铸件的形状和尺寸。
这是工艺设计的基础,涉及到铸件的几何形状、尺寸和重量等参数。
根据铸件的设计图纸,确定铸件的准确尺寸。
然后,选择适当的砂型材料。
砂型材料是砂型铸造中非常重要的因素之一,直接影响到铸件表面质量和精度。
根据铸件的材料和需求,选择适当的砂型材料,如石英砂、粘土砂等。
接下来,设计合适的砂型。
砂型的设计涉及到铸件和模具的结构设计。
首先,根据铸件的形状、尺寸和结构特点,确定合适的砂型结构,包括上、下模、型芯等。
然后,结合砂型材料的特性,设计合理的砂型壁厚和腔型,以保证铸件表面的光洁度和尺寸精度。
在设计砂型的同时,需要考虑到浇注系统的设计。
浇注系统是指将熔化金属引导到砂型腔内的通道系统,包括浇杯、溢流槽、导流槽等。
合理设计浇注系统可以保证金属的顺利流入砂型腔,并且能够避免金属中的气体和杂质混入铸件中。
最后,进行铸造工艺参数的选择和优化。
包括浇注温度、浇注速度、浇注时间、浇注压力等。
通过合理选择和优化这些参数,可以在保证铸件质量的前提下提高生产效率,降低生产成本。
总之,砂型铸造工艺设计是铸造工艺中至关重要的一步,它直接影响到铸件的质量和生产效率。
只有通过科学合理地设计砂型铸造工艺,才能生产出满足要求的铸件。
砂型铸造工艺设计是铸造生产中重要的环节之一,对于确保铸件的质量、做工的精细度以及生产效率的提高具有重要意义。
在砂型铸造工艺设计过程中,不仅需要考虑铸件的形状尺寸和材料特性,还需要合理选择砂型材料、设计适当的砂型结构和浇注系统,优化铸造工艺参数等。
首先,砂型铸造工艺设计的第一步是确定铸件的形状和尺寸。
根据产品的设计图纸和要求,确定铸件的几何形状、尺寸和重量等参数。
这些参数的准确确定是工艺设计的基础,直接影响到最终铸件的形状和尺寸精度。
- 1、下载文档前请自行甄别文档内容的完整性,平台不提供额外的编辑、内容补充、找答案等附加服务。
- 2、"仅部分预览"的文档,不可在线预览部分如存在完整性等问题,可反馈申请退款(可完整预览的文档不适用该条件!)。
- 3、如文档侵犯您的权益,请联系客服反馈,我们会尽快为您处理(人工客服工作时间:9:00-18:30)。
对于要求比较高的单件生产的重要铸件和大量生产的铸件,除要 详细绘制铸造工艺图,填写工艺卡以外,还应绘制铸件图、铸型装配 图以及大量的工装图,如模样图、模板图、砂箱图、芯合图、下芯夹 具图,检验样板及量具图等。
三、铸造工艺设计的一般步骤
1.对零件图纸进行审核和进行铸造工艺性分析 2.选择铸造方法 3.确定铸造工艺方案 4.绘制铸造工艺图 5.绘制铸件图 6.填写铸造工艺卡和绘制铸型装配图 7.绘制各种铸造工艺装备图纸
根据零件图及其相关要求,编制出一个铸件 生产工艺过程的技术文件就是铸造工艺设计。
这些技术文件必须结合工厂的具体条件,是 在总结先进经验的基础上,以图形、文字和表格 的形式对铸件的生产工艺过程加以科学地规定。 它是生产的直接指导性文件,也是技术准备和生 产管理、制定进度计划的依据。
二、铸造工艺设计的内容
起模斜度的形式
三、铸造圆角
铸件上相邻两壁之间的交角,应做出 铸造圆角,防止在尖角处产生冲砂及裂纹 等缺陷。圆角半径一般为相交两壁平均厚 度的1/3~1/2
四、收缩率
铸件由于凝固、冷却后的体积收缩,其各部分尺寸均小 于模样尺寸。为保证铸件尺寸要求,需在模样(芯盒)上加大 一个收缩的尺寸。加大的这部分尺寸称收缩量,一般根据铸 造收缩率来定。铸造收缩率定义如下:
铸造工艺设计包括以下几种主要技术文件:
1.铸造工艺图
5.模样图
2.铸造工艺卡
6.芯合图
3.铸型装配图
7.砂箱图
4.铸件图
8.模板图
由于每个铸件的生产任务和要求不同,生产条件不同,因此,铸
造工艺设计的内容也不同。
对于不太重要的单件小批量生产的铸件,铸造工艺设计比较简单。 一般选用手工造型,只限于绘制铸造工艺图和填写有关工艺卡,即可 投入生产
K=[(L模-L件)/L件]×100% 式中: K为铸造收缩率;L模为模样尺寸;L件为铸件尺寸。
铸造收缩率主要取决于合金的种类,同时与铸件的结构、 大小、壁厚及收缩时受阻碍情况有关。对于一些要求较高的 铸件,如果收缩率选择不当,将影响铸件尺寸精度,使某些 部位偏移,影响切削加工和装配。
通常灰铸铁为0.7~1.0%,铸造碳钢为1.3~2.0%,铝硅
优点是易于充满型腔,型腔中金属的温度自下而上递 增,因而补缩作用好、简单易做、节省金属材料。缺点是 对铸型冲击较大,有可能造成冲砂和飞溅,而且会加剧金 属的氧化。所以这类浇注系统多用于重量轻,高度低和形 状简单的铸件。
目录
顶注式浇注系统
(2)底注式浇注系统
61
与顶注式浇注系统相反,底注式浇注系统是从铸件 底部(下端面)注入型腔的。
★ 铸造工艺图有彩色图和墨线图两种 ★彩色图是利用红、蓝两色铅笔,将各种简明的工艺符号标 注在产品零件图上。铸造工艺图包括的内容: (1)分型面和分模面。 (2)浇注位置、浇冒口的位置、形状、尺寸和数量。 (3)工艺参数。 (4)型芯的形状、位置和数目,型芯头的定位和安装方法。 (5)冷铁的形状、位置、尺寸和数量。 (6)其他。
合金为0.8~1.2%,锡青铜为1.2~1.4%。
第三节 砂芯设计
一、型芯的作用 形成铸件的内腔、孔洞和形状复杂阻碍起 模部分的外形。
二.型芯的数量及分块 ★型芯的数量取决于铸件的形状 ★大型复杂型芯根据需要分块制作
三.型芯的形式 常用的型芯有水平型芯、垂直型芯、
悬臂型芯、悬吊型芯、引申型芯(便于起 模)、外型芯(使三箱造型变为两箱造型) 等六种。
(3)横浇道
横浇道是将直浇道的金属液引入内浇道的水平通道,一般 开在砂型的分型面上。横浇道的主要作用是分配金属液入内 浇道和隔渣。
(4)内浇道
内浇道直接与型腔相连,其作用是调节金属液流入型腔的方 向和速度,以及调节铸件各部分的冷却速度。
60 2.浇注系统的类型
浇注系统的类型很多,根据金属的种类和铸件的形状 及内浇道在铸件上开设的位置,可分为顶注式、底注式、 中间注入式和分段注入式等几种类型。 (1)顶注式浇注系统
上
下
上
②
下
①
第二节 铸造工艺参数的确定
一、机械加工余量和最小铸孔
灰铸铁的机械加工余量
铸件最大 尺寸 (㎜)
浇注时 位置
<50
<120
顶面 3.5~4.5 底、侧面 2.5~3.5
120~260
顶面 4.0~5.0 底、侧面 3.0~4.0
260~500
顶面 4.5~6.0 底、侧面 3.5~4.5
3. 铸件大面积的薄壁部分放在铸型的下部或垂直、倾斜。 原因:这样能增加薄壁处金属液的压强,提高金属液
的流动性,防止薄壁部分产生浇不足或位于分型面附近的上部或侧面
原因:便于安放冒口,实现定向凝固,进行补缩。
二、铸型分型面的选择 原则:在保证质量的前提下,尽量简化工艺
二、冒口
冒口是在铸型中设置的一个储存金属液的空腔。
明冒口 普通冒口
暗冒口
冒口
特种冒口
保温冒口 发热冒口 大气压力冒口 易割冒口
第五节 铸造工艺图实例
铸造工艺图是铸造过程最基本和最重要的工艺文件之一, 它对模样的制造、工艺装备的准备、造型造芯、型砂烘干、合 型浇注、落砂清理及技术检验等都起着指导和依据的作用。
利于档渣和排气,并能控制铸件的凝固顺序。
目录
浇注系统的组成
(1)外浇口
其作用是容纳注入的金属液并缓解液态金属对砂型的冲击。 小型铸件通常为漏斗状(称浇口杯),较大型铸件为盆状(称 浇口盆)。
(2)直浇道
是连接外浇口与横浇道的垂直通道,改变直浇道的高度可以 改变型腔内金属液的静压力从而改善液态金属的充型能力。
四、铸造工艺方案
概括说明铸造生产的基本过程和方法的工艺 文献,包括造型和造芯方法、铸型种类、浇注位 置和分型面的确定等。
第一节 浇注位置与分型面的选择
浇注位置:浇注时铸件在砂型中所处的空间位置。 分型面:铸型组员间的结合面
一、浇注位置的选择原则
原则:主要考虑铸件质量 1.铸件的重要加工面或主要工作面应朝下或位于侧面
原因:铸件的上表面容易产生砂眼、气孔、夹渣等 缺陷,组织也不如下表面致密。
2.铸件的大平面尽可能朝下或采用倾斜浇注
原因:铸型的上表面除了容易产生砂眼、气孔、 夹渣外,大平面还极易产生夹砂缺陷。这是由于在 浇注过程中,高温的液态金属对型腔上表面有强烈 的热辐射,型砂因急剧膨胀和强度下降而拱起或开 裂。拱起处或裂口浸入金属液中,形成夹砂缺陷。 同时铸件的大平面朝下,也有利于排气,减小金属 液对铸型的冲刷力。
注:加工余量数值中下限用于大批大量生产,上限用于单件小批生产
生产批量
大量生产 成批生产 单件、小批生产
最小铸孔
最小铸出孔直径
灰口铸铁件
12~15 15~30 30~50
铸钢件
- 30~50
50
注:对于零件上不要求加工的孔槽,无论大小均应铸出
二、起模斜度 为了起模方便又不损坏砂型,凡垂直于分型面的壁上须 留有斜度。
1.分型面应设在铸件最大截面处,以保证模样从型腔中顺利取出
2.应使造型工艺简化 ★应尽量使分型面平直,以简化模具制造及造型工艺,避免挖砂造型
★尽可能减少铸件的分型面,尽量做到只有一个分型面
★应使型芯和活块数量尽量减少。
3.应使铸件全部或大部放在同一砂箱。
4.应尽量使型腔及主要型芯位于下型,以便于造型、下芯、 合型及检验。
这是一种介于顶注和底注之间的注 入方法,既降低了液流落下的高度,又 使温度的分布较为均匀,内浇道处在分 型面上,便于开设和选择部位。因此, 这种浇注系统的应用很广。
63
(4)阶梯注入式浇注系统
阶梯注入式浇注系统
阶梯注入式浇注系统亦称阶梯式浇注 系统,是在铸件高度上设二层或二层以 上的内浇道,它兼备了顶注式、底注式 和中间注入式浇注系统的优点。
底注式浇注系统
目录
这类浇注系统的优点是充型平稳,排 气方便,不易冲坏型腔和引起飞溅,适宜 于大、中型的铸件。对易于氧化的合金, 如铝、镁合金和某些铜合金也较适宜。
这类浇注系统的缺点是不利于定向凝 固,补缩效果差,充型速度慢,不适合复 杂薄壁铸件的充型。
(3)中间注入式浇注系统
62
中注式浇注系统
目录
第四章 砂型铸造工艺设计
教学目的
1.了解砂型铸造工艺设计有关知识。 2.掌握浇注位置、分型面选择;铸造工艺参数确定;型
芯设计;浇冒系统等有关知识。 3.学会绘制简单铸件的铸造工艺图。
教学重点
1.浇注位置、分型面选择。 2.铸造工艺参数确定。
教学难点: 型芯及浇冒系统设计 计划学时:1学时
概述
一、铸造工艺设计的概念
四、型芯的技术要求
五、型芯的制作
六、型芯头及芯座 型芯头的作用:对型芯起固定、定位、排气作用。
58
第四节 浇注系统和冒口 一、浇注系统
浇注系统是指液态金属流入铸型型腔的通道。 1. 浇注系统的组成及作用
浇注系统一般包括外浇口、直浇道、横浇道、内浇道等。 浇注系统的作用应能平稳地将金属液引入铸型,要有
铸造工艺图实例1
铸造工艺图实例2
作业:P80 (1) 补充作业:
定性画出图示支座的 铸造工艺图 模型图 铸件图
材料:灰铁
铸造工艺:砂型铸造 生产量:单件小批
5.0~5.5 4.0~4.5
6.0~7.0 4.5~5.0
6.5~7.0 4.5~5.5
7.0~8.0 5.0~6.0
6.5~7.0 5.0~6.0
7.0~8.0 5.0~6.0
7.5~8.0 5.5~6.0
7.5~9.0 6.5~7.0
8.0~9.0 5.5~7.0
800~1250
8.5~10 6.5~7.5
500~800