汽车后视镜的风噪声分析
1_ANSYS CFD在汽车外空气动力学及气动噪声领域的应用和案例分享
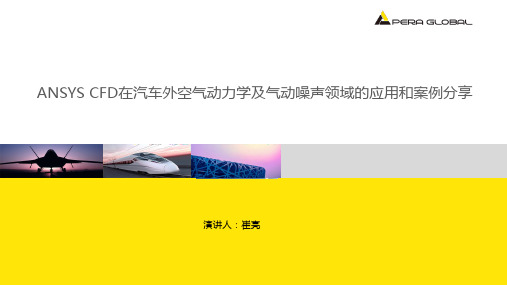
ANSYS CFD解决方案
高精度的湍流模型 自动化、大规模、高质量的网格工具 Model Drag (SCx) DES Exp. 0.70 DDES 0.71 DDES DES 0.75 LES 0.69
接近线性的并行加速比 支持超过一万核的并行
ANSYS CFD解决方案
不使用网格变形的优化过程
基于RBF Morph的优化案例
• 计算网格
• 使用FLUENT Meshing生成约5000万混合网格,共计10层边界层网格
• 计算条件
• 速度:100 kph • 压力基耦合求解器,对流项使用二阶迎风差分格式 • Realizable K-epsilon湍流模型,非平衡壁面函数
基于RBF Morph的优化案例
基于伴随求解器和网格变形的优化案例
优化目标:阻力降低
基于伴随求解器和网格变形的优化案例
基于伴随求解器和网格变形的优化案例
基于RBF Morph的优化案例
• Volvo公司使用ANSYS Fluent、HPC、RBF Morph和DesignXplorer, 实现了对XC60车型的空气动力学性能优化仿真。
• 计算代价较小 • • 计算域只覆盖噪声源的区域 适用于远场计算
• FW-H方法的缺点
• • • 无法考虑声音对流动的反作用 无法考虑反射 从源到接收位置之间需要有直的视线(无遮挡)
ANSYS FLUENT中的气动噪声模拟方法
• Broadband Noise Source Models • 在ANSYS Fluent的宽频噪声模型中,湍流参数通过RANS方程求出,再用一定的半经 验修正模型(如Proudman方程模型、 边界层噪声源模型、 线性Euler方程源项模型、 Lilley方程源项模型)计算表面单元或体积单元的噪声功率。 • Broadband模型是CAA和“声比拟”方法的很好补充,可以采用宽频噪声模型提取有
汽车电子后视镜技术开发及应用

汽车电子后视镜技术开发及应用摘要:电子后视镜近些年出现了里程碑式的发展,各个国家从标准法规上逐渐把电子后视镜的应用及开发技术予以法律化。
国内后视镜法规《GB15084-2022机动车辆间接视野装置性能和安装要求》已于2022年12月28日正式发布,用于替代标准《GB15084-2013机动车辆间接视野装置性能和安装要求》,新版法规增加了针对CMS后视镜的相关要求,这标志着电子后视镜在国内汽车领域的应用有了可行的法律依据。
关键词:汽车;电子后视镜;技术结构;开发应用引言:随着电子影像技术的发展和进步,电子后视镜在汽车上的应用逐渐成为现实。
电子后视镜的优点是可以弥补普通物理后视镜的不足,普通物理后视镜的主要痛点是驾驶员在驾驶车辆过程中,直视场、辅助视场难以避免的盲区,而在雨雾、强光、弱光环境下,物理后视镜也会出现视野模糊,这进一步增加了驾驶风险;此外,由于普通物理后视镜分布在驾驶室的左右两侧,前迎风面积相对较大,因此普通物理后视镜也是导致驾驶风阻增加的重要因素。
因此,汽车电子后视镜在汽车上的应用越来越广泛,近年来,汽车电子后视镜在世界各大车展上的出现也越来越频繁,充分说明这项技术具有非常广阔的应用前景。
1电子后视镜系统的构成及技术优势汽车在倒车过程中,驾驶员一般通过传统后视镜来观察车后状况,观察中会出现视野死角,视线模糊、目测不准等情况而不能实现安全倒车。
1.1电子后视镜系统的构成电子后视镜摄像监控系统,缩写为CMS,由高清摄像机、显示器、成像处理器、图像传感器、控制模块及其他部件和位置组成。
后视镜系统由软件组成。
相对于传统的驾驶室物理/后视镜左右两侧的布置,电子后视镜不仅可以降低车辆的风阻/系数,而且夜视场和视角范围比传动系统更好。
倒后镜具有明显的优势。
电子后视镜也被广泛使用业界称之为具有真正思考能力的后视镜系统,因为CMS 系统不仅具有传统后视镜的基本功能,而且还可以附加到周围移动的物体上,检测和报警功能,以及人机交互,它可以为用户提供更舒适的驾驶体验。
某SUV车型A柱风噪性能优化研究

qiyekejiyufazhan0引言在汽车发展日新月异的今天,人们对乘车舒适度有了更高的要求,而汽车在高速行驶时,由高速不定性气流激励产生的无动力学规律的风噪声会令乘客极为不适,因此如何降低风噪已成为NVH 的重要研究课题。
当车速达到80km/h 时,风噪声逐渐掩盖其他噪声成为主要噪声源,随着车速的提高,更是以车速6次方的关系增加[1],因此高速行驶的汽车噪声控制的有效途径是控制风噪。
影响风噪的因素很多,风噪的大小取决于车速、偏航角、车辆外造型及密封性能等因素,车辆外造型是引起风噪的源头,直接决定了噪声源的大小和位置。
因此,通过CAE 仿真的手段做好外造型的前期控制,不但可以有效抑制风噪,也可减少风洞试验次数,对控制成本与开发周期有利。
车身外造型对风噪影响较大的区域主要是A 柱、后视镜、发动机罩及外造型的搭接方式,其中,A 柱对风噪的影响极为敏感,不但受到机盖尾部流场的影响,经过前风窗的部分气流也会流向A 柱,少部分涡流从前风挡下部流向A 柱与后视镜耦合区域,流动状态急剧变差,故A 柱与后视镜区域产生的声源是整车风噪的最大风噪声源[2]。
因此,控制A 柱造型,减少A 柱气流分离成为控制风噪的关键,通过增加A 柱装饰件和修改A 柱型面,均能明显减小气流分离区[3]。
A 柱造型对风噪很敏感,流向前风挡玻璃的气流从侧面流出,在A 柱上端分开后形成向上移动的圆锥形漩涡,从A 柱分离的流体在侧窗附近产生一个高强度的锥形涡,这里形成的声源离驾驶员耳朵的位置非常靠近,加上窗玻璃是一种很差的绝缘体,因此A 柱声源的重要性显而易见。
A 柱分离后的流体会对外后视镜流场起到增强的作用,所以合适的A 柱对抑制声音目标、降低气流的涡流强度很关键。
本文使用PowerFlow 软件,以某款车型为基础,从正向开发的角度对A 柱断面结构进行仿真分析及优化。
1研究方法本文对某车型的A 柱造型进行优化,其造型特征主要包括前风窗玻璃与A 柱顶点的距离h 、A 柱挠度、A 柱过渡圆角R 、A 柱饰板等(如图1所示)。
风噪产生原理

风噪产生原理
风噪是由于空气流动产生的噪音。
其主要原理可以分为两个方面:
1. 空气流动引起的气动噪声:当风吹过障碍物(例如建筑物、车辆、设备等)或通过狭窄的空间(例如裂缝、孔洞等),会造成空气流动的变化,形成湍流和涡旋。
这种湍流和涡旋的形成会引起空气分子之间压力的不断变化,进而产生气动噪声。
这种噪声在空气流过不规则物体或不平滑表面时尤为显著。
2. 气体振动引起的结构噪声:当风吹过固体物体时,风力会作用于物体表面,引起物体振动。
这种振动可以通过物体的结构传导到周围的空气中,形成声波而产生噪音。
例如,当风吹过建筑物的墙壁、树叶的表面,或者通过挂载在杆上的标志牌或旗帜等,都会引起物体振动和相应的噪音。
风噪的强度和频谱特征取决于风速、风向、环境条件、障碍物的形状和表面特性等因素。
在实际应用中,通过改善建筑物或设施的设计,合理设置隔音措施,选择适当的材料以减少空气流动和振动引起的噪声,可以有效降低风噪的产生。
车身NVH工程培训材料-庞剑

路面 环境激励源:气流、环境噪声…
Input 激励
方向盘抖振 座椅振动
车身
System (车身+底盘)
后视镜振动 车内噪声
Output 响应
ACOUSTIC 听觉
1.1、车内噪声传递路径分析的基本概念
车内噪声和振动往往是由多个激励,经由不同 的传递路径抵达目标位置后叠加而成的。车内噪声 总体上可分为结构声和空气声两种。
(弯曲/扭转)
2
车身NVH传递特性
NTF/VTF/NR
3
接附点刚度
IPI
4
全局/局部类模态
5
板件类模态
6
声腔模态
VTF NTF
V F
Hz
P F
Hz
1st 、2st 弯曲模态
10
静刚度试验
XXX车身NVH目标体系
3.1、车身NVH性能与整车NVH水平密切相关
通过一系列车身NVH指标指导车身结构设计,以达到整车NVH性能开发目标。
4.1、CAE在车身NVH开发的应用 目前,车身NVH性能开发已广泛地利用CAE 工具,大大地降低了开发成
本,缩短开发周期,提高了车身NVH开发的精准性。对于车身低频NVH问题 (5~ 150Hz)主要利用有限元法(FEA) 和边界元 ,中频问题(150~ 400Hz) 可采用FEA与试验结合的混合模型法(Hybrid Model),利用统计能量分析 (SEA )可分析高频(>400Hz)的噪声问题。
与整车动力学相关的车身结构基本性能指标是车身刚度,与整车 NVH性能、疲劳耐久和操稳性能密切相关。
一般,通过合理的整车模态匹配和车身振型调制等方法,设计开发 车身结构的整体和局部刚度,以达到良好的整车振动水平和操稳性能。
汽车NVH常见问题分析及故障诊断思路(四)

检查项目1. 检査传动轴外观(损伤/ 变形/装配松动/平衡块脱 落等)2. 检査传动轴中央轴承装 配位置.(图A )3. 检査传动轴十字节(卡滞 /松动/相位角).4. 测量差速器法兰跳度. (图B )5. 检査传动轴动平衡,若无 动平衡测量仪,则与同型正 常车做替换实验.(图C )通过测量,发现在车速100km /h 、发动机转速3600r/min 时,异响最强,其峰值频率为60Hz 。
E /G 不平衡时的振动频率E/G 转速 r/m in 360060Hz" 60s "" 60 -传动轴不平衡时的振动频率E/G 转速 r /m in360060s X 变速器齿轮比” = 60Hz60X 1计算结果为:发 动机不平衡的振 动频率与传动轴 不平衡的振动频 率一样。
但是由 于异响在E /G 高 速空转时并不出 现,所以,判定 传动轴的不平衡 是振动力的来源。
(B o d y VIDTi症状描述车速100km /h 时,方向盘开始发抖:车速120km/h 时, 方向盘发抖现象最为严重。
VLateral shake(Body and seat vibrateright and left)通过测量,发现方向盘 在车速120k m /h 时振动最大,该峰值频率为18H z 。
轮胎不平衡时的振动频率_车速 <k m /h >x 1000m2tr X轮胎半径(m > X 3600<s e c .>120 X 1000代…0.3 X 3600注:设该车轮胎半径为0.3米因为计算得出的 频率与振动仪测 出的频率相吻合,故推测是轮胎相 关的因素引起了方向盘摆振。
检査项目1. 车辆状态检査(轮胎/轮毂/转向相关/悬架相关)2. 轮毂轴承和轮毂接续部位检査(间隙/装配不良等)3.测量轮胎圆跳度(纵向/横向跳度).(图A )4.测量轮毂偏摆.(图B )5.测量轮毂轴承偏摆.(图C )6.测量轮胎动平衡.(图D )7.检査四轮定位.高惠民(本刊编委会委员)曾任江苏省常州外汽丰田汽车销售服务有限公司技术总监,江苏技术师范学 院、常州机电职业技术学院汽车工程运用系专家委员,高级技师。
减振降噪的智能材料
4
➢悬架系统由路面不平激起振动,这种振动
通过悬架与车身的支点传至车身引起车身 的振动,进一步造成车内低频噪声;作为 悬架系统组成部分的减振器、轮胎等在工 作过程中所产生的噪声则通过车身的缝隙, 由空气传至车内。
2021/3/11
5
智能材料和结构
智能结构是结构的高级形式,实现智能结构的基 本逻辑构思就是:将驱动元件和传感元件紧密融 合在结构中,同时也将逻辑控制电路、信号处理 器、功率放大器、信息处理和人工智能环节以及 数据传递总线等集成在结构中,通过机械、热、 电、磁等激励和控制,使智能结构不仅具有承受 载荷的能力,还具有识别、分析、处理及控制等 多种功能。从原理上讲任何一种存在机械量与非 机械量电、热、磁、光耦合的物理材料都可称之 为智能材料,可用于智能结构中驱动和传感元件 的设计。智能结构中的驱动器将电量、电场强度、 磁通量等非机械量转变为应变、位移等机械量, 以实现结构的应变或位移驱动的目的。智能结构 中的传感器则正好与驱动器的功能相反,它将机 械量转变为非机械信号作为控制器的信号输入。
2021/3/11
13
2021/3/11
14
形状记忆合金的应用
普通金属材料,当其内部应力超过其弹性极限时
将产生塑性变形,由于塑性变形不可逆转,卸载 之后材料的变形不可恢复到原始状态。形状记忆 合金的形状记忆效应是指材料能够记住它在高温 状态下的形状,即处于低温下的形状记忆合金在 外力作用下产生变形后,如果将其加热超过材料 的相变点,它就会恢复到原来高温状态下的形状。 此外形状记忆合金还具有超弹性性能,它的应力 与应变之间呈现出迟滞循环效应,其弹性和超弹 性变形量可分别达到2%和8%。常用的形状记忆 合金有NiTinol 合金(镍钛合金) 。
某车型A柱风噪优化研究
某车型A柱风噪优化研究随着汽车工业的发展,消费者对于汽车的品质和细节越来越注重,其中包括车内的噪音问题。
对于日常驾驶中的车内噪音扰动,主要集中在A柱风噪上。
A柱风噪不仅影响驾驶者的驾驶体验,还会影响乘坐者的舒适性与健康。
A柱风噪的产生原因是空气流动引起的。
在汽车行驶过程中,高速气流会带起A柱附近的气流,产生噪音,影响车内的舒适性。
因此,优化A柱的设计和结构,减少空气流动的干扰,减少A柱区域的噪音扰动,提高车内的舒适性和安静性是当务之急。
在优化A柱设计方面,汽车厂家需要从多个方面出发,对原有A柱结构进行改进。
首先,A柱加入对流风扰切流器,通过改变风线流量在A柱表面流动的分布,减少A柱表面的气流震荡。
接着,优化A柱在结构上的细节设计,例如增加A柱顶部的凸出物,增加表面的顶部厚度,改变A柱边缘的倾斜角度等,进一步减少风流的干扰。
除了改善A柱结构和设计,优化A柱材质也是减少A柱风噪的一个有效途径。
A柱树脂材料是近年来汽车行业广泛采用的材质。
在优化A柱材质方面,厂家可以探索不同类型和厚度的树脂材料,通过实验和仿真分析,寻求最优解决方案。
同时,考虑到A柱加工成本和利用率的问题,厂家还可以采用多种材料组合制造的方法,进行有效的优化。
此外,合适的隔音材料可以有效地减少车内噪音,包括A柱风噪。
在开发和生产A柱的过程中,厂家可以考虑加入更好的隔音材料,例如极振聚丙烯材料、泡沫聚乙烯材料等,使车内噪音得到更大程度的吸收和抑制,提高驾驶者和乘坐者的舒适体验。
总之,A柱风噪优化研究是汽车工业中的一项重要任务,其目的是提高车内噪音的抑制能力,增强驾驶者和乘坐者的舒适度和健康感受。
在解决A柱风噪问题的过程中,汽车厂家可以从多个方面出发,改进A柱的结构、材质和隔音材料使用,推动汽车科技的进步与发展,提升消费者对汽车品质的信心。
除了A柱设计的优化,制造厂商还可以采用一些其他的技术对A柱风噪进行优化处理。
例如,利用计算流体力学(CFD)技术进行优化设计,运用现代计算机技术,实现对A柱风噪的预测和仿真分析。
汽车内外后视镜设计规范
性)
二、汽车后视镜的分类 ◆内后视镜:Ⅰ类、 ◆主外后视镜:Ⅱ和Ⅲ类、 ◆广角外后视镜:Ⅳ类、 ◆补盲镜:Ⅴ类 三、汽车后视镜的曲率半径 ◆内后视镜:Ⅰ类和Ⅲ类主外后视镜为曲率半径 为 1200mm ◆Ⅱ类主外后视镜曲率半径:为1800mm ◆广外后视镜Ⅳ类、补盲镜ห้องสมุดไป่ตู้Ⅴ类曲率半径:为 400mm
• 驾驶员借助外后视镜必须能在水平路面上看见一段宽度至少为3.5米的视野区域, 其左边与汽车纵向基准面平行,且与汽车右边最外侧点相切,并从驾驶员眼点后 30米处延至地平线。此外驾驶员借助外后视镜必须能看见宽度大于0.75米,并 从驾驶员眼点后4米处至上述区域相接的视野区域。
。
9
• 内后视镜视野规定
5)如后视镜外型需要重新造型,设计人员需要提供镜的长、宽, 镜杆位置中心尺寸,镜高,安装位置角度,镜在整车上的最低 高度等技术条件。
5
• 6、外部条件
1)总布置提供所用车型的驾驶室外廓尺寸 2)总布置提供所用车型的车厢尺寸 3)总布置提供所用车型的座椅H点,坐标位置尺
寸 4)总布置提供所用车型的眼椭圆X,Y,Z坐标尺
• 6、镜杆件的材料:管长度、管连接形式、管表面颜色及表面涂层、材料性能标 准等。
• 7、后视镜反射涂层:(电动、手动后视镜相同)
• 8、镀铝膜后视镜反射率不得低于40%
• 镀铬膜后视镜反射率不得低 于4%
• 9、后视镜失真率(电动、手动后视镜相同)
• 平面镜失真率不得大于3%
• 曲面镜失真率不得大于7%
13、后视镜总成耐候 性能:按QC/T531标准规定300h无异常。 14、后视镜总成震动耐久性:按QC/T531标准进行试验不得有变形、 损坏、松动、脱落、和镜面位置改变等现象产生。
NVH介绍要点
一:定义汽车NVH是指汽车的Noise(噪声)、Vibration(振动)和Harshness(舒适性)。
汽车NVH研究以提高顾客的听觉、触觉、视觉等感官舒适度、改善汽车乘坐舒适性为目的,以提高车辆结构动态响应性能为手段,实现汽车的舒适性设计。
Noise(噪声)是指引起人烦躁、音量过强而危害人体健康的声音。
汽车噪音不但增加驾驶员和乘员的疲劳,而且影响汽车的行驶安全。
它是NVH问题中最主要的部分,常用声压级评价。
汽车噪声主要包括车身壁板产生的噪声、空气冲击摩擦车身形成的噪声以及外界噪声源(如发动机、制动器等)传入的噪声。
噪声是NVH问题中最主要的部分,汽车上的噪声主要包括车身壁板振动产生的噪声、空气冲击摩擦车身形成的噪声以及外界噪声源(如发动机、制动器等)传入的噪声。
人耳能分辩的声音频率一般在lkHz以下,噪声常用声压和声压级评价。
国家标准规定:汽车加速行驶时车外噪声要小于88dB,M1类汽车应小于77dBN;而车内噪声会影响乘员的语言交流,损伤驾驶员的听力,美国在1965年就规定公共汽车的车内噪声不得超过88dB。
主要通过频率、级别和音质来描述。
Vibration(振动)描述的是系统状态的参量(如位移)在其基准值上下交替变化的过程。
汽车振动主要包括由路面不平整而引起的车身垂直方向振动、发动机的不平衡往复惯性力产生的车身振动、转向轮的摆振和传动系的扭转摆动等,还有方向盘、仪表板等振动,一般来说,对人体舒适性影响较大的振动主要表现为座椅、地板对人体输入的低频振动,其频率范围在1~80HZ。
主要通过频率、振幅和方向来描述。
Harshness(舒适性)指的是振动和噪声的品质,它并不是一个与振动、噪声相并列的物理概念,而是描述人体对振动和噪声的主观感觉,不能直接用客观测量方法来直接度量。
总的说来,舒适性描述的是振动和噪声共同产生的使人感到疲劳的程度。
二:现象车辆的NVH基本上可以分为车身NVH、发动机NVH和底盘NVH三个部分;类型可以细分为道路NVH、制动NVH、空调系统NVH、空气动力NVH等数个部分。
- 1、下载文档前请自行甄别文档内容的完整性,平台不提供额外的编辑、内容补充、找答案等附加服务。
- 2、"仅部分预览"的文档,不可在线预览部分如存在完整性等问题,可反馈申请退款(可完整预览的文档不适用该条件!)。
- 3、如文档侵犯您的权益,请联系客服反馈,我们会尽快为您处理(人工客服工作时间:9:00-18:30)。
2007年 CDAJ-China 中国用户论文集
- 1 -
汽车后视镜的风噪声分析
The Acoustic Simulation of Auto Rearview Mirro
张建立
(沈阳华晨金杯汽车有限公司研发中心,辽宁 沈阳 110141)
关键词:噪声;后视镜;空气动力学;CFD
摘要:
汽车噪声对环境危害很大,汽车噪声的大小也是衡量汽车质量水平的重要指标。
本文利用STAR-CD对某型汽车的后视镜进行了噪声分析,并对后视镜进行了改进,降低了后
视镜的噪声。
Abstract:
The auto acoustic is very harmful to the environment,and the acoustic
level is one of the most important criterion of the auto quatity.This paper
introduces the process of the auto rearview mirro acoustic simulation with
STAR-CD,and how we reduce its acoustic level by modifying the rearview mirro.
Keyword: Acoustic;Rearview Mirro;Aerodynamics;Computational Fluid Dynamics
1前言
汽车噪声对环境的危害很大,
汽车在给我们带来现代物质文明的同时,也带来了环境噪声
污染等社会问题。根据噪声源的发声机理,汽车噪声主要有两类:机械噪声和空气动力学噪声。
而在汽车高速行驶时,空气动力学噪声表现的尤为明显。空气动力噪声是由于气体流动中的相互
作用或与固体间的作用而产生的
,它包括空气通过车身缝隙或孔道进入车内而产生的冲击噪
声、空气流过车身外凸出物而产生的涡流噪声、空气与车身的摩擦声三个方面
[1]
。其中后视
镜引起的噪声是汽车空气动力学噪声的重要组成部分。
作为汽车乘坐舒适性的重要评价指标,汽车噪音也在很大程度上反映了生产厂家的设计水平
及工艺水平。因此,控制汽车噪音到最低水平一直是汽车设计者追求的方向。
研究表明,为了
降低车身空气动力学噪声并减小高速行驶时的阻力,应采用流线型车身并尽量减少凸出部
件,对于必须暴露的部件(如后视镜)也要尽可能设计成流线型,这样可以减少空气涡流,
减小空气与车身表面的撞击和摩擦
[2]
。我们国家对机动车辆的噪声控制也非常重视,并颁布
了
《汽车加速行驶车外噪声限值和测量方法》(GB1495-2002)等标准来限制汽车行驶时的噪声
[3]
。
本文利用著名的CFD软件STAR-CD对某轻型客车的后视镜进行了稳态的CFD噪声分析,得
到了车身各处特别是后视镜附近的噪声源强度大小及其分布,为后视镜的优化设计提供了依
据。
2007年 CDAJ-China 中国用户论文集
- 2 -
2.模型建立及边界条件确定
2.1 几何模型建立
根据某车型的三维CAD实体模型,取车身外表面生成几何模型。考虑到汽车产品的复杂
性,为了节约计算时间和减少网格数量,在不影响模拟精度的前提下,对车身表面、地板、
底盘等做了一些简化处理;并对车体缝隙、进气隔栅等进行了缝合,以减少其对后视镜噪声
的影响。但对模拟的关键部件,如后视镜等的细部结构则应尽量保留,如图1所示。
由于车身表面非常复杂,而且CAD模型之间有许多缝隙和漏洞,如果直接在CAD软件中
进行模型的前处理,需要花费大量的时间和精力。因此,我们采用先在Hypermesh中划分三
角形的表面网格,这样表面的连接和修补相对容易,然后输出为Nastran格式,作为表面再
导入到Pro-am中划分体网格。图2为后视镜放大图。
图1 几何模型 图2 后视镜放大图
2.2 计算网格划分
在本次分析中,利用自动网格生成软件Pro-am划分体网格,生成为非结构化贴体网格,
绝大部分为六面体。对重点考察区域如后视镜附近、地板和尾流区进行了局部细划,以加强
对此处流动细节的了解。
由于汽车为左右对称,为了减少计算时间,取一半模型进行划分。计算区域取为长方体,
长宽高分别为32m×5m×7m,上游距前车轴8m,如图3所示。整个模型流体网格632662个,
其中边界层网格100751个。图4为计算网格的局部放大图。
2007年 CDAJ-China 中国用户论文集
- 3 -
图3 计算网格 图4 计算网格局部放大图
2.3 边界条件确定
分析中入口采用INLET边界条件,入口速度为30m/s,沿X方向,紊流强度为1%。出口
为OUTLET边界条件。车身中面所在平面为Symmetry对称边界条件。侧面及顶部采用滑移壁
面边界条件,底部及车身表面采用无滑移壁面边界条件。紊流模型采用高雷诺数k-ε湍流
模型。采用SIMPLE算法进行计算
[5]
。
3.计算结果及分析
为降低后视镜噪声,我们对后视镜进行了流线化设计。通过对后视镜优化前后的噪声分
析,我们得出了车身各处的噪声源强度大小及分布等。结果对比表明,后视镜优化设计后,
噪声源强度有明显的降低。
3.1 原始模型计算结果
后视镜的原始几何模型如图2所示。通过计算,我们可以看到,噪声源强度较大的地方
位于后视镜、进气隔栅和轮胎附近,这是由于气流与这些地方发生撞击,产生涡流所致。其
中噪声源强度最大值为13.43,如图5所示。图6为ISO Surface图。
2007年 CDAJ-China 中国用户论文集
- 4 -
图5 噪声源强度分布图 图6 ISO Surface图
从图7和图8沿X和Y方向的剖面可以看出,噪声源强度最大的地方处于后视镜后方。
图7 X方向剖面图 图8 Z方向剖面图
如图9和图10为车身和后视镜周围的速度分布情况。
图9 车身周围速度分布图 图10 后视镜附近速度分布图
3.2 优化设计后计算结果
对比原始模型,我们对后视镜进行了流线化设计,并重新进行了噪声分析。从计算结果
可以看到,噪声源强度最大值为13.12,也位于后视镜后方。如图11为进行流线型设计之后
的后视镜几何模型,图12为优化设计后的噪声源强度分布图。可以看出,进行后视镜的流
线型设计之后,噪声源强度有了明显下降。
2007年 CDAJ-China 中国用户论文集
- 5 -
图11 流线型设计后的后视镜 图12 噪声源强度分布图
4结论
(1)应用STAR-CD分析软件对某车型进行的后视镜噪声分析,可以较准确的得到车身
周围各处的噪声源强度大小及其它详细信息。
(2)计算结果表明,对后视镜进行流线型设计,可以减小后视镜引起的噪声。
(3)在产品开发时应用CFD方法,可以大大缩短开发周期,节省开发费用,分析结果
对于设计开发人员优化产品设计具有重要参考价值。
参考文献:
[1] 陈南.汽车振动与噪声控制.北京:人民交通出版社,2005
[2] 何渝生.汽车噪声控制.北京:机械工业出版社,1996
[3] 汽车加速行驶车外噪声限值和测量方法.GB1495—2002
[4] 陶文铨.数值传热学.西安:西安交通大学出版社
[5] STAR-CD帮助文档