板带轧机换辊液压系统设计
1400毫米冷轧精整机组卷取部分设备液压传动系统设计
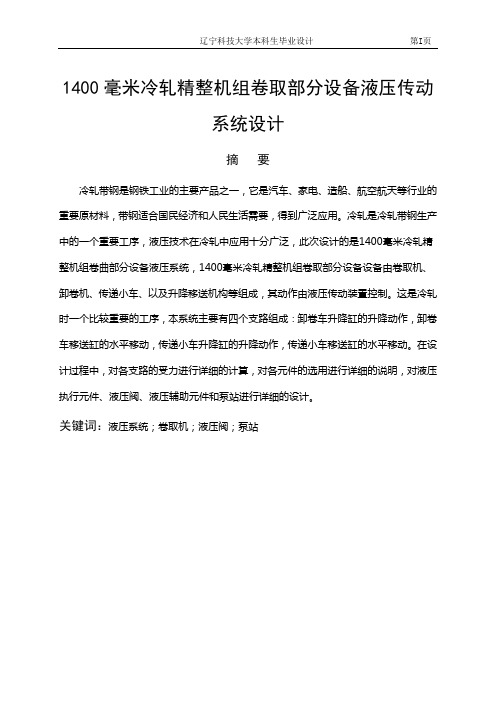
1400毫米冷轧精整机组卷取部分设备液压传动系统设计摘要冷轧带钢是钢铁工业的主要产品之一,它是汽车、家电、造船、航空航天等行业的重要原材料,带钢适合国民经济和人民生活需要,得到广泛应用。
冷轧是冷轧带钢生产中的一个重要工序,液压技术在冷轧中应用十分广泛,此次设计的是1400毫米冷轧精整机组卷曲部分设备液压系统,1400毫米冷轧精整机组卷取部分设备设备由卷取机、卸卷机、传递小车、以及升降移送机构等组成,其动作由液压传动装置控制。
这是冷轧时一个比较重要的工序,本系统主要有四个支路组成:卸卷车升降缸的升降动作,卸卷车移送缸的水平移动,传递小车升降缸的升降动作,传递小车移送缸的水平移动。
在设计过程中,对各支路的受力进行详细的计算,对各元件的选用进行详细的说明,对液压执行元件、液压阀、液压辅助元件和泵站进行详细的设计。
关键词:液压系统;卷取机;液压阀;泵站1400 millimeters of cold Ya Jing whole machine set book take a parts of equipments liquid to press to spread to move a system designAbstractCold Ya's taking a steel is a steel industry of one of the main products, it be the importance of the professions, such as car, appliance, shipbuilding and aviation aerospace...etc. original material, take a steel in keeping with national economy and people life demand, get extensive application.The cold Ya is , in the cold Ya that take a steel to produce of an importance work preface, the liquid press a technique in the cold Ya application very extensive, this time design of is 1400 millimeters of cold equipments liquid with parts of curl of the Ya Jing whole machine set to press system, 1400 millimeters of cold equipments equipments with parts of curl of the Ya Jing whole machine set be taken machine by book, unload a machine, deliver a small car, and ascend and descend move to send to organization's etc. to constitute, it action is press by the liquid to spread to move to equip control.This be the cold Ya 1 more the work preface of importance, this system be main to have four the road constitute:Unload a car ascend and descend an ascend and descend of urn action, unload a the level that the car move to send an urn move, deliver a small car rise and fall ascend and descend of urn action and deliver a small car to move level of send the urn move.In the design process, rightness each being carry on by dint of road detailed of calculation, use to carry on expatiation to choose of each component, to the liquid press performance component, liquid to press valve, liquid to press assistance component and pump station to carry on detailed of design.Keyword: The liquid press system;Book take machine;The liquid press valve;Pump station目录1绪论 (1)1.1课题的背景、目的及意义 (1)1.21400毫米冷轧精整机组卷曲部分设备液压系统简介 (1)1.3国内外冷轧机液压传动系统的发展状况 (3)1.4 本课题的主要设计内容 (3)2 液压系统的相关设计参数 (4)3制定系统方案和拟定液压系统图 (5)3.1液压系统的组成及设计要求 (5)3.2制系统方案定 (5)3.3拟定液压系统原理图 (6)4载荷的组成和计算 (8)4.1液压缸载荷组成 (8)4.2各液压缸载荷的计算 (9)4.2.1卸卷车升降缸的载荷计算 (9)4.2.2卸卷车移送缸的载荷计算 (9)4.2.3传递小车升降缸的载荷计算 (9)4.2.4传递小车移送缸的载荷计算 (11)5 计算液压缸的的主要结构尺寸 (12)5.1初选系统工作压力 (12)5.2液压缸的主要结构尺寸计算 (12)5.2.1液压缸的主要结构尺寸组成 (12)5.2.2液压缸的主要结构尺寸计算 (13)5.3计算液压缸所需流量及实际工作压力 (14)5.3.1卸卷车升降缸所需流量和实际工作压力 (14)5.3.2卸卷车移动缸所需流量和实际工作压力 (15)5.3.3传递小车升降缸所需流量和实际工作压力 (15)5.3.4传递小车移动缸所需流量和实际工作压力 (15)6 液压元件的选择 (16)6.1 液压缸的选用 (16)6.2 液压泵的选用 (20)6.3 电动机的选用 (21)6.4 液压阀的选用 (21)6.5 油管尺寸的计算 (22)6.5.1管道内径的计算 (22)6.5.2管道的选择 (23)6.5.3管接头的选择 (24)6.6 油箱容积确定 (24)6.7 蓄能器的选择 (25)6.8 液压介质的选择 (25)6.9 其余液压辅助元件的选择 (26)7液压系统性能验算 (27)7.1 液压系统压力损失 (28)7.1.1沿程压力损失 (28)7.1.2局部压力损失 (30)7.1.3总的压力损失 (31)7.2 液压系统的发热温升计算 (31)7.2.1计算液压系统的发热功率 (31)7.2.2计算油箱的散热功率 (33)8阀块的设计 (34)9泵站的设计 (35)10环境性能分析 (36)10.1环境污染简介 (38)10.2 机械工业(这里指液压)对环境的危害和防治 (37)10.2.1液压工业对环境的危害 (38)10.2.2解决方法 (38)结论 (40)致谢 (41)参考文献 (42)1绪论1.1课题的背景、目的及意义冷轧是冷轧带钢生产中一个重要工序。
热轧板带轧机立辊压下油缸结构优化设计

热轧板带轧机立辊压下油缸结构优化设计摘要: E1立辊轧机位于R1四辊粗轧机入口侧,用于控制板坯的宽度和形状,同时将板坯的边部由铸态组织变为轧态组织,避免在水平轧制中产生边裂,同时有破鳞的作用。
E1立辊轧机侧压装置分布于轧机传动侧和操作侧,两侧侧压装置共同作用可调整轧辊的开口度,每侧由安装在机架上的立辊压下AWC液压缸与相应侧的平衡液压缸共同调整轧辊的位置。
关键字:热轧;AWC油缸;结构改造一、绪论1、侧压装置原理侧压装置油缸部分主要油缸为4个AWC油缸和2个侧压平衡缸组成,AWC油缸和侧压平衡缸提供侧压主要动力。
4个AWC油缸将立辊向轧制中心推动,2个侧压平衡缸将立辊往两侧回拉,以消除间隙。
2、近期AWC系统故障处理汇总及分析2017年5月以来,AWC油缸发生多起前端盖密封漏油、前后端盖螺丝崩断、前后端盖漏油故障,这些故障处理时间都较长,严重影响生产节奏。
现针对现场使用实际,拟对AWC油缸结构进行部分改造。
二、AWC油缸现场使用情况分析1、AWC油缸受力分析AWC油缸通过两个半圆法兰固定安装在轧机牌坊上,AWC油缸受力分析,油缸受力示意图如下:(1)粗轧AWC控制由4台AWC液压缸及其控制系统构成。
工作侧2台AWC缸、传动侧2台AWC缸。
每台AWC缸由1台三级伺服阀控制。
通过计算机控制伺服阀进油或者回油,从而控制立辊的开合,实现AWC与SSC控制。
(2)油缸安装形式解析:油缸安装在立辊牌坊的孔内,安装时油缸从牌坊外侧装入牌坊孔内,油缸与牌坊孔只存在同心关系,缸筒外壁与牌坊孔无磨擦力约束。
半圆块螺栓紧固安装在牌坊上,半圆块卡住油缸缸筒安装位,两者会有部分静磨擦力,但可忽略不计,油缸有杆腔端盖端面与半圆块接触。
(3)油缸工作过程受力分析:立辊开度调节是由伺服阀控制进入AWC油缸无杆腔的液压油量来控制活塞杆的伸出/缩回进行精确调整,当AWC缸活塞杆动作到指定位置,封油柱完成,在轧制过程中油缸缸筒与无杆腔油液、无杆腔端盖、活塞杆、活塞环,近似可看作刚性结构,承受轧制负载。
轧机液压压下系统分析

轧机液压压下系统分析摘要:本文通过对带钢冷轧机液压压下装置的相关性能特征和工作原理,以及轧机液压轧制控制分析,以及相关的材料工艺选用,得到轧机液压压下系统的高指标性能的依赖于系统的各个环节优良,还需要相关技术工作人员轧制工艺精湛,更需要液压、电气和机械上相互配合,做到各方面优秀,积极运用高技术,保证高专业,配套高综合知识水平,才能保证我们整个轧机液压压下系统的稳定高效运行。
关键词:带钢冷轧机液压压下系统轧制控制一、前言目前我们所说的轧辊压下通常包括液压压下以及电动压下两个主要组成方式。
当下社会,伺服控制液压压下装置的产生和发展较为迅速,与之相配合的液压压下系统也得到了广泛的应用和推广[1]。
此装置克服了传统电动压下装置的一些弊端,并且能极大提高相关精度的调节以及提升了相应的速度,对之前装置存在的系统惯性大也起到了较好的降低作用,较为有效的控制了轧机基座的当量刚度和恒辊缝轧制,这些改善保证了装置能较好的实现恒压力的功能,恒辊缝轧制得到有效控制后能产生过载保护的功能,在出现过载事故时,辊缝能迅速打开并及时卸压,不仅有效的保护了机械设备,还促进了机械传动效率和机组作业率,较好的实现了快速换辊的环节,正是因为该装置存在众多优点,所以在我们现代化冷、热轧和平整机中得以广泛的使用。
二、系统工作原理组成液压压下装置系统的相关零件有:伺服放大器、伺服阀、液压缸、位置传感器等。
在现实情况下液压缸移动的行程受电液伺服阀对液压缸压力和相关流量调节的影响,在此情况下才能对轧辊辊缝的值进行相关调节,通过对轧辊辊缝值的放大设置,向电液伺服阀施加输出,从而驱动液压缸工作,使得辊缝达到预设定。
液压缸内的位置传感器能实时捕捉轧辊的实际位置,这里能产生一个反馈值,如果反馈值与辊缝相关的预定值实现了统一,这就表明辊缝完成参数调整,则指示液压缸停止动作。
如果在轧制过程中,轧制压力产生了一定的变化,此时压力传感器可以对轧制压力变化进行相关波动测量,并转换成对应的位移补偿信号差值,并将信号差值和调节系数进行相乘计算后,重新输入值进行调节辊缝,直至液压缸位移调节量与补偿信号差值相等,这时才表示调节完成,在这种情况下,因为轧制压力的变化,致使轧机弹跳,从而实现了完全补偿。
连轧粗轧换辊系统改造分析

连轧粗轧换辊系统改造分析通过设计计算、重新选型以及设备改造,解决连轧粗轧1#-6#换辊系统换辊时间长、辊缝调整故障率高等问题,大幅度缩短粗轧轧机换辊时间及故障率。
连轧原560轧机辊缝通过液压马达来调整,经常出现压不动的情况,靠人为手动来调辊缝,即增加了工人的劳动强度又延长了换槽、换辊时间。
电气方面换辊系统原使用继电回路控制,控制系统老旧,故障率高且维护不便,同时操作盘安装在轧机机架后,操作不便,且因轧机水喷溅造成操作盘损坏。
对所出现故障进行分析,指定改造方案,缩短了换辊换槽时间,保证了正常的轧制节奏标签:液压阀;锁紧销;改造1 概述(1)连轧粗轧1-6#轧机辊缝是通过液压马达来调整的,经常出现压不动的情况,靠人为手动来调辊缝,即增加了工人的劳动强度又延长了换槽、换辊时间。
(2)连接杆扁头与轧辊轴头无法限位,每次需要焊接连接杆,不仅增加工作量和换辊时间,也严重影响连接杆动平衡,缩短其使用寿命。
(3)轧机在抽辊及装辊时需要用天车吊住连接杆扁头,增加危险性,且占用天车并耽误时间。
(4)连轧1-6#换辊系统原使用继电回路控制,控制系统老旧,故障率高且维护不便,同时操作盘安装在轧机机架后,操作不便,且因轧机水喷溅造成操作盘损坏。
2 技术方案总体思路(1)通过对液压马达输出力矩计算和液压阀重新选型改造来解决轧机辊缝经常压不动的问题。
(2)设计改造连接杆扁头碟簧锁紧销,增强其强度及使用周期。
(3)设计更换托架卡板气缸及移位其气动阀(原位置工作环境差)。
(4)恢复并改造原接轴托架机械机构。
(5)设计换辊系统远程操作台3面,设计换辊系统控制柜1面、升降控制电源柜1面。
(6)安装操作台3面、系统控制柜1面、升降控制电源柜1面。
(7)换辊系统与主轧线PLC联网,调试硬件、网络。
3 技术方案季解决措施3.1 液压部分目前轧线液压站泵输出压力150bar液压马达输出的是机械能,所以它的主要性能参数是转速和转矩,在不考虑任何损失的情况下,根据能量能量守恒定律:pmqn=MT?棕式中pM-马达的进口压力(设马达的出口压力为零)MT-马达的理论轮矩?棕-马达的角度速度由式可得MT=■原理图中35.2减压阀减压后最大调整压力为100bar,考虑回油被压值,取马达的出口被压值为4bar,pM=100-4=96bar。
液压自动平衡控制系统设计

液压自动平衡控制系统设计摘要:轧机上支承辊平衡机构是轧机主体设备的重要部件。
在换辊过程中上工作辊装置及上中间辊装置经常会出现球轴承损坏、辊面压痕的问题。
海上作业及移动设备等特殊工况下工作台表面在外力作用下发生倾斜,影响工作效率及可靠性,对此基于PLC设计了自动液压平衡控制系统。
该系统由PLC、人机交互界面、传感器及液压泵站组成。
传感器对工作面倾角进行监测,通过Modbus-RTU将检测结果传递到PLC进行分析计算,根据分析结果对液压系统进行控制,实现工作面自动平衡。
关键词:液压;自动平衡;控制;设计1导言本文作者基于三菱FX3U系列PLC设计了自动液压平衡系统,系统框图如图1所示。
工作平台表面在外力作用下发生倾斜时,倾斜传感器采集8个不同方向倾斜数据并实时反馈到PLC进行处理,根据处理结果控制液压系统液压缸伸缩量以调整工作面倾角,实现工作台的平衡,同时将工作面倾斜角度显示于人机界面。
系统调整精度为0.2°,调整时间小于6s。
2系统整体设计该平衡控制系统通过对称布置的4个液压缸对工作面进行支撑,将倾斜传感器安装于工作面底面,当工作表面倾斜时,传感器检测当前工作表面倾斜角度,并将检测结果传递给PLC分析计算,通过上位机人机界面显示倾斜角度,同时PLC通过控制电磁阀通/断控制液压缸运动,完成工作面倾角调整,直至工作表面恢复水平。
图2 原液压平衡控制系统原理图由图2可以看出,液压动力站来的压力油经减压阀减压后,电磁换向阀YA1通电,压力油打开液控单向阀进入上支承辊平衡缸有杆腔,上支承辊抬起,平衡上支承辊装置的重量。
电磁换向阀YB1通电则上支承辊装置落下。
平衡缸的运行速度由单向节流阀控制。
溢流阀防止系统过载。
电磁换向阀具有位置保持功能,通电后可以延时断电。
液控单向阀防止在事故状态断流时上支承辊装置下落。
减压阀的设定压力一般根据上支承辊装置的重量、平衡缸无杆腔与有杆腔的受力面积以及考虑到的摩擦力来计算数值。
不锈钢冷轧带钢轧机液压压下装置设计

课程设计___ ________2012-12-21.目录摘要1Abstract21 绪论31.1 课题背景31.1.1 AGC概述31.1.2AGC控制的发展情况31.1.3AGC控制的发展趋势41.1.4AGC控制存在的问题42 方案论述及确定62.1液压压下装置的特点62.2方案论证及确定63液压系统主要参数计算及元件选择93.1 初选系统工作压力93.2 液压缸尺寸计算及选择93.2.1缸尺寸的确定93.2.2 负载压力的计算93.2.3系统流量计算10表3-3系统流量103.3液压缸主要尺寸确定113.4 液压缸强度和稳定性计算:123.4.1缸筒壁厚的校核123.5 液压泵和电动机的选择123.5.1选择液压泵123.5.2选择电动机133.6 液压辅助元器件选择133.6.1过滤器选择143.6.2蓄能器的选择143.6.3其他元器件15表3-4 液压系统各元件一览表153.7油箱尺寸计算163.7.1油箱容量的经验公式163.7.2油箱结构的设计163.7液压压下系统性能验算174 液压压下系统的安装与维护204.1液压压下系统的安装204.2 液压压下系统的维护205 总结错误!未定义书签。
22献文考参.摘要本设计系统为1450五机架冷连轧初轧机工作辊液压压下系统,钢板轧机的轧辊的位置偏差进行反馈纠正,通过这套伺服控制系统,可以精确控制轧机轧制钢板的厚度.本文主要分析了AGC系统国内外发展现状和存在的问题,进行方案设计,原理分析,参数设计,液压元器件选择,还对系统安装维护做出分析,针对已有的设计存在的问题进行创新改善,保证在轧机在轧制过程中控制.油箱AGC 液压冷轧机关键词AbstractThe design system for the1450 five stand cold rolling mill hydraulic AGC control system for steel mill roll position feedback error correction is a servo control system. Mill at home and abroad are introduced the development of hydraulic AGC control of the state and development trends and existing problems. The design principles include tank Manifold design, Design, valve assembly design, system component selection, design and pump station design, the spirit of reasonable co-exist with a certain margin system . of the the requirements, ensure the process the principles of design cost to plate steel thickness control can control this Through servo system precisely the of rolling mill.Cold Rolling MillHydraulic AGCPumping Station Keywords1 绪论1.1 冶金AGC系统在国内外发展现状及存在的问题1.1.1 AGC概述AGC(Automation Gauge Control),即为厚度自动控制.厚度是板带钢最主要的尺寸之一,随着技术的进步,厚度自动控制已成为现代化板带钢生产中不可缺少的重要组成部分.厚度自动控制(AGC-Automation Gauge Control)的基本方式是通过测厚仪或者其他传感器对带钢的实际轧出厚度进行连续测量,根据实测值与给定值相比较得到的偏差信号,借助各种测量装置调整压下量、张力或压下速度,将轧机出口厚度控制在允许的偏差范围内.其基本方式就是通过测厚仪或者其他传感器对带钢的实际轧出厚度进行连续测量,根据实测值与给定值相比较得到的偏差信号,借助各种测量装置调整压下量、张力或压下速度,将轧机出口厚度控制在允许的偏差范围内.1.1.2AGC控制的发展情况图1-1 AGC控制方式简图近30年来,国外轧机的装备水平发展很快.在冷带轧机上广发利用液压压下、液压弯辊、厚度自动控制、板形控制和计算机控制等技术、在新技术运用方面均已采用液压AGC系统与计算机控制相结合的DCS,装设了测量精度高的三测仪表(测厚、测压、测张),且装设了板形检测装置.而国内轧机设备还比较落后,特别是自动控制系统.即使60年代中期从日本、美国等引进的当时属于较先进的单机架轧机,由于当时技术水平的限制,多数未达到设计目标,面临着改造.在采用新技术方面,部分设备采用了液压压下,少数设备将原有的机液伺服改成了电液伺服系统,并装设了AGC系统,安装了三测仪表,实现了张力闭环控制,但是精度不高.面对国内轧机的这种情况及资金短缺的实情,在吸收国外AGC先进控制的基础上,开发实用性、高精度自控系统装备现有的设备,能使我国钢铁冷轧设备的控制水平进一步提高.由于轧机自动化水平及对板带材的质量要求越来越高,对轧机执行机构及控目前,液压技术的应用程度和水平,已成为冶金设.制系统性能的要求也越来越高.备技术水平高低的一项衡量指标.其中液压AGC(Automatic Gauge Control)系统是所有冶金设备中液压技术应用的典型代表,是现代化轧机设备的核心技术.液压AGC系统运行状态的好坏,直接决定了轧机的工作可靠性.长期以来,由于机械设备水平的整体差距,我国的轧机设备主要依赖进口,在技术特别是核心技术方面受到限制.虽然近年来在先进技术的应用方面有重大突破,但仍局限在单机应用的水平.因此,开展液压AGC系统故障诊断技术的研究不仅对提高轧机设备的生产率、提高设备的维护管理水平具有重要意义,同时也对提高国产轧机设备的应用水平具有重要的社会意义.1.1.3AGC控制的发展趋势在连轧工艺发展过程中,轧制过程模型研究一直为钢铁研究企业所重视,由于轧制内部机理十分复杂,目前对数学模型研究多集中在轧机体系模型,分析轧制过程中某一因素对厚度的影响,如张力、轧辊变形等,所建的模型缺乏全面、完整性.因此,建立一个全面、完整、正确的机电一体化轧制模型,进行轧机体系在轧制过程中的实时动态研究是目前的发展趋势.采用智能控制技术(如神经网络)提高自适应学习的精度.模型计算过程中考虑单元细化,如有限元方法和有限元思想的使用.在控制策略的研究方向,基于反馈控制理论,控制模型出现了两个研究方向.一是复合控制,即在常规PID控制的基础上,加入前馈、压力、秒流量等控制策略.这种方法在轧钢工业中得到广泛应用,效果良好;二是利用被控对象建模的新方法(如人工神经网络)、自适应控制、预测控制、优化控制的新算法,构造单环反馈系统,由于这些算法在理论推到研究上有许多假设条件,与实际有很大差距,随着算法的进一步改进,这个方向无疑有很大的发展前景.1.1.4AGC控制存在的问题虽然AGC在各个方面都有了不同程度的发展,但是,由于各方面因素的限制以及AGC控制方式很多,各种AGC复合体统往往相互关联,相互影响,实际上存在最优组合方案.存在的问题和带来的难点主要有:1) 建立真实反映被控对象内在本质的数学模型比较复杂.冷轧机阀控液压系统是一个多变量、非线性、强耦合、参数时变的且带有随机干扰的不确定系统.目前轧机系统的模型都用二阶惯性环节简化代替,由此利用经典的控制方法设计的.控制器很难进一步提高厚度控制的精度,难以适应轧制工艺2) 对于闭环系统而言,系统设定值的精度难以保证,从而限制了AGC的控制精度.3) 影响出口厚度波动的因素很多..测厚仪的安装位置,导致了检测到的出口厚度在反馈控制上的滞后4)2 方案论述及确定2.1液压压下装置的特点随着工业的发展,带钢的轧制速度不断提高,产品的尺寸精度日趋严格.特别是采用厚度自动控制(AGC)系统以后,电动压下装置已远远不能满足工艺要求.目前,新建的冷连轧机组生产线几乎全部采用液压压下装置,热带钢连轧机精轧机组最后一架轧机也往往装有液压压下装置.所谓全液压压下装置,就是取消了电动压下装置,其辊缝的调整均由带位移传感器的液压缸来完成.与电动压下装置比较,全液压压下装置有以下特点:1.快速响应性好,调整精度高;2.过载保护简单可靠;3.采用液压缸压下可以根据需要改变轧机当量刚度,轧机实现从“恒辊缝”;4.到“恒压力”轧制,以适应各种轧制及操作情况;5.较机械传动效率高;6.便于快速换辊,提高轧机作业率.2.2方案论证及确定经过小组讨论,针对该设计要求的工序动作,拟定以下三种方案:第一种方案原理分析:该系统采用双变量液压泵作为油源,一台工作,一台备用,这样可以减少故障带来的经济损失,采用伺服变量泵可以调节流量,来控制系统运行速度,达到调速的目的,在控制油路上采用三位四通电磁伺服阀来进行调平,当系统出现倾斜时,位移传感器和压力传感器反馈信息,控制伺服阀调整进油,以保持两个液压缸同步,该系统将冷却油路设在系统回油路上,不需要另外的液压泵进行循环,这样减少了液压站投资.该系统结构紧凑,既能达到调速.的目的,又能实现双缸同步运行方案一图2-1第二种方案原理分析:辅泵有三个作用:给主泵柱塞泵供油以延长主泵工作寿命、给执行元件液压缸有杆腔产生被压、使多余流量通过溢流阀形成冷却循环;主泵定为恒压变量泵,保证阀台伺服阀的工作稳定性;主泵出口的电磁溢流阀做安全阀用,蓄能器作为辅助动力源,两个温度控制器的作用是保证冷却器和加热器使用时的适当温度.该系统冷却回路单独使用液压泵进行循环,这样减少了系统回路的压力损失,在总油路上有一个较大的蓄能器进行保压蓄能,在两个液压缸的压下油路上没有进行保压,不能及时补充压下压力.:方案二图2-2第三种方案原理分析:该系统使用定量泵进行供油,使用伺服阀进行变换油路,而且该系统使用的是单作用缸,需要另外使用平衡缸,该系统也没有调速回. 路,不能实现变速,也没有保压蓄能设备,不能及时补充系统压力方案三2-3 图综合分析以上三种方案的优缺点,第一种方案经济,结构紧凑,又能达到设.案方种一第择选故,作动的求需计.3液压系统主要参数计算及元件选择3.1 初选系统工作压力,初定系统工作压力根据各种机械常用的系统工作压力数据,由表3-1Ps=10Mpa各种机械常用的系统工作压力图3-1 表类型重型机械、拉床龙门刨床磨床建筑机械、机床起重运输机械液压凿岩机工作压0.8~2 3~5 2~8 8~10 10~18 20~32/MPa力3.2 液压缸尺寸计算及选择3.2.1缸尺寸的确定前面初选系统压力Ps=10Mpa已知:总轧制力Fmax=2.6MN则液压缸最压下力Fmax1 = 1.3MN液压缸压下速度Vc=15mm/s液压缸最大行程S=150mm1)活塞直径D的确定4F4?1.3D???0.441m0?KP3.14?0.85?10S(3-1)D=500mm取K=0.85 K为负荷系数,取其中d)确定活塞杆直径20.6 因为取d的比值大于与Do0.7Do=d 所以?500=350mmd=0.7得出负载压力的计算3.2.2d?500mm轧辊直径1d?900mm支承辊直径2??32?3?7.8?2500?10.21)t?1450?m?10?(14??32?3?7.8?107.)19?m?1450?10t?(900?244N104?g?9.(F?m?m)?231P?0.5MPP为系统背压,根据参考,估计BB22dD?c??0.512D(3-2)??JJ?0.92gg液压缸的机械效率,取表3-2 各工况负载压力压力计算式工况数值610?1F.31?0.51?2P??cp?.1?B1快下8.27MP?JA292500?.?0g14610?F.312???51?0.?2.1cpP?B28.27MP慢下?JA292.500??0g144F104?9.3?0cp?.51?2.1P???B1快上2.09MP?JA2292.(500?300)??0g243.2.3系统流量计算系统流量3-3表工况速度计算式数值??23mL6010.018?500???0Aq?v?快下211.9518?v111mins41??23mL60???.?Av?q0015500?10慢下15?v176.6122mins42?32?260??028?(50010?300?)q?vA?0.液压缸主要尺寸确定3.3L=150mm 液压缸的最大行程1) 最小导向长度2)是指活塞杆全部伸出时,从活塞宽度的中点到导向套滑动面H最小导向长度.中点的距离500150LDmm260H?????)H=350mm (3-3 取max22202B=(0.6~1)D 根据液压缸工作压力和密封方式确定,一般取活塞宽度B300mm?500?B?0.6D?0.6所以)缸筒壁厚计算3DP max?????2(3-4)40512.275?8.?P?1.5P?1.)MP (P取最大工作压力max?MP?353取安全系数45热轧无缝钢管,调质处理,屈服强度缸体选用s?????88.4353/?25/n?MP n=5 材料的许用应力为???2?88.225s PD12.405?500max???35?.14mm??500?2?240?580mmD?D??mm40?,缸的外径考虑一定的刚度取14)缸筒底部厚度P1.5?8.27max??0.433?500?.?0433D?81.17mm???88.25底部设计为平面?mm?85取)导向套滑动面长度5A?(0.6~1)d 80mm?D导向套滑动面长度,时,取A?0.6d?0.6?350?210mm 所以.为保证最小导向长度,不宜过分的增大导向套长度和活塞宽度,最好的办法度长K,其加装一个隔离套之是在导向套与活塞间mm95?300)/2??B)/2?350-(210HC?-(A 3-5 ()3.4 液压缸强度和稳定性计算:3.4.1缸筒壁厚的校核DP y?????2,由《机械设计手册》公式23.6—22??????,—缸体材料许用应力,取MPa)=120(Py =1.25P 则,Py -实验压力,取DP251.900x20x y mm?105??93.75mm???120?22?.由于故缸筒壁厚符合要求=105mm >102.5mm,活塞杆稳定性验算3.4.2与活塞杆直L因为活塞杆在工作时承受很大的压力,所以当活塞杆计算长度活塞杆计算长度就是就是在它.之比大于10时,则应该校核活塞杆的稳定性D径,L=0.45m全部伸出时活塞杆端支点与缸安装点之间的距离,本液压缸计算长度. ,故不作活塞杆稳定性校核因为L/D=0.45/0.5<10液压泵和电动机的选择3.53.5.1选择液压泵快速上行时工作压力最大,估取沿程压力1)计算液压泵的最高工作压力.(MP0.5??p?损失1MP775?8.0??p?p?8.27?.?p)(3-61b)计算液压泵的流量,根据前面的流量计算结果,并取系统泄漏修正因2(K=1.1数'min14L?.95233.??q?Kq1.1211快速上行需泵流量b1''q?Kq?1.1?176.6?194.26Lmin慢速上行需泵流量b2.'''minL168.147?184.96q?Kq?1.1?慢速下行需泵流量b3选择液压泵的规格(3)根据压力和流量值,查相关液压元件产品目录,选取变量柱塞泵,排量为r250mLV?min1000rn? 32MP,额定转速为,容积效率为0.95,额定压力为b. 250CCY14-1B,变量方式为伺服控制,生产厂家:启东高压泵厂型号为液压泵3-1 图3??minL1000?237.5?n?25010?0.95?q?V则:泵的实际流量(3-bvbb 7)3.5.2选择电动机从前面的压力计算图可知,快速上行时,液按液压泵最大功率确定电机功率. 此时液压泵的压力为压缸压力最大.MP77?8.??8.270.5?p?p??p)(3-81b流量为3??minL.595?1000?q?Vn?250?102370?.)(3-9 bvbb 则电动机功率3?6)q(p105?77?10?237..8maxbb KW.578.W?38?P??38571b?60?0.9 3-10()b980rmin,型号为Y250M45KW选用功率为,转速为的电动机.液压辅助元器件选择3.63.6.1过滤器选择1)过滤器一般由滤芯和壳体组成由滤芯上无数微小间隙和小孔组成通流面积.当混入液压介质的污染物粒子的尺寸大于微小间隙活小孔时,杂质被阻隔分离出来.过滤器按精度分可分为粗过滤器和精过滤器两种;按过滤方式分为表面性过滤器、深度性过滤器和中间型过滤器三种;按滤芯的结构分为网式过滤器、线隙式过滤器、纸式过滤器、磁性过滤器、烧结式过滤器、不锈钢纤维式过滤器和合成树脂过滤器.选择过滤器时,应考虑以下几方面:(1) 根据使用目的选择过滤器的类型,根据安装位置情况选择过滤器的安装形式.(2) 过滤器应有足够大得通油能力,并且压力损失要小.(3) 过滤精度应满足液压系统或元件的所需清洁度要求.(4) 滤芯使用的滤材应满足所使用工作介质的要求,并且有足够的强度.(5) 过滤器的强度及压力损失是选择是需要重点考虑的因素,安装过滤气候会对系统造成局部压降或产生背压.(6) 滤芯的更换及清洗要方便.(7) 应根据系统的需要选择合适的滤芯保护附件.(8) 结构应尽量简单、紧凑、安装形式合理.2)辅泵出口过滤器的选择选用过滤器为泵出口过滤器,型号号 ZUH-63 10S,数量:1,过滤精度为?.10.为精过滤器)回油过滤器的选择3选用过滤器为油箱回油过滤器,为油箱内置回油过,过滤精度为2,数量:滤器,型号号 XU-63 50S?.50蓄能器的选择3.6.2)蓄能器压力的选择1.蓄能器是液压系统中一种能量储存装置,它存储多余的压力油液,并在需要蓄能器的种类很多,分为重力式、弹.时放出来供给系统,补充系统流量和压力选择蓄..常用的是充气式,它又分为活塞式,气囊式和隔膜式三种簧式和充气式流量或气体容)(排能器应考虑以下因素:工作压力及耐压性;公称容积及允许吸其次还要考虑到蓄能器的重量级占用积;允许使用的工作介质及介质温度等等.蓄能器为压力容.的空间问题;价格、质量及使用寿命;安装维修的方便器,必须有生产许可证才能生产,所以,一般不能自行设计,制造蓄能器,应选蓄能器3-2图择专业厂家的产品.本系统中选用气囊式蓄能器.2)蓄能器容积的选择气囊式蓄能器惯性小,反应灵敏,结构紧凑,质量轻,充气方便,一次充气后能长时间的保存气体,在液压系统中应用广泛.估算系统压力,选取管路中蓄能器型号,NXQ1-L4,公称容积4L,公称通径32mm,公称压力31.5MP,生产厂家:上海东方液压件产泵站的蓄能器作用是:做辅助动力源,根据经验选用>20L所以,主泵出口处选择型号:NXQ1-L25,公称容积25L,公称通径40mm,公称压力31.5MP,生产厂家:南京锅炉厂.3.6.3其他元器件根据在系统中各阀的最大工作压力和流量选择液压阀.选出的液压阀如下表:表3-4 液压系统各元件一览表3.7油箱尺寸计算3.7.1油箱容量的经验公式?q?V(3-11)b式中,q液压泵的额定流量——b a 与系统压力有关的经验系数,——~107,高压取8低压取2~4,中压取5~L1625?250?5q?6.5V?6.3-3蓄能器图取b油箱主要设计参数如图所示.选取油箱长b、宽a、高h之比为2:1:1,则V=abh得a=1175mm,b=1175mm,h=1175mm3?1622?1175LV油箱容量应能保证液压系统工作时,其最低油面高于滤油器上端200mm以上,以防止泵吸入空气.液压系统停止工作时,其最高液面不得超过油箱高度的80%.而当液压系统中的油液全部返回油箱时,油液不能溢出油箱外.3.7.2油箱结构的设计1)过滤器的设置油箱的回油口一般都设置系统所要求的过滤精度的回油滤油器,以保持返回油箱的油液具有允许的污染等级.油箱的排油口(即泵的吸油口)为了防止意外落入油箱中的污染物,有时也装设吸油网式过滤器.由于这种过滤器侵入油箱深处,不好清理,因此,即使设置,过滤网目也是很低的,一般为60目以下.本油箱选择的是XU-63 50S,数量:22)设置油箱的主要油口油箱的排油口与回油口之间的距离尽可能远些,管口应插入最低油面之下,以免发生吸空和回油冲溅产生气泡.泵的吸油管所装过滤器的下端距油箱底面距离回油管管口应插入最低油面以下,离油箱底面距离应大于管径的20mm.不小于.45度斜口,以增大液流面积倍.吸油管和回油管管口宜切成2~3 )油箱隔板布置3隔板将吸油、回油管路隔开,防止回油被直接吸走,油流中的气泡与杂质分3/4.~.隔板的高度为油面高度的2/3离和沉淀.本设计的隔板为整体式,底部有过油孔油箱.)在开式油箱上部的通气孔上必须配置空气滤清器.兼作注油口的作用4的注油口一般不从油桶中将油液直接注入油箱,而是经过过滤车从注油口注入,.这样可以保证注入油箱中的油液具有一定的污染等级.)放油孔的安装5放油口要设置在油箱的底部最低位置,使患有换油时油液和污物能顺利地从在设计油箱,从结构上应考虑清洗换油的方便,设置清油孔,以便于.放油孔流出.油箱内沉淀物的定期清理.该油箱的放油孔根据要求设置在油箱的底部,直接焊接管接头连接截止阀5341268109图3-3 1—吸油管2—过滤器3—空气过滤器4—回油管5—盖板1—吸油管 2—过滤器 3—空气过滤器 4—回油管6—液位指示器7、9—隔板8—放油管液压压下系统性能验算3.7板 6—液位指示器 7.9—隔板 8—放油管盖5—:1) 进油路沿程压力损失: 主要是液压缸推动下刀架在实施剪切时进油路中的压力损失.30?时的运动粘C,20890kg/m为液压油,其密度L-HL32本系统压力较高,故选用.2?4,进、,管路直径d=30mm度为,油路中流量为泵的流量为250L/min s10m1.0?20m. 回油路管长约250L/min流量:3?q410250?4?1流速:(3-12)5.9m/s???v22??60?0.d03?3.0.9?0vd5?R?,属层流雷诺数:=1770<2320?)=75/1770=0.042e4??101?(沿程阻力因数:3-13=75/6?22?10?5.l9v?20890???p?0.433MP?0.042??沿程压力损失12030.d2,两个个三局部压力损失:进油路经过两个三位四通换向阀?=1.12个直角弯头位四通伺服阀阀7,一个单向阀MP10.?P?,?1117?p()2??p()???p?2?p()3-(3e2?vqqq223e2er11e2qqq3ee2e1 14)6?10890?250250250222?121.()?7?(2?)?2?0.1?)?0.2?(?2?0.212008080=7.8MP回油路2):沿程压力损失流量:min5L250?127.q?cq?0.51?12?3q410?127.54?13.008m/s(3-15)流速:v???22???60.03d?0vd3.008?0.03?R?=902.4<2320 雷诺数:,属层流?=75/沿程阻力因数:=75/902.4=0.083e?4?1?1022?6?10?.20890?3l008v???2228.MPp?0?.083??0沿程压力损失1d20.032个直角5,局部压力损失:进油路经过两个三位四通换向阀?=1.12弯头2?vq2?25)?(?2?p?p(3-16)1r2e2q1e?6105890?127.2?0.2?()?2?5?1.12??1.02MP802进回油路总压力损失:进油路:=8.233MPa:=1.2428MPa路油回4 液压压下系统的安装与维护4.1液压压下系统的安装液压系统安装质量的好坏是关系到液压系统能否可靠工作的关键.必须科学、正常、合理地完成安装过程中的每个环节,才能使液压系统能够正常运行;充分发.挥其效能1. 安装前的准备工作1)明确安装现场施工程序及施工进度方案.2)熟悉安装图样,掌握设备分布及设备基础情况.3)落实好安装所需人员、机械、物资材料的准备工作.4)做好液压设备的现场交货验收工作,根据设备清单进行验收.通过验收掌握设备名称、数量、随机备件、外观质量等情况,发现问题及时处理.5)根据设计图纸对设备基础和预埋件进行曲检查,对液压设备地脚尺寸进行复核,对不符合要求的地方进行处理,防止影响施工进度.2 .液压设备的就位1)液压设备应根据平面布置图对号吊装就位,大型成套液压设备,应由里向外依次进行吊装.2)根据平面布置图测量调整设备安装中心线及标高点,可通过调整安装螺栓旁的垫板达到将设备调平找正,达到图纸要求.3)由于设备基础相关尺寸存在误差,需在设备就位后进行微调,保证泵吸油管处于水平、正直对接状态,4)油箱放油口及各装置集油盘放污口应在设备微调时给予考虑,应是设备水平状态时的最低点.5)应对安装好的设备做适当防护,防止现场脏物污染系统.6)设备就位调整完成后,一般需对设备底座下面进行混凝土浇灌,即二次灌浆.4.2 液压压下系统的维护加油时液压油必须过滤加注,加油工具应可靠清洁.不能为了提高加油速度而去掉油箱加油口处的过滤器.加油人员应使用干净的手套和工作服,以防固体杂质和纤维杂质掉入油中.保养时拆卸液压油箱加油盖、滤清器盖、检测孔、液压油管等部位,造成系统油道暴露时要避开扬尘,拆卸部位要先彻底清洁后才能打开.如拆卸液压油箱加油盖时,先除去油箱盖四周的泥土,拧松油箱盖后,清除残留在接合部位的杂物(不能用水冲洗以免水渗入油箱),确认清洁后才能打开油箱盖.如需使用擦拭材料和铁锤时,应选择不掉纤维杂质的擦拭材料和击打面附着橡胶的专用铁锤.液压元件、液压胶管要认真清洗,用高压风吹干后组装.选用包装完好的正品滤芯(内包装损坏,虽然滤芯完好,也可能不洁).换油时同时清洗滤清器,安装.滤芯前应用擦拭材料认真清洁滤清器壳内底部污物.参考文献[1].邹家祥,轧钢机械,北京,冶金工业出版社 2005[2].朱新才等,液压传动【M】,重庆,重庆大学出版社 2009[3].金兆光,冷轧机压下油缸的设计,北京,化学工业出版社 1998[4].机械设计手册缩委会,机械设计手册(单行本),液压传动与控制【M】,北京,机械工业出版社 2007[5].成大先,机械设计手册,北京,化学工业出版社 20062006张利平,液压控制系统及设计,北京,化学工业出版社[6]. 2009[7].朱新才,液压传动与气压传动,北京,冶金毕业出版社 2008600例,北京,化学工业出版社陆望龙,典型液压元器件结构[8].[9].陈晶,液压缸,北京,化学工业出版社 2009。
第三章轧辊调整平衡及换辊装置

轧辊调整、平衡及换辊装置
采用电动压下和液压压下相结合的压下方式。 在现代的冷连轧机组中,几乎全部采用液压压下装置
轧辊调整、平衡及换辊装置
2、慢速电动压下装置主要结构形式 由于慢速电动压下的传动速比高达1500~2000,同时又要求 频繁的带钢压下,因此,这种压下装置设计比较复杂,常用的 慢速电动压下机构有以下三种形式。 一种是由电动机通过两级蜗轮蜗杆传动的减速器来带动压下 螺丝的压下装置,如图3—7所示。它是由两台电动机传动的, 两台电动机1之间是用电磁离合器3连接在一起的。当打开离合 器3之后可以进行压下螺丝的单独调整,以保证上轧辊调整水平。 这种压下装置的特点是:传速比大、结构紧凑。但传动效率低、 造价球面蜗杆设计及制造工艺技术不 断的发展与完善,这种普通的蜗轮蜗杆机构已逐步被球面蜗轮 蜗杆机构所代替。这样一来不但传动效率大大提高,而且传动 平稳、寿命长,承载能力高。
轧辊调整、平衡及换辊装置
第二种是用圆柱齿轮与蜗轮蜗杆联合减速的压下传动装置,如 图3—8所示。它也是由双电动机1带动的,圆柱齿轮可用两级 也有用一级的。在两个电动机之间用电磁离合器3连接着,其目 的是用来单独调节其中一个压下螺丝的。为了使传动装置的结构 紧凑,可将圆柱齿轮与蜗轮杆机构均放在同一个箱体内。这种装 置的特点是:由于采用了圆柱齿轮,因此传动效率提高了,成本 下降了,所以这种装置在生产中较前一方案应用更为广泛,通常 多用热轧板带轧机上。
轧辊调整、平衡及换辊装置
3.3轧辊辊缝的对称调整装置
轧辊调整、平衡及换辊装置
轧辊辊缝对称调整是指轧制线固定下来, 上、下工作辊中心线同时分开或同时靠 近。图3—3为德国德马克公司高速线材 轧机精轧机组的斜楔式摇臂调整机构。
轧辊调整、平衡及换辊装置
棒材轧机液压系统设计说明
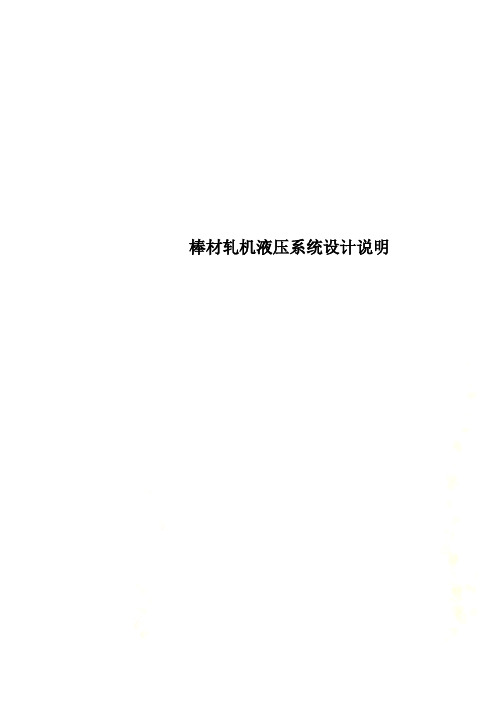
棒材轧机液压系统设计说明毕业设计棒材轧机液压系统设计说明书目录1.前言 (1)2.绪论 (2)2.1液压技术概况 (2)2.2本课题主要研究内容 (2)2.3设计步骤 (3)3.液压系统的工作要求 (5)3.1液压系统的组成 (5)3.2棒材轧机液压系统工作原理 (5)3.3液压系统参数计算 (5)3.3.1确定液压缸负载 (5)3.3.2液压缸主要尺寸的确定 (6)3.3.3确定液压泵的流量、压力和选择泵的规格 (7)3.3.4与液压泵匹配的电动机的选定 (8)4.确定液压系统方案、绘制液压系统原理图 (9)4.1确定液压系统方案 (9)4.1.1液压基本回路 (9)4.1.2选择液压回路 (9)4.2绘制液压系统图 (10)4.2.1将基本回路组成系统原理图 (10)4.2.2液压元件选择 (11)4.3液压系统的验算 (11)4.3.1系统压力损失计算 (12)4.3.2系统效率计算 (13)5.液压站的设计 (15)5.1液压站简介 (15)5.2油箱设计 (15)5.2.1油箱有效容积的确定 (16)5.2.2油箱的结构设计 (17)5.3油箱结构 (20)5.4液压站的结构设计 (21)5.4.1液压泵的安装方式 (21)5.4.2液压泵与电动机的连接 (22)5.5辅助元件 (24)5.5.1滤油器 (24)5.5.2空气滤清器 (24)5.5.3液压油 (24)5.5.4液压控制装置的集成 (24)5.6绘制装配图 (25)5.7液压系统清洗、使用与维护 (26)5.7.1清洗液压系统 (26)5.7.2系统的使用和维护 (27)6.结论 (29)谢辞 (30)参考文献 (31)外文资料 (32)1.前言毕业设计是我们在学完大学全部课程及进行完生产实习之后进行的,它是对我们大学三年学习的一次深入的综合性考察,也是我们步入社会所要从事工作的提前预测,同时还是我们将在校期间所学到的理论基础知识运用到实践中去解决问题的一次很好的锻炼。
- 1、下载文档前请自行甄别文档内容的完整性,平台不提供额外的编辑、内容补充、找答案等附加服务。
- 2、"仅部分预览"的文档,不可在线预览部分如存在完整性等问题,可反馈申请退款(可完整预览的文档不适用该条件!)。
- 3、如文档侵犯您的权益,请联系客服反馈,我们会尽快为您处理(人工客服工作时间:9:00-18:30)。
1绪论液压传动是一门较新的技术,是有很多其他传动所不能比拟的独特优点。
因此,近年来,各种机械设备应用液压技术越来越普遍。
世界各国对液压机械装置的需求量也急速上升。
目前,液压技术不仅应用于一般机械、高精密机械和超大型设备,而且还应用于航海与海洋技术开发技术中。
同时,也正应用于各种生活设施中。
总之,液压技术已经广泛地深入到各个领域。
我国的液压技术发展的也很快。
特别是在工程机械、锻压机械、金属切削机床、采掘设备、轧钢设备、农业机械等机械制造和国防工业等一些部门。
液压技术的应用日益增多。
现在,我国已经制定了一些液压传动的技术标准,自行设计了各种液压元件,在标准、系列化、通用花方面做了大量工作。
在液压技术的研究方面也取得了可喜的成果。
1.1 液压传动技术的发展和趋势远在17世纪至19世纪,欧洲人对液体力学、流体传动、机构学及控制理论与机械制造就做出了主要贡献。
其中包括1648年法国的B.帕斯卡提出的液体中压力传递的基本规律。
1850年英国工程师William George Armstrong关于液压蓄能器的发明以及1895年英国人约瑟夫·布瑞玛的第一台液压机的英国专利。
这些贡献与成就为20世纪的液压传动与控制技术的发展奠定了科学与工艺基础。
19世纪,工业上所使用的液压传动装置是以水作为介质,因其密封问题一直未能很好的解决以及电器传动技术的发展竞争,曾一度导致液压技术停滞不前。
20世纪30年代后,由于车辆、航空、船舶等功率传动的推动,相继出现了斜轴式及弯轴式轴向柱塞泵、径向和轴向液压马达。
1936年Harry Vickers发明了先导控制阀为标志的管式系列液压控制元件。
第二次世界大战期间,由于军事上的需要,出现了以电液伺服系统为代表的响应快、精度高的液压元件和控制信号。
从而使液压技术得到迅猛发展。
20世纪50年代,随着各国经济的恢复和发展,生产过程自动化的不断增长,使液压技术很快转入民用工业,在机械制造、其中运输机械及各类施工机械、船舶、航空等领域得到广泛发展。
20世纪60年代以来,随着原子能、航空航天技术、微电子技术的发展液压技术在更深更广阔的领域里得到了发展。
这期间出现了板式、叠加式液压阀系列。
发展了以比例电磁铁为电器——机械转换的电液比例控制阀并被广泛用于工业控制中,提高了电液控制系统的抗污染能力和性能价格比。
70年代出现了插装式系列液压元件。
80年代以来,液压技术与现代数学、力学微电子技术、计算机技术、控制科学等紧密结合,出现了微处理机、电子放大器、传感测量元件和和液压控制单元相互集成的机电一体化产品,提高了液压系统的智能化程度和可靠性,并应用计算机技术开展了对液压元件和系统的动、静态性能数字传真及结构的辅助设计和制造。
如前所述,随着科学技术的进步和人类环保、能源危机意识的提高,近20年来,人们重新认识和以历史上以纯水作为工作介质的纯水液压传动技术,并在理论上和应用研究上,都得到了持续稳定地复苏和发展。
正在逐渐成为现代液压传动技术的热点技术和新的发展方向之一。
21世纪必将是信息化、网络化、知识化和全球化的世纪。
信息技术、生命科学、生物技术和纳米技术等新科技的日益进展,必将对液压传动和控制技术的研究、设计观念及方法。
对包括液压阀在内的各种液压产品的结构与工艺的应用领域带来革命性的变化。
液压技术也必将广泛应用诸多高科技的成果。
如自动化控制技术、微电子技术可靠的技术及其新的工艺、新材料等使传统的液压技术有新的发展,也使液压系统及其元件的质量、水平有一定的提高。
起发展趋势必将集中在如下几个方面:1、减少能耗,充分利用能量,提高效率;2、提高控制功能,适应机电一体化发展;3、提高可靠性、寿命、安全性和维修性;4、环境保护及低噪音、振动,无泄漏;5、适应国际市场的需求。
1.2 课题的研究内容和方法近年来,国外轧钢行业相继出现了高效化、自动化等低能耗环保型新轧钢企业。
二辊轧机液压辅助系统作为其中一个环节也不容忽视,值得研究。
总的来说,液压传动技术的发展方向是:大型化、连续化、高速化和自动化。
发展的途径是,提高产品性能、高效节能、用微电子技术改进传统液压系统、发展机电一体化产品、提高设备使用寿命和改善操作性能等。
这无疑对液压元件同时有很高的要求:1、高精度和高响应。
提高电液位置控制系统的精度。
如轧机板厚、板宽等2、提高元件的可靠性。
如电磁阀的使用寿命要达到1000万次以上。
3、广泛采取集成化(插装阀、叠加阀等)和符合化元件及系统。
4、易维修,实现液压系统的故障自动诊断。
5、适应IS014000环境保护标准要求,开发并应用水压技术。
轧辊磨损后,几何尺寸和轧辊形状均将发生变化,为了保证轧材质量,必须及时更换轧辊。
轧制速度的提高,更加加速了轧辊的磨损,使得轧辊的更换次数越来越频繁。
然而换辊装置的基本类型很多,但利用液压系统作为辅助系统的换辊装置较其他方法来比,更能缩短换辊时间,有利于保证产品质量,减少停机时间,提高轧机作业率,增加产品产量和降低成本。
而且,由液压系统组成的换辊装置类型结构简单,易于实现自动化且在换辊过程中灵活多变,容易控制。
在现代化的冷轧中较为常用的换辊装置如下:1、横移小车式换辊装置这种装置主要由换辊车和推杆组成。
换辊车是一台双层电动小车,车上带有二对轨道的平台(可沿车架滑道作横向移动)。
平台下面也有一台小车,它可以沿轧机旁铺设的轨道纵向移动。
其主要的换辊步骤可简要描述为:换辊小车前进至轧机旁;推杆推出旧轧辊至小车上;换辊小车横移;新轧辊被拉回轧机内;换辊小车退回。
2、横移平台式换辊装置它由换辊小车和横移平台组成。
换辊小车作用于横移小车式一样。
横移平台的作用是当旧轧辊拉出后,将新轧辊对准轧机机座的中心线,以便将新轧辊顺利推入机座中。
其主要的换辊过程有:旧轧辊拉出;横移平台横移;新轧辊推入轧机座;旧轧辊移走;横移平台恢复原位。
除了上述的两种方式外还有,转盘式换辊装置、套筒换辊装置和C型钩换辊装置等。
从理论角度和上述的换辊方式来分析,本设计的液压系统由如下几个液压缸组成:平衡缸、上升缸、抱紧缸和换辊缸。
通过这几个液压缸的动作将两根1.2米长,直径为0.8米的轧辊平稳更换。
设计时,不仅要满足系统的最终目的——换辊,还充分考虑所设计系统的可实施性,及在换辊过程中的平稳和快速。
尤其是阀块在实际工作中的工作情况和换向阀,液控单向阀的选取。
除了考虑整个系统的压力,流量的因素,各个元件的实用性,经济性等也是很重要的因素。
2 设计要求及系统工作过程简介2.1 设计要求本次设计的液压系统为板带轧机换辊装置的液压传动系统。
在设计过程中要求将二辊轧机中的长度为1.2米,直径是800mm 的两个轧辊能被顺利推出和拉回,该系统通过五个液压缸来执行全部动作,在各个动作中,要求液压缸动作平稳,压力冲击小。
能源及控制部分由液压站提供(如图2.1),而操作控制则由电气系统控制完成,液压缸是系统的执行部分。
图2.1 液压泵站2.2 系统工作过程整套轧机设备的液压系统的工作过程是:当电动机通电工作后,使得液压泵从油箱吸油。
从液压泵出来的压力油经管式单向阀后给蓄能器充进压力油,然后压力油进入控制元件电磁换向阀。
先使平衡缸的控制阀带电进行工作,压力油进入平衡缸的无杆腔端,活塞杆伸出,到达行程末端停止。
其次是抱紧缸在电磁换向阀控制下工作——抱紧轧辊,抱紧机构是连接在刚性机架上的,完成抱紧的动作后,上升缸在控制阀的作用下提升整个机架,到达换辊位置。
控制阀处于中位,液压回路锁紧。
换辊缸开始动作,在推力和惯性力的作用下使得轧辊推出完成一个工作循环。
空气滤清器滤清器阀块组电动机液压泵3液压系统设计本系统是全套的液压系统设备,根据现场实际情况和液压传动系统设计过程,确定系统的基本组成如下:系统由多个缸组成,每个缸都与控制阀结合组成单独的回路,系统的液压原理图如图3.1所示。
图 3.1液压系统原理图3.1系统回路设计方案液压回路就是将液压泵、液压马达、液压缸、液压阀、管路、油箱等液压元件有次序有组织的联接起来。
能够实现某种特殊的功能和性能。
按照作用的不同,液压基本回路包括压力控制回路、速度控制回路、方向控制回路、多执行元件动作回路、液压油源控制回路等。
根据现场实习情况和所学的知识分析,该系统应该由五个基本回路组成。
油源回路、平衡缸回路、上升缸回路、抱紧缸回路、换辊缸回路。
虽然回路较多,但是每个回路的功能相似,进而每个回路的液压元件也很相同。
这可以从图3.1清楚的看到。
3.1.1 油源回路图3.2油源回路Array由图3.2所示,该回路由电动机、变量柱塞泵、管式单向阀、溢流阀、压力表(开关)、空气滤清器、回油滤油器和液位计组成。
油源回路除了有效地供给液压缸等执行器必要的功能、性能所需的流量和压力外,还考虑其安全性、温度的调节及油液污染的清除等情况。
这个回路是操纵二位二通电磁换向阀使溢流阀卸荷的。
是定量泵并联溢流阀回路。
单向阀是防止因系统压力突然增加而损害液压泵;溢流阀起到卸荷的作用;滤油器是液压系统中对油液进行过滤的重要元件。
3.1.2 平衡缸平衡系统回路(图3.3)图3.3平衡缸平衡系统回路在这个回路中用到双单向节流阀、液控单向阀和电磁换向阀。
双单向节流阀起到出口节流调速控制;液控单向阀用于对液压缸锁闭、保压,同时用于防止活塞杆在轧辊重力作用下的自动下滑。
通过改变电磁换向阀的工作位置而改变油液的流动方向[3]。
3.1.3 抱紧缸同步动作系统回路(图3.4)这个回路的组成和平衡缸回路近似一样。
各个元件的功能也相同。
只是这个回路的双单向节流阀是进油节流调速控制。
在将两根轧辊抱紧的过程中,要求两个液压缸能实现同步,再次在抱紧过程中要求压力保持性能好。
液压缸不允许有泄漏现象,惯性力不能太大,动作应该缓慢而稳。
3.1.4 上升缸提升系统回路们在换辊的过程中起的作用也大同小异。
上升缸上升时要保持平稳的特性,而且在停止时保持锁紧防止下滑,将整个机架提升都是通过该回路来实现。
3.1.5 换辊缸换辊系统回路(图3.5)由于这个回路中液压缸是水平放置的所以不再需要液控单向阀的锁紧。
工作时要平稳的推出旧轧辊和平稳的拉回新轧辊,所以要求其缓慢动作[2]。
图3.4 抱紧缸同步动作系统回路3.2液压阀块的设计液压阀块是液压系统无管化连接方式的一种常用方法,Array它不仅能简化液压系统的设计和安装,且便于实现液压系统的集成化和标准化。
它有以下特点1、利用标准元件或标准参数的元件,按典型动作与块体构成标准回路,选块叠积组成系统,大大的缩短了设计和制造周期。
2、基本回路和液压系统的变化灵活。
3、省去了大量管子和接头,结构紧凑,占地面积小。
4、元件距离近,油道短,压力损失小,效率高。
5、无管子引起的振动、泄漏小,系统稳定性好。