应用数据分析法进行简易的设备故障诊断
大数据背景下机械故障的智能诊断发展研究

大数据背景下机械故障的智能诊断发展研究随着大数据技术的不断发展和普及,各行各业都在探索如何利用大数据技术来提高工作效率和降低成本。
机械设备的维护和故障诊断一直是一个重要的领域,而在大数据背景下,如何利用大数据来进行机械故障的智能诊断成为了一个备受关注的话题。
本文将从大数据技术在机械故障智能诊断中的应用现状、存在的问题以及未来发展趋势三个方面展开研究。
一、大数据技术在机械故障智能诊断中的应用现状1. 传统故障诊断方法的局限性传统的故障诊断方法主要依靠专业技术人员的经验和观察,存在主观性强、效率低、依赖人员素质等问题。
而且在实际工程中,机械设备所产生的数据量巨大,传统的故障诊断方法无法有效地处理这些数据,导致诊断结果不够准确和及时。
大数据技术以其高效的数据处理能力和强大的数据分析能力,为机械故障智能诊断提供了新的解决方案。
通过收集、存储和分析机械设备产生的数据,可以实现对机械故障的自动诊断和预警。
利用大数据技术可以对机械设备的运行状态进行实时监测和分析,通过对数据的挖掘和分析,可以及时识别出故障的迹象,提前进行预警和维护,避免故障的发生。
目前,大数据技术在机械故障智能诊断领域已经取得了一些成功的应用案例。
某公司利用大数据技术对其生产车间的机械设备进行了监测和分析,通过对设备产生的数据进行挖掘和分析,成功地识别出了一台设备存在的故障隐患,并采取了相应的维护措施,避免了设备的损坏和生产线的停机。
二、存在的问题虽然大数据技术在机械故障智能诊断中已经取得了一定的进展,但是在实际应用中还面临着一些问题和挑战。
1. 数据采集和整理的难度机械设备产生的数据种类繁多、格式不一,数据采集和整理的难度较大,需要消耗大量的人力和物力资源。
2. 数据分析和处理的复杂性机械设备产生的数据量巨大,对数据的分析和处理能力提出了较高的要求,传统的数据分析工具和方法无法满足大数据的处理需求。
3. 系统的智能化程度不高目前大部分机械设备的监测和诊断系统还处于人工干预较多的状态,缺乏智能化和自动化的特点,导致诊断的准确性和效率不够高。
设备故障的分析与诊断方法

经验诊断法
根据维修人员的经验,通过触 摸、听声、观察等方式对设备 进行诊断,判断设备是否存在 故障。
现代诊断法
利用现代科技手段,如振动分 析、红外线检测、超声波检测 等,对设备进行全面检测和诊
断。
02
设备故障分析方法
故障模式分析
总结词
故障模式分析是一种通过研究设备故障的表现形式,找出故障发生的原因和机理的分析 方法。
案例三:工业设备的故障诊断与修复
总结词
工业设备的故障通常表现为生产线停滞、设备效率降 低、能源消耗增加等。
详细描述
对于工业设备的故障诊断,可以采用生产流程分析、 能源消耗分析、设备性能测试等方法。通过这些方法 ,可以检测到工业设备的异常,并确定故障的具体位 置和原因。在修复故障时,可能需要调整工艺参数、 更换损坏的部件或进行设备大修。
实时监测与预警
实时监测设备状态
01
通过实时监测设备的运行参数和状态,及时发现异常情况并进
行处理。
预警系统
02
设置预警阈值,当设备运行参数超过预设的阈值时,预警系统
会及时发出警报,提醒工作人员进行处理。
在线专家诊断系统
03
利用在线专家诊断系统,对设备故障进行快速准确的诊断,提
供针对性的维护建议和解决方案。
基于知识的诊断方法
总结词
基于专家经验和知识的方法,通过专家系统 、模糊逻辑等技术进行故障诊断。
详细描述
基于知识的诊断方法利用专家经验和知识, 通过专家系统、模糊逻辑等技术进行故障诊 断。这种方法需要建立知识库和推理机制, 能够根据设备的历史运行情况和专家的经验 进行故障诊断,具有较高的智能化水平。
03
设备故障诊断方法
基于模型的诊断方法
Matlab技术在故障诊断中的应用指南
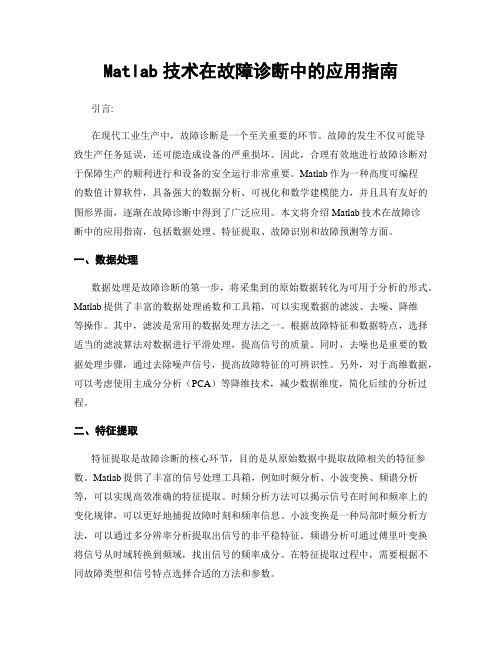
Matlab技术在故障诊断中的应用指南引言:在现代工业生产中,故障诊断是一个至关重要的环节。
故障的发生不仅可能导致生产任务延误,还可能造成设备的严重损坏。
因此,合理有效地进行故障诊断对于保障生产的顺利进行和设备的安全运行非常重要。
Matlab作为一种高度可编程的数值计算软件,具备强大的数据分析、可视化和数学建模能力,并且具有友好的图形界面,逐渐在故障诊断中得到了广泛应用。
本文将介绍Matlab技术在故障诊断中的应用指南,包括数据处理、特征提取、故障识别和故障预测等方面。
一、数据处理数据处理是故障诊断的第一步,将采集到的原始数据转化为可用于分析的形式。
Matlab提供了丰富的数据处理函数和工具箱,可以实现数据的滤波、去噪、降维等操作。
其中,滤波是常用的数据处理方法之一。
根据故障特征和数据特点,选择适当的滤波算法对数据进行平滑处理,提高信号的质量。
同时,去噪也是重要的数据处理步骤,通过去除噪声信号,提高故障特征的可辨识性。
另外,对于高维数据,可以考虑使用主成分分析(PCA)等降维技术,减少数据维度,简化后续的分析过程。
二、特征提取特征提取是故障诊断的核心环节,目的是从原始数据中提取故障相关的特征参数。
Matlab提供了丰富的信号处理工具箱,例如时频分析、小波变换、频谱分析等,可以实现高效准确的特征提取。
时频分析方法可以揭示信号在时间和频率上的变化规律,可以更好地捕捉故障时刻和频率信息。
小波变换是一种局部时频分析方法,可以通过多分辨率分析提取出信号的非平稳特征。
频谱分析可通过傅里叶变换将信号从时域转换到频域,找出信号的频率成分。
在特征提取过程中,需要根据不同故障类型和信号特点选择合适的方法和参数。
三、故障识别故障识别是根据提取的特征参数,判断设备是否发生故障,以及故障类型和严重程度。
Matlab提供了各种分类和聚类算法,例如支持向量机(SVM)、人工神经网络(ANN)和K均值聚类,可以对提取的特征进行有效分类和聚类。
风机叶片故障诊断与健康监测系统研究

风机叶片故障诊断与健康监测系统研究在现代工业中,风机是一种重要的设备,广泛应用于发电厂、炼油厂、化工厂等众多领域。
风机的叶片是其核心部件之一,对其进行故障诊断和健康监测,可以确保风机的正常运行,提高生产效率和安全性。
本文将对风机叶片故障诊断与健康监测系统的研究进行探讨。
1. 前言在风机的运行过程中,叶片可能会因为磨损、断裂、结构松动等原因出现故障,导致风机性能下降、噪声增加甚至是设备损坏。
因此,建立风机叶片故障诊断与健康监测系统,实时监测风机叶片的状态,对故障进行诊断和预警,具有重要意义。
2. 故障诊断方法2.1 传统方法传统的风机叶片故障诊断方法主要依靠人工观察和经验,通过观察叶片表面的磨损、断裂情况,判断叶片的健康状况。
这种方法存在主观性较强、效率低下的问题,无法满足现代工业对高效准确诊断的需求。
2.2 基于数据分析的方法近年来,随着传感器技术和数据分析技术的发展,基于数据分析的故障诊断方法成为研究的热点。
这种方法通过使用加速度传感器、振动传感器等设备采集风机叶片的振动数据,结合数据处理和模式识别算法,实现对风机叶片故障的自动诊断。
3. 健康监测系统设计3.1 数据采集与传输健康监测系统首先需要采集风机叶片的振动数据,包括叶片的振动频率、幅值和相位等信息。
采集到的数据可以通过有线或者无线方式传输到数据处理中心。
3.2 数据处理与分析数据处理与分析是风机叶片故障诊断的关键步骤。
通过对采集到的振动数据进行数字滤波、特征提取和数据降维等处理,可以得到反映叶片健康状况的有效特征参数。
然后,利用数据挖掘和机器学习算法,建立故障模型,实现对风机叶片故障的诊断和预测。
3.3 故障诊断与预警在风机叶片的健康监测系统中,故障诊断和预警是非常重要的功能。
一旦监测到叶片出现故障,系统会及时发出警报,同时提供详细的故障类型和位置信息,以便维护人员进行及时维修和更换。
4. 实验与应用为了验证风机叶片故障诊断与健康监测系统的有效性,研究人员通常会进行一系列的实验。
基于模型的故障诊断方法研究

基于模型的故障诊断方法研究随着工业自动化的普及和发展,大量的机械设备和装置被广泛应用于生产制造和工业领域。
然而,在长期使用过程中,这些设备和装置也会存在各种故障和问题。
因此,如何快速准确地诊断故障,对于确保设备运行的稳定和生产效率具有非常重要的意义。
基于模型的故障诊断方法是目前工业领域中较为常用的一种方法。
该方法主要是通过建立设备的数学模型,将实际运行时的数据输入到模型中,然后通过对比实际值和模型值之间的差异,判断设备是否存在故障,并定位故障点。
本文将针对该方法进行详细探讨,分析其优缺点,并对其未来发展方向进行展望。
一、基于模型的故障诊断方法的原理基于模型的故障诊断方法需要建立一个符合实际运行情况的设备模型。
这个模型可以基于原理模型、经验模型、统计模型以及神经网络等方法建立。
一旦模型建立成功,就可以根据表现型状态分析的原理预测设备的故障,其操作流程如下:1. 数据采集:将设备工作时产生的数据进行采集,并将其记录下来。
2. 数据预处理:将采集到的数据进行处理,例如:去噪、滤波等,以提高数据处理的准确性。
3. 建立模型:通过使用原理模型、经验模型、统计模型以及神经网络等方法建立设备的数学模型。
4. 模型训练:将采集到的数据输入到模型中,通过不断优化,提高模型的预测精度。
5. 故障诊断:将实际运行数据输入到模型中,与模型值进行对比,判断设备是否存在故障,并定位故障点。
6. 预测分析:根据模型的结果,对未来的设备故障进行预测和分析。
二、基于模型的故障诊断方法的优缺点相比较于其他的故障诊断方法,基于模型的故障诊断方法具有如下优点:1. 可以提高故障诊断的准确性和精确度:该方法通过建立设备的数学模型,将实际运行数据输入到模型中,对比实际值和模型值之间的差异,可以准确地判断设备是否存在故障,并定位故障点。
2. 可以大幅度降低运维成本:通过使用该方法进行故障诊断,可以在第一时间内判断设备是否有问题,减少无效的现场巡视,提高维修的效率和准确性,降低运维成本。
设备故障诊断与维护技术
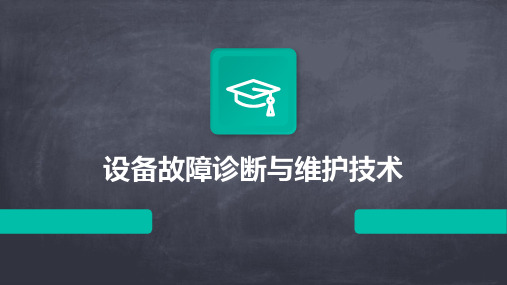
经过维护后,飞机仪表板恢复正常工作, 保障了飞行安全和乘客舒适度。
05
结论
Chapter
设备故障诊断与维护的重要性
保障生产安全
及时诊断和修复设备故障可以避免生产事故 ,确保生产安全。
提升生产效率
设备故障的及时修复可以保证生产的连续性 和稳定性,从而提高生产效率。
提高设备使用寿命
定期维护和保养设备可以延长设备的使用寿 命,降低更换成本。
数据分析
02
对监测数据进行深入分析,预测设备可能出现的故障和问题。
预警与预防
03
根据分析结果,提前预警并采取预防措施,降低设备故障风险
。
修复性维护
故障诊断
对设备出现的故障进行诊 断,确定故障原因和位置 。
修复与更换
对故障进行修复或更换损 坏的部件,使设备恢复正 常运行。
记录与反馈
记录设备故障和维护情况 ,为后续维护提供参考和 改进依据。
设备故障诊断与维护技术
目录
• 设备故障诊断技术 • 设备维护技术 • 设备故障诊断与维护技术的发展趋势 • 实际应用案例 • 结论
01
设备故障诊断技术
Chapter
故障检测与诊断方法
通过红外测温仪等设备检测设备 表面或内部的温度,判断是否出 现异常温升。
利用声音传感器采集设备运行时 的声音信号,通过分析声音的频 率、振幅等参数,识别异常噪声 ,诊断故障部位。
远程诊断与维护技术需要建立完善的远程监测系统和通信网络,以确保数据传输 的稳定性和实时性。同时,还需要加强数据安全和隐私保护,防止设备数据泄露 和被非法利用。
集成化诊断与维护
集成化诊断与维护是指将各种诊断与维护技术进行整合,形 成一套完整的设备维护体系。通过集成化诊断与维护,能够 实现对设备的全面监测、分析和维护,提高设备的整体运行 效率和可靠性。
设备故障分析与管理

设备故障分析与管理在故障管理工作中,不但要对每一项具体的设备故障进行分析,查明发生的原因和机理,采取预防措施,防止故障重复出现。
同时,还必须对本系统、企业全部设备的故障基本状况、主要问题、发展趋势等有全面的了解,找出管理中的薄弱环节,并从本企业设备着眼,采取针对性措施,预防或减少故障,改善技术状态。
因此,对故障的统计分析是故障管理中必不可少的内容,是制定管理目标的主要依据。
1.故障信息数据收集与统计(1)故障信息的主要内容①故障对象的有关数据有系统、设备的种类、编号、生产厂家、使用经历等;②故障识别数据有故障类型、故障现场的形态表述、故障时间等;③故障鉴定数据有故障现象、故障原因、测试数据等;④有关故障设备的历史资料。
(2)故障信息的来源①故障现场调查资料;②故障专题分析报告;③故障修理单;④设备使用情况报告(运行日志);⑤定期检查记录;⑥状态监测和故障诊断记录;⑦产品说明书,出厂检验、试验数据;⑧设备安装、调试记录;⑨修理检验记录。
(3)收集故障数据资料的注意事项①按规定的程序和方法收集数据;②对故障要有具体的判断标准;③各种时间要素的定义要准确,计算各种有关费用的方法和标准要统一;④数据必须准确、真实、可靠、完整,要对记录人员进行教育、培训,健全责任制;⑤收集信息要及时。
(4)做好设备故障的原始记录①跟班维修人员做好检修记录,要详细记录设备故障的全过程,如故障部位、停机时间、处理情况、产生的原因等,对一些不能立即处理的设备隐患也要详细记载;②操作工人要做好设备点检(日常的定期预防性检查)记录,每班按点检要求对设备做逐点检查、逐项记录,对点检中发现的设备隐患,除按规定要求进行处理外,对隐患处理情况也要按要求认真填写,以上检修记录和点检记录定期汇集整理后,上交企业设备管理部门;③填好设备故障修理单,当有关技术人员会同维修人员对设备故障进行分析处理后,要把详细情况填入故障修理单,故障修理单是故障管理中的主要信息源。
CNC机床加工中的工艺监控与故障诊断

CNC机床加工中的工艺监控与故障诊断CNC机床作为现代制造业的重要设备,广泛应用于各个行业。
然而,在CNC机床加工过程中,工艺监控和故障诊断一直是制约机床性能和生产效率的重要问题。
本文将探讨CNC机床加工中的工艺监控与故障诊断技术,并提出一些解决方案。
一、工艺监控工艺监控是在CNC机床加工过程中对各项工艺参数进行实时监测和控制,以提高产品质量和生产效率。
在进行工艺监控时,可以采用以下几种方式:1. 传感器监测:通过安装传感器,监测加工过程中的温度、压力、力度等参数。
这些传感器可以实时采集数据,并通过数据分析系统进行处理和监控。
例如,在铣削过程中,可以使用力传感器来检测切削力的变化,以判断切削情况是否正常。
2. 图像处理技术:应用图像处理技术可以实现对加工过程中的图像进行实时识别和分析。
通过对加工过程中的图像进行处理,可以提取出关键特征,判断加工质量的好坏。
例如,在零件表面缺陷检测中,可以使用图像处理技术来检测表面的裂纹、划痕等缺陷。
3. 数据分析与挖掘:将CNC机床加工过程中产生的大量数据进行统计和分析,可以发现加工过程中存在的问题,并及时采取措施进行调整。
数据分析与挖掘可以帮助人们理解加工过程中的规律和趋势,进而提高加工效果。
二、故障诊断CNC机床加工中常常会出现各种故障,例如刀具磨损、零件偏差过大等。
及时准确地进行故障诊断,对于保证加工质量和设备稳定运行至关重要。
以下是一些常用的故障诊断方法:1. 经验诊断法:经验诊断法是一种基于经验的诊断方法,通过经验和专业知识来判断故障原因。
例如,根据刀具磨损情况和加工声音的变化来判断是否需要更换刀具。
2. 模型诊断法:模型诊断法通过建立数学模型,对机床加工过程进行模拟和仿真。
通过与实际加工数据进行比对,可以找出存在的差异并进行故障诊断。
例如,在铣削过程中,可以建立切削力模型,通过与实际测得的切削力进行对比,来判断是否存在刀具损伤。
3. 基于机器学习的诊断方法:随着人工智能技术的发展,基于机器学习的故障诊断方法逐渐得到应用。
- 1、下载文档前请自行甄别文档内容的完整性,平台不提供额外的编辑、内容补充、找答案等附加服务。
- 2、"仅部分预览"的文档,不可在线预览部分如存在完整性等问题,可反馈申请退款(可完整预览的文档不适用该条件!)。
- 3、如文档侵犯您的权益,请联系客服反馈,我们会尽快为您处理(人工客服工作时间:9:00-18:30)。
应用数据分析法进行简易的设备故障诊断
秦涛
摘要理论与实践证明,借助一定的测量技巧和规律,通过对便携式测振仪采集的数据进行分析,基本可以满足现场对设备故障点进行粗略佑计的要求。
运用便携式测振仪进行故障分析,对于普及设备状态监测与故障诊断工作、量化设备管理及维修具有重要的意义。
结合两个典型的现场案例,对应用数据分析法开展简易的设备故障诊断工作进行探讨。
关键词便携式测振仪数据分析故障诊断
为了对转动设备实施有效的管理,在开展设备状态监测与故障诊断的时候,仅笼统地从总体上判断设备正常与否是远远不够的,还需要进一步弄清设备故障的具体类型和部位。
精密诊断仪能够借助相对较多的手段(如时域分析、频域分析、轴心轨迹分析等),分析设备的故障点及故障原因,为检修提供必要的指导。
但是,由于精密诊断仪价格昂贵,对操作人员的理论知识储备要求较高,因此很难在现场普及推广。
主要应用于状态监测的便携式测振仪(如公司采用的HG2500系列)具有价格低、易操作、携带方便、便于普及装备和应用等优点。
理论与实践证明,借助一定的测量技巧和规律,通过对便携式测振仪采集的数据进行分析,同样可以满足现场对设备故障原因进行粗略估计的要求。
在此结合在现场工作中所处理的典型案例,对应用数据分析法进行简易的设备故障诊断做一引证论述。
一、案例一离心式式压缩机震动故障
1.设备基本情况
电机型号YKK4005-2,功率500kW,转速2976r/min,经增速比3.51的行星齿轮增速器驱动主机;主机型号4H-4,转速10459r/min,3725m3/h,进口压力0.088Mpa,出口压力0.47MPa。
输送介质为氯气。
2005年8月6日,巡检发现离心式压缩机振动异常。
2.振动测量与分析
现场应用便携式测振仪对主机前后轴承部位进行振动测量。
测量结果如表1所示。
根据表1中数值分析如下:
表1 离心式压缩机振动值
(1)根据化工行业HGJ1018-79位移振幅标准及ISO2372标准中关于机械振动烈度的规定:离心式压缩机全位移振动值应不大于0.015mm;对于功率大于75kW、转速介于600~
12000r/min之间刚性安装的大型机械,其振动烈度阑值为1.12cm/s。
现该压缩机前后轴承水平振动值均已超标,且远远大于历史振动值,故不能继续运行。
(2)从数值的方向分析,前后轴承均为水平方向振动大于垂直方向,具有明显的不平衡特征。
初步结论:该压缩机需做停机处理,故障原因有可能是转子不平衡。
8月7日,对该设备进行了解体检修,情况为:后轴承下瓦有轻微磨损,由于氯气含水量超标,导致主轴轴套严重腐蚀,整个转子已失去原有的平衡。
3.总结
(1)此案例是一个典型的不平衡故障。
由于不平衡在频段划分上属于中低频类,而位移、速度指标能够较好地反映中低频故障,故测量数据中位移、速度指标变化比较显著。
(2)转动设备运行中,由于其水平方向的动刚度较垂直方向小,故一旦出现不平衡因素,其水平方向振动较垂直方向表现强烈。
在此案例中,前后轴承的水平方向振值均大于垂直方向本符合不平衡的方向特征。
二、案例二鼓风机电机异常声响故障
1.设备基本情况
电机型号YK3556-2,功率400kW,转速2980r/min,经鼓风机机体内置的传动比3.79的增速器驱动鼓风机;鼓风机型号45L-3,输出转速11306r/min,流量334m3/h,进口压力0.016Mpa。
电极驱动轴承型号为NU217及6217,非驱动端轴承型号为NU215。
2006年8月2日,鼓风机电机非驱动端有不均匀、不连续异常声响。
2.振动测量与分析
对异常电机进行了振动测量,测量值如表2所示。
为确保数据的准确性,对电机非驱动端垂直方向的加速度作了再次测量,测量结果见表中斜线后数值。
表2 鼓风机电机振动测量值
根据表2中数值分析如下:
(1)电机整体振动的位移、速度参数未超过振动标准,故该电机可继续运行。
(2)电机各测点的低频加速度值基本稳定于5.0m/s2,高频加速度值除非驱动端垂直测点外,基本稳定在15m/s2,但非驱动端垂直测点该值最高达47.9m/s2,Hi/Lo最大为11.14,大雨正常比值(正常比值一般小于5),且远远大于其他测点的比值,该数值表明:电机的异常由高频原因引起,异常源很有可能存在于轴承。
(3)从振动值的方向分析,非驱动端在垂直方向上振动异常,基本符合轴承故障的方
向特征。
初步结论:该电机可继续监视运行;异常声响可能由电机轴承的高频振动引起。
根据以往经验,现场操作人员对该电机进行加油处理。
运行稳定后对电机非驱动端相同测点复测,测量结果见表2,可见非驱动端垂直方向高频振值下降,Hi/Lo值基本正常,电机整体运行平稳,异常声响消失。
3.总结
(1)电机在润滑状况不佳的情况下运行,属于滚动轴承的高频干摩擦冲击(该电机已运行1年,轴承滚道上应该会有不同程度的损伤),而加速度能够较好地反映高频特性。
位移、速度的是疲劳中低频特性,这也是为何电机的位移、速度值比较正常,但加速度异常的原因。
(2)轴承的承载区一般位于水平中心线以下、垂直中心线在右对称α角度(滚动轴承为45°,滑动轴承为30°),当轴承承载性能下降时,便会在承载区内出现显著异常,即表现为垂直方向振动较大。
(3)油滚动轴承支撑酌设备在考虑位移、速度振动值时,还要综合测量加速度值,以衡量轴承的工作状态,防止由于滚动轴承的早期异常而引发设备故障。
三、诊断操作要点
结合以上两个典型案例的分析过程,在运用数据分析法进行简易故障诊断时应注意以下几个方面:
(1)综合运用绝对标准、相对标准、类比标准,对设备的当前状态做整体评判。
无论采用哪种方法进行故障诊断,该工作一定不能省略。
(2)根据测量参数的物理意义及适用的频率段,合理选择参数进行数据采集。
一般来讲,位移、速度参数反映了设备的疲劳及能量破坏,加速度则体现了设备的冲击特性。
参数选取的一般原则见表3。
在案例二中,如果漏掉了加速度分析,就很难捕根到滚动铀承的工作特性。
表3 参数选区的一般原则
(3)牢牢把握典型故障的振动方向特性,根据测量数据所反映的方向性信息进行故障类型估计。
这是振动数据分析法进行故障诊断的核心。
一般来讲,不平衡的特征方向为水平,轴承的特征方向为垂直,不对中则表现为轴向振动较大。
文中所列的案例基本都符合该规律。
(4)深入掌握机械设备的相关物理特性,如滑动轴承的承载机理、高服频振动传递的特点等,这是深入剖析设备故障原因、加深理解状态监测与故障诊断工作的理论基础。
(5)打破传统观念,深入分析便携式测振仪采集的各种振动参数,以获取尽可能多的设备状态信息,而不要单纯地认为,振动测量的目的就是测量几个参数,对设备只做出异常与否的简单判断。
(6)运用振动数据分析法进行简易故障诊断有其局限性,仅适用于粗略估计不平衡、不对中、地脚松动、轴承故障、由滚动轴承支撑的一级齿轮传动系统、电机电气故障的排除等,并且要有丰富的现场经验。
总之,运用振动数据分析法进行简易的故障诊断,关键在于根据状态参数的大小及其特征,辅以各种简单有效的判别方法,衡量设备的整体工作状态,推断故障的部位及原因。