热处理工艺化学热处理
热处理工艺

热处理工艺热处理工艺是通过加热和冷却对金属材料进行控制的工艺过程,目的是改变其原有的物理和化学性质,以提升材料的性能。
热处理工艺包括退火、正火、淬火、回火、疏松加热等不同方法。
本文将介绍热处理工艺的原理、方法和应用。
一、热处理工艺原理1.金属材料的组织结构与性能金属材料由于晶粒和晶界结构,其中晶粒内的原子排列方式称为晶态。
金属材料的物理和力学性质与其晶粒和晶界结构有关。
晶粒的大小、形状、分布和晶界的状态对金属材料的强度、硬度、塑性、韧性、导电性等性质影响显著。
2.热处理过程的原理由于金属材料在加热和冷却过程中的物理和化学反应,其晶粒和晶界组成的结构也会发生变化,从而影响其物理和化学性质。
热处理工艺就是通过控制材料的加热、保温时间和冷却速度等参数来控制金属材料的组织结构,从而提高材料的性能。
二、热处理方法1.退火退火是将金属材料加热至一定温度,保温一定时间后慢冷的热处理方法。
通过退火可以改变金属材料的晶界和晶粒的结构,增强塑性、韧性和延展性能。
退火方法也有多种不同的类型,包括全退火、球化退火、等温退火和局部退火等。
2.正火正火是将金属材料加热至一定温度,保温一定时间后慢冷的热处理方法。
通过正火可以改变金属材料的晶粒组织结构,提高其强度和硬度。
3.淬火淬火是将金属材料加热至一定温度,然后迅速浸入冷却介质中,使其迅速冷却的热处理方法。
淬火可以使晶粒迅速细化,提高材料的硬度和强度,但同时也会减少塑性和韧性。
4.回火回火是在淬火后将材料重新加热至一定温度并保温一定时间后冷却的热处理方法。
回火可以通过改变材料的晶界和晶粒组织结构来调整其硬度和韧性。
5.疏松加热疏松加热是将金属材料加热至一定温度并保温一定时间,旨在在已存在的材料中生成孔洞或气体,使材料产生疏松现象。
此工艺常用于铸造后处理中,其目的是在材料中消除潜在的缺陷和裂纹。
三、应用热处理工艺广泛应用于制造业中,包括钢铁、铸造、航空航天、汽车和电子等领域。
热处理工艺

等温冷却
连续冷却
时间
过冷奥氏体的两种冷却方式
G A3
A
E
Acm
Arcm
0.0218
P
S
Ar3 P
Q
A1 Ar1
0.77
2.11
含碳量( %)
孕育期
一. 过冷奥氏体的等温转变曲线(C曲线) 金相法
过冷奥氏体
转变开始
转变过渡区(过冷奥氏 体和转变产物)
转变结束(转变产物: 珠光体(>550℃); 贝氏体(< 550℃); 马氏体(Ms与Mf 之间)
1.工艺:A1以下某一温度(150~650 ℃),保温后出炉 空冷 。
2.目的:(1)通过回火,使马氏体发生转变,并控制转 变程度获得不同的回火组织,使钢具有所需要的性能; (2)降低或消除淬火应力,减小变形,防止开裂; (3)通过不同的回火温度来调整硬度,减小脆性; (4)使淬火组织稳定化,避免工件在使用过程中发生 尺寸和形状的变化。
C)目的: 使热轧、锻造空 冷后组织中的网状二次渗碳 体和珠光体中片层状的渗碳 体球化,降低硬度,改善切 削性能,并为后续的淬火做 好组织准备。
D)适用范围: 过共析钢、 合金工具钢
Ac3 Ac1
等温退火
球化退火 完全退火
4、去应力退火:
A)工艺: A1以下某一温度(500~650 ℃),保温后随 炉缓冷至200 ℃以下出炉空冷 。 B)特点:低温退火,无组织变化 C)目的: 消除铸、锻、焊件等的残余应力 D)适用范围: 所有碳钢
3.淬火钢在回火时的组织和性能的转变
1)马氏体的分解:在100℃以上,马氏体就开始 分解,其中的碳以ε-Fe2.4C的形式析出,饱和度 降低,此时的组织为极细的ε-Fe2.4C和低过饱和 度的铁素体组成,称为回火马氏体M回。这一阶 段内应力减小,力学性能变化不大。
表面化学热处理技术

化学热处理渗碳:为了获得高硬度、高耐磨的表面及强韧的心部,渗碳后必须进行淬火加低温回火处理。
按渗碳介质可分为:气体渗碳、液体渗碳、固体渗碳。
渗氮:①渗氮层具有高硬度、高耐磨性;②渗氮层比热容打,在钢件表面形成压应力层可显著提高耐疲劳性能,渗氮层的耐疲劳性优于渗碳层;③渗氮层表面有化学稳定性高的ε相,能显著提高耐腐蚀性。
渗氮能形成性能优越的渗氮层,但由于工艺时间太长,使得生产率太低,成本高,应尽量少采用。
渗氮一般用在强烈磨损、耐疲劳性要求非常高的零件,有的场合是除要求机械性能外还要求耐腐蚀的零件。
碳氮共渗(俗称“氰化”):按工艺温度分:低温碳氮共渗(520-580℃),工艺温度低,共渗过程是以氮原子为主、碳原子为辅的渗入过程,俗称“软氮化”;中温碳氮共渗(780-880℃);高温碳氮共渗(880-930℃)。
优点:①与渗碳相比处理温度低,渗后可直接淬火,工艺简单,晶粒不易长大,变形裂倾向小,能源消耗少,共渗层的疲劳性和抗回火稳定性好;②与渗氮相比,生产周期大大缩短,对材料适用广。
氮碳共渗:氮碳共渗起源于西德,是在液体渗氮基础上发展起来的。
早期氮碳共渗是在含氰化物的盐浴中进行的。
由于处理温度低,一般在500-600℃,过程以渗氮为主,渗碳为辅,所以又称为“软氮化”。
氮碳共渗工艺的优点如下:①氮碳共渗有优良的性能:渗层硬度高,碳钢氮碳共渗处理后渗层硬度可达HV570-680;渗氮钢、高速钢、模具钢共渗后硬度可达HV850-1200;脆性低,有优良的耐磨性、耐疲劳性、抗咬合性和耐腐蚀性。
②工艺温度低,且不淬火,工件变形小。
③处理时间短,经济性好。
④设备简单,工艺易掌握。
存在问题是:渗层浅,承受重载荷零件不宜采用。
渗硼:渗硼是一种有效地表面硬化工艺。
将工件置于能产生活性硼的介质中,经过加热、保温,使硼原子渗入工件表面形成硼化物层的过程称为渗硼。
金属零件渗硼后,表面形成的硼化物(FeB、Fe2B、TiB2、ZrB2、VB2、CrB2)及碳化硼等化合物的硬度极高,热稳定性。
热处理工艺(预先和最终)

三、退火和正火的选取原则
( 1 )Wc< 0.25 %的低碳钢,正火代替退火, 利于切削加工;防止游离三次渗碳体的析出, 提高工件的冷变形性。 (2)Wc=0.25~0.5%的中碳钢,也采用正 火,硬度偏高,但因成本低,生产率高; ( 3 )Wc=0 .5 ~0 .75% 的中高碳钢,一般 采用完全退火,降低硬度,改善切削加工性; ( 4 )Wc>0 .75% 的高碳钢或工具钢,一 般采用球化退火。若有网状二次渗碳体,先正 火消除之。 ( 5 )含碳量、合金元素高,奥氏体稳定性高, 完全退火,易缓冷得到马氏体和贝氏体,应高 温回火。
2、淬火加热温度: 原则:得到均匀细小的A组织,以便冷却后 得到均匀细小的马氏体组织; 亚共析钢:Ac3+30~50℃ 共析钢、过共析钢:Ac1+30~50℃ 合金钢: 低合金钢:Ac1或Ac3+50~100 ℃; 高合金钢:温度更高; (合金元素的作用,淬火加热温度应相应的提 高,以使合金元素的作用能充分地发挥出来)。 组织: 亚共析钢:细小的板条马氏体+少量残余奥氏体; 过共析钢:隐晶马氏体+细小的碳化物 +残余奥氏体。
等温退火的等温温度根据钢的成分和要求的硬度,由该 种钢的C曲线确定。
Accm之间的两相区加热,保温,得到不完全奥氏体 后,缓慢冷却以得到近于平衡组织的热处理工艺。 (1)目的: 细化晶粒,均匀组织,降低硬度,减小内应力, 改善切削加工性。 (2)适用钢种:共析钢、过共析钢、亚共析钢中 无大缺陷; (3)工艺参数: 加热温度:AC1+20~30℃ 优点:加热温度低,易操作,节能、降耗, 提高生产率。
钢的热处理工艺
热处理工艺:通过加热、保温和冷却的方法改变钢 的组织结构以获得工件所要求性能的技术操作; 制定基础: 热处理原理 种类: 普通热处理(退火、正火、淬火和回火) 表面热处理(表面淬火和化学热处理) 形变热处理 预备热处理,最终热处理
化学热处理-3

常见渗氮缺陷:
1.变形 2.脆性和渗氮层剥落 3.渗氮层硬度不足及软点
废气中氢、氮体积之和 废气中氢、氮、氨体积 之和
α低,则气氛氮势高; α高,则气氛氮势低;
测定氨分解率的原理与分解率的定义示意图
3、渗氮工艺 根据渗氮目的不同: 一:提高表面硬度、耐磨性及疲劳强度等的渗氮称为强化渗氮; 二:提高表面抗腐蚀性能的渗氮,称为抗腐蚀渗氮或防腐渗氮。 强化渗氮:等温渗氮(一段渗氮)、两段渗氮、三段渗氮。 抗腐蚀渗氮:在工件表面获得0.015-0.06mm厚的致密、化学稳定性 高的ε相层,提高工件的抗腐蚀性能 。
氨在钢件表面的分解和氮原子被 吸收的示意图
3. 氮原子的扩散 氮在铁中扩散系数可由下式表示
D
a N
a N
=D0exp(-Q/RT)
D ——氮在a-Fe中的扩散系数 D0——常数(0.3㎜2/s)
R——气体常数 Q——激活能(76.12kJ/mol) 由于氮的原子半径(0.071nm)比碳 的(0.077nm)小,故氮的扩散系数 要比碳的大(碳的相应常数D0=2.0㎜ 2/s,Q=84.1kJ/mol)。与渗碳时类 似,渗氮层的深度也随时间呈抛物线 的关系增加:符合δ=K t 的关系。
③三段渗氮:首先在较低温度下(520℃),使工件表面为氮所饱和;然后在 560℃的温度下使氮充分向内扩散;最后再降温,让氮重新饱和工件表面层。 特点:氮化层可以较深;氮化层中含氮量较高;氮化周期较长。
渗氮工件的质量检查:
外观检查、渗层金相组织检查、渗层深度、表面硬度、渗层脆性及
变形检查。 硬度测定:维氏硬度或表面洛氏硬度 渗层脆性:四级。Ⅰ级和Ⅱ级为合格。
渗氮的特点(与渗碳相比)
1)更高的硬度,更高的耐磨性,HV950~1200。 如38CrMoAl,渗C淬火,HRC58~63;渗N后,相当于HRC65~72; 2)具有高的红硬性。 渗C工件只适用于在<200℃工作,而渗N可在500~600℃工作; 3)具有高残余压应力。表层形成比容更大的高氮相ε(Fe3N);
钢的化学热处理

渗剂
吸收: 析出的活性原子克服表面能垒进入金属表面, 形成固溶体或化合物。
Fe〃[C]吸附 → Fe〃C溶
溶解
3Fe〃[C]吸附 → Fe3C
化合
吸收必须进行得足够快,否则会因发生其它反应而失去活性 。 吸收能力与钢的表面活性有关,表面缺陷多(位错、晶界露 头)、粗糙、干净无污染则表面活性高,吸附力强,可促进化 学热处理。
常用的气体介质:天然气、煤气、液化石油气。
使用时,直接通入炉罐里。 CH4→2H2+[C]
2CO→CO2+[C]
CO+H2→H2O+[C]
良好的渗碳介质应具备下列条件:
价格低廉,安全卫生,易于获取; 具有较好的活性,既保证能获得较高的渗碳速度,同时不致使
渗碳层碳浓度过高,而造成大量的过剩碳化物;
5)化学催渗:渗剂中加入一定的化学药剂或触媒剂以加速分解或吸收过程
6)物理催渗:eg:高频电场下的扩散。
化学热处理进行的条件:
1. 渗入元素的原子必须是活性原子, 而且具有较大的扩散能力 2. 零件本身具有吸收渗入原子的能力, 即对渗入原子有一定的 溶解度或能与之化合, 形成化合物。
分解、吸收、扩散三者的协调进行是确保化学热处理成功进行的关键。
产生的“碳黑”“焦炭”少。 渗碳剂分解产物中如果含有较多的不饱和碳氢化合物易形成过
多的碳黑附着在零件表面,使渗碳不均匀;附着在炉壁上,使
炉罐导热性差,从而使渗碳速度降低,同时也增加清理时的麻 烦。 含硫量低。
举例:
18CrMnTi钢汽车后桥主动伞齿轮渗碳工艺
固体渗碳:
《热处理原理及工艺》课件
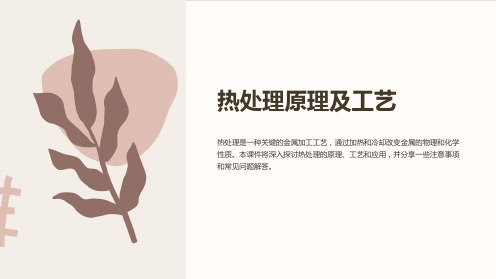
热处理的基本原理
热处理基于材料的相变和晶体结构变化。通过控制加热温度、保温时间和冷 却速率,可以调控晶粒尺寸、相组成和硬度。
热处理工艺流程
热处理工艺包括加热、保温和冷却阶段。常见的工艺流程包括退火、淬火、 回火和表面处理。
热处理常用的设备和工具
热处理设备包括炉子、加热器、冷却介质和测温仪器。常用的工具有夹具、 夹具和渗碳等。每种方法具有不同的应用场景和效果。
热处理的应用范围和优势
热处理广泛应用于航空航天、汽车制造、机械加工等领域。它能够提高材料 的强度、硬度、耐磨性和耐腐蚀性。
热处理的注意事项和常见问题解答
热处理过程中需要注意温度控制、冷却方式和工艺参数的选择。课件中还将解答常见问题,帮助您更好地理解 和应用热处理技术。
热处理原理及工艺
热处理是一种关键的金属加工工艺,通过加热和冷却改变金属的物理和化学 性质。本课件将深入探讨热处理的原理、工艺和应用,并分享一些注意事项 和常见问题解答。
热处理的定义和作用
热处理是通过加热和冷却控制材料的结构和性能,从而改变其力学性质、导 热性、电性能等。它广泛应用于金属加工、材料改良和工业制造。
热处理的四个阶段
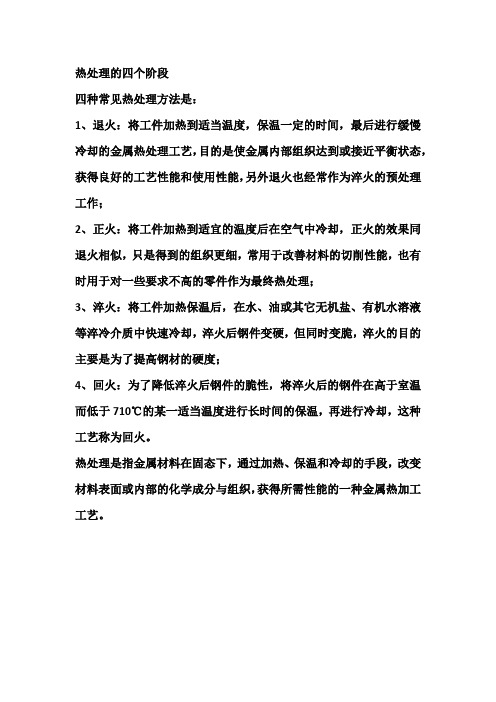
热处理的四个阶段
四种常见热处理方法是:
1、退火:将工件加热到适当温度,保温一定的时间,最后进行缓慢冷却的金属热处理工艺,目的是使金属内部组织达到或接近平衡状态,获得良好的工艺性能和使用性能,另外退火也经常作为淬火的预处理工作;
2、正火:将工件加热到适宜的温度后在空气中冷却,正火的效果同退火相似,只是得到的组织更细,常用于改善材料的切削性能,也有时用于对一些要求不高的零件作为最终热处理;
3、淬火:将工件加热保温后,在水、油或其它无机盐、有机水溶液等淬冷介质中快速冷却,淬火后钢件变硬,但同时变脆,淬火的目的主要是为了提高钢材的硬度;
4、回火:为了降低淬火后钢件的脆性,将淬火后的钢件在高于室温而低于710℃的某一适当温度进行长时间的保温,再进行冷却,这种工艺称为回火。
热处理是指金属材料在固态下,通过加热、保温和冷却的手段,改变材料表面或内部的化学成分与组织,获得所需性能的一种金属热加工工艺。