高强度灰铸铁(HT300)研究
铸铁件生产过程铁水特性若干问题的探讨(1)
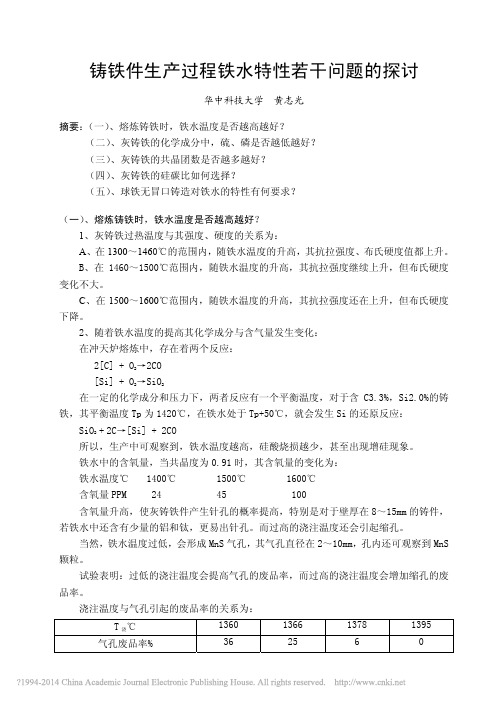
A、含硫量对灰铸铁共晶团的影响:
由于硫化物可以作为共晶石墨形核的基底,同时又能抑制共晶团的长大,但是,硫又
是促进铸铁形成白口的元素,所以,适当的硫量是有利的。
铸铁的化学成分为:C 3.19% Si 2.1% Mn 0.75% P 0.04%时,硫量的变化为 S 0.016%,0.014%,0.4%时,壁厚变化从 5/8 英寸至 3 英寸时,对铸件的白口宽度和共 晶团个数的关系为:(一英寸=25.4mm)
HT300
3.48
15~30 ﹥30
15~30
HT350
3.30
﹥30~50
﹥50
铁水适宜温度℃ 1430 1420 1450 1440 1430 1460 1450 1470 1460 1480 1470 1460
值得指出:牌号越高,虽然温度要求越高,但是其过热度不但没升高,反而下降。如 对于同时壁厚为 15mm,其牌号与过热度的关系为:
若铁水中还含有少量的铝和钛,更易出针孔。而过高的浇注温度还会引起缩孔。
当然,铁水温度过低,会形成 MnS 气孔,其气孔直径在 2~10mm,孔内还可观察到 MnS
颗粒。
试验表明:过低的浇注温度会提高气孔的废品率,而过高的浇注温度会增加缩孔的废
品率。
浇注温度与气孔引起的废品率的关系为:
T 浇℃ 气孔废品率%
而可使铸件表面光洁。生产实践表明,当磷含量在 0.02-0.04$时,铸件出现粘砂,而将含
磷量增加至 0.09-0.12%时,铸件粘砂就消失,并且铸件清砂时间可以减少 35%。
磷为什么有减少铸件粘砂的作用?铸件粘砂主要产生在热节处,尤其是内腔的热节
处,而不是发生在铁水静压力最大的位置即铸件的下部。粘砂是发生在铸件的凝固过程,
铸铁知识介绍

铸造知识介绍铸造:是一种金属材料的成形方法。
将熔融金属浇注、压射或吸入铸型型腔,凝固后成为具有一定形状和性能的铸件。
铸造方法有砂型铸造和特种铸造,既可用手工单件小批量生产,也可用机械化、自动化生造型方法大量成批生产。
铸造流程:制模——造型——烘干——熔炼——孕育处理——炉前分析——浇注——落砂清理——去浇冒口——铸件检验及缺陷分析——铸铁及熔炼白口铸铁:白口铸铁中的碳全部以渗透碳体(Fe 3c )形式存在,因断口呈亮白色。
故称白口铸铁,由于有大量硬而脆的Fe 3c ,白口铸铁硬度高、脆性大、很难加工。
因此,在工业应用方面很少直接使用,只用于少数要求耐磨而不受冲击的制件,如拔丝模、球磨机铁球等。
大多用作炼钢和可锻铸铁的坯料。
灰口铸铁;铸铁中的碳大部或全部以自由状态片状石墨存在。
断口呈灰色。
它具有良好铸造性能、切削加工性好,减磨性,耐磨性好、加上它熔化配料简单,成本低、广泛用于制造结构复杂铸件和耐磨件。
灰口铸铁按基体组织不同,分为铁素体基灰口铸铁、珠光体+铁素体基灰口铸铁和珠光体基灰口铸铁三类。
由于灰口铸铁内存在片状石墨,而石墨是一种密度小,强度低、硬度低、塑性和韧性趋于零的组分。
它的存在如同在钢的基体上存在大量小缺口,即减少承载面积,又增加裂纹源,所以灰口铸铁强度低、韧性差,不能进行压力加工。
为改善其性能,在浇注前在铁水中加入一定量的硅铁,硅钙等孕育剂,使珠光体基体细化,石墨变细小而均匀分布,经过这种孕育处理的铸铁。
称为孕育铸铁。
灰口铸铁的牌号、性能组织及用途见下表,国家标准根据直径30mm 单铸试棒的抗拉强度,将灰铸铁分为六个牌号。
牌号中的“HT ”是“灰铁”的汉语拼音的第一个大写字母,其后面的数字表示该牌号灰铸铁的最小抗拉强度。
灰铸铁的牌号及力学性能指标(GB5675-85)铸铁的化学成份对灰铸铁的组织有很大影响,各种牌号的灰铸铁的化学成份与铸件壁厚有关,下表数据供参考。
碳和硅是灰铸铁中最主要的化学成份,它们都是强烈促进石墨化的元素,对铸铁的组织和性能起着决定性影响。
灰铸铁件的氮气孔及其防止
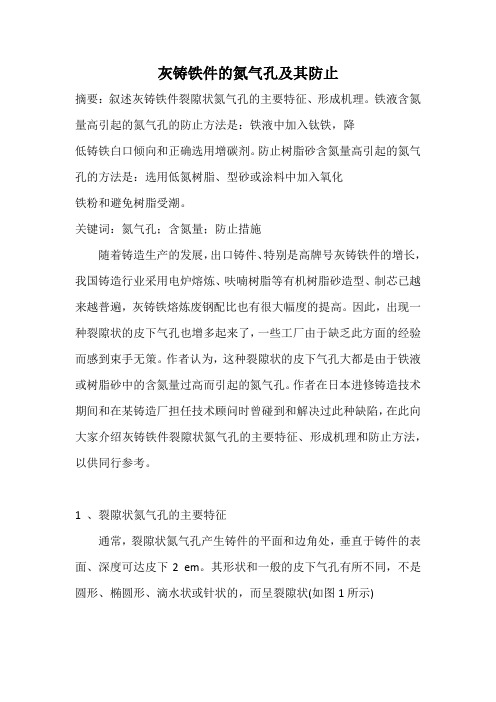
灰铸铁件的氮气孔及其防止摘要:叙述灰铸铁件裂隙状氮气孔的主要特征、形成机理。
铁液含氮量高引起的氮气孔的防止方法是:铁液中加入钛铁,降低铸铁白口倾向和正确选用增碳剂。
防止树脂砂含氮量高引起的氮气孔的方法是:选用低氮树脂、型砂或涂料中加入氧化铁粉和避免树脂受潮。
关键词:氮气孔;含氮量;防止措施随着铸造生产的发展,出口铸件、特别是高牌号灰铸铁件的增长,我国铸造行业采用电炉熔炼、呋喃树脂等有机树脂砂造型、制芯已越来越普遍,灰铸铁熔炼废钢配比也有很大幅度的提高。
因此,出现一种裂隙状的皮下气孔也增多起来了,一些工厂由于缺乏此方面的经验而感到束手无策。
作者认为,这种裂隙状的皮下气孔大都是由于铁液或树脂砂中的含氮量过高而引起的氮气孔。
作者在日本进修铸造技术期间和在某铸造厂担任技术顾问时曾碰到和解决过此种缺陷,在此向大家介绍灰铸铁件裂隙状氮气孔的主要特征、形成机理和防止方法,以供同行参考。
1 、裂隙状氮气孔的主要特征通常,裂隙状氮气孔产生铸件的平面和边角处,垂直于铸件的表面、深度可达皮下2 em。
其形状和一般的皮下气孔有所不同,不是圆形、椭圆形、滴水状或针状的,而呈裂隙状(如图1所示)2 、裂隙状氮气孔的形成机理一般灰铸铁的含氮量为(40~70)×lO-6,适量的氮有助于改善石墨形状,促进基体的珠光体化,提高抗拉强度。
但当铁液在熔炼过程中吸收的氮量超过一定的临界值(通常大lO×lO -6)时,在铸件凝固后期析出,周围又被已经形成固体的枝晶壁所包围、得不到铁液的补充时,就会形成存在于枝晶间的裂隙状皮下气孔。
其实,这种裂隙状氮气孔不是直接由于氮气形成的。
因为氮气是非活性气体,在铁液中的溶解量低于0.015%。
而氮的化合物受铁液高温分解,成为初生态原子氮[N],并可大量熔人铁液之中。
生产实践证明,铁液碳当量低、炉料中废钢配比高、采用电炉熔炼、树脂砂中树脂的NH2超量是产生裂隙状氮气孔的主要原因。
下面就由铁液化学成分和炉料配比、熔炼方法及呋喃树脂等氮含量而引起的裂隙状氮气孔,加以说明。
灰铸铁的组织及性能

灰铸铁的金相组织及其对性能的影响
灰铸铁的金相组织
(一) 石 墨(P29)
凝固条件不同 (化学成分、冷却速度、形核能力)
名称 片状 菊花状 块片状 枝晶点状 枝晶片状 星状
表2-1 石墨形状分类
代号
说明
A
片状石墨均匀分布
B
片状与点状石墨聚集成菊花状分布
C
部分带尖角块状、粗大片状初生石墨及小片状石墨
D
金相组织对性能的影响
(三) 共晶团的影响: 影响因素:炉料、化学成分、熔化工艺、孕育剂与孕育
方法、冷却速度。 优点:共晶团细化,明显提高σb; 缺点:过多共晶团会增加缩孔,缩松倾向。
灰铸铁的金相组织及其对性能的影响
金相组织对性能的影响
(四) 非金属夹杂物的影响(P35): Mn低时,S形成三元硫化物共晶或富铁硫化物,影响σb; Mn高时,形成MnS (Tm = 1650℃),入渣; 磷共晶常沿共晶团晶界呈网状、岛状或鱼骨状分布; 硬而脆,韧性极低,但耐磨,可用于缸套或刹车盘。
灰铸铁的金相组织
(二) 基 体(P30)
铸态或热处理后,分为:铁素体、片状珠光体、粒状珠光体、托 氏体、粒状贝氏体、针状贝氏体、马氏体(表2-4)。
组织名称
说明
铁素体
白色块状组织为α铁素体
片状珠光体
珠光体中碳化物和铁素体均呈片状,近似平行排列
粒状珠光体
在白色铁素体基体上分布着粒状碳化物
托氏体
在晶界呈黑团状组织,该种组织在高倍观察时,可看到针片状铁素体和碳化物的混合体
灰铸铁的性能
力学性能 Φ30mm试棒,不完全代表不同形状、壁厚的铸件性能(P36)
➢ 抗拉强度 σb: 用于区分铸铁等级 HT100~HT350; σb = 786.5 - 150×C % - 47×Si % + 45×Mn % +219×S %
铸铁概述

铸铁的概念:含碳量大于2.11%(一般为2.5%~4.0%) 铁碳合金
(含Si、Mn、S、P等元素)
铸铁的特点:
① 历史上使用较早
② 最便宜的金属材料之一
③ 铸造性能极好,且只能用铸造成形
④ 生产成本低,工艺简单,减震性耐磨性好,切削加工性好
⑤ 应用广——主要用于制造各种机器零件
壁厚 b
mm MPa %
硬度 HB
>12 300 6 120~163
>12 330 8 120~163
>12 350 10 120~163
>12 370 12 120~163
450 5 152~219
500 4 179~241
600 3 201~269
700 2 240~270
* 试棒直径16mm
铁素体可锻铸铁 珠光体可锻铸铁
ZG45 0.42-0.52 0.50-0.80 0.20-0.45 320 580 12 20 300
ZG55 0.52-0.62 0.50-0.80 0.20-0.45 350 650 10 18 200
铸钢
热处理 ——退火或正火,细化晶粒,消除魏氏组织及铸造应力。 组织 —— P+F 用途 —— 形状复杂,需一定强度、塑性、韧性的零件 机车车辆、船舶、重型机械齿轮、轴、轧辊、机座、缸体、外壳、阀体等
管道接口
连杆
蠕墨铸铁
蠕墨铸铁——在铁水浇注前加蠕化剂而得 牌号 —— 如 RuT420 ,表示 b≥420 组织 —— 钢基体+ 蠕虫状G 性能 —— 强度、塑韧性优于灰铸铁。 应用 —— 高压热交换器、汽缸盖、液压阀等
进气管
排气管
蠕墨铸铁
牌号
(HT) 可锻铸铁(KTH) 铸钢(WCA、WCB、WCC)

牌号
HT100
HT150
HT200
HT250
HT300
HT350
5
二、可锻铸铁(KTH)
可锻铸铁:用白口铸铁经过热处理后制成的有韧性的铸铁,别名: 马铁和玛钢;可锻铸铁通过石墨化退火处理得到一种高强韧铸铁, 具有较高的强度、塑性、和冲击韧度,可以部分代替碳钢。与灰 铸铁相比有较好的强度和塑性,特别是低温冲击性能较好,耐磨 性和减震性优于普通碳素钢。缺点是:在热处理过程中,工件易 变现,而且热处理工艺复杂,耗时久后续还需通过整形工序以消 除工件在热处理过程中的变形;可锻铸铁适宜于薄壁小工件,厚 大工件在厚壁处易形成缩松等铸造缺陷。
8
三、铸钢(WCA、WCB、WCC)
可锻附:某款切断阀阀体材质报告(WCB) 产品质量证明书
化学成分 炉号 名称 阀体 1#试块 图号 RQZ-50/4.0 材质 WCB WCB 数量 50件 2件 0.24 0.48 0.88 0.035 0.034 C Si Mn s p
阀体
2#试块 阀体
RQZ-80/4.0
6
二、可锻铸铁(KTH)
可锻我们在燃气输配设备中常用的是黑心可锻铸铁,他的组织为: 铁素体+团絮状石墨;目前国内90%的可锻铸铁为黑心可锻铸铁,其 常见牌号为: KTH300--06 KTH330-08 KTH350-10 KTH370-12 牌号表示方法为:
可锻铸铁由于其铸造特性,通常用于燃气用小型阀门和其他薄壁工 件。
素钢铸件技术条件》之要求。
10
四、球磨铸铁(QT)
可锻其基体为铁素体,韧性和塑性高,有较强的抗冲击性能,具 有抗温度急变和耐腐蚀性,用途很广,其机械性能远胜于灰口铸 铁而接近于钢;他具有优良的铸造、切削、和耐磨性能,有一定 的弹性,适用于阀体、曲轴、齿轮等制造。球铁的热处理规范为: 铸态或正火;其铸态状态金相组织是:石墨+铁素体+珠光体; 正 火状态金相组织是:石墨+较多的珠光体+铁素体,这样可获得较 高的综合机械性能,特别是其塑性和韧性提高,故球铁是兼具钢 和铸铁的优点的优良材料;他既具有钢的强度和韧性,又具有铸 铁的易于加工切削的优点。 以QT450-10举例: 抗拉强度:σ b≥450MPa; 屈服强度σ s ≥310MPa;伸长率δ (%) ≥10 硬度:160-210HB
含锑灰铁
一、研究背景: 1、机床用铸铁 铸铁一直是机床基础零件的主要结构材料,这是因为其有良好的精度稳定性、抗压强度、阻尼性能(减震性)、机械加工性能与铸造性能以及高的弹性模量与耐磨性能,且成本低。 随着机床技术的发展,数控技术、加工中心、柔性加工单元(FMC)和柔性加工系统(FMS)成为机床发展的方向。高度自动化、高精度和高效率要求基础件具有更高的刚度和精度保持性,要求提高材质的内在质量来保证机床在一定的寿命期限内的使用可靠性[1]。 在设计选材时,日本提出的机床铸件的牌号一般均高于过去我国同类机床铸件。MAZAK和MATE车床床身要求FC35,床头箱、溜板要求FC3O,连床腿、油盘亦采用FC20以上牌号的铸铁。材质牌号提高,机床部件的刚度、精度均得到保证。 分析现有机械工业铸件结构发现,在满足其适用性和寿命的同时,使铸件轻量化潜力是很大的。近年来已减少至14-20mm。切削力小的小型精密机床床身主要壁厚仅为8-l0mmo减薄壁厚必须以改善铸铁性能作为前提,只有采用高强度灰铸铁才能在减薄壁厚的同时,提高铸件刚度。 由于原材料质量及管理上的一系列问题,加上工艺水平差,与国外相比,材质性能差距大,由此造成机械产品的性能和单耗的落后状态,并成为机械产品更新换代的主要技术关键之一。[2] 1、与国外相比存在的主要差距: (1)在相同的碳当量下,灰铸铁强度值比国外差1一2个牌号,发动机缸体、拖拉机底盘中的大部分铸铁件国外普遍用HT250,而我国多数采用HT200。 (2)相同牌号的灰铸铁,我们的碳当量低,由此造成铸造性能差,断面敏感性和白口倾向大,缩松、渗漏缺陷严重,加工性能差。 (3)材质稳定性差,工艺出品率低,铸件本体材质稳定性及均一性更差。 可见,灰铸铁生产不但存在着材质性能的提高问题,还存在着综合性能的开发和提高问题。将铸件壁厚减薄使整机重量减轻,同时稳定试棒的力学性能合格率在98%以上,提高薄壁处的金相组织和保持断面均匀性,这都是努力的方向。 2提高灰铸铁材质的技术方向 国外生产高牌号质量灰铸铁[3]的工艺基本上已规范化,他们稳定获得高的力学性能的办法是: ①以高温熔炼获得优质铁液,单一用冲天炉时采用热风温度为500一600℃的热风冲天炉,投用固定碳为90%以上的铸造焦,保证出铁温度为1500一1550 ℃。 ②采用冲天炉一电炉双联熔炼工艺通过直读光谱仪、热分析仪快速测定铁液成分,做到铁液成分和温度稳定。 ③炉料中大量采用废钢的配比,确保高的力学性能。 ④材质微合金化和低合金化,强化基体组织,改善断面均匀性。 ⑤采用各种常用和特殊孕育处理,达到不同的综合效果。国外的这些做法对我们有启发和借鉴作用。[2] 本厂主要产品是为日本客户生产,其对材质要求较高,并且其产品结构大多壁厚<20mm。为了达到这一要求原来方法是在HT300内加Cu,但近年来Cu的价格涨幅较大,所以期望通过其他方法来达到这一要求。 2、含锑铸铁 Sb是我国的富有资源,在铸铁中加入适量的Sb,可改善其性能,可代替部分昂贵的稀缺金属,从而降低材料的成本[4]。 含锑灰铁在工业发达国家应用相当普遍,我国由于熔炼条件等原因所限锑铸铁应用较少,人们对锑灰铁的使用条件和锑的最佳加入量,尚缺乏统一认识。锑是强烈地稳定珠光体元素,然而对促进珠光体的形式及提高珠光体稳定性的机理众说纷纭。[5] 在《铸造合金及其熔炼》[6]一书中,作者提到Sb有强烈的促进形成珠光体的作用,并且含量0.002%-0.01%时,对球墨铸铁有使石墨球细化的作用,在灰铸铁中的加入量则要〈0.02%。 沈定钊 朱玉龙[5]认为综合锑对灰铁组织和机械性能的作用,灰铁中锑的合理加入量为0.05%。锑通过影响 转变的动力学条件,增加碳原子扩散阻力,从而起促进和稳定珠光体的作用。 三、实验内容及目的 微量锑既能增加铸铁共晶时的过冷也能增加共析转变时的过冷,因而能使铸铁中石墨细化,同时又增加了基体中的珠光体的体积分数,促使铸件的硬度和强度提高。由于锑所导致的共晶过冷有限,所以铸件的显微组织中不会出现游离碳化物。本实验就是通过对HT300铸铁内加入微量Sb,从而得到高强度和高硬度的铸铁,达到机床件性能的要求。并且用Sb来替代原来的Cu,达到降低成本的作用。 具体有如下内容: 1、不同Sb含量下的HT300抗拉强度。 2、不同Sb含量下的HT300硬度。 3、不同Sb含量下的HT300中石墨形态及尺寸 4、用化学法和光谱法测定最终成分。
灰铸铁的牌号、力学性能、用途及金相组织
灰铸铁的牌号、力学性能及用途材料牌号 石墨类型 石墨尺寸 金相组织HT150 A+B 无定向分布 120~250um (4级) 40%~90%中粗片状珠光体,10%~60%铁素体,二元磷共晶<7%HT200 A+B 允许10%~20%D 型 60~250um (4~5级)>95%中片状珠光体,<5%铁素体, 二元磷共晶<4%HT250 A+B 允许5%~15%D 型60~250um (4~5级) >98%中细片状珠光体,二元磷共晶<2%力学性能 铸铁类别牌号铸件壁厚/mmσb /MPa ≥HBS应用2.5~10 130 10~16610~20 100 93~14020~30 90 87~131铁素体 灰铸铁 HT100 30~50 80 82~122 适用于载荷小、对摩擦和磨损无特殊要求的不重要铸件,如防护罩、盖、油盘、手轮、支架、底板、重锤、小手柄等2.5~10 175 137~20510~20 145 119~17920~30 130 110~166铁素体—珠光体 灰铸铁HT150 30~50 120 105~157承受中等载荷的铸件,如机座、支架、箱体、刀架、床身、轴承座、工作台、带轮、端盖、泵体、阀体、管路、飞轮、电机座等2.5~10 220 157~23610~20 195 148~222 20~30 170 134~200HT20030~50 160 129~192 4.0~10 270 175~26210~20 240 164~247 20~30 220 157~236 珠光体 灰铸铁HT25030~50 200 150~225 承受较大载荷和要求一定的气密性或耐蚀性等较重要铸件,如汽缸、齿轮、机座、飞轮、床身、气缸体、气缸套、活塞、齿轮箱、刹车轮、联轴器盘、中等压力阀体等 10~20 290 182~27220~30 250 168~251HT300 30~50 230 161~24110~20 340199~29820~30 290182~272 孕育铸铁HT350 30~50 260171~257承受高载荷、耐磨和高气密性重要铸件,如重型机床、剪床、压力机、自动车床的床身、机座、机架,高压液压件,活塞环,受力较大的齿轮、凸轮、衬套,大型发动机的曲轴、气缸体、缸套、气缸盖等 PDF 文件使用 "pdfFactory Pro" 试用版本创建 。
铸铁
2、性能:
铸铁的缺点是由于石墨的存在,使它的强度、塑 性及韧性较差,不能锻造,优点是其接近共晶成 分,具有良好的铸造性;由于游离态石墨存在, 使铸铁具有高的减摩性、切削加工性和低的缺口 敏感性。目前,许多重要的机械零件能够用球墨 铸铁来代替合金钢。 铸铁的生产设备和工艺简单,价格便宜,并具有许 多优良的使用性能和工艺性能,所以应用非常广泛, 是工程上最常用的金属材料之一。它可用于制造各 种机器零件,如机床的床身、床头箱;发动机的汽 缸体、缸套、活塞环、曲轴、凸轮轴;轧机的轧辊 及机器的底座等。
●当WCE=4.28%,共晶成分;
●当WCE<4.28%,亚共晶成分; ●当WCE>4.28%,过共晶成分。
②冷却条件
●浇注温度↑
●冷却速度↓
铸型导热性↑ 铸件壁厚↓
石墨化程度↑
石墨化程度↑
石墨化程度↓ 石墨化程度↓
冷却速度的影响 冷速慢有利于按Fe-G相图进行结晶, 石墨化越容易进行。冷速快有利于形成白 口铁
二、铸铁的强化
强化途径:
1、铸铁的石墨化
2、改变石墨的大小和形状 3、改变基体组织
1、铸铁的石墨化
1)概念 石墨化过程是指铸铁中析出碳原子形成石墨的过程,即按Fe-G相 图结晶的过程。石墨既可以从液体和奥氏体中析出,也可以通过渗碳体 分解来获得。 • 石墨及其性能 石墨具有简单六方晶格,是碳 的一种同素异构晶体。其底面 原子呈六方网格排列,原子间 距小(1.42×10-10m),结 合力很强;而底面之间的间距 较大(3.04×10-10m),结 合力较弱。故石墨的强度、塑 性和韧性极低,接近于零;硬 度也很低,约为3~5HBS。
牌 号 抗拉强度 MPa 屈服强度 Mpa 伸长率 % 硬度 HB
灰铸铁的热处理
灰铸铁的热处理灰铸铁的热处理退火1. 去应力退火为了消除铸件的残余应力,稳定其几何尺寸,减少或消除切削加工后产生的畸变,需要对铸件进行去应力退火。
去应力退火温度的确定,必须考虑铸铁的化学成分。
普通灰铸铁当温度起过550C 时,即可能发生部分渗碳体的石墨化和粒化,使强度和硬度降低。
当含有合金元素时,渗碳体开始分解的温度可提高到650°C左右。
通常,普通灰铸铁去应力退火温度以550C为宜,低合金灰铸铁为600C,高合金灰铸铁是可提高到650C,加热速度一般选用60〜120C/h •保温时间决定于加热温度、铸件的大小和结构复杂程度以及对消除应力程度的要求。
铸件去应力退火的冷却速度必须缓慢,以免产生二次残余内应力,冷却速度一般控制在20〜40C /h,冷却到200〜150C以下,可出炉空冷。
一些灰铸铁件的去应力退火规范示于表1.2. 石墨化退火灰铸铁件进行石墨化退火是为了降低硬度,改善加工性能,提高铸铁的塑性和韧性。
若铸件中不存在共晶渗碳体或其数量不多时,可进行低温石墨化退火;当铸件中共晶渗碳体数量较多时,须进行高温石墨化退火。
(1)低温石墨化退火,铸铁低温退火时会出现共析渗碳体石墨化与粒化,从而使铸件硬度降低,塑性增加。
灰铸铁低温石墨化退火工艺是将铸件加热到稍低于Ac1下限温度,保温一段时间使共析渗碳体分解,然后随炉冷却。
(2)咼温石墨化退火,咼温石墨化退火工艺是将铸件加热至咼于Ac1上限以上的温度,使铸铁中的自由渗碳体分解为奥氏体和石墨,保温一段时间后根据所要求的基体组织按不同的方式进行冷却。
正火灰铸铁正火的目的是提高铸件的强度、硬度和耐磨性,或作为表面淬火的预备热处理,改善基体组织。
一般的正火是将铸件加热到Ac上限+30〜50C,使原始组织转变为奥氏体,保温一段时间后出炉空冷。
形状复杂的或较重要的铸件正火处理后需再进行消除内应力的退火。
如铸铁原始组织中存在过量的自由渗碳体,则必须先加热到Ac1上限+50〜100C的温度,先进行高温石墨化以消除自由渗碳体在正火温度范围内,温度愈高,硬度也愈高。
- 1、下载文档前请自行甄别文档内容的完整性,平台不提供额外的编辑、内容补充、找答案等附加服务。
- 2、"仅部分预览"的文档,不可在线预览部分如存在完整性等问题,可反馈申请退款(可完整预览的文档不适用该条件!)。
- 3、如文档侵犯您的权益,请联系客服反馈,我们会尽快为您处理(人工客服工作时间:9:00-18:30)。
高强度灰铸铁(HT300)研究
虽然人类掌握灰铸铁的熔炼技术已有好几千年的历史,但是在如何提高其强度和力学性能方面,我们仍然有很多工作要做。
在探寻企业在有效控制产品成本的前提下,稳定高效的生产高强度、高使用性能的灰铸铁的方法,提高产品的市场
适应力,增强企业的市场竞争力。
标签:高强度灰铸铁;铸造;熔炼工艺
0 前言
随着公司市场开发拓展,越来越多的高技术质量要求的铸造产品纳入公司的生产序列。
在有效控制生产成木的前提下,如何稳定高效的获得高强度灰铸铁,满足顾客的定货要求,是我们一个研究课题,本文叙述了在电炉熔炼的条件下,高强
度(HT300)灰铸铁的生产技术。
1 目标
在尽量保持原有的熔炼工艺基础上,通过综合运用现有的熔炼技术,达到细化灰铸铁中的石墨,适当增加灰铸铁中珠光体含量,形成碳化物以提高灰铸铁的机械性能,使其抗拉强度达到300N/mm2,并将三角试片白口宽度控制在4mm以下,防
止“白口”现象的发生,以保证产品的质量。
2 面临的问题
我们厂生产的灰铸铁件主要牌号足HT200和HT250,无法生产抗拉强度达300N/mm2到合格的HT300产品。
主要原因是铸件内部珠光体含量少,石墨多数成片状,从而分割基休,在石墨尖角处且易造成应力集中,形成了许多微小裂纹,使
灰铸铁的抗拉强度、塑性和韧性远低于钢,因此降低了铸件的机械性能。
3 分析
影响材料性能的因数有:
3.1 碳当量对材料性能的影响
决定灰铸铁性能的主要因素为石墨形态和金属基体的性能。
当碳当量(CE=C+1/3Si)较高时,石墨的数量增加,在孕育条件不好或有微量有害元素时,形成大量片状石墨。
这样的石翠会大大降低灰铸铁的强度。
在材料中珠光体具有好的强度、硬度,而铁素体则质底较软而且强度较低。
当随着C、Si的量提高,会使珠光体量减少,铁素体量增加。
因此,碳当量的提高将在石墨形状和基体组织两方面影响铸铁铸件的抗拉强度和铸件实体的硬度。
在熔炼过程控制小,碳当量的控制
是解决材料性能的一个很重要的因素。
3.2 合金元素对材料性能的影响
在灰铸铁中的合金元素主要是指Mn、Cr、Cu、Sn、Mo等促进珠光体生成元素,这些元素含量会直接影响珠光体的含量,同时由于合金元素的加入,在一定程度上细化了石墨,使基体中铁索体的量减少甚至消失,珠光体则一定的程度上得到细化,使铸铁有较高的强度性能。
在熔炼过程控制中,对合金的控制同样是重要
的手段。
但人为过多添加合金元素,对成本的控制有较大的负面影响。
3.3 微量元素对材料性能的影响
以往我们在熔炼过程中只注意常规五大元素对铸铁材质的影响,而忽略其它一些微量元素的作用。
众多微量元素对石墨形态的影响往往是无法预测的,从而导致形成的珠光体量的不确定,最终影响灰铸铁性能的。
所以在配料过程中应考
虑微量元素的影响。
4 解决方法
对实际生产中影响低灰铸铁强度一些主要问题,进行因果分析。
并根据反复测试,对原材料、操作、方法等方面实行整改措施。
具体操作落实到工作人员、
检查人员,以保证解决方案的顺利实施。
4.1 严格管理原材料
为了确保投入原料内各种元素含量的稳定性,对原材料的采购进行定点订购,
从而达到稳定熔炼配料,同时认真做好原材料进厂时的成分化验检验工作,避免由于原材料变化引灰铸铁性能变化而发生不良品产生的情况。
4.2 确定最佳的配料方案
通过计算,确保各原料最佳的加入比例:废钢25%;新生铁30%;回炉铁20%;留用铁水为25%,使原铁水的化学成保持相对稳定。
4.3 强化熔炼工艺,规范投料顺序
严格按照规程顺序操作:留用铁水——废钢——熔剂——新生铁——回炉铁——硅锰铁——除渣——增碳剂——合金——陈渣。
4.4 炉前控制
对每炉铁水试样做好及时地光谱分析,根据实际情况及时调整原料和辅料的投放量,保证铁水成分的稳定:同时做好湿型三角试片检测,保证原铁水白口宽度
一般控制在4毫米以下。
4.5 严格控制过程温度
在实际测试中发现,出铁水最佳温度应控制在1500℃-1520℃之间,浇铸温度应控制在1470℃-1490℃之间。
4.6 确定合理的合金加入量
经过多次反复调整,最终确定合金:(铜)按0.9%加入:氮化铬与孕育剂(锶硅)按0.3%:0.6%加入,铁水的含碳量控制在C=3.30(%)-3.35(%)之间,含硅量控制在Si-1.70(%)-1.90(%)之间,此时铸件的抗拉强度仍可达到320N/mm2以上,同时铁水的流动性好,铸件的各项性能指标都表现良好。
5 实施效果
通过调整合金加入量,不仅叫可以在铁水共析转变时显著地稳定和部分细化珠光体,而且能促进碳化物形成,减少片状石墨对基体的切割作用,同时适当增加共晶团数和促进细片珠光体的形成,有效的提高了灰铸铁的强度。