精益生产之价值流图Value_Stream_Mapping
精益价值流—价值 ppt课件

“Whenever there is a product for a customer, there is a value stream. The challenge lies in seeing it.”
价值流程图的作用
识别浪费的工具,发现浪费的根源。
改善沟通的工具。用价值流图可反映各项作业怎样与生产控制中 心沟通信息;典型的产品作为深入调查分析的对象。
销售金额大、生产数量多、生产周期长。
2 价值流图常用符号
3 绘制当前状态图
1、收集相关信息 一般从最下游的作业(即发货)开始,收集实际的过程数据,例 如发货频率、订货量、工艺流程图、各工序作业时间、换模时间、 操作工人数、班次、周期时间等。
产品的生产周期
推行JIT,首先分析企业自身是如何组织生产的,从而把企业在组织生产过程中存在的问题暴露出 来,然后运用JIT的一系列方法进行变革和改善。要分析企业自身组织生产的特点则必须首先了解 产品的生产周期(Lead Time)。
产品的生产周期是由信息处理周期和实物流动周期组成。信息流、实物流和资金流将企业、客户以 及供应商这三者有机地连接在一起。 1. 信息处理周期。接受订单、形成销售决议,然后制定出生产计划并下发到各个制造车间,再根据生 产计划向供应商发出采购订单。信息的流转形成了一条从客户到供应商的信息流,完成一次信息流 所需的时间构成信息处理周期。 2. 物品流动周期。供应商在获得订单后,在采购周期内向企业供应原材料;企业经过加工周期、组装 周期和送货周期,将成品送到客户手中。物品完成流转所需的时间构成物品流动周期。 缩短产品的生产周期是迅速适应市场需求的关键,而价值流程图分析方法正是了解产品生产周期的 有效工具。
流程的系统性诊断工具。从整个流程而非某个工艺过程分析问题。
价值流图VSM

© 2013 ZOGG All rights reserved.
5
Value added or not 价值增加或者没有?
接收 检查 库存
设置 / 转拉 移动/ 寻找 组装
物料运输
数据登记 计算
包装
仓库 返工
今天只有5%的活动增加了价值
© 2013 ZOGG All rights reserved.
2.
3.
© 2013 ZOGG All rights reserved.
12
Blocks of Value Stream Map 价值流图的5大板块
30 Days
MRP
Supplier
Supplier Loop
Monthl y Orders
8Байду номын сангаас0
Customer
Customer Loop
Takt Time = 440 min/44 = 10 min/unit
Non-Value Added
Any activity that does not add market form or function or is not necessary. (These activities should be eliminated, simplified, reduced or integrated.) 任何不增加市场或产品和服务的功能(这些活动应当消除,简 化,减少或合并)
价值流程图-VSM

PROCESSES
Products
Receiving Cutting Strip Soldering Crimp Insertion molding test inspect Pack
A
x
x
x
x
x
x
x
x
x
B
x
x
x
x
x
x
x
x
x
C
x
x
x
一次质量
2 x/ day
发运
I
500 pcs
Inventory Part A = 750 pcs Part B = 600 pcs Part C = 1650 pcs
# of shifts =
环节6:定义信息流
绘制从收到订单到下达生产订单(客户旳订单,生产订 单,采购订单)旳信息流。
统计生产订单及有关产品。 统计生产计划系统及随产品经过系统旳文件材料。 统计你怎样与供给商和客户沟通。 统计信息怎样整顿和发放,例如:电子方式,手工方式,
区别流动中旳推动和拉动。 包括产品接受和质量检验旳全部控制。
推动
流程生产不考虑下游(内部 )客户流程旳实际需求,直 接推动未完毕产品经过流程 。生产根据既定计划。
VS
拉动
每个后续生产环节都是前一 流程环节旳客户。当需要时 (拉动)由客户要求数量, 而不是简朴旳根据前面生产 环节生产并直接送到客户处 (推动)。
怎样辨认流程中旳挥霍?
价值流图(VSM)
价值流图消除挥霍
价值流图旳目旳在揭发挥霍旳起源。
我们应着眼于回答下述问题: “我们怎样能够仅生产下个流程所需,并仅在该流程需要时生产旳方式
精益工具之价值流程图

客户订单 采购原材料
生产制造
成品入库
发货
二、价值流
What is The Function Of Value Steam Function? 价值流的作用? ①一个交流或改善的公共基础平台; ②一个贯穿“产-供-销”的实物流和信息流的流程汇集; ③一个现状描述、发现问题及未来展示的工具; ④一个串联精益概念和技术的纽带或桥梁; ⑤一个优秀的精益生产改善工具;
1.CT: 2.ACT: A: 4.OEE: 5.FTQ: 6.C/O: 7.Avail. Time: 8.Shift:
⑴ 生产过程:
定义生产流程(冲压、焊接、机加、装配等),每班配备
人数,流程设备台数等;
①与②协
⑵数据盒子:
同使用
1.CT:Cycle Time,节拍;
2.ACT:Actual Cycle Time,实际节拍=CT ÷ OEE;
FTQ=First Time Good Parts ÷ Total Parts
6.C/O:Changeover Time (Good Part To Good Part);
7.Avail. Time:用于生产的总时间(Non OEE);
8.Shift:班次,即开班次数.
三、价值流绘制及分析
⑶ 外部资源(Out side Sources):
机:11
1.8
1.2
K
K
C/T:245S
C/O:15M
Shift:3
TVA:1715S
OEE:0.85
245S
产品 日需求量 A 300 B 200
客户
C 100
装配
人:15 机:2
检查
人:1 机:1
价值流图VSM
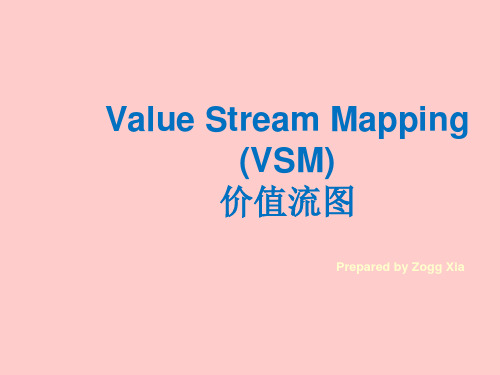
价值流图
Prepared by Zogg Xia
What’s Lean 什么是精益生产
Philosophy Thinking Toolkit Practice Journeys Life
NOT a program Not flavor Not a campaign
F
G
H Cycl e tim e RTY o r F TT Scr ap r ate Up/Do wn t ime Star ve/Blo ck t ime EPE / Set up t ime Avai lable tim e TAKT tim e
H
J
#
_K _
_M _
FG
I
- L= 0 -
__
__
➢ Make value-creating stepEssFtaLbOlisWh Pull
➢ Let customer PULL p3roduct from you as needed
➢ Pursue PERFECTION (CermeapteoFwloewr people who add
value)
价值流程图是用铅笔和白纸作为工具,帮助你去识别和理解在整个产
品价值流中的物流和信息流然后利用精益工具,消除浪费。
1. 让所有与目标价值流有关的人对当前以及未来的状态形成共同看法。 2. 为便于交流,提供可视化图,提供共同语言。 3. 使每个人都能看到浪费的现象,从而将大家的注意力都集中到改进
生产上来。 4. 帮助你看到不仅仅是单一的过程,将物流和信息流联系起来 5. 为推进改善提供蓝图。 6. 将精益的概念和技术紧密结合起来
Blocks of Value Stream Map 价值流图的5大板块
实施精益生产过程中价值流析方法的应用
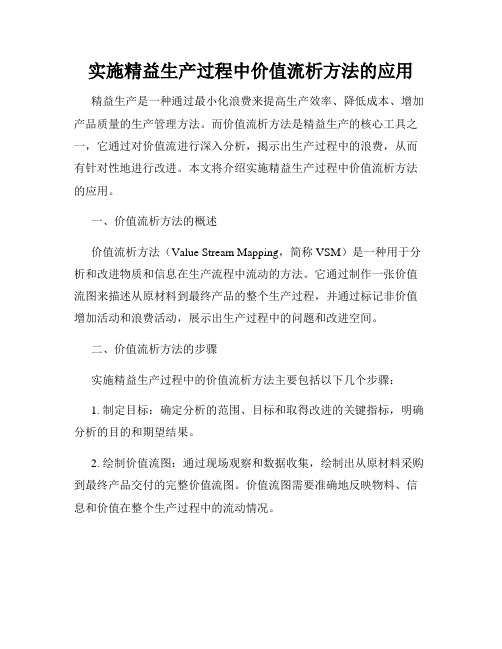
实施精益生产过程中价值流析方法的应用精益生产是一种通过最小化浪费来提高生产效率、降低成本、增加产品质量的生产管理方法。
而价值流析方法是精益生产的核心工具之一,它通过对价值流进行深入分析,揭示出生产过程中的浪费,从而有针对性地进行改进。
本文将介绍实施精益生产过程中价值流析方法的应用。
一、价值流析方法的概述价值流析方法(Value Stream Mapping,简称VSM)是一种用于分析和改进物质和信息在生产流程中流动的方法。
它通过制作一张价值流图来描述从原材料到最终产品的整个生产过程,并通过标记非价值增加活动和浪费活动,展示出生产过程中的问题和改进空间。
二、价值流析方法的步骤实施精益生产过程中的价值流析方法主要包括以下几个步骤:1. 制定目标:确定分析的范围、目标和取得改进的关键指标,明确分析的目的和期望结果。
2. 绘制价值流图:通过现场观察和数据收集,绘制出从原材料采购到最终产品交付的完整价值流图。
价值流图需要准确地反映物料、信息和价值在整个生产过程中的流动情况。
3. 识别浪费活动:在绘制的价值流图上标记出所有的活动,并识别出哪些是非价值增加的活动和浪费活动。
常见的浪费活动包括等待、运输、库存、过程瑕疵等。
4. 分析问题和瓶颈:通过对浪费活动的分析,找出造成浪费的根本原因和存在的问题。
同时,识别出生产流程中的瓶颈环节和影响生产效率的因素。
5. 制定改进方案:针对分析中发现的问题和瓶颈,制定具体的改进方案。
改进方案可以包括优化流程、减少浪费、提高效率、降低成本等。
6. 实施改进:根据制定的改进方案,逐步实施改进措施。
在实施过程中,需要与相关部门和员工进行充分的沟通和协作,确保改进方案的有效实施和持续改进。
三、实施精益生产的效果实施精益生产过程中的价值流析方法可以带来许多益处,包括:1. 提高生产效率:通过消除浪费和优化流程,可以减少生产过程中的非价值增加活动,提高生产效率和生产能力。
2. 降低成本:通过精细化管理和有效利用资源,可以降低生产成本和运营成本,并提高企业的竞争力。
精益生产管理三大手法
精益生产管理三大手法1. 价值流分析(Value Stream Mapping)价值流分析是精益生产管理的核心工具之一,它用于识别、分析和改进产品或服务提供过程中的价值流。
价值流分析的目标是优化价值流,消除浪费和提高整体效率。
1.1 价值流图价值流图是价值流分析的可视化工具,它展示了从原材料到最终交付产品或服务的整个过程。
使用符号和注释,价值流图能清晰地展示价值流中每个环节的处理时间、等待时间以及物料或信息的流动情况。
1.2 价值流分析的步骤•确定价值流的起点和终点:确定产品或服务提供过程的起点和终点,明确价值流的范围。
•绘制当前状态价值流图:详细描述当前的价值流,包括所有活动、等待和库存。
通过绘制当前状态价值流图,可以看清存在的浪费和问题。
•识别浪费:分析当前状态价值流图,识别并标记出所有的非价值增加的活动,比如等待、运输、库存等。
•绘制未来状态价值流图:在识别浪费后,根据精益原则和目标设定,重新设计未来的价值流图。
优化过程中,可以采用改进技术如单一分钟交换、工作细化等。
•实施改进措施:根据未来状态价值流图,实施改进措施,消除浪费,提高生产效率和质量。
•持续改进:价值流分析是一个持续的过程,通过不断地识别、改进和监控,实现精益生产的持续改进和优化。
2. 5S 方法5S 是一种基于现场管理的方法,旨在改善工作环境和工作效率。
它由五个日语单词的首字母组成,分别是“整理”(Seiri)、“整顿”(Seiton)、“清扫”(Seiso)、“清洁”(Seiketsu)和“素养”(Shitsuke)。
2.1 5S 方法的步骤•整理(Seiri):将工作区域清理整理,去除非必要的物品。
通过分类和标记,使工作区域更加整洁和高效。
•整顿(Seiton):对工作区域进行整顿和布置。
将工具和物料按照使用频率、工序顺序等进行合理摆放,便于工作人员快速获取所需。
•清扫(Seiso):持续清洁和维护工作区域,保持整洁和安全。
精益生产之价值流程图的简介
(二)发展历史 为了解决七种常见的浪费行为 1.生产过剩(快于必要的速度); 2.等待; 3.运输(搬运); 4.不当流程; 5.不必要的库存(超出的库存); 6.不必要的行动; 7.次品(改正错误)。
(三)见的七种工具
1.流程活动图(Process Activity Mapping)。 起源: 工业工 程。 2.供应链反应矩阵(Supply Chain Response Matrix)。 起源: 时间加速与后勤学。 3.生产多样性漏斗(Production Variety Funnel)。 起源: 运营管理。 4.质量过滤图(Quality Filter Mapping)。 5.需求扩大图(Demand Amplification Mapping)。 起源: 系统动力学。 6.决策点分析(Decision Point Analysis)。 起源: 有效消费 者反应/物流学。 7.物理结构图(Physical Structure Mapping)。
谢谢观看
为了缩短信息流处理时间,这家公司采取了一些有效的改善方案:第一、将所 有客户、产品进行编码,产品实现标准化,包括规格、尺寸、材质等技术要求,制 定消耗量标准BOM(物料消耗清单)构成表;第二、建立关键产能数据库。 如下 图所示,通过这样的改善之后,当客户下达订单后,销售部门只需要输入产品的编 码,就能够从数据库中获得所有的相关信息,不需要再找技术部门。如果客户对产 品提出新的要求,则可以通过技术部门对该产品重新编码,更换物料消耗单。销售 部门通过产品编码就可获得完整的虚拟订单,马上就可生成生产计划以及详细的原 材料采购订单。经过这样的处理后,整个信息流的处理时间仅仅需要2天!
(五)案例 据统计,某企业处理订单平均需要9 天的时间。这家公司接 到某个订单后信息流处理过程如下:客户下达订单后,6月13日销 售部对订单进行登记,并开始合同评审。由于财务部门的经理出 差,6月 18日才完成财务评审。同一天将合同转交给技术部评审, 技术部根据产品的技术要求规范,将确认条件写出来。6月19日合 同转给采购部,采购部计算出耗量、控量等成本指标后,开出采 购订单交给公司副总经理审批,6月22日得到批准。7月1日各车 间得到生产计划。整个订单处理过程花费了整整19天时间,比客 户要求的出货时间延误了10天。 从这家企业的信息流处理过程可以发现很多问题点:第一、 信息属于串联式,在财务部门没有审核之前,其他部门毫不知情, 无法预先做出准备;第二、产品的技术与BOM(物料消耗清单) 要求没有数据库,每次都需重复编写;第三、任何一个部门经理 不在,信息就断流;第四,由于信息流时间长,当生产计划明确后, 留给生产组织的时间变短,因此就需要物料、半成品提前做库存 来满足交货。
精益生产的十大工具
精益生产的十大工具作为企业管理领域中最重要的观念和模式之一,精益生产是由日本丰田公司于上世纪六十年代创造的一套最新生产质量管理的方法和理念,位于丰田汽车公司的耀眼位置。
精益生产与其他生产管理模式不同之处在于其很大程度上依赖于员工的主动性和自我监控能力,尤其是关注高质量的生态系统和追求最小化浪费的做法。
今天,在创造性和聚集力方面,精益相对于其他模式已经被证明是成功的。
以下是精益生产中的十大工具:1.价值流图(Value stream mapping)价值流图是分析组织流程的重要工具,它将一个产品或服务从采购原材料到交付给客户的所有步骤和信息流程绘制成一个连续的图形化流程。
价值流图就是图示化的一个流程,包括每个步骤的准确时间、输出和所用资源。
这使得有关制造流程的所有信息都可以一目了然,并帮助确定可以优化或省略的步骤。
价值流图可帮助企业精确分析整个流程,以便逐步优化操作和流程效率。
2.5S框架(5S framework)5S是改进生产效率和操作安全的一种工具,包括整顿、整理、清扫、标准化和自律。
这个框架被认为是整个精益系统的第一步,并使企业以整洁的生产环境开始。
5S使用标准化操作程序(SOP)和工具使工作区域保持整洁、有组织和安全,并且设施能够保持良好的生产态势和操作效率。
3.业务流程映射(Business Process Mapping)业务流程映射也被称为过程绘图,是企业中获得一些方案和改善的关键步骤。
此工具小组可以使用符号和图形描述企业中任何类型的业务流程和相关信息。
这可以揭示在过程中发生的问题、浪费、冗余和延迟,因此有助于消除不必要的步骤、改善流程的质量和效率。
4.一次流程变更(Single Piece Flow)这是一种最小化生产时间的原则,可以通过同一物品的生产技术一步步生产出多个物品。
使用一次流程变更工具,可以有效地降低制造成本,并使产品变得更加高效和可追溯,提高产品的核心竞争力。
5.生产平衡(Production Levelling)生产平衡是实现精益生产中的关键工具,可以帮助企业产生一个稳定的、平均的生产率水平。
ValueStreamMapping精益生产
S
U
P P
I N
L
P
I
U
E
T
Boundary (“Triggers” Process)
Module=100
1/Week 2/Day
Receiving Warehouse
•Raw material •Daily schedule
Forge
•Forge material •Daily schedule
Machine
• Bolts, nuts, washers • Daily schedule
Identify and Prioritize Improvement Opportunities
Determine Future State
Implement Improvements to Achieve Future State
Value Stream Mapping
6
Define
4 hours
Production lead time = 18 hours 33 min
30 sec
45 sec
60 sec
50 sec
Processing time =
185 seconds
9
Value Stream Mapping
9
Define Measure Analyze Improve Control
Define
Value Stream Manager
Assign Value Stream Manager
One person to manage the mapping of the total flow Has the capability to make changes across departmental