流化床溶剂脱蜡工艺的工业开发
润滑油加氢异构脱蜡装置工艺
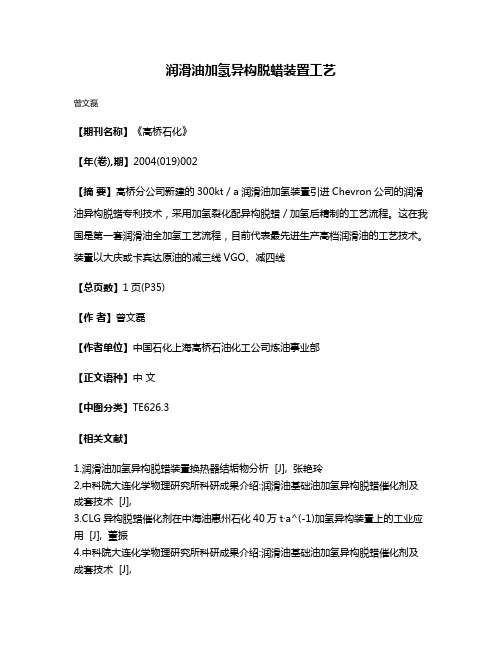
润滑油加氢异构脱蜡装置工艺
曾文磊
【期刊名称】《高桥石化》
【年(卷),期】2004(019)002
【摘要】高桥分公司新建的300kt/a润滑油加氢装置引进Chevron公司的润滑油异构脱蜡专利技术,采用加氢裂化配异构脱蜡/加氢后精制的工艺流程。
这在我国是第一套润滑油全加氢工艺流程,目前代表最先进生产高档润滑油的工艺技术。
装置以大庆或卡宾达原油的减三线VGO、减四线
【总页数】1页(P35)
【作者】曾文磊
【作者单位】中国石化上海高桥石油化工公司炼油事业部
【正文语种】中文
【中图分类】TE626.3
【相关文献】
1.润滑油加氢异构脱蜡装置换热器结垢物分析 [J], 张艳玲
2.中科院大连化学物理研究所科研成果介绍:润滑油基础油加氢异构脱蜡催化剂及成套技术 [J],
3.CLG异构脱蜡催化剂在中海油惠州石化40万t·a^(-1)加氢异构装置上的工业应用 [J], 董振
4.中科院大连化学物理研究所科研成果介绍:润滑油基础油加氢异构脱蜡催化剂及成套技术 [J],
5.中科院大连化学物理研究所科研成果介绍润滑油基础油加氢异构脱蜡催化剂及成套技术 [J],
因版权原因,仅展示原文概要,查看原文内容请购买。
正丁烯的开发与利用

正丁烯的开发与利用1、前言我国有近2 Mt/a的C4资源,其中来自炼油厂的约有1.3 Mt/a。
炼油厂的C4馏分主要山正丁‘烯(丁烯一1,顺丁‘烯一2、反丁‘烯一2)、异丁烯、正丁烷、异丁烷和丁二烯等组成。
其中,1,3- 丁二烯可以用抽提的方法分离出来,用作合成橡胶的原料,剩余C4统称为混合C4)馏分中的异丁烯可以通过醚化装置与甲醇反应生成甲基叔丁基醚MTBE)而得到有效利用。
而醚化后的C4馏分中的正丁烯有很多利用方向,自从德国的德士占公司Deuscho Texaco)开发成功正丁烯水合法生产甲乙酮的工艺后,解决了过去硫酸水合法生产甲乙酮带来的设备腐蚀问题,使甲乙酮的产量和应用范围迅速扩大,使正丁烯得到了有效合理的利用。
正丁烯的工业利用可分燃料和化工利用两个方而。
在化工利用方而,美国、西欧与日木用于生产仲丁醇和!甲乙酮的正丁烯占正丁烯消费比例的60 %左右。
在美国处于第2和第3位的利用是生产聚丁烯一1, 丁烯一1和庚烯;在西欧和日木,处于第2位的利用是生产顺丁烯二酸酐(顺酐)。
正丁烯及混合丁烯作为燃料,目前,在美国及西欧占有很大的比例。
美国烷基化油的总生产量约占原有处理量的6.2 %,催化裂化C4绝大部分用于制造烷基化油。
目前,我国对正丁烯的化工利用,主要是脱氢制丁二烯。
我国正丁烯的化工利用率还很低,丁烯衍生物不仅品种少,产量低,而且工艺技术落后。
特别是当前国外正丁烯化工利用的主要产品,在我国还是薄弱环节,甚至有相当数量的异戊橡胶、丁基橡胶、甲乙酮等产品还得依靠进口。
2、燃料方面的利用我国炼厂C4烯烃的利用以正丁烯与烷基化反应制烷基化汽友为主。
烷基化油辛烷值高、敏感性(研究法辛烷值与马达法辛烷值之差)小,具有理想的挥发性和清洁的燃烧性,是航空汽油和车用汽油的理想调合组分。
烷基化工艺具有充分利用炼厂气体资源的优点,是炼油厂中广泛应用的一种气体加工过程。
烷基化工艺有硫酸法烷基化和氢氟酸法烷基化两种,目前我国有硫酸法烷基化生产装置7套,总生产能力为443 kt/a,氢氟酸法烷基化装置12套,总生产能力为820 kt/a。
第1章 绪论-全

石油产品自给率,%
10
29
39
41
19
浙江海洋学院
我国炼油工业发展概况
(2)1960-1978年全面大发展时期
自 1960 年开始的大庆石油会战到 1978 年,我国原油产量 突破1亿吨,这19年是中国原油生产实现历史性转变和持 续大幅度增长的时期,也是中国石油加工工业全面大发 展时期
第一阶段:1960-1965年
12
浙江海洋学院
1、世界炼油技术的发展过程
进入1980s’ ,从世界范围来看,炼油工业的规模和 基本技术构成相对比较稳定,但是对具体的各项技 术,如工艺设备、催化剂、系统优化、过程模拟和 先进控制、环境保护等方面,都有了重要的进步和 发展 纵观炼油技术发展的历史,促进炼油技术发展的最 基本动力:
建设了大庆、南京等大型炼油厂
改扩建了上海炼油厂、大连石化七厂
将过去主要生产加工人造石油的抚顺石油一厂、二厂、 五厂、茂名石油公司改为加工天然石油的炼油厂
浙江海洋学院
20
21
浙江海洋学院
我国炼油工业发展概况
第二阶段:1966-1978年
我国新建的几条长距离输油管线投入使用 在技术方面,炼油工业的“五朵金花”-即流化催化裂 化、催化重整、延迟焦化、尿素脱蜡以及催化剂、添加 剂五方面工艺技术开发成功 国内各个老厂都进行了技术改造扩建,并且发挥中央和 地方两个积极性,在全国建设了一批大中型炼油厂和地 方、油田小炼油厂
充分利用 技术进步
合理加工利用
节约
32
浙江海洋学院
意培养兴趣
5
浙江海洋学院
教材及主要参考资料
林世雄.《石油炼制工程》(第3版),北京:石油 工业出版社,2000 寿德清,山红红 .《石油加工概论》,东营:石油 大学出版社,1996
催化脱蜡:改善柴油低温流动性的关键工艺

Vol.43No.5May 2018上海化工Shanghai Chemical Industry催化脱蜡:改善柴油低温流动性的关键工艺可持续发展在过去几年中,柴油燃料因其燃烧会排放一氧化碳、氮氧化物、颗粒物等污染物,由此损害健康与环境而成为了众矢之的。
多国政府和国际监管机构纷纷发表声明,提出希望在各自指定的时间范围内逐步淘汰传统的烃基发动机燃料。
产品规格越来越严,提高柴油质量和达到更高性能、满足合规要求是全球炼油厂面临的主要挑战。
另一大难题是在寒冷气候时柴油燃料中逐渐沉积的石蜡,及其对发动机启动所带来的负面影响。
当环境温度下降时,柴油中的蜡会开始形成结晶并凝固,从而影响柴油的流动性。
这些蜡晶可能会带来一系列潜在问题,如堵塞燃油滤清器,妨碍发动机点火,导致设备损坏。
抵抗出现蜡晶的方法为了生产出满足在低温环境下,仍需保持一定流动性的柴油产品,业界使用了各种技术改善冷流需求:从最简单的在柴油中添加煤油这样的轻质燃料,到使用添加剂,或溶剂脱蜡,以及单独添加异构化反应器和先进的催化脱蜡。
然而,这些方法或具有局限性,或有高成本和损失成品率等重大缺陷。
相较而言,使用加氢器改善低温流动性具备其它方式无法比拟的操作优势和经济优势,异构化脱蜡和选择性裂解脱蜡是两种可行的方法。
加氢异构化通过将碳原子从直链的正构烷烃重排为支链的异构烷烃来改善原料的低温流动性,而加氢裂化则通过将长链正构烷烃分解成两个更小的分子来降低浊点和/或倾点。
为了在加氢器或是超低硫柴油单元中对石蜡烃进行选择性裂解,而避免低温流动性良好的环烷或异构烷烃的性状产生不良的改变就必须使用特殊催化剂。
科莱恩催化剂的作用加氢裂化催化剂由于其对支链异构烷烃和直链正构烷烃的选择性,在业界使用了近20年之后仍然是中间馏分油品脱蜡处理的实际标准。
科莱恩的中孔沸石催化剂,例如用于含硫柴油(与加氢脱硫催化剂合用)的HYDEX-G 及其姊妹催化剂,用于润滑油的HY -DEX-L ,因其独特的酸性分布特点,处理效果卓越。
酮苯脱蜡装置在脱蜡脱油工艺方面改进
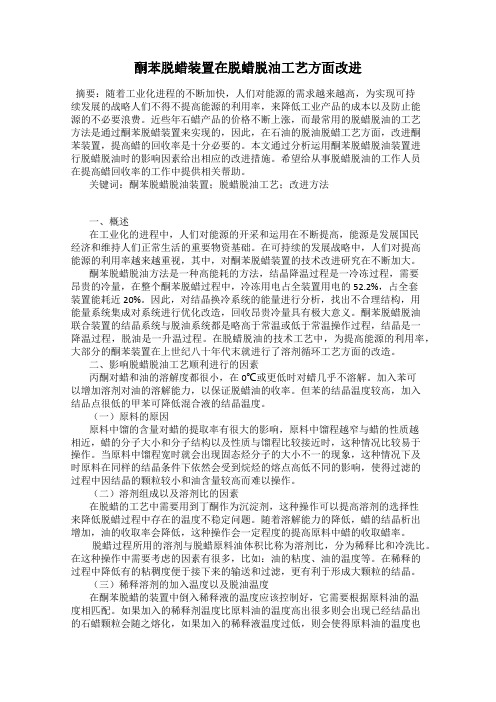
酮苯脱蜡装置在脱蜡脱油工艺方面改进摘要:随着工业化进程的不断加快,人们对能源的需求越来越高,为实现可持续发展的战略人们不得不提高能源的利用率,来降低工业产品的成本以及防止能源的不必要浪费。
近些年石蜡产品的价格不断上涨,而最常用的脱蜡脱油的工艺方法是通过酮苯脱蜡装置来实现的,因此,在石油的脱油脱蜡工艺方面,改进酮苯装置,提高蜡的回收率是十分必要的。
本文通过分析运用酮苯脱蜡脱油装置进行脱蜡脱油时的影响因素给出相应的改进措施。
希望给从事脱蜡脱油的工作人员在提高蜡回收率的工作中提供相关帮助。
关键词:酮苯脱蜡脱油装置;脱蜡脱油工艺;改进方法一、概述在工业化的进程中,人们对能源的开采和运用在不断提高,能源是发展国民经济和维持人们正常生活的重要物资基础。
在可持续的发展战略中,人们对提高能源的利用率越来越重视,其中,对酮苯脱蜡装置的技术改进研究在不断加大。
酮苯脱蜡脱油方法是一种高能耗的方法,结晶降温过程是一冷冻过程,需要昂贵的冷量,在整个酮苯脱蜡过程中,冷冻用电占全装置用电的52.2%,占全套装置能耗近20%。
因此,对结晶换冷系统的能量进行分析,找出不合理结构,用能量系统集成对系统进行优化改造,回收昂贵冷量具有极大意义。
酮苯脱蜡脱油联合装置的结晶系统与脱油系统都是略高于常温或低于常温操作过程,结晶是一降温过程,脱油是一升温过程。
在脱蜡脱油的技术工艺中,为提高能源的利用率,大部分的酮苯装置在上世纪八十年代末就进行了溶剂循环工艺方面的改造。
二、影响脱蜡脱油工艺顺利进行的因素丙酮对蜡和油的溶解度都很小,在0℃或更低时对蜡几乎不溶解。
加入苯可以增加溶剂对油的溶解能力,以保证脱蜡油的收率。
但苯的结晶温度较高,加入结品点很低的甲苯可降低混合液的结晶温度。
(一)原料的原因原料中馏的含量对蜡的提取率有很大的影响,原料中馏程越窄与蜡的性质越相近,蜡的分子大小和分子结构以及性质与馏程比较接近时,这种情况比较易于操作。
当原料中馏程宽时就会出现固态烃分子的大小不一的现象,这种情况下及时原料在同样的结晶条件下依然会受到烷烃的熔点高低不同的影响,使得过滤的过程中因结晶的颗粒较小和油含量较高而难以操作。
悬浮流化床在双氧水生产工艺的应用

26当前全球双氧水生产工艺大多采用蒽醌法,该方法具体分为氢化、氧化、萃取以及后处理等工艺流程,其中催化加氢作为蒽醌法生产双氧水核心工艺之一,其氢化效率对于产品生产质量影响较为明显。
1 双氧水蒽醌法氢化流化床技术应用优势由于催化加氢方式差异,蒽醌法具体包括流化床及固定床工艺,其中我国基本采用固定床工艺。
目前氢化流化床业已在国内推广使用,而国外很多双氧水生产企业使用流化床加氢工艺,固定床使用比例极少。
固定床加氢工艺实际应用过程中,常出现局部反应温度过高,催化剂实际利用效率低,产品质量差,并且单位产品生产效率较低,这在一定程度上限制国内双氧水生产行业发展。
同时流化床基本使用粉末催化剂,由于这些催化剂粒径小,催化效率因子高,实际加氢效率为固定床1.5~2倍,所以开发应用流化床蒽醌加氢工艺已成为国内蒽醌法工艺发展的关键方向之一。
双氧水蒽醌法氢化流化床主要采用高活性、高选择性流化床钯催化剂,采用气态搅拌方式使得催化剂呈现流化状态,进而提升传质、传热效率。
与固定床反应器相比,扩大双氧水生产规模时,流化床工艺不会出现偏流、沟流及触媒板结等问题,并且氢化效率常稳定在11g/L以上,相关副反应及氢化降解物明显降低。
同时生产过程中仅有10%~15%工作液流入活性氧化铝再生床,这样可以减少再生设备数量及工作负担,再生剂活性氧化铝消耗量小[1]。
2 双氧水蒽醌法氢化流化床的影响因素一般来说,双氧水蒽醌法氢化流化床应用过程影响因素较多,其中较为重要的影响因素具体包括下列两个。
2.1 流化床催化剂双氧水蒽醌法氢化流化床技术应用过程中,应选择合适的催化剂。
目前流化床蒽醌加氢主要采用Pd 系催化剂,其基于采用粉状Al 2O 3和粉状SiO 2作为载体还使用无载体Pd 黑催化剂。
催化剂粒径对于生产影响较大,如果粒径过大,而催化剂难以和工作液形成浆液相,这样明显减少催化剂和反应物之间的分散效果,催化剂颗粒常出现破碎问题,但催化剂粒径过小时,其会导致催化剂和氢化后的工作液分离难度明显增加,当前工业生产过程中常用的流化床催化剂粒径大多为20~200μm 。
石油炼制过程(2)

• FDFCC工艺特别适合于重油催化裂化,能使装置的焦炭燃 烧热得到有效的利用。
• FDFCC工艺可采用常规的催化裂化催化剂, 也可以采用具 有降烯烃功能的催化剂。
石油炼制过程 双沉降器、双分馏塔流程
FDFCC-B流程
石油炼制过程
裂化反应和转化反应: 两个反应区概念
现有催化裂化过程仅是裂化反 应一维结构; 对于既要完成烃类的充分裂
化、又要促进能大幅度降低汽 油烯烃的氢转移反应则难免顾 此失彼。
具有裂化反应和氢转移反应的 二维反应结构, 可以满足裂化 反应和氢转移反应各自的需求
若只有1套催化裂化装置, 且对汽油 降烯烃要求不高, 可采用单沉降器、 单分馏塔催化裂化汽油改质流程
石油炼制过程
石油炼制过程
催化裂化过程
热裂化过程 催化裂化过程 催化裂解工艺
催化裂化过程发展核心
1. 催化剂:从无定型硅铝催化剂、X型分子筛、 Y型分子筛和超稳分子筛到中孔分子筛
2. 反应器:从固定床、移动床、密相流化床到提 升管反应器
3. 反应再生系统:两段再生、烧焦罐等催化剂再 生技术;快速汽化、快速反应和快速分离的 “ 三快” 技术,以及催化剂预提升技术等
石油炼制过程
石油炼制过程
催化裂化
我国催化裂化装置以FCC为主,40%原料为渣油。 所生产的汽油和柴油组分分别占成品汽、柴油总量的75%和30% 左右, 所生产的丙烯量约占丙烯总产量的40%。 同时, 还可以为烷基化装置和醚化装置提供原料。
催化汽油中烯烃含量明显超过清洁汽油标准。因此降低催化裂化汽 油烯烃含量是我国流化催化裂化技术面临的重要和紧迫的任务。
白油异构脱蜡技术在加氢装置上的应用
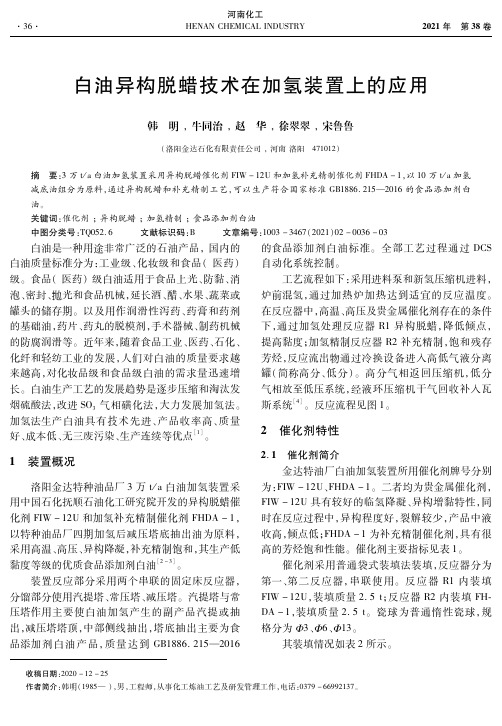
白油异构脱蜡技术在加氢装置上的应用韩 明,牛同治,赵 华,徐翠翠,宋鲁鲁(洛阳金达石化有限责任公司,河南洛阳 471012)摘 要:3万t/a白油加氢装置采用异构脱蜡催化剂FIW-12U和加氢补充精制催化剂FHDA-1,以10万t/a加氢减底油组分为原料,通过异构脱蜡和补充精制工艺,可以生产符合国家标准GB1886.215—2016的食品添加剂白油。
关键词:催化剂;异构脱蜡;加氢精制;食品添加剂白油中图分类号:TQ052.6 文献标识码:B 文章编号:1003-3467(2021)02-0036-03 白油是一种用途非常广泛的石油产品,国内的白油质量标准分为:工业级、化妆级和食品(医药)级。
食品(医药)级白油适用于食品上光、防黏、消泡、密封、抛光和食品机械,延长酒、醋、水果、蔬菜或罐头的储存期。
以及用作润滑性泻药、药膏和药剂的基础油,药片、药丸的脱模剂,手术器械、制药机械的防腐润滑等。
近年来,随着食品工业、医药、石化、化纤和轻纺工业的发展,人们对白油的质量要求越来越高,对化妆品级和食品级白油的需求量迅速增长。
白油生产工艺的发展趋势是逐步压缩和淘汰发烟硫酸法,改进SO3气相磺化法,大力发展加氢法。
加氢法生产白油具有技术先进、产品收率高、质量好、成本低、无三废污染、生产连续等优点[1]。
1 装置概况洛阳金达特种油品厂3万t/a白油加氢装置采用中国石化抚顺石油化工研究院开发的异构脱蜡催化剂FIW-12U和加氢补充精制催化剂FHDA-1,以特种油品厂四期加氢后减压塔底抽出油为原料,采用高温、高压、异构降凝,补充精制饱和,其生产低黏度等级的优质食品添加剂白油[2-3]。
装置反应部分采用两个串联的固定床反应器,分馏部分使用汽提塔、常压塔、减压塔。
汽提塔与常压塔作用主要使白油加氢产生的副产品汽提或抽出,减压塔塔顶,中部侧线抽出,塔底抽出主要为食品添加剂白油产品,质量达到GB1886.215—2016的食品添加剂白油标准。
- 1、下载文档前请自行甄别文档内容的完整性,平台不提供额外的编辑、内容补充、找答案等附加服务。
- 2、"仅部分预览"的文档,不可在线预览部分如存在完整性等问题,可反馈申请退款(可完整预览的文档不适用该条件!)。
- 3、如文档侵犯您的权益,请联系客服反馈,我们会尽快为您处理(人工客服工作时间:9:00-18:30)。
© 1994-2010 China Academic Journal Electronic Publishing House. All rights reserved. http://www.cnki.net2002年4月炼 油 设 计PETROLEUMREFINERYENGINEERING第32卷第4期流化床溶剂脱蜡工艺的工业开发姜春华 李裕如中国石油兰州石化公司(甘肃省兰州市730060
)
李志东清华大学化工系(北京市100084
)
摘要:在兰州石化公司80kt/a流化床溶剂脱蜡工业试验装置上对流化床溶剂脱蜡新工艺进行了工业开发,取得了突破性进展,基本实现了工业化正常操作,在国内外首次使该工艺实现工业化。工业开发表明,流化床脱蜡工艺与现有脱蜡工艺相比具有设备总传热系数高(450~1000W/(m2・K)),油收率高(与冷点工艺比提高5个百分点以上),蜡中油含量低(与冷点工艺比二段过滤蜡的油含量降低4~5个百分点),工艺和溶剂组成都对原料变化的适应性强等优点。
主题词:流化床 溶剂脱蜡 工业规模 流化床溶剂脱蜡工艺是一项具有世界先进水平的润滑油溶剂脱蜡新工艺,但国内外尚无工业化装置。1995年烟台大学等单位进行了流化床溶剂脱蜡工艺的中型试验,并获得了成功[1]。为了使该研究成果尽快工业化,在中型试验的基础上,1996年8月在兰州炼油化工总厂炼油二厂(现兰州石油化工公司炼油厂)Ⅲ套溶剂脱蜡装置的基础上,新建了流化床结晶系统,形成加工能力80kt/a的流化床溶剂脱蜡工业化试验装置。几年来,经过不断完善,逐步解决了流化床溶剂脱蜡工业化试验中暴露出的技术问题,实现了流化床溶剂脱蜡工业化装置的正常操作,取得良好效果。1 工艺介绍1.1 流化床结晶器工业试验采用分流式流化床结晶器,该结晶器分为换冷结晶器和氨冷结晶器。每台换冷结晶器由1根提升管插入1个壳体内构成,每台氨冷结晶器由m根提升管并联地装在1个壳体内构成。每路流化床结晶器由n台换冷结晶器和氨冷结晶器串联组成。图1为流化床工艺原则流程。换冷结晶器和氨冷结晶器内管内径为100mm。每条提升管内预装入一定数量的小钢球作为流化固体颗粒。1.2 基本原理用流化床结晶器代替套管结晶器进行溶剂脱蜡。大量的固体颗粒在流化床结晶器中湍动,使附着在流化床结晶器管壁上的蜡迅速地被刮掉,
这一过程清洁了管壁,结果总传热系数高,同时析出的蜡结晶颗粒均匀、包油少,便于油和蜡的分离。因此该工艺在传热、油收率、蜡中油含量等方面有明显的优越性。1.3 工艺流程原料与一次稀释溶剂按一定比例混合后,经冷却进缓冲罐。流化床进料泵抽缓冲罐混合液,
经流量控制器,分几路从内管下部进入换冷流化床与冷滤液逆流换冷,混合液达到一定温度后,再经氨冷流化床与液氨逆流换冷。混合液达到脱蜡温度后,从氨冷流化床最后一级流出进入过滤中间罐,经真空过滤机过滤分离,并加入冷洗溶剂。过滤系统分离出的一段冷滤液作为流化床换冷段的冷剂;分离出的一段蜡液加入三次溶剂后再次过滤,分离出的二段滤液循环使用。液氨经多点进入氨冷流化床的壳体。
收稿日期:2001-10-19。作者简介:姜春华,高级工程师,1985年抚顺石油学院毕业,
1997年石油大学(北京)硕士研究生毕业,一直从事炼油技术管理工作。© 1994-2010 China Academic Journal Electronic Publishing House. All rights reserved. http://www.cnki.net
图1 流化床工艺原则流程2 工业试验2.1 试验条件及结果1999年底至2000年初,成功地进行了流化床脱蜡工艺第五次工业试验。这次试验对新疆混合原油和青海原油的减压精制油、残渣油等不同原料进行了试验,重点通过对青海减一、二线油的试验,考察流化床工艺对石蜡基油的适应性;通过对青海减二线油及残渣油的试验,考察流化床工艺的溶剂组成对不同原料的适应性;通过对同一罐减三线油原料冷点工艺与流化床工艺对比试验,考察新老工艺的去蜡油收率、蜡中油含量等生产技术指标情况。试验期间操作较平稳、产品质量合格、试验周期较长,取得的数据能客观反映实际生产情况。工业试验中的原料性质、主要操作条件及试验结果见表1。表1 原料性质、主要操作条件及试验结果
项 目减一线油(青海/新疆)减二线油(青海/新疆)减三线油(新疆混合)残渣油(新疆混合)原料性质 粘度(50℃)/mm2・s
-17.2/6.613.8/16.75.6~5.7①31
①
密度(20℃)/kg・m
-3836.2/874.8847.6/884.9865.8~872894.9
凝点/℃27/-132~3748
比色/号3.0/3.03.5/2.01.0~1.50.44(残炭) 闪点/℃161/157212/195210
中和值/mgKOH・g
-10.53/1.910.45/2.640.09~0.120.2
主要操作条件 原料量/t・h
-17.5±0.36.67±0.38.57±0.37.5±0.3
溶剂中甲乙酮质量含量,%65~6865~6864~6765~68
总溶剂质量比3.0±0.23.5±0.22.5±0.23.0±0.2
流化床进料温度/℃30~3530~3535~4035~40
换冷流化床出口温度/℃-2~109~163~78~20
氨冷流化床出口温度/℃-30~-33-19~-23-19~-23-18~-20
试验结果 去蜡油凝点/℃-27~-25-14~-16-12~-19-5~-17
流化床工艺去蜡油收率,%65.76/93.7950.12/61.6971.98~84.8577.2~86.8
流化床工艺去蜡油收率平均值,%83.4559.7281.0081.61
冷点工艺去蜡油收率,%74.34
②50.1964.24~77.89③69.6②
冷点工艺去蜡油收率平均值,%74.34
②50.1970.90③69.6②
流化床工艺蜡中油含量,%4.6/11.35.66~19.214.28~17.41
流化床工艺蜡中油含量平均值,%9.798.5
流化床工艺模拟过滤蜡中油含量,%1.02~2.30
冷点工艺蜡中油含量,%8.81~22.38
冷点工艺蜡中油含量平均值,%13.72
注:①100℃粘度;
②一段过滤工艺数据,其余为二段过滤工艺数据;
③冷点工艺抽同一罐减三线原料试验统计数据,其余冷点工艺数据为1999年年报统计数据。
—11—第4期 姜春华等.流化床溶剂脱蜡工艺的工业开发© 1994-2010 China Academic Journal Electronic Publishing House. All rights reserved. http://www.cnki.net
2.2 试验结果讨论2.2.1 蜡中油含量流化床内固体颗粒对蜡结晶的挤压和流化床内的湍流状态加快了蜡分子的扩散,形成更紧密的蜡球,这种蜡球的油含量低,并且由于流化颗粒对管壁的快速、均匀的碰撞,不会造成大量蜡积累,从而可以得到油含量较低的蜡。工业试验中,加工同一罐减三线油原料,流化床工艺与冷点工艺二段泵出口蜡膏油含量对比数据见表1,流化床工艺蜡中油含量降低4~5个百分点。后又用吸滤棒法进行模拟过滤试验,对吸出的蜡膏分析其蜡中油含量,如表1中所示,其蜡中油含量平均值为1.77%。预计若采用三段过滤流化床工艺可得到相当于冷点工艺需四段过滤的油含量效果。2.2.2 去蜡油收率从表1中可以看到,流化床工艺平均油收率为59.72%~83.45%(二段过滤),而冷点脱蜡油收率为50.19%~74.34%(部分为一段过滤),高出冷点工艺9个百分点以上,由此可进一步证实流化床工艺蜡中油含量很低。为排除原料性质差异的影响,试验期间采用同一罐新疆混合减三线油原料,冷点工艺与流化床工艺(均为二段过滤)进行对比,由表1可见,流化床工艺较冷点工艺油收率提高10.1个百分点。扣除试验时溶剂比较大及二段过滤比一段过滤去蜡油收率提高3%~5%的影响,流化床工艺比冷点工艺的去蜡油收率提高达5个百分点以上。2.2.3 总传热系数由于流化床结晶器有效换热段内有很多相互碰撞的钢球,不但有利于传热,而且能及时清除结晶器内管壁上结出的蜡,有利于总传热系数的提高。工业试生产时采用了结构上进行特殊处理的流化床结晶器,有利于达到高的总传热系数的效果。表2 流化床工艺与冷点工艺 总传热系数比较 W/(m2・K)项 目减三线油 流化床 冷点 残渣油 流化床 冷点 换冷819.381361185102氨冷480.378556975 由表2可见,流化床工艺的总传系数为450~1000W/(m2・K),比冷点工艺高6~11倍。
3 流化床脱蜡工艺特点分析及问题讨论3.1 流化床压力降增大问题流化床依靠床内流化固体搅动并冲刷管壁将管壁上的结蜡刮落。当固体颗粒(钢球)直径已选定,在一定流速下,它的刮蜡能力也已确定。如果刮蜡能力超过由于冷冻而在管壁上结蜡的数量,
流化床可以平稳地进行脱蜡操作。但如刮蜡能力小于结蜡能力,管壁结蜡不能全部刮下并逐渐积累,使管内流通面积变小,阻碍流体流动,将导致压力降增大。流化床刮蜡能力虽然不能做很大的改变,但其结蜡能力是可以调节的。例如对蜡含量高的原料可选用较高的溶剂比,而对蜡含量低的原料可选用较低的溶剂比,以保证在单位面积上单位时间内析出的蜡量小于刮蜡能力,流化床就可以稳定操作。前期工业试验过程中都有压力降增大问题。经多次分析试验认为,流化床高度对压力降的影响是至关重要的。由于试验初期缺少测定流化床高度的手段以及流量测量仪表不准,致使操作规定条件很难保证。后来安装了看窗,对流化床高度进行校正调节,这样流化床压力降增大问题基本得到解决。若要实现长期平稳操作,还应采取冷冻系统高低压分离等措施。3.2 溶剂组成对原料变化的适应性如表1所示,试验期间,采用65%~68%酮含量的溶剂处理减一、二、三线油及残渣原料均取得了较好效果。工业试验证明,该工艺对原料的适应性强,且表现出溶剂组成对原料变化的适应性也强,尤其在处理残渣原料时效果更明显。在用冷点工艺处理残渣原料时,用68%酮含量的溶剂会出现蜡饼过敏不成型现象,而流化床工艺处理残渣原料时,不但油收率高、蜡中油含量低,而且过滤速度快。初步分析认为,可能是与后者结晶过程快,在流化床结晶器中原料与溶剂停留时间短(温降为0.78~1.01℃/m),颗粒扰动大等特点有关。这一优势,对工业化装置非常有利,装置切换原料时勿需频繁调整溶剂组成。
4 结 论(1)流化床溶剂脱蜡工业开发试生产表明,采
—21—炼 油 设 计 2002年第32卷