第三节活性染料染色
活性染料染色原理
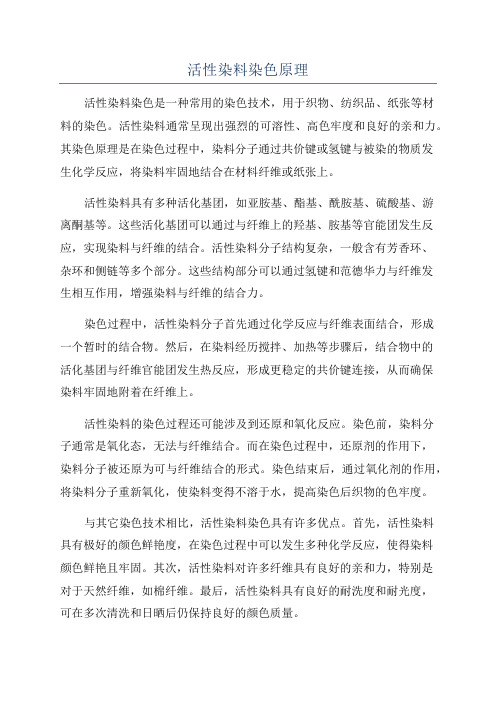
活性染料染色原理活性染料染色是一种常用的染色技术,用于织物、纺织品、纸张等材料的染色。
活性染料通常呈现出强烈的可溶性、高色牢度和良好的亲和力。
其染色原理是在染色过程中,染料分子通过共价键或氢键与被染的物质发生化学反应,将染料牢固地结合在材料纤维或纸张上。
活性染料具有多种活化基团,如亚胺基、酯基、酰胺基、硫酸基、游离酮基等。
这些活化基团可以通过与纤维上的羟基、胺基等官能团发生反应,实现染料与纤维的结合。
活性染料分子结构复杂,一般含有芳香环、杂环和侧链等多个部分。
这些结构部分可以通过氢键和范德华力与纤维发生相互作用,增强染料与纤维的结合力。
染色过程中,活性染料分子首先通过化学反应与纤维表面结合,形成一个暂时的结合物。
然后,在染料经历搅拌、加热等步骤后,结合物中的活化基团与纤维官能团发生热反应,形成更稳定的共价键连接,从而确保染料牢固地附着在纤维上。
活性染料的染色过程还可能涉及到还原和氧化反应。
染色前,染料分子通常是氧化态,无法与纤维结合。
而在染色过程中,还原剂的作用下,染料分子被还原为可与纤维结合的形式。
染色结束后,通过氧化剂的作用,将染料分子重新氧化,使染料变得不溶于水,提高染色后织物的色牢度。
与其它染色技术相比,活性染料染色具有许多优点。
首先,活性染料具有极好的颜色鲜艳度,在染色过程中可以发生多种化学反应,使得染料颜色鲜艳且牢固。
其次,活性染料对许多纤维具有良好的亲和力,特别是对于天然纤维,如棉纤维。
最后,活性染料具有良好的耐洗度和耐光度,可在多次清洗和日晒后仍保持良好的颜色质量。
总之,活性染料染色是一种重要的染色技术,通过染料分子与纤维官能团发生化学反应,实现染料与纤维的牢固结合。
活性染料染色具有良好的亲和力、色牢度和耐洗度,广泛应用于织物、纺织品和纸张等材料的染色。
随着科技的进步,活性染料染色技术不断发展,为纺织品印染行业带来更多的颜色选择和实现更高的染色质量。
活性染料染色(1)

棉织物的活性染料染色一、实验目的(1)自行选取染料及设计工艺,掌握活性染料对棉的染色过程,巩固所学的活性染料对棉纤维染色的基本理论知识,学会自己设计工艺处方和工艺条件,并进行染色试验。
(2)学会活性染料吸尽率和固色率的测定二、实验原理(1)染色原理:活性染料是一种含有能与纤维起反应形成共价键的活性基团的染料,常见的活性基团有二氯均三嗪型、乙烯砜型和一氯均三嗪型等三种,它们的反应能力各不相同,所以采用的工艺条件也不同,分别采用低温、中温和高温进行染色。
活性染料染色时通过纤维对染料的吸附、染料扩散进入纤维内部达到上染平衡,加入碱后,染料开始与纤维发生反应而固着,并重新达到一个平衡。
染后进行皂煮,除去并未与纤维固着的染料或水解染料,提高色泽的鲜艳度。
活性染料浸染的上染曲线由于活性染料在水溶液中要发生水解,从而影响活性染料的利用率,为了改善上述情况,现在开发出双活性基团甚至三活性基团的活性染料,可以使活性染料的固色率达到80%以上。
双活性基染料常见的有:含两个相同的一氯均三嗪型如国内KE型活性染料;含一个一氯均三嗪、一个为乙烯砜型的染料如国内M型活性染料。
(2) 固色原理: 活性染料与棉纤维的反应在碱性条件下,纤维素能形成纤维素负离子,能和活性染料发生亲核取代、加成反应,进而形成染料--纤维共价键,二氯均三嗪型较活泼,只需在较低温度下即可反应,而一氯均三嗪型则需在温度较高、碱性较强条件下才能反应。
影响此反应的因素有很多。
染料与纤维与水的反应为平行反应,因为水也是亲核试剂,反应条件机理相同。
染料一经水解即失去与纤维的反应能力,固色率大为降低。
从反应动力学研究得到,固着反应比水解反应快40倍左右,染色时PH一般为10~11为宜,X型可用碱性较弱的小苏打,对K型,则采用Na2CO3、Na3po4,甚至NaOH。
染色温度具体根据不同染料性能而定。
促染用元明粉,加入要掌握一多二早,分批加入的原则。
浴比尽可能小些,以提高固色率。
活性染料染色—活性染料对纤维素纤维染色的方法及工艺

特点:设备简单、能耗低、染料利用率较高,匀染性好 ,适用于小批量,多品种生产
染料要求:反应性强,直接性低,扩散速率快的染料
活性染料对纤维素纤维的染色
活性染料对纤维素纤维的染色
§二浴二步法 1)工艺流程 练漂半制品→(水洗润湿)→染色(上染)→固色→冷 水洗→热水洗→皂煮→热水洗→冷水洗→脱水→烘干 2)工艺处方及条件
活性染料对纤维素纤维的染色
活性染料对纤维素纤维的染色
§一浴一步法 1)工艺流程 练漂半制品→染色(上染、固色)→冷水洗→热水洗 →皂煮→热水洗→冷水洗→脱水→烘干 2)工艺处方及工艺条件
活性染料对纤维素纤维的染色
2)一浴二步法 这种染色方法是先在中性浴中进行染色,让染料上染
纤维,并加电解质进行促染,再加入碱剂固色。 特点:染浴吸尽率较高,染浴稳定性好,色光易控制, 织物的染色牢度较好,一般不续缸染色。
这种方法主要适用于小批量、多品种的染色,目前棉 针织物、纱线等一般都采用这种方法进行染色。
电解质一般选用元明粉,其用量取决于染料亲和力的高低、 色泽的深浅、和染料溶解度的大小。
亲和力高、溶解度小、色泽浅,可不加或少加,以保证匀染 效果,反之则应多加,提高染料上染百分率。
活性染料对纤维素纤维的染色
碱剂通常为纯碱和磷酸三钠,少数也可用烧碱。染料反应 性强的宜用纯碱,反应性较弱的宜用磷酸三钠,个别情况 可用烧碱。由于纯碱价廉,目前工厂采用纯碱的比较多。 ④后处理 一般不采用碱性皂洗,防止引起染料—纤维键色光改变和 染色牢度下降。 织物上的碱要充分洗净,防止织物在贮存过程中发生色变 ,即“风印”。防止办法: 1)充分洗除织物上的碱剂 2)水洗后烘干前浸轧醋酸1g/L
棉织物活性染料染色
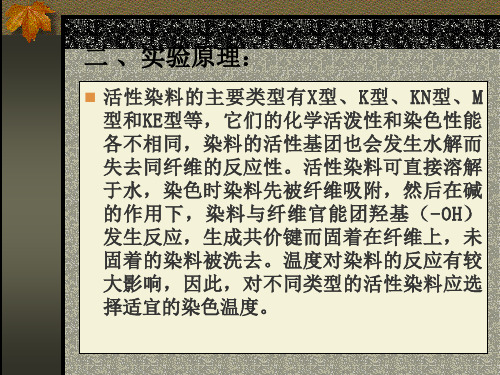
活性染料的主要类型有X型、K型、KN型、M 型和KE型等,它们的化学活泼性和染色性能 各不相同,染料的活性基团也会发生水解而 失去同纤维的反应性。活性染料可直接溶解 于水,染色时染料先被纤维吸附,然后在碱 的作用下,染料与纤维官能团羟基(-OH) 发生反应,生成共价键而固着在纤维上,未 固着的染料被洗去。温度对染料的反应有较 大影响,因此,对不同类型的活性染料应选 择适宜的染色温度。
三、主要仪器和染化料
恒温水浴锅、烧杯。 氯化钠、碳酸钠、磷酸钠、活性红X-3B、
活性蓝KGL。
四 、 实验步骤
温度影响实验
1 、处方和工艺条件
染化料
Hale Waihona Puke 1#活性红X-3B(对织重%) 2
活性兰KGL(对织重%) —
2# 3# 4#
2 ——
—2
2
食盐(g/l) 碱剂(g/l) 温度
30 30 碳酸钠15 室温 90ºC
五 、结果和讨论
1、 贴样,记录实验现象 2、分别写出X型和K型 染料适宜的染色温度,
并阐述染浴温度对染料染色性能的影响。
30 30 磷酸钠15 室温 90ºC
浴比
50:1
2 、工艺步骤
按处方配置染浴,称取2g棉织物4块,用 水浸渍后挤干,分别投入染浴中,1#、3# 室温,2#、4#放入90℃恒温水浴中,染杯 上盖表面皿防止染液蒸发。染15min后,加 入食盐,再染15min后,加入碱剂,固色 30min,染毕取出试样,充分水洗,并皂煮 5min(肥皂5g/l,浴比50:1)后水洗,晾 干。
活 性 染 料
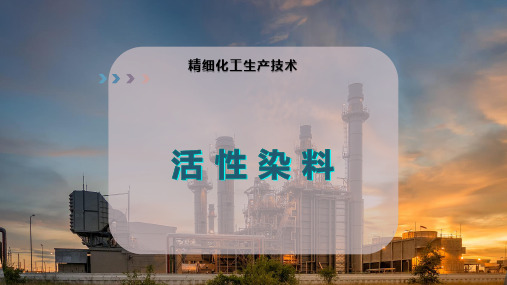
活性染料
§8.1 引言 ➢ 活性染料(Reactive dyes)是一类在化学结构上含有活
性基团的水溶性染料,主要由染料母体[Parent dye(s)]、 能与纤维官能团反应的活性基[Reactive group(s)],以及 连接染料母体与活性基的连接基(或桥基,Bridging group)三部分组成。 ➢ 染料母体是活性染料的共轭发色体系,直接决定活性染 料的颜色特征,染料对纤维的直接性,上染特性及部分 染色坚牢度。活性基决定了活性染料的反应活泼性,直 接影响染料的固色率和固色效率。活性基与纤维成键稳 定性的高低影响到印染产品的各种湿处理牢度。
活性染料
➢ 通常活性染料的染料母体可以用偶氮、蒽醌、酞菁等各 种结构类型,合成工艺路线一般采用预制的染料母体再 与多官能团的活性基进行缩合而得,也可先在染料中间 体上接入活性基,然后再合成染料母体的方法得到。
➢ 染色过程包括上染、固色、皂煮等工序。 ➢ 活性染料色谱齐全,湿处理牢度高,匀染性好;染色方
法简单; ➢ 适用纤维:纤维素纤维,也用于蛋白质纤维、锦纶; ➢ 缺点:储存稳定性差,某些品种日晒、耐气候牢度差,
染料利用率低,造成浪费、污染。
精细化工生产技术
活性染料SO3NΒιβλιοθήκη NN NaO3SOH NH
N NH
NN Cl
Cl SO3Na
➢染料母体:发色体系——使染料具有一定的颜色;水溶 性基团——使染料易溶于水,呈单分子状态。
➢活性基:具有与纤维反应的能力。连接基——连接活性 基和染料母体;离去基——在反应中被纤维分子取代而 脱离染料;取代基——可以影响活性基的活性。
毛用活性染料染色的实验报告_实验报告_

毛用活性染料染色的实验报告一、实验目的(1)自行选取染料及设计工艺,掌握活性染料对棉的染色过程,巩固所学的活性染料对棉纤维染色的基本理论知识,学会自己设计工艺处方和工艺条件,并进行染色试验。
(2)学会活性染料吸尽率和固色率的测定二、实验原理(1)染色原理:活性染料是一种含有能与纤维起反应形成共价键的活性基团的染料,常见的活性基团有二氯均三嗪型、乙烯砜型和一氯均三嗪型等三种,它们的反应能力各不相同,所以采用的工艺条件也不同,分别采用低温、中温和高温进行染色。
活性染料染色时通过纤维对染料的吸附、染料扩散进入纤维内部达到上染平衡,加入碱后,染料开始与纤维发生反应而固着,并重新达到一个平衡。
染后进行皂煮,除去并未与纤维固着的染料或水解染料,提高色泽的鲜艳度。
活性染料浸染的上染曲线由于活性染料在水溶液中要发生水解,从而影响活性染料的利用率,为了改善上述情况,现在开发出双活性基团甚至三活性基团的活性染料,可以使活性染料的固色率达到80%以上。
双活性基染料常见的有:含两个相同的一氯均三嗪型如国内KE型活性染料;含一个一氯均三嗪、一个为乙烯砜型的染料如国内M型活性染料。
(2) 固色原理: 活性染料与棉纤维的反应在碱性条件下,纤维素能形成纤维素负离子,能和活性染料发生亲核取代、加成反应,进而形成染料--纤维共价键,二氯均三嗪型较活泼,只需在较低温度下即可反应,而一氯均三嗪型则需在温度较高、碱性较强条件下才能反应。
影响此反应的因素有很多。
染料与纤维与水的反应为平行反应,因为水也是亲核试剂,反应条件机理相同。
染料一经水解即失去与纤维的反应能力,固色率大为降低。
从反应动力学研究得到,固着反应比水解反应快40倍左右,染色时PH一般为10~11为宜,X型可用碱性较弱的小苏打,对K型,则采用Na2CO3、Na3po4,甚至NaOH。
染色温度具体根据不同染料性能而定。
促染用元明粉,加入要掌握一多二早,分批加入的原则。
浴比尽可能小些,以提高固色率。
活性染料染色ReactiveDye

O D H N C C X CH2
五、多活性基类(Bifunctional reactive dyes)
一氯均三嗪基和β-乙烯砜硫酸酯基——国产 M型、国外Sumifix supra、部分Procion Supra,兼顾两者长处。 一氟均三嗪基和β-乙烯砜硫酸酯基——国外 Cibacron FN 型,主要用于印花及连续轧染。 两个一氯均三嗪——国产的KE、部分KD、 国外的Procion supra。
第四章 活性染料染色 Reactive Dye
第一节 引言(Introduction)
活性染料——含有一个或一个以上的反应性 基团(reactive group),在适当的条件下, 能和纤维上的羟基、氨基等发生反应,形成 共价键结合的一类染料。
Dyeing properties 1. Advantages——Simple structure,Bright color, Wide range of color,Simplicity of application, Low cost,Hard-water resistant,Good leveling dyeing,good washing and crocking fastness. 2. Disvantages——Low utilization (60~70%)and high chroma in waste water due to the hydrolysis of dye; Consumption of considerable amounts of salt to accelerating dyeing; poor fastness to chlorine-bleaching.
OH D P O OH
• Α-卤代丙烯酰胺型——国产PW型、国外商品有 Lanasol(X为Br)和Lanasyrein(X为Cl),主要用 于蛋白质纤维的染色。
活性染料染色原理

活性染料染色原理
活性染料是一类在纤维材料上进行染色的染料,其分子中含有与纤维材料分子结构相似的活性基团,能够与纤维材料发生共价键结合,并通过共价键稳定地附着在纤维上。
活性染料染色具有颜色鲜艳、染色均匀、耐洗、耐光、耐热、耐摩擦等特点,因此得到广泛应用。
首先,物理吸附是活性染料附着在纤维表面的一种吸附现象。
纤维材料表面通常带有一定的电荷,而活性染料分子中的活性基团带有正电荷或负电荷,通过静电吸引力与纤维表面的电荷相互作用,形成物理吸附。
这种吸附是可逆的,容易受到洗涤、摩擦等外界因素的影响。
其次,离子键是活性染料与纤维材料结合的一种化学键。
活性染料分子中的活性基团与纤维表面的官能团结合,形成离子键。
这种键结合强度较高,不容易受到洗涤、摩擦等外界因素的影响。
但是,离子键只能在纤维表面形成,无法深入到纤维内部,因此染色效果较浅。
最后,共价键是活性染料与纤维材料结合的一种化学键。
在活性染料中,含有与纤维表面官能团相似的活性基团,能够与纤维表面的官能团发生化学反应,形成共价键。
这种键结合非常稳定,不容易受到洗涤、摩擦等外界因素的影响。
共价键的形成使活性染料能够深入到纤维内部,染色效果较为明显。
总之,活性染料的染色原理可以通过物理吸附、离子键和共价键来解释。
不同类型的活性染料具有不同的染色原理,选择适合的活性染料对于实现理想的染色效果是非常重要的。
- 1、下载文档前请自行甄别文档内容的完整性,平台不提供额外的编辑、内容补充、找答案等附加服务。
- 2、"仅部分预览"的文档,不可在线预览部分如存在完整性等问题,可反馈申请退款(可完整预览的文档不适用该条件!)。
- 3、如文档侵犯您的权益,请联系客服反馈,我们会尽快为您处理(人工客服工作时间:9:00-18:30)。
第三节 活性染料染色 活性染料是其离子或分子中含有一个或一个以上的反应性基团(俗称活性基团),在适当条件下,能与纤维素纤维上的羟基、蛋白质及聚酰胺纤维上的氨基等发生键合反应,在染料和纤维之间生成共价键结合的一类染料。 按照染料索引分类,该类染料称为反应性染料,我国称为活性染料 活性染料的分子结构简单,色泽鲜艳,色谱齐全,使用方便,成本较低,含有磺酸基水溶性基团,在水中电离成染料阴离子,对硬水有较高的稳定性,扩散性和匀染性较好 活性染料还会与水发生水解反应,降低染料利用率,残液中染料含量高达30%~40% 活性染料染色时间较长,染料和化学品的耗用量大,需加大量中性盐促染,对环保不利 活性染料的皂洗牢度和摩擦牢度较好,日晒牢度与染料母体结构有关,随染色浓度提高而改善 活性染料耐氯漂牢度较低,蒽醌结构的蓝色品种染料有烟气褪色现象 可用于纤维素纤维、蛋白质纤维、聚酰胺纤维,特殊活性基团的活性染料还可用于涤纶等纤维的染色 一、活性染料的结构和类型 活性染料结构通式W—D—B—Re
Re为反应性基团(活性基),可与纤维反应生成共价结合,影响染料的反应性以及染料和纤维间的共价键的稳定性 B为活性基与母体的连接基或桥基,部分染料无,影响染料的稳定性及染料和纤维间共价键的稳定性 D为染料发色体或母体,影响染料的亲和力、扩散性、颜色和耐晒牢度 W为水溶性基团,一般为磺酸基 二、活性染料和纤维素纤维的反应性 1.纤维素纤维的化学结构和反应性 纤维素是多糖化合物,其分子链主要由β-D-葡萄糖剩基彼此以1,4苷键联结而成 反应性主要取决于分子链中的葡萄糖剩基上的三个羟基的性质 只有无定形区的葡萄糖剩基上的羟基才可能与染料发生反应 染料可及区约占纤维总体积的5%~14%,随前处理和染色时的溶胀状态而不同 不同大小结构的染料分子,可及区有差别 实际参加反应的羟基仅是可及羟基很少一部分,与各羟基的反应性和空间阻碍等因素有关 第2位的反应性最强,但空间阻碍比第6位的大,对体积较大的分子(如染料)反应几率较低 第6位的伯羟基的反应性较强,受空间阻碍影响较小,发生亲核反应的几率较高 第3位的仲羟基受空间影响较大,且易与相邻的葡萄糖剩基形成内氢键,反应性最低 在正常反应条件下,第2位空间阻碍较第6位的大,所以染料主要和第6位的羟基反应 2.活性染料的反应 纤维素和水都可作为亲核试剂与染料发生反应 染料与水反应就失去与纤维的反应能力,反应越快,损伤染料越多,固色率较低 染料与水反应是均相反应,与纤维素反应是非均相反应 水解反应可以发生在溶液中,也可以发生在纤维内孔道中 一般使用水溶性多元醇代替纤维素纤维进行研究 在醇的碱性溶液可发生如下反应 AOH → AO- + H+ 醇的离解 AO- + D → AOD 染料的醇解 OH- + D → HOD 水解产物 醇解相当于和纤维素的反应 三、活性染料的染色过程 与其它染料一样在上染过程中,也存在着吸附、扩散和固着的过 程。 在纤维中扩散的同时,还存在着染料与纤维的键合反应和染料与水的水解反应。 四、影响固色反应速率及效率的因素 1.染料的反应性及反应性比 活性染料的反应性包括与纤维素纤维的反应,也包括水解反应 应该提高染料与纤维的反应速率,降低其水解速率 要保证染料具有一定的反应性,又要有高的固色效率 2. 染料的亲和力或直接性 活性染料母体一般是简单的酸性或直接染料,故具有较低的直接性和良好的扩散性 活性基越大,直接性有一定提高,扩散性能则有所降低 活性染料的亲和力或直接性越高,越有利于染料和纤维的反应,固色效率和固色速率都可提高 竭染常数 直接性过高,没有必要 并且会使染料的扩散性及匀染性降低,水解染料难以去除 3.染料的扩散性 与上染速率、匀染性、透染性、固色效率有关 对于皮芯结构和低温染色的粘胶尤其重要 比一般直接染料高 4.pH值 pH值升高,纤维素电离程度增加,纤维带负电荷也多,对染料阴离子的斥力增大,使其亲和力(或直接性)降低 pH值升高,可提高染料和纤维的反应速率,水解反应速度也迅速增加,固色效率越低 活性染料应在碱性溶液中进行,但碱性不要太强 5.温度 提高温度,染料水解和染料和纤维的反应速率都增高,对水解影响更显著 温度越高,染料的亲和力或直接性越低,染料平衡吸附量降低,竭染常数或固色率越低 6. 电解质 与直接染料促染机理相同 加入元明粉等中性电解质可提高染料的吸附速率、平衡吸附量及纤维上的吸附密度 电解质浓度过高,将增加染料在溶液中发生聚集而生成沉淀的程度,影响固色速率和效率、染色匀染性 7.助剂或添加剂的影响 在轧染或印花时,溶解度较低的染料或染料浓度高时,需加尿素助溶 尿素可加速纤维溶胀,其水溶液比纯水对纤维的溶胀能力强 8.浴比 降低浴比可降低活性染料的直接性,增加纤维上的染料浓度,因而可提高固色速率及固色效率 9.纤维的结构和性质 遵循孔道模型 纤维充分溶胀,空隙尺寸增加,染料扩散速率快,提高染料的固色效率 纤维越细,纤维比表面积越大,固色速率及固色效率越高 五、纤维素纤维纺织品的浸染工艺 活性染料的上染特殊之处:在吸附和扩散的同时发生与纤维的键合反应(固色)及水解反应 染料反应性越强,直接性越高,扩散性越低,匀染和透染性就越差 因此纤维素染色时,应在近中性上染,待达到或接近吸附平衡后再加碱剂(固色剂),提高染液的pH值,加快固色反应 减少染料的水解几率,提高固色率,而且还会获得良好的匀染及透染效果 固色率:染料与纤维发生共价结合的染料量占投入染料总量的百分率 1.染色特征值 S值过高或过低都会使匀染性及透染性变差 S值高的染料,可通过分批加盐、控制染色温度和时间来增加移染 S值小、E值大,不能通过移染达到匀染,须通过分批加碱获得匀染 S值较大,E-S值相对较小: 通过加盐量控制吸附速率 盐控型染料 S值很高,E-S值较小: 染料呈聚集状态,提高温度提高匀染性 温控性染料 S值较低,E-S值较大: 加碱后E值提高较大,称为碱控性染料或自匀性染料 R值表示固色快慢,与匀染性有关 R、F值关系到最终固色效率 大部分染料浸染采用染料和碱剂分两次加入的工艺 近年来全料阶段(All In)染色工艺 2.浸染主要工艺因素 不同反应性基团的染料要求不同的染色及固色温度,反应性强的温度低,反之较高 固色pH值一般以10~11较合适,常用碱剂是碳酸钠,可维持pH值在10.5左右;促进渗透可使用小苏打和纯碱混合碱剂;水玻璃缓冲能力强,但会增加溶液粘度,用量过高影响渗透 活性染料直接性较低,故用量比直接染料高,但要防止过高用量引起染料聚集 浴比主要由染色设备决定。浴比小,染料利用率高,但会影响匀染效果 3.浸染工艺过程 两浴两阶段工艺、一浴两阶段工艺及全料一阶段工艺 两浴两阶段工艺 染料在中性浴中上染,然后在不含染料的碱性固色浴中固色 吸附浴和固色浴可以续缸使用,染料利用率高,固色效率高 用于纱线浸染生产,染料的固色率和给色量比较稳定,不易产生误差 一浴两阶段工艺 大多数纺织品采用 质量容易控制,色差较少 不能续缸生产 全料一阶段工艺 工艺简便 染料水解率较高,染色质量稳定性较差 适于结构较疏松的织物或纱线,或在碱剂碱性较弱的情况下采用 以染浅、中色为主 卷染也属于浸染 适合小批量、多品种的生产,灵活性较强 上染时浴比较小 活性染料的水洗后处理 目的是去除未固着的染料、盐及碱,使染色织物的pH接近中性,是整个染色工艺过程的重要环节 所有活性染料都存在着固着不充分、在纤维上留下大量水解染料的缺点 活性染料的亲和性影响了其易洗涤性,低亲和性可用冷水去除,而高亲和性的染料需要高温洗涤 水洗处理时间一般是染料的上染及固着过程的二倍多,大量的水和热用于水洗后处理 水洗过程:冷水洗、热水洗、皂洗、热水洗、冷水洗等 冷水洗、热水洗(40~50℃),稀释阶段,尽可能去除盐、碱及未固着的染料,提高皂洗效率 皂洗前最好在醋酸浴中进行中和,防止染料在皂洗过程中水解,避免碱剂去除不干净 残留的电解质影响织物耐洗牢度,残碱影响色光 皂洗过程促使纤维内部未固着的水解染料扩散到纤维表面,同时解吸到洗涤液中 提高温度——提高水解染料扩散速率,降低水解染料的亲和性,提高染料的解吸效率 常规使用的皂类洗涤剂及非离子表面活性剂并不能加速水解染料的扩散 皂洗后热水洗(70℃,<10min),进一步去除粘附在纤维上的染料溶液 水洗后处理的染色物耐水色牢度(水渍牢度)良好,耐洗色牢度较差——检查电解质、金属离子、皂洗温度,可进行二次皂洗 耐洗色牢度好、水渍牢度差——提高净洗效果 连续轧染工艺 包括浸轧染液、烘干、汽蒸(高压饱和蒸汽)或焙烘(干热空气或常压高温蒸汽)固色、平洗后处理 可分为一相法和两相法 一相法——染料和碱剂在同一染浴中,烘干后进行后续工序 两相法——浸轧染液和烘干后,浸轧或喷淋含碱剂的固色液,再经过汽蒸或焙烘处理 两相法的染料适用性更广 染料要充分溶解,尽快使用,避免染料水解 在轧染液中可加一定量的弱碱剂,提高固色率 固色液中,食盐或元明粉一般接近饱和浓度,减轻染料在浸轧碱液时发生解吸,减少织物上的染料溶落 加入尿素,帮助染料溶解,汽蒸时提高纤维吸湿性,增加纤维的溶胀度,加速染料扩散,提高固色率 织物浸轧染液、烘干后应立即浸轧固色液,由于不存在碱剂对染料直接性或扩散性的影响,可选碱性强的烧碱做碱剂 固色液碱性强,汽蒸固色时间短,提高生产效率 不同类型的染料,碱剂的种类和用量不同 浸轧方式:一浸一轧、二浸二轧 棉带液率控制在60~70%,粘胶80~90% 温度可适当高一点,保证染料充分溶解 可加适量渗透剂,帮助染液渗透 海藻酸钠糊作防泳移剂,减轻染料烘干时色泳移 防染盐S(弱氧化剂)防止染料在气体时受还原性物质影响,破坏结构,纤维素纤维在碱性条件下汽蒸时有一定的还原性 轧染易发生头尾色差——染料对纤维的亲和力较高,染料发生水解 要选用直接性低的染料 开车时稀释染液 色差产生原因:染液不稳定、染料发生水解 浸轧染液后烘干,先热风或红外线,再烘筒,减少染料泳移 汽蒸(100~102℃饱和饱和蒸汽,1~3min),时间过长,染料水解率提高,固色率提高不明显 上染过程 上染原理与浸染相同:染料必须充分溶解并被纤维吸附扩散后才能和纤维充分反应 浸轧织物上的染料烘干时只有少量对纤维发生吸附、扩散和固着,大部分染料沉积在织物表面纤维的毛细管中。 在用饱和蒸汽汽蒸时,染料从蒸汽中吸收水分后溶解在纤维间的毛细管中,被纤维吸附的同时向纤维内部扩散,并发生固色反应 要加一定助剂(尿素或双氰胺)帮助上染及固着 可采用轧-蒸工艺,省略中间烘干,不存在泳移现象,适用于毛巾布、天鹅绒等 轧卷堆染色工艺 浆织物浸轧染液(染料、碱剂、助剂)后于一定温度打卷堆置,缓慢转动,使染料完成均匀吸附、扩散和固色反应,然后经水洗等加工的染色方法 具有设备简单、浴比小、能源消耗小,匀染性和重现性好,固色率较高,适用染料品种多,排放污水少,加工成本低 适合加工小批量、多品种的产品 最常用的是室温下卷堆工艺——冷轧堆工艺 冷轧堆染色浴比小,上染和固色温度低,染料扩散慢,固色和水解速率慢,上染和固色