介绍几个常用的刀具监测参数-三线
一些常用刀具使用参数的参考值

1100--1200
300--350
φ8R4
1200-1300
300--350
φ6R3
1300--1500
300-350
φ5R2.5
1500-1700
150--200
φ4R2
1700--1800
150--200
φ3R1.5
1800--1900
100--150
φ2R1
2000
100
常用开粗硬质合金刀(镶刀片类)
品牌
型号
推荐切深h(mm)
推荐转速rpm
推荐进给mm/min
SECO、三菱
φ32R6
0.7—0.8
1200
800---1200
SECO、三菱
φ30R5
0.5—0.7
1250
8பைடு நூலகம்0---1200
SECO、三菱
φ16R0.8
0.3---0.5
1800-2000
750---1200
常用精加工硬质合金刀
品牌
1.普通平底白钢刀
所用刀具为普通白刚刀时,每一刀在深度方向的切深h推荐值:h=φ/4~φ/5,例如,一把φ16的白刚平底铣刀,它的每刀切深推荐值约为3—4mm之间。
其它参数如下:
刀具直径(mm)
转速(rpm)
进给(mm/min)
φ25
230--250
75--100
φ16
350---400
75--100
5180019001001502r12000100常用开粗硬质合金刀镶刀片类品牌型号推荐切深hmm推荐转速rpm推荐进给mmminseco三菱32r6070812008001200seco三菱30r5050712508001200seco三菱16r0
常用刀具的切削参数

常用刀具的切削参数1.钻头:钻头是一种旋转式刀具,通常用于在硬材料上钻孔。
切削速度是指钻头每分钟旋转圈数,一般以转/分钟(RPM)为单位。
切削速度的选择将受到材料类型和钻头直径的影响。
对于大型孔径和脆性材料,较低的切削速度可能更合适。
进给量是指每转刀具在轴向(沿钻孔方向)上移动的距离。
进给量的选择将受到钻头直径和材料类型的影响。
较大直径的钻头可能需要较大的进给量。
切削深度是指钻头在一次进给中的轴向深度。
如果切削深度太大,可能会导致钻头断裂或切削不洁净。
切削深度的选择还将受到材料类型和钻头直径的影响。
2.铣刀:铣刀是一种回转和前进运动刀具,常用于平面加工、开槽和切割。
切削速度是指铣刀每分钟旋转圈数,同样以转/分钟(RPM)为单位。
切削速度的选择将受到材料类型、铣刀材料和刀具直径的影响。
进给量是指铣刀在工件表面上移动的距离。
较大的进给量将导致更高的切削速度,但也可能影响切削表面的质量。
切削深度是指铣刀在一次运动中与工件表面的最大距离。
切削深度的选择将受到材料类型和铣刀直径的影响。
3.车刀:车刀是一种在工件上进行旋转切削的刀具,常用于车削和车削加工。
切削速度是指车刀每分钟旋转圈数,仍然以转/分钟(RPM)为单位。
切削速度的选择将受到材料类型、车刀材料和刀具直径的影响。
进给量是指车刀在工件上移动的距离。
较大的进给量可以提高生产效率,但也可能影响切削表面的质量。
切削深度是指车刀与工件表面的最大距离。
切削深度的选择将受到材料类型和车刀直径的影响。
4.锯片:锯片是一种用于切割材料的刀具,常用于金属、木材和塑料加工。
切削速度是指锯片每分钟旋转圈数,仍然以转/分钟(RPM)为单位。
切削速度的选择将受到材料类型、锯片材料和刀具直径的影响。
进给量是指锯片在工件上移动的距离。
较大的进给量可以提高切割速度,但也可能导致切割表面质量的下降。
切削深度是指锯片与工件表面的最大距离。
切削深度的选择通常由锯片的直径和材料类型确定。
刀检测标准

刀检测标准一、外观检测1.刀的外观应无明显瑕疵、毛刺、划痕等表面缺陷。
2.刀的刀身应平直,无明显弯曲或扭曲。
3.刀柄部分应牢固、不易松动,符合人体工程学设计,握感舒适。
4.刀的装配应符合设计要求,各部件配合良好,无明显松动和错位。
二、力学性能检测1.刀的硬度应符合相关标准要求,通常采用洛氏硬度计进行检测。
2.刀的抗冲击性能应良好,能够承受一定的冲击力而不发生变形或断裂。
3.刀的抗疲劳性能应良好,能够在多次使用后保持原有的锋利度和耐久性。
4.刀的强度和韧性应满足使用要求,能够承受一定的载荷而不发生断裂。
三、耐腐蚀性能检测1.刀的耐腐蚀性能应良好,能够抵抗常见的化学物质腐蚀。
2.在一定湿度和温度环境下,刀的耐腐蚀性能应保持稳定。
3.刀表面应采用防锈涂层等措施,以增强防腐蚀能力。
四、刀锋利度检测1.刀的锋利度应符合使用要求,能够轻松切割各种材料。
2.采用专业仪器对刀的锋利度进行检测,如测量切割阻力、切割速度等指标。
3.在使用过程中,刀的锋利度应保持稳定,经过多次使用后仍能保持原有的锋利度。
五、平衡性检测1.刀在使用时应具有良好的平衡性,不会产生明显的偏重或摇晃。
2.采用专业仪器对刀的平衡性进行检测,如测量重心位置、转动惯量等指标。
3.刀的平衡性对使用体验有很大影响,好的平衡性能提高使用效率和安全性。
六、安全性检测1.刀的设计应符合人体工程学原理,避免在使用过程中出现过度用力或操作不当的情况。
2.刀的材料和工艺应安全可靠,无毒无害,符合相关法规要求。
3.在使用过程中,刀不应产生明显的振动、噪音等问题,影响使用体验和安全性。
4.刀的装配和拆卸应方便快捷,不会对使用者造成伤害。
5.对于带有自锁装置的刀,应进行安全性能测试,确保在正常使用时不会发生意外自锁。
6.在包装或运输过程中,刀不应突出或暴露在外,以免误伤他人或自己。
7.在产品说明书中应对安全使用注意事项进行详细说明,以保障使用者的人身安全。
合理选择刀具几何参数

低碳钢 8°~10° 10°~12°
中碳钢 5°~7° 6°~8°
淬火钢 8°~10°
不锈钢 6°~8° 8°~10°
灰铸铁 4°~6° 6°~8°
铝及铝合金 8°~10° 10°~12°
跳到 P130
12
二、后角 o 和后刀面的选择
2.后刀面型式
后刀面的型式有双重后刀面、消振棱和刃带3种,如图所示。
9
二、后角 o 和后刀面的选择
机械制造基础
1.后角 o 的功用及选择
(1)后角 o 的功用
后角 o 可以减小后刀面与工件之间的摩擦,减少刀具磨损。但后角 o 过大会降低切削刃的强度和
散热能力,从而降低刀具寿命。
(2)后角 o 的选择 后角o 的选择应首先考虑切削厚度 hD,其次考虑工件材料和加工条件。
机械制造基础
刀具几何参数对切削变形、切削力、切削温度、刀具 磨损和已加工表面等都有很大的影响。因此,合理地选择 刀具几何参数,能够充分发挥刀具的切削性能,提高生产 率。
刀具几何参数的合理选择主要包括前角 o 和前刀面、 后角o 和后刀面、主偏角 r 、副偏角 r 、过渡刃、刃 倾角 s 的选择。
减小刀具的径向磨损值NB值,如图所示。
11
二、后角 o 和后刀面的选择
提示
在规定了后刀面磨钝标准VB的情况下,后角较大的刀具达到磨钝标 准时,磨去金属的体积较大,如图所示,从而加大刀具的径向磨损值 NB, 这会影响工件的尺寸精度。
机械制造基础
硬质合金车刀合理后角的参考值如表所示。
工件材料 粗车 精车
塑性大时,后刀面磨损严重,应选取较大的后角 o;工件材料脆性较大时,载荷集中在切削刃处,为提高 切削刃强度,应选取较小的后角 o 。
刀具参数的知识点总结

刀具参数的知识点总结刀具参数的种类繁多,下面将对其中的一些常见参数进行详细介绍。
1. 刀具硬度刀具硬度是刀具参数中最基本的性能指标之一。
它指的是刀具表面的硬度,通常采用洛氏硬度(HRC)来表示。
刀具硬度的高低直接影响到刀具的耐磨性和刀具的寿命。
一般来说,在加工硬度高的材料时,需要选择硬度较高的刀具,而在加工硬度低的材料时,可以选择硬度适中的刀具。
2. 刀具韧性刀具韧性是刀具参数中另一个非常重要的指标。
它指的是刀具在受到冲击或振动时的抗击破性能。
刀具的韧性越好,其抗冲击能力就越强,这对于一些高速加工或者重切削的场合尤为重要。
3. 刀具刚度刀具刚度指的是刀具在切削过程中的抗变形能力。
刀具刚度越大,刀具的抗挠度也就越大,可以有效防止刀具在加工过程中出现挠曲或者变形,从而保证加工的精度。
4. 刀具的刃角刀具的刃角是刀具参数中最为直观的指标之一。
不同的切削条件需要选择不同的刃角,比如斜角刀适合高速切削,前角大的刀适合粗磨大扫后角小的刀适用于精益磨。
5. 刀尖圆弧半径刀尖圆弧半径是指刀具刀尖部分的圆弧半径,它的大小直接影响到切削力和切削效果。
通常来说,刀尖圆弧半径越小,刀具的切削力就越小,切削效果就越好。
6. 刀具的刚性刀具的刚性指的是刀具在切削过程中的抗扭转能力。
刚性越大,刀具在加工过程中的形变就越小,切削的精度和表面质量就越高。
7. 刀具的涂层刀具的涂层是刀具参数中的另一个重要指标。
合适的涂层可以有效提高刀具的耐磨性、抗腐蚀性和导热性能,从而提高刀具的使用寿命和加工效率。
总的来说,正确的掌握和应用刀具参数,能够有效提高刀具的加工性能、延长刀具的使用寿命、降低加工成本、提高产品质量,这对于提高加工效率和降低生产成本具有重要意义。
因此,加工人员在选择刀具时,应该根据具体的加工要求,合理选择刀具参数,以达到最佳的加工效果。
刀具状态检测方法
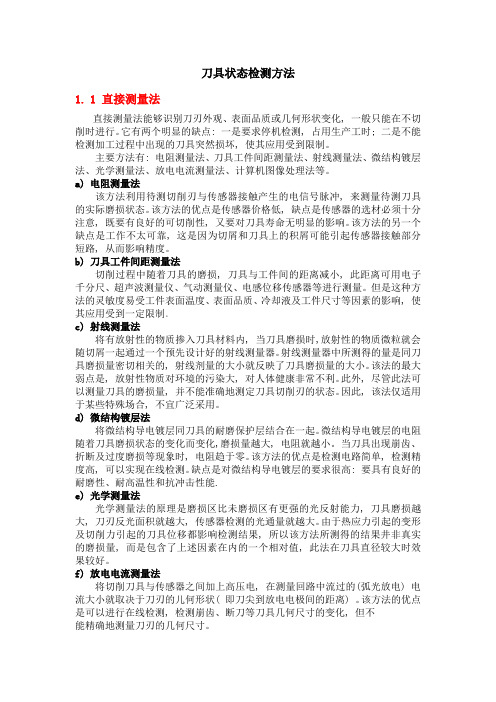
刀具状态检测方法1.1直接测量法直接测量法能够识别刀刃外观、表面品质或几何形状变化, 一般只能在不切削时进行。
它有两个明显的缺点: 一是要求停机检测, 占用生产工时; 二是不能检测加工过程中出现的刀具突然损坏, 使其应用受到限制。
主要方法有: 电阻测量法、刀具工件间距测量法、射线测量法、微结构镀层法、光学测量法、放电电流测量法、计算机图像处理法等。
a)电阻测量法该方法利用待测切削刃与传感器接触产生的电信号脉冲, 来测量待测刀具的实际磨损状态。
该方法的优点是传感器价格低, 缺点是传感器的选材必须十分注意, 既要有良好的可切削性, 又要对刀具寿命无明显的影响。
该方法的另一个缺点是工作不太可靠, 这是因为切屑和刀具上的积屑可能引起传感器接触部分短路, 从而影响精度。
b) 刀具工件间距测量法切削过程中随着刀具的磨损, 刀具与工件间的距离减小, 此距离可用电子千分尺、超声波测量仪、气动测量仪、电感位移传感器等进行测量。
但是这种方法的灵敏度易受工件表面温度、表面品质、冷却液及工件尺寸等因素的影响, 使其应用受到一定限制。
c) 射线测量法将有放射性的物质掺入刀具材料内, 当刀具磨损时,放射性的物质微粒就会随切屑一起通过一个预先设计好的射线测量器。
射线测量器中所测得的量是同刀具磨损量密切相关的, 射线剂量的大小就反映了刀具磨损量的大小。
该法的最大弱点是, 放射性物质对环境的污染大, 对人体健康非常不利。
此外, 尽管此法可以测量刀具的磨损量, 并不能准确地测定刀具切削刃的状态。
因此, 该法仅适用于某些特殊场合, 不宜广泛采用。
d) 微结构镀层法将微结构导电镀层同刀具的耐磨保护层结合在一起。
微结构导电镀层的电阻随着刀具磨损状态的变化而变化,磨损量越大, 电阻就越小。
当刀具出现崩齿、折断及过度磨损等现象时, 电阻趋于零。
该方法的优点是检测电路简单, 检测精度高, 可以实现在线检测。
缺点是对微结构导电镀层的要求很高: 要具有良好的耐磨性、耐高温性和抗冲击性能.e) 光学测量法光学测量法的原理是磨损区比未磨损区有更强的光反射能力, 刀具磨损越大, 刀刃反光面积就越大, 传感器检测的光通量就越大。
刀具(厨刀小刀)刃角测量

刀具刃角测量
一把好用的刀必需锋利持久耐用,这取决要有好的钢材和处理工艺,刃角是影响锋利度的重要因素。
刃角越小,刃部越尖,切入阻力也越小,锋利度也越高。
一,刀具常规开刃角度(以下指是双边角度,单边除2) 34度:一般是西式刀厨刀或菜刀的角度,国际标准(ISO8442)不超40度, 日系刀大多在30度左右。
40度:可提供一相当锐利的刃面,一般用作随身小刀。
50度:兼具刀刃锐利及持续性的开刃角度。
一般野外用刀多为此角度。
60度:刺刀或野外用刀使用,不易变钝,易于研磨是其优点。
二,生产工厂如何控制刃角。
老式的砂轮机定好角度开出的刃肯定能达到标准,但这种方法锋利度谁用谁知道在此就不多说了。
当前最普及的是湿式开刃法,采取湿式方法开刃是保证刃口不发生相变的工艺保证。
但好坏取决开刃工人的水平,开刃角度难以标准 ,一批产品出现30-50度大幅偏差也是常态。
解决这个问题必需加强品控,配备专业的测量工具是刀具生产工厂提升品质必不可少的利器。
三,如何选择刃角测量仪
随着国内刀具厂家慢慢地从以前的普通产品走向高端产品。
然而重要性作用的刃角测量方面存在瓶颈, LH公司刃角测量仪可以满足工厂的检测需要提高产品质量。
LH产品设计上除了精准外还考虑实用,耐用和完美的外观。
用现在流行的来说就是:
高端大气上档次,实用耐用更给力!
六合科技阳江总代理 QQ 3576153415。
刀具及切削参数选择
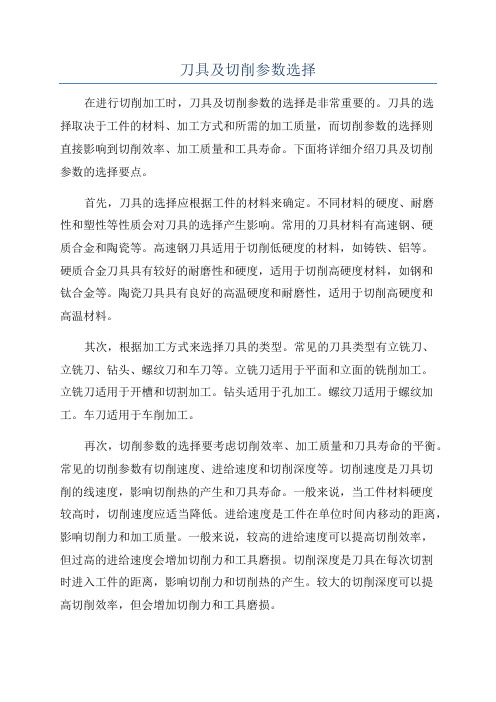
刀具及切削参数选择在进行切削加工时,刀具及切削参数的选择是非常重要的。
刀具的选择取决于工件的材料、加工方式和所需的加工质量,而切削参数的选择则直接影响到切削效率、加工质量和工具寿命。
下面将详细介绍刀具及切削参数的选择要点。
首先,刀具的选择应根据工件的材料来确定。
不同材料的硬度、耐磨性和塑性等性质会对刀具的选择产生影响。
常用的刀具材料有高速钢、硬质合金和陶瓷等。
高速钢刀具适用于切削低硬度的材料,如铸铁、铝等。
硬质合金刀具具有较好的耐磨性和硬度,适用于切削高硬度材料,如钢和钛合金等。
陶瓷刀具具有良好的高温硬度和耐磨性,适用于切削高硬度和高温材料。
其次,根据加工方式来选择刀具的类型。
常见的刀具类型有立铣刀、立铣刀、钻头、螺纹刀和车刀等。
立铣刀适用于平面和立面的铣削加工。
立铣刀适用于开槽和切割加工。
钻头适用于孔加工。
螺纹刀适用于螺纹加工。
车刀适用于车削加工。
再次,切削参数的选择要考虑切削效率、加工质量和刀具寿命的平衡。
常见的切削参数有切削速度、进给速度和切削深度等。
切削速度是刀具切削的线速度,影响切削热的产生和刀具寿命。
一般来说,当工件材料硬度较高时,切削速度应适当降低。
进给速度是工件在单位时间内移动的距离,影响切削力和加工质量。
一般来说,较高的进给速度可以提高切削效率,但过高的进给速度会增加切削力和工具磨损。
切削深度是刀具在每次切割时进入工件的距离,影响切削力和切削热的产生。
较大的切削深度可以提高切削效率,但会增加切削力和工具磨损。
此外,还应考虑冷却润滑剂的选择和使用。
合适的冷却润滑剂可以降低切削热的产生,减小工具磨损,提高加工质量。
综上所述,刀具及切削参数的选择需要考虑工件材料、加工方式和所需加工质量。
合理选择刀具类型和切削参数可以提高切削效率、加工质量和工具寿命。
在实际应用中,还需要根据具体情况进行调整和优化。
- 1、下载文档前请自行甄别文档内容的完整性,平台不提供额外的编辑、内容补充、找答案等附加服务。
- 2、"仅部分预览"的文档,不可在线预览部分如存在完整性等问题,可反馈申请退款(可完整预览的文档不适用该条件!)。
- 3、如文档侵犯您的权益,请联系客服反馈,我们会尽快为您处理(人工客服工作时间:9:00-18:30)。
介绍几个常用的刀具监测参数
刀具监测系统共有26个参数,主参数15个,高级参数11个,下面介绍部分常用参数,
参数T-ECH是样本曲线两个采样点之间的时间间隔。
刀具切削的最大持续时间等于3000个T-ECH 值,在加工监测期间,WattPilote 的扫描周期为5 ms
参数T-ECH 值通常选择尽可能小。
FS :电机额定功率
时间参数P-ABS 设定了功率的安全极限,它对应于刀具切削时允许的最大功率,当切削功率达到该值时,设备立刻停机(信号STP output),Watte Pilote 系统等待故障复位后(信号ACQ input)继续进行监测。
上偏差= 样本曲线x ( 1 + P-SUP/100)
参数P-SUP 用来定义功率的上限值,它是一个样本曲线的百分值
当切削功率达到参数P-SUP设定的值时,设备立刻停机(信号STP output),Watte Pilote 系统
时间
下偏差= 样本曲线x ( 1 - P-INF/100)
参数P-INF 用来定义功率的下限值,它是一个样本曲线的百分值
当切削功率低于参数P-INF设定的值时,设备立刻停机(信号STP output),这意味着设备可能没有安装刀具或没有零件,Watte Pilote 系统等待故障复位后(信号ACQ input)继续进行监测。
如果:参数P-INF =100 意味着没有下限控制。
时间
参数:T-BEG 的作用是屏蔽掉了曲线的起始部分,使得能量和功率的监测仅仅涵盖了零件切削的部分。
时间
参数:T-END的作用是屏蔽掉了曲线的結束部分。
注意:T-END并不能屏蔽掉安全极限P-ABS 的作用。
时间
参数:E-SUP 定义了刀具磨损的最大报警值,当磨损率超过E-SUP时机床报警,同时机床停机,Watte Pilote 系统等待故障复位后(信号ACQ input)继续进行监测。
报警,提请操作者注意,但机床不停机。
参数:P-LER 定义了样本曲线的采样数量,当采样数量大于1时,样本曲线取其P-LER定义值的平均值。
这样可以达到平滑曲线的作用。
T-REG =1 系统强制执行调整模式
参数:P-COR用来消除刀具磨损对功率偏差控制的影响,对于每一个切削循环参照样本曲线,磨损系数对功率曲线进行修正。
参数:P-COR = 0 无磨损修正
P-COR = 1 有磨损修正
主轴电机消耗的功率包含两部分:1)刀具在切削之前消耗的空载功率2)刀具在切削过程中消耗的功率
主轴电机消耗的总功率= 刀具切削功率+ 刀具切削前的空载功率
当刀具磨损时刀具在切削过程中消耗的功率将会增加,而空载功率保持不变,如果不将空载功率分离出来,那么所有基于磨损系数之上的功率曲线调整都将产生错误,(磨损系数是样本曲线与带有磨损刀具切削功率曲线之间的一个比率系数)因此必须将空载功率从总功率中分离出来,参数:P-DYN 的设定是一个最好的解决办法,或者使用空载功率静态偏移参数:P-STA 进行设定。
参数:P-DYN = 0 没有空载功率动态偏移作用,此时仅空载功率静态偏移参数:P-STA起作用P-DYN = 1 空载功率动态偏移在刀具切削的整个循环中起作用
P-DYN = 2作用与P-DYN = 1基本相同,但有一点区别,它是在参数:T-BEG 结束实时起作用。
FS :电机额定功率
没有设定,那么需要用静态参数:P-STA进行设定。
设定参数:P-STA 的值等于空载功率值即可。