浮法玻璃生产工艺40年风雨历程
浮法平板玻璃制造工艺的发展与改进

浮法平板玻璃制造工艺的发展与改进标题:浮法平板玻璃制造工艺的发展与改进摘要:浮法平板玻璃制造工艺是目前全球平板玻璃生产中最常用的技术之一。
本文将介绍浮法平板玻璃制造工艺的发展历程以及主要的改进措施,以提高玻璃质量、生产效率和环境友好性。
1.引言浮法平板玻璃制造工艺作为主要生产平板玻璃的方法,自20世纪50年代问世以来得到了广泛的应用。
通过对工艺的发展和改进,使得平板玻璃在建筑、汽车、电子等领域得到了广泛的应用。
本文将重点介绍浮法平板玻璃制造工艺的发展历程和相关的改进措施。
2.浮法平板玻璃制造工艺的发展2.1 初期发展浮法平板玻璃制造工艺最早于1959年在美国贝尔实验室问世。
这种工艺通过将玻璃原料熔化后,缓慢地倾倒在锡液上,使其均匀浮在上面,并在熔融状态下冷却固化,从而得到均匀平整的玻璃板。
2.2 技术进步随着对浮法平板玻璃制造工艺的深入研究,工艺不断进步。
通过改进熔融炉设计、提高玻璃熔化温度控制的精度以及优化锡液浴等措施,使得玻璃质量得到了显著提升。
此外,还引入了在线涂层、印刷和划痕抗性等新技术,以满足不同领域对玻璃板属性的需求。
3.浮法平板玻璃制造工艺的改进3.1 玻璃质量改进为了提高玻璃的质量,浮法平板玻璃制造工艺进行了多方面的改进。
例如,优化熔融炉和冷却系统,以提高玻璃的均匀性和厚度控制精度。
改进锡液浴和过渡区域加热系统,以减少浮璃上的气泡和其他缺陷。
此外,还利用高效的涂层和印刷技术,提高玻璃的光学性能和抗划伤性能。
3.2 生产效率改进为了提升浮法平板玻璃制造工艺的生产效率,一系列的改进措施被引入。
例如,提高熔融炉的燃烧效率和熔化速度,减少能源消耗和生产周期。
改善玻璃束带自动控制系统,提高玻璃的产量和质量稳定性。
此外,通过自动化技术的应用,减少了工人操作和监控的需求,提高了生产效率。
3.3 环境友好改进在当前环境保护意识不断提高的背景下,浮法平板玻璃制造工艺也在不断改进以降低对环境的影响。
“中国洛阳浮法玻璃工艺"的发展历程
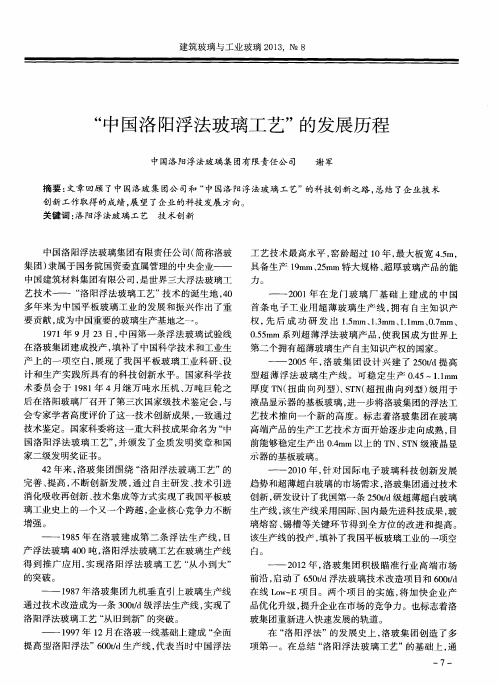
“ 中国洛 阳浮法玻璃工 艺"的发展历程
中国洛 阳浮法玻 璃 集 团有 限责任公 司 谢 军
摘要 : 文章回顾 了中国洛玻集团公司和 “ 中国洛 阳浮法玻璃工艺” 的科技创新之路 , 总结了企业技 术 创 新 工作取 得 的成绩 , 展 望 了企业 的科技 发展 方 向 。
通过技术改造成为一条 3 0 0 t / d 级浮法生产线 , 实现 了 洛 阳浮 法玻璃 工 艺 “ 从 旧到新”的 突破 。
— —
品优化升级 , 提升企业在市场的竞争力。也标志着洛 玻集团重新进入快速发展 的轨道。
在 “ 洛 阳 浮法 ”的发 展 史 上 , 洛玻 集 团创 造 了多 项 第 一 。 在 总结 “ 洛 阳浮 法 玻 璃 工 艺 ”的基 础 上 , 通
的 突破 。
— —
2 0 1 2年 , 洛玻 集 团 积 极 瞄 准 行 业 高 端 市 场
前沿 , 启动了 6 5 0 t / d浮法 玻 璃 技术 改 造项 目和 6 0 0 d d 在线 L o w — E项 目。两 个 项 目的实 施 , 将 加 快 企业 产
后 在洛 阳玻璃 厂 召开 了第 三次 国家 级技 术 鉴定会 , 与 会 专家 学 者高度 评 价 了这 一技术 创 新成 果 , 一致 通过
液晶显示器的基板玻璃 , 进一步将洛玻集团的浮法工 艺技术推 向一个新 的高度。标志着洛玻集团在玻璃 高端产品的生产工艺技术方面开始逐步走向成熟 , 目
关 键词 : 洛 阳 浮法玻璃 工艺 技 术创 新
中国洛阳浮法玻璃集团有 限责任公司( 简称洛玻 集团) 隶属于国务院国资委直属管理的中央企业—— 中 国建 筑 材料 集 团有 限公 司 , 是世 界 三大 浮法 玻璃 工 艺技 术 —— “ 洛 阳浮 法玻 璃 工 艺 ” 技 术 的诞 生 地 , 4 0
1952 年至 1959 年间英国皮尔金顿兄弟有限公司创造了浮法玻璃生产工艺

1952 年至 1959 年间英国皮尔金顿兄弟有限公司创造了浮法玻璃生产工艺, 可以看作是平板玻璃制造中的一次革命.开始时还只打算用它来代替当时流行的成本很高的镜面玻璃制造方法.不久就发现,它完全可以代替全部或绝大部分各种常用的平板玻璃制造方法.浮法是一种新型的工业制造方法,它本身已具有全自动化生产的可能条件.我国也于 1970 年独自研制成功了"洛阳浮法玻璃工艺技术".伴随着我国经济腾飞,浮法玻璃也得到迅猛发展,截止到 2005 年底,我国已建成 140 多条浮法玻璃生产线. 浮法的原理是:冷却到1100℃的玻璃液,从玻璃熔窑冷却部经流液道进入锡槽.锡槽用电加热保持所要求的温度.为了防止锡的表面层氧化,在锡槽空间充满氮气加一定比例氢气的保护气体. 液态玻璃在自身重量的作用下在锡液皨??面铺开. 在表面张力的作用下玻璃层的平衡厚度保持在 6~7 ㎜左右.当要求玻璃带的厚度小于 6 ㎜时,可在玻璃带的两边用拉边机机头将玻璃拉伸.要求厚度大于 7 ㎜时拉边机头则设置成负角度,将玻璃向中部推,从而堆厚.玻璃带离开锡槽后则由过渡辊台提升辊引入退火窑. 当生产厚度小于平衡厚度的玻璃时,玻璃带要受拉伸的作用.与传统的引上法类似,玻璃中存在的化学不均匀或热学不均匀都会显示出特别明显的光学畸变.玻璃板上的厚度差别,表面不平整或玻璃中存在的不均匀物,都会在****光或反射光中出现光学的不正常现象.浮法玻璃的像畸变可分为平行于拉制方向,横向或斜向等类.属于第一类的有不连续线上的变形.它是在拉制方向的线 , 上断断续续出现的形变. 有时也在连续的线上出现或只有一段变形(脊形歪痕, 英文 ridge distortion) 但出现在玻璃带行进的方向上.横向形变是在横跨玻璃带的线上出现变形区.斜向畸变(鲱鱼骨型扭曲变形,英文 herringbone distortion)一般出现在玻璃带的两侧而向倾斜的方向发展. 在玻璃带的上面或下面还可能出现线道(拉引线道,英文ream) .下面有时还出现"冷玻璃线"(粗筋, 英文ripple) . 在保护气体(掺有少量氢的氮气)气氛中,虽然在操作的高温下玻璃是不会与锡发生反应的, 可是如果有少量的氧或硫进入系统中就会形成 SnO 或 SnS,一部分挥发进入锡槽的气氛中或凝结在槽顶,最后聚积成滴落在玻璃带上面使玻璃变形.玻璃上的锡滴坑(英文 drip crater)就是这样形成的缺陷,它与小滴的锡或锡的化合物有关.在显微镜下能分辨出,周围有一道有色的反应环,玻璃表面出现轻微的变形. 浮法玻璃带下方在辊子转动时按转动周期有少量锡的化合物附着在玻璃带上形成印纹,还可能造成微裂纹,称为滚轴印纹(英文 roller imprints)或锡印纹(带裂纹的锡渣斑,英文 dross spots) . 由于浮法操作的化学变化可能既在玻璃带的下方出现开口气泡,又在上方出现表面气泡,玻璃内部带熔液环的气泡也会使玻璃表面轻微变形. 至于玻璃生产中因原料系统和熔化系统造成的玻璃缺陷,如与平拉法和引上法完全共同的缺陷,像澄清气泡,结石,线道等,限于篇幅,则不在本文讨论之列. 应该说,经过多年的摸索和研究,大部分浮法玻璃的特征缺陷都已在很大程度上解决了,但在浮法研制与发展过程中,有些缺陷还顽固地存在,长期困扰着从事浮法玻璃生产和研究设计的人们.我们应该感谢浮法玻璃行业的前辈们,由于他们的不懈努力,积累了大量宝贵的经验,才使我们今天能够在面对浮法缺陷的时候能够有成熟的方法消除它,使浮法玻璃的质量日益提高. 二. 浮法玻璃成形缺陷的外观描述,产生原因与消除方法 1. 锡滴锡滴(英文 drip crater)是指掉落到玻璃带上表面含锡的固态或液态物,通常是 SnS,SnO2 或 Sn,也称为"掉锡点".掉锡点一般很小,粒径约为 0.1~0.5 ㎜,大部分在 0.3 ㎜左右,肉眼很难从运行的玻璃带上发现它.切割之后玻璃板在辊道上输送时,用手触摸会有触感.对静止的玻璃板仔细观察,可发现小黑点.在 50 倍的显微镜下观察,看得非常清晰,呈现出两种形状:一种是亮晶晶的小珠,不打光是小黑珠;另一种是带网格的薄膜,网线发亮.掉锡点虽小,但能使直径约 5~10 ㎜的周围玻璃表面产生严重的光学扭曲,所以又称"光畸变点",使玻璃成品成为废品. 掉锡点的形态因在锡槽内所处的温度环境而不同.900℃温度附近区域落下,形成较圆的珠状体,并嵌入玻璃板中,嵌入深度约为其粒径的三分之一左右,冷却后手指甲抠不掉.低于800℃部位落下, 嵌入玻璃板中较浅,冷却后能用指甲抠去.低于700℃部位落下在玻璃板上成了边缘体,酷似贴膜, 无法抠下来. 产生"掉锡点"要同时具备两个因素,一是锡槽气氛中含有挥发的锡化合物,如氧化锡,硫化亚锡和锡金属的蒸汽等;其二是玻璃带尚未硬化时,其上面空间或锡槽顶盖有低温部位,使含锡及锡化合物的挥发物得以冷凝成液体或固体,然后掉落到玻璃带上表面,从而破坏玻璃的平整度.如果锡液受氧或硫的污染严重,促进锡化合物的大量挥发,再加上锡槽顶盖在高中温区域有许多较冷的砖缝或孔洞(如顶盖支撑砖及组合砖缝,保护气体进气孔,加热元件引出孔,测温元件孔洞等)或水冷却器等,让挥发物得以大量冷凝或沉积,掉锡点就增加.Pilkington 提出了锡槽中氧污染的循环图和硫污染的循环图,并认为由于 SnS 的挥发量比 SnO 大几十倍,所以掉锡点主要是由于硫的污染而产生的. 预防掉锡点生成,首先是杜绝氧,水汽以及硫等进入锡槽.硫的来源可能是玻璃带本身含有的硫化物,或者使用氨分解法制取氢气时因氨中含有硫,所制得的氢气中也含有硫.降低玻璃原料中含硫原料和使用含硫分低的燃料有助于降低玻璃带本身带入锡槽的硫.而采用电解水的方法制取氢气则可以避免保护气体带入硫.硫的另外一个来源还有可能是在过渡辊台安装的二氧化硫装置过于靠近锡槽,导致硫扩散到锡槽内.对于氧的污染,除了玻璃本身是一个可能的污染源之外,更主要的来源是空气漏入锡槽中.其次,改进锡槽顶盖结构,减少甚至消除局部低温冷却部位,也很有效果.对于使用铁—铬—铝电加热元件的锡槽,减少顶盖砖缝,把砖缝上下堵严,甚至热电偶的插入孔也应该上下堵严,就可以消除砖缝的冷凝作用;采用三相硅碳棒作加热元件的锡槽,顶盖是由小砖拼装而成,有很多孔洞缝隙,给掉锡点的冷凝提供了极多机会. 采用高压纯氮气对缝隙进行吹扫可以有效消除掉锡点.方法是采用脉冲振动原理,使存在于锡槽顶盖或内壁上的凝结物受到震动后自动飘落沉降.具体来说就是利用锡槽保护气体,产生脉冲振动来对锡槽进行吹扫.其方法是,在锡槽密封的状态下,瞬间增大或减少氮气的供应量,达到一定时间后将增供或减少的氮气量突然减少或增加,如此反复而产生脉冲振动,对锡槽进行吹扫.该方法对锡槽的吹扫时间短,吹扫效果好,对生产影响时间短,且对环境没有任何污染.另外,对冷却器进行定期清扫也可以起到预防掉锡点生成的作用.采取加大保护气体量,分比例供氢并在高温区将锡槽内污染的保护气体导流排空,将污染物迅速排出锡槽外,也是有效的办法.但其前提是锡槽气密性要好. 国外有报道向锡槽内通入一定浓度的氯气,使锡槽内壁上的锡沉积物在短时间内得以清除.氯气处理的作用方式取决于浓度和处理时间的长短,0.07m3/h 的给气量足以使小的锡沉积物在与气体接触时流到一起并从顶盖滴落下来. 2.钢化彩虹浮法玻璃钢化彩虹(国外称为"起霜",英文 tempering bloom) ,是指浮法玻璃在进行钢化或热弯等热加工时,玻璃下表面(成形时与锡液接触的表面)呈现蓝色的荧光,在显微镜下观察是玻璃表面有微皱纹.它是由玻璃下表面的锡造成的,是一种薄膜干涉现象.所谓薄膜干涉现象,是指从扩散光源发出的光波,在薄膜两表面反射后相互叠加而产生的干涉现象.例如太阳光照在肥皂膜或照在漂浮在水面上的油膜时所观察到的彩色条纹,即是薄膜的干涉.由于微皱纹对光线干涉,反射时呈现蓝色,严重时甚至可使玻璃表面粗糙发毛而不透明.在生产线上有时从退火窑起直到整个冷端长达几百米的玻璃带都呈现此种蓝色虹彩.其原因是锡液受到氧的严重污染后,SnO 渗透到玻璃下表面内,形成一层很薄的薄膜.没有钢化时,由于这层膜太薄,在自然光照射下是观察不到彩虹的. 当玻璃板在氧化气氛中再被加热时,SnO 吸收氧进一步氧化成 SnO2,体积膨胀,使玻璃表面形成皱纹.反应过程如下: 在 540~750℃之间,在中性气氛下,SnO 发生岐化反应,反应较完全: 2SnO=SnO2+Sn 在含氧气氛中: SnO+ O2=SnO2 由于 SnO 吸收了空气中的 O2, 使得局部体积膨胀, 薄膜表面产生了折皱, 膜厚增加, 因而产生干涉, 能观察到彩虹. 所以形成皱纹的条件有三个,其一是表面渗入过量的SnO,其二是在氧化气氛中热加工,第三是热处理温度达到玻璃软化的温度.如果钢化时严格控制温度使之接近软化温度但玻璃表面未软化,也不出现皱纹.有试验表明含 SnO 很少的浮法玻璃,即使加热到软化温度也不出现皱纹.加强锡槽气密性和提高保护气体纯度后,可以保持锡中氧的浓度在一个可以接受的数值.锡的氧化物在玻璃中一般都以非晶态的形式存在. 钢化彩虹的形成及其严重程度与玻璃表面的渗锡量有直接的关系.研究表明,浮法玻璃下表面锡的扩散深度可达 12~36m.随深度增加,渗锡量逐渐变小.我国现阶段浮法玻璃下表面的渗锡量大约为 60~95g/㎝ 2,高质量的合资生产线玻璃下表面渗锡量仅为 5~6g/㎝ 2.相应地,钢化彩虹出现的程度要比国内轻微或者根本没有. 要避免玻璃出现热加工彩虹,首先要保证保护气体的供应纯度以及加强锡槽密封,先做到锡槽出口段液面没有SnO2 浮渣. 另外国外有专利报道用石墨或无定形的碳与锡液和保护气体接触能使保护气体保持还原状态,从而最大限度减少锡液上锡的氧化物含量,可以防止锡被氧化及恢复保护气体的保护性能,因为碳可以先于锡液被氧化,成为一氧化碳,从而不会形成 SnO,也就使与锡液接触的玻璃表面不呈现虹彩. 3.沾锡沾锡(英文tin pick-up) ,浮法玻璃下表面附着肉眼可见的金属锡,小的直径不足 1㎜,大的可成线状,片状甚至带状.它们与玻璃附着的界面呈现银白色金属光泽,像镜子一样,严重时每平方米玻璃表面锡可以以克计.虽然这些锡可以剥去,但玻璃表面往往残留有轻微痕迹,而且不胜其烦.沾锡的玻璃属于废品. 沾锡的机理目前尚不清楚.从原理上说,金属和玻璃在结构键上不同,二者是互不浸润的.对易于极化的金属,必须在二者的接触界面处有过渡层,即向玻璃一侧的金属原子呈现非金属行为而与玻璃粘附,向金属一侧的金属原子仍呈金属行为,而与金属结合,使金属得以附着在玻璃表面. 浮法玻璃在成形过程中所渗入下表面的 SnO,即引起钢化彩虹的 SnO,应不是导致沾锡的过渡层. 因为所有的浮法玻璃下表面内都含有 SnO,但不是所有下表面都沾有锡.实践证实,沾锡是在锡槽出口处才发生的,工厂解决沾锡的办法也是增加玻璃带抬起处的保护气体量,以及掏尽 SnO2 浮渣. 导致沾锡的过渡层应是当玻璃带脱离锡液面的瞬间,有空气进入,与刚刚暴露出的而且不停轻微波动的锡液面接触,而将其氧化,形成沾锡的过渡层,在与玻璃下表面接触时,引起锡的附着,所以沾锡现象严重时,外表往往可以呈现锡液波动的形状. 沾锡严重时的碎玻璃不要再回收,以免再熔化时产生"锡石结石"(cassiteritestones)缺陷. 防止沾锡的办法是清除出口处玻璃带下的 SnO2 浮渣或其他漂浮物, 这些漂浮物可能来自于锡槽的前端,被运行的玻璃带带到了此处,或者就是在此处形成的.让该处被保护气体充满,并增加保护气体量,不让空气漏入.锡槽出口温度不要过高,保持在 595~605℃范围之内.适当降低玻璃板宽, 提升拉引速度.加强出口部位的密封,检查此处挡帘,边封及石墨擦锡装置运行是否正常.当然也还要提高锡液面,尽量减少和消除玻璃带下表面与锡液面所形成的三角空间. 4.成形气泡气泡(英文 bubble)是指玻璃中的可见气体夹杂物,它不仅影响玻璃的外观质量,更重要的是影响玻璃的透明性和机械强度,是一种极易引起人们注意的玻璃缺陷.气泡产生的原因很多,情况复杂. 与熔化有关的一次气泡,再生气泡(重沸气泡) ,外界空气气泡,耐火材料气泡及金属铁引起的气泡等等不在本文讨论之列.这里仅对浮法玻璃在成形过程中出现的气泡缺陷加以讨论. 与成形有关的气泡可分为上表面泡和下表面泡. 上表面泡一般较小,直径不超过 0.1 ㎜,且位于玻璃表面内,主要来自于流道部位.其形成原因第一种可能是保护气体中的氢在从调节闸板处的空隙溢出时在玻璃表面燃烧,生成直径约为 0.05 ㎜小气泡,通常出现在玻璃边部.加强调节闸板附近的密封和减少锡槽入口端的保护气体氢气含量有助于改善和消除该种气泡.第二种可能是新更换调节闸板后,闸板气孔内的气体溢出.刚出现时气泡体积较大,运行一段时间以后逐渐减小至直径 0.1 ㎜,24 小时之后可消失.更换调节闸板前如果对新闸板进行预热则可以避免该气泡产生. 第三种可能是调节闸板与玻璃液反应产生, 气泡直径约为 0.05 ㎜,整个玻璃板都可以出现.降低流道温度,增加锡槽前端保护气体量并降低氢含率可以使该种气泡缺陷情况得到改善. 下表面气泡(即通常所说的板下泡) ,分为两类:即小的板下泡和大的板下泡. 小的板下泡一般都来自于流道或者锡槽的前端部位.开口的板下小气泡有可能是流道耐火材料接缝空隙中的气体在流道玻璃液温度波动时被排出,或是流道处有污染物.通过加强流道部位保温或是升高该部位的温度可以消除这一缺陷.另外一种产生板下小泡的原因是背衬砖区域温度太低或运作不正常,玻璃在此处停止不流动.当唇砖有裂纹时被玻璃液侵蚀也会出现该种气泡.这种气泡为下开口泡,通常成群呈线状,气泡直径与深度之比在3∶1~4∶1 之间.调整背衬砖和定边砖使其安装正常,玻璃能够从中部向边部流动,同时提升流道温度,调整调节闸板水平及位置,检查唇砖,必要时更换唇砖.如果是背衬砖或者定边砖发生移位,也会出现小气泡.气泡分布在距玻璃板下表面三分之一厚度的地方,通常出现在玻璃带的一侧,严重时可以达到一半玻璃带的宽度.很显然通过调整背衬砖或定边砖的安装位置,不让玻璃在此处受阻,就可以消除这种气泡.当唇砖材质不好被玻璃侵蚀较快时会出现板下小的闭口泡,呈线状或是带状分布在玻璃带的中部.降低流道温度或者更换唇砖后会得到改善及消除.玻璃液从唇砖流到锡液面上时如果温度过高,或者唇砖的位置设置 ."抛光泡"为板下闭口小气泡,呈抛物线形分不对,会产生所谓的"抛光泡"(英文:lapping bubble ) 布在玻璃带上,且重复出现.此抛物线形分布的气泡宽度小于 1m,有时也会出现在玻璃板的整个宽度,极个别情况时会是开口气泡.降低流道温度,降低唇砖与锡液面的距离(即减小玻璃液的落差) 可以消除"抛光泡".锡槽在施工过程中如果不小心将电焊渣等落入砖缝,或是槽底钢板或槽底螺栓受到锡液侵蚀,以及锡液内的其他污染物等也会造成板下泡,称为"污染泡"(contamination bubble) . 发生在锡槽热端的"污染泡"其直径与深度之比为3∶1~4∶1,而在冷端发生则为20∶1.不言而喻, 这种泡难以定位,消除也很困难,所以应特别注意避免"污染泡"出现. 大的板下泡通常为开口泡,直径大于 10 ㎜,被称为"牛眼泡".如果是由于锡槽槽底砖砖缝内的气体逸出所导致的,发生在锡槽热端时其直径与深度之比为3∶1~4∶1,而在冷端发生则为20∶1.槽底钢板得到正常而均匀的冷却可以确保不出现"牛眼泡".为了控制锡液对流而设计的石墨挡坎,如果设置的过于接近热端,也会冒"牛眼泡",气泡位置固定,规律性强,拆除后可消失.大的板下开口泡的另外一种可能来源是由于锡液中溶解的氢气的逸出, 为直径大于 10 ㎜开口泡, 即"氢泡",在锡槽的热端发生.通常出现在锡槽热端有较多的冷却器时,此处锡液温差较大.降低保护气体中氢气比例,移走热端的冷却器可消除"氢泡".还有一种"水泡",是指锡槽槽底耐火材料中的水分在锡槽烘烤时未能充分排除,生产过程中如遇温度波动,会有水蒸气排出,产生大的板下泡,其特征与"牛眼泡"类似.我国在浮法玻璃发展早期使用耐火混凝土现浇锡槽槽底耐火材料结构时曾有长期出现"水泡"的经历,严重影响了成品率和玻璃产率.现在在使用烧结锡槽底砖之后已不多见. 5.雾点雾点(hot end dust)是浮法玻璃下表面的开口微气泡,直径只有几微米,数量多时每平方厘米可达几十万个.肉眼观察隐约可见在玻璃表面上有一层薄雾.程度轻者仅在强光黑背景中可看出,严重时可使玻璃表面粗糙,玻璃本身好像磨砂毛玻璃而不透明. 形成雾点的原因是由于浮法生产条件急剧变化,锡液中原来溶解的气体(如氢气等) ,在平衡条件破坏后达到过饱和而释放出来,被夹持到玻璃液和锡液面之间,如果此处玻璃带温度仍较高,即软化状态,气体在玻璃下表面留下痕迹,就形成较小的开口气泡,即"雾点".雾点的特征,同时也是与板下小气泡的区别是直径更小,只有几微米,肉眼看不出来,此外数量巨大,每平方厘米可达几十万个. 保护气体量过小,纯度不达标,补充加锡,高温区锡液温度急剧下降,例如往锡液中插水管等生产工艺参数不正常也可能产生雾点. 5.划伤与辊印划伤(scratch)是指玻璃表面的机械擦伤,在玻璃的上下表面都可能发生. 上表面划伤多为过渡辊台挡帘高度太低接触到玻璃板,或是挡帘下端积聚的 SnO,Sn 与玻璃接触所引起.外观一般为细小且连续的线状擦伤. 下表面划伤为连续性擦伤.锡槽出口唇砖部位有碎玻璃或耐火材料碎块,氧化锡浮渣太多,出口唇砖损坏,当出口玻璃板温度太高,以至于擦在上面时便出现擦伤.要使这种状况得到改善,首先应清扫锡槽出口唇砖,加大锡液深度,降低出口玻璃板温度,或调整过渡辊水平高度. 由辊子(包括过渡辊和退火窑辊)带来的缺陷即辊印(英文 roller imprints) ,主要是玻璃与辊子接触受压产生.如果辊子表面有凹凸不平,自然会将玻璃板压出刻痕.锡,锡的氧化物及其他浮渣,碎玻璃屑等如果被玻璃带带到辊子上,则会给玻璃造成印痕,划痕或锡渣斑.要避免这种缺陷,首先要避免浮渣的生成,做好锡槽密封,尤其是锡槽出口部位的密封,在"引头子"时提高保护气体的氢气含量到 10%,尽可能使锡槽内没有氧的污染.在锡槽出口部位使用"扒渣机"(一种特殊用途的直线电机) ,经常清除锡槽出口浮渣,并使锡槽出口温度尽量较低.其次调整过渡辊及退火窑辊子的高度,使玻璃拉出锡槽时平均分布于辊子上,更换损坏,受污染或变形,偏心的辊子.再就是在过渡辊台或退火窑的前部玻璃底下施加 SO2.不过,施加 SO2 虽然可以暂时解决问题,但是 SO2 易侵蚀棍子表面,并在棍子上产生沉积物,可能造成长期的问题.另外,如果施加 SO2 的部位过于靠前接近锡槽,有可能造成锡槽内出现严重的状滴落物等等. 波筋是指与拉引方向基本平行的波筋,是一种玻璃不平整缺陷.它可以由原料成分波动,配合料混合不均匀,运输投料过程中的分料以及熔化过程产生的分料等,引起玻璃液本身的组成不均匀,会在浮法玻璃上出现波筋,降低成品外观质量.成形过程中出现的波筋,也是因为玻璃液温度不均匀, 特别是在流道口及其上游附近因强制冷却造成温度不均匀形成的.流道部位耐火材料的损坏,例如调节闸板有缺口,唇砖有裂缝,侵蚀不均匀等也会形成波筋.拉边机参数设置不合理,局部温差太大等都会有波筋出现. 小波纹是一种成形不完善的缺陷,很短,有周期性,在玻璃带上分布也有规律.小波纹与玻璃液在背衬砖与定边砖处的液流轨迹密切相关.生产中锡槽高温区玻璃液或锡液温度太低,玻璃板上就会出现小波纹. 用平行光以一定角度照射玻璃板, 在背景上可以看到有规则波纹的阴影, 波长约 2.5 ㎝, 起伏约 5~10m.理论计算表明,1050℃的玻璃液在锡槽抛光区的摊平时间至少为 72 秒钟,所以设计时适当延长锡槽高温区,防止玻璃液或锡液降温过快对玻璃平整化和消除小波纹有利.锡槽低温区的冷锡液回流,影响高温区抛光,也会出现小波纹. 厚薄差大是指生产不同厚度玻璃时,其边部与中部厚度不一致,相差太大.它是因锡槽内锡液的横向温差所引起.加强锡槽边部的保温,打开边部电加热补充热损失对改善厚薄差大有帮助.为防止玻璃边部过冷,必要时可以对拉边机,冷却器等进行局部保温,防止带走过多的热量.使用直线电机控制锡液流动可以降低锡液横向温差,从而改变厚薄差大的情况. 玻璃带热弯曲,是指玻璃带有较大面积的弯曲,在生产线上观察玻璃带上表面的厂房或墙壁上直线物体的影像,往往有周期性波浪起伏的特点.锡槽出口处玻璃带温度太高,未硬化而爬坡易产生这种缺陷. 析晶通常发生在玻璃带中央,由背衬砖系统作用不正常产生,发生前往往伴随着背衬砖小气泡出现. 调整背衬砖及定边砖位置,并检查流道热电偶位置是否正确,排除这一缺陷. 固体夹杂物多为高温区锡槽槽底砖"霞石化"后疏松剥落,上浮而沾到玻璃下表面所产生.随着锡槽槽底砖制造技术的不断进步,"霞石化"的情况已大大改观,此种缺陷现在已不多见.另外,锡槽内的固体氧化物杂质及其它固体杂质也可引起固体夹杂物缺陷. 顶盖玻璃状滴落物不是顶盖耐火材料中加入了磷酸盐结合剂,造成顶盖表面及硅碳棒电加热元件上凝聚了大量的玻璃状的物质, 当其积聚到一定程度,便掉落到玻璃带上,造成缺陷.这些玻璃状滴落物是含有锡的氧化物杂质的磷酸盐玻璃.锡槽耐火材料,特别是顶盖耐火材料中要避免使用含有磷酸盐的添加剂.。
洛阳浮法玻璃工艺诞生40周年座谈会召开

在 产业 生 产 规 模 、 种 质 量 、 构 调 整 、 术 装 备 水 品 结 技 平 、 能减排 、 济社会 效 益 、 节 经 对外 开 放 等诸 多方 面 取 得 的成 就 , 将 “ 阳 浮法 玻 璃 工 艺 ” 0年 的 发 展 进 并 洛 4
一
线 6 0吨技 改工 程 竣工 ,并 于 2 0 年批 量 生产 出 0 01
通过重组 联合组 建玻璃 大集 团 ; 通过政 府进 一步 明确
会 议 决定 下 次 会议 由江 苏 华尔 润集 团公 司择期
召开 。
支持 鼓励 发展 的大型 企业 名单 目录 , 管齐 下 , 本 多 标
兼治 , 促进 玻 璃工 业科 学发 展 , 真正 实现 中国玻 璃 工
业“ 由大变 强 、 靠新 出强 ” 的发展战 略 。希 望 中国建 材 集 团能在遏 制平板玻 璃重复 建设 、 建玻 璃行 业大 企 组 业集 团等方 面做 出新 的应有 的贡献 。
究 中获 得更大 突破 。
式命 名为 “ 阳浮 法玻 璃 工艺 ” 同年 1 洛 。 0月 ,洛 阳浮 “ 法玻璃 工 艺 ” 国家发 明二等 奖 , 为新 中 国成 立 后 , 获 成 继 万 吨轮 、 吨水 压机 后 的第 三个 获 国家 发 明奖 的重 万
大项 目, 奖单 位包 括 : 阳玻 璃厂 、 皇 岛玻璃 研 究 获 洛 秦
建 筑 的 发 展 为 契 机 , 控 总 量 , 力 缩 小 与 国 际 先 进 调 努
21 0 华 东地 区 第九 次 市 场 研讨 会 会 议纪 要 1年
21 0 1年 l 0月 9 日 由 中 国 玻 璃 控 股 有 限 公 司 市
水 平 的差 距 , 实现 由大变强 , 中国玻 璃工 业建 设 成 将
浮法玻璃技术
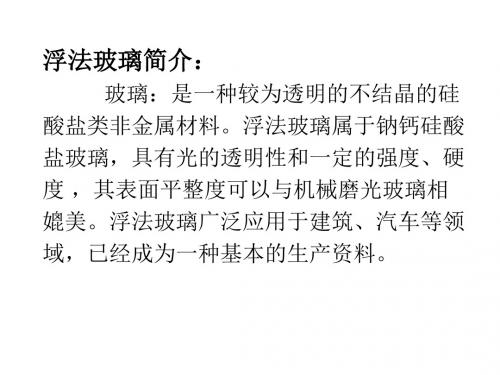
6、光学性能
公称厚度/mm 2 可见光透射比最小值/% 89
3
4
88
87
5 6
8
86 85
83
10
12 15 19 22 25
81
79 76 72 69 67
本体着色平板玻璃透射比偏差
种类 可见光(380nm-780nm)透射比 太阳光(300nm-2500nm)直接 透射比 太阳能(300nm-2500nm)总透 射比 偏差/% 2.0 3.0 4.0
优等品:优等品的平板玻璃主要用于镀银玻 璃镜、镀铝玻璃镜、离线镀膜玻璃的原片。 这些产品主要用在室内装饰和高档建筑门 窗,用低辐射镀膜(LOW-E)玻璃还可制 作节能性能优越的中空玻璃。 超薄平板玻璃(0.55 mm—2mm)主要用于电 子信息行业,如ITO导电膜玻璃、精密仪 器、仪表、液晶显示器、光伏玻璃、电子 触摸屏等方面。
我国浮法玻璃状况
我国从上世纪80年代初开始,建了一 大批浮法玻璃生产线,1985年原国家建材 局又明确指出,我国今后建设日熔化300 吨以上的玻璃生产线,必须采用浮法工艺。 1990年我国平板玻璃产量已位居世界第 一 ,但其中浮法玻璃产量还不到40%。经 过二十多年的努力发展,截止2011年,我 国浮法玻璃生产线已达260余条,
平板玻璃标准
我国强制性平板玻璃标准GB11614-2009 按照质量分为合格品、一等品和优等品三 个等级,不同等级的平板玻璃质量水平不 同,按厚度分2-25mm, 按颜色属性分为无 色透明平板玻璃和本体着色平板玻璃,消 费者可按自己要求选择使用。
合格品:合格品的平板玻璃主要用在六层 以下的一般民用建筑、酒店、写字楼。 一等品:一等品的平板玻璃主要用于汽车 玻璃和深加工玻璃的原片,如钢化玻璃、 中空玻璃、夹层玻璃、防火玻璃、防爆玻 璃等安全玻璃。
“洛阳浮法玻璃工艺”的诞生与创新发展

“洛阳浮法玻璃工艺”的诞生与创新发展刘成雄1曹大伟1陈福1林楚荣2(1.秦皇岛玻璃工业研究设计院有限公司秦皇岛066004;2.中国新型建材设计研究院有限公司杭州310022)中图分类号:TQ171文献标识码:A文章编号:1003-1987(2020)"-0003-08“洛阳浮法玻璃工艺”是我国拥有自主知识产权,在世界玻璃工业中与英国皮尔金顿浮法、美国匹兹堡浮法并驾齐驱的世界三大浮法工艺之一。
自上世纪60年代初开始,由主要发明单位建材科学研究院、秦皇岛玻璃研究所、杭州新材院、秦皇岛玻璃设计院和株洲玻璃厂、洛阳玻璃厂一起经历了艰难的探索,用智慧和汗水让“洛阳浮法玻璃工艺”在中华大地上诞生,在近50年的风雨砥砺中使该技术得到了不断的创新发展,先后自主创新研发了超厚和超薄浮法玻璃技术、大规模浮法玻璃技术、在线镀膜改性技术、浮法特种玻璃等,成功为我国玻璃工业的发展壮大竖起了一座雄伟的丰碑。
一、“洛阳浮法玻璃工艺”的艰辛研发历程(一)浮法的由来在20世纪50年代,英国皮尔金顿(Pilkington)公司经过了7年的研究,于1959年宣布“浮法”发明成功,并获得专利权。
浮法工艺巧妙地利用了玻璃的重力和表面张力的作用,玻璃平整如镜,浮法玻璃质量可以同机械磨光玻璃相媲美,而且产量大,生产效率提高了几十倍。
浮法玻璃的发明一下轰动了国际玻璃界,被誉为平板玻璃史上的一次新的革命,并且迅速在世界上推广发展,逐步取代了机械磨光和其它成型方法,各国竞相购买英国专利,纷纷建设浮法生产线。
同时,英国人对浮法技术严格保密,购买专利的条件十分苛刻。
(二)研发历程回顾I960年北京建材科学研究院开始收集有关浮法玻璃工艺的信息。
在国内率先立项对浮法工艺进行研究。
1964年,北京建材研究院任命黄钧工程师为浮法项目负责人,1965年开始全面的实验室研究工作阶段,从探索浮法成形原理、成形条件、玻璃成分等最基础的工作做起。
研究人员根据掌握的科学知识,几经反复深入研究和试验,从初选的几种金属中确定了用锡作为浮法成型介质,对浮法工艺的基本原理和各个关键因素分别进行了深入的研究,取得了阶段性的进展。
中国浮法的摇篮———写在“洛阳浮法”工艺诞生25周年之际
中国浮法的摇篮———写在“洛阳浮法”工艺诞生25周年之
际
车明
【期刊名称】《中国建材》
【年(卷),期】1996()10
【摘要】中国浮法的摇篮———写在“洛阳浮法”工艺诞生25周年之际车明长期以来,史学家们一直在争论,中国的玻璃是“自创”,还是“泊来”的?但有一点可以肯定,早在西周春秋时期,伴随青铜器冶炼技术的出现,中国就已经能够生产玻璃了。
当时的玻璃只是低熔点玻璃珠,呈浅绿...
【总页数】3页(P29-31)
【关键词】浮法玻璃;生产工艺;洛阳
【作者】车明
【作者单位】
【正文语种】中文
【中图分类】TQ171.721
【相关文献】
1.纪念“中国洛阳浮法工艺”诞生40周年 [J], 林鸿宾
2.“中国洛阳浮法工艺”的技术进步及玻璃工业的发展趋势 [J], 陈双七;刘成雄
3.洛阳浮法绽放熠熠光辉——纪念中国“洛阳浮法玻璃工艺”诞生40周年 [J],
4.中国洛阳浮法技术日趋成熟的典型:昆破六改浮400t/d浮法线顺利投产 [J],
张玉斌
5.中国洛阳浮法技术日趋成熟的典型——昆玻六改浮400t/d浮法线顺利投产 [J], 张玉斌
因版权原因,仅展示原文概要,查看原文内容请购买。
中国浮法玻璃的发展历程
中国浮法玻璃的发展(一)“洛阳浮法”技术的诞生“洛阳浮法”技术的研制,始于60年代初。
当时,英国皮尔金顿兄弟玻璃公司刚刚发表了经过约十年研制,发明并取得成功的国际上最新最先进的平板玻璃生产方法——浮法的问世。
同时,国际上一些学术刊物、杂志、论文和专利,都相继对有关浮法玻璃技术进行报道和简介。
但是这些报道都侧重于商品的性能和功能,而对浮法技术,不仅没有什么具体内容,相当多的都是不真实的,甚至进行误导。
而且当时的中国是处在以美国为首的世界发达国家的经济封锁的情况下,不要说参观工厂和购买技术是不可能的,就是想买一点浮法玻璃的样品,都难以实现。
因此,我国是在一无资料,二无情报,三无样品的情况下,根据物理化学的公共原理,“白手起家”着手进行研制的。
1960年开始时,曾由北京管庄建材科学研究院与上海耀华玻璃厂协作,进行过浮法工艺的初步探索。
后来在建材部主管领导的倡议和支持下,在建材研究院建筑玻璃研究室进行了实验阶段的研究。
通过静态单元试验、半连续工艺试验和连续性工艺试验,特别是对浮抛介质的选择,保护气体的成分和净化,玻璃成分的组成,以及加热元件和锡槽结构及耐火材料的选取等,都历经多次的试验,探索和筛选,直到1967年终于获得了一系列试验室阶段性成果。
接着在此基础上进入中间试验阶段,同时有些试验室阶段的工作,还继续同步进行。
1968年由建材研究院、玻璃设计院、湖南株洲玻璃厂三家合作,利用株洲玻璃厂尚未建成的玻璃球车间,改建为浮法玻璃中间试验线。
经过二年的努力,最后在1970年7月完成了中国浮法玻璃的中间试验。
经过长达6个月连续试验,终于取得了突破性的进展,其中最主要的成果是解决了浮法玻璃的成形方法——玻璃液的直接流入法,并生产出了中国的第一批6毫米浮法玻璃样品。
同时,在技术上对流槽的安装,槽体的构造,雾点的消除以及操作方法和工艺制度等多方面都取得了相当丰富的经验和成果。
紧接着在中间试验成功的基础上与河南洛阳玻璃厂合作,将洛阳玻璃厂建成投产不久的压延玻璃生产线改造为浮法玻璃工业性试验生产线,即进入工业性试验生产阶段,在秦皇岛玻璃研究院(建材研究院玻璃室的一部分)、株洲玻璃设计所(原北京玻璃设计院的一部分)、株洲玻璃厂、管庄建材研究院和洛阳玻璃厂等五个单位的协同合作下,扩大进行浮法玻璃的工业性试验,经过短短几个月的共同奋战,克服了一系列的困难后,终于在1971年9月胜利投产,并成功地拉出了原板宽近2米、厚6毫米的质量较好的浮法玻璃,并向市场提供了商品,取得了商业性的成果。
建筑玻璃生产技术的发展历史
一、建筑玻璃生产技术的发展历史在人类发展历史的长河中,玻璃是人了文明发展的载体之一,玻璃生产技术的进步,贯穿于人类发展历史的全过程。
据考证,人类最早制造玻璃是在五千年前,一般认为古埃及人是创造这一人类文明的创始者,他们使用特制的泥灌烧制玻璃,采用压制和捏朔的方法制造简单的生活器皿和饰物。
大约在公元前1世纪,古罗马人创造出利用铁管吹制玻璃技术,采用一直金属管将熔融的玻璃吹成中空的泡,最后制成形状各异的玻璃器皿。
玻璃器皿吹制法的发明,将玻璃生产技术向前推进了一大步。
就是在今天有些玻璃制品仍然采用这一古老的方法生产。
考古学发现,在公元79年被火山灰埋没的古城中,发现有些建筑在青铜窗框上安装着平板玻璃,这是至今为止发现最早将玻璃作为建筑材料用于居室采光的例证。
由于当时熔化玻璃液的温度较低,因此在玻璃中存在大量未融化的颗粒杂质,玻璃中的颗粒杂质造成光线的散射,使得玻璃只透光而不透明。
同时,当时生产玻璃的工艺是将玻璃液浇铸挤压成玻璃板,因此玻璃板的表面凹凸不平,造成光线的散射,是造成当时生产的玻璃板透光不透明的另外原因之一。
在11~15世纪期间,威尼斯开发了许多玻璃品种,如建筑门窗玻璃、玻璃瓶、玻璃器皿、玻璃镜和其他装饰玻璃,发明改进了多种玻璃生产工艺,逐渐成为全世界玻璃制造中心。
1291年威尼斯政府为了保护自己的玻璃生产工艺,将大量的玻璃工厂迁至穆兰诺岛。
由于当时的生产技术有了很大的进步,生产的玻璃制品十分精美,深受欧洲宫廷贵族的喜爱,价格昂贵,具有极高的艺术观赏价值。
16世纪以后,部分威尼斯穆兰诺岛的工人流亡到国外,将威尼斯当时先进的玻璃生产技术传播到国外,继而在整个欧洲得以普及。
至17世纪以后,欧洲的许多国家都兴建了玻璃制造工厂,改进了玻璃熔制工艺,改木材燃料为煤燃料,稳定了玻璃熔制工艺,提高了玻璃熔化温度,使得玻璃制造技术又向前推进了一步。
瑞士人狄南(Guinand)于1790年发明了利用搅拌法制造光学玻璃,可提高玻璃的熔化均匀度,这一方法应用至今。
浮法玻璃工业简史及生产现状与发展趋势
浮法玻璃工业简史及生产现状与发展趋势浮法玻璃工业是一种广泛应用于建筑、汽车和家电等领域的化工工艺,在现代工业生产中具有重要地位。
本文将介绍浮法玻璃工业的简史,并分析当前的生产现状和发展趋势。
浮法玻璃工业起源于20世纪50年代,其核心技术是将熔融的玻璃液浮在熔融的锡液上,通过表面张力使玻璃液变为平整的连续薄膜,并在空气中冷却固化形成玻璃板。
相比传统玻璃加工方法,浮法工艺具有生产效率高、产品质量稳定等优点,因此在市场上迅速获得了广泛应用。
在浮法玻璃工业的发展历程中,随着科技的进步和市场需求的变化,生产工艺和设备不断升级和改进。
目前,浮法玻璃工业已进入了高度自动化和智能化的阶段,生产效率大幅提高,产品品质更加稳定,满足了各种特殊需要。
同时,新型材料和技术的应用也使得浮法玻璃在防火、隔音、保温等方面的性能得到了进一步提升。
当前,浮法玻璃工业面临着许多挑战和机遇。
一方面,市场竞争激烈,企业需要不断创新和改进,提高产品质量和技术含量,以满足不同客户的需求。
另一方面,环境问题和资源紧缺也成为了工业发展的限制因素。
因此,可持续发展和节能减排已经成为浮法玻璃工业的重要方向。
未来,浮法玻璃工业有望继续保持稳定增长,并拥有更广阔的市场空间。
随着新兴行业如光伏、建筑以及汽车等的快速发展,对高质量玻璃的需求将持续增长。
同时,技术创新和工艺改进也将推动浮法玻璃工业的发展,例如采用新材料和新工艺提升产品性能。
此外,全球环保意识的提升也将促使浮法玻璃工业在可持续发展方面加大投入和努力。
总结而言,浮法玻璃工业在过去几十年里取得了巨大的发展,已成为现代工业中不可或缺的一部分。
当前,浮法玻璃工业正朝着更高质量、更环保和更智能的方向发展。
我们有理由相信,在不久的将来,浮法玻璃工业将会实现更好的发展,并为我们的生活带来更多的便利和美好。
- 1、下载文档前请自行甄别文档内容的完整性,平台不提供额外的编辑、内容补充、找答案等附加服务。
- 2、"仅部分预览"的文档,不可在线预览部分如存在完整性等问题,可反馈申请退款(可完整预览的文档不适用该条件!)。
- 3、如文档侵犯您的权益,请联系客服反馈,我们会尽快为您处理(人工客服工作时间:9:00-18:30)。
40年风雨历程,洛阳浮法绽放熠熠光辉
中国“洛阳浮法玻璃工艺”诞生已经四十多年,回首往昔,作为世界三大浮法玻璃工艺诞生地之一的中国建材集团,始终高举民族玻璃工业大旗,强化战略驱动,实现科学发展,不断完善提高“洛阳浮法玻璃工艺”,在我国玻璃行业树立起了一座又一座丰碑,引领了中国玻璃制造工艺的伟大革新,为中国民族玻璃工业的发展壮大做出了卓越的贡献。
中国“洛阳浮法玻璃工艺”的诞生
我国上世纪五、六十年代平板玻璃工业十分落后,虽然恢复、扩建、新建了几个平板玻璃厂,但年产量只有几百万重量箱,远不能满足国民经济发展的需要。
而拥有“浮法玻璃技术”的欧美国家对我进行技术封锁,我国科技人员自力更生,开始研发“浮法玻璃技术”。
1960年北京的建筑材料工业部建筑材料科学研究院开始收集研究有关浮法玻璃工艺的信息。
1965年,建筑材料工业部玻璃工业设计院派选工艺、窑炉、机电、煤气等专业技术人员参加浮法玻璃试验工作,正式开展浮法玻璃实验室阶段研究。
1967年获得了一系列试验室阶段性成果,拉出了200-250mm宽的浮法玻璃带。
1971年9月,80t/d浮法玻璃生产线在洛阳玻璃厂胜利投产,成功拉引出原板宽近2m、厚6mm质量较好的浮法玻璃,投入市场后取得良好的经济效益。
1981年4月30日,国家科委、计委和建筑材料工业部对我国
第一条浮法玻璃工业性试验生产线进行了技术鉴定,并命名“洛阳浮法玻璃工艺”,这是文革后第一个通过国家级技术鉴定的科研项目。
同年10月,“洛阳浮法玻璃工艺”获国家发明二等奖,这是新中国成立后,继万吨轮、万吨水压机后第三个获国家发明奖的重大项目,获奖单位包括:洛阳玻璃厂、秦皇岛玻璃研究所、杭州新型建筑材料设计院、株洲玻璃厂、建筑材料科学研究院、秦皇岛玻璃设计院。
“洛阳浮法玻璃工艺”的诞生,迎来了中国玻璃工业发展的新曙光,开辟了中国玻璃工业变革、创新和发展的新时代,为我国玻璃工业的发展竖起一座雄伟的丰碑,成为与英国皮尔金顿浮法工艺、美国匹兹堡浮法工艺并驾齐驱的世界三大浮法工艺之一。
中国浮法玻璃的发展
1983年国家建材局确定了我国平板玻璃工业要以浮法工艺为中心的发展战略。
1985年洛阳玻璃厂建成当时国内最大的400吨级生产线,实现了中国“洛阳浮法玻璃工艺”“由小到大”的重大突破,为“洛阳浮法”技术在行业的全面推广奠定了基础。
到20世纪90年代,浮法工艺在全国遍地开花,迅速发展。
国家连续在几个五年计划中就浮法技术立项组织科技攻关,并在秦皇岛建立了浮法试验基地。
我国还先后向印尼等国出口了四条产能为300至500t/d 的“洛阳浮法”技术和装备生产线。
进入二十一世纪,洛阳浮法玻璃技术得到了飞跃式的发展,规模大型化、品种高档化、功能化和清洁生产、节能减排已成为浮法玻璃
发展的主要趋势。
截至2010年,我国已建成了230余条国产的浮法玻璃生产线,浮法玻璃占到平板玻璃总产量的85%以上,浮法玻璃生产线的平均熔化能力已超过500t/d,其最大规模已达1100t/d。
我国浮法玻璃的年产量已达到5.4亿重量箱,占全球平板玻璃产量的50%左右,其产量稳居世界第一。
2010年1月10日,在中国建材集团的大力支持和协调下,经国家科技部批准,洛玻集团与蚌埠院联合申请的浮法玻璃新技术国家重点实验室进入第二批企业国家重点实验室名单。
组建浮法玻璃新技术国家重点实验室,就是要针对制约我国浮法玻璃技术发展的关键环节进行创新性研究,进一步形成有自主知识产权的关键技术原型和基础研究成果,推进我国浮法玻璃行业的整体技术进步。
这是洛玻继1994年成功组建国家级企业技术中心后在科技创新体系建设方面取得的又一重大突破。