铝型材电解着色工艺规程
电镀工艺:铝合金氧化膜的电解着色

电镀工艺:铝合金氧化膜的电解着色电镀工艺:铝合金氧化膜的电解着色1.铝合金氧化膜的常用着色工艺:铝合金常用着色工艺大体上可以分为三类:a.整体着色法:包括自然发色和电解发色两种,自然发色指阳极氧化过程使铝合金中添加成分(Si、Fe、Mn等)氧化,而发生氧化膜的着色。
电解发色指电解液组成及电解条件的变化而引起的氧化膜的着色。
b.染色法:以一次氧化膜为基础,用无机颜料或者有机染料进行染色的氧化膜。
c.电解着色法:以一次氧化膜为基础,在含金属盐的溶液中用直流或交流电进行电解着色的方法,电解着色的耐候性、耐光性和使用寿命比染色法要好、其成本远低于整体着色法,目前广发应用于建筑铝型材的着色。
国内外工业化的电解着色槽液基本上都是镍盐和锡盐(包括锡镍混合盐)溶液两大类,颜色大体上都是从浅到深的古铜色系。
2.电解着色的原理多孔型阳极氧化膜的有规律和可控制的微孔,通过电解着色在孔的底部沉积非常细的金属和(或)氧化物颗粒,由于光的散射效应可以得到不同的颜色。
颜色的深浅和沉积颗粒的数量有关,也就是与着色时间和外加电压有关。
一般来说,电解着色颜色类似都是从香槟色、浅到深的青铜色一直到黑色,色调又不完全相同,这与析出颗粒的尺寸分布有关。
目前电解着色只有于古铜色、黑色、金黄色、枣红色几种。
3.电解着色的应用Sn盐和Sn-Ni混合盐是我国和欧美主要的着色方法,其盐为SnSO4,是利用Sn2+电解还原在阳极氧化的微孔中析出而着色;但Sn2+稳定性差易被氧化成没有着色能力的Sn4+,因此锡盐着色关键是槽液成分和锡盐稳定性是此工艺的关键,锡盐对杂质不敏感,着色均匀性比较好,对水污染不大。
Ni盐电解着色在日本比较普遍,他常用于浅色系(仿不锈钢色、浅香槟色),他着色速度快,槽液稳定性好,但对杂质敏感,目前除杂质设备已成熟,但需要一次性投资大。
阳极氧化电解着色
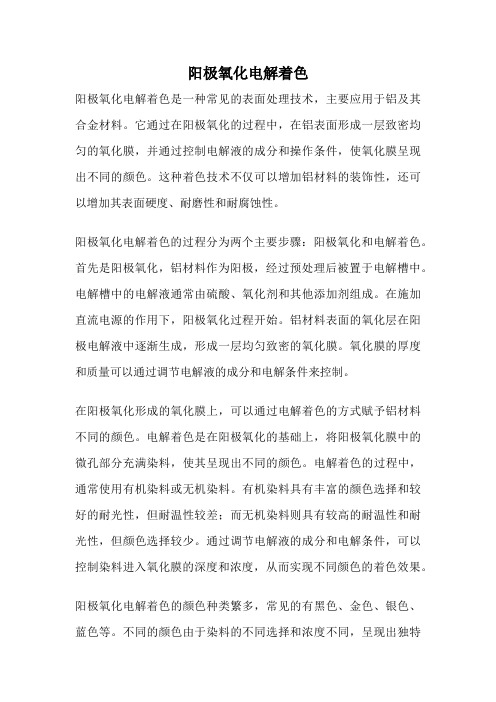
阳极氧化电解着色阳极氧化电解着色是一种常见的表面处理技术,主要应用于铝及其合金材料。
它通过在阳极氧化的过程中,在铝表面形成一层致密均匀的氧化膜,并通过控制电解液的成分和操作条件,使氧化膜呈现出不同的颜色。
这种着色技术不仅可以增加铝材料的装饰性,还可以增加其表面硬度、耐磨性和耐腐蚀性。
阳极氧化电解着色的过程分为两个主要步骤:阳极氧化和电解着色。
首先是阳极氧化,铝材料作为阳极,经过预处理后被置于电解槽中。
电解槽中的电解液通常由硫酸、氧化剂和其他添加剂组成。
在施加直流电源的作用下,阳极氧化过程开始。
铝材料表面的氧化层在阳极电解液中逐渐生成,形成一层均匀致密的氧化膜。
氧化膜的厚度和质量可以通过调节电解液的成分和电解条件来控制。
在阳极氧化形成的氧化膜上,可以通过电解着色的方式赋予铝材料不同的颜色。
电解着色是在阳极氧化的基础上,将阳极氧化膜中的微孔部分充满染料,使其呈现出不同的颜色。
电解着色的过程中,通常使用有机染料或无机染料。
有机染料具有丰富的颜色选择和较好的耐光性,但耐温性较差;而无机染料则具有较高的耐温性和耐光性,但颜色选择较少。
通过调节电解液的成分和电解条件,可以控制染料进入氧化膜的深度和浓度,从而实现不同颜色的着色效果。
阳极氧化电解着色的颜色种类繁多,常见的有黑色、金色、银色、蓝色等。
不同的颜色由于染料的不同选择和浓度不同,呈现出独特的视觉效果。
例如,金色着色常使用硫酸铜和硫酸镁的电解液,并在阳极氧化膜中充满金色染料;而黑色着色则常使用硫酸镍和硫酸铜的电解液,并在氧化膜中充满黑色染料。
不同颜色的着色效果可以根据客户的需求来选择,以满足不同的装饰要求。
阳极氧化电解着色技术具有许多优点。
首先,它能够增加铝材料表面的硬度和耐磨性,提高其使用寿命。
其次,通过选择不同染料和调节电解条件,可以实现多种颜色的着色效果,增加了铝材料的装饰性。
此外,阳极氧化膜具有良好的耐腐蚀性,能够保护铝材料不受外界环境的侵蚀。
因此,阳极氧化电解着色技术被广泛应用于建筑、航空航天、汽车和电子等领域。
铝材阳极氧化工艺

铝材阳极氧化工艺主要通过,盐雾、耐摩擦、电导率、电击穿等测试来判定膜层的好坏。
工艺:除油--水洗--水洗--阳极反应--水洗--封闭--烘烤铝制品阳极氧化工艺流程铝制品阳极氧化通用的工艺流程如下:铝工件→上挂具→脱脂→水洗→碱蚀→水洗→出光→水洗→阳极氧化→水洗→去离子水洗→染色或电解着色→水洗→去离子水洗→封闭→水洗→下挂具对于要求高光亮度的铝制品,可采用如下的工艺流程:铝工件→机械抛光→脱脂→水洗→中和→水洗→化学或电化学抛光→水洗→阳极氧化→水洗→去离子水洗→染色或电解着色→水洗→去离子水洗→封闭→水洗→机械光亮铝及铝合金阳极氧化着色工艺流程(图)铝及铝合金阳极氧化着色工艺规程 1、主题内容与适用范围:本规程规定了铝及铝合金阳极氧化、着色、电泳生产的工艺和操作的技术要求及规范。
2、工艺流程(线路图)基材→装挂→脱脂→碱蚀→中和→阳极氧化→电解着色→封孔→电泳涂漆→固化→卸料包装→入库3、装挂:3.1装挂前的准备。
3.1.1检查导电梁、导电杆等导电部位能否充分导电、并定期打磨、清洗或修理。
3.1.2准备好导电用的铝片和铝丝。
3.1.3检查气动工具及相关设备是否正常。
3.1.4核对流转单或生产任务单的型号、长度、支数、颜色、膜厚等要求是否与订单及实物相符。
3.1.5根据型材规格(外接圆尺寸、外表面积等)确定装挂的支数和间距、色料间距控制在型材水平宽度的1.2倍左右,白料间距控制在型材宽度的1倍左右。
3.1.6选择合适的挂具,确保正、副挂具的挂钩数与型材的装挂支数一致。
3.2 装挂:3.2.1装挂时应先挂最上面一支,再固定最下面一支,然后将其余型材均匀排布在中间、并旋紧所有铝螺丝。
3.2.2装挂前在型材与铝螺丝间夹放铝片,以防型材与挂具间的导电不良而影响氧化、着色或电泳。
3.2.3装挂时,严禁将型材全部装挂在挂具的下部或上部。
3.2.4装挂的型材必须保持一定的倾斜度(>5°)以利于电泳或着色时排气,减少斑点(气泡)。
铝型材厂工艺操作规程范本

铝型材厂工艺操作规程范本第一章总则第一条为了规范铝型材厂的工艺操作行为,确保生产过程的安全和产品质量,制定本规程。
第二条本规程适用于铝型材厂的生产操作过程中涉及到的工艺操作。
第三条工艺操作人员应严格遵守本规程,保持操作规范和注意安全。
第四条工艺操作人员应接受相关的培训和考核,持有相应的工艺操作证书。
第五条工艺操作人员应了解产品的工艺要求和相关操作规程,确保按规定进行操作。
第二章操作规范第六条工艺操作人员应佩戴防护装备,包括安全帽、防护眼镜、口罩等,确保自身和他人的安全。
第七条工艺操作人员应按照工艺要求,选择合适的设备和工具进行操作。
第八条工艺操作人员在进行设备操作之前,应仔细检查设备的运行状况,确保设备正常。
第九条工艺操作人员应按照工艺要求,准确测量和调整参数,如温度、压力等。
第十条工艺操作人员应按照工艺要求,严格控制操作时间和操作速度,确保产品质量。
第十一条工艺操作人员应按照工艺要求,进行现场清理和维护工作,确保设备和环境的清洁。
第十二条工艺操作人员应及时反馈设备异常和质量问题,并积极参与问题解决过程。
第三章安全措施第十三条工艺操作人员应熟悉厂区的安全规定,并严格遵守。
第十四条工艺操作人员应定期参加安全培训,了解应急处理和事故防范知识。
第十五条工艺操作人员应严格遵守消防安全规定,禁止在生产区域吸烟、使用明火等。
第十六条工艺操作人员应使用防护用品,如手套、耳塞等,减少设备操作对身体的伤害。
第十七条工艺操作人员应注意设备周围的隐患,并及时报告处理,确保设备安全。
第十八条工艺操作人员在操作结束后,应及时关闭设备,切断电源,确保设备的安全。
第四章质量控制第十九条工艺操作人员应按照质量要求,严格控制操作过程中的参数,确保产品质量。
第二十条工艺操作人员应及时记录关键参数和质量数据,做好相关的统计和分析工作。
第二十一条工艺操作人员应及时发现和处理产品质量问题,以及时止损,防止不良品流出。
第二十二条工艺操作人员应及时清理设备和操作环境,减少杂质对产品质量的影响。
电解铝工艺流程及技术规程
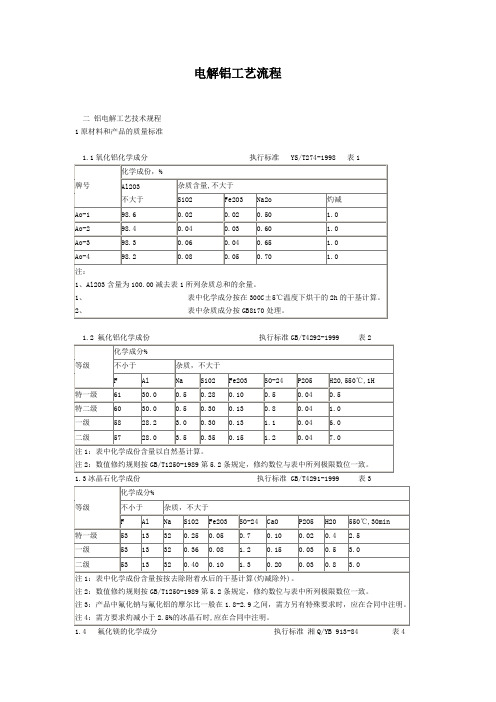
电解铝工艺流程二铝电解工艺技术规程1原材料和产品的质量标准1.1氧化铝化学成分执行标准 YS/T274-1998 表11.2 氟化铝化学成份执行标准GB/T4292-1999 表21.3冰晶石化学成份执行标准 GB/T4291-1999 表31.4 氟化镁的化学成分执行标准湘Q/YB 913-84 表41.5 预焙阳极炭块理化性能指标执行标准YS/T 285-1998 表51. 6重熔用铝锭的化学成分执行标准GB/T1196-2002 表61.7电工圆铝杆的电性能执行标准GB3954-83 表7注:1 N/mm2=1mpa=0.102kgf/ mm2。
2工艺技术参数2.1 电解槽技术参数2.1.1 电解槽结构参数:电流强度: 200KA;母线进电方式:大面四点;阳极碳块尺寸:1500×660×550mm;阳极组数:28组;阳极底掌面积:27.72㎡;阳极电流密度:0.722A/cm2;阳极钢爪数:4个;槽壳外形尺寸:11594×4738×1796mm;槽膛尺寸:10600×3780×470mm;大面宽度:300mm;小面宽度:420mm;阳极中缝:180mm;阳极间缝:40mm;电解槽下料点:4点;阴极碳块尺寸:3250×515×450mm;阴极碳块组数:18组;阴极钢棒尺寸:65 ×180×1985mm;侧部碳块厚度:125mm;槽壳结构:船形摇篮槽壳,17只摇篮架,槽壳总重26.125t;电解槽集气效率:98 %。
2.1.2 阳极升降装置阳极升降装置为螺旋起重器;阳极升降速度99.3mm/min;阳极升降有效行程270mm,上读数50mm ,下读数320mm,总起重量50t 。
2.1.3 打壳下料装置2.1.3.1 打壳机构适用压缩空气气压大于0.55Mpa,气缸工作温度80~90℃,打壳机构打击速度0~85cm/s,行程550mm;2.1.3.2 下料方式:1.8升定容下料器四点交叉下料,3.6kg/次。
铝合金电解着色技术_周蕾玲
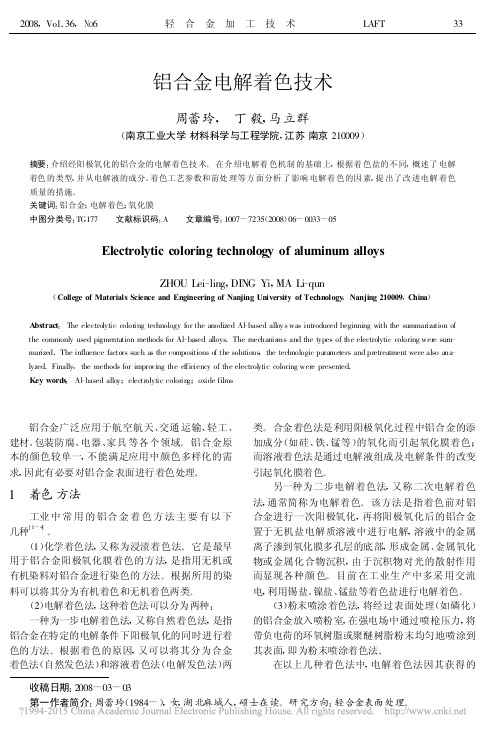
着色盐 Ni 盐 Co 盐 Cu 盐
着色后氧化膜颜色 黄色 , 青铜色 , 黑色 黄色 , 青铜色 , 黑色 茶色 , 青铜色 , 红褐色 , 黑色
Sn 盐 Pb 盐 , Ca 盐 , Zn 盐 Ag 盐 Au 盐 TeO3 盐 MnO4 盐 SeO 3 盐 Se 盐 Cr 盐 Ba 盐 , Ca 盐 Mo , W 盐 Cu , Sn 混合盐 15 %H2SO4 +CuSO4 磷酸 +N iSO4 氰化亚铁
稳定剂酚类铜盐她堑银盐衄稳定剂硒盐鸭碲酸钠添加剂表不同金属盐电解着色对应的氧化膜颜色着色盐着色后氧化膜颜色盐盐盐盐盐盐盈盐盐盐妈盐晚盐盐盐盐盐盐盐混合盐磷酸氰化亚铁黄色青铜色黑色黄色青铜色黑色茶色青铜色红褐色黑色茶色青铜色黑色青铜色系绿色紫色浅青铜色金黄色浅青铜色浅金色红色绿色白色黄色蓝色茶色青铜色红褐色黑色绿色蓝色紫色黄色绿色蓝色紫色黄色蓝色影响着色速度而络合剂浓度却不会但是络合剂浓度与电压温度着色时间硫酸亚锡浓度值一样会对着色均匀性产生影响
锡盐电解着色抗杂质性能好 , 电解着色溶液分 布能力强 , 工业控制较简单 。 但是 , 就浅色系着色而 言 , 锡盐着色的色差和色调比较难控制 。 3 .2 镍盐电解着色
镍盐电解着色在日本比较普遍 , 早在 40 多年前 日本人浅田太平就申请了有关交流镍盐电解着色的 专利 。镍盐电解着色常用的着色盐是硫酸镍 , 由其 提供金属镍离子 , 在电解过程中沉积并显色 。
茶色 , 青铜色 , 黑色 青铜色系 绿色 紫色 浅青铜色 金黄色 , 浅青铜色 浅金色 红色 绿色 白色 黄色 , 蓝色 茶色 , 青铜色 , 红褐色 , 黑色 绿色 , 蓝色 , 紫色 , 黄色 绿色 , 蓝色 , 紫色 , 黄色 蓝色
影响着色速度 , 而络合剂浓度却不会 , 但是络合剂浓 度与电压 、温度 、着色时间 、硫酸亚锡浓度 、pH 值一 样 , 会对着色均匀性产生影响 。
铝电解生产安全操作规程

铝电解生产安全操作规程铝电解生产是一种涉及高温、高压等危险因素的生产过程,为了确保安全生产和员工的人身安全,制定和遵守铝电解生产安全操作规程非常重要。
以下是一个关于铝电解生产安全操作规程的示范,总计2000字。
一、安全操作规程的目的和适用范围1. 目的:确保铝电解生产过程中的安全生产,防止事故发生,保障员工的人身安全。
2. 适用范围:适用于铝电解生产车间的所有工作人员和管理人员。
二、基本安全原则1. 生产过程需保持高度集中注意力,不得擅自离开工作岗位。
2. 严禁吸烟、火种、明火等,以防止火灾事故的发生。
3. 强制佩戴个人防护装备,如头盔、防护眼镜、防护手套、防滑鞋等。
4. 遵守工作区域的安全标识和标记。
5. 严格遵循操作程序和步骤,不得随意改变操作方法。
三、安全措施1. 对设备的安全操作:- 在操作前必须对设备进行检查,确保其正常运转且与相关设备配备正确。
- 操作前必须向电气设备投入地线。
- 严禁私自改变设备的操作程序,如需更改应向上级主管报告并经过批准。
2. 防止化学品事故的控制:- 确定和标记储存铝电解所需化学品的储存位置,保持通风良好。
- 仅限于经过培训和授权的人员处理化学品。
- 化学品资料应妥善保存,定期检查其有效性和完整性。
3. 高温和高压操作的安全措施:- 高温和高压操作前必须穿戴适当的防护装备,如耐高温服装、耐高温手套、保护面罩等。
- 高温和高压设备的操作必须经过相关培训,并持有相关证书。
- 高温和高压设备的开关必须由经过培训和授权的人员操作,严禁私自操作。
4. 火灾事故的控制:- 确保消防设备的有效性,包括灭火器、灭火系统等。
- 定期检查消防通道的畅通性,防止堵塞影响撤离。
- 发现火灾迹象时,立即发出警报并按地区火灾预案进行撤离。
5. 电气安全措施:- 高压电设备和线路必须经过专业人员定期检查和维护。
- 维护电气设备的通风良好,防止过热。
- 严禁擅自触碰或操作电气设备,不得随意接触电线和插头。
电解着色工艺
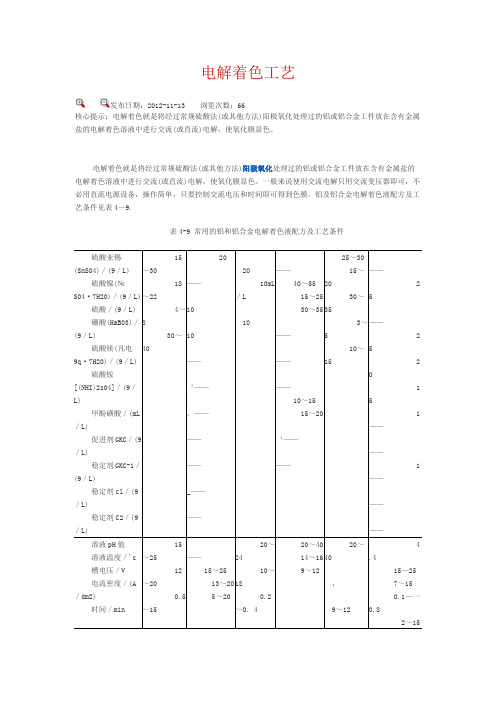
电解着色工艺发布日期:2012-11-13 浏览次数:66核心提示:电解着色就是将经过常规硫酸法(或其他方法)阳极氧化处理过的铝或铝合金工件放在含有金属盐的电解着色溶液中进行交流(或直流)电解,使氧化膜显色。
电解着色就是将经过常规硫酸法(或其他方法)阳极氧化处理过的铝或铝合金工件放在含有金属盐的电解着色溶液中进行交流(或直流)电解,使氧化膜显色。
一般来说使用交流电解只用交流变压器即可,不必用直流电源设备,操作简单,只要控制交流电压和时间即可得到色膜。
铝及铝合金电解着色液配方及工艺条件见表4—9.表4-9 常用的铝和铝合金电解着色液配方及工艺条件实际上很多种金属的无机盐溶液都可以做为电解着色液,溶液的配方及工艺也有很多种。
国内常用的主要是镍盐、锡盐和钴盐为主盐或者这三种盐组合而成的着色液。
其中亚锡盐的着色最容易掌握,也比较简单,所得色泽范围也较宽,只要控制着色时间,就可以得到由青铜色到黄色到古铜色、棕色,最后为黑色的各种颜色,而且色泽很均匀一致,但是槽液不稳定,亚锡离子(Sn2+)很容易氧化成锡离子(Snt+)形成白色沉淀,故必须加入稳定剂防止其氧化沉淀过快。
作者20世纪80年代在南海、顺德一带几家铝型材厂就是采取亚锡盐着色并添加稳定剂,后来也有改用镍盐为主的着色液。
镍盐着色液稳定性比较好,污染敏感性也较少,成本相对也较低,但是着色的范围较窄,尤其是深黑色很难得到颜色的均一性,有时也不好控制。
交流电解着色的处理过程中,铝及铝合金工件经阳极氧化后,要清洗干净氧化的酸液,然后马上放进着色槽着色。
在空气中停留的时间不能过长,如未能马上进入着色槽,应浸泡在洁净的清水中,避免被空气氧化。
进入着色槽后,不要马上通电,应先静置1"一2min,电压用调压器控制由零开始慢慢升高,并在lmin内调至规定的着色电压值。
亚锡盐或镍盐交流电解着色可以得到由青铜到黑色由浅至深的各种颜色。
色泽的控制通常是恒定电压,然后控制着色时间。
- 1、下载文档前请自行甄别文档内容的完整性,平台不提供额外的编辑、内容补充、找答案等附加服务。
- 2、"仅部分预览"的文档,不可在线预览部分如存在完整性等问题,可反馈申请退款(可完整预览的文档不适用该条件!)。
- 3、如文档侵犯您的权益,请联系客服反馈,我们会尽快为您处理(人工客服工作时间:9:00-18:30)。
铝型材电解着色工艺规程
1、主要方法介绍
着色工艺方法分为:锡盐和锡镍混合盐槽液电解着色法(香槟色系);镍盐电解着色工艺(香槟色系);锰盐电解着色工艺(金黄色)和亚硒酸盐着色工艺(钛金色)等几大类。
锡盐槽液的着色电源是比较简单的普通交流着色电源,在中国和欧洲都已经广泛生产和应用。
但是锡盐槽液不容易得到稳定均匀的浅色体系。
仿不锈钢色和香槟色等浅色系的获得还是以选择镍盐电解着色法比较可靠。
在我国使用较多的是从日本引进的“住化”法,亦称直接镍盐着色法(即单镍盐着色法)。
2、工艺控制注意事项
铝型材阳极氧化工序完毕,不需封孔,直接转入着色工序(不需着色处理的铝型材,可直接转入电泳工序进行处理)。
阳极氧化工序需注意,应尽量控制阳极氧化槽液的温度,严禁槽液温度超过22℃,导电大梁两端的电流应一致,保持氧化膜均匀,尽量减少因氧化工序的工艺控制不当而导致着色不均等缺陷的产生。
着色铝型材的生产在实际操作中,着色时间的控制要求精确到秒,温度范围控制±2℃,PH值控制在上下0.10之间为宜,各项工艺指标波动范围越小越好,在其他工艺参数正常的情况下,颜色的深浅根据时间确定。
一般情况下,尽量略为深一点。
因为在纯水洗(①槽)时,颜色会减浅一些。
着色槽进料时,应斜着进入,待料平稳,无气泡后,才能通电。
先进先出,以保证型材二端头的颜色一致。
通电的顺序:氧化后必须彻底清洗,然后浸入槽液中上下提升数次,并静置1min,其后接通电源并缓慢地以0.35V/S的速度从零增至所需电压,此时电流密度很快上升至最大限疫(1.5-2A/dm2)),着色硅机工作时不得断电.
着色完成应立即起吊,转入下道水洗槽再对色,不可在着色槽停留,严格控制转移时间, 着色后水洗槽的PH值要求≥3.
下面简单介绍几种着色方法的生产工艺参数。
二、电泳
(一)电泳涂装工艺流程:
1、电泳涂装工艺原理见设备平面示意图
2.电泳涂装工序工艺流程:
热纯水洗→纯水洗→电泳→一次水洗(RO
1)→二次水洗(RO
2
)→沥干→固
化(烘干)→冷却→下排。
每道工序都会对电泳型材质量造成直接影响,所以每工序都有严格的工艺技术要求,操作过程一定要规范,各工序之间连续性较强。
若操作不当,可能会造成各槽液交叉污染,处理起来比较困难,增加生产成本。
(二) 电泳涂装各工序工艺控制技术参数及操作要点
1.纯水洗工序工艺控制范围
不管是阳极氧化未经着色工序的铝型材,还是经过着色处理的铝型材,都必须经过二次纯水洗。
才能进入电泳涂装工序,第一次热纯水洗。
工艺控制参数如下:
电导率<100us/cm,温度:70℃—80℃
PH值:4.5—6.0,也可调整到6.5—7.5时间, 3min左右
第二次纯水洗(现在也有一些厂家抛弃此工序)工艺参数控制:
电导率<50us/cm, PH值:5.0—8.0
二次水洗槽内的水体要求洁净,不得有任向杂质及漂浮物,防止灰尘进入,避免电泳型材表面粗糙.毛刺。
若用肉眼观察,水底有沉淀物时,应及时换水。
2..电泳工序工艺技术控制规范
本工序主要控制漆膜均匀达标,各项理化指标合格,防止漆膜偏厚或达不到标准要求。
GB5237.3-2004复合膜厚度国家标准:≥16um,其控制主要从以下几个方面入手,电泳涂装工艺技术参数如下:
(1). 主槽工艺参数控制范围
固体分:6%—8%(一般控制在7%左右为宜)
电导率:300us/cm—800us/cm, PH值:7.5—8.2
电压:130V—140V(银白漆涂装可调至160 V左右)
温度:20℃—22℃, 时间:3min左右
酸值:35—45KOHmg/g-R(山东半岛地区以外25—30KOHmg/g-R)
胺值:20—25(山东半岛地区以外17—20)
胺克分子比:0.68—0.75, 异丙醇:1.5%—3.5%,
乙二醇单丁醚:0.5%—1.5%, 硫酸根离子:≤20ppm,
氯离子:≤5ppm.
槽工艺控制范围:
(2).RO
1
电导率:≤200us/cm, PH值:7.9—9.0之间,
固体分:0.5—1.5%, 异丙醇:0.3%,
乙二醇单丁醚:0.1%, 时间:3—5min.
槽工艺控制范围:
(3).RO
2
固体分:≤0.5%, 电导率:≤50 us/cm,
PH值:8.5—10.0, 时间:2—3min.。
3. 电泳涂装工序操作要点:
(1)热纯水洗
配槽初始注入的纯水要求水质电导率10us/cm以下,PH值4.5以上。
操作过程会从前处理工序带入一部分酸液等污染物,导致水质下降。
日常生产中要求:电导率100us/cm以下,PH值5.5以上,水温70℃-80℃,浸泡时间2-3min。
上下最低提升2次。
热纯水洗要起到“半封孔”作用,使氧化膜孔隙扩张,充分洗去从前工序带入的酸液杂质,热纯水洗槽液的液面要高于前工序槽液液面,这样可以充分洗去挂具、导电杆上残留的酸液杂质,减轻对后纯水洗的压力。
(2)纯水洗:
进一步浇洗型材及挂具上的污染物,此纯水洗水温不宜过高,以便能较容易地将型材基体温度降到32℃以下。
配槽初始加水水质要求10us/cm以下,PH值6.5-7.5,浸泡时间1-2min,提升2次,因操作过程中随前工序的带入,PH值可能会下降,适时用中和剂调整PH值。
(3)电泳:
将型材缓慢浸入槽液,上下提升2次,使型材中的气体排出,放正静止30s-60s后,开始缓慢升至140V,作用时间宜控制在3min左右,完毕将型材吊出,控液标准以型材上不流槽液为宜。
放置沥干区,待固化。
4. 电泳涂装工序工艺控制注意事项
RO
2槽固体分含量高时,可向RO
1
槽压,RO
1
槽固体分含量高时,可向主槽压。
通过管阀人为控制,RO
1槽、RO
2
槽固体分一旦超过工艺控制范围,必须开动回收
系统,回收实际是一个反渗透过程。
回收的电泳漆,循环到副槽,再循环到主槽。
回收后的液体回到了RO
2
槽。
开回收时,必须注意添加异丙醇、乙二醇单丁醚。
其作用为:乙二醇单丁醚作用于流平性好、亮度高。
异丙醇作用主要起消泡(槽液气泡),流平作用。
若型材表面没有光泽,漆膜上膜慢(其他工艺正确)的情况出现时,就要考虑添加异丙醇、单丁醚。
其控制范围为:异丙醇1.5%—3.5%,乙二醇单丁醚0.5%—1.5%(河北枣强漆、广东佛山漆、日本漆、意大利漆、台
湾漆都有一定的差别,视其具体情况,可做0.3—0.5的调整)。
RO
1槽、RO
2
槽
固体分含量高时,特别是RO
2
槽固体分超标时,型材不易沥干,影响固化。
而沥干放置时间长,又容易污染灰尘,产生废品。
电压软启动时间:30—50s,预侵泡时间1min,断电后侵泡时间30s循环过滤精度为3 um,冬天不生产时需保温10℃以上。
电泳工序还有几点需引起重视,也是节约电耗的一个措施。
固体分含量高(7%以上),在电压不变的情况下(一般取140V),可缩短电泳时间,视漆膜厚度在2min的范围内,可缩短通电时间30s左右,照常能够获得理想的漆膜。
(笔者在山东临沂地区试验过槽液固体份含量3%也能达到理想的漆膜,但在其他地区试验没有成功。
具体机理有待验证。
)若电泳槽的电导率高,反映PH值上升,导致漆膜上膜慢,而且漆膜不均匀。
采取措施是:开动精制系统,降低PH值,降低电导率。
5. 电泳槽液的控制措施:
电泳槽液的控制措施见下表:
(三). 电泳槽液调整公式及糟液原漆存量的计算方法
1. 电泳槽液补给量按下式来计算:
补给量=主槽[含副槽] 的总含量[kg]×不足的含量÷50%[或60%]。
如果电泳槽固体份过高(>8)或液面位置超低,用纯水对液面进行
调整(也可用RO
1或RO
2
水进行补给)
2. 月. 季. 年盘点核算电泳漆消耗时,需要首先弄清楚生产线槽内电泳漆存量,下面介绍一种计算方法。
计算主槽、副槽、RO
1槽、RO
2
槽内电泳漆存量方法:
固体份数(化验结果T值)×槽子的立方数(实际容量)÷原漆的固体分值(50%或60%)=存量(T值需转算成kg)。
三. 工艺控制温度180—190℃, 保温时间30min, 注意炉瞠内各点温度应不超过5℃, 同时炉瞠内一定要保持清洁, 不得让灰尘. 泄露的烟气进入.。