深冷处理的优点及最新进展
深冷空分法、变压吸附法、膜分离法制氮优缺点对比表

设备相对简单,无需大型设备,易于集成和操作
能耗
高能耗,需要耗费大量电力和制冷能源
中等能耗,需要周期性地调节吸附剂的压力
低能耗,通常使用压力驱动或温度差驱动,较为节能
维护成本
较高,需要保持设备在低温下运行,维护成本较高
中等,需要定期更换吸附剂
低,膜组件相对稳定,维护成本较低
纯度控制
可以获得较高纯度的氮气
纯度受吸附剂和操作控制
纯度受膜材料和操作控制
适用范围
适用于大型工业制氮,需求纯度较高的场合
适用于小型或移动式制氮需求
适用于中小型制氮设备,对纯度要求适中的场合
这张表格概括了深冷空分法、变压吸附法和膜分离法在制氮过程中的优缺点和适用范围。不同的制氮方法适用于不同的场合,取决于所需的氮气纯度、产量、能耗要求以及设备规模等因素。
深冷空分法、变压吸附法、膜分离法制氮优缺点对比表
方法
深冷空分法
变压吸附法
膜分离法
制氮原理
利用空分设备将空气中的氧气、氩气等分离出去,得到高纯度氮气
通过周期性变换吸附剂的压力来实现氮气与氧气的分离
利用半透膜对气体进行分离,通透性较小的氧气被阻隔,而氮气通过
设备复杂度
需要大型的空分设备和低温条件,设备较复杂
D2钢冷冲模具深冷处理工艺研究

2 试验结果及分析
2.1 淬火和回火工艺
淬火工艺 在 650 和 850 二次预热 在 1 030
加热保温 1 5 m i n 油冷 回火工艺: 1 8 0
60
m i n 有利于消除淬火残留应力
根据深冷处理工艺不同 我们制定 7 个方案
试验工艺 1 未深冷处理 +180 180 min 回火;
D2 钢冷冲模具深冷处理工艺研究
朱繁康 张伟文( 华南理工大学科技实业总厂)
摘 要 研究了深冷处理对 D 2 钢冷冲模具金相组织 硬度和红硬性 冲击韧性及耐磨性的影响 试验和实践结果 表明 深冷处理不仅细化 D 2 冷作模具钢的显微组织 提高其室温硬度和红硬性 而且明显改善冷冲模具 钢的冲击韧性 延长冷作模具的使用寿命
D 2 钢被广泛应用于冷冲模具 由其制作的冷冲 模具由于碳化物呈网状分布完整 且堆积严重 热 处理后进行机械加工时容易发生开裂 使用时刃口 容易崩 因此 对 D2 钢冷冲模具深冷处理工艺进行 研究意义重大
1 试验方法
试验材料采用模具厂家提供的早期失效的 D2 模 具钢板材 化学成分(w%)为 1.5C 11.8Cr 0.9Mo 1 . 0 V 深冷处理以液氮作为冷却介质 升降温速度 控制在一定范围内 并在 -120 -160 和 -196 温度下保温一定时间 对模具和试样进行深冷处理 深冷处理后的模具与常规处理的模具在使用中进行 对比 标准试块在洛氏硬度计 冲击试验机和磨损
3 模具深冷处理使用效果
从表 1 可以看出深冷处理后硬度普遍提高 0.5 1.2 HRC 试样深冷处理后具有较高的抗回火稳定性
红硬性 试样经 4 0 0 回火后 其硬度仍可达 6 0 HRC
2.2 结果分析 2.2.1 金相组织变化
大型深冷工艺要点问题及改善对策

大型深冷工艺要点问题及改善对策摘要:随着我国深冷分离技术应用的增多,深冷分离普遍存在冷箱冻堵,换热效果差等问题;对于以上的问题进行分析,总结;通过技术改进、回收等措施,使其达到节能减排,操作过程简单,合成气冷箱达到设计产量。
下面以某深冷分离分子筛、冷箱为例,对其运行情况及存在问题进行分析冷箱压差上升,换热效果差,分子筛切换气量波动大,工艺超指标,过滤器过滤效果差等,通过改进过滤器,更换分子筛,冷箱爆破吹扫,优化分子筛操作等措施,保证冷箱压差稳定和良好的换热效果。
关键词:冷箱、分子筛、冻堵、改善对策在我国煤制合成气化工中大型深冷工艺使用非常普遍,冷箱的基本结构是板翅式换热器,他能把几组物料根据不同升降温度的需求组合在一个设备内。
由于冷箱具有结构紧凑,通热量大,传热量温差低等优点。
其使用范围逐步增大,特别在乙二醇装置中要求高,深冷冷箱冷量回收及利用上发挥了重要作用。
一、概述该项目为某化工24万吨/年合成气制乙二醇的前工序,工艺分为原料气净化系统和CO 提纯冷箱系统。
原料气净化系统是利用纯化器内吸附剂在不同压力和温度下吸附容量存在差异及选择性吸附的特性来将原料气中的 CO2、H2O 脱除,达到原料气预处理的目的;CO提纯冷箱系统在制冷工艺上,主要采用产品CO节流制冷的工艺原理为整个系统提供冷量。
利用混合气中各组分凝点的不同,经过部分冷凝工艺冷凝下来的低温CO液体在CO精馏塔中精馏提纯。
产品液体CO经节流阀送入CO精馏塔顶部,为冷凝器提供冷源,同时自身得以汽化,汽化后的CO经板翅式换热器复温后出冷箱,进入CO压缩机增压至产品所需压力。
二、简易流程三、运行情况及存在问题冷箱由于结构上的特殊性,致使他存在易堵塞的缺陷。
在国内冷箱由于堵塞而导致冷箱报废的事故时有发生。
堵塞会使其使用效果换热变差,达不到效果设计的换热能力,从而造成动力消耗增加和生产负荷受限。
冷箱压差变高,换热效果差的原因:1.纯化器分子筛再生不完全,原料气中的CO2随着时间运行推移,分子筛饱和穿透,co2进入冷箱冻结在管壁。
铝合金的深冷处理研究
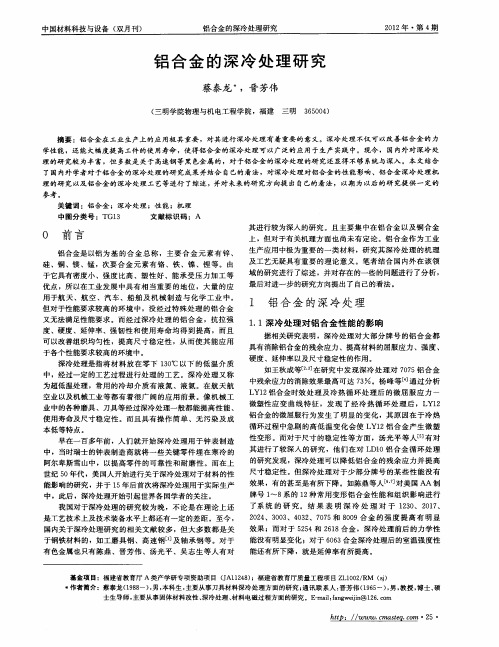
硅 、铜 、镁 、锰 ,次要合 金 元素 有铬 、铁 、镍 、锂 等 。由
于它具有 密度小 、强度 比高 、塑性好 、能 承受压 力加 工等
优 点 ,所 以在 工业 发 展 中具 有 相 当重 要 的地 位 ,大 量 的 应
是 _艺技术上及技术装备水平上都还有一定的差距 。至今 , T 国内关 于深冷处理研 究 的相 关文献较 多 ,但大多 数都 是关
2 2 、30 、4 3 、7 7 0 4 0 3 0 2 0 5和 8 0 0 9合 金 的 强度 提 高有 明显
效果 ;而对 于 5 5 24和 2 1 68合 金 ,深冷处理 前后 的力 学性
微塑性应 变 曲线 特征 ,发现 了经冷 热循 环 处理 后 ,L 2 Y1
使用寿命及尺寸稳定性 。而且具 有操作 简单 、无 污染及 成
本低等特点 。
早 在 一 百 多 年 前 ,人 们 就 开 始 深 冷 处 理 用 于 钟 表 制 造
铝合金 的微屈服行 为发生 了明显 的变化 ,其 原 因在于冷 热 循环 过程 中急剧 的高低 温变化 会使 L 1 Y 2铝 合金 产生微 塑 性变形 。而对 于尺寸 的稳定性 等方 面,汤光平 等人I 有 对 5 ] 其进行 了较深 入 的研 究 ,他们 在对 L 0铝合 金循 环处 理 D1
用 于航 天 、航 空 、汽 车 、船舶 及机 械 制造 与化 学 工业 中。 但对 于性 能要求较 高的环境 中 ,没经过 特殊处理 的铝 合金 又无 法满 足性 能要 求 。而经过 深冷处 理 的铝 合金 ,抗 拉强 度 、硬度 、延伸率 、强 韧性 和使 用寿 命均得 到提 高 ,而且 可以改善组织均匀性 ,提高 尺寸稳定 性 ,从而使 其能 应用 于各个性能要 求较高的环境 中。 深冷处理是指将材 料放 在零 下 lO 以下 的低温 介质 3℃ 中,经过一定的工艺过程进 行处理 的工艺 。深 冷处理 又称 为超低温处理 ,常用 的冷却介质 有液氮 、液氨 。在航 天航 空业 以及机械工业等都 有着很广 阔 的应用 前景 。像 机械工 业 中的各种磨具 、刀具等经过深 冷处 理一般都 能提 高性能 、
天然气深冷分离技术
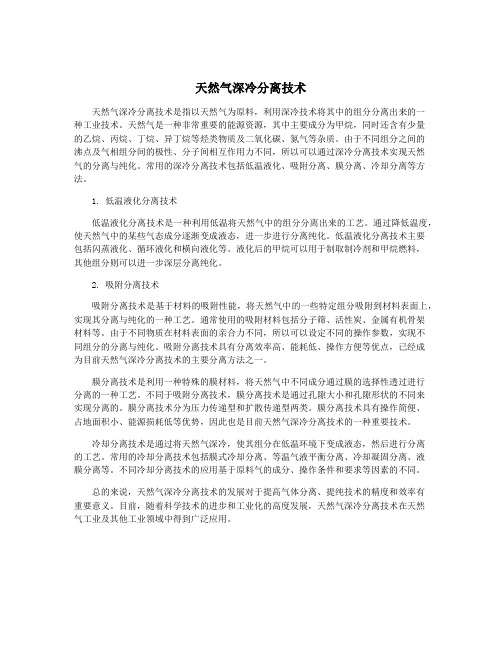
天然气深冷分离技术天然气深冷分离技术是指以天然气为原料,利用深冷技术将其中的组分分离出来的一种工业技术。
天然气是一种非常重要的能源资源,其中主要成分为甲烷,同时还含有少量的乙烷、丙烷、丁烷、异丁烷等烃类物质及二氧化碳、氮气等杂质。
由于不同组分之间的沸点及气相组分间的极性、分子间相互作用力不同,所以可以通过深冷分离技术实现天然气的分离与纯化。
常用的深冷分离技术包括低温液化、吸附分离、膜分离、冷却分离等方法。
1. 低温液化分离技术低温液化分离技术是一种利用低温将天然气中的组分分离出来的工艺。
通过降低温度,使天然气中的某些气态成分逐渐变成液态,进一步进行分离纯化。
低温液化分离技术主要包括闪蒸液化、循环液化和横向液化等。
液化后的甲烷可以用于制取制冷剂和甲烷燃料,其他组分则可以进一步深层分离纯化。
2. 吸附分离技术吸附分离技术是基于材料的吸附性能,将天然气中的一些特定组分吸附到材料表面上,实现其分离与纯化的一种工艺。
通常使用的吸附材料包括分子筛、活性炭、金属有机骨架材料等。
由于不同物质在材料表面的亲合力不同,所以可以设定不同的操作参数,实现不同组分的分离与纯化。
吸附分离技术具有分离效率高、能耗低、操作方便等优点,已经成为目前天然气深冷分离技术的主要分离方法之一。
膜分离技术是利用一种特殊的膜材料,将天然气中不同成分通过膜的选择性透过进行分离的一种工艺。
不同于吸附分离技术,膜分离技术是通过孔隙大小和孔隙形状的不同来实现分离的。
膜分离技术分为压力传递型和扩散传递型两类。
膜分离技术具有操作简便、占地面积小、能源损耗低等优势,因此也是目前天然气深冷分离技术的一种重要技术。
冷却分离技术是通过将天然气深冷,使其组分在低温环境下变成液态,然后进行分离的工艺。
常用的冷却分离技术包括膜式冷却分离、等温气液平衡分离、冷却凝固分离、液膜分离等。
不同冷却分离技术的应用基于原料气的成分、操作条件和要求等因素的不同。
总的来说,天然气深冷分离技术的发展对于提高气体分离、提纯技术的精度和效率有重要意义。
深冷制氮与变压吸附制氮比较研究

深冷制氮与变压吸附制氮比较研究摘要:氮气有着很高的应用率,结合社会工业发展实际情况及其表现出来的各种生产需求,制氮技术得到了很好的延伸。
以此为背景,采用何种技术进行优质且有较广应用范围的氮气的生产,目前已经被氮气生产领域视作实现进一步发展的重要目标之一,本文对深冷制氮与变压吸附制氮两种技术展开研究,分析各自的原理与工艺流程,并对它们作出相应的比较分析。
关键词:深冷制氮,变压吸附制氮,原理,工艺流程,比较1深冷制氮原理与工艺流程1.1深冷制氮原理考虑到空气中氮气和氧气两种气体之间的沸点存在差异,深冷制氮技术对高温蒸馏的方式加以采用,执行空气中氮气的分离作业。
根据化学理论可知,氮气与氧气的沸点分别为-196℃与-183℃,前者明显低于后者,所以,在执行高温蒸馏作业之时,氮气与氧气相比达到沸点要更为简单一些,时间也会更早,故在经过多次蒸发以及冷凝等表现出循环式特点的处理之后,便可以得到符合较高纯度要求的氮气。
而在完成对氮气的分离任务后,首先需要将其在精馏塔内存放,所以其纯度会由精馏塔塔板级别和精馏效率来决定。
1.2深冷制氮工艺流程业界人士与研究人员对深冷制氮技术作出了比较多的探索,进行的压力实验分析类型也较多,依次包括高压、中高压、重压以及全低压实验类型在内,在此基础上,总结出了压力不同的深冷制氮技术流程。
基于现代化物理和化学等相关技术飞速发展的有力支持,空分工艺技术表现出来的应用性能愈发得优异,既可以与不同压强相对应,执行对纯度不同的氮气的生产任务,实现对差异化市场需求的满足,又可以与设备等的具体等级进行结合,采取有效的辅助手段提升氮气生产效率,加快生产速度,在大中型低温空分装置的运行中,可以很好地将其作业效率提升。
理论层面上看,全低空分工艺的技术实施与氧气和氮气两种产品的不同属性相结合,对砌体进行循环式压缩处理,同时,将整个制氮流程划分为内压缩与外压缩两个主要的流程,前者的功能主要为在加压泵的运行支持下执行对精馏所得液态氧的处理任务,生产用户需要的气体,进一步地,在经过相应的复热处理之后将其提供给用户;后者则是进行低压氧气或氮气的生产,同时,借助于外置压缩机持续性地将氮气输送至用户端。
深冷空分
深冷空分制冷工艺流程概要1.深冷技术定义:深冷技术就是利用冷媒介质作为冷却介质,将淬火后的金属材料的冷却过程继续下去,达到远低于室温的某一温度(-196℃),从而达到发送金属材料性能的目的。
原理:深冷技术是近年来兴起的一种发送金属工件性能的新工艺技术,是目前最有效、最经济的技术手段。
在深冷加工过程中,金属中大量残余奥体转变为马氏体,特别是过饱和的亚稳定马氏体在从-196℃至室温的过程中会降低过饱和度,析出弥散、尺寸仅为20~60A并与基体保持共格关系的超微细碳化物,可以使马氏体晶格畸变减少,微观应力降低,而细小弥散的碳化物在材料塑性变形时可以阻碍位错运动,从而强化基体组织。
同时由于超微细碳化物颗粒析出后均匀分布在马氏体基体上,减弱了晶界脆化作用,而基体组织的细化既减弱了杂质元素在晶界的偏聚程度,又发挥了晶界强化作用,从而改善了工模具的性能,使硬度、抗冲击韧性和耐磨性都显著提高。
深冷技术的改进效果不仅限于工作表面,它渗入工件内部,体现的是整体效应,所以可对工件进行重磨,反复使用,而且对工件还有减少淬火应力和增强尺寸稳定性的作用。
2.空分技术定义:简单地说,就是用来把空气中的各组份气体分离,生产氧气、氮气和氩气的一套工业设备。
还有稀有气体氦、氖、氩、氪、氙、氡等空气分离的几种方法1、低温法(经典,传统的空气分离方法)压缩膨胀液化(深冷)精馏低温法的核心2、吸附法:利用固体吸附剂(分子筛、活性炭、硅胶、铝胶)对气体混合物中某些特定的组分吸附能力的差异进行的一种分离方法。
特点:投资省、上马快、生产能力低、纯度低(93%左右)、切换周期短、对阀的要求或寿命影响大。
3、膜分离法:利用有机聚合膜对气体混合物的渗透选择性。
穿透膜的速度比快约4-5 倍,但这种分离方法生产能力更低,纯度低(氧气纯度约25%~35%)获得低温的方法(1)绝热节流(2)相变制冷(3)等熵膨胀3.工艺流程1.净化系统—2.压缩—3.冷却—4.纯化—5.分馏(制冷系统,换热系统,精馏系统)液体:贮存及汽化系统;气体:压送系统;○净化系统:除尘过滤,去除灰尘和机械杂质。
变压吸附制氧与传统深冷法制氧的安全性比较
变压吸附空分制氧始创于 2 0世纪 印 年代初 , 并于 7 0年代 实现工业化生产。在此之前 , 统的工业 空分 装置 大部分采 用 传 深冷法制氧。 变压吸附是通过压力的变化而使混合气体 在吸附剂 中吸附 和脱 附交替进行 的循环过程 , 按照脱附方式的不同 , 变压吸附空
・
22・ 6
广 州化 工
21 00年 3 第 8期 8卷
变 压 吸 附 制 氧 与 传 统 深 冷 法 制 氧 的 安 全 性 比较
张丽 霞
( 江省 安全 工程 与技 术研 究重 点 实验 室 ,浙江省 安全 生产科 学研 究所 ,浙江 浙 杭 州 30 1 ) 10 2
摘 要 : 1 年来, 近 0 变压吸附制氧法发展迅速, 其在氧气纯度要求不高、 规模不大的用氧场合很有优势, 被迅速普及。本文通
过比较两种 主要工业制氧方法——深冷法制氧 和真空变压 吸附制 氧法 的工 艺特 点 , 出在一定 的用氧场合 , 指 变压吸附制氧法在安全 性和可靠性上有着更大 的优势 。
关键 词 : 真空变压吸附;PA 制氧; VS; 安全性
Co p rs n o e urt e we n Va uu e s e S n m a io fS c iy b t e c m Pr sur wi g
te e a e s h s ra .
Ke r s:v c u p e s r wi g a s r to y wo d a u m r s u e s n d o in;VPS p A;o y e x g n—ma n kig;s c rt e法发展 迅速 , 在灵活 、 其 多变 的用 氧场合 中很有优势 , 被迅速普及 。与传统深冷 法制氧相 比 , 两种 制氧法各有优点 , 但在制氧规模 小于 10 0 h 标 准状态下 ) 50 m / ( 、 氧气纯度要求不高 的场合 , 电炉 炼钢 、 如 有色金 属冶炼 、 璃加 玻 工、 甲醇 生产 、 碳黑生产 、 化肥造气 、 化学 氧化过程 、 纸浆漂 白、 污 水处理 、 生物发酵 、 水产养 殖 、 医疗和军事等诸多领域 , 变压吸 附
vocs深冷冷凝回收工艺简介
vocs深冷冷凝回收工艺简介标题:VOCs深冷冷凝回收工艺简介引言:挥发性有机化合物(Volatile Organic Compounds,简称VOCs)是一类在常温下易挥发的有机化学物质,其大量排放对环境和人体健康带来了严重的影响。
为了有效控制和减少VOCs的排放,深冷冷凝回收工艺被广泛应用于工业生产过程中。
本文将介绍VOCs深冷冷凝回收工艺的基本原理、关键技术和应用案例,以帮助读者深入了解该工艺及其在环境保护中的重要性。
第一节:VOCs深冷冷凝回收工艺的基本原理1.1 VOCs的定义和特点1.2 深冷冷凝回收工艺的原理和作用机制1.3 工艺流程和基本组成元件第二节:VOCs深冷冷凝回收工艺的关键技术2.1 深冷冷凝器的设计和选择2.2 温度和压力控制技术2.3 冷却介质的选择和处理2.4 废气流量计量和监测技术第三节:VOCs深冷冷凝回收工艺的应用案例3.1 石化行业中的VOCs深冷冷凝回收应用3.2 印刷工业中的VOCs深冷冷凝回收应用3.3 汽车涂装行业中的VOCs深冷冷凝回收应用第四节:我对VOCs深冷冷凝回收工艺的观点和理解4.1 对该工艺的优点和潜力的认识4.2 对改进和进一步发展的建议4.3 对环境保护和可持续发展的重要性的认识结论:VOCs深冷冷凝回收工艺作为一种有效的VOCs控制技术,在工业生产中起着重要的作用。
通过对该工艺的深入探讨,我们可以更好地理解其基本原理、关键技术和应用案例,并认识到其在环境保护和可持续发展中的关键作用。
为了更好地应对VOCs排放问题,我们应该不断改进和发展该工艺,并加强环保意识,推动可持续发展的目标。
字数:3315字。
制氧系统中深冷空气分离技术的运用探讨
制氧系统中深冷空气分离技术的运用探讨摘要:随着现代社会经济发展速度不断加快,氧气在各行业中的作用得以凸显,并且需求量也逐渐开始加大。
在现代工业以及医疗产业中,氧气所具备应用优势也得到凸显。
因此,研究高纯度制氧技术,已经成为现代氧气制造企业所关注的重点。
深冷空气分离法一般情况下能够较好应用于我国制氧企业中,尤其是部分纯度要求较高的大型空气分离技术方面。
本文研究深冷空气分离制氧特点,针对制氧系统中深冷空气分离技术的运动进行深入性探究,以期为现代制氧企业对氧气的制造和提取提供一定参考。
关键词:制氧系统;深冷空气分离技术;运用引言深冷空气分离法作为现代制氧企业最为常见制氧方式之一,也被称为低温精馏法。
从本质上来说,深冷空气法属于一种气体液化技术,研究人员根据空气中各组分沸点的不同,对空气中各组分采取连续多次的部分蒸发和冷凝后获取所需要的纯净氧气、氮气或者是稀有气体。
现代医学和工业行业发展,离不开氧气。
因此,如何制备出高纯度氧气,是现代科学研究的重要课题。
1深冷空气分离制氧的特点1.1对设备材料要求高制氧人员在对空气进行液化处理时,需要采用空气体积压缩及热交换的方式。
因此,制氧企业会对制氧设备的热传导材料提出较高的要求,制造低温设备材料时,需要选用较强耐压能力,并且接口焊接要求较高合金材料。
为防止外源热量传入,选用的热传导材料需要安装保冷箱,设备管道需要采用热绝缘性较为良好的材料对其进行包裹。
此外,保冷箱的填充物则需要选用一些热传导较为惰性的材料。
对此,我们需要注意的是,设备材料不可选用碳钢,这类材料较为脆弱并且无法承担强大的压力,导致制氧设备在运作时出现故障。
1.2杂质组分易产生问题空气中含有一定二氧化碳以及水蒸气,二者凝固点较高,氧气还未被液化时,他们就会逐渐开始成为固态。
在深冷空气分离制氧设备进行运作时,空气中的二氧化碳及水蒸气等杂质组分对管道及阀门出入口进行堵塞,等到精馏时,液态氧无法被分流出来,会对装置的正常运作产生影响。
- 1、下载文档前请自行甄别文档内容的完整性,平台不提供额外的编辑、内容补充、找答案等附加服务。
- 2、"仅部分预览"的文档,不可在线预览部分如存在完整性等问题,可反馈申请退款(可完整预览的文档不适用该条件!)。
- 3、如文档侵犯您的权益,请联系客服反馈,我们会尽快为您处理(人工客服工作时间:9:00-18:30)。
深冷处理的优点及最新进展.txt30生命的美丽,永远展现在她的进取之中;就像大树的美丽,
是展现在它负势向上高耸入云的蓬勃生机中;像雄鹰的美丽,是展现在它搏风击雨如苍天之
魂的翱翔中;像江河的美丽,是展现在它波涛汹涌一泻千里的奔流中。深冷处理的优点及最
新进展
深冷处理的优点及最新进展
所谓冷处理,一般将0~100℃的冷处理定义为普通冷处理,将-130℃以下的处理称为深冷处
理,它是最新的强韧化处理工艺之一。深冷处理按照工艺可分为深冷急热法和冷热循环法两
种。冷热循环稳定化处理是先将零件冷却到—40℃~—90℃或者更底的温度,保温一定时间,
然后再把零件加热到不致降低零件机械性能的某一温度(通常为80℃~190℃),保温一段时
间并重复多次这种循环过程。“冷处理急热法”是日本大和久重雄提出的方法,该方法是将
工、模具淬火后,不立即进行冷处理,先水浴后再置于处理槽当中于—80℃或—180℃下处理。
即—80℃为普通冷处理;—180℃为深冷处理,保温时间按每英寸体积为1小时计算。保温后
取出放入热水中快速加热。
在美国、前苏联、日本等国,不但把深冷技术用于高速钢、轴承钢、模具钢,以提高材料的
耐磨性和强韧性,进而提高工件的整体使用寿命,同时还利用深冷技术对铝合金、铜合金、
硬质合金、塑料、玻璃等进行深冷改性。改善均匀性、稳定尺寸、减小变形、提高使用寿命。
⑵ 深冷处理机理
钢的淬火过程就是使钢获得马氏体的过程,而淬火不能使钢中奥氏体全部转变为淬火组织,
各种钢材热处理后都有部分奥氏体残存,其残存量随钢种及加热温度不同而变化,同时还有
一定量的残余应力存在。它们存在对工件的使用性能会产生或多或少的影响,深冷处理能使
钢中奥氏体进一步转变为马氏体,并能改善和消除钢中残余应力的分布,析出更多的细小碳
化物,从而起到弥散强化的作用,对无相变材料能使晶界发生畸变,从而增强基体性能。
⑶ 深冷处理的优点
SSZ处理的最大优点是因γR的马氏体化使得工件硬度升高,从而提高了工件的耐蚀磨碎性
能。同时,防止时效变形,帕伦博士的研究表明,经深冷处理的工件具有下述优点:
① γR在实质上已近乎完全转变为M;
② 与未经SSZ处理的工件或经普通冷处理之工件相比耐磨性得以提高;
③ 进行了组织的细化和细小碳化物的析出过程;
④ 硬度与CSZ处理工件几乎相同。
⑷ 深冷处理注意事项
① 不得将淬火时未冷至室温的工件直接放入深冷装置,以免开裂。
② 冷至室温的工件应尽快放入深冷装置,以免使奥氏体稳定化,影响处理效果。
③ 一般钢深冷处理前不应回火,高速钢可在回火一次后进行深冷处理。
深冷处理研究的最新进展
近十多年以来特别是近两年来,国内以甘肃理工大学、河北工学院和中南工业大学等高校为
首的科研机构一直致力于对工具钢、模具钢、刃具钢、量具钢以及有色金属的深冷处理的工
艺及机理研究,并取得了一定的成果,部分成果已经应用于生产,还有一些成果处于中试阶
段。
如甘肃工业大学对高速钢W18Cr4V深冷后发现,不仅合金的强韧性、耐磨性有所提高,用其
制造的工模具使用寿命可以提高2~5倍,在解释这一现象时,不仅仅局限于残余奥氏体向马
氏体转变、晶粒细化、析出弥散的碳化物等传统的机理,而是提出了自己全新的、更加详细
的解释。
①模具材料在多次冲击条件下的韧性与残余奥氏体的形态及分布有关,刀具材料的强度与红
硬性与马氏体脱溶微细碳花物有关。
②通过TEM观察证明,深冷处理有弥散碳化物分布在马氏体的挛晶带上,其直径在3~10nm,
该碳化物的晶体结构为M6C型。
③通过X衍射晶体结构分析发现,深冷处理后马氏体晶格的轴比降低,这也证明了马氏体发
生了碳化物脱溶分解。
④借助自行设计的低温动态组织计算机处理系统观察到金属材料在深冷处理过程中残余奥氏
体向马氏体原位动态组织转变,并且残余奥氏体向马氏体转变时存在孕育时间,转变首先发
生在试块的边缘附近,然后向内部深处发展。在-196℃有明显的等温马氏体转变。同时还发
现深冷处理后的激烈升温阶段也发生少量的马氏体转变,但转变速度较慢,转变量较少。
⑤通过正电子湮没试验发现深冷处理后点缺陷密度有所变化。黑色金属在深冷处理后的点缺
陷密度有所上升,有色金属在深冷处理后的点缺陷密度有所下降。点缺陷密度的变化对金属
材料的性能有很多的影响,如有色金属铜合金经过深冷处理的空位密度下降,将使材料的电
阻率有所下降,强度有所上升,密度增加等。