面向制造和装配的产品设计
浅析DFMA在家具产品开发中的应用

0 0 6 } F u r n i t u r e
E 翟诹幽
和 装 配 的设 汁 (De s
s e n
,
【 ≯
Fu
rn
—
。
’
”
o o
,
12
-
引
剐
札
20 。 4
ቤተ መጻሕፍቲ ባይዱv 蝴
No 1
.
ig n
fo r
,
Ma
n u
fa
c
tu
r
in g
a n
d
As
.
能确 保零 件 快 速 有 效 地 进 行装 配
向 制 造 的 没 汁 ( D F M ) 的核 心 完整 的 D F M
尔 景
z…
q - 上卜
昂
o e
I栅
Fu r n i t u r e 201 4 Vo l 35 No. 1
浅析 D F MA在 家具产 品开发 中的应用
陈伟伟 , 刘春 兵
( 1 .南京林业大学家具与工业设计学院 , 南京 2 1 0 0 3 7 ;2 .震旦( 中国 ) 有限公司设计中心 , 上海 2 0 1 8 1 8 )
,
DFA
是指
产 品设 计 需 要 具 有 良好 的 可 装 配 性 使 得 装 配 T 序
程 的核 心 技 术 在 并行 的 开 发 流程 巾发 挥着 重 并行 l : 要 作用
、 。
品 外 观 功 能 和可 靠性 等前 提 下 通 过 提 高产 品 的
、 ,
如图 l 所 示 这 是 并 行 T 程 所 采 川 的产 品 )干
,
‘
可 制 造 性 和 可 装 配 性 从 而 保证 以 更 低 的 成 本 更
公差分析1
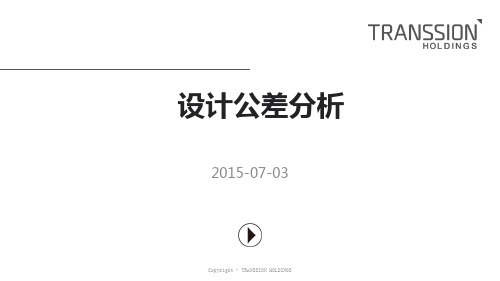
T T T T
1 2 3
2
2
2
T
i 1
n
2
i
让我们用 WC 和 RSS来计算这些变量,然后做个比较!
Copyright © TRANSSION HOLDINGS
第六步 – 计算变异, WC
极值法 (WC)
1. 确定组装要求
•
间隙变量是个体公差的总和.
n
2. 建立封闭尺寸链图 3. 转换名义尺寸,将公差 转成对称公差 4. 按要求计算名义尺寸
• •
• • • • • •
装配要求 换壳;无固定的配对组装(多套模具或模穴)
功能要求 电子方面;PWB与弹片的可靠接触 结构方面;良好的滑动结构,翻盖结构,或机构装置 品质要求 外观;外壳与按键之间的间隙 其他; 良好的运动或一些奇怪的杂音,零件松动
5. 确定公差分析的方法
6. 按要求计算变异
Copyright © TRANSSION HOLDINGS
第五步 – 公差分析方法的定义
1. 确定组装要求
怎样计算间隙的变异 ?
一般应用比较多的公差分析模式是: 1. 极值法 (Worst Case),简称WC
– – – – 验证 100 % 性能 简单并且最保守的手法 用于零件数量少的情况 用于产量不大的零件
2. 建立封闭尺寸链图 3. 转换名义尺寸,将公差 转成对称公差 4. 按要求计算名义尺寸
200-204
Copyright © TRANSSION HOLDINGS
205-209
变异的一般分布图
正态分布 normality distribution
100
双峰分布(非正态分布)
并行工程和传统串行工程两者的比较
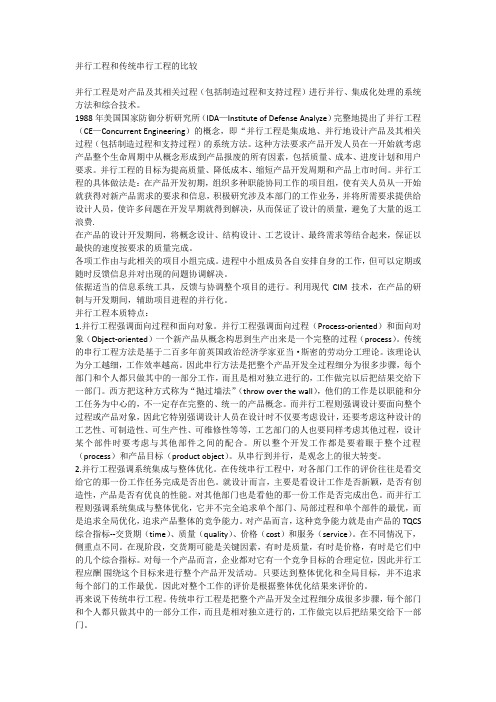
并行工程和传统串行工程的比较并行工程是对产品及其相关过程(包括制造过程和支持过程)进行并行、集成化处理的系统方法和综合技术。
1988年美国国家防御分析研究所(IDA—Institute of Defense Analyze)完整地提出了并行工程(CE—Concurrent Engineering)的概念,即“并行工程是集成地、并行地设计产品及其相关过程(包括制造过程和支持过程)的系统方法。
这种方法要求产品开发人员在一开始就考虑产品整个生命周期中从概念形成到产品报废的所有因素,包括质量、成本、进度计划和用户要求。
并行工程的目标为提高质量、降低成本、缩短产品开发周期和产品上市时间。
并行工程的具体做法是:在产品开发初期,组织多种职能协同工作的项目组,使有关人员从一开始就获得对新产品需求的要求和信息,积极研究涉及本部门的工作业务,并将所需要求提供给设计人员,使许多问题在开发早期就得到解决,从而保证了设计的质量,避免了大量的返工浪费.在产品的设计开发期间,将概念设计、结构设计、工艺设计、最终需求等结合起来,保证以最快的速度按要求的质量完成。
各项工作由与此相关的项目小组完成。
进程中小组成员各自安排自身的工作,但可以定期或随时反馈信息并对出现的问题协调解决。
依据适当的信息系统工具,反馈与协调整个项目的进行。
利用现代CIM技术,在产品的研制与开发期间,辅助项目进程的并行化。
并行工程本质特点:1.并行工程强调面向过程和面向对象。
并行工程强调面向过程(Process-oriented)和面向对象(Object-oriented)一个新产品从概念构思到生产出来是一个完整的过程(process)。
传统的串行工程方法是基于二百多年前英国政治经济学家亚当·斯密的劳动分工理论。
该理论认为分工越细,工作效率越高。
因此串行方法是把整个产品开发全过程细分为很多步骤,每个部门和个人都只做其中的一部分工作,而且是相对独立进行的,工作做完以后把结果交给下一部门。
DFMA在航空工业里的理解利用

DFMA在航空工业里的理解利用1DFMA技术内涵面向制造与装配的设计与精益制造、质量工程等一样,是一种设计理念。
DFMA强调在产品设计的各个阶段,对产品加工、装配直至后续维护等实行综合设计和优化,提升产品的可制造性、可装配性、可维护性等。
产品的可制造性、可装配性在我国的工业界一般称为结构工艺性,包括面向机加、铸造、焊接、压力成型等各种单元加工的制造工艺性以及在产品部装、总装阶段的装配工艺性、装配准确性和装配协调性等。
实施DFMA的基本思想是通过减少零件数量、简化产品结构,实现减少单个零件的加工时间和总的装配时间,从而减少整个制造成本的目的。
DFMA适用于任何企业和产品,尤其对飞机等大型复杂产品能够起到显著作用。
实施DFMA理念的企业强调在设计过程中采用并行工程方式,以保证产品的质量能够由设计师及其他开发人员共同实现和保证。
所以DFMA也被认为是并行工程的核心技术之一。
2DFMA技术的分类DFMA强调在设计的各个阶段,尤其是设计的早期,通过建立并行工程团队,使产品设计人员能够对关于材料选择、制造工艺、装配过程、维护过程等实行同步的设计与优化,以减少制造和装配时间,从而降低生产成本,提升产品质量和可靠性。
DFMA根据所达到的目标,可划分为面向制造的设计(DesignforManufacture,DFM)、面向装配的设计(DesignforAssembly,DFA)、面向测试的设计(DesignforTesting,DFT)、面向服务的设计(DesignforService,DFS)、面向环境的设计(DesignforEnvironment,DFE)等。
其中DFM 是根据企业自身及供应商的工艺水平和制造水平,综合考虑零件的设计对零件制造过程中材料处理、加工成型、质量检验等环节的影响,通过对材料选择、结构设计、尺寸公差等的改进和优化,使零件能够在企业已有设备资源条件下,经济、高效、高质量地制造和生产。
采用DFM技术,能够在设计阶段对不同设计方案实行制造时间和成本的快速定量分析,比较与评价各种结构设计与工艺方案。
DFMA产品可制造和装配设计检查表汇编
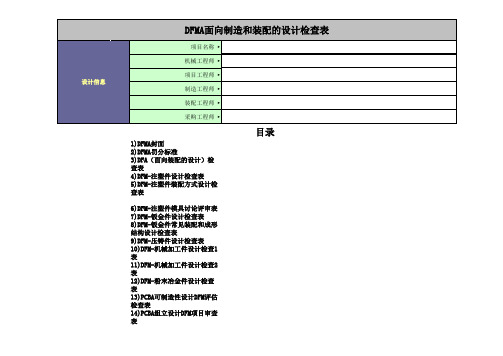
DFMA面向制造和装配的设计检查表
项目名称 ►
机械工程师 ►
项目工程师 ►
设计信息
制造工程师 ►
装配工程师 ►
采购工程师 ►
目录
1)DFMA封面
2)DFMA罚分标准
3)DFA(面向装配的设计)检
查表
4)DFM-注塑件设计检查表
5)DFM-注塑件装配方式设计检
查表
6)DFM-注塑件模具讨论评审表
7)DFM-钣金件设计检查表
8)DFM-钣金件常见装配和成形
结构设计检查表
9)DFM-压铸件设计检查表
10)DFM-机械加工件设计检查1
表
11)DFM-机械加工件设计检查2
表
12)DFM-粉末冶金件设计检查
表
13)PCBA可制造性设计DFM评估
检查表
14)PCBA组立设计DFM项目审查
表。
面向自动化装配的产品设计

面向自动化装配的产品设计面向自动化装配的产品设计有着广泛的应用领域,包括汽车制造、电子设备生产、机械设备生产等。
在这些领域中,自动化装配的产品设计需要考虑到生产效率的提高、质量的保证、工作人员的安全等因素。
本文将针对面向自动化装配的产品设计进行详细阐述。
首先,面向自动化装配的产品设计需要考虑到生产效率的提高。
在自动化装配生产线中,产品的设计应具有良好的可装配性。
这意味着产品的设计应简单明了,易于操作,并能够与其他组件高效地连接。
同时,产品的设计应考虑到生产线上的自动化设备,以便能够与这些设备无缝配合。
例如,产品的尺寸、形状应易于被自动化设备抓取、搬运和连接。
其次,面向自动化装配的产品设计需要考虑到质量的保证。
通过自动化装配可以减少人为错误,提高产品装配的一致性和准确性。
产品的设计应注重组件之间的质量控制,确保每个组件的尺寸、材料和性能都符合要求。
此外,产品的设计应考虑到装配过程中可能出现的问题,如组件之间的干涉、松动等,并采取相应的措施来解决这些问题。
最后,面向自动化装配的产品设计需要考虑到工作人员的安全。
自动化装配生产线通常包括诸如机械臂、传送带等设备,这些设备可能会对工作人员的安全构成威胁。
因此,在产品设计中应考虑到工作人员的操作空间和安全措施。
例如,产品的设计应具有圆滑的边缘和避免尖锐的零部件,以减少工作人员受伤的风险。
此外,产品的设计应易于维护和修理,以帮助工作人员更好地管理和维护装配设备。
总结起来,面向自动化装配的产品设计需要考虑到生产效率的提高、质量的保证和工作人员的安全。
为了实现这些目标,产品的设计应具备良好的可装配性、质量控制和安全性。
通过合理的产品设计,可以提高装配效率、降低生产成本并保证产品的质量和工作人员的安全。
产品全生命周期设计

产品全生命周期设计产品全生命周期设计2011年07月13日产品全生命周期设计机械产品的全生命周期设计是多学科融合的综合科学,并涉及许多新兴学科和现代先进技术。
探讨了机械产品全生命周期设计概念和思想、主要研究内容和涉及的学科前沿课题。
全生命周期设计的提出和建立是现代设计理论发展的产物,也将是机械设计发展的必然方向。
1、全生命周期设计的基本概念1.1、全生命周期产品的全生命周期与产品的寿命是不同的概念。
产品的全生命周期包括产品的孕育期(产品市场需求的形成、产品规划、设计)、生产期(材料选择制备、产品制造、装配)、储运销售期(存储、包装、运输、销售、安装调试)、服役期(产品运行、检修、待工) 和转化再生期(产品报废、零部件再用、废件的再生制造、原材料回收再利用、废料降解处理等) 的整个闭环周期。
而产品的寿命往往指产品出厂或投入使用后至产品报废不再使用的一段区间, 仅是全生命周期内服役期的一部分。
由于传统的产品功能和性能主要在服役期实现, 传统设计主要为产品的运行功能设计和产品的使用寿命以及近年来日益重视的产品自然寿命设计。
基于产品的社会效应, 全生命周期包括对产品的社会需求的形成, 产品的设计、试验、定型, 产品的制造、使用、维修以及达到其经济使用寿命之后的回收利用和再生产的整个闭环周期。
如图1所示, 机械的全生命周期涵盖全寿命期, 全寿命期涵盖经济使用寿命和安全使用寿命。
图1 全生命周期与全寿命期作为全生命周期的一个重要转折点, 产品报废一般有3 种判据: 功能失效、安全失效、经济失效。
1.2、全生命周期设计所谓全生命周期设计, 就是面向产品全生命周期全过程的设计, 要考虑从产品的社会需求分析、产品概念的形成、知识及技术资源的调研、成本价格分析、详细机械设计、制造、装配、使用寿命、安全保障与维修计划, 直至产品报废与回收、再生利用的全过程, 全面优化产品的功能ö性能 (F)、生产效率(T )、品质ö质量(Q )、经济性(C)、环保性(E) 和能源ö资源利用率(R ) 等目标函数,求得其最佳平衡点。
面向制造和装配的设计(DFMA)检查表
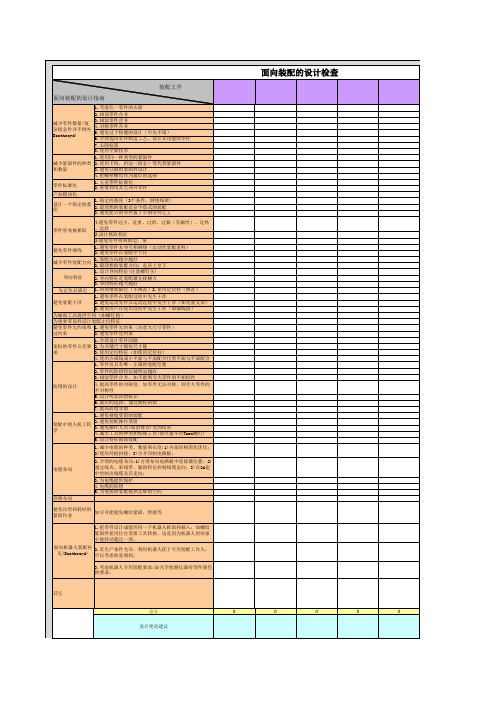
、过软
2.设计抓取特征 3.避免零件锋利的边、角
避免零件缠绕
1.避免零件本身互相缠绕(自动化装配进料) 2.避免零件在装配中卡住
减少零件装配方向
1.装配方向越少越好 2.最理想的装配方向:是从上至下
1.设计导向特征(注意螺钉头)
导向特征 2.导向特征是装配最先接触点
3.导向特征越大越好
先定位后固定 1.四周增加限位(不推荐)2.使用定位柱(推荐)
装配工序
面向装配的设计指南
1.考虑任一零件的去除
2.相邻零件合并
减少零件数量(复 杂钣金件亦不例外 Boothroyd)
3.相似零件合并 4.对称零件合并 5.避免过于稳健的设计(可先不填)标签 8.使用全新技术
1.使用同一种类型的紧固件
减少紧固件的种类 2.使用卡钩、折边(钣金)等代替紧固件
3.为电缆提供保护 4.电缆的防错 5.为电缆的装配提供足够的空间
管路布局
避免昂贵和耗时的 紧固作业
如尽可能避免螺纹紧固,焊接等
1.把零件设计成能用同一个机器人抓取和插入:如螺纹 紧固件使用往往需要工具转换,这是因为机器人肘结很 少能转动超过一周。
面向机器人装配补 2.若生产条件允许,利用机器人优于专用装配工作头, 充(Boothroyd) 可以考虑放宽规则。
和数量
3.避免分散的紧固件设计
4.把螺栓螺母作为最后的选择
零件标准化
1.五金零件标准化 2.重复利用其它项目零件
产品模块化
设计一个稳定的基 座
1.稳定的基座(3个条件,例绕线架) 2.最理想的装配是金字塔式的装配 3.避免把大的零件置于小的零件之上
1.避免零件过小、过重、过滑、过黏(有磁性)、过热
- 1、下载文档前请自行甄别文档内容的完整性,平台不提供额外的编辑、内容补充、找答案等附加服务。
- 2、"仅部分预览"的文档,不可在线预览部分如存在完整性等问题,可反馈申请退款(可完整预览的文档不适用该条件!)。
- 3、如文档侵犯您的权益,请联系客服反馈,我们会尽快为您处理(人工客服工作时间:9:00-18:30)。
iPhone iPhone利润分配图利润分配图
品牌
产品设计
产品制造
iPhone iPhone利润分配利润分配利润分配::
苹果获得苹果获得58.5%58.5%58.5%的利润的利润的利润;;
中国台湾和中国工人仅仅分别获得中国台湾和中国工人仅仅分别获得0.5%0.5%0.5%和和1.8%1.8%的利润的利润的利润;;代价代价::为什么苹果
能获得暴利能获得暴利??而我们仅获得微薄利润得微薄利润??
跳楼中毒环境污染
企业在产
业链中的位置决定了企业的利润
微笑曲线微笑曲线::
产品设计是整个产业链的核心产品设计是整个产业链的核心,,产生最多的附加价值产生最多的附加价值;;
产品制造处于整个产业链的底端产品制造处于整个产业链的底端,,产生最少的附加价值产生最少的附加价值;;
产品设计
技术研发
品牌品牌、、渠道物流物流、、服务
产品制造
附
加价值
1.1.产品设计决定了产品成本产品设计决定了产品成本
产品设计阶段的成本仅仅占整个产品开发投入成本的产品设计阶段的成本仅仅占整个产品开发投入成本的5%5% 产品设计决定了产品设计决定了75%75%75%的产品成本的产品成本
产品设计在很大程度上决定了材料产品设计在很大程度上决定了材料、、劳动力和管理的成本劳动力和管理的成本,,如果没有产
品设计的优化品设计的优化,,材料材料、、劳动力和管理对于降低产品成本影响很小
为什么说产品设计决定了为什么说产品设计决定了75%75%75%的产品成本的产品成本的产品成本??
产品设计决定了零件的材料
产品设计决定了零件的制造和装配工艺 产品设计决定了零件的简单与复杂度 产品设计决定了产品结构的简单与复杂度 产品设计决定了产品的修改次数
产品设计决定了产品的不良率
2. 2. 产品设计决定了产品质量产品设计决定了产品质量
质量从哪里来?
质量是检验出来的?质量是制造出来的?质量是设计出来的? Taguchi :产品质量首先是设计出来的产品质量首先是设计出来的,,然后才是制造出来的然后才是制造出来的。
德国人对质量的定义德国人对质量的定义::优秀的产品设计加上精致的制造优秀的产品设计加上精致的制造。
二八原则二八原则::80%80%左右的产品质量问题是由设计造成的左右的产品质量问题是由设计造成的左右的产品质量问题是由设计造成的。
3. 3. 产品设计决定了产品的开发周期产品设计决定了产品的开发周期
事后把关,挑出不合格;仅仅是实现设计要求;设计决定产品基因
DFM (Design for Manufacturing)
DFA (Design for Assembly)
DFMA
今天才知道为什么之前那么好的设计没有中标今天才知道为什么之前那么好的设计没有中标,,
那是因为没有认真的去考虑用户的需求
二、DFX (Design for X )
1.1.传统产品开发模式传统产品开发模式传统产品开发模式::定义定义::
产品开发过程分为产品设计阶段和产品制造阶段产品开发过程分为产品设计阶段和产品制造阶段,,分别由机械工程师和
制造工程师负责制造工程师负责。
在产品设计阶段在产品设计阶段,,机械工程师关注的是如何实现产品的功能机械工程师关注的是如何实现产品的功能、、外观和可靠性等要求靠性等要求,,而不去关心产品是如何制造而不去关心产品是如何制造、、如何装配的如何装配的;;
当机械工程师完成产品设计后当机械工程师完成产品设计后,,由制造工程师进行产品的制造和装配由制造工程师进行产品的制造和装配,,当然当然,,制造工程师也不关心产品的功能制造工程师也不关心产品的功能、、外观和可靠性等要求外观和可靠性等要求;;
1.1.传统产品开发模式传统产品开发模式传统产品开发模式::开发流程开发流程::
1.1.传统产品开发模式传统产品开发模式传统产品开发模式::特点特点::
抛墙式设计抛墙式设计,,我们设计我们设计,,你们制造你们制造,,设计不考虑制造的要求; 反反复复修改直到把事情做对反反复复修改直到把事情做对;;
产品开发成本高产品开发成本高,,开发周期长开发周期长,,产品质量低产品质量低;;
1.1.传统产品开发模式传统产品开发模式传统产品开发模式::
产品设计
产品制造
1.1.传统产品开发模式传统产品开发模式传统产品开发模式::产品设计的精髓产品设计的精髓::
2. DFMA 概念概念::
面向制造和装配的产品设计面向制造和装配的产品设计((Design for Manufacturing and
Assembly, 简称DFMA ):):在考虑产品外观在考虑产品外观在考虑产品外观、、功能和可靠性等前提下功能和可靠性等前提下,,通过提高产品的可制造性和可装配性,从而保证以更低的成本从而保证以更低的成本、、更短的时间和更高的质量进行产品设计时间和更高的质量进行产品设计。
可制造性可制造性::制造工艺对零件的设计要求制造工艺对零件的设计要求,,确保零件容易制造确保零件容易制造、、制造成本低、质量高等质量高等。
可装配性可装配性::装配工序和装配工艺对产品的设计要求装配工序和装配工艺对产品的设计要求,,确保装配效率高确保装配效率高、、装配不良率低装配不良率低、、装配成本低装配成本低、、装配质量高等装配质量高等。
DFMA 是一种设计思想
3. DFMA 的特点的特点::
我们设计我们设计,,你们制造你们制造,,设计充分考虑制造的要求设计充分考虑制造的要求;; 第一次就把事情做对第一次就把事情做对;;
4. DFMA 开发流程:
定义产品规格概念设计量产
测试产品装配产品制造样品制作DFMA讨论材料和工艺选择成本分析DFMA设计小批量试产DFMA
5. DFMA 是一项团队工作
测试工程师装配工程师
制造工程师
项目工程师
机械工程师
DFMA团队
四、DFMA的价值
一.产品设计的重要性 二.Design for X 三.DFMA的介绍 四.DFMA的价值 五.DFMA的实施
DFMA
22
四、DFMA的价值
DFMA
缩短产品上市时间
减少产品维修次数 减少装配不良率
减少单独的紧固件
减少装配工序 减少装配时间
减少产品成本 减少装配成本
减少零件数量
0%
10%
20%
30%
40%
50%
60%
70%
数据来源于BDI DFMA
DFMA的价值
23
四、DFMA的价值
DFMA
减少产品设计修 改
缩短产品开发周 期
价值1
价值2
DFMA
价值4
价值3
提高产品质量
降低产品成本
24
四、DFMA的价值
DFMA
1. 减少产品设计修改
产品具有很好的可制造性和可装配性,产品制造和装配顺利,设计修改少 把设计修改集中在产品设计阶段,第一次就把事情做对 产品设计阶段设计修改灵活性高,修改容易;产品制造和装配阶段以及量 产设计修改灵活性低,修改困难
25
四、DFMA的价值
DFMA
2. 缩短产品开发周期
第一次就把事情做对,相比传统产品开发,缩短39%的开发周期 DFMA要求投入较多的时间和精力在产品设计之中
26
四、DFMA的价值
3. 降低产品成本
在设计阶段进行成本分析,降低产品成本; 减少设计修改,降低成本;
DFMA设计修改少 DFMA把设计修改集中在设计修改费用最少的产品设计阶段
DFMA
27
四、DFMA的价值
3. 降低产品成本
简化产品设计,降低产品成本;
DFMA
原始设计
优化设计
最终设计
28
四、DFMA的价值
3. 降低产品成本
简化产品设计,降低产品成本;
DFMA
29
四、DFMA的价值
3. 降低产品成本
简化零件设计,降低零件制造成本; 减少装配工序和装配时间,降低装配成本; 降低产品不良率,减少成本浪费;
DFMA
30
四、DFMA的价值
DFMA
4. 提高产品质量
通过DFMA,产品具有很好的可制造性和可装配性,产品设计在产品开 发阶段就得到了优化和完善,因此避免了产品在后期制造和装配产生中 的质量问题,大大提高了产品的质量
错误的设计
零件扭曲和缩水
正确的设计
31
1.1.转变思想转变思想
机械工程师机械工程师::“设计不考虑制造和装配的需求设计不考虑制造和装配的需求””“设计充分考虑制造和装配的需求制造和装配的需求””
企业企业::“重制造重制造,,轻设计轻设计””“轻制造轻制造,,重设计重设计””
2. 2. 建立建立DFMA 团队
DFMA 团队团队::机械工程师机械工程师,,项目工程师项目工程师,,制造工程师制造工程师,,装配工程师装配工程师,,测试工程师等工程师等。
3. 3. 实施实施DFMA 开发流程
4. 4. 进行进行DFMA 培训
5. 5. 把工程师派到工厂去把工程师派到工厂去
6. 6. 使用使用DFMA 检查表
DFMA 谢谢!。