铝合金熔体的熔剂精炼
铝合金精炼剂生产过程

铝合金精炼剂生产过程
铝合金精炼剂的生产过程主要包括以下步骤:
1. 原料准备:选用高纯度的铝、硅、锂等金属物质作为主要原料。
同时根据配方要求,还需要准备其他辅助原料,如碳素材料、气体等。
2. 混合与粉碎:将所需的原料按照一定的比例混合,并进行粉碎处理,使其颗粒度均匀。
3. 氧化还原反应:将混合好的原料置于高温高压的反应器中,加入还原气体(如氢气),进行氧化还原反应。
这一步骤主要是将金属物质氧化成相应的金属离子,同时还原其中的杂质。
4. 过滤与脱水:经过氧化还原反应后,得到的金属溶液需要进行过滤和脱水处理,去除其中的杂质和水分。
5. 沉淀与分离:将过滤好的金属溶液通过控制温度和pH值等条件,使其中的金属离子逐渐沉淀生成金属化合物。
然后通过离心、过滤等步骤对沉淀物与溶液进行分离。
6. 干燥与烧结:将分离好的金属沉淀物进行干燥,并加热至一定温度进行烧结,使其形成固体的金属合金精炼剂。
7. 包装与贮存:将金属合金精炼剂进行包装,并进行贮存,以保证其质量和稳定性。
需要注意的是,不同厂家和产品的制造工艺可能会有所差异,以上只是一般的生产流程,具体的步骤和条件可能会有所不同。
铝合金精炼的原理

铝合金精炼的原理铝合金精炼是提高铝合金质量和性能的过程,通过调整铝合金的成分和组织结构,去除杂质和非金属夹杂物,以提升其力学性能、耐热性和耐腐蚀性。
铝合金精炼的原理主要包括氧化物的处理、过滤和除杂、合金组织调整等环节。
首先,铝合金精炼的过程中要处理氧化物。
铝在空气中容易与氧气发生反应生成氧化铝,而氧化铝的存在会影响铝合金的性能。
因此,要通过适当的处理方法将氧化物去除或转化。
常用的方法有气氛调整、熔渣法和焙烧法等。
其中,气氛调整是在熔炼过程中通过调整炉内气氛(如减压、加氢等)来去除氧化物,熔渣法是添加合适的熔渣来吸收和分离氧化物,焙烧法是将氧化物经过高温烘烤使其转化成可溶性的化合物,从而实现去除氧化物。
其次,铝合金精炼的过程中要进行过滤和除杂。
铝合金中常常含有各种杂质和非金属夹杂物,如气泡、夹杂金属、氧化物等。
这些杂质和非金属夹杂物会影响铝合金的力学性能和加工性能,因此需要通过过滤和除杂的方法将其去除。
过滤一般采用陶瓷过滤器,可以通过筛选的方式去除粗大的杂质颗粒;除杂一般采用捞渣(将熔融金属表面的熔渣捞掉)和改变金属的温度和分子结构等方法,以获得较纯净的铝合金。
最后,铝合金精炼的过程中要进行合金组织的调整。
合金组织的好坏直接影响着铝合金的性能。
常用的调整方法包括相成分的改变、相变和再结晶等。
相成分的改变可以通过添加合适的合金元素来改变合金的化学成分,进而改变合金的力学性能和耐腐蚀性能。
相变是指合金中两种或多种相的相互转变,常用的相变有固溶体相变和析出相变等,通过相变可以调整合金的硬度、强度和导热性等性能。
再结晶是指在加热过程中,金属材料的晶粒重新长大,消除变形应力,得到均匀细小的晶粒,从而提高材料的韧性和延展性。
总的来说,铝合金精炼的原理是通过处理氧化物、过滤和除杂、合金组织调整等环节来提高铝合金的质量和性能。
这些环节相互作用,综合运用可以获得高质量的铝合金。
铝合金精炼技术的不断改进和发展,有助于满足不同领域对高性能铝材料的需求,推动着铝合金产业的进步和发展。
铸造铝合金的熔炼工艺
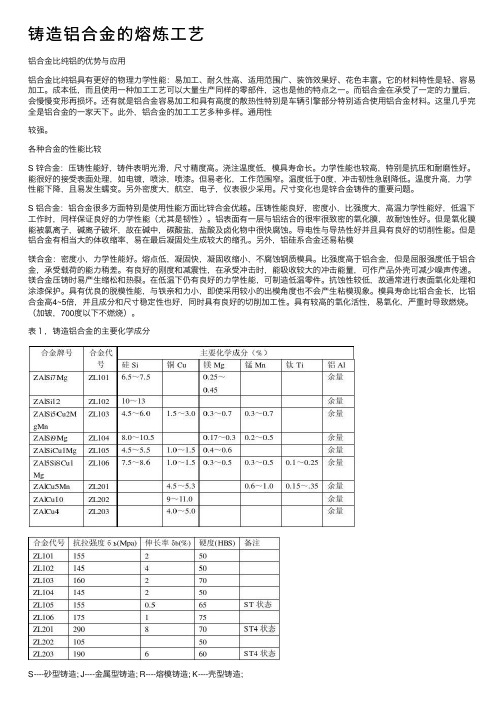
铸造铝合⾦的熔炼⼯艺铝合⾦⽐纯铝的优势与应⽤铝合⾦⽐纯铝具有更好的物理⼒学性能:易加⼯、耐久性⾼、适⽤范围⼴、装饰效果好、花⾊丰富。
它的材料特性是轻、容易加⼯。
成本低,⽽且使⽤⼀种加⼯⼯艺可以⼤量⽣产同样的零部件,这也是他的特点之⼀。
⽽铝合⾦在承受了⼀定的⼒量后,会慢慢变形再损坏。
还有就是铝合⾦容易加⼯和具有⾼度的散热性特别是车辆引擎部分特别适合使⽤铝合⾦材料。
这⾥⼏乎完全是铝合⾦的⼀家天下。
此外,铝合⾦的加⼯⼯艺多种多样。
通⽤性较强。
各种合⾦的性能⽐较S 锌合⾦:压铸性能好,铸件表明光滑,尺⼨精度⾼。
浇注温度低,模具寿命长。
⼒学性能也较⾼,特别是抗压和耐磨性好。
能很好的接受表⾯处理,如电镀,喷涂,喷漆。
但易⽼化,⼯作范围窄。
温度低于0度,冲击韧性急剧降低。
温度升⾼,⼒学性能下降,且易发⽣蠕变。
另外密度⼤,航空,电⼦,仪表很少采⽤。
尺⼨变化也是锌合⾦铸件的重要问题。
S 铝合⾦:铝合⾦很多⽅⾯特别是使⽤性能⽅⾯⽐锌合⾦优越。
压铸性能良好,密度⼩,⽐强度⼤,⾼温⼒学性能好,低温下⼯作时,同样保证良好的⼒学性能(尤其是韧性)。
铝表⾯有⼀层与铝结合的很牢很致密的氧化膜,故耐蚀性好。
但是氧化膜能被氯离⼦,碱离⼦破坏,故在碱中,碳酸盐,盐酸及卤化物中很快腐蚀。
导电性与导热性好并且具有良好的切削性能。
但是铝合⾦有相当⼤的体收缩率,易在最后凝固处⽣成较⼤的缩孔。
另外,铝硅系合⾦还易粘模镁合⾦:密度⼩,⼒学性能好。
熔点低,凝固快,凝固收缩⼩,不腐蚀钢质模具。
⽐强度⾼于铝合⾦,但是屈服强度低于铝合⾦,承受载荷的能⼒稍差。
有良好的刚度和减震性,在承受冲击时,能吸收较⼤的冲击能量,可作产品外壳可减少噪声传递。
镁合⾦压铸时易产⽣缩松和热裂。
在低温下仍有良好的⼒学性能,可制造低温零件。
抗蚀性较低,故通常进⾏表⾯氧化处理和涂漆保护。
具有优良的脱模性能,与铁亲和⼒⼩,即使采⽤较⼩的出模⾓度也不会产⽣粘模现象。
模具寿命⽐铝合⾦长,⽐铝合⾦⾼4~5倍,并且成分和尺⼨稳定性也好,同时具有良好的切削加⼯性。
高性能铝合金精炼剂论文

高性能铝合金精炼剂的探讨摘要:对于铝合金来说,由于al的化学活性很强,在熔炼过程中容易产生夹杂、气体等缺陷,它们在熔体凝固后会分布在合金内部,对材料性能产生很大影响。
因此,要提高铸造铝及其合金的性能,必须充分除去熔体中的氧化夹杂和气体,避免铸件中缺陷的产生。
关键词:铝合金精炼剂氧化物夹杂1 氧化物夹杂的类型熔融金属液在精炼处理以及运输过程中,氧化皮、金属间化合物、炉膛碎片等异质物容易被带入到金属液中,形成非金属夹杂,这些非金属夹杂主要是氧化物夹杂。
根据其在熔化和浇铸过程中形成时期的不同,可以分为一次氧化物夹杂和二次氧化物夹杂。
一次氧化物夹杂主要是指铝液浇注前形成的所有氧化物夹杂。
一次氧化物夹杂按其形状可分两类:一类是宏观组织中分布不均匀的大块夹杂物,这类夹杂物,使合金组织不连续,降低工件的气密性能,成为腐蚀的根源,明显降低铝合金的强度和塑性,也往往成为零件的裂纹源,第二类氧化物夹杂是指细小的、弥散的夹杂物,即使经过仔细净化也不能全除去,它使金属液粘度增大,降低凝固时铝液的补缩能力,易造成铸件的缩松。
二次氧化物夹杂,又称为内生夹杂物,主要是在浇注过程中形成的。
内生夹杂物一般来说分布比较均匀,颗粒也比较小。
铝液在浇注过程中的飞溅、紊流是二次氧化物夹杂的主要来源。
铝液在砂型中,与型砂中的水分作用,经水分解为氧和氢,氧与铝作用形成氧化物夹杂,氢溶于铝液。
2 杂质去除方法铝熔体中的有害杂质元素可用真空处理去除和精炼剂法化学去除。
真空处理就是在真空条件下,利用杂质元素的沸点低于铝(沸点为1800℃)和铝合金主要成分的沸点,通过蒸发使之去除。
真空处理可以将钙、锌等的量降低到lppm以下,但是还未获得工业应用。
有害杂质元素可与精炼剂发生化学反应而生成能够与铝分离的化合物,并通过精炼剂的吸附作用而被带入精炼渣中排出。
其它金属与氧、按和硫的生成热大小排列如下:氧化物:镁、铝、钠、硅、锰、锌、铁、镍、铅、铜;氯化物: 钠、镁、铝、锰、锌、铅、铁、镍、铜、硅;硫化物:钠、镁、锰、锌、铝、铁、铜、铅、硅、镍以去除氧化物夹杂为主的方法主要有:电熔剂法、过滤法和精炼剂法。
铝及铝合金用熔剂

铝及其合金,作为现代工业中不可或缺的材料,广泛应用于航空、汽车、建筑、包装等众多领域。
在铝及铝合金的生产和加工过程中,熔剂起着至关重要的作用。
本文将对铝及铝合金用熔剂进行深入解析,探讨其种类、功能、应用及未来发展趋势。
一、铝及铝合金用熔剂的种类铝及铝合金用熔剂主要包括氯化物熔剂、氟化物熔剂和复合熔剂等。
氯化物熔剂以氯化钠、氯化钾等为主要成分,具有良好的熔解氧化铝的能力;氟化物熔剂则以氟化铝、氟化钠等为主要成分,对氧化铝的熔解效果更佳,但价格相对较高;复合熔剂则是结合氯化物和氟化物的优点,通过科学配比而成,旨在达到更好的熔解效果和经济效益。
二、铝及铝合金用熔剂的功能铝及铝合金用熔剂的主要功能包括:1. 清除氧化铝:铝及铝合金在高温下易与氧气反应生成氧化铝,熔剂能有效熔解氧化铝,防止其对熔体的污染。
2. 降低熔体粘度:熔剂可以降低铝及铝合金熔体的粘度,提高其流动性,有助于浇铸和成型。
3. 净化熔体:熔剂可以吸附和溶解熔体中的杂质,提高铝及铝合金的纯度。
4. 调节熔体温度:部分熔剂具有调节熔体温度的作用,有助于控制熔炼过程。
三、铝及铝合金用熔剂的应用铝及铝合金用熔剂广泛应用于原生铝和再生铝的生产过程中。
在原生铝生产中,熔剂主要用于清除氧化铝、降低熔体粘度和净化熔体,以确保铝锭的质量和产量。
在再生铝生产中,熔剂则更多地用于处理废铝中的油漆、塑料等有机物,以及吸附和溶解其他杂质,实现废铝的高效回收和再利用。
四、铝及铝合金用熔剂的发展趋势随着环保意识的日益增强和铝工业的不断发展,铝及铝合金用熔剂正朝着环保、高效、多功能的方向发展。
1. 环保型熔剂:传统的熔剂在生产和使用过程中可能产生有害气体和废渣,对环境造成污染。
未来,研发低毒、低烟、低废渣的环保型熔剂将成为重要趋势。
2. 高效熔剂:为了提高生产效率和降低成本,研发具有快速熔解氧化铝、高效净化熔体等功能的高效熔剂具有重要意义。
3. 多功能熔剂:结合不同熔剂的优点,研发具有清除氧化铝、降低熔体粘度、净化熔体、调节熔体温度等多种功能的多功能熔剂,以满足铝及铝合金生产过程中的多样化需求。
铝合金熔炼工艺流程和操作工艺

铝合金熔炼工艺流程和操作工艺(一)装料熔炼时,装入炉料的顺序和方法不仅关系到熔炼的时间、金属的烧损、热能消耗,还会影响到金属熔体的质量和炉子的使用寿命。
装料的原则有:1、装炉料顺序应合理。
正确的装料要根据所加入炉料性质与状态而定,而且还应考虑到最快的熔化速度,最少的烧损以及准确的化学成分控制。
装料时,先装小块或薄片废料,铝锭和大块料装在中间,最后装中间合金。
熔点易氧化的中间合金装在中下层。
所装入的炉料应当在熔池中均匀分布,防止偏重。
小块或薄板料装在熔池下层,这样可减少烧损,同时还可以保护炉体免受大块料的直接冲击而损坏。
中间合金有的熔点高,如AL-NI和AL-MN合金的熔点为750- 800C,装在上层,由于炉内上部温度高容易熔化,也有充分的时间扩散;使中间合金分布均匀,则有利于熔体的成分控制。
炉料装平,各处熔化速度相差不多这样可以防止偏重时造成的局部金属过热。
炉料应进量一次入炉,二次或多次加料会增加非金属夹杂物及含气量。
2、对于质量要求高的产品(包括锻件、模锻件、空心大梁和大梁型材等)的炉料除上述的装料要求外,在装料前必须向熔池内撒20-30kg粉状熔剂,在装炉过程中对炉料要分层撒粉状熔剂,这样可提高炉体的纯洁度,也可以减少损耗。
3、电炉装料时,应注意炉料最高点距电阻丝的距离不得少于100mm,否则容易引起短路。
炉料装完后即可升温。
熔化是从固态转变为液态的过程。
这一过程的好坏,对产品质量有决定性的影响。
A、覆盖时,应适当向金属表面撒上一层粉状熔剂覆盖,其用量见表。
这样也可以减少熔化过程中的金 炉型及制品 电气熔炼覆盖剂用量 普通制品特殊制品(占投量)/%0.4-0.5 覆盖剂种类 粉状熔剂煤气炉熔炼普通制品特殊制品 0.5-0.61-2 2-4 Kcl : Nacl 按 1 : 1 混合 当炉料熔化一部分后,即可向液体中均匀加入锌锭或铜板,以熔池中的熔体刚好能淹没住锌 很容易破裂,将逐渐失去保护作用。
铝合金熔炼与铸造

1.铸造温度
T浇:T浇↑↑,G↑→ 热裂倾向↑;液穴↑→ 内部质量↓;吸气↑→ 气孔倾向↑;
晶粒粗化(非均质核心数↓);拉漏。
T浇↑→ 有利于表面质量。 T浇↓→ 避免上述缺陷、细化晶粒、V铸↑ T浇↓↓,η↑ 流动性↓→气孔、缩孔、 表面夹渣倾向↑;易堵眼;冷隔、拉裂
(横裂)倾向↑。
➢二次冷却:(直接冷却)带走金属凝固 全部过程散热量的70~80%。
➢铸锭向周围的热散失
热平衡
➢半连续铸造时单位时间பைடு நூலகம்浇入结晶器 的金属熔体所带进的热量为Q
➢一次冷却带走的热量为Q1 ➢二次冷却带走的热量为Q2 ➢铸锭向周围的热散失的热量为Q3
Q=Q1+Q2+Q3
➢热平衡是半连续铸造的先决条件
5.2 结晶器内的凝固壳和液穴
液穴形状示意图
影响过渡带尺寸的因素
• 结晶温度范围窄的合金,过渡带小 • 冷却强度大,则温度梯度大,过渡带小 • 铸锭断面尺寸大,过渡带深度和宽度大 • 铸造速度快,过渡带深度增加,宽度减小 • 结晶器越高,过渡带的宽度越大 • 其他因素:铸造温度、金属的导入方式、
漏斗大小、结晶器锥度以及冷却介质等
预 净先 化处 去理 油
复 大化 料流 铺程 底
复化锭废的保管
干 燥 去 水
按炉料号、 行熔分次的复化组号保进管
搅 拌 扒 渣
制
铸
团
造
第六章 铝合金熔体的净化
联合在线精炼
• 联合在线精练:在炉外配备一套装置, 以炉外连续处理工艺取代传统的炉内 间歇式分批处理工艺。
• FILD法 • SNIF法
水平连续铸造原理
水平连续铸造是将保温炉中的金属熔 体通过液流控制装置直接导入结晶器 中,在结晶器内先凝固成具有一定强 度的凝壳,然后借助引锭杆及牵引辊 将已凝固的铸锭水平连续地拉出结晶 器,这就形成了水平连续铸锭的全过 程。
熔炼工艺

铝合金的熔炼工艺烘炉—>涂料—>装料—>搅拌—>去渣剂—>精炼剂—>静置—>扒渣—>化验1烘炉按照说明书进行烘炉;2涂料坩埚预热到180-250度,涂防腐涂料;3装料原则如下:1)易烧损的炉料应装在炉底,或加入液体铝中;2)熔点较高的中间合金应装在炉料上层;3)大块废料和原铝锭应装在中间层;4)低熔点和易烧损的纯金属待炉料熔化后加入;5)为保护炉底,装炉前最好以废板材或短料铺底;6)除铜、镁、锌外,其余炉料应尽可能一次装入;7)电炉接受液体料时,在来料过程中,最好先将所补入或冲淡用料加入炉内。
8)对装炉的基本要求是:紧密均匀,尽可能一次装入;炉料不与加热元件接触,不妨碍火焰正常流动;装炉时间短,尽可能机械化、自动化。
4搅拌搅拌是贯穿熔炼全过程的,特别是在还没有完全溶解的时候,搅拌有利于温度的扩散和合金的熔化,合金熔化完之后在加入元素合金或精炼剂后也要充分搅拌;5去渣剂添加剂分为:覆盖剂、溶剂、变质剂、精炼剂、辅助材料。
1)采用覆盖剂时,应在炉料开始熔化时就加入熔剂2)6精炼剂(铝合金熔体的净化)1)一般所谓“去气”是指去除合金中的气体,“精炼”是指去除合金中的夹杂物。
去气精炼的目的就是清除或尽量降低氧化物夹杂和气体,以提高金属的净化程度。
故去气和精炼通常称净化处理,俗称“精炼处理”。
2)炉前检验:用勺取约半勺合金液,用干净铁片刮去表面氧化物和渣,露出镜面样液面,冷却后如有气泡析出,则除气效果差,反之则效果好。
3)炉后检验,试样经腐蚀后看到针孔的大小和多少。
4)炉料全部熔化后,当合金液温度到690~740℃时,用钟罩分2~3批将精炼剂压入合金液内,距离坩埚底部10~15cm处,缓慢均匀转动,直到反应停止后,取出钟罩。
5)精炼后,静置10~20min,然后去除合金液表面的熔渣,再将合金液转入保温炉或直接浇注。
7静置1)精炼后,静置10~20min,然后去除合金液表面的熔渣,再将合金液转入保温炉。
- 1、下载文档前请自行甄别文档内容的完整性,平台不提供额外的编辑、内容补充、找答案等附加服务。
- 2、"仅部分预览"的文档,不可在线预览部分如存在完整性等问题,可反馈申请退款(可完整预览的文档不适用该条件!)。
- 3、如文档侵犯您的权益,请联系客服反馈,我们会尽快为您处理(人工客服工作时间:9:00-18:30)。
铝合金熔体的熔剂精炼 本文介绍了熔剂精炼在铝合金熔体净化过程中的作用,熔剂的分类和要求,常用熔 剂的组成,适用范围及使用方法等。
在铝及铝合金熔炼过程中,氢及氧化夹杂是污染铝熔体的主要物质。铝极易与氧生 成A1202或次氧化铝(A12O及A10).同时也极易吸收气体(H)其含量占铝熔体中气体总 量的70 — 90 %,而铸造铝合金中的主要缺陷——气孔和夹渣,就是由于残留在合金中的 气体和氧化物等固体颗粒造成的。因此,要获得高质量的熔体,不仅要选择正确合理的 熔炼工艺,而且熔体的精炼净化处理也是很重要的。
铝及铝合金熔体的精炼净化方法较多,主要有浮游法、熔剂精炼法、熔体过滤法、 真空法和联合法。本文介绍熔剂精炼法在铝合金熔炼中的应用。
1 熔剂的作用
熔盐熔剂广泛地用于原铝和再生铝的生产,以提高熔体质量和金属铝的回收率 [1.2]。熔剂的作用有四个:其一,改变铝熔体对氧化物(氧化铝)的润湿性,使铝熔体易 于与氧化物(氧化铝)分离,从而使氧化物(氧化铝)大部分进入熔剂中而减少了熔体中的 氧化物的含量。其二,熔剂能改变熔体表面氧化膜的状态。这是因为它能使熔体表面上 那层坚固致密的氧化膜破碎成为细小颗粒,因而有利于熔体中的氢从氧化膜层的颗粒空 隙中透过逸出,进入大气中。其三,熔剂层的存在,能隔绝大气中水蒸气与铝熔体的接 触,使氢难以进入铝熔体中,同时能防止熔体氧化烧损。其四,熔剂能吸附铝熔体中的 氧化物,使熔体得以净化。总之,熔剂精炼的除去夹杂物作用主要是通过与熔体中的氧 化膜及非金属夹杂物发生吸附,溶解和化学作用来实现的。
2 熔剂的分类和选择
2. 1熔剂的分类和要求
铝合金熔炼中使用的熔剂种类很多,可分为覆盖剂(防止熔体氧化烧损及吸气的熔 剂)和精炼剂(除气、除夹杂物的熔剂)两大类,不同的铝合金所用的覆盖剂和精炼剂不同。 但是,铝合金熔炼过程中使用的任何熔剂,必须符合下列条件[3.8]。
① 熔点应低于铝合金的熔化温度。 ② 比重应小于铝合金的比重。 ③ 能吸附、溶解熔体中的夹杂物,并能从熔体中将气体排除。 ④ 不应与金属及炉衬起化学作用,如果与金属起作用时,应只能产生不溶于金属的 惰性气体,且熔剂应不溶于熔体金属中。 ⑤ 吸湿性要小,蒸发压要低。 ⑥ 不应含有或产生有害杂质及气体。 ⑦ 要有适当的粘度及流动性。 ⑧ 制造方便:价格便宜。
2. 2熔剂的成分及熔盐酌作用
铝合金用熔剂一般由碱金属及碱土金属的氯化物及氟化物组成,其主要成分是KCl、 NaCl、NaF. CaF, .、Na3A1F6、Na2SiF6 等。熔剂的物理、化 学性能(熔点、密度、粘 度、 挥发性、吸湿性以及与氧化物的界面作用
等)对精炼效果起决定性作用. 2. 2. 1.氯盐
:
氯盐是铝合金熔剂中最常见的基本组元,而45 % NaCl+55 % KCl的混合盐应用最广。 由于它们对固态Al2O3,夹杂物和氧化膜有很强的浸润能力(与Al2O3,的润湿角为20多 度)且在熔炼温度下NaCl和KCl的比重
只有1.55g / cm3和l.50g / cm3,显著小于铝熔 体的比重,故能很好地铺展在铝熔体表面,破碎和吸附熔体表面的氧化膜。但仅含氯盐 的熔剂,破碎和吸附过程进行得缓慢,必须进行人工搅拌以加速上述过程的进行。 氯化物的表面张力小,润湿性好,适于作覆盖剂,其中具有分子晶型的氯盐如 CCl4 ,SiCl4 , A1C13 ,等可单独作为净化剂,而具有离子晶型的氯盐如LiCl、NaC l毛 KCl、MgC12:等适于作混合盐熔剂。 2。2 . 2 .氟盐:
在氯盐混合物中加入NaF. Na3A1F6、CaF2。等少量氟盐,主 要起精炼作用,如 吸附、 溶解Al2O3 ,。氟盐还能有效地去除熔体表面的氧化膜,提高除气效果。这是因为:a) 氟盐可与铝熔体发生化学反应生成气态的A1F,、SiF4 ,、BF3,等,它们以机械作用促 使氧化膜与铝熔体分离,并将氧化膜挤破,推入熔剂中; b)在发生上述反应的
界面上 产生的电流亦使氧化膜受“冲刷”而破碎。因此,氟盐的存在使铝熔体表面的氧化膜的 破坏过程显著加速,熔体中的氢就能较方便的逸出;c)氟盐(特别是CaF2 :)能增大混合 熔盐的表面张力,使已吸附氧化物的熔盐球状化,便于与熔体分离,减少固熔渣夹裹铝 而造成的损耗,而且由于熔剂——熔体表面张力的提高,加速了熔剂吸附夹杂的过程。
3铝合金熔炼中常用熔剂
熔剂精炼法对排出非金属夹杂物有很好的效果,但是清除熔体中非金属夹杂物的净 化程度,除与熔剂的物理、化学性能有关外,在很大程度上还取决于精炼工艺条件,如 熔剂的用量,熔剂与熔体的接触时间、接触面积、搅拌情况、温度等。
3. 1常用熔剂
为精炼铝合金熔体,人们已研制出上百种熔剂,以钠、钾为基的氯化物熔剂应用最 广。对含镁量低的铝合金广泛采用以钠钾为基的氯化物精炼剂,含镁量高的铝合金为避 免钠脆性则采用不含钠的以光卤石为基的精炼熔剂。
铝合金熔炼过程中常用熔剂的成分及作用如表1(4-7)。 表1 常用熔剂的成分及应用 溶剂种类组分含量,%
NaCl KCl MgCl2 Na3AlF6 其它成分 适用 的合金
覆盖剂 39 50 6.6 CaF2 4.4 Al-Cu 系,Al-Cu-Mg 系,Al-Cu-Si 系 Al-Cu-Mg-Zn 系 Na2CO385.CaF15 一般 铝合金
50 50 一般铝合金
KCl,MgCl280 CaF220 Al-Mg 系 Al-Mg-Si 系合金
31 14 CaF210 CaCL244 Al-Mg 系合金
8 67 CaF210,MgF215 Al-Mg 系合金
精炼剂 25-35 40-50 18-26 除 Al-Mg 系,Al-Mg-Si 系以外的其它合金 8 67 MgF215,CaF210 Al-Mg 系合金
KCl,MgCl260,CaF240 Al-Mg 系 Al-Mg--Si 系合金
42 46 Bacl26 (2号熔剂) Al-Mg 系合金
22 56 22 一般铝合金
50 35 15 一般铝合金
40 50 NaF10 一般铝合金 50 35 5 CaF210 一般铝合金
60 CaF220,NaF20 一般铝合金
36-45 50-55 3-7 CaF 21.5-4 一般 铝合金
Na2SiF630-50,C2Cl650-70 一般 铝合金
40.5 49.5 KF10 易拉罐合金
从上表中可以看出,有些熔剂组分的含量变化范围较大,可以根据实际情况来确定。 首先要根据合金元素的含量来确定[8],因为大多数铝合金中主要元素含量都可在一定范 围内变化,其次要根据所除杂质成分及含量来确定。因此,使用厂家除使用熔剂厂生产 的熔剂外,最好根据所熔炼铝合金的成分调正熔剂组分比例,以找出最佳熔剂组成。
综合以上各种熔剂不难看出,当要熔制的铝合金成分确定后,熔剂成分的设计首先 是主要成分(如氯化物)用量配比的选择,其次是添加组分(如氟化物)的选择。熔剂配好 后,最好是经熔炼、冷凝成块、再粉碎后使用,因为机械混合状态的效果不好。
3.2熔剂用量 .
熔炼铝合金废料时,废料质量不同,覆盖剂及精炼剂的用量也不同。 3.2.1 .主覆盖剂用量
a)熔炼质量较好的废料,如块状料、管、片时覆盖剂用量(见表2)。
表2 覆盖剂种类及用量 炉料及制品 覆盖剂用量(占投料量的%)覆盖剂种类 电炉熔炼:一般制品特殊制品 0.4 — 0.5 % 0.5 — 0.6 % 普通粉状溶剂普通粉状溶 剂 煤气炉熔炼:原铝锭废 料 1 — 2% 2 — 4% KC1:NaC1 按1:1混合 KC1:NaC1 按 1:1 混合
注:对高镁铝合金,应一律用不含钠盐的熔剂进行覆盖,避免和含钠的熔剂接触。 b)熔炼质量较差的废料,如由锯、车、铳等工序下来的碎屑及熔炼扒渣等时,覆盖 剂用量(见表3)。
表3: 覆盖剂用量 类别用量(占投料量的%) 小碎片碎 屑号外渣子 6 — 810 — 1515 — 20 3. 2. 2精炼剂用量
不同铝合金、不同制品,精炼剂用量也各不相同(见表4)。 表4 精炼剂用量 合金及制品熔炼炉静置炉 高镁合金 2号熔剂5-6kg/t 2号熔剂5-6kg/t 特殊制品除高镁合金 普通熔剂5-6kg/t 普通熔剂6-7kg/t LT66、LT62、LG1、LG2、LG3、LG4 出炉时用普通熔剂、叠熔剂坝
其它合金普通熔剂5-6kg/t
① 在潮湿地区和潮湿季节, 熔剂用量应有所增加 ② 对大规格的圆锭,其熔剂用量也应适当增加。 3.3熔剂使用方法
熔剂精炼法熔炼铝合金生产中常用以下几种方法: ① 熔体在浇包内精炼。首先在浇包内放入一包熔剂,然后注入熔体,并充分搅拌, 以增加二者的接触面积。 ② 熔体在感应炉内精炼。熔剂装入感应炉内,借助于感应磁场的搅拌作用使熔剂与 熔体充分混合,达到精炼的目的。
③ 在浇包内或炉中用搅拌机精炼,使熔剂机械弥散于熔体中。 ④ 熔体在磁场搅拌装置中精炼。,该法依靠电磁力的作用,向熔剂一一金属界面连 续不断地输送熔体,以达到铝熔体与熔剂间的活性接触,熔体旋转速度越高,其精炼效 果越好。
⑤ 电熔剂精炼。此法是使熔体通过加有电场(在金属 ------------------ 熔剂界面上)的熔剂层,进 行连续精炼。 在这五种方法中,电熔剂精炼效果最好。