轿车车身刚度分析与结构优化研究
汽车车身刚性设计

汽车车身刚性设计在汽车工程领域中,车身刚性设计是一个至关重要的方面。
车身刚性直接关系到汽车的安全性、稳定性和乘坐舒适性。
本文将从汽车车身刚性设计的原理、优化方法以及发展趋势等方面进行探讨。
一、汽车车身刚性设计的原理汽车车身的刚性主要指的是车身的扭转刚性和弯曲刚性。
扭转刚性是指车身在行驶过程中扭转变形的能力,弯曲刚性则是指车身在受力下弯曲变形的能力。
这两个刚性指标越高,说明车身结构越稳定,具有更好的行驶性能和安全性。
车身刚性设计的原理主要包括以下几个方面:1. 结构优化:通过钢材的选择和优化布局来提高车身的刚性。
高强度钢材的使用可以增加车身的刚度,并且减少车身重量。
2. 加强梁的设计:在车身结构关键位置设置加强梁,可以有效地提高车身的刚性。
特别是在车身的前后部分和底部,加强梁的设置可以提升整体刚性。
3. 空间结构设计:合理的空间结构设计可以增加车身的刚性。
例如,设置横梁和纵梁等结构,能够有效地减少车身的形变和振动。
4. 焊接技术:采用先进的焊接技术来提高车身的整体刚性。
优化焊接点的设计,使焊接点具有更好的连接性和刚性。
二、汽车车身刚性设计的优化方法为了实现更好的车身刚性设计,汽车工程师需要采用一些优化方法。
下面介绍几种常见的优化方法:1. 结构拓扑优化:通过数值模拟和仿真分析,找到车身结构中的薄弱环节,并进行结构调整和优化。
通过减少材料的使用和改变结构布局,来提高车身刚性。
2. 材料优化:选择高强度、高刚性和轻量化的材料,如高强度钢、铝合金等,来替代传统的钢材。
同时,还可以采用复合材料和纤维增强材料等,以进一步提高刚性和降低重量。
3. 车身加固:在车身结构中加入加强件,如加强梁、加固板等,以提高车身的整体刚性。
通过有限元分析和试验验证,确定加固部位和加固方式,实现刚性的最优化设计。
三、汽车车身刚性设计的发展趋势随着汽车工业的不断发展和技术的进步,汽车车身刚性设计也在不断演进。
以下是一些当前和未来的发展趋势:1. 轻量化设计:为了减少车身重量,提高燃油经济性和环保性能,汽车制造商将采用更多的轻质材料,如碳纤维复合材料、镁合金等。
车身结构优化设计研究

车身结构优化设计研究随着人们对安全性和环保性的日益关注,汽车制造技术也在不断更新和优化。
车身结构优化设计研究是其中一个重要的方向。
本文将从车身结构优化设计的意义、方法与技术、优化设计的实际应用等方面进行探讨。
一、车身结构优化设计的意义车身结构是汽车整车的一个重要组成部分,它不仅关系到汽车的安全性和性能,还与车辆的质量、制造工艺、成本等方面都有密切关系。
因此,在汽车的制造过程中,车身结构的设计优化是非常重要的。
车身结构优化设计旨在通过优化车身结构的设计,达到提高汽车整车的性能和安全性,降低成本和优化制造工艺等目的。
同时,优化车身结构还可以减少汽车的燃料消耗和排放,达到环保目标,具有重要的意义。
二、车身结构优化设计的方法与技术车身结构优化设计的方法主要包括三个方面:模拟分析、参数优化和实验验证。
其中,模拟分析是车身结构优化设计的重要方法和手段。
模拟分析可以通过对汽车的结构进行建模,对结构进行数字化仿真分析,以达到模拟汽车在不同工况下的运动状态、力学性能、疲劳寿命等方面的表现。
同时,模拟分析还可以对车身结构进行优化设计,以提高汽车的性能和安全性,并达到降低成本和优化制造工艺的目的。
在车身结构优化设计中,参数优化也是一种重要的方法和技术。
参数优化可以通过对汽车结构的参数进行调整,以达到优化汽车性能和安全性的目的。
同时,通过对参数进行优化设计,还可以减少汽车的燃料消耗和排放,达到环保目标。
实验验证是车身结构优化设计中的另一种重要方法和技术。
实验验证可以通过对汽车结构实际进行测试和验证,以验证模拟分析和参数优化的结果。
同时,实验验证还可以为汽车的制造提供重要的参考依据,达到优化制造工艺的目的。
三、车身结构优化设计的实际应用车身结构优化设计在实际应用中具有广泛的应用前景。
在汽车制造的各个环节中,优化车身结构设计都具有重要的意义。
首先,在汽车设计制造的初期阶段,车身结构优化设计可以为汽车的整车设计提供重要的参考依据,以确保汽车的结构设计符合整车性能和安全性的要求。
汽车设计中的结构分析和优化研究
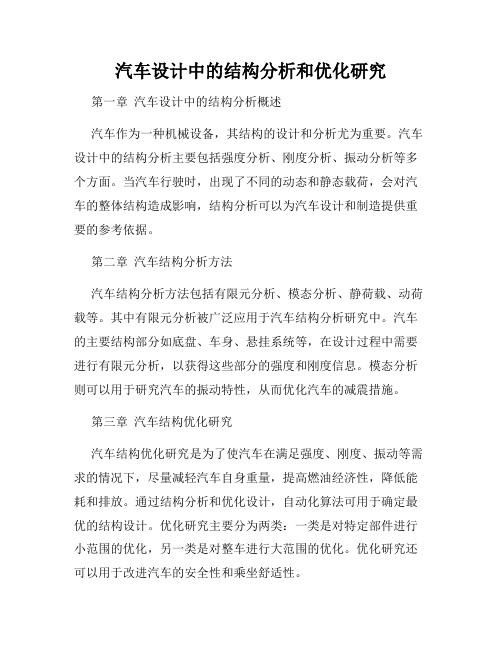
汽车设计中的结构分析和优化研究第一章汽车设计中的结构分析概述汽车作为一种机械设备,其结构的设计和分析尤为重要。
汽车设计中的结构分析主要包括强度分析、刚度分析、振动分析等多个方面。
当汽车行驶时,出现了不同的动态和静态载荷,会对汽车的整体结构造成影响,结构分析可以为汽车设计和制造提供重要的参考依据。
第二章汽车结构分析方法汽车结构分析方法包括有限元分析、模态分析、静荷载、动荷载等。
其中有限元分析被广泛应用于汽车结构分析研究中。
汽车的主要结构部分如底盘、车身、悬挂系统等,在设计过程中需要进行有限元分析,以获得这些部分的强度和刚度信息。
模态分析则可以用于研究汽车的振动特性,从而优化汽车的减震措施。
第三章汽车结构优化研究汽车结构优化研究是为了使汽车在满足强度、刚度、振动等需求的情况下,尽量减轻汽车自身重量,提高燃油经济性,降低能耗和排放。
通过结构分析和优化设计,自动化算法可用于确定最优的结构设计。
优化研究主要分为两类:一类是对特定部件进行小范围的优化,另一类是对整车进行大范围的优化。
优化研究还可以用于改进汽车的安全性和乘坐舒适性。
第四章结构分析在汽车设计中的应用汽车结构分析在汽车设计中的应用非常广泛。
在实际生产中,汽车制造商选择适当的分析工具和算法,通过对汽车不同部位的强度刚度等分析,提高产品的质量和竞争力。
结构分析可以用于改进和优化各种车型的设计,以满足客户的需求。
例如,对于商用车,需要更加强调结构的强度并增强载重能力;对于休闲车,则需要更加注重舒适性和安全性。
第五章结构分析未来的发展方向随着汽车工业的发展,汽车结构分析也在不断地发展和更新。
未来,汽车结构分析的关键发展方向在于更加准确的软件算法和更加准确的测试仪器。
深度学习和机器学习的发展也将使得汽车的结构分析程序变得更加自动化和智能化。
此外,随着氢燃料电池汽车和电动汽车等新型车型的发展,其独特的结构需求也将成为未来汽车结构分析研究的重点方向。
结论汽车的结构分析在汽车设计制造中扮演着不可或缺的角色。
某型小汽车运输铁路专用车车体强度分析及结构优化

某型小汽车运输铁路专用车车体强度分析及结构优化某型小汽车运输铁路专用车车体强度分析及结构优化1.引言某型小汽车运输铁路专用车是一种用于将小汽车从一个地点运输到另一个地点的专用车辆。
为了确保车辆的安全和稳定运行,需要进行车体强度分析和结构优化。
本文将对该型号车辆车体进行强度分析,并提出结构优化方案。
2.车体强度分析2.1 模型建立首先,对该型车辆进行三维建模。
选择合适的软件,进行车辆车体的建模和网格划分,得到完整的有限元模型。
模型的划分应按照车身结构进行,包括车身底板、车身壳体、支撑结构等。
2.2载荷分析根据设计标准和实际使用情况,确定各种载荷条件。
主要包括静态荷载、动态荷载和温度荷载等。
静态荷载包括自重、车辆载荷和小汽车载荷等;动态荷载包括行车、刹车、转弯等时产生的加速度;温度荷载则是指因温度变化引起的应力。
2.3边界条件的设定根据实际情况,设定相应的边界条件。
例如,固定底板和支撑结构的连杆连接处,设定其固定约束。
同时,还需设置诸如悬挂、支撑连接处的约束。
2.4材料性能参数设置选择车辆的主要构件材料,并设置相应的材料性能参数。
包括杨氏模量、泊松比、抗拉强度、屈服强度等。
这些参数直接影响整个模型在载荷作用下的变形和应力情况。
2.5加载及分析根据前述模型的建立、载荷和边界条件的设定以及材料性能参数的设置,进行有限元分析。
根据模拟结果,获取车体在不同荷载工况下的应力、应变等信息。
3.结构优化根据车体的强度分析结果,进行结构优化。
主要通过调整结构的材料、厚度和减少不必要零件等方式,提高车身的强度。
优化的目标是在保证车辆运行稳定的前提下,尽量减少车身的重量。
3.1选用优质材料根据强度分析结果,选择优质材料以提高车体的强度。
合理选择材料可以有效减少车身的重量,并且提高车身的刚度和抗拉强度。
3.2优化车身结构通过优化车身结构,减少不必要的零件和连接件,降低车身的重量。
可以使用拓扑优化方法,分析不同结构形式下车体的强度。
基于有限元分析的车身刚度强度优化设计

基于有限元分析的车身刚度强度优化设计近年来,随着汽车工业的快速发展,汽车的安全性能逐渐成为人们选择汽车的重要考虑因素之一。
而车身强度和刚度则是影响汽车安全性能的关键因素之一。
为了提高车身强度和刚度,借助有限元分析技术进行优化设计成为了一种重要的方法。
有限元分析是通过将连续体分割为有限个小元素,再在这些小元素上进行计算,求解结构中的应力和应变分布的一种数值分析方法。
在进行车身强度和刚度的优化设计时,有限元分析技术能够通过对车身构件的应力和变形特性进行分析,确定车身构件的受力区域,并对其进行重新设计,从而达到提高车身强度和刚度的目的。
在进行有限元分析之前,需要先确定车身强度和刚度优化设计的目标。
一般来说,车身强度的主要考虑因素包括车辆碰撞时撞击能的吸收、安全气囊的触发时间和车辆的耐久性。
而车身刚度则主要考虑车辆悬架的调校和车辆的操控性。
在确定了优化目标之后,需要对车身的结构进行有限元模型的建立和计算。
在车身刚度的优化设计中,焊接是一个非常重要的因素。
大量的焊接会使车身的刚性有所改变,而焊缝的质量也会对车身的刚性产生影响。
因此,在进行有限元分析时,需要对车身的焊接进行细致的分析,并且对焊缝进行优化设计。
通常情况下,焊接的质量对于车身刚度的影响可以通过进行试验数据进行验证。
在车身强度的优化设计中,需要考虑车身不同部位应受的应力大小,从而确定车身的强度分布。
通常情况下,车辆前方受到的力大,因此车身前部结构需要更加坚固。
而车辆的底部则需要更加耐久,以保证车辆在行驶过程中不受损伤。
另外,车辆的后部结构需要采用抗震设计,在车辆碰撞时能够承受更大的冲击。
除了车身结构的优化设计之外,在材料选择和工艺的使用上也有许多需要考虑的因素。
目前,汽车车身大多使用钢材和铝合金材料进行制造。
在材料选择上,需要考虑材料的强度和刚度,同时需要和其他件匹配,保证车身的整体性能。
另外,需要将车身制造工艺和焊接工艺纳入考虑,这能够直接影响到车身的刚度和强度。
轻型汽车车身结构设计与优化

轻型汽车车身结构设计与优化现今,轻型汽车成为人们日常生活中必不可少的交通工具。
而轻型汽车的车身结构设计与优化已经成为汽车制造业的研究热点之一。
轻型汽车车身结构设计的主要目的是为了提升汽车的安全性、驾驶舒适性、能源利用效率和减轻整车重量等方面,而车身结构优化则是为了通过技术手段使得轻型汽车减少整车重量以及提高整车综合性能。
轻型汽车车身结构的设计必须考虑到以下几个方面:1.结构的强度与刚度轻型汽车的车身结构必须保证足够的强度和刚度,以抵御意外碰撞或其他外力的影响。
优秀的车身结构设计要确保车辆在车祸中的碰撞安全,避免人员和物品的损失。
一般来说,此类车型会采用各种合金材料,通过压铸及其他制造方法,减轻车身自重以达到增强强度与刚度的目的。
2.空气动力学设计空气动力学设计是一项重要的设计考虑因素,它可以有效提高轻型汽车的行驶稳定性和车辆油耗。
空气动力学测试可以反映出来车辆行驶中受到的空气阻力和气流,一款脱离空气动力学基础测试的汽车,无法确保驾驶员和乘客在汽车高速移动中的安全。
3.人机工程学设计在轻型汽车设计的全过程中,人机工程学设计也是非常重要的一部分,其目的在于设计出切合人体工程学规律的驾驶舱室空间,让驾驶员在驾驶过程中更加舒适自如。
4.制造成本轻型汽车的制造成本在合理控制之后,其价格也可以降低,对消费者的物质压力也有所缓解。
因此,在车身结构设计中,切合实际的制造成本也是一项非常重要的考虑因素。
对于轻型汽车的结构优化而言,主要包括如下几个方面:1.减少车身自重为了降低轻型汽车的整车重量,在配备安全性能的情况下尽量减少车身自重。
这需要采用各种轻量化材料,如高强度钢材料、碳纤维等。
2.提高车身刚度在自重减少的情况下,也需要保持足够的车身刚度,以确保轻型汽车的驾驶稳定性。
3.改进动力系统轻型汽车的动力系统可以通过改进提高其工作效率,使其能在一定程度上减少车身自重。
总结起来,轻型汽车车身结构设计与优化需要综合考虑诸多因素。
汽车底盘结构的刚性与轻量化设计优化技巧

汽车底盘结构的刚性与轻量化设计优化技巧在汽车工程中,底盘结构的设计是至关重要的。
底盘是汽车的骨架,它不仅要承受汽车本身的重量,还要应对各种复杂的路况和动力输出。
因此,底盘结构的刚性和轻量化设计优化技巧成为了汽车制造商和设计师们关注的焦点。
1. 刚性设计优化技巧底盘的刚性对车辆的操控性和安全性有着重要的影响。
一种常见的刚性设计优化技巧是利用模态分析和有限元分析方法,通过改变材料和结构的分布,提高底盘的整体刚度。
此外,还可以采用螺栓连接和焊接技术,增加连接部件的刚性。
刚性的底盘结构可以降低车辆在行驶过程中的振动和噪音,提高乘坐舒适性。
2. 轻量化设计优化技巧轻量化设计是现代汽车工业的一个重要发展方向。
为了减少车辆的自重和燃油消耗,汽车制造商和设计师们采用了多种轻量化设计优化技巧。
其中一种主要的技术是使用高强度轻质材料,如铝合金和碳纤维复合材料,来替代传统的钢材。
这样可以在保持足够刚性的前提下,减少底盘的重量。
此外,还可以优化底盘的结构设计,通过合理分配和优化布局来减少冗余材料的使用,实现底盘的轻量化。
3. 结构优化技巧汽车底盘的结构设计是一个复杂而关键的环节。
为了提高刚性和轻量化,可以采用拼接结构和空心结构的设计。
拼接结构是将多个零部件通过焊接、螺栓连接等方式进行组装,形成整个底盘的结构。
这种方式可以根据需要灵活调整底盘的刚性和重量。
空心结构则是采用中空的设计,通过减少材料的使用来降低底盘的重量。
此外,还可以采用优化材料的厚度和形状,合理分配应力和负荷,提高底盘整体的性能。
总结:汽车底盘结构的刚性和轻量化设计优化技巧是现代汽车工程不可或缺的部分。
通过刚性设计优化技巧,可以提高底盘的整体刚性和稳定性,提升乘坐舒适性和操控性。
而轻量化设计优化技巧可以减少底盘的自重和燃油消耗,提高汽车的燃油经济性。
结构优化技巧则可以根据具体需求,灵活调整底盘的结构形式和材料使用,实现底盘性能的最佳化。
在未来的汽车设计中,刚性和轻量化的底盘结构将继续得到重视,以满足人们对于安全、经济和环保等方面的需求。
车身扭转刚度分析及拓扑优化
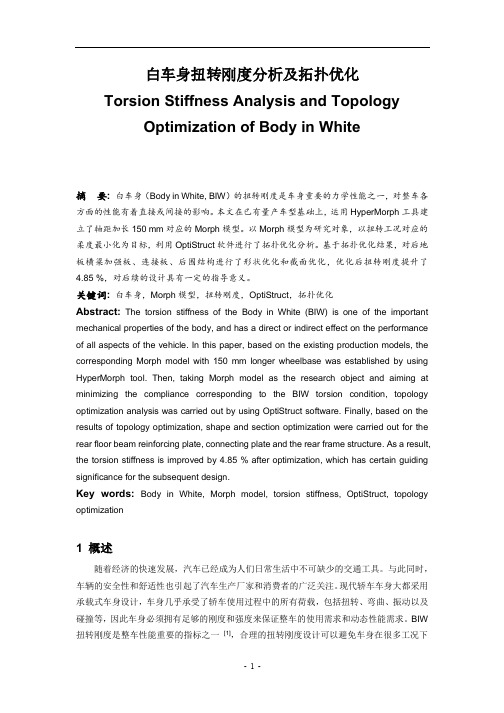
白车身扭转刚度分析及拓扑优化Torsion Stiffness Analysis and TopologyOptimization of Body in White摘要: 白车身(Body in White, BIW)的扭转刚度是车身重要的力学性能之一,对整车各方面的性能有着直接或间接的影响。
本文在已有量产车型基础上,运用HyperMorph工具建立了轴距加长150 mm对应的Morph模型。
以Morph模型为研究对象,以扭转工况对应的柔度最小化为目标,利用OptiStruct软件进行了拓扑优化分析。
基于拓扑优化结果,对后地板横梁加强板、连接板、后围结构进行了形状优化和截面优化,优化后扭转刚度提升了4.85 %,对后续的设计具有一定的指导意义。
关键词:白车身,Morph模型,扭转刚度,OptiStruct,拓扑优化Abstract:The torsion stiffness of the Body in White (BIW) is one of the important mechanical properties of the body, and has a direct or indirect effect on the performance of all aspects of the vehicle. In this paper, based on the existing production models, the corresponding Morph model with 150 mm longer wheelbase was established by using HyperMorph tool. Then, taking Morph model as the research object and aiming at minimizing the compliance corresponding to the BIW torsion condition, topology optimization analysis was carried out by using OptiStruct software. Finally, based on the results of topology optimization, shape and section optimization were carried out for the rear floor beam reinforcing plate, connecting plate and the rear frame structure. As a result, the torsion stiffness is improved by 4.85 % after optimization, which has certain guiding significance for the subsequent design.Key words:Body in White, Morph model, torsion stiffness, OptiStruct, topology optimization1 概述随着经济的快速发展,汽车已经成为人们日常生活中不可缺少的交通工具。