HyperMesh白车身结构强度分析报告
基于Hyperworks某乘用车白车身刚度及模态分析
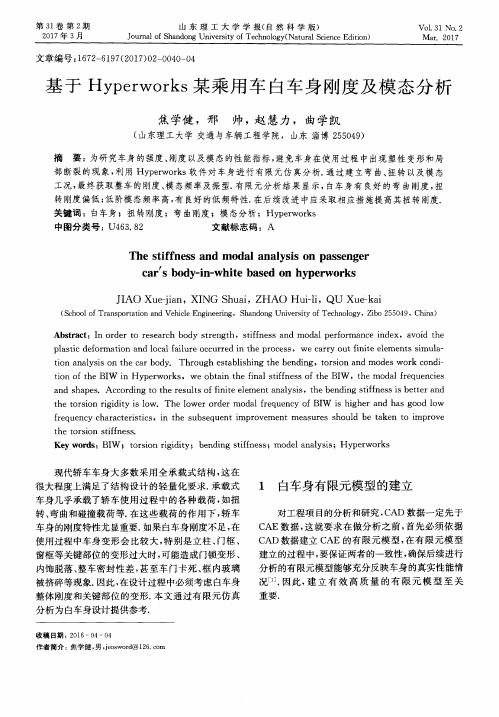
Ma r .2 0 1 7
文 章编 号 : 1 6 7 2 — 6 1 9 7 ( 2 0 1 7 ) 0 2 — 0 0 4 0 — 0 4
基 于 Hy p e r wo r k s 某 乘 用 车 白车身 刚度 及模 态分 析
焦 学健 ,邢 帅 , 赵 慧 力 , 曲学 凯
中 图分类 号 :U4 6 3 . 8 2 文献标 志码 :A
Th e s t i f f ne s s a nd mo d a l a na l y s i s o n p a s s e n g e r
c a r S b o d y - i n — wh i t e ba s e d o n h y p e r wo r k s
t h e t o r s i o n r i g i d i t y i s l o w. Th e l o we r o r d e r mo d a l f r e q u e n c y o f BI W i s h i g h e r a n d h a s g o o d l o w
工况, 最终获取整车的刚度、 模态频率及振型. 有限元分析结果显示, 白车身有 良好的弯曲刚度 , 扭 转 刚度偏 低 ; 低 阶模 态 频率高 , 有 良好 的低 频特 性. 在后 续 改进 中应采取 相应 措施提 高 其扭 转 刚度.
关键 词 :白车身 ;扭 转 刚度 ;弯 曲刚度 ;模 态 分析 ;Hy p e r wo r k s
第 3 1 卷 第 2期
2 0 1 7年 3月
山 东 理 工 大 学 学 报( 自 然 科 学 版)
J o u r n a l o f S h a n d o n g Un i v e r s i t y o f Te c h n o l o g y ( Na t u r a l S c i e n c e Ed i t i o n )
白车身强度分析报告

白车身强度分析报告1. 引言白车身是指汽车的主体骨架部分,它承受着车辆的重量和各种外部力的作用。
白车身的强度是保证车辆在运行过程中能够承受各种力和压力而不发生变形或破裂的重要指标。
本文将对白车身的强度进行分析,以提供有关白车身设计和改进的参考。
2. 强度分析方法为了分析白车身的强度,我们可以采用有限元分析(FEA)方法。
有限元分析是一种工程设计和分析的常用方法,通过将结构细分为有限数量的元素,利用数值计算方法对每个元素进行分析,从而得出整个结构的行为。
以下是强度分析的步骤:2.1 几何建模首先,需要建立一个准确的白车身的几何模型。
可以利用计算机辅助设计(CAD)软件或三维扫描技术获得车身的三维模型。
2.2 材料属性定义每种材料都有其特定的力学性质,如弹性模量、屈服强度和断裂韧性等。
在分析中,需要将这些材料属性定义在模型中。
2.3 边界条件设定在分析中,需要考虑车身受到的各种外部力和约束条件。
这些外部力可以是来自引擎、悬挂系统或碰撞等。
同时,还需要考虑车身的支撑条件和连接点的约束。
2.4 网格划分为了对车身进行数值计算,需要将其细分为有限数量的元素。
这些元素可以是三角形、四边形或六边形等。
网格划分的密度和精度对分析结果的准确性有很大影响。
2.5 载荷施加在分析中,需要根据实际情况施加各种载荷,如静载荷、动载荷和碰撞载荷等。
这些载荷将作用于车身结构上,并导致应力和变形的产生。
2.6 求解和结果分析经过以上步骤的准备,可以使用有限元软件对车身进行数值计算。
通过求解有限元方程,可以得到车身在不同载荷下的应力和变形分布。
然后,可以对分析结果进行评估和比较,以了解车身的强度和刚度。
3. 强度改进措施根据强度分析结果,可以提出一些改进措施来增强白车身的强度和刚度。
以下是一些常见的改进措施:3.1 材料优化选择具有更高强度和刚度的材料,如高强度钢或铝合金,可以显著提高白车身的整体强度。
3.2 结构优化通过对车身结构进行优化设计,可以减少材料的使用量,同时提高整体的强度。
基于HyperWorks的某轿车白车身刚度分析及优化

博士 ・ 专家论 坛
基 于 H p r rs的某 轿车白车身 刚度分析 及优化 y eWo k
湖 北汽车 工业 学 院 张继伟 胡 花
[ 摘 要] 本文以某轿车 白车 身为研 究对象, 用有 限元 分析软件 H pr r 建立其有 限元模型 , 对白车身的扭 转工况和弯曲工 使 ye Wo s k 再 况进行 分析 , 并根据评价指标对该白车身的刚度进行 分析评 价, 出该轿车 白车身的扭转刚度满足 国外轿 车较 高设计要 求, 弯曲 得 但 刚度偏低 。然后对 白车身进行尺寸优化 , 优化后 虽然扭转刚度有些减 小, 但增加 了弯 曲刚度 , 小了白车 身质量, 减 达到 了在 白车身轻
如式 ( : 4)
最大扭转载荷 T 05X前轴最大负荷 ×轮距 =.
得:=. T 05×10 ×9 11 . 8×1 3 : 8 98 N・ . 3 8 0 .7 m 6
() 1
FI =. 8×乘客室负荷
得 : =I F . 8×7 5×5 . 6 1 N ×98 6 5 =
扭
2
3 4 5 6 7 8
9 1 1 1 0 1 2
转 角 2. 21 97 37 02 68 36 93 57 J7 f4 O l I6 07 . 2 2 I0 i. 6 i3 8 . 5 3 3 2 4 8
/ ( )
白车身扭转刚度计算公式为 :
G = / J T0 () 3
一
图 1自车身有限元模 型
3白 车 身 刚度 分 析 . 31 . 扭转刚度分析
其 中, T为扭矩 ; 0为轴间相对扭转角。 由 白车身 z向扭 转变 形 图得 左 右前 悬架 座 的最 大 变形 分 别为 6 3 mm、. 2 . 8 66 mm, 4 2 由公式( ) 3 和相关的数值 , 计算 的自车身相对扭转 刚度 为 :
HyperMesh白车身结构强度分析报告
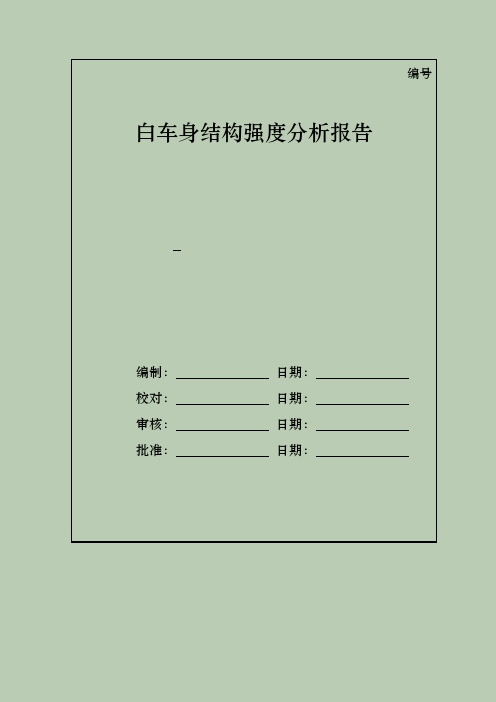
编号白车身结构强度分析报告编制:日期:校对:日期:审核:日期:批准:日期:目录1.分析目的 (1)2.使用软件说明 (1)3.模型建立 (1)4边界条件 (3)5.分析结果 (3)6.结论 (21)1.分析目的白车身结构的静强度不足则会引起构件在使用过程中出现失效。
本报告采用有限元方法对Q11白车身分别进行了满载、1g制动、0.8g转弯、右前轮抬高150mm、左后轮抬高150mm、右前轮左后轮同时抬高150mm,6种工况的强度分析,观察整车受力状况,找出高应力区,考察其零部件的强度是否满足要求,定性地评价Q11白车身的结构设计,并提出相应建议。
2.使用软件说明本次分析采用HyperMesh作前处理,Altair optistruct求解。
HyperMesh是世界领先的、功能强大的CAE应用软件包,也是一个创新、开放的企业级CAE平台,它集成了设计与分析所需的各种工具,具有无与伦比的性能以及高度的开放性、灵活性和友好的用户界面,与多种CAD和CAE软件有良好的接口并具有高效的网格划分功能;Altair Optistruct是一个综和隐式和显示求解器与一体的大规模有限元计算软件,几乎所有的线性和非线性问题都可以通过其进行求解。
通过Altair Optistruct可以进行任何形状、尺寸、拓扑结构的优化,采用固定的内存分配技术,具有很高的计算精度和效率。
3.模型建立对车身设计部门提供的Q11白车身CAD模型进行有限单元离散,CAD模型以及有限元模型如图3.1所示。
白车身所有零部件均采用板壳单元进行离散,并尽量采用四边形板壳单元模拟,少量三角形单元以满足高质量网格的过渡需要,网格描述见表3.1。
图3.1Q11白车身CAD以及有限元模型表3.1网格描述单元类型四边形单元三角形单元单元数目46970015543三角形单元比例 3.4%焊接模拟Rbe单元及实体单元涂胶模拟实体单元单元质量良好强度分析模型质量按整车满载质量计算,其中的白车身附加质量(见表3.2)用质量点单元CONM2单元模拟。
白车身结构强度分析报告模版

目录1.分析目的 (1)2.使用软件说明 (1)3.模型建立 (1)4 边界条件 (3)5.分析结果 (3)6.结论 (21)1.分析目的白车身结构的静强度不足则会引起构件在使用过程中出现失效。
本报告采用有限元方法对Q11白车身分别进行了满载、1g制动、0.8g转弯、右前轮抬高150mm、左后轮抬高150mm、右前轮左后轮同时抬高150mm,6种工况的强度分析,观察整车受力状况,找出高应力区,考察其零部件的强度是否满足要求,定性地评价Q11白车身的结构设计,并提出相应建议。
2.使用软件说明本次分析采用HyperMesh作前处理,Altair optistruct求解。
HyperMesh是世界领先的、功能强大的CAE应用软件包,也是一个创新、开放的企业级CAE平台,它集成了设计与分析所需的各种工具,具有无与伦比的性能以及高度的开放性、灵活性和友好的用户界面,与多种CAD和CAE软件有良好的接口并具有高效的网格划分功能;Altair Optistruct是一个综和隐式和显示求解器与一体的大规模有限元计算软件,几乎所有的线性和非线性问题都可以通过其进行求解。
通过Altair Optistruct可以进行任何形状、尺寸、拓扑结构的优化,采用固定的存分配技术,具有很高的计算精度和效率。
3.模型建立对车身设计部门提供的Q11白车身CAD模型进行有限单元离散,CAD模型以及有限元模型如图3.1所示。
白车身所有零部件均采用板壳单元进行离散,并尽量采用四边形板壳图3.1 Q11白车身CAD以及有限元模型单元类型四边形单元三角形单元单元数目46970015543三角形单元比例 3.4%焊接模拟Rbe单元及实体单元涂胶模拟实体单元单元质量良好强度分析模型质量按整车满载质量计算,其中的白车身附加质量(见表 3.2)用质量点单元CONM2单元模拟。
发动机和变速箱、油箱、备胎、冷凝器、前门总成、滑移门总成、后背门总成、发动机罩总成、前排座椅及乘员等使用RBE刚性单元加载到相应总成的安装处。
石朝亮_基于HyperWorks白车身灵敏度分析及结构优化

KU P
式中,K 是刚度矩阵;U 是单元节点位移矢量;P 是单元节点载荷矢量。
K U P U K X X X
则
U P K U K 1 X X X
一般,结构相应(如约束函数 g)可以描述为位移矢量 U 的函数:
g QTU
所以结构响应的灵敏度[2]为:
各板件质量灵敏度和刚度灵敏度值序号质量灵敏度刚度灵敏度序号质量灵敏度刚度灵敏度220e04600e0510157e04841e05286e03292e0211226e04228e04360e04428e0412342e04141e04117e02191e0213123e03109e03509e03123e0214903e04450e04595e04244e0415305e03428e03120e04188e04158e04693e05186467e03730e02119e04151e04187246e03598e03altair2012hyperworks技术大会论文集白车身各刚度灵敏度区间板件42确定优化方案结合上述质量灵敏度和刚度灵敏度的分析结果增厚质量小且对刚度敏感的板件减薄质量大且对刚度不敏感的板件
-3-
Altair 2012 HyperWorks 技术大会论文集
<1%
1%~3%
3%~5% 图 2 白车身各刚度灵敏度区间板件
>5%
4.2 确定优化方案
结合上述质量灵敏度和刚度灵敏度的分析结果,增厚质量小且对刚度敏感的板件,减薄质 量大且对刚度不敏感的板件。由于白车身中碰撞吸能区、能量传递区和乘员保护区等部位影响 汽车的碰撞性能,在确定优化方案的过程中,这些部位的汽车板件暂不作厚度更改。 在确定零件厚度变化范围时,只要车身零件的厚度调整适度,相应的加工模具就可以不用 改动或只作小改动。根据实际经验,当板件厚度<1.5mm 时,板件增厚与减薄最大值分别为 0.2mm 与 0.1mm;当板件厚度≥1.5mm 时,板件增厚与减薄最大值均为 0.2mm。 最终确定减薄和增厚的部件如图 3 所示,具体参见表 2。
ATC报告_基于Hypermesh二次开发实现汽车结构分析自动化_长安汽车_王朋波
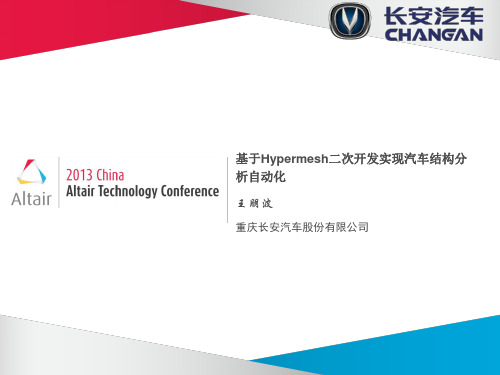
安装孔中心建立局部坐标系
将局部坐标系赋给孔中心节点
新建一load collector并在 孔中载荷约束
为loadstep设置结果输出选项
关于常规分析项的自动化
• 示例2-安装点刚度分析自动化工具
中加标记示警。
命名中加标记示警。
关于建模效率提升
工具1工作步骤
各comp以零件号命名 启动工具程序 根据提示选定CSV格式的BOM表文 件 根据提示输入BOM表材料和厚度 的列号 根据提示选择需要操作的多个co mp 程序根据零件号搜索bom表,确 定相应的行,再根据厚度列号和 列号读取相应数据。 程序对comp重新命名,在命名中 体现厚度和材料信息
费时较长
•通常需要2~3次试算。 •每项分析需要4h~20h。
关于常规分析项的自动化
• 示例1-抗凹分析自动化工具
抗凹性分析自动化工具开发思路
确定选择考察 点的有效方案
采用单点加力方案,选
参数设置模板化
总结多个项目的经验,确 定一套通用性好的Abaqus分 析参数,对于大多数情况均能 保证计算收敛性和精度。
• 检查connector 是否与几何点匹 配,清理重复的 焊点
• 一键显示组件多 项信息。 • 自动统一组件ID 、属性ID和零件 号。 • 清理分析设置仅 保留基本模型信 息。
关于建模效率提升
• 示例1-Batchmesh工具
直接用Batchmesher模块进行网格自动划分,用户需进行以下操作
计算精度
参数设置难以统一,不同的参 数对结果影响较大,且经常不 收敛。
通常需要2~3次试算,需花费 工时2h~10h 。
基于HyperWorks的某商务车白车身刚度分析

9 2
湖 北 工 业 大 学 学
报
21 0 0年 第 4期
2 2 有 限元分析 计算 .
根据上 述 1 3个测 点 的 z 向位 移 以及 它 们 的 z
向平 均位移 的测量 数 据 绘 出 图 6所 示测 点 曲线 , 由 测点 曲线可 以 明 显看 出底 板 ( 即纵 梁 )在 车 身 长度 方 向上 的垂 直挠度 ( Z向位移 ) 变化 曲线 连续 无 明显
1 1 弯 曲 刚 度 .
身 的刚度 ( 曲刚 度 和扭 转 刚度 ) 行 了模 拟分 析 , 弯 进 并 与 目标值进 行 比较 .
2 1 主 要步 骤 .
图 1所示 为利 用 Hy ewok p r r s系列软 件进行 商
务 车 白车身静 刚 度有 限元分 析 的主要 步 骤 [ , 处 3 前 ]
车身整体 的弯 曲 刚度
由车 身底 架 的 最大 垂
理 ( 画线 框 中 的 内容 ) Hy eMeh中完 成 ; 点 在 pr s 求 解利 用 Hy ew rs自带 的 求 解 器 R do s 行 , pr ok a is 进
直挠度 以及底 板在车 身长度 方 向上 的垂直 挠度 变化
[ 中图 分 类 号 ]U4 2 3 6 .
[ 文献 标 识 码 ] A :
所谓“ 白车身” 是 由各 种各 样 的骨 架件 和钣金 就
G 一 7 0. J L/
() 2
ቤተ መጻሕፍቲ ባይዱ
件通 过焊接拼 装而 成 的 汽车 车 身. 商务 车 的 白车身 刚度分 析是整 车开 发 设 计过 程 中必 不 可 少 的环 节 , 对于改 进车身 结构 , 善 车辆 强 度 、 度状 况 , 高 改 刚 提 车辆舒适 性和 可靠 性均 具 有 很重 要 的实 际意 义. 利 用先进 的有 限元 软件 对 其 进 行分 析 计算 , 指导 生 产 开发 , 于缩短产 品开 发周期 、 对 降低产 品开 发成本 能 起 到一定 的作用 , 可 以指 导设 计 人 员 对 车身 结 构 并 进 行优化从 而提 高车身 的碰撞 安全性 .
- 1、下载文档前请自行甄别文档内容的完整性,平台不提供额外的编辑、内容补充、找答案等附加服务。
- 2、"仅部分预览"的文档,不可在线预览部分如存在完整性等问题,可反馈申请退款(可完整预览的文档不适用该条件!)。
- 3、如文档侵犯您的权益,请联系客服反馈,我们会尽快为您处理(人工客服工作时间:9:00-18:30)。
编号白车身结构强度分析报告
编制:日期:
校对:日期:
审核:日期:
批准:日期:
目录
1.分析目的 (1)
2.使用软件说明 (1)
3.模型建立 (1)
4边界条件 (3)
5.分析结果 (3)
6.结论 (21)
1.分析目的
白车身结构的静强度不足则会引起构件在使用过程中出现失效。
本报告采用有限元方法对Q11白车身分别进行了满载、1g制动、0.8g转弯、右前轮抬高150mm、左后轮抬高150mm、右前轮左后轮同时抬高150mm,6种工况的强度分析,观察整车受力状况,找出高应力区,考察其零部件的强度是否满足要求,定性地评价Q11白车身的结构设计,并提出相应建议。
2.使用软件说明
本次分析采用HyperMesh作前处理,Altair optistruct求解。
HyperMesh是世界领先的、功能强大的CAE应用软件包,也是一个创新、开放的企业级CAE平台,它集成了设计与分析所需的各种工具,具有无与伦比的性能以及高度的开放性、灵活性和友好的用户界面,与多种CAD和CAE软件有良好的接口并具有高效的网格划分功能;Altair Optistruct是一个综和隐式和显示求解器与一体的大规模有限元计算软件,几乎所有的线性和非线性问题都可以通过其进行求解。
通过Altair Optistruct可以进行任何形状、尺寸、拓扑结构的优化,采用固定的内存分配技术,具有很高的计算精度和效率。
3.模型建立
对车身设计部门提供的Q11白车身CAD模型进行有限单元离散,CAD模型以及有限元模型如图3.1所示。
白车身所有零部件均采用板壳单元进行离散,并尽量采用四边形板壳单元模拟,少量三角形单元以满足高质量网格的过渡需要,网格描述见表3.1。
图3.1Q11白车身CAD以及有限元模型
表3.1网格描述
单元类型四边形单元三角形单元
单元数目46970015543
三角形单元比例 3.4%
焊接模拟Rbe单元及实体单元
涂胶模拟实体单元
单元质量良好
强度分析模型质量按整车满载质量计算,其中的白车身附加质量(见表3.2)用质量点单元CONM2单元模拟。
发动机和变速箱、油箱、备胎、冷凝器、前门总成、滑移门总成、后背门总成、发动机罩总成、前排座椅及乘员等使用RBE刚性单元加载到相应总成的安装处。
由于额定载货质心的不可确定性,无法给定具体质心位置,因此本次分析在经验基础上确定质心位置,并将额定载货分布于后地板多处主要受力点处进行模拟。
具体质量点分布情况可参考图3.2。
表3.2Q11白车身附加质量及质心
序号部件质心坐标(X,Y,Z),mm质量,kg
1发动机和变速箱1036.0,-24.0,187.7130
2燃油箱1958.9,258.4,54.034
3备胎3525.8,94.8,22.212
4散热器-64.2,0.70,350.4 2.5
5蓄电池1061.903,-456.199,270.09410
6前门总成813,±731,671.323/23
7中门总成1763.3,±733.8,649.725/25
8后背门总成3627.1,0,918.727
9发动机罩总成-66.9,0,787 6.5
10主、副驾驶座椅及乘员1195,-295/320,61687.5/87.5
11二排座椅及乘员质量、质心2048.457,-166.498,589.908164
12三排座椅及乘员质量、质心2896.054,0,617.012243
13仪表台质量、质心475.8,13.3,813.85
14行李3341.6,0,421225
15白车身质量1769.404,-0.7,552.975309
16整车满载状态质量参数1858.4,-3.7,497.81810
图3.2Q11白车身附加质量分布
4边界条件
以满载状态下计算车身在以下工况下的强度应力。
计算工况包括满载工况(工况1)、制动工况(工况2)、转弯工况(工况3)、右前轮抬高150mm工况(工况4)、左后轮抬高150mm工况(工况5)、右前轮左后轮同时抬高150mm(工况6)。
载荷如表4.1所示。
表4.1Q11白车身强度分析工况载荷
工况载荷(加速度)
满载-Z向1g满载
制动-X向1g;-Z向1g满载
转向-Y向0.8g;-Z向1g满载
右前轮抬高150mm-Z向1g满载
左后轮抬高150mm-Z向1g满载
右前轮左后轮同时抬高150mm-Z向1g满载
5.分析结果
5.1满载工况:
满载工况下,车身和主要零部件应力云图如下所示。
车身应力
云图
Q11前轮壳和前地
板
Q11后轮
罩
Q11顶盖和后背门
框
Q11后地
板
Q11横梁
Q11纵梁
5.2制动工况
1g制动工况下,车身和主要零部件应力云图如下所示。
车身受力
云图
Q11前轮壳和前地
板
Q11后轮
罩
Q11顶盖和后背门
框
Q11后地
板
Q11横梁
Q11纵梁
5.3转弯工况
0.8g转弯工况下,车身和主要零部件应力云图如下所示。
车身受力
云图
Q11前轮壳和前地
板
Q11后轮
罩
Q11顶盖和后背门
框
Q11后地
板
Q11横梁
Q11纵梁
5.4右前轮抬高150mm
右前轮抬高150mm工况下,车身和主要零部件应力云图如下所示。
车身受力
云图
Q11前轮壳和前地
板
Q11后轮
罩
Q11顶盖和后背门
框
Q11后地
板
Q11横梁Q11纵梁
5.5左后轮抬高150mm
左后轮抬高150mm工况下,车身和主要零部件应力云图如下所示。
车身受力
云图
Q11前轮
壳和前地
板
Q11后轮
罩
Q11顶盖和后背门
框
Q11后地
板
Q11横梁
Q11纵梁
5.6右前轮左后轮同时抬高150mm
右前轮左后轮同时抬高150mm工况下,车身和主要零部件应力云图如下所示。
车身受力
云图
Q11前轮壳和前地
板
Q11后轮
罩
Q11顶盖和后背门
框
Q11后地
板
Q11横梁
Q11纵梁
通过以上6中工况的计算,综合Q11所用材料的屈服强度值(见表5.1),下面列出各种工况下主要零部件的应力值,见表5.2。
表5.1Q11车身所用部分材料及其强度参数
材料名称屈服强度(MPa)抗拉强度(MPa)
DC01130-260≥270
DC03120-240≥270
DC04140-210≥270
DC06100-180≥250
08F175295
20245410
表5.2主要零部件的应力值及其安全系数统计表
零件名满载工况制动工况转弯工况右前轮抬
高150mm
左后轮抬
高150mm
右前轮左
后轮同时
抬高
150mm
前轮壳48.77201.3151.0384.3300.0275.8后轮罩24.2530.3742.7138.6657.3266.07顶盖37.4941.20125.2133.6289.3302.1后地板186.1350.2307.7188.7204.3201.0横梁112.6211.8173.4113.3113.5112.3纵梁81.9179.8799.19105.4138.8119.3
6.结论
1六个典型工况下,白车身绝大部分零部件应力较小;
2一些部件出现应力集中区域,分析结果显示超过材料的屈服极限;
3前轮壳高应力集中区域为前轮壳与前地板连接处附近区域,可以考虑对此附近区域进行加强;
4后地板高应力集中区域为座椅安装点附近区域,由于座椅及人采用集中质量单元,并用rbe3单元加载的方法模拟,此处存在模拟不精确产生的虚假应力集中现象;
5制动、转向均按路面最大附着系数0.8计算(参见《汽车理论》),在实际汽车行驶中几乎不会出现这些工况,所以在汽车实际运行时,其强度安全系数会高于仿真分析的安全系数。