JASO C437-1984 中文版 制动器摩擦材料的接合强度试验方法
SAE J661-1987 中文版 制动器衬片质量控制测试规程

SAE J661-1987Brake lining Quality Control Test Procedure制动器衬片质量控制测试规程1.目的本标准为SAE推荐标准,其目的在于一种统一的实验室测试方法,以便于对制动衬片的安全情况及摩擦磨损特性做出报告。
本规范的测试数据可以用于制动衬片生产厂内的质量控制,也可以用于外购制动鼓衬片的质量评估。
2.设备图1和图2展示了一种典型的,具有商业用途的设备结构,该设备称作摩擦材料试验机,可用于执行本测试规范,这台摩擦材料试验机应具有如下功能:1)测量鼓温2)加热试验鼓3)控制试验鼓的升温速率4)仅从鼓的背面对鼓进行冷却5)控制试验鼓降温速率6)测量摩擦力7)测量鼓的转动速度同时还应具有对试样的重量及厚度进行测量的条件。
温度的测量装置有焊接的热电偶、市合金属环、银石墨碳刷、温度显示器和高输入阻抗的记录仪组成。
鼓的升温速率可按下述方法进行调整,并且在测试过程中保持此速率,鼓的旋转速度为411rpm,打开冷却空气,从300F(149℃)冷却至200F(93℃),然后关闭冷却风使鼓冷却至180F(82℃),在180F(82℃),在180F(82℃)时打开加热器并记录时间,加热10分钟,鼓温应在10分钟时送到430±25F(221±14℃)。
鼓的降温速率可按下述方法调整,鼓的转速为411rpm,打开加热器加热试验鼓,使其温度达到700F(371℃)关闭加热器并打开冷却空气,当鼓温降至650F(343℃)时开始计时,冷却10分钟,在10分钟时鼓的温度应该是200±25F(93±14℃)。
温度测量系统的精度应达到满量程的±2%。
摩擦力测量系统的精度应达到满量程的±2%。
试验鼓转速的测量系统的精度应达到满量程的±2%。
试验鼓内径的有效使用范围为277.0~280.0毫米,在鼓的外圆周上有三个热电偶的孔位,每一个孔位与内径位277.0mm的新鼓内表面距离位2.55mm(打印位置号1),3.05mm (打印位置号2)合3.55mm(打印位置号3)。
制动软管的结构 性能要求及试验方法 宣贯
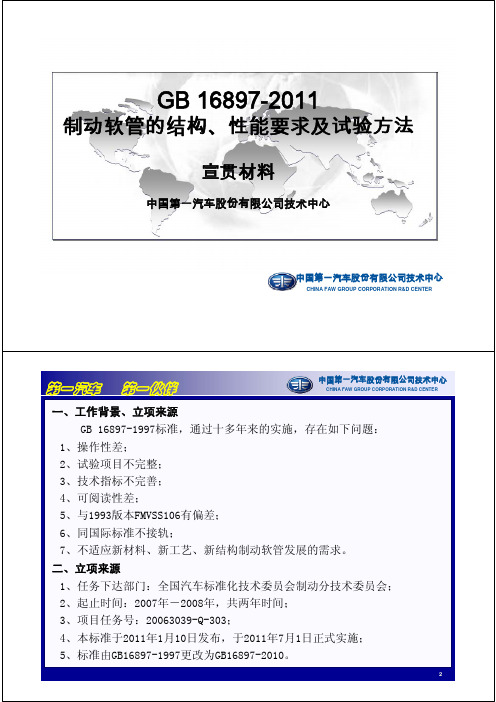
1中国第一汽车股份有限公司技术中心CHINA FAW GROUP CORPORATION R&D CENTERGB 16897-2011制动软管的结构、性能要求及试验方法宣贯材料中国第一汽车股份有限公司技术中心中国第一汽车股份有限公司技术中心CHINA FAW GROUP CORPORATION R&D CENTER第一汽车第一伙伴1、操作性差;2、试验项目不完整;3、技术指标不完善;4、可阅读性差;5、与1993版本FMVSS106有偏差;6、同国际标准不接轨;7、不适应新材料、新工艺、新结构制动软管发展的需求。
1、任务下达部门:全国汽车标准化技术委员会制动分技术委员会;2、起止时间:2007年-2008年,共两年时间;3、项目任务号:20063039-Q-303;4、本标准于2011年1月10日发布,于2011年7月1日正式实施;5、标准由GB16897-1997更改为GB16897-2010。
二、立项来源1、补充和完善现行标准的不足,达到与国际标准接轨;2、更有效的控制产品质量;3、提高整车制动安全性;4、提升行业整体技术水平;5、为国家质检中心提供可操作性的、先进的检测标准。
四、修订原则本次修订非等效采用FMVSS106 -1993标准,同时参考了ISO3996-1995 、JISD2601-1995、JISD2606-1999、JISD2607-1999、SAEJ1401-2003、SAEJ1402-2005、SAEJ1403-2005、DIN73378-1996 、DIN73324-1、QC/T80-1993等标准,另外对进口和国产制动软管及总成进行了大量的验证试验,结合试验数据及在保证装车使用安全可靠前提下,对原标准进行了修订。
中国第一汽车股份有限公司技术中心第一汽车第一伙伴CHINA FAW GROUP CORPORATION R&D CENTER1、增加了术语的英文名称(见第3章);2、增加了试验样品数量规定(见表1、表6、表9);3、增加了液压制动软管总成的“耐高温脉冲性”试验(见表1);4、增加了塑料软管的“爆裂强度”计算公式(见表6);5、修改了用于真空制动软管的标识(见第8章);6、删除了“永久联接管接头”和“真空管系连接器”术语(1997版3.6条、3.8条);7、删除了气压制动软管总成的“耐寒性”中的“气密性”试验(1997版6.2.8款);8、修改了内径Φ3.2 mm液压制动软管总成爆裂强度的评价指标(见表1);9、对真空制动软管规格尺寸和部分项目的试验要求进行了修订(见第7章);10、修改了试验项目术语;11、对原标准没有规定公差的试验条件规定了公差;12、增加了表7;13、增加了“VH、VL”标志(见第8章),对管接头的标志要求进行了修改14、标准名称“制动软管”改为“制动软管的结构、性能要求及试验方法”。
汽车用制动器衬片

GB 5763—1998前言本标准根据日本工业标准JIS D4411—1993《汽车用制动器衬片与衬垫》对GB 5763—86进行修订。
本标准非等效采用JIS D44ll—1993,但标准的主要核心内容——摩擦性能及其试验方法是与日本标准相同的。
本标准与GB 5763—86对照,有些重要技术内容作了修改:——指标值采用法定计量单位;——产品仅按用途来分类;——摩擦性能重新修改,规定与实际相符的摩擦系数范围和最高试验温度时△μ;——摩擦性能试验方法部分修改;——检验规则内容重新编写;——标志和包装修改;——柔软性和产品标注取消。
本标准附录A、附录B均为提示的附录。
本标准自生效之日起,代替GB 5763-86。
本标准由国家建筑材料工业局提出。
本标准由杭州制动材料厂归口。
本标准起草单位:杭城摩擦材料有限公司、国家建筑材料工业局咸阳非金属矿研究设计院。
本标准主要起草人:江世履、蔡仁华、蒋立峰、尚兴春、石志刚。
本标准于1986年1月首次发布。
本标准委托杭州制动材料厂负责解释。
中华人民共和国国家标准GB 5763—1998代替 GB 5763—86汽车用制动器衬片Brake linings for automobiles1 范围本标准规定了汽车用制动器衬片的分类、技术要求、试验方法、检验规则、标志、包装、运输与贮存等。
本标准适用于汽车用制动器衬片(以下简称衬片)。
2 引用标准下列标准所包含的条文,通过在本标准中引用而构成为本标准的条文。
本标准出版时,所示版本均为有效。
所有标准都会被修订,使用本标准的各方应探讨使用下列标准最新版本的可能性。
GB/T 2828—87 逐批检查计数抽样程序及抽样表(适用于连续批的检查)GB/T 9439—88 灰铸铁件JB/T 7498—94 砂纸3 分类衬片按用途分为四类,见表1。
表 1 衬片分类4 技术要求4.1 外观质量4.1.1 衬片表面加工与否由供需双方商定。
4.1.2 衬片不允许有龟裂、起泡、凹凸不平、翘曲、扭曲等影响使用的缺陷。
QCT 583-1999 汽车制动器衬片显气孔率试验方法

中华人民共和国行业标准 QC/T 583—1999ZB/T T24006—89汽车制动器衬片显气孔率试验方法1 主题内容与适用范围本标准规定了测定汽车制动器衬片显气孔率的试验设备、试样制备、试验程序和数据处理方法。
本标准适用于汽车鼓式制动器衬片和盘式制动器衬垫,也适用于汽车离合器摩擦片。
2 引用标准SY 1172工业齿轮油3 测定原理由液体浸渍前后试样质量之差与液体密度的比值,计算开口气孔体积。
再由开口气孔体积与总体积的百分比值,计算显气孔率。
4 试验仪器、设备与材料a. 电热干燥箱;b. 干燥器;c. 分析天平,感量0.1mg;d. 液体密度天平或容量50ml的密度瓶;e. 电加热管;f. 温度指示控制仪;g. 恒温水浴器;h. 显气孔率测试仪器装置(如附录A):i. 游标卡尺,精度0.02mm;j. 烧杯,容量400ml;k. 定性滤纸;l. 细铜丝,长约150mm;m. 浸渍液,符合SY 1172的50号齿轮油。
5 试样制备5.1 从库存成品中随机抽取的样品上制取试样。
试样总数至少3个,应尽可能取自同一片样品;若样品较小,则应从尽量少的样品上制取。
5.2 取样部位应距样品边缘至少5mm。
试样应具有代表性,不可带有钢背。
若有消音层、隔热层等,也应将它们除去。
5.3 试样表面应平整、清洁,不允许有起泡、裂纹、加工刀痕等缺陷。
5.4 试样规格:长25±0.5mm;宽25±0.5mm,厚5±0.1mm。
若样品厚度小于5mm,就以此样品厚度为基础,加工成相互平行的两个平面。
6 试验程序6.1 用游标卡尺测量,并记录每个试样的长、宽、厚。
6.2 用细铜丝将试样扎紧,并在上端扎成吊环状,以便悬挂,用天平称量,并记录试样质量M。
记录格式如附录B。
16.3 将试样悬浸人盛油烧杯中,试样与试样、试样与杯壁不得相互接触。
在徐徐搅拌下,将油加热至90±5℃,保持8h。
6.4 将试样移人另一处于室温的油液中,静置浸溃12h。
20140504_动车组闸片暂行技术条件
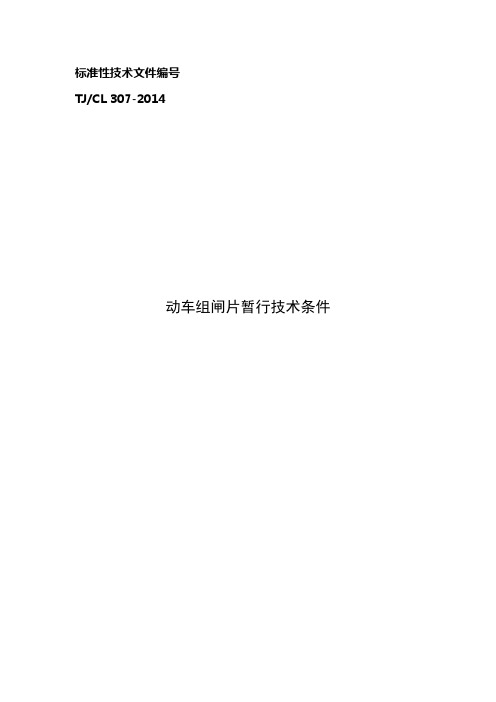
抽样方法同TB/T 3118物理及力学性能检验(6.1.4) 。
8.2 型式试验 8.2.1 8.2.2 型式试验项目见表 1。 在出现以下情况之一时应进行型式试验:
a)新产品定型; b)当产品性能、结构、生产工艺或材料有重大改变; c)产品或同类型产品停产两年以上恢复生产,以及连续生产四年以上,不能证明产品性能、 质量一致性的; d)法律法规要求的。
GB/T 1033.1-2008 GB/T 1184-1996 GB/T 1804-2000 GB/T 5121.1-2008 GB/T 10421-2002 TB/T 3005-2008
TB/T 3118-2005 铁道车辆用合成闸片 UIC 541-3-2010 制动装置-盘形制动装置及其应用-闸片许可的一般规定
动车组闸片暂行技术条件
1
范围
本技术条件规定了 CRH 系列动车组用闸片的技术要求、检验方法、检验规则、使用寿命、标志、 运输与储存要求等。用于指导动车组用闸片的设计、制造、检验、试验和认证。 本技术条件不能涵盖的内容,应参见供需双方技术协议。
2
规范性引用文件
下列文件对于本技术条件的应用是必不可少的。凡是注日期的引用文件,仅注日期的版本适用
闸片在试验期间不应出现烧痕、隆起、变形、摩擦材料熔化、金属镶嵌、掉
块、持续啸叫及其它缺陷。
7
检验方法
7.1 外观检查
闸片外形尺寸应用专用的样板或精度不低于 0.02mm 的量具检查。
7.3 物理及力学性能试验 7.3.1 7.3.2 试样制取 密度试验
试样应从闸片摩擦体上制取。取样方法和要求参照相关试验标准。
标准性技术文件编号 TJ/CL 307-2014
动车组闸片暂行技术条件
我国汽车摩擦材料标准体系现状及其完善

第30卷第6期非金属矿V ol.30 No.6 2007年11月Non-Metallic Mines Nov, 2007随着近几年出口贸易的急剧增长,为我们提供了极多的与国外先进摩擦材料制造企业和汽车厂交流的机会,使我国摩擦材料行业在技术测试方法与标准、测试设备等方面获得了大量的信息与提高,我们也一定要认真分析我们在技术特别是标准方面的不足,通过借鉴国外经验建立起中国特色的汽车摩擦材料标准体系,才能不断地缩短与发达国家的差距,有利于摩擦材料产品质量的提高。
本文以我国摩擦材料标准现状、国外摩擦材料标准发展并通过比较,提出我国的标准体系。
1 我国汽车摩擦材料标准发展沿革1.1 解放后五十年代至六十年代中期 行业标准化是在解放后,尤其是五十年代大跃进时期起步的。
1961年,发布了三项产品标准,建标46-61(刹车片)、建标47-61(离合器片)、建标48-61(刹车带)。
1966年修订了其中的两项,成为JC123-66(代替建标46-61)和JC124-66(代替建标47-61);同时还制定发布了四项测试方法标准:JC126-66(布氏硬度)、JC127-66(冲击强度)、JC128-66(吸水率和吸油率)和JC129-66(摩擦性能)。
这些制、修订的几项行业标准,均采用当时苏联标准模式。
1.2 上世纪八十年代初至九十年代初 为加强行业标准化技术归口,国家建材局明确了我国制动制品标准化技术归口单位为杭州制动材料厂;中汽总公司也明确了汽车摩擦材料标准化技术归口单位是杭州摩擦材料研究所。
在此期间,国家鼓励采用国际和国外先进标准。
于是制定了一批与此水平相当的国标和行标。
产品标准有GB5763-86(代替JC123-66,JC129-66),GB5764-86(代替JC124-66,JC129-66)。
GB11834-89(代替建标48-61)。
测试方法标准有GB5765-86(代替JC124-66),GB5766-86(代替JC126-66)。
制动标准大全
十七、制动标准GB 12676—2014 商用车辆和挂车制动系统技术要求及试验方法GB/T 12676—1999 GB 16897—2010 制动软管的结构、性能要求及试验方法GB 16897—1997GB 21670—2008 乘用车制动系统技术要求及试验方法GB/T 5335—2008 汽车液压制动装置压力测试连接器技术要求GB/T 5335—1985 GB/T 5345—2008 道路车辆石油基或非石油基制动液容器的标识GB/T 14168—1993、GB/T 5345—1985 GB/T 5620—2002 道路车辆汽车和挂车制动名词术语及其定义GB/T 5620.1—1985、GB/T 5620.2—1985 GB/T 5921—1986 汽车和挂车气压制动系部件上接口的识别标记GB/T 5922—2008 汽车和挂车气压制动装置压力测试连接器技术要求GB/T 5922—1986 GB/T 7361—1987 半挂牵引车的制动及电路连接位置GB/T 7362—1987 全挂牵引车和货车的制动及电路连接位置GB/T 13594—2003 机动车和挂车防抱制动性能和试验方法GB 13594—1992GB/T 14171—1993 汽车气制动系管路螺纹孔和管接头外螺纹GB/T 30513—2014 乘用车爆胎监测及控制系统技术要求和试验方法GB/T 30677—2014 轻型汽车电子稳定性控制系统性能要求及试验方法QC/T 35—1992(2009) 汽车与挂车气压控制装置台架试验方法JB 3737—1984QC/T 36—1992(2009) 汽车与挂车气压控制装置通用技术条件JB 3738—1984QC/T 37—1992(2009) 汽车与挂车气压调节保护装置通用技术条件QC/T 38—1992(2009) 汽车与挂车气压调节保护装置台架试验方法QC/T 77—1993(2009) 汽车液压制动轮缸技术条件JB 540—1964QC/T 79.1—2008 道路车辆牵引车和挂车之间气制动连接用螺旋管总成第1部分:尺寸QC/T 79—1993QC/T 79.2—2008 道路车辆牵引车和挂车之间气制动连接用螺旋管总成第2部分:性能要求QC/T 79—1993QC/T 200—1995(2009) 汽车气制动装置用储气筒技术条件JB 3783.1—1984、JB 3783.2—1984 QC/T 201—1995 (2009) 汽车气制动用热塑管接头尺寸QC/T 237—1997(2009) 汽车驻车制动器性能台架试验方法QC/T 239—1997(2009) 货车、客车制动器性能要求JB 3935—1985QC/T 307—1999(2009) 真空助力器技术条件ZB/T24 003—1987、ZB/T24 004—1987 QC/T 311—2008 汽车液压制动主缸性能要求及台架试验方法QC/T 311—1999 QC/T 316—1999(2009) 汽车行车制动器疲劳强度台架试验方法ZB/T T24 013—1990 QC/T 479—1999(2009) 货车、客车制动器台架试验方法JB 2805—1979*QC/T 556—1999(2009) 汽车制动器温度测量和热电偶安装JB 3936—1985*QC/T 564—2008 乘用车制动器性能要求及台架试验方法QC/T 564—1999 QC/T 592—2013 液压制动钳总成性能要求及台架试验方法QC/T 592—1999 QC/T 593—2014 汽车液压比例阀性能要求及台架试验方法QC/T 593—1999QC/T 764—2006※汽车液压制动系金属管、内外螺纹管接头和软管端部接头GB/T 11611—1989(国标转行标)QC/T 788—2007 汽车踏板装置性能要求及台架试验方法QC/T 789—2007 汽车电涡流缓速器总成性能要求及台架试验方法QC/T 790—2007 制动气室性能要求及台架试验方法QC/T 958—2013 汽车真空泵性能要求及台架试验方法QC/T 959—2013 机械式驻车制动操纵杆总成性能要求及台架试验方法QC/T 960.1—2013 道路车辆液压制动系统第1部分:双喇叭金属管、螺纹孔、螺纹管接头和管座QC/T 961—2013 液压制动系统塑料储液罐性能要求及台架试验方法QC/T29078—1992(2009)汽车用空气压缩机技术条件QC/T 29101—1992(2009) 汽车用拉索总成*********GB 5763—2008 汽车用制动器衬片GB 5763—1998 GB/T 5766—2007 摩擦材料洛氏硬度试验方法GB/T 5766—1996 GB/T 17469—2012 汽车制动器衬片摩擦性能评价小样台架试验方法GB/T 17469—1998GB/T 18849—2011 机动工业车辆制动器性能和零件强度GB/T 18849—2002 GB/T 22309—2008 道路车辆制动衬片盘式制动块总成和鼓式制动蹄总成剪切强度试验方法GB/T 22310—2008 道路车辆制动衬片盘式制动衬块受热膨胀量试验方法GB/T 22311—2008 道路车辆制动衬片压缩应变试验方法GB/T 26736—2011 道路车辆制动衬片耐水、盐水、油和制动液性能试验方法GB/T 26737—2011 道路车辆制动衬片锈蚀对铁偶合面粘结影响的试验方法GB/T 26738—2011 道路车辆制动衬片摩擦材料产品确认和质量保证GB/T 26739—2011 道路车辆制动衬片材料内剪切强度试验方法GB/T 26740—2011 道路车辆制动衬片盘式制动衬块试验后表面和材料缺陷的评价方法GB/T 26741—2011 机动三轮车用制动器衬片GB/T 29063—2012 道路车辆制动衬片摩擦材料气制动商用车性能试验方法GB/T 29064—2012 道路车辆制动衬片摩擦材料汽车制动系统摩擦性能评价方法GB/T 29065—2012 道路车辆制动衬片摩擦材料涂漆背板和制动蹄耐腐蚀性能评价方法GB/T 29066—2012 道路车辆制动衬片摩擦材料气制动商用车磨损试验方法。
AK实验标准
Surface vehicle recommended practice SAE J2522 issued 2003-6测功圆盘制动器效能前言-不同摩擦材料的评价和比较可行性试验方法的恰当规定已成为工业自动化趋势的全球性趋势。
这些比较试验法在摩擦称片的研制,选择和质量控制方面被证明是有效的。
代表欧洲摩擦称片和客车制动器的AK 工作组在最近几年研制AK Master 标准。
SAE 制动器试验机试验号标准制动系统具有全面的性能和安全性。
因此,委员会将把AK Master 标准作为SAE 的工业标准。
此资料应该与其它应用标准和试验方法共同使用(SAE ,美国联邦标准或其它特定试验程序)为特殊的应用或汽车平台来充分评价摩擦材料。
1. 适用范围1.1 SAE 工业标准规定了惯性试验机的试验方法,此方法为配有液压传动制动制动器的汽车在压力,温度和速度方面评价摩擦材料的效能。
1.2 SAE J2522标准的主要目的是在尽可能相同的条件下进行摩擦材料的对比。
为解释不同试验台的冷却工况,其衰退部分由温度控制。
2. 相关参考-这里没有出版的相关参考书目。
3. 定义-为使此资料更便利的使用,应用如下的术语和定义。
3.1 制动过程的摩擦系数值-制动过程所有测得摩擦力的平均值。
3.2 额定摩擦系数值-没有衰退和温度等级的制动过程所有测得摩擦力的平均值。
3.3 最小摩擦系数值-有衰退和温度等级的制动过程所有测得摩擦力的最低算术平均值。
3.4 摩擦系数值-在特定时间点盘式制动器输出与输入扭矩的比值 根据方程1ημ***)(2eff Piston ThresholdBraker A p p Md-=(方程1)3.5 C*值-在特定时间点鼓式制动器输出与输入扭矩的比值根据方程2η***)(2*100*eff p ThresholdBraker A p p MdC -=(方程2)4. 符号和缩写-在试验中用符号和缩写来进行必要的计算4.1 μ-摩擦系数(非单元体) 4.2 BrakeMd-测量扭矩[M N ⋅]4.3 p-制动压力[kPa]4.4 Threshold p -盘式制动的初始压力值为50kPa ,鼓式制动器的初始值根据制动器来确定[kPa]4.5 Ap -活塞面积4.6 r eff -有效半径[mm] 4.7 η-效率100%4.8 60P μ-在6.3中第1次到第6次制动的摩擦系数平均值4.9 120v μ-在6.4.3中压力为2000、3000和4000kPa 制动时的摩擦系数平均值 4.10 max v μ-在6.4.5中压力为2000、3000和4000kPa 制动时的摩擦系数平均值 4.11 60P μ-在6.5中第1次到第六次制动的摩擦系数平均值 4.12 40T μ-在6.6中第1次制动的摩擦系数 4.13 2MW μ-在6.7中第2次制动的摩擦系数4.14 180P μ-在6.8中第1次到第18次制动的摩擦系数平均值 4.15 1F μ-在6.9中第1次到第15次制动的摩擦系数最大值 4.16 180P μ-在6.10中第1次到第18次制动的摩擦系数平均值 4.17 500T μ300/T μ-在6.12.1和6.12.2中温度序列的摩擦系数最小值 4.18 180P μ-在6.13中第1次到第18次制动的摩擦系数平均值 4.19 2F μ-在6.14中第1次到第15次制动的摩擦系数最大值 4.20 180P μ-在6.15中第1次到第18次制动的摩擦系数平均值5. 试验条件5.1 前轴惯量-若没有其它规定按机器总重量的75%计算 5.2 后轴惯量-若没有其它规定按机器总重量的25%计算 5.3 压力增加率-25000kPa/s ±5000kPa5.4 取样率-最短时间为50ms 测取压力和扭矩值5.5 温度测量-位置热电偶置于盘式片外表面或鼓式片接触面的摩擦轨迹中心半径处,附加热电偶置于摩擦材料里来记录温度。
制动标准
制动标准GB 12676—1999 汽车制动系统结构、性能和试验方法GB/T 12676—1990GB 16897—2010 制动软管的结构、性能要求及试验方法GB 16897—1997GB 21670—2008 乘用车制动系统技术要求及试验方法GB/T 5335—2008 汽车液压制动装置压力测试连接器技术要求GB/T 5335—1985GB/T 5345—2008 道路车辆石油基或非石油基制动液容器的标识GB/T 14168—1993、GB/T5345—1985GB/T 5620—2002 道路车辆汽车和挂车制动名词术语及其定义GB/T 5620.1—1985、GB/T5620.2—1985GB/T 5921—1986 汽车和挂车气压制动系部件上接口的识别标记GB/T 5922—2008 汽车和挂车气压制动装置压力测试连接器技术要求GB/T 5922—1986GB/T 7361—1987 半挂牵引车的制动及电路连接位置GB/T 7362—1987 全挂牵引车和货车的制动及电路连接位置GB/T 13594—2003 机动车和挂车防抱制动性能和试验方法GB 13594—1992GB/T 14171—1993 汽车气制动系管路螺纹孔和管接头外螺纹GB/T 30513—2014 乘用车爆胎监测及控制系统技术要求和试验方法QC/T 35—1992(2009) 汽车与挂车气压控制装置台架试验方法QC/T 36—1992(2009) 汽车与挂车气压控制装置通用技术条件QC/T 37—1992(2009) 汽车与挂车气压调节保护装置通用技术条件QC/T 38—1992(2009) 汽车与挂车气压调节保护装置台架试验方法QC/T 77—1993(2009) 汽车液压制动轮缸技术条件QC/T 79.1—2008 道路车辆牵引车和挂车之间气制动连接用螺旋管总成第1部分:尺寸QC/T 79—1993QC/T 79.2—2008 道路车辆牵引车和挂车之间气制动连接用螺旋管总成第2部分:性能要求QC/T 79—1993QC/T 200—1995(2009) 汽车气制动装置用储气筒技术条件QC/T 201—1995 (2009) 汽车气制动用热塑管接头尺寸QC/T 237—1997(2009) 汽车驻车制动器性能台架试验方法QC/T 239—1997(2009) 货车、客车制动器性能要求QC/T 307—1999(2009) 真空助力器技术条件QC/T 311—2008 汽车液压制动主缸性能要求及台架试验方法QC/T 311—1999QC/T 316—1999(2009) 汽车行车制动器疲劳强度台架试验方法QC/T 479—1999(2009) 货车、客车制动器台架试验方法QC/T 556—1999(2009) 汽车制动器温度测量和热电偶安装QC/T 564—2008 乘用车制动器性能要求及台架试验方法QC/T 564—1999QC/T 592—2013 液压制动钳总成性能要求及台架试验方法QC/T 592—1999QC/T 593—1999(2009) 液压感载比例阀技术条件QC/T 764—2006※汽车液压制动系金属管、内外螺纹管接头和软管端部接头GB/T 11611—1989(国标转行标)QC/T 788—2007 汽车踏板装置性能要求及台架试验方法QC/T 789—2007 汽车电涡流缓速器总成性能要求及台架试验方法QC/T 790—2007 制动气室性能要求及台架试验方法QC/T 958—2013 汽车真空泵性能要求及台架试验方法QC/T 959—2013 机械式驻车制动操纵杆总成性能要求及台架试验方法QC/T 960.1—2013 道路车辆液压制动系统第1部分:双喇叭金属管、螺纹孔、螺纹管接头和管座QC/T 961—2013 液压制动系统塑料储液罐性能要求及台架试验方法QC/T29078—1992(2009)汽车用空气压缩机技术条件QC/T29101—1992(2009)汽车用拉索总成*********GB 5763—2008 汽车用制动器衬片GB 5763—1998 GB/T 5766—2007 摩擦材料洛氏硬度试验方法GB/T 5766—1996 GB/T 17469—2012 汽车制动器衬片摩擦性能评价小样台架试验方法GB/T 17469—1998 GB/T 18849—2011 机动工业车辆制动器性能和零件强度GB/T 18849—2002 GB/T 22309—2008 道路车辆制动衬片盘式制动块总成和鼓式制动蹄总成剪切强度试验方法GB/T 22310—2008 道路车辆制动衬片盘式制动衬块受热膨胀量试验方法GB/T 22311—2008 道路车辆制动衬片压缩应变试验方法GB/T 26736—2011 道路车辆制动衬片耐水、盐水、油和制动液性能试验方法GB/T 26737—2011 道路车辆制动衬片锈蚀对铁偶合面粘结影响的试验方法GB/T 26738—2011 道路车辆制动衬片摩擦材料产品确认和质量保证GB/T 26739—2011 道路车辆制动衬片材料内剪切强度试验方法GB/T 26740—2011 道路车辆制动衬片盘式制动衬块试验后表面和材料缺陷的评价方法GB/T 26741—2011 机动三轮车用制动器衬片GB/T 29063—2012 道路车辆制动衬片摩擦材料气制动商用车性能试验方法GB/T 29064—2012 道路车辆制动衬片摩擦材料汽车制动系统摩擦性能评价方法GB/T 29065—2012 道路车辆制动衬片摩擦材料涂漆背板和制动蹄耐腐蚀性能评价方法GB/T 29066—2012 道路车辆制动衬片摩擦材料气制动商用车磨损试验方法。