提高焦炭质量的技术途径
高配比配用贫瘦煤生产优质焦炭技术的开发与应用杨鹏

高配比配用贫瘦煤生产优质焦炭技术的开发与应用杨鹏发布时间:2023-05-10T08:10:44.648Z 来源:《科技新时代》2023年5期作者:杨鹏[导读] 采用贫瘦煤替代瘦煤进行配煤炼焦,降低配合煤成本;同时逐渐加大了配合煤中贫瘦煤的配入比例,在保证焦炭质量的前提下,取得了较大的经济效益。
山西沁新能源集团股份有限公司山西长治 046500摘要:采用贫瘦煤替代瘦煤进行配煤炼焦,降低配合煤成本;同时逐渐加大了配合煤中贫瘦煤的配入比例,在保证焦炭质量的前提下,取得了较大的经济效益。
关键词:贫瘦煤;配煤;煤化度前言焦炭在高炉炼铁过程中起着热源、渗碳、还原剂和骨架的作用,随着高炉容积的不断扩大和喷吹燃料等高炉下部操作的改进,焦炭质量的好坏,对高炉顺行和高炉冶炼的技术经济指标具有重大的影响。
随着国家推进“碳达峰碳中和”政策,节约宝贵的炼焦煤资源是焦化工作者面临的新课题。
发展资源较为丰富的贫瘦煤等非炼焦煤用于配煤炼焦,是扩大炼焦用煤,节约优质炼焦煤,降低成本,提高焦炭质量,解决炼焦煤资源紧缺问题的重要途径之一。
两座JN60-60型焦炉,年产焦炭106万吨,耗洗精煤150余万吨。
今年以来随着炼焦煤价格的大幅上升,优质炼焦煤的供求关系十分紧张,焦化厂生产成本的压力越来越大。
为此,宁钢开发了价格低廉的贫瘦煤替代瘦煤进行配煤炼焦,降低配合煤成本;同时逐渐加大了配合煤中贫瘦煤的配入比例,取得了较大的经济效益。
1贫瘦煤的性质分析贫瘦煤是一种高煤化度、低挥发分、弱粘结性的烟煤。
单独炼焦时,所得焦炭裂纹少、块度大,生成的焦粉多,耐磨强度差。
在配煤炼焦中,可以使焦炭的块度增加,从而起到瘦化剂的作用。
1.1工业分析指标使用的贫瘦煤为三给贫瘦煤,对其进行化验分析,挥发分一般在14~15%,G值在10~20%,Y值在0~6mm之间,按照中国煤炭分类标准,属于贫瘦煤,如表1所示。
表1贫瘦煤的工业分析时间Ad/%G/%Mt/%Std/%Vd/%VdaW X/%Y/mm2021年1月10.6915.0011.330.9713.5915.2220.40 6.002021年2月10.4615.3310.270.8113.0114.9117.00 4.002021年3月10.0310.6711.00 1.0613.1514.6114.470.002021年4月10.0020.0010.57 1.1213.8415.3818.00 3.002021年5月9.7514.0010.40 1.1112.9814.3816.570.002021年6月10.3813.3311.200.8813.1814.7019.270.002021年7月9.9514.0010.330.9213.1014.5518.400.002021年8月10.0015.0011.230.9313.4714.9918.070.002021年9月10.1413.6710.130.8713.3714.9017.200.00 2贫瘦煤的配煤机理研究焦化厂配煤工艺采用先配后粉的流程,因此实验上采用直接配入的方法,即贫瘦煤配合前不需要先破碎,而是随着其他煤种按计划比例配入后,再将配合煤进行粉饰,配合煤细度也按照工业生产要求保持在74~76%。
炼焦新技术

炼焦新技术—煤调湿技术我国现有焦炉生产能力较大,占世界第一位,炼焦煤水分偏高,而且优质炼焦煤日益短缺,围绕现有焦炉和炼焦生产工艺,开发提高焦炭质量和利用炼焦余热的新工艺、新技术是适应企业发展,提高企业经济效益的有效途径。
煤调湿技术可降低入炉煤水分,降低炼焦耗热量,增加入炉煤堆密度,提高焦炭质量。
近几年来,煤调湿技术在国内外炼焦行业异军突起,得到了广泛的应用,究其原因是煤调湿技术具有其独特的优越性:可使焦炭和化工产品增产11%,提高经济效益;焦炉加热用燃料降低,减少耗热量;焦炭质量得到提高;充分利用了焦炉余热,取得了明显的经济和社会效益。
一、煤调湿(Coal Moisture Control ,简称“ CMC ”)技术简述煤调湿技术是通过直接或间接加热来降低并稳定控制入炉煤的水分,该技术不追求最大限度地去除入炉煤的水分,而只把水分稳定在相对低的水平,既可达到增加效益的目的,又不因水分过低而引起焦炉和回收系统操作的困难,使入炉煤密度增大、焦炭及化工产品增产、焦炉加热用煤气量减少、焦炭质量提高和焦炉操作稳定等效果。
二、煤调湿的基本原理利用外界热能将入炉煤在焦炉外干燥,控制入炉煤的水分,从而控制炼焦耗热量、改善焦炉操作、提高焦炭产量或扩大弱粘结性煤的用量。
三、工艺流程及发展煤调湿技术通过直接或间接加热来降低并稳定控制入炉煤水分,并不追求最大限度地去除入炉煤气的水分,而只是把水分稳定在相对较低的水平,就可以达到增加效益的目的,又不会因水分过低而引起焦炉和回收系统操作困难。
煤调湿技术于20世纪80年代初在日本开始应用,历经了3 种工艺技术的变革:第一代是热媒油干燥方式;第二代是蒸汽干燥方式;第三代是最新一代的流化床装置,设有热风炉,采用焦炉烟道废气或焦炉煤气对其进行加热的干燥方式。
1、第一代煤调湿技术第一代CMC是热煤油干燥方式,其工艺见下图。
热媒油式煤调湿工艺流程图利用热油回收焦炉上升管煤气显热和焦炉烟道气的余热,温度升高到195℃的热油通过干燥机将常温的煤预热到80℃,煤的水分由9%左右降到5.7%,调湿后的煤在运输过程中水分还将降低0.7%,装入煤水分保持在5%±0.7%。
降低焦比的措施及原理全解

摘要目前的国际国内趋势下,如何降低焦比的措施及所采取相应的措施,从原料优化到系统设备以及工艺方法等的改进和优化,不断地提升冶炼水平,降低成本,保护环境,保障钢铁事业的稳定快速可持续发展。
本文从焦炭利用,热量有效利用,高炉内还原反应情况等角度出发综合分析并论述了降低高炉焦比的六项具体的途径与措施,即提高铁矿石的品位;采取高风温;喷吹燃料;综合鼓风喷吹;炉顶高压操作;改善焦炭质量,减少灰分。
关键词:节焦,富氧鼓风,提高风温,喷煤,焦炭质量1 前言1.1 焦比焦比是高炉每冶炼一吨生铁所耗用焦炭的公斤数。
它是高炉炼铁的主要技术经济指标。
综合反映了高炉炼铁原料、燃料、设备和技术操作的水平。
1.2 国内焦比情况20世纪六七十年代我国钢铁企业焦比约550kg/t,高炉利用系数在1.5t/(m3.d)左右。
上世纪末焦比降低到520kg/t左右,平均利用系数为1.8t/(m3.d)左右。
近几年焦比平均为300kg/t--420kg/t炉子利用系数上升到2.2t/(m3.d)---2.5t/(m3.d)。
据中国钢铁企业网上的资料显示,2009年前5个月全国重点钢铁企业高炉入炉焦比为374 kg/t,比上年度下降25 kg/t,是近年来下降幅度最大的一年,创造出历史最好水平。
焦比较低的企业有:宝钢294 kg/t,太钢301 kg/t,武钢311 kg/t,首钢314 kg/t,鄂钢330 kg/t,鞍钢331 kg/t,长冶332 kg/t,马钢340 kg/t,湘钢345 kg/t,莱钢348 kg/t;最高值的企业达到549 kg/t。
2 降低焦比的措施2.1 提高矿石品位和还原性铁矿石品位是指铁矿石的含铁量,以TFe%表示,是评价铁矿石质量的主要指标。
铁矿石含铁量高有利于降低焦比和提高产量。
根据生产经验证实,矿石品位提高1%,焦比还原的难易程度, 降低2%,产量提高3%。
铁矿石还原性是指铁矿石被还原性气体CO或H2也是其质量的主要指标。
炼焦配煤

1配煤的必要配煤作为炼焦煤准备的工序之一。
炼焦或碳化前煤料的一个重要准备过程。
即为了生产符合质量要求的焦炭,把不同煤牌号的炼焦用煤按适当的比例配合起来。
炼焦用煤品种较多,应用配煤技术,不仅能保证焦炭质量,还能合理地利用煤炭资源,节约优质炼焦煤,扩大炼焦煤资源。
配煤技术涉及煤的多项工艺性质、结焦特性和灰分、硫分、挥发分的配合性质和煤的成焦机理等。
长期以来,配煤试验一直是选定配煤方案、验证焦炭质量的不可缺少的配煤技术程序早期炼焦只用单种煤,随着焦化行业的发展,炼焦煤储量的明显不足,高炉用焦要求的提高,单种煤已不可能用来炼焦,走配煤之路已势在必行。
如济源金马焦化配煤比:35%ZJM,35%JM,15%FM,15%SM,可练出供济钢用的一级冶金焦,同时加入了肥煤,增加了化产回收,成本在1000元/t,而只用主焦煤炼焦成本在1200元/t,同时降低了化产回收,配煤效益可见一斑。
2 配煤的选择及方法各单种煤的结焦性(1)褐煤褐煤的变质程度高于泥煤而低于分类方案中的其它所有煤种。
在分类方案中,它的可燃基挥发分大于40%,煤中含有多量水分,加热时它不能产生胶质体,因此没有粘结性,在现代炼焦炉中不结焦,我们不将它划分在炼焦煤范围内。
在某些炼焦煤非常缺乏的国家,他们是通过复杂的工艺,利用褐煤制造型块炼成型焦,这已不属配煤炼焦的范畴,故不多述。
(2)长焰煤长焰煤的变质程度比褐煤高,在分类中其可燃基挥发分大于37%,胶质层厚度小于5毫米,这种煤粘结性极弱,在现代炼焦炉中不能单独结成焦炭。
在某些长焰煤多的地区,可以少量配用,但配入量稍多时,常会使焦炭强度和耐磨变坏,尤其是配煤中肥煤不够多时更为明显。
所以长焰煤也不列入炼焦煤范围内。
(3) 气煤气煤的变质程度较长焰煤高。
在分类图中气煤是一大类,它包括可燃基挥发分在30%~37%、胶质层厚度大于9~25毫米以及可燃基挥发分大于37%、胶质层厚度大于5~25毫米两区域。
前者属肥气煤,有一定的结焦性,其中二号肥气煤在现代焦炉中能单独炼焦,但质量较差,只能供中、小高炉使用。
兰炭行业能耗的影响因素及控制措施
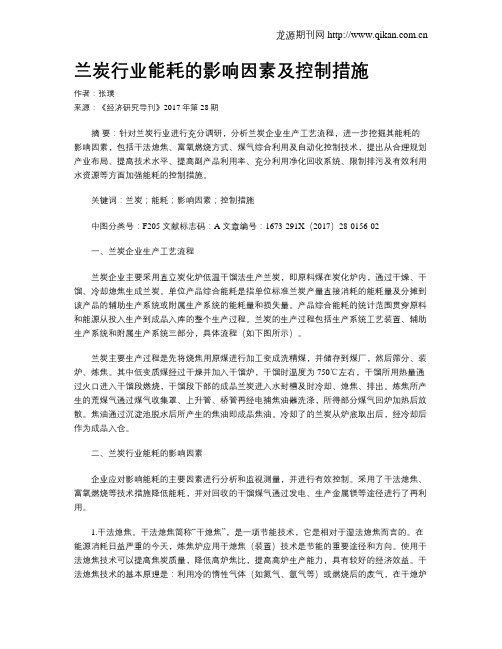
兰炭行业能耗的影响因素及控制措施作者:张璞来源:《经济研究导刊》2017年第28期摘要:针对兰炭行业进行充分调研,分析兰炭企业生产工艺流程,进一步挖掘其能耗的影响因素,包括干法熄焦、富氧燃烧方式、煤气综合利用及自动化控制技术,提出从合理规划产业布局、提高技术水平、提高副产品利用率、充分利用净化回收系统、限制排污及有效利用水资源等方面加强能耗的控制措施。
关键词:兰炭;能耗;影响因素;控制措施中图分类号:F205 文献标志码:A 文章编号:1673-291X(2017)28-0156-02一、兰炭企业生产工艺流程兰炭企业主要采用直立炭化炉低温干馏法生产兰炭,即原料煤在炭化炉内,通过干燥、干馏、冷却熄焦生成兰炭。
单位产品综合能耗是指单位标准兰炭产量直接消耗的能耗量及分摊到该产品的辅助生产系统或附属生产系统的能耗量和损失量。
产品综合能耗的统计范围贯穿原料和能源从投入生产到成品入库的整个生产过程。
兰炭的生产过程包括生产系统工艺装置、辅助生产系统和附属生产系统三部分,具体流程(如下图所示)。
兰炭主要生产过程是先将烧焦用原煤进行加工变成洗精煤,并储存到煤厂,然后筛分、装炉、炼焦。
其中低变质煤经过干燥并加入干馏炉,干馏时温度为750℃左右,干馏所用热量通过火口进入干馏段燃烧,干馏段下部的成品兰炭进入水封槽及时冷却、熄焦、排出。
炼焦所产生的荒煤气通过煤气收集罩、上升管、桥管再经电捕焦油器洗涤,所得部分煤气回炉加热后放散。
焦油通过沉淀池脱水后所产生的焦油即成品焦油。
冷却了的兰炭从炉底取出后,经冷却后作为成品入仓。
二、兰炭行业能耗的影响因素企业应对影响能耗的主要因素进行分析和监视测量,并进行有效控制。
采用了干法熄焦、富氧燃烧等技术措施降低能耗,并对回收的干馏煤气通过发电、生产金属镁等途径进行了再利用。
1.干法熄焦。
干法熄焦简称“干熄焦”,是一项节能技术,它是相对于湿法熄焦而言的。
在能源消耗日益严重的今天,炼焦炉应用干熄焦(装置)技术是节能的重要途径和方向。
提高焦炭质量的技术途径

提升焦炭质量技术路径(一)1.焦炭在高炉炼铁中地位和作用焦炭在高炉炼铁中是不可缺乏炉料, 对高炉炼铁技术进步影响率在30%以上, 在高炉炼铁精料技术中占相关键地位。
焦炭对高炉炼铁作用是:(1)关键热量起源。
高炉炼铁炭素(包含焦炭和煤粉)燃烧所提供热量, 占高炉炼铁总热量起源71%。
伴随喷煤比提升, 焦炭用量在逐步降低。
不过, 焦炭用量总是要大于喷煤量。
理论最低焦比为250kg/t, 焦炭在风口燃烧掉55%~65%。
(2)还原剂。
焦炭还原作用是以C和CO形式来对铁矿石起还原作用。
炉料到风口焦炭溶反应为25%~35%。
(3)生铁溶碳。
在高炉炼铁过程中焦炭中碳是逐步渗透到生铁中。
通常铸造生铁含碳3.9%左右, 炼钢生铁在4.3%左右。
生铁渗碳消耗焦炭7%~10%。
(4)炉料骨架作用焦炭在高炉内是起骨架作用, 支撑着炼铁原料(烧结矿, 球团矿, 天然块矿), 又起到煤气透气窗作用。
焦炭4种作用中, 提供热源主导作用不会改变, 这就决定3个理论焦比最低值。
低于这个最低值, 高炉炼铁就难以正常生产, 或经济上就不合算了。
在多种条件下高炉炼铁中碳还原作用和渗碳功效不会有较大改变。
在高喷煤比条件下, 焦炭骨架作用会显得愈加突出, 对应对焦炭质量要求也会越来越高。
不然, 是难以实现高喷煤比, 高炉炼铁不能正常生产。
焦炭从料线到风口平均粒度降低20%~40%。
劣质焦炭和热反应性差粉化率会很大。
宝钢高炉缸内焦炭粒度可达33mm。
2.高炉炼铁对焦炭质量要求各国依据资源条件, 高炉炼铁要求焦炭质量是有较大差异(详见表1)。
不过, 工业发达国家焦炭质量是显著优于中国, 这是这些高炉技术经济指标优于中国关键原因。
表1 各国冶金焦炭质量情况美国Gary 厂焦炭挥发份为1.8%, 德国蒂森和瑞典SSAB 分别为1.1%和1.0%。
我们认为, 焦炭挥发份应控制在0.5%~1.0%为宜。
过高会有生焦存在, 焦炭强度差; 过低是因为炼焦过火原因, 这时焦炭裂纹多, 易碎。
如何提高焦炭的质量
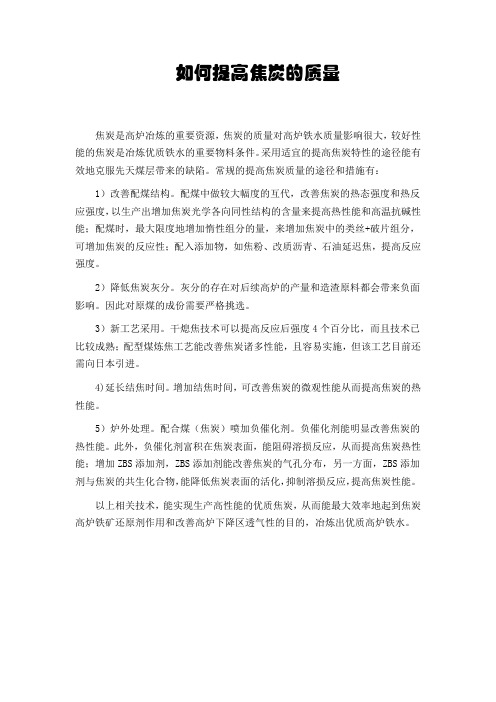
如何提高焦炭的质量
焦炭是高炉冶炼的重要资源,焦炭的质量对高炉铁水质量影响很大,较好性能的焦炭是冶炼优质铁水的重要物料条件。
采用适宜的提高焦炭特性的途径能有效地克服先天煤层带来的缺陷。
常规的提高焦炭质量的途径和措施有:1)改善配煤结构。
配煤中做较大幅度的互代,改善焦炭的热态强度和热反应强度,以生产出增加焦炭光学各向同性结构的含量来提高热性能和高温抗碱性能;配煤时,最大限度地增加惰性组分的量,来增加焦炭中的类丝+破片组分,可增加焦炭的反应性;配入添加物,如焦粉、改质沥青、石油延迟焦,提高反应强度。
2)降低焦炭灰分。
灰分的存在对后续高炉的产量和造渣原料都会带来负面影响。
因此对原煤的成份需要严格挑选。
3)新工艺采用。
干熄焦技术可以提高反应后强度4个百分比,而且技术已比较成熟;配型煤炼焦工艺能改善焦炭诸多性能,且容易实施,但该工艺目前还需向日本引进。
4)延长结焦时间。
增加结焦时间,可改善焦炭的微观性能从而提高焦炭的热性能。
5)炉外处理。
配合煤(焦炭)喷加负催化剂。
负催化剂能明显改善焦炭的热性能。
此外,负催化剂富积在焦炭表面,能阻碍溶损反应,从而提高焦炭热性能;增加ZBS添加剂,ZBS添加剂能改善焦炭的气孔分布,另一方面,ZBS添加剂与焦炭的共生化合物,能降低焦炭表面的活化,抑制溶损反应,提高焦炭性能。
以上相关技术,能实现生产高性能的优质焦炭,从而能最大效率地起到焦炭高炉铁矿还原剂作用和改善高炉下降区透气性的目的,冶炼出优质高炉铁水。
采取技术措施-提高焦炭质量分析
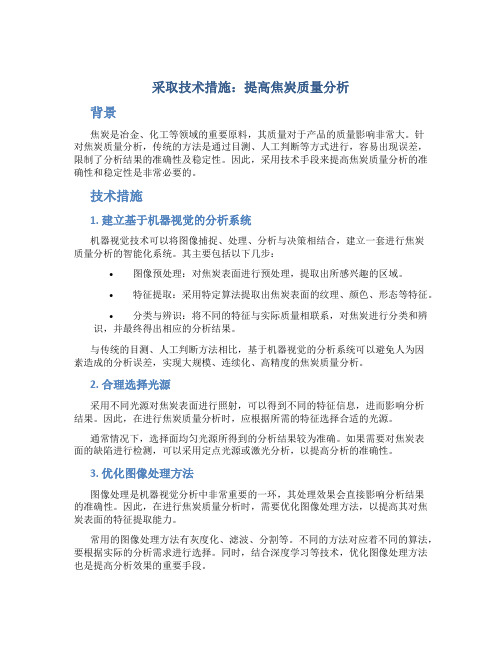
采取技术措施:提高焦炭质量分析背景焦炭是冶金、化工等领域的重要原料,其质量对于产品的质量影响非常大。
针对焦炭质量分析,传统的方法是通过目测、人工判断等方式进行,容易出现误差,限制了分析结果的准确性及稳定性。
因此,采用技术手段来提高焦炭质量分析的准确性和稳定性是非常必要的。
技术措施1. 建立基于机器视觉的分析系统机器视觉技术可以将图像捕捉、处理、分析与决策相结合,建立一套进行焦炭质量分析的智能化系统。
其主要包括以下几步:•图像预处理:对焦炭表面进行预处理,提取出所感兴趣的区域。
•特征提取:采用特定算法提取出焦炭表面的纹理、颜色、形态等特征。
•分类与辨识:将不同的特征与实际质量相联系,对焦炭进行分类和辨识,并最终得出相应的分析结果。
与传统的目测、人工判断方法相比,基于机器视觉的分析系统可以避免人为因素造成的分析误差,实现大规模、连续化、高精度的焦炭质量分析。
2. 合理选择光源采用不同光源对焦炭表面进行照射,可以得到不同的特征信息,进而影响分析结果。
因此,在进行焦炭质量分析时,应根据所需的特征选择合适的光源。
通常情况下,选择面均匀光源所得到的分析结果较为准确。
如果需要对焦炭表面的缺陷进行检测,可以采用定点光源或激光分析,以提高分析的准确性。
3. 优化图像处理方法图像处理是机器视觉分析中非常重要的一环,其处理效果会直接影响分析结果的准确性。
因此,在进行焦炭质量分析时,需要优化图像处理方法,以提高其对焦炭表面的特征提取能力。
常用的图像处理方法有灰度化、滤波、分割等。
不同的方法对应着不同的算法,要根据实际的分析需求进行选择。
同时,结合深度学习等技术,优化图像处理方法也是提高分析效果的重要手段。
结论采取技术手段来提高焦炭质量分析的准确性和稳定性,是冶金、化工等生产领域所必须面对的问题。
如何选择合适的光源、优化图像处理方法,以及建立基于机器视觉的分析系统,是关键的解决策略。
通过这些措施,不仅可以提高焦炭质量分析的准确度和效率,也能为生产的发展提供强有力的支撑。
- 1、下载文档前请自行甄别文档内容的完整性,平台不提供额外的编辑、内容补充、找答案等附加服务。
- 2、"仅部分预览"的文档,不可在线预览部分如存在完整性等问题,可反馈申请退款(可完整预览的文档不适用该条件!)。
- 3、如文档侵犯您的权益,请联系客服反馈,我们会尽快为您处理(人工客服工作时间:9:00-18:30)。
提高焦炭质量的技术途径焦炭在高炉炼铁中的地位和作用焦炭在高炉炼铁中是不可缺少的炉料,对高炉炼铁技术进步的影响率在30%以上,在高炉炼铁精料技术中占有重要的地位。
焦炭对高炉炼铁的作用是:(1)主要的热量来源。
高炉炼铁炭素(包括焦炭和煤粉)燃烧所提供的热量,占高炉炼铁总热量来源的71%。
随着喷煤比的提高,焦炭用量在逐步减少。
但是,焦炭的用量总是要大于喷煤量。
理论最低焦比为250kg/t, 焦炭在风口燃烧掉55%~65%。
(2)还原剂。
焦炭还原作用是以C和CO形式来对铁矿石起还原作用。
炉料到风口焦炭溶反应为25%~35%。
(3)生铁的溶碳。
在高炉炼铁过程中焦炭中的碳是逐步渗透到生铁中。
一般铸造生铁含碳3.9%左右,炼钢生铁在4.3%左右。
生铁渗碳消耗焦炭7%~10%。
(4)炉料的骨架作用。
焦炭在高炉内是起骨架作用,支撑着炼铁原料(烧结矿,球团矿,天然块矿),又起到煤气的透气窗作用。
焦炭的4种作用中,提供热源的主导作用不会改变,这就决定3个理论焦比最低值。
低于这个最低值,高炉炼铁就难以正常生产,或经济上就不合算了。
在各种条件下高炉炼铁中碳的还原作用和渗碳功能不会有较大的变化。
在高喷煤比条件下,焦炭的骨架作用会显得更加突出,相应对焦炭的质量要求也会越来越高。
否则,是难以实现高喷煤比,高炉炼铁不能正常生产。
焦炭从料线到风口平均粒度减少20%~40%。
劣质焦炭和热反应性差粉化率会很大。
宝钢高炉缸内的焦炭粒度可达33mm。
高炉炼铁对焦炭质量的要求各国根据资源条件,高炉炼铁要求的焦炭质量是有较大差别(详见表1)。
但是,工业发达国家的焦炭质量是明显优于中国,这是这些高炉技术经济指标优于中国的重要原因。
表1 各国冶金焦炭质量情况美国Gary厂焦炭的挥发份为1.8%,德国蒂森和瑞典SSAB分别为1.1%和1.0%。
我们认为,焦炭的挥发份应控制在0.5%~1.0%为宜。
过高会有生焦存在,焦炭强度差;过低是由于炼焦过火的原因,这时焦炭裂纹多,易碎。
1 高炉大型化以后对焦炭质量提出了高要求,並对焦炭热性能有要求高炉大型化以后,料柱增高后,料的压缩率提高了,透气性变差。
特别是炉缸容积变大以后,炉缸的焦炭状态对高炉生产的影响更大了。
炼铁工作者希望对不同容积高炉焦炭有不同的质量,详见表2。
焦炭质量标准中应有热性能的要求。
焦炭含有K2O+Na2O有害杂质含量小于3.0Kg/t。
表2 不同容积高炉对焦炭质量要求2 焦炭质量变化对高炉炼铁的影响表3 焦炭质量对高炉炼铁的影响从表3可看出焦炭质量变化对高炉炼铁的影响是比较大的。
通过洗煤可以降低煤炭中的灰分和硫分,采用干法熄焦可以降低焦炭的水分,提高主焦煤的配比和条取综合技术装备可以改善焦炭的M40和M10指标。
从技术上讲上述措施均是可行的。
但是要把技术与经济管理相结合,找出最佳操作点,同时还要考虑到资源供给的条件。
所以各企业要根据客观条件,本企业技术装备现状,科学、合理地提出不同时期不同炉容的高炉对焦炭质量标准。
提高焦炭质量的技术办法1 资源条件的制约据统计,我国煤炭资源保有储量为10070亿吨,其中可开采储量为1891亿吨,但炼焦煤的储量占全国煤炭贮量的25.28%,主要炼焦煤种(焦煤和肥煤) 的储量又在炼焦煤储量的40%以下。
所以,仅靠提高主焦煤的配比来提高焦炭质量是不科学,也不经济的。
现在我国焦炭生产能力已超过3亿吨。
2006年上半年全国规模以上炼焦企业共生产焦炭1.2897亿吨,同比增长13.63%。
按这种发展态势估计,我国炼焦煤资源很快就会出现供应紧张的局面。
所以,我们应依靠炼焦科技进步,逐步减少主焦煤的配比,而又不影响焦炭质量,甚至有所提高,才能实现我国炼焦工业的可持续发展。
2 建立合理的炼焦煤基地和优化配煤焦灰质量的优劣主要取决于炼焦煤的性质。
所以,合理选择炼焦煤基地是保障焦炭质量的首要措施。
炼焦煤基地的理想条件是:煤质好(含碳高,灰分少,含硫低,可磨和可选性好,强粘接性好等)、性能稳定,供应量稳定,价格适中,争取运距短等。
能够实现主焦煤、肥煤、气煤、瘦煤,1/3焦煤(或气肥煤)等煤种的优化配置。
最终炼焦煤的挥发在25%~30%,胶质层厚度Y值为14~18mm,奥亚膨胀度b>20%,基氏流动度MF为50~100ddpm,在配合煤有足够的粘结性时还要配入软固温度区间较大的煤,煤岩相组分比例要适当(在平均最大反射率Rmax<1.3时,惰性组分为25%~32%;在平均最大反射率Rmax>1.3时,惰性组分为25%~30%),煤的灰分、硫分、磷含量、K2O和Na2O 的含量均要符合要求。
一般强粘接性煤配比在55%~60%。
3 优化煤的粉碎工艺炼焦用煤的粉碎和粒度组成对焦炭质量影响较大。
不应当把各种煤先混合再去粉碎,要根据不同煤种(岩相组成的硬度差异),按不同粒度要求进行粉碎和筛分(可使用机械或风力)。
对于硬度较高的气煤等煤种要细破碎,对于易粉碎的焦煤和肥煤可有较大的粒度。
不同煤种,分组进行粉碎,提出不同粒度要求,这叫做选择粉碎煤工艺。
这种工艺能够提高煤的结焦性和减少焦炭裂纹,进而提高焦炭质量。
要通过试验,优化出本企业的最佳配气煤度的方案,来指导炼焦优化生产。
我国炼焦配煤中难破碎的气煤配比较高,要重视对气煤的细粒度要求,是可以获得较好的经济效益。
我国已开发出不同煤种配煤后焦炭性能预测的软件。
4 煤的调湿煤的调湿是将煤在装炉之前除掉一部分水分,并要保证水分低,且稳定。
一般控制水分在6%左右。
脱湿有显著的节能、环保和经济效益,同时可以提高焦炭质量。
如煤的水分能稳定在6%左右,其焦炭产量可提高7.7%,装炉密度可提高4%—7%,转鼓指数D150提高0.8%—1.5%。
煤脱湿可使用流化床技术,用焦炉烟道气与湿煤进行热交换;也可以使用干熄焦发电机抽出的蒸汽为热源,在回转式干燥机(多管)内间接热交换。
5 配添加剂在炼焦煤中适量配入粘结剂、抗裂剂等非煤添加剂,可以改善煤的结焦性能。
配入粘结剂工艺适用于低流动性的弱粘结性的煤种,可以改善焦炭的机械强度和焦炭的反应性。
抗裂剂使用工艺适用于高流动性的高挥发性煤种,可增大焦炭块度,提高强度、改善焦炭气孔结构,提高焦炭反应后强度。
我国一些焦化厂用无烟煤(或焦粉)作为抗裂剂,其技术要求是寻找最佳粒度、配量、混匀方法等。
这样可以扩大炼焦煤源或减缓半焦收缩,增大焦炭块度。
6 煤的捣固把煤捣固,使其密度提高到950—1150kg/m3,可使焦炭M40提高1%—6%,M10降低2%—4%,反应后强度CSR,提高1%—6%。
在焦炭质量变化不大的条件下,煤捣固可以多配5%—20%弱粘结性的气肥煤、气煤,这样可少用主焦煤。
煤捣固的方法,一般是在焦炉外进行。
将煤压块状(可方型、长型、球型等)。
与散状煤料混合装入焦炉,可提高装炉煤料的密度。
当配入30%~50%的型煤时,其煤的密度可达800kg/m3,可以显著改善焦炭质量,同时可以允许增加10%~15%的弱粘结性煤的用量。
7 结焦速度和闷炉降低结焦速度和闷炉都是延长结焦时间。
对于粘结性能好的煤,延长结焦时间可以提高焦炭的强度。
其机理是:焦饼在焦炉内成熟之后,再经过一段时间闷炉,达到提高焦炭质量的目的。
实践表明,延长结焦时间1小时,可提高焦炭M401%。
8 干熄焦采用惰性气体熄灭红热焦炭的熄焦方法称之为干法熄焦。
干熄焦与湿法焦对比、干熄焦的焦炭M40可提高3%~8%,M10降低0.3%~0.8%,焦炭反应必降低,粒度均匀。
进而改善了高炉炼铁技术经济标(焦比降低2%,产量提高1%),提高了钢铁企业的市场竞争力。
干法熄焦可以减少熄焦对环境的污染、同时可以回收红焦显热的80%。
能量转化为电能,又能缓解电力供应紧张。
据计算,年处理能力110万t的干熄焦炭装置,吨焦收益在63.09扣除吨焦综合成本38.70元,可获净利吨焦24.39元。
9 新型熄焦方法改进传统的湿法熄焦,在喷淋量和控制方法上进行改进,即可熄焦,又使焦炭水份降低(在2%~4%)、稳定,粒度均匀,裂纹减少,实现提高焦炭质量。
现在比较成熟的工艺有,德国的稳定熄焦和美钢联的低水分熄焦工艺。
我国莱钢、武钢邯钢和鞍钢等企业已引用。
10 煤预热工艺将装炉煤预热到150~200℃后再装炉,不但可以降低煤中的水份,而且可以提高煤的流动性进而提高了装炉煤的密度。
这样有利于煤的表面粘结和界面反应,进而改善了焦炭的气孔结构,实现焦炭质量的提高。
煤的预热可以提高焦炉的生产能力和降低炼焦工序能耗。
实施煤的预热尚存在一些技术难点,影响了该技术的进一步推广。
11 焦炉应向大型化发展焦炉增加炭化室室容积的办法是可以提主焦炉高度(如由4.3m升高到6m),也可以增加炭化室宽度。
增加焦炉炭化室容积的好处是提高装炉煤的散密度(煤进入高的炭化室下落时间长,动能增大致)使煤压实,炭化室的宽度增大,减少了煤对炭化室炉墙的“边壁效应”),煤饼加大后热态煤颗粒之间接触点多,热解液相产物和气象物多,膨胀压力大,利于煤的表面粘接和界面反应,实现提高焦炭质量和节约能耗。
大型焦炉自动化水平高,生产出焦炭质量稳定,劳动产率高,成本低。
使用同样煤种炼焦,6m焦炉生产的焦炭比4.3m焦炉的M40要高3%~4%,M10降低0.5%。
2 加强对焦炉的管理焦炉的操作水平和热工制度对焦炭质量、焦炉寿命,生产成本均有较大的影响,建立起相应的管理制度。
稳定配煤、稳定操作、稳定焦炭质量是实现焦化生产的前提条件。
要最大限度地减少人为变动因素。
不是搞放卫星创高产活动。
也不要低生产率作业。
任何剧烈的变动,均会影响焦炭质量和焦炉寿命。
建立设备定检定修制度,采用先进的炉体修补技术,加强对人员的继续工程教育,使劳动者的技能得到不断补充和提高是建立现代企业管理制度的需求。
大焦炉要采用自动控温技术,加强日常焦炉热工调节。
对于保证焦炉炉温均匀,焦炭成熟均匀,节能降耗、提高和稳定焦炭质量是十分重要的。
要科学地管理焦炉生产。
专家们认为,在不改变炼焦配煤比条件下,焦炭质量与装炉煤的备煤工艺,炼焦工艺,焦炭的后处理有关。
在顶装煤常规炼焦工艺条件下,焦煤加肥煤配比在50%时,配煤挥发份在20%~30%,胶质层厚度Y值在14~28mm,焦炭质量就可以达到:M40>80%,M10≤7% CSR>60%,CRI<28%。
在顶装煤常规炼焦工艺条件下,再有干熄焦情况下,焦炭质量大体上可以实现M40≥83%,M10≤6.7%,CSR>62%,CRI<26%。
在顶装煤常规炼焦工艺条件下,再有干熄焦加上型煤压块(占15%)情况下,焦炭质量可以实现M40≥88%,M10<6.0%,CSR>66%,CRI<25%。