钢的渗氮技术及检验PPT课件
钢铁零件渗氮层深度测定和金相组织检验

钢铁零件渗氮层深度测定和金相组织检验一、引言随着工业化的发展,钢铁材料在各个行业中得到了广泛应用。
而钢铁零件的质量直接关系到机械设备的性能和安全,因此,对钢铁零件进行渗氮层深度测定和金相组织检验就显得尤为重要。
这两项工作可以有效地评估钢铁零件的质量和使用性能,保障设备的正常运行。
本文将对钢铁零件渗氮层深度测定和金相组织检验进行详细介绍。
二、钢铁零件渗氮层深度测定1.渗氮层深度测定的意义钢铁材料在使用过程中需要具备一定的硬度和耐磨性,而渗氮技术可以有效提高钢铁材料的表面硬度和耐磨性。
因此,渗氮层深度测定是评估渗氮工艺效果的重要手段。
通过测定渗氮层的深度,可以了解到渗氮工艺的渗透程度和均匀性,从而判断钢铁零件的质量和性能。
2.渗氮层深度测定的方法目前,常用的渗氮层深度测定方法主要有金相显微镜法、深度硬度测试法和化学分析法等。
其中,金相显微镜法是最为常用的方法之一。
这种方法利用金相显微镜对试样进行金相观察,通过显微镜下清晰的图像可以准确地判断渗氮层的深度和均匀性。
3.渗氮层深度测定的步骤进行渗氮层深度测定时,首先需要选择合适的试样,然后对试样进行金相显微镜观察,测定渗氮层深度。
具体步骤如下:(1)制备试样:根据需要测定的零件类型和表面情况,选择合适的试样并进行制备。
(2)金相显微镜观察:将试样放入金相显微镜中,调节合适的放大倍数,观察渗氮层的深度和均匀性。
(3)测量和记录:利用金相显微镜对渗氮层的深度进行测量和记录,得出准确的数据。
4.渗氮层深度测定结果的分析得到渗氮层深度测定结果后,需要对数据进行仔细分析。
通过分析可以得出渗氮工艺的效果和存在的问题,为进一步改进和优化工艺提供重要参考依据。
三、金相组织检验1.金相组织检验的意义金相组织检验是评估金属材料组织和性能的重要手段。
通过金相组织检验可以了解到钢铁零件的晶粒结构、相含量、析出物和缺陷等情况,从而评估材料的性能和质量。
2.金相组织检验的方法目前,金相组织检验常用的方法主要有腐蚀剥离法、照相显微镜法和扫描电镜法等。
渗氮及氮化处理

渗氮渗氮,是在一定温度下一定介质中使氮原子渗入工件表层的化学热处理工艺。
常见有液体渗氮、气体渗氮、离子渗氮。
传统的气体渗氮是把工件放入密封容器中,通以流动的氨气并加热,保温较长时间后,氨气热分解产生活性氮原子,不断吸附到工件表面,并扩散渗入工件表层内,从而改变表层的化学成分和组织,获得优良的表面性能。
如果在渗氮过程中同时渗入碳以促进氮的扩散,则称为氮碳共渗。
常用的是气体渗氮和离子渗氮。
原理应用渗入钢中的氮一方面由表及里与铁形成不同含氮量的氮化铁,一方面与钢中的合金元素结合形成各种合金氮化物,特别是氮化铝、氮化铬。
这些氮化物具有很高的硬度、热稳定性和很高的弥散度,因而可使渗氮后的钢件得到高的表面硬度、耐磨性、疲劳强度、抗咬合性、抗大气和过热蒸汽腐蚀能力、抗回火软化能力,并降低缺口敏感性。
与渗碳工艺相比,渗氮温度比较低,因而畸变小,但由于心部硬度较低,渗层也较浅,一般只能满足承受轻、中等载荷的耐磨、耐疲劳要求,或有一定耐热、耐腐蚀要求的机器零件,以及各种切削刀具、冷作和热作模具等。
渗氮有多种方法,常用的是气体渗氮和离子渗氮。
钢铁渗氮的研究始于20世纪初,20年代以后获得工业应用。
最初的气体渗氮,仅限于含铬、铝的钢,后来才扩大到其他钢种。
从70年代开始,渗氮从理论到工艺都得到迅速发展并日趋完善,适用的材料和工件也日益扩大,成为重要的化学热处理工艺之一。
气体渗氮一般以提高金属的耐磨性为主要目的,因此需要获得高的表面硬度。
它适用于38CrMoAl等渗氮钢。
渗氮后工件表面硬度可达HV850~1200。
渗氮温度低,工件畸变小,可用于精度要求高、又有耐磨要求的零件,如镗床镗杆和主轴、磨床主轴、气缸套筒等。
但由于渗氮层较薄,不适于承受重载的耐磨零件。
气体参氮可采用一般渗氮法(即等温渗氮)或多段(二段、三段)渗氮法。
前者是在整个渗氮过程中渗氮温度和氨气分解率保持不变。
温度一般在480~520℃之间,氨气分解率为15~30%,保温时间近80小时。
金属热处理生产工艺 渗氮工艺的技能操作 渗氮工艺的技能操作

6. 操作
(1)升温之前先检查炉子是否漏气,然后通氨气 ,按照工艺 规范加热升温 ,进行排气。
(2)为了减少变形采用阶梯升温方法 , 当炉温到达渗氮温度时, 调节好氨的分解率后开始计保温时间 。当氨分解率达到18% 左右时可点燃废气以保护环境。
(3)为了降低渗层的脆性 ,应进行退氮处理 ,此时应关闭出气 孔 , 只通入少量的氨气以保持炉内正压力。
度≥0.43mm;硬
度要求: 磨去
0. 1mm后硬度≥ 900HV; 畸变要求:
径向圆跳动≤
o.05mm。
2. 渗氮前的预备热处理
(1)调质 。粗车后加热到940 ℃保温2.5~3h ,油冷,在650~ 690 ℃回火,保温3.5h 。调质后硬度为248~280HBS。
(2)高温回火 。半精车后在610 ℃保温5~5.5h ,炉冷至≤ 350℃出炉空冷 。主要是消除机加工过程中的应力, 防止 渗氮过程中变形。
• (5)畸变 。主轴渗氮后精磨0. 1mm,径向跳动 0.03mm为合格 。如变形超差 ,主要原因是渗氮 前未很好地消除应力;温度不均匀 ,升温太快; 零件结构不合理等。
6.2.3训练3 齿轮气体渗氮(中级工)
• 1.技术要求 高速齿轮 ,30万吨合成氨离心空气压缩机的增速 器齿轮 ,材料25Cr2MoV ,渗氮层深0.45~
0.55mm。
• 2.加热设备及渗氮方式的选择 加热设备选用井式气体渗氮炉 ,采用气体渗氮方 式。
• 3.零件预备热处理 齿轮调质处理后精加工 ,精加工后进行消除应力 退火。
5. 质量检验
• (1)表面质量 。 目测氮化表面色泽 ,银灰色、不发亮为正 常 。如果发黑,说明炉内含氧量过高,零件去油污不好 。 解决的办法是检查泄漏 ,并注意清洗零件 ,清洗后一定要 干燥进炉。 (2)表面硬度。用试样检查表面硬度,再磨去0. 1mm后检 测硬度 。发现硬度低 ,说明渗氮温度过高或过低; 时间短 渗层太浅;真空度低 ,漏气造成氧化;氮势不足;材料用 错等 。解决的办法是严格执行工艺 ,检查漏气的原因 ,供 气适当 ,改正材料等。
不锈钢表面离子渗氮技术
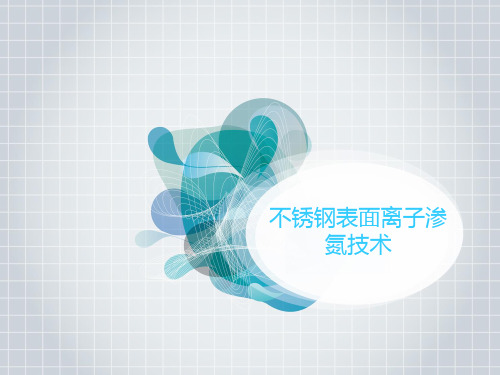
•
渗氮后的不锈钢硬度和耐磨性均有显著提高。但是常规的离子渗氮容易 在不锈钢表面形成CrN而使基体出现贫铬,进而降低不锈钢的耐蚀性。所以, 尽管经离子渗氮处理后不锈钢的表面硬度、耐磨性和抗擦伤、抗胶合能力有 大幅度提高,但若处理不当,容易发生表层剥落、硬化层(渗氮层) 厚度不均 匀以及耐腐蚀性大幅下降等质量问题。
不锈钢表面离子渗 氮技术
•
Hale Waihona Puke 不锈钢应用范围十分广泛。面对当前资源严重短缺的现状,采用各种强 化措施来改善已开发不锈钢钢种的性能,进一步发挥各种不锈钢的优势,拓 展其应用范围,是一项迫切而意义深远的工作。表面改性处理是低成本而有 效提高材料表面硬度、耐磨性和抗疲劳性能的重要方法。
•
由于不锈钢表面氧化膜的存在,使一般的气体渗氮很难进行。虽然表面 活化处理后的不锈钢可以进行气体渗氮处理,但是工序复杂,不易控制,所 以人们逐渐采用了一些新的渗氮工艺技术。离子渗氮技术就是其中应用最广 的一种。常规离子渗氮是在 500~560℃温度下的N2和H2或NH3混合气氛中 进行的。由于离子渗氮能直接去除不锈钢表面的钝化膜,并易于实现局部渗 氮和较容易控制氮势,在不锈钢表面强化方面显示出较大优越性。对一些马 氏体不锈钢进行离子渗氮的结果表明,离子渗氮可有效地在不锈钢表面形成 一定厚度的渗氮层,而不需要进行去除氧化膜的预处理。
•
与渗氮相似,对不锈钢进行渗碳处理也可分为气体渗碳和离子渗碳两大 类型。传统气体渗碳温度很高,一般在800~1000℃,所以对不锈钢很少使 用,主要采用低温离子渗碳技术。低温离子渗碳处理通常在550℃以下进行, 所用气体为H2和CH4或C2H2的混合气体。/
•
为了避免高温下形成CrN,损害不锈钢固有的耐蚀性,必须发展低温处 理方法。上世纪80年代研发了等离子体低温渗氮研究,很好地解决了奥氏体 不锈钢经处理后耐蚀性降低的技术难题。该技术的关键是在低温下(350~ 450℃) 进行,以避免形成CrN而使基体贫铬后耐蚀性下降。
中国古代的钢铁渗碳和渗氮技术全解
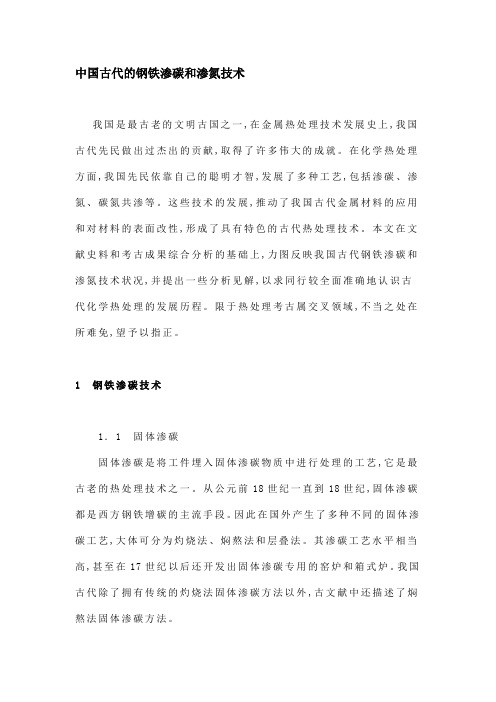
中国古代的钢铁渗碳和渗氮技术我国是最古老的文明古国之一,在金属热处理技术发展史上,我国古代先民做出过杰出的贡献,取得了许多伟大的成就。
在化学热处理方面,我国先民依靠自己的聪明才智,发展了多种工艺,包括渗碳、渗氮、碳氮共渗等。
这些技术的发展,推动了我国古代金属材料的应用和对材料的表面改性,形成了具有特色的古代热处理技术。
本文在文献史料和考古成果综合分析的基础上,力图反映我国古代钢铁渗碳和渗氮技术状况,并提出一些分析见解,以求同行较全面准确地认识古代化学热处理的发展历程。
限于热处理考古属交叉领域,不当之处在所难免,望予以指正。
1 钢铁渗碳技术1.1 固体渗碳固体渗碳是将工件埋入固体渗碳物质中进行处理的工艺,它是最古老的热处理技术之一。
从公元前18世纪一直到18世纪,固体渗碳都是西方钢铁增碳的主流手段。
因此在国外产生了多种不同的固体渗碳工艺,大体可分为灼烧法、焖熬法和层叠法。
其渗碳工艺水平相当高,甚至在17世纪以后还开发出固体渗碳专用的窑炉和箱式炉。
我国古代除了拥有传统的灼烧法固体渗碳方法以外,古文献中还描述了焖熬法固体渗碳方法。
1.1.1 灼烧法固体渗碳一般认为人工冶铁的发源地是两河流域北部、土耳其及其附近地区。
该地有很多的铁矿,而铜矿又较少。
在靠近土耳其的Changar Ba zar镇出土的匕首柄,其年代可定为公元前2700年以前。
而根据报道,在Gizeh的大金字塔内遗存一块铁板,使人工冶炼金属铁板的年代提前到公元前2761年以前。
这些人工冶铁器件是将铁矿石还原后经锻接的产物。
人工冶铁的初级产品是海绵铁,它是由铁矿石在约1200℃的木炭火的温度下还原出来的,海绵铁是杂质含量很高的松散、柔软的金属块,其杂质主要有未还原的氧化铁、铁橄榄石、木炭粉等,为了用它制作器物,只有将其反复加热锻打、去渣、聚块、分散杂质后,才能获得可以造型的熟铁,这种熟铁通常被称为块炼铁。
海绵铁的加热往往是在灼热的木炭中进行,其时铁被埋在木炭之间,在铁的作用下,未完全燃烧的一氧化碳发生分解,分解的活性碳形成高的碳势,铁在碳势气氛中,自然而然地被渗碳。
65mn渗氮在零件表面的氮化物厚度

一、概述1.1 介绍65Mn渗氮技术65Mn钢是一种经常用于制造机械零部件的优质碳素钢,其具有良好的韧性和强度,被广泛应用于机械制造领域。
为了提高其表面硬度和耐磨性,常采用渗氮技术进行处理。
通过在65Mn钢表面形成氮化层,可以显著改善其性能,延长使用寿命。
1.2 目的和意义65Mn渗氮在零件表面形成的氮化层的厚度对零件的使用性能具有重要影响。
本文旨在探讨65Mn渗氮工艺对氮化物层厚度的影响,以为相关行业提供参考和指导。
二、65Mn渗氮工艺2.1 渗氮原理65Mn渗氮是将成品零件置于含氮化剂的气氛中进行热处理,使得氮原子在零件表面扩散并与基体元素形成氮化物层。
常用的渗氮工艺包括氨气渗氮、氮气渗氮和氮化钠渗氮等。
2.2 渗氮参数渗氮工艺中的参数设置对氮化层的形成有着至关重要的影响,包括温度、时间、气氛成分等。
合理的参数设置可以保证氮化层在零件表面的均匀性和稳定性。
2.3 后处理工艺渗氮完成后,通常还需要进行调质处理或回火处理,以消除残余应力和提高零件整体性能。
三、影响氮化层厚度的因素3.1 温度温度是影响氮化层厚度的重要因素之一。
较高的温度可以加快氮原子的扩散速度,促进氮化层的形成,但过高的温度也容易造成表面粗晶和氮化层过厚。
3.2 时间渗氮时间的长短直接影响着氮化层的厚度,渗氮时间过短则可能导致氮化层太薄,而过长则会增加生产成本,适当的时间是保证氮化层质量的关键。
3.3 渗氮气氛渗氮过程中的气氛成分对氮化层的形成也有重要影响。
不同组成的气氛将影响着氮原子的扩散速度和形成氮化物的能力。
3.4 基体材料基体材料的成分和结构对氮化层的厚度同样具有影响。
不同的材料可能会有不同的扩散速率和形成能力,从而影响氮化层的厚度和性能。
四、氮化层厚度测试方法4.1 金相显微镜观察法金相显微镜是常用于观察金属材料显微组织和氮化层厚度的测试方法之一。
通过金相显微镜观察样品的横截面,对氮化层厚度进行测量和分析。
4.2 检测设备X射线衍射仪、扫描电镜和硬度计等设备也常用于氮化层的厚度和性能测试,在实际生产制造中,根据需求和条件选用合适的测试方法和设备。
不锈钢低温渗氮工艺
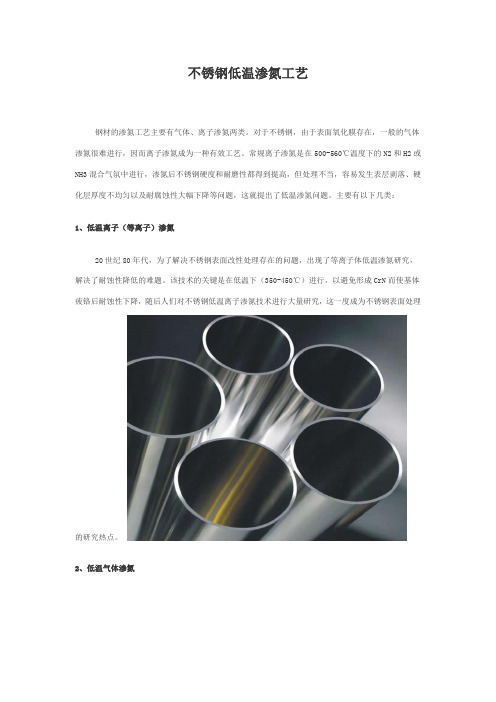
不锈钢低温渗氮工艺钢材的渗氮工艺主要有气体、离子渗氮两类。
对于不锈钢,由于表面氧化膜存在,一般的气体渗氮很难进行,因而离子渗氮成为一种有效工艺。
常规离子渗氮是在500-560℃温度下的N2和H2或NH3混合气氛中进行,渗氮后不锈钢硬度和耐磨性都得到提高,但处理不当,容易发生表层剥落、硬化层厚度不均匀以及耐腐蚀性大幅下降等问题,这就提出了低温渗氮问题。
主要有以下几类:1、低温离子(等离子)渗氮20世纪80年代,为了解决不锈钢表面改性处理存在的问题,出现了等离子体低温渗氮研究,解决了耐蚀性降低的难题。
该技术的关键是在低温下(350-450℃)进行,以避免形成CrN而使基体疲铬后耐蚀性下降,随后人们对不锈钢低温离子渗氮技术进行大量研究,这一度成为不锈钢表面处理的研究热点。
2、低温气体渗氮在不锈钢的低温离子渗氮研究如火如荼地开展的同时,另一些研究者对气体渗氮进行了改进,开发了低温气体渗氮技术(<500℃)。
科研人员利用离子溅射+低温气体渗氮的方法对不锈钢成功进行了改性处理,获得的改性层不仅具有很高的硬度,还有很高的耐磨性。
3、其它低温渗氮低温等离子体渗氮技术已用于工业生产,但在实际中发现,等离子体低温渗氮也有本身的缺点,如边界效应、空心阴极效应,以及工件温度不均等。
为了克服离子渗氮的缺点,人们开发了阴极笼或活化屏离子渗氮技术,在活化屏渗氮技术中,工件处于悬浮状态,离子轰击金属屏而不是工件本身。
与常规离子渗氮相比,该技术可以处理不同形状的工件,并能消除边缘效应以及空心阴极效应,还能方便地测量工件的温度等。
这些渗氮工艺在不锈钢表面改性方面,处理效果十分诱人,但目前这些主要集中在奥氏体不锈钢方面,对于马氏体不锈钢方面国内研究很少,借助现用研究结果,马氏体不锈钢采用低温渗氮后,性能也得到大幅改善,这是一个新的领域。
归纳之,低温处理工艺对不锈钢渗氮改性效果十分适合。
资料整理——东莞市泽洋金属材料有限公司(东莞泽洋金属材料)。
渗氮处理及工艺,总结的挺全面

渗氮处理及工艺,总结的挺全面渗氮又称氮化,指使氮原子渗入钢铁工件表层内的化学热处理工艺,其目的是提高零件表面硬度和耐磨性,以及提高疲劳强度和抗腐蚀性。
它是利用氨气在加热时分解出活性氮原子,被零件吸收后在其表面形成氮化层,同时向心部扩散。
氮化通常利用专门设备或井式渗氮炉来进行。
气体渗氮在1923年左右,由德国人Fry首度研究发展并加以工业化,目前渗氮从理论到工艺都得到迅速发展并日趋完善,适用的材料和工件也日益扩大。
由于经渗氮处理的制品具有优异的耐磨性、耐疲劳性、耐蚀性、耐高温性、抗咬合性、抗大气和过热蒸汽腐蚀能力、抗回火软化能力,并降低缺口敏感性,与渗碳工艺相比,渗氮温度比较低,因而工件畸变小,已成为重要的化学热处理工艺之一,广泛应用于机械、冶金和矿山等行业的齿轮、凸轮、曲轴、工具、冷作模具、热作模具等零件和产品的表面处理。
一、氮化常用材料传统的合金钢材料中的铝、铬、钒及钼元素在渗氮过程中,与初生态的氮原子接触时,就能生成安定的氮化物,尤其是钼元素,不仅是生成氮化物元素,还能降低在渗氮时所产生的脆性。
其他合金钢中的元素,如镍、铜、硅、锰等,对渗氮特性并无多大的帮助。
一般而言,如果钢料中含有一种或多种的氮化物生成元素,氮化后的效果比较良好。
其中铝是最强的氮化物元素,含有0.85~1.5%铝的渗氮结果最佳,如果有足够的铬含量,亦可得到很好的效果,没有含合金的碳钢,因其生成的渗氮层很脆,容易剥落,不适合作为渗氮钢。
二、渗氮过程控制1.渗氮前的零件表面清洗通常使用气体去油法去油后立刻渗氮2.排除渗氮炉中的空气将被处理零件置于渗氮炉中,并将炉盖密封后即可加热,但加热至150℃以前须作排除炉内空气工作。
排除炉内空气的主要目的是使参与渗氮处理的气体,只有氨气和氮气两种气体,防止氨气分解时与空气接触而发生爆炸性气体,及防止被处理零件及支架的表面氧化。
3.氨的分解率渗氮是其它合金元素与初生态的氮接触而进行(初生态氮的产生,由氨气与加热中的零件接触时零件本身成为触媒而促进氨的分解),虽然在各种分解率的氨气下,皆可渗氮,但一般都采用15~30%的分解率,并按渗氮所需厚度保持4~10小时,处理温度保持在520℃左右。