连铸主要设备介绍页PPT文档
合集下载
连铸可视化说明书PPT课件

77336723料位计配电+器 7384配电器切断阀 78339056无纸记热录电仪+阻
保温24定7#炉测子空厚温气4仪度调5节反馈 27 3
保温15定2#炉测子空厚温气1仪度0调6节控制
5 1559
风机房、循环水站、一混二混、一烧 6 16260
7 16271 8 16282
主体、转炉泥。 9 16593
DP:5
频器
频器
频器
频器
1流马达柜
液压站
ET200S 7
DP:2
结晶器电搅
ET200S DP:5
DCD:台下
ET200M
4流电搅变 DP:8
公用马达柜
ET200S DP:6
频器 显示屏 DP:9
3流电搅变 频器 1流/2流/3流/4流
DP:11/12/13/14
末端电搅
大包回转台/
2流电搅变 频器 DP:10/12/13/14/15/16
执行器+ 二点混22火加#1定风蒸水子箱汽流温压调量度力节反1 反馈馈信号
风机房
9 8397热电阻调节+阀 1#2环煤冷气机总2出管口压压力力
18 35
99330189差压变压送力器+变送2冷点#器4环却火冷器炉机进煤3出水气口流压压量力力
19 9420配电器
+
2电机进水流量
35 9431流量开关
16 9442
转炉泥
差压配变电+送器器1引机风#风火尾2机9箱空除入压气尘口力压出温7力口度压力
23 24
77221278调节器差压+变送点火器41定空#测子气厚温调1仪度节3控制
电 阀动热调电++节阻碟2炉#一风1膛混箱压加压力水力压21力
炼钢连铸工艺介绍PPT课件

2). 结晶器振动。铸坯表面薄弱点是弯月面坯壳形成 “振动痕迹”。易在波谷处形成横裂纹、气泡。采用高频 小振幅的结晶器振动机构,可以减少振痕深度。
.
26
提高连铸坯表面质量的措施
3). 初生坯壳的均匀性。结晶器弯月面初生坯壳不均 匀会造成纵裂和凹陷,导致拉漏。坯壳生成的均匀性决 定于钢成分、结晶器冷却、钢液面稳定性和保护渣润滑 性能。
沿窄面向上流股动量太强或流股中含有沿窄面向上流股动量太强或流股中含有气泡降低了密度流股向上提升引起了弯月气泡降低了密度流股向上提升引起了弯月面区液面波动太大液渣渗入到坯壳与铜板的面区液面波动太大液渣渗入到坯壳与铜板的气隙困难导致弯月面的不均匀热流从而产气隙困难导致弯月面的不均匀热流从而产生纵裂纹
阳春新钢铁连铸工艺介绍
2.中间包:它的作用是减压、稳流、去渣、 贮钢、分流和中间包冶金等重要作用。
3.中包小车:它的作用是用来支撑、运输、 更换中间包的设备。
.
3
4.结晶器:它的作用是一个水冷的钢锭模,是 连铸机非常重要的部件,是连铸设备的心 脏。
5.结晶器振动装置:它的作用是固定结晶器、 铸坯脱模。
6.二次冷却系统装置:它的作用是冷却、支 撑、导向。
⑴钢中总氧法
钢中的氧以两种形式存在:溶解于钢中的 溶解氧和存在于氧化物的氧,钢中的总氧 含量是两者之和。钢中的总氧含量越低, 说明钢中氧化物夹杂越少,钢就越干净。
⑵钢中酸溶铝损失法
.
15
定义:二次氧化是指钢水中的合金元素与空气中的 氧、炉渣、耐火材料中的氧化物发生化学反应,生 成新的氧化物相而污染钢水。 2.1:钢水与空气的二次氧化: 2.1.1:注流与空气接触吸氧 2.1.2:注流卷入空气吸氧 2.1.3:钢水裸露吸氧 2.2:钢水与耐火材料的二次氧化: 2.2.1:中间包衬 包衬材料中含有SiO2被钢水中的Al还原生成Al2O3, 使钢洁净度降低。因此,中间衬向碱性材质方向发 展。
.
26
提高连铸坯表面质量的措施
3). 初生坯壳的均匀性。结晶器弯月面初生坯壳不均 匀会造成纵裂和凹陷,导致拉漏。坯壳生成的均匀性决 定于钢成分、结晶器冷却、钢液面稳定性和保护渣润滑 性能。
沿窄面向上流股动量太强或流股中含有沿窄面向上流股动量太强或流股中含有气泡降低了密度流股向上提升引起了弯月气泡降低了密度流股向上提升引起了弯月面区液面波动太大液渣渗入到坯壳与铜板的面区液面波动太大液渣渗入到坯壳与铜板的气隙困难导致弯月面的不均匀热流从而产气隙困难导致弯月面的不均匀热流从而产生纵裂纹
阳春新钢铁连铸工艺介绍
2.中间包:它的作用是减压、稳流、去渣、 贮钢、分流和中间包冶金等重要作用。
3.中包小车:它的作用是用来支撑、运输、 更换中间包的设备。
.
3
4.结晶器:它的作用是一个水冷的钢锭模,是 连铸机非常重要的部件,是连铸设备的心 脏。
5.结晶器振动装置:它的作用是固定结晶器、 铸坯脱模。
6.二次冷却系统装置:它的作用是冷却、支 撑、导向。
⑴钢中总氧法
钢中的氧以两种形式存在:溶解于钢中的 溶解氧和存在于氧化物的氧,钢中的总氧 含量是两者之和。钢中的总氧含量越低, 说明钢中氧化物夹杂越少,钢就越干净。
⑵钢中酸溶铝损失法
.
15
定义:二次氧化是指钢水中的合金元素与空气中的 氧、炉渣、耐火材料中的氧化物发生化学反应,生 成新的氧化物相而污染钢水。 2.1:钢水与空气的二次氧化: 2.1.1:注流与空气接触吸氧 2.1.2:注流卷入空气吸氧 2.1.3:钢水裸露吸氧 2.2:钢水与耐火材料的二次氧化: 2.2.1:中间包衬 包衬材料中含有SiO2被钢水中的Al还原生成Al2O3, 使钢洁净度降低。因此,中间衬向碱性材质方向发 展。
连铸工艺、设备06连铸保护浇注.pptx

2.钢包渣中(FeO+MnO)含量越高,钢水中 ∑[O]也就越高。
因此转炉出钢时应采取挡渣措施,尽量减 少下渣,同时也要防止钢包渣下到中间包, 以免影响中间包钢水质量。
② 钢水与水口耐火材料相互作用
熔融石英质水口不能浇高锰钢的原因是发 生了以下反应:
2[Mn]+(SiO2)=2(MnO)+[Si] (MnO)+(SiO2)=MnO·SiO2
四.钢液与渣相的相互作用
1.转炉出钢时,高碱度高氧化性的渣子进入钢 包,使加入的铁合金回收率不稳定;悬浮 在钢水中的渣滴在上浮过程中会与钢水中 的Al、Si、Mn等元素发生化学反应,成为 铸坯中夹杂物来源之一。
§6—2 浇注过程中二次氧化源
浇注过程二次氧化源是: A.注流与空气接触直接吸氧; B.中间包、结晶器钢液面与空气相互作用; C.钢水与耐火材料、保护渣相互作用; D.卷入的渣滴与钢水相互作用。
连铸过程二次氧化源: 1—钢∕空气; 2—渣∕钢; 3—包衬∕钢; 4—卷入气泡和炉渣质点; 5—耐火材料∕钢; 6—保护渣∕钢
特征:分布均匀;颗粒细小。
B.外来夹杂物
从炼钢到浇注的全过程中,钢液与空气、 耐火材料、炉渣相互作用的产物以及耐火 材料、熔渣等在冶炼、出钢、浇注过程中 进入钢中并滞留在钢中造成的夹杂物。
特征:组成复杂、外形不规则;尺寸比较 大;偶然地在这里或那里出现。
连铸坯中外来夹杂物主要来源: A.二次氧化产物 浇注过程中钢包和中间包的钢水注流,结晶器液面裸露与大
第六章 连铸保护浇注 §6—1 钢水二次氧化与钢的清洁度
一.钢清洁度及铸坯中夹杂物的特征 1.钢的清洁度:
指钢中非金属夹杂物的数量、尺寸、分布和 形态。
2.连铸坯夹杂物按来源分类:
A. 内生夹杂物
因此转炉出钢时应采取挡渣措施,尽量减 少下渣,同时也要防止钢包渣下到中间包, 以免影响中间包钢水质量。
② 钢水与水口耐火材料相互作用
熔融石英质水口不能浇高锰钢的原因是发 生了以下反应:
2[Mn]+(SiO2)=2(MnO)+[Si] (MnO)+(SiO2)=MnO·SiO2
四.钢液与渣相的相互作用
1.转炉出钢时,高碱度高氧化性的渣子进入钢 包,使加入的铁合金回收率不稳定;悬浮 在钢水中的渣滴在上浮过程中会与钢水中 的Al、Si、Mn等元素发生化学反应,成为 铸坯中夹杂物来源之一。
§6—2 浇注过程中二次氧化源
浇注过程二次氧化源是: A.注流与空气接触直接吸氧; B.中间包、结晶器钢液面与空气相互作用; C.钢水与耐火材料、保护渣相互作用; D.卷入的渣滴与钢水相互作用。
连铸过程二次氧化源: 1—钢∕空气; 2—渣∕钢; 3—包衬∕钢; 4—卷入气泡和炉渣质点; 5—耐火材料∕钢; 6—保护渣∕钢
特征:分布均匀;颗粒细小。
B.外来夹杂物
从炼钢到浇注的全过程中,钢液与空气、 耐火材料、炉渣相互作用的产物以及耐火 材料、熔渣等在冶炼、出钢、浇注过程中 进入钢中并滞留在钢中造成的夹杂物。
特征:组成复杂、外形不规则;尺寸比较 大;偶然地在这里或那里出现。
连铸坯中外来夹杂物主要来源: A.二次氧化产物 浇注过程中钢包和中间包的钢水注流,结晶器液面裸露与大
第六章 连铸保护浇注 §6—1 钢水二次氧化与钢的清洁度
一.钢清洁度及铸坯中夹杂物的特征 1.钢的清洁度:
指钢中非金属夹杂物的数量、尺寸、分布和 形态。
2.连铸坯夹杂物按来源分类:
A. 内生夹杂物
5-连铸设备与工艺

17
机型的特点
(4)弧形连铸机
分为弧形结晶器和直结晶器两种
优点:
机身高度为立式连铸机的1/2~1/3, 占地面积和 立弯式相同,基建费用低;
钢液静压小,鼓肚、裂纹等缺陷少;
加长机身容易,可高速浇铸,生产率高;
18
机型的特点
缺点:
〃 机器设备占地面积较立式大; 〃 内弧夹杂物容易集聚; 〃 弧形结晶器加工较复杂; 〃 直结晶器在出口处为弧形和 直线切点,容易漏钢。
提高金属的收得率 7~12%。
建设费用降低30%左 右。 有助于实现钢铁生产的 紧凑化和连续化。 改善作业环境。 节约能源及原材料消耗, 降低人工费用.
12
5.1.2 连铸机的机型及其特点
1) 连铸机的机型
(1) 按外形分类;
13
(2)按铸坯断面分类
表 各种机型浇注的铸坯断面(㎜×㎜)
机型
最大断面 mm×mm 300×2640 310×2500 最小断面 mm×mm 130×250 经常浇注断面 mm×mm 180×700~ 300×2000
16
机型的特点
(3)带直线段的弧形连铸机
有垂直段,夹杂物容易上浮,具有立弯式连铸机的优点; 多点弯曲。减小应力集中,裂纹少; 可在未完全凝固进入弧形段,故可以提高生产率,增大 拉速。 例如:宝钢板坯连铸机: 直线段: 2.55m 弯曲半径:48.5/22.5/16.5/12/9.555m 矫直半径:9.555/11.5/16/31m 连铸机长度:39.39m
9
1958年我国的第一台连铸机在重庆第三 钢铁厂建成。
50~60年代,连铸技术发展缓慢。
连铸坯的质量不如模铸。 对已经建成的初轧机的依赖。
连铸工艺设备连铸坯凝固与传热培训ppt课件

21
21
21
最大的热阻是来自于坯壳与结晶器 壁之间的气隙。
21
结晶器横向气隙的形成:
结晶器传热示意图:
21
2.影响结晶器传热的主要因素⑴结晶器设计参数对传热的影响 A.结晶器锥度的影响
合适的倒锥度,可以减小下部气隙厚 度,改善传热。
结晶器长度以不增加拉漏为原则。通常为700~900mm。对传热影响不大。
角部成了坯 壳最薄弱的部位。
21
结晶器内气隙的形成过程:
21
坯壳急剧收缩是导致结晶器最大热流减少的原因
21
减轻弯月面区坯壳过度收缩、减少凹陷的形成的措施
21
二.结晶器坯壳生长规律结晶器内坯壳的生长规律服从平方根定律:
21
铸坯表面组织的形成:
21
促进结晶器坯壳均匀生长的操作注意事项
21
三.结晶器传热与热阻
2.弯月面的形成
10
钢液与铜壁弯月面的形成:
10
良好稳定的弯月面可确保初生坯壳的表面质量和坯壳的均匀性。带有夹渣的坯壳是薄弱部位,易发生漏钢。
10
10
4.气隙的形成、稳定及角部气隙
已凝固的高温坯壳发生δ→γ的相变,引起坯壳收缩,收缩力牵引坯壳离开铜壁,气 隙开始形成。周期 性的离合2~3次,坯壳达到一定厚度并完 全脱离铜壁,气隙稳定形成。
二冷区铸坯表面热量传递方式:
37
铸坯二冷传热方式:
37
二.影响二冷区传热的因素
54
表面温度与热流的关系:
54
54
54
三.二冷区凝固坯壳的生长
54
54
四.铸坯的液相穴深度
54
§3—4 连铸坯凝固结构
54
21
21
最大的热阻是来自于坯壳与结晶器 壁之间的气隙。
21
结晶器横向气隙的形成:
结晶器传热示意图:
21
2.影响结晶器传热的主要因素⑴结晶器设计参数对传热的影响 A.结晶器锥度的影响
合适的倒锥度,可以减小下部气隙厚 度,改善传热。
结晶器长度以不增加拉漏为原则。通常为700~900mm。对传热影响不大。
角部成了坯 壳最薄弱的部位。
21
结晶器内气隙的形成过程:
21
坯壳急剧收缩是导致结晶器最大热流减少的原因
21
减轻弯月面区坯壳过度收缩、减少凹陷的形成的措施
21
二.结晶器坯壳生长规律结晶器内坯壳的生长规律服从平方根定律:
21
铸坯表面组织的形成:
21
促进结晶器坯壳均匀生长的操作注意事项
21
三.结晶器传热与热阻
2.弯月面的形成
10
钢液与铜壁弯月面的形成:
10
良好稳定的弯月面可确保初生坯壳的表面质量和坯壳的均匀性。带有夹渣的坯壳是薄弱部位,易发生漏钢。
10
10
4.气隙的形成、稳定及角部气隙
已凝固的高温坯壳发生δ→γ的相变,引起坯壳收缩,收缩力牵引坯壳离开铜壁,气 隙开始形成。周期 性的离合2~3次,坯壳达到一定厚度并完 全脱离铜壁,气隙稳定形成。
二冷区铸坯表面热量传递方式:
37
铸坯二冷传热方式:
37
二.影响二冷区传热的因素
54
表面温度与热流的关系:
54
54
54
三.二冷区凝固坯壳的生长
54
54
四.铸坯的液相穴深度
54
§3—4 连铸坯凝固结构
54
连铸工艺设备09连铸坯质量控制PPT课件

11
二.连铸坯夹杂物
1.连铸坯夹杂物的形成特征
一是连铸坯由于钢液凝固速度快,其夹杂物 聚集长大机会少,因而尺寸较小,不易从钢 液中上浮;
其二是多了一个中间包,钢液和大气、熔渣、 耐火材料接触时间长易被污染;同时在钢液 进入结晶器后,在钢液流股影响下,夹杂物 难以从钢液分离;
其三是连铸坯仅靠切头切尾难以解决夹杂物 问题。
对于带垂直段的立弯式连铸机,结晶器注流 冲击深度的影响区在直线部分,夹杂物在夜 相穴内容易上浮,铸坯中夹杂物分布均匀。
14
液相穴内夹杂物上浮示意图: a—带垂直段立弯式连铸机; b—弧形连铸机
15
16
B.连铸操作对铸坯中夹杂物的影响
连铸操作有正常浇注和非正常浇注两种情况。
在正常浇注下,浇注过程比较稳定,铸坯中 夹杂物多少主要由钢液的纯净度决定。
符合规定要求。 铸坯的外观形状与结晶器内腔尺寸和表面
状态及冷却的均匀性有关。
5
连铸坯质量控制示意图:
6
§9—1 铸坯纯净度
一.铸坯纯净度与产品质量 连铸坯的纯净度是指钢中夹杂物的数量、
形态和分布。 1.连铸坯中夹杂物特点: ① 来源广泛,组成复杂; ② 结晶器液相穴内夹杂物上浮困难。
7
2.钢中夹杂物分类: ① 超显微夹杂,均匀分布在钢中; ② 显微夹杂,其尺寸小于50µm,它与钢中溶
17
C.在操作中,注温和拉速对铸坯中夹杂物也有 一定影响
当钢液温度降低时,夹杂物指数升高;随着 拉速的提高,铸坯中夹杂物有增多的趋势。
D.耐火材料质量对铸坯夹杂物的影响 注连铸过程中由于钢液和耐火材料接触,
钢液中的元素(锰和铝等)会与耐火材料中 的氧化物发生作用生成夹杂物,当其不能上 浮时就遗留在铸坯中。
二.连铸坯夹杂物
1.连铸坯夹杂物的形成特征
一是连铸坯由于钢液凝固速度快,其夹杂物 聚集长大机会少,因而尺寸较小,不易从钢 液中上浮;
其二是多了一个中间包,钢液和大气、熔渣、 耐火材料接触时间长易被污染;同时在钢液 进入结晶器后,在钢液流股影响下,夹杂物 难以从钢液分离;
其三是连铸坯仅靠切头切尾难以解决夹杂物 问题。
对于带垂直段的立弯式连铸机,结晶器注流 冲击深度的影响区在直线部分,夹杂物在夜 相穴内容易上浮,铸坯中夹杂物分布均匀。
14
液相穴内夹杂物上浮示意图: a—带垂直段立弯式连铸机; b—弧形连铸机
15
16
B.连铸操作对铸坯中夹杂物的影响
连铸操作有正常浇注和非正常浇注两种情况。
在正常浇注下,浇注过程比较稳定,铸坯中 夹杂物多少主要由钢液的纯净度决定。
符合规定要求。 铸坯的外观形状与结晶器内腔尺寸和表面
状态及冷却的均匀性有关。
5
连铸坯质量控制示意图:
6
§9—1 铸坯纯净度
一.铸坯纯净度与产品质量 连铸坯的纯净度是指钢中夹杂物的数量、
形态和分布。 1.连铸坯中夹杂物特点: ① 来源广泛,组成复杂; ② 结晶器液相穴内夹杂物上浮困难。
7
2.钢中夹杂物分类: ① 超显微夹杂,均匀分布在钢中; ② 显微夹杂,其尺寸小于50µm,它与钢中溶
17
C.在操作中,注温和拉速对铸坯中夹杂物也有 一定影响
当钢液温度降低时,夹杂物指数升高;随着 拉速的提高,铸坯中夹杂物有增多的趋势。
D.耐火材料质量对铸坯夹杂物的影响 注连铸过程中由于钢液和耐火材料接触,
钢液中的元素(锰和铝等)会与耐火材料中 的氧化物发生作用生成夹杂物,当其不能上 浮时就遗留在铸坯中。
《方坯连铸机》课件

定期清洁
定期对设备进行清洁,保 持设备整洁,防止灰尘和 杂物影响设备的正常运行 。
定期更换易损件
对设备中的易损件进行定 期更换,如轴承、密封件 等,确保设备的稳定运行 。
常见故障及排除方法
漏钢事故
裂纹事故
当发现漏钢事故时,应立即停机检查 ,可能是由于结晶器或二冷室堵塞等 原因引起的。应清理结晶器和二冷室 ,确保其通畅。
方坯连铸机的工作原理
总结词
方坯连铸机通过将熔融金属浇注到结晶器中,经过冷却、凝固后,将固态方坯从 结晶器中拉出,再经过切割、矫直等工序,形成成品方坯。
详细描述
熔融金属在达到合适的温度和成分后,通过钢包注入到结晶器中。结晶器是一个 铜制外壳,内部有冷却水,使金属快速冷却并开始凝固。随着结晶器的移动,固 态方坯被拉出并经过切割、矫直等工序,最终形成成品方坯。
结晶器
• 结晶器:方坯连铸机中的核心部件,用于使钢水冷却凝固 成固体并形成一定形状的钢坯。
二次冷却系统
• 二次冷却系统:由多组喷嘴组成,用于对从结晶 器出来的钢坯进行二次冷却,控制钢坯的凝固速 度和温度分布。
拉矫机和切割设备
拉矫机
用于对钢坯进行拉伸、矫直和调整几 何形状。
切割设备
用于将拉矫后的钢坯按照要求进行切 割,以便于后续加工和使用。
发展带来新的机遇和挑战。
方坯连铸机在未来钢铁工业中的地位和作用
总结词
地位、作用
详细描述
方坯连铸机作为钢铁工业中的重要设备之一,在未来 仍将占据重要地位。随着钢铁工业的发展和技术的进 步,方坯连铸机的作用将更加突出。它将继续为钢铁 企业提供高效、低能耗、环保的生产方式,推动钢铁 工业的可持续发展。同时,方坯连铸机的发展也将促 进相关领域的技术进步和创新。
最新方坯连铸机PPT课件
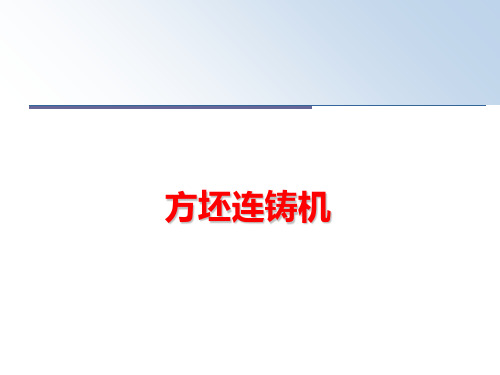
设置在连铸浇注平台上,一般每台连铸 机配备两台中间包车,互为备用,当一台 浇注时,另一台处于加热烘烤位置。利于 快速更换中间包,提高连铸机作业率。
中间包车的形式有门型、半门型和悬挂 型。
2、冶金区
2.1 结晶器
结晶器是一个水冷的钢锭模,是连铸机的核心 部件,称之为连铸设备的心脏。
结晶器的作用:钢液在结晶器内冷却、初步凝固 成型,且均匀形成具有一定厚度的坯壳。结晶器采 用冷却水冷却,通常称为一次冷却。
钢包回转台主要有直臂式和双臂式两类。
1.2 中间包
中间包也叫做中包、中间罐。中间包是 位于钢包与结晶器之间用于钢液浇注的过 渡装置,其主要作用是:
(1)中间包可减少钢液静压力,稳定注流;
(2)中间包有利于夹杂物上浮,净化钢液;
(3)在多流连铸机上,中间包将钢液分配给 每个结晶器;
(4)在多炉连浇时,中间包贮存一定量的钢 液,更换钢包时不会停浇;
270 218 152 115 95 95 86 66 52 44 34 20Cr δbδs 158 156 120 87 64 60 52 44 34 26 21
3Cr13 δbδs
91
133
78
44
76
95
51
38
从表中可见当铸坯温度从950~1000℃(矫直温度) 下降到600℃时其δs将会增加2~4倍。
拉钢机、铸坯存放台架
结束语
谢谢大家聆听!!!
47
铸机最小圆弧半径:
R≥cD 式中 R—连铸机圆弧半径;
D—铸坯厚度; c—系数,一般中小型铸坯取30~40; 大型板坯及合金钢,取40以上。国外,普 通钢种取33~35,优质钢取42~45。
3、液相深度
液相深度L液是指铸坯从结晶器液面开 始到铸坯中心液相凝固终了的长度,也称 为液心长度。
中间包车的形式有门型、半门型和悬挂 型。
2、冶金区
2.1 结晶器
结晶器是一个水冷的钢锭模,是连铸机的核心 部件,称之为连铸设备的心脏。
结晶器的作用:钢液在结晶器内冷却、初步凝固 成型,且均匀形成具有一定厚度的坯壳。结晶器采 用冷却水冷却,通常称为一次冷却。
钢包回转台主要有直臂式和双臂式两类。
1.2 中间包
中间包也叫做中包、中间罐。中间包是 位于钢包与结晶器之间用于钢液浇注的过 渡装置,其主要作用是:
(1)中间包可减少钢液静压力,稳定注流;
(2)中间包有利于夹杂物上浮,净化钢液;
(3)在多流连铸机上,中间包将钢液分配给 每个结晶器;
(4)在多炉连浇时,中间包贮存一定量的钢 液,更换钢包时不会停浇;
270 218 152 115 95 95 86 66 52 44 34 20Cr δbδs 158 156 120 87 64 60 52 44 34 26 21
3Cr13 δbδs
91
133
78
44
76
95
51
38
从表中可见当铸坯温度从950~1000℃(矫直温度) 下降到600℃时其δs将会增加2~4倍。
拉钢机、铸坯存放台架
结束语
谢谢大家聆听!!!
47
铸机最小圆弧半径:
R≥cD 式中 R—连铸机圆弧半径;
D—铸坯厚度; c—系数,一般中小型铸坯取30~40; 大型板坯及合金钢,取40以上。国外,普 通钢种取33~35,优质钢取42~45。
3、液相深度
液相深度L液是指铸坯从结晶器液面开 始到铸坯中心液相凝固终了的长度,也称 为液心长度。
- 1、下载文档前请自行甄别文档内容的完整性,平台不提供额外的编辑、内容补充、找答案等附加服务。
- 2、"仅部分预览"的文档,不可在线预览部分如存在完整性等问题,可反馈申请退款(可完整预览的文档不适用该条件!)。
- 3、如文档侵犯您的权益,请联系客服反馈,我们会尽快为您处理(人工客服工作时间:9:00-18:30)。
VOD法是在真空室内由炉顶向钢液吹氧,同时由 钢包底部吹氩搅拌钢水,当精炼达到脱碳要求时, 停止吹氧,然后提高真空度进行脱氧,最后加 Fe-Si脱氧。它可以在真空下加合金,取样和测温。 因为强烈的碳氧反应,要求钢包上部的自由空间 的高度为1.0~1.2m,故出钢量要低一些,运行 成本高。
VOD法具有脱碳、脱氧、脱气、脱硫及合金化等 功能。主要用于生产不锈钢或超低碳合金钢。
LF炉主要冶金功能及精炼手段 LF炉具有的主要冶金功能有: 钢水升温、调温及保温功能 强化脱氧、脱硫功能 合金微调功能 采用的精炼手段有: 吹氩搅拌 埋弧加热 造强还原气氛 造碱性合成渣
适用的钢种 除超低碳、氮、硫等超纯钢外,几乎所有的钢种
都可以采用LF法精炼,特别适合轴承钢、合金结 构钢、工具钢及弹簧钢等的精炼。 精炼后轴承钢 全氧含量降至0.001%,[H]降至0.0003%~ 0.0005%,[N]降至0.0015%~0.002%,非金 属夹杂物总量在0.004%~0.005%。
铁水预处理设备
铁水预处理就是在铁水兑入转炉之前对其进行脱 除杂质元素或从铁水中回收有价值元素的一种铁 水处理工艺。普通铁水预处理包括铁水脱硅、脱 硫和脱磷(即“三脱”)。特殊铁水预处理是针 对铁水中的特殊元素进行提纯精炼或资源综合利 用而进行的处理过程,如铁水提钒、提铌、提钨 等。
根据我厂铁水及设备的实际情况,主要介绍现普 遍采用的类似生产二区的喷吹Mg-CaO的铁水喷 粉脱硫设备。
系统
RH示意图
(五)VOD真空吹氧脱碳法炉
VOD法(Vacuum Oxygen Decarburization)称为真空吹氧脱碳法, 它是1965年由德国维腾公司开发出的技术。 VOD设备与VD设备的构成基本相同,主要 的区别在于VOD法增加了氧枪及其升降系 统、供氧系统。
真空循环脱气的工作原理:当两个插入管 插入钢液一定深度时,启动真空泵,真空 室被抽成真空,由于内外压力差,钢液上 升一定高度;与此同时上升管输入驱动气 体(氩气),受热膨胀,引起等温膨胀, 钢液与气体混合比重降低,驱动钢液项喷 泉一样涌入真空室,使真空室的平衡破坏, 为保持平衡,一部分钢液从下降管回到钢 包中,就这样在钢水压力差和驱动气体的 作用下不断地从上升管涌入真空室,并经 过下降管回落到钢包内,周而复始的实现 钢液循环,从而通过造渣净化钢液。
连铸机横向布置示意图 1—操作台,2—转炉;3—铸锭
设备;4—连铸机 5—铸坯运行辊道;6—大包转
台
2、纵向布置:纵向布置是指连铸机的中心线与 厂房纵向柱列线相平行的布置形式 ,转炉跨与连 铸坯跨之间用钢包运输线分开,钢水可分别用吊 车供应各台连铸机,比较方便。但车间一般较长, 再新建连铸机比较困难。 一般不采用。
(二)喷粉及喂丝
合金的喂入与喷粉工艺示意图
(三)LF炉
钢包处理型处理钢水过程中,因钢水的温降而使 渣及合金成分的调整以及处理时间等都受到限制。 如果用提高初炼炉出钢温度的办法保证渣熔化及 足够的精炼时间,势必加重初炼炉的负担,降低 炉衬寿命,命中率也比较低,不具备工业性连续 生产的条件。
臂和扒渣耙子摆动,将铁水渣扒除。 7、铁水罐倾翻车:主要是两个液压缸 8、渣罐及渣盘车、电子称、电控系统、液压渣、
氮气管路
精炼设备简介
一、二次冶金工艺流程: 高炉——铁水预处理——转炉——钢水二次精
炼——连铸 二、主要的精炼方式: 二次精炼就是对转炉钢水根据目的进行炉外(相
1971年,日本特殊钢公司开发的Ladle Furnace, 简称“LF”、“LF炉”、“LF钢包炉”、“LF钢 包精炼炉”、 “钢包炉”、“钢包精炼炉”等。
该炉采用碱性合成渣,埋弧加热,吹氩搅拌,在 还原气氛下精炼,钢包炉的原理图见图
主要设备构成:LF炉主要由钢包炉体、钢 包车(分单工位和双工位)、电极加热 系统、吹氩搅拌系统、合金加料系统以 及测温取样系统、高压室、操作室、液 压站(实现电极、炉盖的升降)等部分 组成。
可以达到的冶金效果(S≤0.005%)
精炼及连铸设备
北营炼钢厂
铁水包脱硫工艺设备图
铁水喷粉脱硫的主要设备: 1、铁水罐 2、储存仓:内部装有高地位料位指示器、液态化
床 3、喷粉罐:由于喷粉的高压容器,能稳定而无脉
冲的将脱硫粉剂经喷枪喷至铁水罐内。 4、喷枪及喷枪支架 5、测温取样装置 6、扒渣机:扒渣小车以液压缸为动力,带动扒渣
主要设备构成:
1、真空泵系统:真空泵组、冷 凝器、气体冷却器、伸缩接头、 真空切断阀、防爆阀、蒸汽供 应管网、冷凝水供应设备
2、真空室 3、真空室运输车系统 4、合金上料及添加系统 5、驱动气体供应系统 6、真空室加热、烘烤系统 7、真空吹氧系统 8、自动控制系统、测脱气法是德国蒂森公司所 属鲁尔(Ruhrstahl)公司和海拉斯 (Heraeus)公司于1959年研制成功的循 环真空脱气装置。它将真空精炼与钢水循 环流动结合起来。
最初RH装置主要是对钢水脱氢,后来增加 了真空脱碳、真空脱氧、改善钢水纯净度 及合金化等功能。RH法具有处理周期短, 生产能力大,精炼效果好的优点,非常适 合与大型炼钢炉相配合
连铸设备介绍
一、浇注跨的布置形式 分为:横向布置、纵向布置及靠近轧钢车间布置等几种形式 1、横向布置:横向布置是指连铸机的中心线与厂房纵向柱列
线相垂直的布置形式,我厂主厂房有 、原料跨、转炉跨、分配 跨(钢水及炉外精炼跨)、浇铸跨、出坯跨、成品跨多个跨间 平行布置。而连铸机的摆布采用的就是这种横向布置方式。
对于转炉)处理。为了创造最佳的冶金反应条件, 所采用的基本手段不外乎搅拌、真空、加热、渣 洗、喷吹及喂丝等几种或几种的组合。 根据主要 功能,常见的精炼设备有: 吹氩设备、喂丝设备、LF炉 、DH、RH、LVD、 ASEA-SKF、V0D等
三、各种精炼设备介绍: (一)吹氩:分为底吹、顶吹两种方式。