案例2-离合器膜片弹簧的有限元分析
第三章膜片弹簧离合器第一节膜片式离合器的结构与工作原理
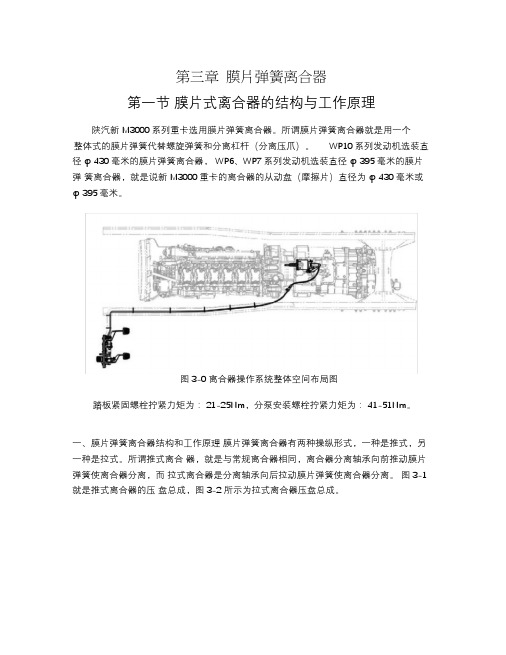
第三章膜片弹簧离合器第一节膜片式离合器的结构与工作原理陕汽新 M3000系列重卡选用膜片弹簧离合器。
所谓膜片弹簧离合器就是用一个整体式的膜片弹簧代替螺旋弹簧和分离杠杆(分离压爪)。
WP10系列发动机选装直径φ 430毫米的膜片弹簧离合器, WP6、WP7系列发动机选装直径φ 395毫米的膜片弹簧离合器,就是说新 M3000重卡的离合器的从动盘(摩擦片)直径为φ 430毫米或φ 395毫米。
图3-0 离合器操作系统整体空间布局图踏板紧固螺栓拧紧力矩为: 21-25Nm,分泵安装螺栓拧紧力矩为: 41-51Nm。
一、膜片弹簧离合器结构和工作原理膜片弹簧离合器有两种操纵形式,一种是推式,另一种是拉式。
所谓推式离合器,就是与常规离合器相同,离合器分离轴承向前推动膜片弹簧使离合器分离,而拉式离合器是分离轴承向后拉动膜片弹簧使离合器分离。
图3-1 就是推式离合器的压盘总成,图 3-2 所示为拉式离合器压盘总成。
图3-1 推式离合器压盘总成图3-2 拉式离合器压盘总成1、推式离合器1. 从动盘2. 飞轮3. 压盘4. 膜片弹簧5. 分离轴承6. 分离拐臂7. 压盘壳8. 分离轴承壳9. 飞轮壳10. 离合器工作缸(分泵)11. 推杆图3-3 推式离合器结构示意图图3-3和3-4分别给出推式离合器结构和原理简图。
如图 3-3 ,推式离合器与常规的螺旋弹簧离合器结构相近,只是用一只膜片弹簧代替了螺旋弹簧和分离杠杆(分离压爪)。
膜片弹簧 4是一个鼓形弹簧,在内圈圆周上开有若干槽,它一方面起到将压盘 3紧紧地将从动盘 1压紧在飞轮 2上的作用,同时又起到分离杠杆的作用。
如图3-5 ,与常规螺旋弹簧离合器不同的是,膜片弹簧离合器在圆周上布置有四片联接压盘壳和压盘的传动片。
每个传动片都是由四片弹性刚片组成。
它的作用是将发动机旋转的动力传递给压盘,从而使压紧的压盘和飞轮共同带动从动盘摩擦片共同旋转。
1. 从动盘2. 飞轮3. 压盘4. 膜片弹簧5. 分离轴承6. 分离拐臂7. 压盘壳8. 分离轴承壳9. 飞轮壳10. 离合器工作缸(分泵)11. 推杆图3-4 推式离合器工作原理图图3-5 压盘壳与压盘之间的传动片如图3-3和3-4 ,膜片 4靠弹力将压盘 3和从动盘摩擦片 1紧紧地压紧在飞轮 2的表面上。
乘用车膜片弹簧离合器设计方案

乘用车膜片弹簧离合器设计方案引言随着汽车产业的发展,离合器作为乘用车中的重要部件之一,在车辆的操控性和舒适性方面起着重要作用。
传统的离合器设计方案如钢板弹簧离合器存在着一些问题,例如质量大,减震效果差等。
为了优化离合器的设计方案,提高其性能,膜片弹簧离合器应运而生。
本文将介绍乘用车膜片弹簧离合器的设计方案。
膜片弹簧的特点膜片弹簧是一种特殊的弹簧,由多个膜片组成。
与传统的钢板弹簧相比,膜片弹簧具有以下特点:1.重量轻:膜片弹簧采用薄型结构,相比于钢板弹簧具有较小的质量,可以有效减轻整个离合器系统的重量。
2.弹性好:膜片弹簧在受力时可以均匀分布应力,具有较好的弹性恢复性能,能够提供更好的减震效果。
3.能量传递效率高:膜片弹簧可以通过调整其刚度和形状,使得其在多个工况下具有较好的能量传递效率。
膜片弹簧离合器设计方案膜片弹簧的选材在选择膜片弹簧的材料时,需要考虑到其强度、硬度、耐热性和耐疲劳性等因素。
常见的膜片弹簧材料有合金钢、不锈钢和高强度复合材料等。
根据实际需求和成本考虑,选择合适的材料。
膜片弹簧的结构设计膜片弹簧的结构设计主要包括片数、片厚、片形状和连接方式等。
片数的选择需要考虑到离合器的传动比和负载情况,片数过多会增加制造成本,过少会影响性能。
片厚的选择需要根据实际承受的压力和弯曲挠度进行合理设计。
片形状的选择应与离合器的工作原理相匹配,以保证传递能量的效率。
连接方式的选择需要考虑到装配方便性和持久性。
膜片弹簧离合器的优化设计为了进一步优化膜片弹簧离合器的性能,可以使用计算机辅助设计和仿真技术进行优化设计。
通过建立离合器系统的模型,可以进行参数化设计和性能优化分析,以满足不同工况下的性能需求。
结论乘用车膜片弹簧离合器是传统离合器的优化方案之一。
通过选用合适的膜片弹簧材料和进行结构设计优化,可以提高离合器的性能,包括减轻重量、提高弹性和能量传递效率。
计算机辅助设计和仿真技术为膜片弹簧离合器的优化设计提供了便利工具。
汽车离合器膜片弹簧的有限元分析

汽车离合器膜片弹簧的有限元分析
杨橙
【期刊名称】《机电技术》
【年(卷),期】2005(028)001
【摘要】膜片弹簧是现代汽车离合器有限元法,分别建立了适宜于膜片弹簧仿真分析的轴对称模型、板壳模型和实体模型,以期能对膜片弹簧的精益设计提供一些参考.
【总页数】2页(P37-38)
【作者】杨橙
【作者单位】福州大学机械工程及自动化学院,福建,福州,350002
【正文语种】中文
【中图分类】U463.211
【相关文献】
1.汽车膜片弹簧离合器中膜片弹簧的仿真分析 [J], 曾环;张晔;秦艳芳
2.自调式离合器膜片弹簧优化设计及有限元分析 [J], 孟姝君;崔胜民;孙宇航
3.双离合器膜片弹簧应力有限元分析 [J], 焦光龙;刘振峰;顾力强
4.汽目离合器膜片弹簧有限元分析 [J], 刘从权;陈照中
5.干式双离合器膜片弹簧的有限元分析 [J], 尹宗军;汪帆;王玲芝;陈晨;苏蓉;刘雨因版权原因,仅展示原文概要,查看原文内容请购买。
膜片弹簧力学特性CAE分析

模型导入 将hypermesh中生成的网格模型导入 到abaqus。设置膜片弹簧三角形单元类型 为STRI65,四边形单元类型为S8R,均为 二次单元。材料为60Si2Mn,弹性模量 E=206000MPa,泊松比为0.29。支承环与 压盘单元类型为C3D4, 材料为碳素钢,弹 性模量210000MPa,泊松比为0.27。
三、分析结果
将数据导入matlab中处理,得到膜片弹簧压紧过程的弹性特性 曲线,其中x轴为支承环的位移,y轴为支承环与膜片弹簧之间沿 膜片弹簧轴向方向的接触力大小。
通过A-L法理论计算得到的弹性特性曲线:
两种方法得到的弹性特性曲线的对比: (如图,峰值大的是CAE分析曲线,峰值小的是理论计算曲线 )
接触条件 建立支承环与膜片弹簧之间的面接触, 建立膜片弹簧与压盘之间的面接触,两个接 触为库伦摩擦,摩擦系数为0.18。
施加位移载荷 位移载荷分两个分析步施加,两个分析 步均设置为非线性。第一个分析步使RP-2在 膜片弹簧轴向方向下压0.02mm(将膜片弹 簧压平),这样是为了先让两对接触面的接 触关系平稳的建立起来,这个分析步中时间 增量步设为1。第二个分析步使RP-2在膜片 弹簧轴向方向下压6mm,分20个时间增量步 进行加载,即每个增量步中支承环下压 0.3mm。
边界条件 约束压盘全部节点的所有自由度。在A 处建立局部坐标系,以在膜片弹簧平面内并 垂直于A边方向为Y方向,以轴向方向为X方 向。同理在B处也建立局部坐标系,以在膜 片弹簧平面内并垂直于B边方向为Y方向,以 轴向方向为X方向。在局部坐标系中约束膜片 弹簧A、B处所有节点的U2(Y方向)、UR1 (X方向转动)、UR3(Z方向转动)三个自 由度。将参考点RP-2与支承环所有节点刚性 耦合,约束RP-2除膜片弹簧轴向方向外的其 余五个自由度。
双离合器自动变速器膜片杠杆弹簧载荷-变形特性的有限元分析
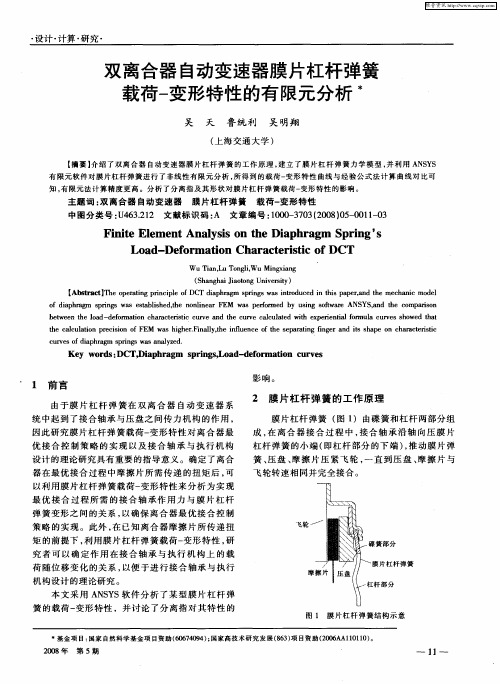
L0 d De o m a i n Ch r c e it fDCT a — f r to a a t r si o c
W u T a ,u To g i u Mi g i n inL n lW n xa g ,
( h n h i ioo gUnvri ) S a g a a tn ies y J t
o ip r g s rn s Wa sa l h d t e n n ie r F f d a h a m p g s e t b i e , o l a EM a ef r d b s g s f r i s h n w s p r me y u i o t e ANS , d t e c mp r o o n wa YS a o a i n n h s b t e n t e l a — eo ai n c a a trsi u v d t e c r e c l u ae i x e e t o ua c r e h we a e w e o d d fr t h r c e t c r e a h u v ac l td w t e p r n i f r l u v s s o d t t h m o i c n h i l a m h h a u a i r cso fF M a h g e . n l t n u n e o h e a ai n e n t s a e o h r ce t t e c c lt n p e ii n o E W ih r i al , e i f e c ft e s p r t g f g r a d i h p n c a a trs c l o s F yh l n i s i i C l e fda h g s rn a n lz d U W so ip r m p g w sa ay e . a i s
离合器设计(推式膜片弹簧)

辽宁工业大学汽车设计课程设计(论文)题目: 1.6LMT马自达3轿车离合器设计院(系):汽车与交通工程学院专业班级:车辆工程075学号:071201127学生姓名:张相坤指导教师:王天利教师职称:教授起止时间:2012.1.8~2012.2.25课程设计(论文)任务及评语目录第1章离合器设计的目的和要求 (1)1.1离合器设计的目的 (1)1.2离合器设计的要求 (1)第2章离合器设计的内容和方案的分析与确定 (2)2.1离合器设计的内容 (2)2.2离合器方案的分析与确定 (2)第3章主要零部件设计计算和验算的简要过程 (5)3.1 摩擦片的设计 (5)3.2 离合器基本参数的优化 (7)3.3 膜片弹簧的设计 (10)第4章主要部件结构设计说明 (15)4.1从动盘总成的设计 (15)4.2离合器盖和压盘的方式选择 (16)4.3分离轴承的选择 (17)4.4离合器的通风散热 (17)4.5扭转减振器的设计 (17)4.6离合器的操纵机构选择 (21)第5章经济、技术分析及对设计所作的简要评语 (22)5.1经济、技术分析 (22)5.2简评 (22)参考文献 (23)致谢 (24)附录 (25)第1章离合器设计的目的和要求1.1离合器设计的目的离合器是汽车传动系统中直接与发动机相联系的部件,按其功能要求,在结构上主要由主动部分 (发动机飞轮、离合器盖和压盘等)、从动部分 (从动盘)压紧机构 (压紧弹簧)和操纵机构 (分离叉、分离轴承、离合器踏板及传动部件等)等组成。
主要作用是保证汽车起步平稳,保证传动系统换挡时工作平顺,防止传动系统过载等,本次马自达3轿车离合器设计的目的是通过本课程设计,掌握膜片弹簧压紧型式的离合器的设计方法、步骤,进一步了解离合器的工作状况和性能,提高机械产品的设计能力。
1.2离合器设计的要求摩擦式离合器的结构类型非常多,而且有多种组合方式,但不管哪种结构类型,也不管什么组合方式,对它们的使用要求是一致的。
膜片弹簧的力学性能分析.

膜片弹簧的力学性能分析
膜片弹簧是膜片弹簧离合器的关键零件,其设计质量的优劣不仅直接影响离合器的使用性能和使用寿命,而且还影响离合器与整车的匹配。
因此在设计膜片弹簧离合器时,精确计算膜片弹簧的负载特性是非常重要的。
目前,膜片弹簧的设计仍普遍采用美国人J.o.Almen和Laszlo所提出的近似公式(简称A-L
公式),但工程人员在设计制造膜片弹簧的实践中发现,根据A-L公式设计的膜片弹簧,在膜片弹簧试制后的试验中,其大端载荷、升程等均不能完全符合设计要求,往往需要修改膜片弹簧尺寸参数,再进行试验。
这样,既延长了试制周期,又增加了成本。
因此,有必要寻找一种更有效的计算方法。
本文以膜片弹簧为研究对象,首先介绍了传统的A-L计算方法和膜片弹簧的基本特性。
然后,采用有限元的方法对膜片弹簧进行力学性能的仿真分析研究。
利用ANSYS参数化设计语言APDL,建立膜片弹簧自由状态下的三维参数化模型,大大简化了复杂繁琐的建模过程;通过适当的方法,对三维模型进行映射网格划分,确定相应的边界条件,建立起膜片弹簧的有限元模型。
模拟加载过程,计算得到膜片弹簧负载特性曲线,通过实验结果的比较,验证了有限元模型的正确性。
在膜片弹簧有限元分析的基础上,建立膜片弹簧负载特性的数学回归模型,对A-L公式系数进行了修正,提高了其计算的精度。
通过对应力分布的分析和膜片弹簧失效的特点,确定了其疲劳危险区域,利用材料的σ-N曲线,采用ANSYS疲劳分析模块估算了膜片弹簧的疲劳寿命。
最后,建立了膜片弹簧的优化模型,对其进行结构优化,取得了较好的结果。
乘用车膜片弹簧离合器设计方案

乘用车膜片弹簧离合器设计方案引言膜片弹簧离合器是一种常用于乘用车的传动装置。
它通过利用弹性薄膜片的变形来实现传递和别离动力,具有结构简单、启动平稳、传动效率高等优点。
本文将介绍乘用车膜片弹簧离合器的设计方案,包括设计原那么、材料选择、计算方法等内容。
设计原那么乘用车膜片弹簧离合器的设计需要遵循以下原那么: 1. 功能可靠:离合器需要能够有效地传递和别离动力,确保车辆平稳启动和换挡。
2. 结构简单:离合器的结构应当尽量简单,减少本钱和维护的复杂性。
3. 重量轻:乘用车需要提高燃油经济性,因此离合器的重量应当尽量轻,减少车辆的整体重量。
4. 寿命长:离合器的设计应当考虑到长时间使用时的磨损和疲劳,提高离合器的寿命。
材料选择膜片弹簧离合器的弹簧片通常使用高强度钢板制成。
选择适宜的弹簧片材料可以提高离合器的性能和寿命。
常用的弹簧片材料有以下几种: 1. 高碳钢:具有较高的强度和硬度,适用于高负荷和高温环境下的离合器。
2. 钢-铍合金:具有较高的弹性模量和疲劳强度,适用于长寿命和高性能的离合器。
3. 高速钢:具有较高的硬度和耐磨性,适用于高速和高负荷的离合器。
在选择材料时,需要考虑离合器的工作环境、预期寿命和本钱等因素,综合考虑选择最适宜的材料。
计算方法设计乘用车膜片弹簧离合器需要进行一系列的计算,包括弹簧片的尺寸、刚度和载荷等参数。
以下是常用的计算方法: 1. 计算载荷:根据车辆的最大扭矩和传动比,计算出离合器所需的最大传递扭矩。
2. 计算尺寸:根据传递扭矩和弹簧片的刚度,计算出弹簧片的长度、宽度和厚度等尺寸。
3. 计算刚度:根据弹簧片的材料和几何尺寸,计算出弹簧片的刚度系数。
4. 计算变形:根据载荷和刚度,计算出离合器在工作过程中的变形量。
5. 计算寿命:根据变形和材料的疲劳特性,估算离合器的寿命。
以上是一般的计算方法,具体的计算过程需要根据离合器的具体设计要求和工作条件进行调整。
结论乘用车膜片弹簧离合器是一种常用的传动装置,具有结构简单、启动平稳、传动效率高等优点。
- 1、下载文档前请自行甄别文档内容的完整性,平台不提供额外的编辑、内容补充、找答案等附加服务。
- 2、"仅部分预览"的文档,不可在线预览部分如存在完整性等问题,可反馈申请退款(可完整预览的文档不适用该条件!)。
- 3、如文档侵犯您的权益,请联系客服反馈,我们会尽快为您处理(人工客服工作时间:9:00-18:30)。
〖汽车理论与设计〗精品课程建设 福州大学机械工程及自动化学院车辆工程系 1图1 膜片弹簧的基本结构 案例二、离合器膜片弹簧的有限元分析 在工程技术领域,对于许多力学问题和物理问题,人们已经得到了它们应遵循的基本方程和相应的定解条件,但对于其中的大多数问题,由于方程某些特性的非线性性质,或由于求解区域的几何形状比较复杂,不能求得解析解。对于这类问题,以前常常通过引入简化条件,进行简化状态下的解答,但过多的简化可能导致误差很大甚至是错误。二十世纪六十年代以来,随着计算机的飞速发展和广泛应用,数值分析方法已经成为求解这类问题的主要工具,其中,有限单元法(Finite Element Method)在工程实践中已得到了广泛的认可。 有限单元法的基本思路是将复杂的结构视为由有限的、简单的基本单元所组成。这种基于离散化的数值计算方法,借助于矩阵方法与计算机相结合,几乎适用于求解所有的连续介质和场问题。对于有限元法的原理,大家可到图书馆参阅相关书籍[1]。在汽车设计中,与固
体力学、流体力学、热力学、声学、电磁学等相关的问题都可以应用有限元法求解,并且在很多问题上已经成为汽车研发流程中重要的环节。 在下面的例子中,应用有限元法分析了离合器膜片弹簧的弹性特性。膜片弹簧离合器由于具有诸多优点,目前在从轻型到重型的各类汽车上都得到了广泛应用。这里选用了通用有限元分析软件Ansys,它提供了两种工作模式,既可以通过界面操作进行,也可以编写命令流文件完成。关于软件的应用方法,大家可在以下说明的基础上,查阅帮助文档或到图书馆借阅相关书籍。 一、问题的提出 膜片弹簧是由弹簧钢制成的截锥形薄壁膜片,如图1所示,自其小端在锥面上开有许多径向切槽形成弹性杠杆,在离合器总成中起分离指的作用;未切槽的大端截锥部分称为碟簧,起到压紧弹簧的作用。通过合理地选择结构参数,膜片弹簧可以在简化汽车离合器构件的同时提供适宜的非线性弹性特性。 二、膜片弹簧的有限元分析(轴对称模型) 理论分析认为,膜片弹簧的弹性特性是由碟簧部分所决定[2] ,因此在其设计分析中大
多沿用Almen-Laszlo公式,即假设膜片弹簧在承载过程中,其子午断面刚性地绕此断面上的某中性点转动,则压紧时压紧力1F和加载点间的相对轴向变形1λ有如下的关系[3]: 课程反馈信箱:fzuqiche@126.com 2⎥⎦⎤⎢⎣
⎡+−−−−−−−−==2
1111112112111)2)(()()/ln()1(6)(hrRrRHrRrRHrRrREhfF
λλμλπλ
式中,E为材料弹性模量,钢材取2.1×105 MPa;μ为材料泊松比,钢取0.3;H为自由状态下碟簧部分的内截锥高度;h为膜片弹簧钢板的厚度;R、r分别为自由状态下碟簧部分大、小端的半径;1R、1r分别为压盘作用点和支承环作用点的半径。 从结构而言,碟簧部分为一完整的截锥,是典型的轴对称结构,取其旋转子午面,可建立如图2所示的轴对称分析模型,其中A、B分别为支承环作用点和压盘作用点的位置。
假定某推式膜片弹簧具有如下参数: 材料弹性模量MPaE5101.2×=,材料泊松比3.0=μ 自由状态下碟簧部分的内截锥高度mmH3.4=,膜片弹簧钢板的厚度mmh6.2= 自由状态下碟簧部分大、小端的半径分别为mmR105=、mmr5.83= 压盘作用点的半径mmR1031=,支承环作用点的半径mmr841= 在Ansys界面环境下,交互式建模的基本过程可按以下的步骤进行。 1、前处理阶段:其基本任务是根据问题的特点,权衡计算成本与精度的要求,建立结构的几何模型,给定材料常数,划分相应的单元网格。 1)建立膜片弹簧的轴对称模型 根据已知条件,该膜片弹簧自由状态下圆锥底角1974.0arctan≈−=rR
Hα弧度,换
算为度数约为°31.11,而碟簧子午断面长方形长度mmrRHL926.21)(22≈−+=。 启动ANSYS,定义分析标题:File(菜单)→Change Title,在出现的对话框中输入“The Diaphragm Spring”,单击OK以确定。 创建关键点1,坐标)0,(R:ANSYS Main Menu(左侧主菜单)→Preprocessor→Modeling→Create→Keypoints→In Active CS,出现Create Keypoints in Active Coordinate System对话框,在X,Y,Z Location in active CS输入框中输入坐标值105、0、0,单击OK以确定。
图2 膜片弹簧轴对称模型 〖汽车理论与设计〗精品课程建设 福州大学机械工程及自动化学院车辆工程系 3在点1处创建碟簧子午断面的局部坐标系:WorkPlane(菜单)→Local Coordinate Systems→Create Local CS→At Specified Loc,出现Create CS at Location选择框,在图形窗口选择已创建的关键点1,单击OK后弹出Create Local CS at Specified Location对话框,在THXY Rotation about local Z后输入-11.31,保持其他项内容不变(注意 KCN Ref number of new coord sys中的数值为11,代表该局部坐标系的编号),单击OK以确定。 提示:在此处创建局部坐标系是为了方便建模,在THXY Rotation about local Z输入的值单位为度数,负值表示相对于该轴顺时针旋转,即系统默认右手坐标系。 将创建的局部坐标系定义为工作平面以用于建模:WorkPlane→Align WP with→Specified Coord Sys,弹出Align WP with Specified CS对话框,在KCN Coordinate system number中输入11(即刚创建的局部坐标系),单击OK以确定。 创建碟簧子午断面:Main Menu→Preprocessor→Modeling→Create→Areas→Rectangle→By Dimensions,弹出Create Rectangle by Dimensions对话框,在X1,X2 X-coordinates后的输入框中输入-21.926、0,在Y1,Y2 Y-coordinates后的输入框中输入-1.3、1.3,单击OK以确定,即通过)2/,(hL−−、)2/,0(h两点创建矩形的子午断面。
将工作平面恢复为整体直角坐标系:WorkPlane→Align WP with→Global Cartesian。 激活整体直角坐标系:WorkPlane→Change Active CS to→Global Cartesian。 通过线与线相交获得B点,即压盘作用点的位置:用与创建关键点1类似的方法先创建两个关键点)10,103(、)10,103(−,然后Preprocessor→Modeling→Create→Lines→Straight
Line,出现Create Straight Line选择框,在图形窗口选择刚创建的两个关键点,从而生成一直线,其X轴的坐标为1
R,接着Preprocessor→Modeling→Operate→Booleans→Divide→Line
by Line,出现Divide Line by Line选择框,在图形窗口选择碟簧子午断面下缘的直线,单击选择框中的Apply,再选择刚创建的直线,单击OK以确定,这样就获得了B点。 通过线与线相交获得A点,即支承环作用点的位置:用上述同样的方法,再碟簧子午断面的上缘获得A点,注意其X轴的坐标为1
r。
2)定义单元属性 选择单元类型为PLANE183(二维8节点平面单元):Preprocessor→Element Type→Add/Edit/Delete,弹出Element Types对话框,单击Add...,弹出Library of Element Types对话框,在右侧的选择窗口中选择Structural Mass下的Solid,然后在更右边的窗口选择8node 课程反馈信箱:fzuqiche@126.com 4183,单击OK回到Element Types对话框,单击Options...,弹出PLANE183 element type options对话框,将Element behavior K3后下拉选择框中的内容改为Axisymmetric(表示该单元将应用于轴对称问题的求解),单击OK又回到Element Types对话框,单击Close以确定。 定义材料特性,其中弹性模量MPaE5101.2×=,泊松比3.0=μ:Preprocessor→
Material Props→Material Models,弹出Define Material Model Behavior对话框,在右侧窗口选择Structural→Linear→Elastic→Isotropic,弹出Linear Isotropic Material Properties for Material Number 1对话框,在EX后的窗口输入2.1e5,在PRXY后的窗口输入0.3,单击OK回到Define Material Model Behavior对话框,单击右上角的×关闭该窗口。 3)划分单元网格 为了说明方便,选用软件的智能划分网格方式:Preprocessor→Meshing→MeshTool,弹出MeshTool对话框,勾选Smart Size前的选择框,调整其下的Fine-Coarse值到3,单击Mesh,弹出Mesh Areas选择框,选择图形窗口中已创建的子午面,单击OK以确定。 2、求解阶段:其基本任务是对结构承受的载荷和支承方式进行处理,即对结构的有限元模型施加载荷和约束条件,然后选择对应的方法和参数进行有限元计算。 指定分析类型:Main Menu→Solution→Analysis Type→New Analysis,确认Static项选中,单击OK以确定。 指定分析选项:Main Menu→Solution→Analysis Type→Sol'n Controls,在Basic页中将Analysis Options项改为Large Displacement Static,将Automatic time stepping项改为On,将Number of substeps改为100,将Max no. of substeps改为1000,将Min no. of substeps改为20,单击OK以确定。 施加位移约束,即在A点(膜片弹簧上表面支承圈位置)施加零位移约束:Solution→Define Loads→Apply→Structural→Displacement→On Keypoints,弹出Apply U,ROT on KPs选择框,在图形窗口选择已创建的关键点(A点),单击OK弹出Apply U,ROT on KPs对话框,在Lab2 DOFs to be constrained项选择UY,在VALUE Displacement value项输入0,单击OK以确定。 施加变形量,即在B点(碟簧与压盘接触位置)处施加指定的变形量,此处假定变形为上移mm4,对应膜片弹簧的一种压紧状态:Solution→Define Loads→Apply→Structural