气动注液泵说明书
注射泵说明书

注射泵说明书注射泵使用说明书一、产品概述本注射泵是一种高精度的电子化泵,能够准确地控制输液的速率和容积。
适用于各种临床领域,如输液、营养注射、化疗、麻醉、监测等。
二、产品特点1. 采用先进的微处理器技术,可以实现多种输注模式。
2. 具有触摸屏幕,用户操作简单方便。
3. 支持多种流速、容量的输注设置,可根据临床需要设置多种参数。
4. 具有输注过程中的语音提示和报警功能,可以有效防止输液错误。
5. 采用紧凑型设计,重量轻,易于安装和携带。
6. 具有高精度、高稳定性、低噪音等优点,可确保输液的安全和精确。
三、操作方法1. 打开注射泵电源,进行必要的预热和检测。
2. 将液体输送管正确地安装在注射泵的输液口和患者的静脉输液管上。
3. 按照临床要求设置输注参数,包括流速、容量、输液时间等。
4. 开始输注前,仔细检查设置参数是否正确,确保输注的准确性和安全性。
5. 输注过程中,观察注射泵上的工作状态指示灯,并随时注意听取语音提示和报警信息,及时处理异常情况。
6. 输注结束后,关闭注射泵电源,取下输液管,清洁注射泵和输液管。
四、注意事项1. 请严格按照说明书的操作步骤进行操作。
2. 为避免交叉感染,请使用一次性输液管和注射器。
3. 在使用过程中如发现异常情况,请立即停止使用并联系售后服务部门。
4. 请勿将注射泵接入任何未知来源的电源或设备。
5. 不要在多湿、多尘、多振动的环境中使用注射泵。
6. 在携带注射泵时,请轻拿轻放,避免碰撞和摔落。
五、维修保养1. 在注射泵运行过程中,定期检查设备工作状态和管路连接情况。
2. 如发现注射泵出现故障或异常情况,请及时联系售后服务部门进行维修。
3. 维修前请关闭电源。
电源插头不能湿手插拔。
4. 定期对注射泵执行清洁和消毒工作。
六、技术参数1. 测量范围:0.1~1200 ml/h2. 分辨率:0.1 ml/h3. 灵敏度:±2%4. 输液容量:0.1~9999.9 ml5. 功率:<25W6. 外形尺寸:220mm×120mm×150mm七、包装清单1. 注射泵主机2. 输液管3. 电源线4. 使用说明书五、售后服务如有任何问题或需求,请联系售后服务部门,我们将竭诚为您提供服务。
ACHL系列空气驱动手动高压液体泵操作与维护手册说明书
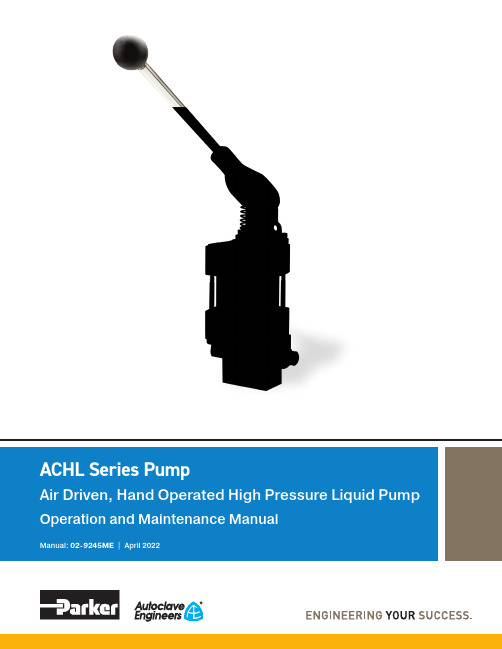
| April 2022Operation & Maintenance Manual | 04/2202-9245ME : ACHL Series Pump2FAILURE, IMPROPER SELECTION OR IMPROPER USE OF THE PRODUCTS AND/OR SYSTEMS DESCRIBED HEREINOR RELATED ITEMS CAN CAUSE DEATH, PERSONAL INJURY AND PROPERTY DAMAGE.This document and other information from Parker Hannifin Corporation, its subsidiaries and authorized distributors provide product and/or system options for further investigation by users having technical expertise. It is important that you analyze all aspects of your application and review the information concerning the product or system in the current product catalog.Due to the variety of operating conditions and applications for these products or systems, the user, through its own analysis and testing, is solely responsible for making the final selection of the products and systems and assuring that all performance, safety and warning requirements of the application are met.The products described herein, including without limitation, product features, specifications, designs, availability and pricing, are subject to change by Parker Hannifin Corporation and its subsidiaries at any time without notice.ALL PARKER VALVES MUST PASS A RIGID OPERATIONAL AND LEAKAGE TEST BEFORE LEAVING THE FACTORY. IT IS RECOMMENDED AFTER ANY REASSEMBLY, THE VALVE SHOULD BE TESTED BY THE USER FOR OPERATION AND LEAKAGE. IF THESE INSTRUCTIONS ARE NOT FULLY COMPLIED WITH, THE REPAIRED PRODUCT MAY FAIL AND CAUSE DAMAGE TO PROPERTY OR INJURY TO PERSONS. PARKER HANNIFIN CANNOT ASSUME RESPONSIBILITY FOR PERFORMANCE OF A CUSTOMER SERVICED VALVE.Live Chat Support is available from /IPD when the Chat icon “ ” is visible on screen.Parker Instrumentation Products Divison (IPD)02-9245ME : ACHL Series PumpOperation & Maintenance Manual | 04/223Product DrawingsTypical Pump Cross Sectional View ....................................................................................4 ACHL Pump Dimensional View . (5)Operation & Maintenance Information1.0 Introduction (6)2.0 Meaning of Safety Words .......................................................................................... 63.0Product Specification (6)4.0 Unpacking ..............................................................................................................6 5.0 Tools ...................................................................................................................... 6 6.0 Installation .............................................................................................................. 7 6.1 Compressed Air Supply . (7)6.2 Liquid Section ......................................................................................................... 87.0 Pump Start-Up ........................................................................................................ 88.0 Process Media ........................................................................................................ 99.0Pump Functionality (10)10.0 Suggested Maintenance (11)T roubleshooting Information11.0 Repair Kit Options .................................................................................................. 11 12.0 ACHL Series Drawings ............................................................................................12 13.0 Trouble Shooting-Pneumatic Section ...................................................................... 14 14.0 Trouble Shooting-High Pressure, Liquid Section .. (15)15.0 Service (15)T able of ContentsPageOperation & Maintenance Manual | 04/2202-9245ME : ACHL Series Pump4Typical Pump: Cross Sectional View(ASL Pump Shown)02-9245ME : ACHL Series PumpOperation & Maintenance Manual | 04/225ACHL Pump Dimensional ViewAll ACHL Series Pumps have a 1/4" FNPT regulated main air drive supply connectionNote:• Each Mounting Bracket includes (2) 11/32" (8.73) holes for 5/16" Bolts.• Spool air tubing not shown for clarity.• All dimensions are for reference only and are subject to change without notice.• Primary Dimensions: Inches• Secondary Dimensions: (Millimeters)Left View6Section 3.0 Product SpecificationsSection 1.0IntroductionThe Parker Autoclave Engineers pump discussed in this manual is operated using compressed air up to 150 psi (10 bar). Parker Autoclave Engineers ACL Series pumps are used for pumping oil, water and oil/water mixtures. Special seals are also available for chemical service. Please contact Parker Autoclave Engineers to discuss availability of special seals. The pump operates using a pressure ratio of the air piston surface area to the liquid plunger surface area.(Output liquid pressure = actual pump pressure ratio x input air pressure). Refer to the product literature for each pump model’s actual air pressure ratio.Section 2.0Meaning of Safety WordsA safety related message is identified by a safety alert symbol and a signal word to indicate the level of risk involved with a particular hazard. The definitions of the three signal words are as follows:Special notes intended to bring attention to procedures that must be followed to ensure proper installation and performance will be placed in a box labeled NOTICE.Section 4.0The pump has been assembled and pressure tested at Parker Autoclave Engineers and is ready to be put into service. The shipping carton should be opened and the contents carefully examined upon receipt from the carrier. Make sure there is no obvious damage to the contents. DO NOT use the equipment if any damage is evident.If damage has occurred, file a claim with the shipper be-fore contacting Parker Autoclave Engineers Service Department.Examine all material within the container and check against the packing list to be sure all items are accounted for and are not damaged. Verify that the equipment model number supplied agrees with what was ordered.See assembly drawing for product specifications:- Pump Geometry- Pump Materials of Construction- Maximum Allowable Working Pressure- Maximum Working Temperature- Pressure Ratio- Displacement- Repair Kit Part Numbers- Torque Information- WeightsUnpackingSection 4.0UnpackingAt minimum, the tools required for installation of the pump include a torque wrench, an open end wrench adapter (crows foot adapter) and an open end adjustable wrench. Refer to the Tools, Maintenance and Installation Manual provided with the Data Book for information on torque wrenches and torque values for Parker Autoclave Engineers tubing and fittings.Section 5.0ToolsOperation & Maintenance InformationOperation & Maintenance Manual | 04/22 02-9245ME: ACHL Series Pump02-9245ME : ACHL Series PumpOperation & Maintenance Manual | 04/227Section 6.0InstallationSection 6.1Compressed Air SupplyUnless otherwise noted, all air line accessories for the pump air drive should have, at minimum, a 1/4" FNPT connection. The tubing/piping used to connect the components should have the maximum ID the pressure rating will allow. Reducing the size before the air inlet will reduce air pressure flow andreduce flow rate of the pump.NOTICEThe main air drive connection port on the pump is a female 1/4" FNPT and is located in the spool valve housing.The use of an air line lubricator is not required and is not recommended. The oil in the air lubricator will cause the factory installed grease to be purged from the pump. Once an air lubricator is used the pump can never again be operated withoutan air lubricator.NOTICEAn air line filter with a minimum 5 microns filtration rating must be used on the supply line. If the air supply is not dry, a mist separator must be used to remove moisture in the air line.The pump is designed to function from 15 psi to 150 psi (1 to 10 bar) air input pressure.For best performance and life, the pump should be installed in the vertical position. This will prevent side loading on the air piston seals. The pump will, however, function in any position.The pump will attach to the mounting location using (4) 5/16" bolts. There are 4 holes provided on each pump for mounting.Operation & Maintenance Manual | 04/2202-9245ME : ACHL Series Pump 8Section 4.0UnpackingAll ACHL series pumps have a high pressure liquid outletport located on the side of the pump head. The suction inlet port on all ACHL series pumps is positioned either at the bottom or side of the head depending on the model purchased. See order code details in the product litera-ture for catalog number suffix.Inlet: A liquid filter with at least a 100 mesh size must be installed before the suction port inlet to prevent dam-age to the check valves and high pressure seals due to debris.Section 6.2Liquid Section For best performance, a liquid supply reservoir should be located higher than the inlet gland on the pump to create a small pressure head. Be sure to make an air tight seal between the reservoir and the pump inlet connection. The connections between the reservoir and pump inlet should not be reducedfrom the 3/8" FNPT connection size.NOTICEThe tubing or piping should be made from a corrosion resistant material and sized with a maximum ID to fit the 3/8" pipe connections.Restricting flow at the liquid inlet will causeproblems with check valve performance and reduceoutput flow.NOTICEOutlet: The outlet tubing ID must, at minimum, match the same size of the pump check valve gland port. Referto product literature for outlet connections details for each pump. Reducing outlet tubing or connection will reduce output liquid flow capacity.Section 4.0UnpackingSection 7.0Pump Start-Up Air Line SchematicAs shown above, a filtered main air supply line is required. The filtered air supply will go to a pressure regulator which can be set to achieve the desired output liquid pressure according to the pressure ratio of the pump.LIQUID INLETAIRREGULA TORAIR02-9245ME : ACHL Series PumpOperation & Maintenance Manual | 04/229The pumps unique design allows for self priming.To prime, regulate the air pressure to between 5-15 psi or use an air flow regulator to reduce to a slow stroke frequency. With the high pressure side connected to a vented system, allow the pump to cycle till a consistent flow of liquid is achieved.Let the pump flow freely to purge any air in the liquid system. Loosening the outlet gland or pipe can also assist in priming the pump.Section 4.0UnpackingSection 8.0Process Media Parker Autoclave Engineers pumps discussed in thismanual are used for pumping oil, water and oil/water mixtures. Special seals are also available for chemical service. Please contact Parker Autoclave Engineers todiscuss availability of special seals.Pumps are not designed to run for long periods of time without liquid process media. Short, dry pumping cycles should not be a cause for concern.However, pumps are built using lubricant in the seal areas and pumping without fluid will wear away lubricant and compromise the seal .The operating temperatures of the pump are between 0°F to 140°F (18°F to 60°F).Operation & Maintenance Manual | 04/2202-9245ME : ACHL Series Pump10Section 4.0UnpackingSection 9.0Pump Functionality When the pump is installed, regulated air is connectedto the spool housing at the ¼” FNPT pump inlet.The explanation below assumes pump is already primed with liquid.1. The pump is supplied with the piston in theupward position, which keeps the pilot valve in the open position.2. When regulated air is supplied to the pump, it enters the spool housing and energizes the large end of the spool, which shifts the spool to the left.3. The shifting of the spool causes regulated air to pass through the spool valve and pushes the air piston and liquid plunger d ownward toward the pump head.4. The liquid plunger moving toward the headcompresses fluid and forcing the inlet check valve to close and the outlet check valve to open.5. The plunger continues in the downward motion until it reaches the full stroke length.6. At the end of the stroke, air pressure is released from the large side of the spool, which causes the spool to shift and exhaust the air from the top of the piston through the muffler.7. The spring underneath the piston then returns the piston to the starting position.8. During the return, the pump performs a suction stroke. During a suction stroke, the plunger is moving away from the head causing the inlet check valve to open, which allows liquid to be drawn into the head while the outlet check valve is forced closed.9. Once the pump returns to the original starting position, the pilot valve opens and the entire process will continue to repeat until thepump reaches its stal pressure.Note: The ACHL series pump can be operated using a manual hand lever.Push the hand lever down to manually compress fluid and build liquid pressure. You can either stop when you reach your desired pressure, or when the pump reaches the end of its stroke. At the end of the stroke, keep your hand on the hand lever and slowly allow the springs to return the pump hand lever to its original position and perform a suction stroke.Do not let go of handle until the springs have returned the hand lever to its original position. Repeat this action until desired output pressure is reached.02-9245ME : ACHL Series PumpOperation & Maintenance Manual | 04/2211Section 4.0UnpackingSection 10.0Suggested MaintenanceA.Before each pump use, a quick inspection should be performed to insure there are no loose bolts, nuts, set screws or check valve glands. Tighten any loose bolts and fittings ac-cording to the torque values listed on the pump assembly drawing. A visual inspection should also be made before each use and at startup to make sure there is no evidence of fluid leaks from bottom end cap, weep holes or check valves. Refer to the troubleshooting guide for solutions to these fluid leaks.B.The maintenance schedule of the pumpdepends on the frequency of use, cleanliness of media, type of media, cycle rates, output pres-sures, cleanliness of air or any other conditions that may be damaging to seal integrity.Once a clear pattern develops of how long a pump is in service before pump performance declines, it is recommended to performmaintenance in advance of this time frame.At minimum, perform maintenance on the pump once a year as described below.Maintenance would include:• Re-lubrication or replacement of spool valve o-ring• Re-lubrication or replacement of air drive seals• Re-lubrication or replacement of pilot valve o-rings and gaskets• Replace check valve components • Replace high pressure hydraulic seals C.Maintenance instructions are supplied with appropriate rebuild kits. Kit part numbers are listed on the assembly drawing.Section 4.0Unpacking Section 11.0ACHL Series Repair Kit OptionsOperation & Maintenance Manual | 04/2202-9245ME : ACHL Series Pump12Section 12.0ACHL72-01-N Series Pump Drawing02-9245ME : ACHL Series PumpOperation & Maintenance Manual | 04/2213Section 4.0Unpacking Section 12.0ACHL189-01-N Series Pump DrawingOperation & Maintenance Manual | 04/2202-9245ME : ACHL Series Pump 14TroubleshootingSection 4.0UnpackingSection 13.0Troubleshooting - Pneumatic Section Problem: Pump will not operate with low air pressure.Cause:Excessive friction of o-rings on the spool valve has increased the pressure requiredto move spool.Solution: Replace and lubricate the o-rings on spoolProblem: Pump can only be actuated at high air pressure.Cause: a) Air is leaking through the plunger bore in the top end cap.b) Air is leaking through the o-rings between the top end cap and air cylinder.c) Bottom cap breather vent clogged.Solution: a) Replace and lubricate o-rings on upper plunger and in the bore located in the top cap. b) Replace and lubricate o-ring on lip of top end cap.c) Clean or replace breather vent.Problem: Pump will not run and air escaped through the exhaust muffler. Cause: a) Spool valve o-rings are leaking.b) Spool sleeve o-rings are leaking.Solution: a) Replace and lubricate spool valve o-rings.b) Replace and lubricate sleeve o-rings.Problem: Pump will not run and air escapes through the breather vent in the bottom end cap Cause: a) Outside o-ring on air piston is leaking. b) Seal between air piston and liquid plunger is leaking.Solution: a) Replace and lubricate air piston o-ring.b) Add Loctite 2760 thread locker with sealant on the plunger threads (one piece plunger designs)..Problem: Pump operates at a high frequency and short strokes.Cause: a) The top pilot valve is defectiveb) Air is leaking through the piston bore in thetop end cap.Solution: a) Replace and lubricate both tappet gaskets and o-ring. If necessary, also replace the tappet rod. b) Replace and lubricate o-ring on upper plunger and in the bore located in thetop cap.Problem: Pump functions slowly or doesn’t operate at all.Cause: a) Condensation from air supply is freezing the spool valve.b) Air muffler is clogged.Solution: a) Stop pump for a short period and replaceor add a mist separator in the air line.b) Clean or replace air muffler02-9245ME : ACHL Series PumpOperation & Maintenance Manual | 04/2215Section 4.0UnpackingSection 14.0Troubleshooting - High Pressure, Liquid Section Problem: Pump does not produce liquid flow, operates irregularly or does not maintain pressure.Cause: a) Air in the hydraulic system. b) Suction line excessively long. c) Suction tubing sized too small. d) Failure of one of the check valves. e) Liquid inlet filter is blocked.f) High pressure seal excessively worn.g) Supply liquid pressure head too low.Solution: a) Check inlet suction line and connections for leaks and allow pump to flow freely downstream so as to remove any air. b) Shorten liquid supply line.c) Increase tubing ID size between reservoir and pump inlet.d) Clean or replace both inlet and outlet check valve assemblies. e) Clean or replace liquid inlet filter. f) Replace high pressure seal assembly. g) Raise liquid reservoir to higher locationuntil pump is fully primed.Problem: Fluid escapes through the breather vent.Cause: High pressure seal is leaking.Solution: a) Clean fluid from air section. b) Replace and lubricate o-rings as necessary in the air section c) Replace high pressure liquid sealassembly.Section 4.0Unpacking Section 15.0ServiceParker Autoclave Engineers now require all pump repairbe sent to an authorized repair facility. Contact Parker Autoclave Engineers for recommendations.Pumps returned for service should be accompanied with the model number, serial number, manufacture date and problems you are experiencing.02-9245ME: ACHL Series Pump16Operation & Maintenance Manual | 04/22Operation & Maintenance Manual | 04/221702-9245ME: ACHL Series Pump02-9245ME: ACHL Series Pump18Operation & Maintenance Manual | 04/22Parker’s Motion & Control TechnologiesAt Parker, we’re guided by a relentless drive to help our customers become more productive and achieve higher levels of profitability by engineer-ing the best systems for their requirements. It means looking at customer applications from many angles to find new ways to create value. What-ever the motion and control technology need, Parker has the experience, breadth of product and global reach to consistently deliver. No companyknows more about motion and control technology than Parker. For further information call 1-800-C-Parker.02-9245ME April 2022© 2022 Parker Hannifin Corporation | Instrumentation Products Division1005 A Cleaner WayHuntsville, AL 35805 USA Tel: 256.881.2040Fax: /IPDOperation and Maintenance Manual ACHL Series: Liquid PumpsParker WorldwideNorth AmericaUSA – Corporate, Cleveland, OH Tel: +1 256 896 3000USA – IPD, Huntsville, AL Tel: +1 256 881 2040*****************USA – IPD, (Autoclave), Erie, PA Tel: +1 814 860 5700*******************CA – Canada, Grimsby, Ontario Tel +1 905-945-2274*********************South AmericaAR – Argentina, Buenos Aires Tel: +54 3327 44 4129 ******************BR – Brazil, Diadema, SP Diadema, SPTel: +55 11 4360 6700******************CL – Chile, Santiago Tel: +56 (0) 2 2303 9640******************MX – Mexico, Toluca Tel: +52 722 275 4200*******************Asia PacificAU – Australia, Dandenong Tel: +61 (0)2 9842 5150******************************CN – China, Shanghai Tel: +86 21 2899 5000*****************************HK – Hong Kong Tel: +852 2428 8008IN – India, MumbaiTel: +91 22 6513 7081-85ID – Indonesia, Tangerang Tel: +62 2977 7900********************JP – Japan, Tokyo Tel: +(81) 3 6365 4020******************KR – South Korea, Seoul Tel: +82 2 559 0400*******************MY – Malaysia, Selangor Tel: +603 784 90 800*******************SG – Singapore,Tel: +65 6887 6300*******************TH – Thailand, Bangkok Tel: +66 2 186 7000*********************TW – Taiwan, Taipei Tel: +886 2 2298 8987*************************VN – Vietnam, Hochi Minh City Tel: +848 382 508 56**********************Europe, Middle East, AfricaAE – UAE, Dubai Tel: +971 4 812 7100********************AT – Austria, Wiener Neustadt Tel: +43 (0)2622 23501-0*************************AT – Eastern Europe, Wiener Neustadt Tel: +43 (0)2622 23501 900****************************AZ – Azerbaijan, Baku Tel: +994 50 2233 458****************************BE/LU – Belgium, Nivelles Tel: +32 (0)67 280 900*************************BG – Bulgaria, Sofia Tel: +359 2 980 1344**************************BY – Belarus, Minsk Tel: +48 (0)22 573 24 00*************************CH – Switzerland, Etoy Tel: +41 (0) 21 821 87 00*****************************CZ – Czech Republic, Klecany Tel: +420 284 083 111*******************************DE – Germany, Kaarst Tel: +49 (0)2131 4016 0*************************DK – Denmark, Ballerup Tel: +45 43 56 04 00*************************ES – Spain, Madrid Tel: +34 902 33 00 01***********************FI – Finland, VantaaTel: +358 (0)20 753 2500*************************FR – France, Contamine s/Arve Tel: +33 (0)4 50 25 80 25************************GR – Greece, Athens Tel: +30 210 933 6450************************HU – Hungary, Budapest Tel: +36 223 885 470*************************IE – Ireland, DublinTel: +353 (0)1 466 6370*************************IT – Italy, Corsico (Ml)Tel: +39 02 45 19 21***********************KZ – Kazakhstan, Almaty Tel: +7 7273 561 000****************************NL – The Netherlands, Oldenzaal Tel: +31 (0)541 585 000********************NO – Norway, Stavanger Tel: +47 66 75 34 00************************PL – Poland, Warsaw Tel: +48 (0)22 573 24 00************************PT – Portugal, Leca da Palmeira Tel: +351 22 999 7360**************************RO – Romania, Bucharest Tel: +40 21 252 1382*************************RU – Russia, Moscow Tel: +7 495 645-2156************************SE – Sweden, Spånga Tel: +46 (0)8 59 79 50 00************************SK – Slovakia, Banská Bystrica Tel: +421 484 162 252**************************SL – Slovenia, Novo Mesto Tel: +386 7 337 6650**************************TR – Turkey, Istanbul Tel: +90 216 4997081************************UA – Ukraine, KievTel: +48 (0)22 573 24 00*************************UK – United Kingdom, Warwick Tel: +44 (0)1926 317 878********************ZA – South Africa, Kempton Park Tel: +27 (0)11 961 0700*****************************Questions?8325 Hessinger Drive Erie, PA 16509 USA Tel: 814 860 5700Fax: 814 860 Instrumentation Products Division。
气液混合泵使用说明11-推荐下载

的稳定吸入和高效溶解。
B、气体吸嘴前需要安装气体流量计,以便调节哈控制吸气量。气体流量计与吸气管路 之间需要安装开闭阀,这样可以避免每次开启水泵时重新调节吸气流量,同时可以 防止关闭水泵时液体倒灌入吸气管路。臭氧水制取用途请在臭氧发生器与吸入管路 之间安装单向止回阀+电磁阀,以免臭氧发生器进水损坏。
100%,比文氏混合器效率高三倍。 4、长期稳定性能、易操作易维护低噪音。
二、用途 1、臭氧水制取设备(纯净饮用水灭菌保鲜、污水脱臭脱色、改善 COD、BOD 等) 2、富氧水制取设备(富氧饮用水、密集鱼鳖养殖、水耕栽培等) 3、溶气气浮处理设备(各种类型气浮装置) 4、生化曝气设备(改善 COD、BOD、地下水除铁除锰等)
1.4
2.4
4.7
7.6
12
26
54
/
/
/
/
/
/
四、管路及附属件设备 1、吸入管路
1. 吸入管路的直径一般与泵的吸入口径相同或略大。利用负压吸入气体的情况下,吸入管 路的直径有时需要细一个等级,但不要过细。
2、供水槽的液面低于泵的中心高度,吸入管路需要安装底阀。 3、吸入管路需要安装滤网或 Y 形过滤器(60 目),以免液体中的固体物对泵叶轮造成损 坏。 2、排水管路 1、排水管路的直径一般与泵的排出口径相同或略大。 2、排水管路中需要安装气液分离罐(参照 4 其它附属件),气液分离罐后的管路至阀门的
长度一般为 0.5-1 米。 3、阀门(以截止阀为妥)需设置在排水管路末端(即气浮处理设备附近)。 4、阀门后面的管路(溶气水释放管路)应尽可能短且直,管径应略大于排水管口径。
备注:1.进水:溶气气浮用途,回流水由水处理槽直接进泵。2.进气:空气、氧气、臭氧 等。 3、溶气水释放管路
说明书

CP-1100型医用注射泵
检查注射泵是否完整、无损坏,电力输入电缆线是否与电源插头相适应。
首次使用前应充电12小时,以保证内部电池的正常使用。
接通AC电源,打开注射泵背部的电源开关,注射泵自动检测内部硬件工作状态。
开机:扳动注射泵后面板的黑色开关,注射泵进入待运行状态,显示视窗显示开机默认速度000.0ml/h,总量显示0.00ml。
关机:扳动注射泵后面板的黑色开关,注射泵退出待运行状态,显示视窗清除。
电池充电:在插好电源插座的情况下,面板上的交流指示灯亮,注射泵电池自动进入充电状态。
注射器安装及校正
把注射器压把提起,逆时针旋转90°,将注射器针管凸缘压在凹槽内,压把顺时针旋转压紧注射器。
按下防虹吸挡片按钮,按压注射器推座板机,可自由移动推座位置,将注射器推座向前推动,推座前面的触发点与注射器活塞尾端接触,当听到“咔”声后,防虹吸挡片按钮弹起,注射器安装完毕。
校正系数的方法:
将50ml(20ml)注射器的50ml(20ml)刻度线与校正指示标尺的其实线对齐,注射器0ml刻度线于标尺进行比较,确定注射器长度。
设定注射速度
注射泵处于停止状态,面板速度指示灯亮起:使用/ 键,增加或减小速度显示视窗对应列的数值,速度单位ml/h,按(开始)键。
SHNP 气动增压泵 操作和维护手册说明书
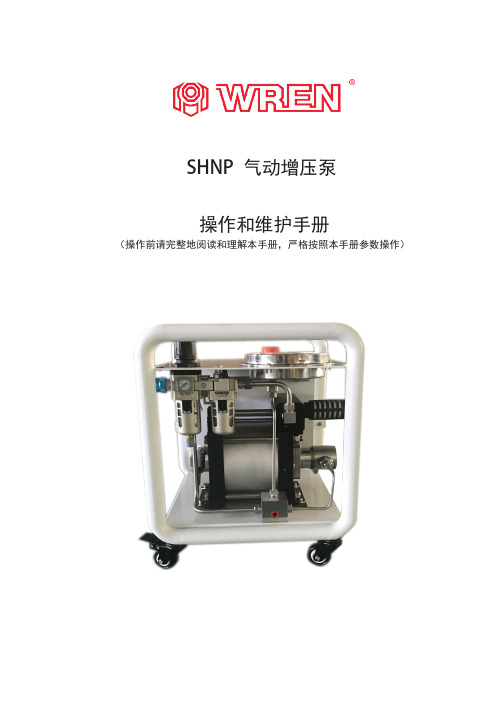
SHNP 气动增压泵操作和维护手册(操作前请完整地阅读和理解本手册,严格按照本手册参数操作)目录 1.0 介绍1.0介绍………………………………………22.0操作原理…………………………………23.0安装………………………………………34.0操作………………………………………35.0故障排除…………………………………46.0换向阀组件………………………………47.0撞针组件…………………………………68.0驱动主体及高压部分……………………7 此安装操作手册,提供了详细的信息 服务,内容为最新款SHNP 系列气 动增压泵。
SHNP 气动增压泵产品,一些组件的安 装及维护,和其他系列泵的维护相同 或相似。
本手册包含大部分信息,适用于所有 的SHNP 系列气动增压泵产品。
9.0技术参数.................................... 14 10.0 说明部分分解和补充数据 (15)条款和条件................................. 14 注意事项 (25)2.0 操作原理 危险!压缩空气或液体如果滥用可能导致严重伤害或死亡. 采取以下预防措施以减少风险. ●操作前完整地阅读和理解本手册●必须穿戴安全眼镜●加压中不要随意断开高压管路●不要在卸压时接触高压液体管路的出口●确认连接泵进出口的压力为泵的额定压力SHNP 系列气动增压泵是单头气驱液体增压泵,具有输出压力高、保压不能耗、自动吸液、自动保压、自动补压,并适用于多种介质等优点,并且应用领域广、结构简单、可靠性强、易于维护。
SHNP 系列气动增压泵广泛地应用于各种工业领域的设备配套。
如井口控制柜、胶管测试台、阀门测试台、容器测试设备、液体爆破测试台、液压工具动力包等。
SHNP 系列气动增压泵的驱动活塞直径为160mm 。
SHNP 系列气动增压泵的驱动气体入口为G1/2″,驱动气压≤8.3Bar 。
气动注浆泵讲解

ZBQ-50/6 型气动注浆泵使用说明书(本产品按MT124-85、Q/321100ZMZ030-2007标准生产)2007年4月编写第一版2007年5月出版目录安全警示 (1)一、概述 (1)二、结构及工作原理 (1)1.产品型号及意义 (1)2. 结构 (1)3. 工作原理 (2)4. 注浆 (2)三、基本参数 (3)四、使用与维护 (4)1.开泵前的准备 (4)2.注浆中的操作 (4)3.停泵后的维护 (4)4.可能发生的故障与处理 (5)附:气动注浆泵总装示意图 (6)气动注浆泵总装示意目录 (7)安全警示1、注浆前严格检查出浆胶管接头,确保牢固可靠;2、注浆时,高压胶管不允许非人为控制甩动,确保人身、设备安全;3、整机高压部位贴有安全标识及阀门开启方向;4、工作压力不允许超过7MPa;5、配套安标件不允许随意更换厂家。
一、概述ZBQ—50/6气动注浆泵主要用于矿井,地铁、隧道、水利、建筑等注浆堵水及破碎岩层的注浆凝结工程,也可以用于矿井适应的工作面预注浆。
该泵采用气压传动,体积小,重量轻,可无级调量,能定压自动调量,使用可靠,适用于井下作业。
在易燃,易爆,强磁、辐射,多尘埃,温度变化大以及淋水的场所,均可以安全使用。
●该泵在煤矿井下使用必须配用阻燃抗静电胶管!二、结构及工作原理1.产品型号及意义Z B Q □/ □压力MPa排量L/min气动注浆泵标记示例:ZBQ-50/6表示最大排量50L/min,最大输出压力6MPa的气动注浆泵。
2.结构泵的基本结构主要由管架、气缸、活塞、端盖、联接箱、液缸、进排浆缸、换向阀和一些辅助件组成。
该泵出厂时配有φ60mm,φ100mm两种液缸和二个φ100m的套,注浆时根据需要可以更换液缸。
更换时,先松开液缸左端4个M12螺母,拆下前缸盖,拿下液缸。
当需φ60mm液缸时,只需拿下前后缸盖的套即可直接安装φ60mm 的液缸;当需φ100mm液缸时,拿下前后缸盖上φ75mm的套,换上φ100mm的套便可安装φ100mm液缸。
DAB 193 中央气动泵说明书
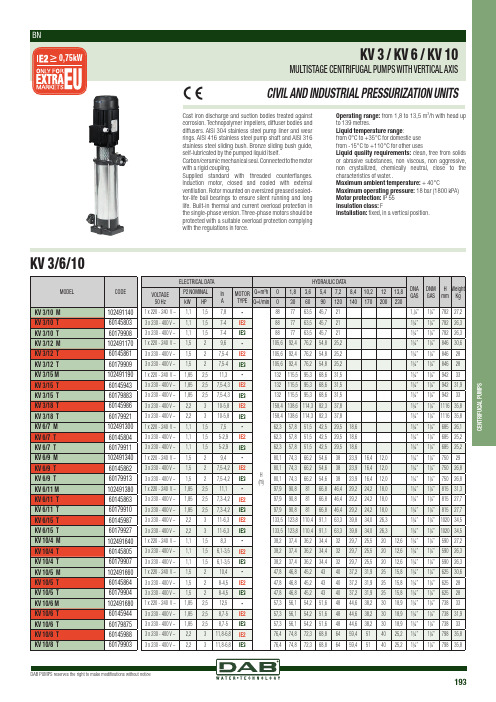
DAB PUMPS reserves the right to make modifications without notice193C E N T R I F U G A L P U M P SCast iron discharge and suction bodies treated against corrosion. Technopolymer impellers, diffuser bodies and diffusers. AISI 304 stainless steel pump liner and wear rings. AISI 416 stainless steel pump shaft and AISI 316 stainless steel sliding bush. Bronze sliding bush guide, self-lubricated by the pumped liquid itself.Carbon/ceramic m echanical s eal. C onnected t o t he m otor with a rigid coupling.Supplied standard with threaded counterflanges. Induction motor, closed and cooled with external ventilation. Rotor mounted on oversized greased sealed-for-life ball bearings to ensure silent running and long life. Built-in thermal and current overload protection in the single-phase version. Three-phase motors should be protected with a suitable overload protection complying with the regulations in force.Operating range: from 1,8 to 13,5 m3/h with head up to 139 metres.Liquid temperature range:from 0°C to +35°C for domestic usefrom -15°C to +110°C for other usesLiquid quality requirements: clean, free from solids or abrasive substances, non viscous, non aggressive, non crystallized, chemically neutral, close to the characteristics of water..Maximum ambient temperature: + 40°C Maximum operating pressure: 18 bar (1800 kPA) Motor protection: IP 55Insulation class: FInstallation: fixed, in a vertical position.KV 3/6/10。
Max Tool 气油水泵产品说明书
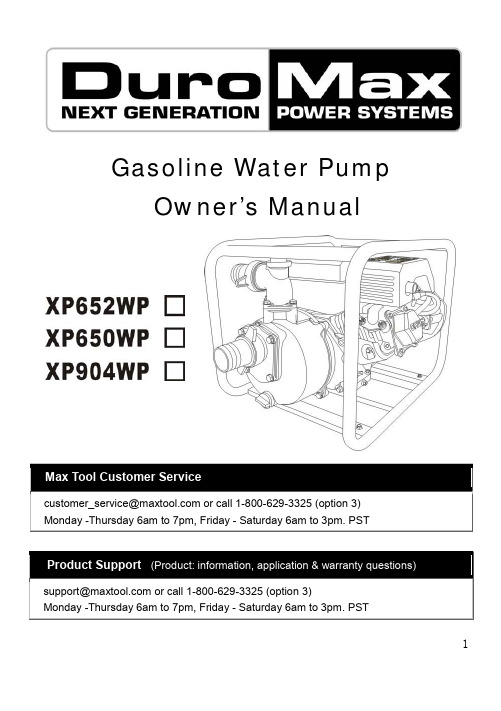
1Gasoline Water PumpOwner’s ManualThis manual provides information regarding the operation and maintenance of these products. We have made every effort to ensure the accuracy of the information in this manual. We reserve the right to change this product at any time without prior notice.Please keep this manual available to all users during the entire life of the gasoline water pump.CONTENTSⅠ. General Safeguards (1)Ⅱ. Location of Component Parts (3)Ⅲ. Operation before Starting Up (4)Ⅳ. Starting of Engine (9)Ⅴ. Use in Highland Areas (11)Ⅵ. Operation of Water Pump (12)Ⅶ. Shutting Down the Engine (13)Ⅷ. Maintenance (14)Ⅸ. Transportation and Storage (19)Ⅹ. Troubleshooting (21)Ⅺ. Specifications (23)23Ⅰ. General SafeguardsSafety PrecautionsBefore starting the engine, perform inspections according to the procedures described on pre-operation inspections to avoid accidents and damage to your machine.For safety, never attempt using this GEP (gasoline engine powered) water pump to deliver inflammable or corrosive liquids (such as gasoline and acids). Likewise, corrosive mediums, seawater, chemical solvents, alkaline liquids (such as used gasoline, liquor and honey) should be avoided.Place the water pump on a solid, level position surface to avoid tilting or turnover that may give rise to spilling of fuel.To prevent fire hazards, keep the pump well ventilated during operation and maintain a distance of at least l meter between the machine and the wall or other machines. Keep away from inflammable substances.Do not allow children and pets to enter the working area as this may increase the chance of their getting burned by hot surfaces of the operating parts.Know how to stop the water pump quickly how to operate the controls. Do not use the pump against the prescribed operating rules.WARNING :Safety PrecautionsThe gasoline fuel is highly inflammable and may explode under certain conditions.Do the fueling with the engine shut down and in a well-ventilatedenvironment. No smoking is allowed and no open fire or sparks allowed to exist in areas where fueling is carried out or the fuel is stored.Do not allow the fuel to overflow the fuel tank. Be sure to recap the tank and tighten it after refueling.When fueling, take care not to spill the gasoline about as the gasoline vapor may easily get ignited to cause a fire hazard. Be sure to remove the spilled gasoline as by wiping before starting the engine.Do not run the engine indoors or in a poorly ventilated space as the exhaust gas produced by the running engine contains toxic carbon monoxide that may cause the loss of personal consciousness or even death.45Ⅱ. Location of Component Parts6Ⅲ. Operation before Starting Up1. Connecting the water inletConnect the water inlet with a commercially available hose, connector and fastener clip. The inlet hose must be a continuous non-foldable structure with a length not more than required and should be placed near to the source of water so as to achieve the pump should be fitted to the end of the hose with the hose connector as shown in the figure below.CAUTION: Before pumping water, attach the filter to the end of the hose to filter out foreign matters in the water, the presence of which may cause clogging and damage to the wane wheel.NOTE: The hose connector and fastener clip should be securely fastened to prevent air leaks and reduction in suction power. A loosehose will reduce the pump performance and self-suction capacity.2. Connecting the water outletConnect the water outlet with a commercially available hose, hose connector and fastener clip. Large diameter hoses are the most effective while small ones will increase the flow resistance and reduce the output power of the pump.7NOTE:Be sure to the fastener clip is securely fastened to prevent the outlet hose from coming off under high water pressure.3.Checking the oil levelCAUTION:·The oil is one of the major factors affecting engine performance and life. Do not use dirty oil or vegetable oil.·Be sure to check the oil level with the engine shut down and placed on a level surface.Please use the SE15-40, 4-stroke engine oil as recommended.Please use the type of oil with a proper viscosity according to the local average temperature.Oil shortage alarm system (OSAS) (installation position)The OSAS is designed to avoid damage of the engine due to the shortage of oil in the crankcase. The system will automatically shut down the engine just before the crankcase oil level drops down to the minimum line of safety (with the engine switch staying in the ON position).If the engine is shut down and cannot be started again, check the oil level before initiating further troubleshooting procedures.Remove the oil dipstick and wipe it dry.Insert the dipstick into the oil filler but not screw it in.Replenish the crankcase with the recommended type of oil until8the oil level comes up to the upper most position of the refilled if the existing oil level is found too low.CAUTON:·Running the engine at a low oil level will cause damage to it.4. Checking the fuel levelUncap the fuel tank and check the fuel level. Pouring gasoline if the fuel level is found too low.Please use the type of gasoline recommended by the Dealer (Using the low lead content or lead-free gasoline type is good for minimizing carbon deposits inside the combustion chamber).Do not use a mixture of gasoline and oil or dirty gasoline to prevent dirt, dust or water from entering the fuel tank.CAUTION:·The gasoline fuel is highly inflammable and may explode under certain conditions.·Do the fueling with the engine shut down and in a well-ventilated environment. No smoking is allowed and no open fire or sparks allowed to exist in areas where fueling is carried out or the fuel is stored.·Do not allow the fuel to overflow the fuel tank. Be sure to recap the tank and tighten it after refueling.9·When fueling, take care not to spill the gasoline about as the gasoline vapor may easily get ignited to cause a fire hazard. Be sure to remove the spilled gasoline as by wiping before starting the engine.·Avoid frequent or extensive exposure of the skin to gasoline or breathing in the gasoline vapor. Keep the gasoline out of the reach of children.·Fuel tank capacity: 1.0 gallons (US. 3.6 liters)Screw the wing nut and remove the washer and cleaner cover.Check the filter element to see if it is too dirty and clean it if necessary.CAUTION:Do not run the engine without the air cleaner as this may quicken engine wear if dirt or dust is sucked into the engine through the carburetor.106. Checking and filling the pump with cooling waterThe pump must be filled with water before it is put to operation. CAUTION:·Do not attempt running the pump without cooling water or the pump will get overheated. Extensive running without cooling water may also damage the air tightness of the pump. If the pump is found running dry, stop the engine and pouring in water when it coolsdown.11Ⅳ. Starting engine1. Turn on the fuel tap (by setting it to the ON position).2. Close the choke.NOTE:·The choke is not required when starting the engine warm or the ambient temperature is rather high, (i.e. keep the choke open when starting the engine).3. Set the engine switch to the ON position.4. Turn the throttle control lever slowly to the left.5. Gently pull up the starter lever until a resistance is felt and then quickly pull it up.CAUTION:·Do not allow the starter lever to retract quickly into the engine. Let it go back gently to avoid damaging the starter.Ⅴ.Use in Highland AreasOperation in Highland ConditionsIn highland areas (with a high ASL elevation), the air-fuel mixture produced by a standard carburetor will be too thick and result in a reduced engine performance and soared fuel consumption. For operation in highland areas, the engine performance may be increased by using a smaller diameter carburetor nozzle and readjusting the carburetor idle speed. If the water pump is frequently used in areas with a ASL elevation of more than 1800 meters (6000 feet), ask the local dealer to replace or readjust the carburetor beforehand. Even if the engine is fitted with a carburetor nozzle of an appropriate size, the engine power will still go down by about 3.5% each time when the ASL elevation goes up by 305 meters (1000 feet). If no replacement or readjustment is ever made of the carburetor, the highland effect of the engine output power will be even more obvious.CAUTION:1213·Using the water pump in areas where the ASL elevation is lower than suitable for the carburetor nozzle will lead to a decreased engine performance and overheating of the engine and even cause serious damage to the engine due to an extremely thin air-fuel mixture.Ⅵ. Operation of the Water Pump1. Gradually open the choke after the engine warms up.2. Set the throttle to the predetermined RPM.Ⅶ. Shutting Down the Engine1. Set the throttle control lever to the right end.2. Set the engine switch to the OFF position.3. Turn off the fuel tap (by setting to the OFF position).NOTE:·To shut down the engine in an emergency, simply set the engine switch to the OFF position.Ⅷ. MaintenancePeriodic inspections and fine-tuning are simply indispensable to keep the water pump working with high performance and regular maintenance may also lengthen the pump life. Supplied in the table on the next page are intervals at which the schedules maintenance jobs are to be done.WARNING:·Before any maintenance attempt, be sure to shut down the engine. If the maintenance job has to be done with the engine at work, it should take place in a well-ventilated space as the exhaust gas contains toxic carbon monoxide that causes the loss of personal consciousness or even death.14CAUTION:·In cases when the pump is used to suck up seawater, be sure to flush it with fresh water immediately after use to minimize corrosion and remove deposits.·Always use the original parts and relevant tools supplied with the machine to carry out maintenance. Failure to do this may cause damage to the pump.NOTE:⑴Inspection and maintenance should take place more frequently if the pump is used in a dirty environment.⑵Leave the following inspection and maintenance jobs to the authorized dealers unless you, the user, have the relevant tools and necessary DIY skills. In the latter case, refer to service manual.16general power machinery Co., Ltd.1. Replacing the engine oilOil drains easily and quickly while the engine is warm.1. Remove the oil dipstick and drain bolt to let out the oil.2. Screw the drain bolt back in place and tighten it.3. Pour in clean oil until the desired level is reached.Oil sump capacity: 0.6 litersClean the hands with soap if stained with the engine oil.NOTE: Be sure to keep the environment clean when disposing used engine oil. We suggest you collect the waste oil in a container to be sent to a waste disposal site or a recycling service center of spill it in the garbage or on the ground.2. Maintaining the air cleanerA dirty air cleaner will let less air into the carburetor. To prevent carburetor malfunctions, be sure to maintain the air cleaner periodically. More frequent maintenance of the air cleaner will be necessary if the pump is working in an extremely dirty environment. DO not clean the air cleaner with a low ignition point solvent because it may get enflamed or even explode under certain17circumstances.CAUTION: Do not use the water pump without an air cleaner. Thedirt or dust if sucked into the engine may quicken engine wear.1) Unscrew the wing nut and remove the air cleaner cover and filter element.2) Clean the filter element with a detergent solution inflammable or with a high ignition point and let it dry thoroughly after cleaning.3) Immerse the filter element into clean oil and then squeeze out the excessive amount of oil.4) Put the filter element as well as the air cleaner back in place.3. Maintaining the spark plugThe recommended type of spark plug is NHSP LD P6RTCU.To ensure normal operation of the engine, the spark plug should have a correct gap and should remain free of carbon deposits.1) Remove the plug cap.The muffler may be very hot if the engine is still running. Take care not to touch the muffler.2) Check the spark plug visually. Discard the spark plug if it is18obviously worn out or the insulation ring on it is broken or cracked. Clean the spark plug with a brush when put it back in place.3) Check the plug gap with a feeler gauge.Vary the gap by moving the side electrode.Normal plug gap: 0.70~0.80mm4) Check the plug O-ring for normal condition. Screw it in with theplug wrench to protect the plug thread.NOTE:·In the case of screwing in a new spark plug, tighten it by an additional 1/2 screw turn after the plug reaches and pushes on the O-ring, while in the case of a used spark plug, an additional 1/2~1/4 screw turn is necessary.CAUTION:·Make sure the spark plug is properly tightened. Impropertightening may cause the engine to be overheated or damaged. Never use spark plugs with an incorrect thermal value range.Ⅸ. Transportation and Storage CAUTION:·To avoid causing a fire hazard, let the engine cool down before transportation or indoor storage of the pump.·Before transporting the pump, set the fuel tap to the OFF position and place the pump body in a level position to prevent the fuel from spilling out. The spilled gasoline or the gasoline vapor may get ignited.Note and do the following before storing pump for an extended period of time:1) Make sure the storage area is free of moisture or dust.2) Ch\lean the inside of the pump.The pump may get clogged if it is used to suck up water containing such matters as earth, sand or heavy fragments.Before storing, clean the pump by sucking up clean water or otherwise the wane wheel may be damaged when the pump is put to use again. After cleaning, unscrew the water drain plug to drain off the water from inside the pump casing as much as possible. Then screw the drain plug back into place.3) Drain off the fuel.a. Turn off the fuel tap (OFF position), unscrew the drain screw from the carburetor float chamber to drain off the fuel from inside the carburetor and collect the gasoline in a suitable container.b. Turn on the fuel tap (ON position) and collect the gasoline in a suitable container.c. Screw the carburetor fuel drain screw back into place.19204) Replace the engine oil.5) Screw off the spark plug, pour a spoonful of clean oil into the cylinder, turn the engine alternatively for several times to allow uniform distribution of oil, and then screw in the spark plug again.6) Pull up the starter lever until a resistance is felt. Stop pull for a while and pull it up again until the triangle mark on the starter wheel gets into collimation with the screw hole in the starter (as shown the sketch below). In this position, both the inlet valve and outlet valve is closed to prevent corrosion inside the engine.7) Cover up the pump to keep out dust.Ⅹ. TroubleshootingEngine unable to get started:1) Is there enough fuel?2) Is the fuel tap turned on?213) Has the fuel reached the carburetor? Make the check by unscrewing the oil drain screw from under the carburetor with thefuel tap turned on.WARNING:·Should there be a spill of fuel, be sure to clean it before checking the spark plug and start the engine or otherwise the spilled fuel or fuel vapor may get ignited4) Is the engine switch set to the ON position? 5) Is there enough oil in the crankcase? 6) Is the spark plug generating sparks?a. Uncap the spark plug, clear off the dirt from around the plug and remove the spark plug.b. Fit the spark plug into the plug cap.c. Turn on the engine with the side electrode and pull up the starter lever to see if there is sparks generated.d. Ground the engine with the side electrode and pull up the starter lever to see if there is sparks generated.e. Replace the spark plug if no spark is found.Start the engine as directed in the operation manual if sparks are generated.7) If the engine still refuses to get started, send the pump to any of the authorized dealers.22The pump unable to such up water: 1) Is it filled with enough amount of water?2) Is the filter clogged?3) Is the hose fastener clip tightened? 4) Is the hose damaged?5) Is the suction head too high?6) If the pump still fails to work, send it to any of the authorized dealers.Ⅺ. Specifications2324PARTS LIST AND ASSEMBLY (XP652WP/XP650WP)2526272829XP652WP3031XP650WP3233PARTS LIST AND ASSEMBLY(XP904WP)353637。
- 1、下载文档前请自行甄别文档内容的完整性,平台不提供额外的编辑、内容补充、找答案等附加服务。
- 2、"仅部分预览"的文档,不可在线预览部分如存在完整性等问题,可反馈申请退款(可完整预览的文档不适用该条件!)。
- 3、如文档侵犯您的权益,请联系客服反馈,我们会尽快为您处理(人工客服工作时间:9:00-18:30)。
一、概述
本气动注浆泵执行标准:Q/XSR 001—2011
1、产品特点:
2ZBQ—8/12型气动注浆泵动力为全气动,可单、双液注浆,压力可调式注浆泵;气动注浆泵设计结构简单、性能稳定可靠,使用可靠,寿命长,具有体积小,重量轻,灵活可靠,应用广泛等众多特点,移动搬运方便,适应移动频繁的多点注浆。
2ZBQ—8/12型气动双液注浆泵由于采用气压传动,配气换向装置技术先进,配气换向动作灵敏,能够改变压气的流量进行无级调速。
使泵的注浆性能非常适合于注浆压力低时大流量,而注浆压力升高时小流量的工况。
因采用气压传动在易燃、高爆、淋水、尘埃大等工作环境下也可使用。
在浆液比要求严格的条件下可用一泵就可实现双液注浆,大大降低施工设备购置费用。
注浆泵直接放置在比较平整的地面上即可;泵的进出口均采用快插接口,连接吸排料管方便快捷,而且密封可靠;气动马达带动三个活塞,马达和三个活塞的活塞面积比为27:1。
气缸活塞作往复运动。
因气缸拉杆与浆缸拉杆相连接,从而气缸活塞往复运动同时也推动浆缸活塞作往复运动完成吸排浆动作,达到连续注浆要求。
2、用途:
气动注浆泵主要用于树脂、溶剂等液体介质的压送。
主要应用于
煤矿、隧道等工程中双组份材料的输送、混合。
当压送某种材料时,
一定要详细阅读材料使用说明。
3、型号及其意义
2ZB Q — 8 / 12
额定排浆压力(MPa)
额定流量(L / min)
动力为气动式
表示为双液注浆泵
4、使用环境条件
气动注浆泵使用温度为0—80℃之间,置于有压缩空气的地方,气压在0.2—0.63MPa范围内,供气压力切勿超过最大值0.8Mpa。
注意有压气供应时注浆泵活塞运动,运动着的活塞及其部件有可能夹住甚至夹断手指或身体其它部位,开启或使用泵时与活塞及其运动部件保持距离。
维修和停止气泵工作前一定要停止压气供应并且进行卸压,以防气泵意外启动。
运动部件对气泵和人身造成伤害。
每次注浆泵注浆完毕后,应对泵进行冲洗,按照使用材料对清洗剂的要求说明选择清洗剂,切勿乱用清洗剂造成堵塞报废。
二、结构特征
图1 注浆泵示意图
图1说明
三、技术特性
四、使用、操作
1、使用前的准备和检查
①、注浆泵、软管和混合枪是否已按图1接好,按比例要求将软管(15、
16、17)分别接到相应的A、B、C接口上,并要检查U型卡是否完整无缺、正确安装。
安装方法如图2。
图2:软管连接
②、各部件是否完整无缺、正确安装、无损坏和失灵情况。
③、混合枪操作人员和泵操作人员是否联系方便,不受二者距离的限制。
④、润滑空气过滤器是否缺油。
⑤、干燥器是否多水。
⑥、供气压力要控制在0.7MPa以下。
⑦、准备好一桶(20Kg )所压送原料专用清洗剂。
2、操作方法:(零部件标号如图1,其中阀门原始状态均为关闭)
①、将吸料软管(12、13、14)分别插进两种液体桶中,打开球阀(20、
21、24)。
②、打开球阀(10),泵开始工作。
③、当两种原料分别从球阀(21、24)流出,关闭球阀(10)停泵,
关闭球阀(21、24),然后打开球阀(25)。
④、打开球阀(10)泵开始压送两液体料在混合管(27)混合后经高压管(28)送到目的位置。
3、注射中要时常观察以下参数保证泵良好的工作。
①、压力表(8);
②、两种液体的混合比例;
③、泵活塞的运动速度
4、停泵和冲洗
①、当压送完毕后,将吸料软管从料桶抽出,插到清洗剂桶中,清洗剂用完后,换清水。
②、清水清洗约2分钟,关闭球阀(10)停泵。
③、断开气压供应管
④、拆下吸料管(12、13、14)、高压管(15、16、17)和混合枪(29)分别包装后放置到安全位置。
5、注意:
压送物料时,一定要详细阅读物料的使用说明和注意事项,并认真按泵的操作规程操作。
五、故障分析与排除
1、维修需用工具:
∙ 1 把开口扳子 (10 x 12) ∙ 1 把开口扳子 (13 x 15) ∙ 1 把开口扳子 (14 x 17) ∙ 1 把开口扳子 (16 x 18) ∙ 1 把开口扳子 (19 x 22) ∙ 1 把开口扳子 (21 x 24) ∙ 1 把开口扳子 (27 x 30) ∙ 1 把内六角扳子(10)∙ 1 把勾扳子(42)∙ 1 把勾扳子(55)∙ 1 把管钳
∙ 1 把15 "活络扳子∙ 2 把螺丝刀
∙ 1 把普通钢丝钳
∙ 1 把锤子
∙
2、维修需用备件:
建议常备以下备件,以便泵工作时出现问题即时更换。
∙ 1 个30活塞∙ 1 个21活塞∙ 1 套座阀
∙ 2 个KJ13球阀∙ 1 个DN13的单向阀∙ 2 个混合管
∙ 1 套混合枪
∙ 1 套密封圈
六、保养维护:
大约压送30吨原料后就要更换A活塞和A/2活塞磨损的部件。
养护工作前先要卸压。
即使原来部件外观仍然良好,也要更换所有原来部件。
图4 活塞剖面图
1.拆卸:
卸下活塞(图4)的底阀(19)。
如
果座阀粘住卸不下,在其螺纹里
滴几滴油,用锤子轻敲活塞来卸
下座阀。
分别卸下销子(13),钢球
(1),阀套(14)和密封圈(15)。
清洗
所有部件确保无损坏。
用备件袋
里的钢球(1)和密封圈(15)换下损坏
的零件。
拧开压紧螺母(4),将活
塞杆(17)向下推取出。
注意:拆卸过程中不要划坏活塞
的光滑表面。
从活塞杆(17)上拧下活塞底
座(20),取下滚珠(2),去掉垫片
(10和11),衬垫(16) 和垫圈(18)。
清洗所有部件确保无损坏。
更换钢球(2),凸型、凹型支撑圈(10和11)和V 型密封圈( (16)。
拧下压紧螺母4),取下导向套(6), V型密封圈(12),凸型、凹型支撑圈 (7和8)和垫圈(9)。
清洗所有部件确保无损坏。
更换V 型密封圈(12),凸型、凹型支撑圈(7和8)。
2、安装:
安装前所有部件上润滑油。
重新安装活塞时注意垫片和衬垫的顺序,衬垫凹型放置,以承受原料压力。
安装垫圈(9),衬垫(12),垫片(7和8),轴承(6)和封严帽螺母,封严帽螺母不要拧紧。
衬垫凸型放置,以承受原料压力。
将滚珠(2)装进活塞杆(17)。
往活塞底座的螺纹里涂上密封胶,将其拧进活塞杆(17)。
从活塞底部装进活塞杆,用10mm 内六角扳手拧紧底座。
上底阀固定。
七、开箱及检查
开箱后检查泵、工具及备件数量及附件是否符合,如有不附之处,请与我公司联系。