锂离子电池极耳胶腐蚀机理
详解软包锂离子电池极耳

详解软包锂离子电池极耳1. 电池极耳是什么?极耳,是软包锂离子电池产品的一种组件。
电池分为正极和负极,极耳就是从电芯中将正负极引出来的金属导电体,通俗的说电池正负两极的耳朵是在进行充放电时的接触点。
电池的正极使用铝(Al)材料,负极使用镍(Ni)材料,负极也有铜镀镍(Ni—Cu)材料,它们都是由胶片和金属带两部分复合而成。
2.极耳的分类2.1按极耳金属带材质分:⑴铝(Al)极耳,一般用作正极极耳,如果电池为钛酸锂负极时,也用作负极极耳。
⑵镍(Ni)极耳,用作负极极耳,主要用在数码类小电池上,例如:手机电池、移动电源电池、平板电脑电池、智能传递设备电池等。
⑶铜镀镍(Ni—Cu)极耳,用作负极极耳,主要应用于动力电池和高倍率电池。
2.2 按照极耳胶来分(国内市场):⑴黑胶极耳,一般用在中低端数码类小电池上。
⑵黄胶极耳,一般用在中低端动力电池和高倍率电池上。
⑶白胶极耳,一般用在高端数码电池、动力电池和高倍率电池上。
2.3极耳的成品包装分为:⑴盘式极耳(整条金属带通过设备加上胶片后整条的卷绕成盘),用在自动化生产产线⑵板式极耳(金属带加上胶片后裁切成单个的,然后成排摆放用两片薄透明塑料片夹在中间),用于普通生产产线。
3.电池极耳金属带材质AL1050铝合金为纯铝中添加少量铜元素形成,具有极佳的成形加工特性、高耐腐蚀性、良好的焊接性和导电性。
TU1为无氧铜,氧和杂质含量极低,纯度高,导电导热性极好,延展性极好,透气率低,无“氢病”或极少“氢病”;加工性能、焊接、耐蚀耐寒性均好。
4.各种品牌极耳胶结构与性质4.1. 各种品牌极耳胶结构目前极耳胶都是从日本进口而来,极耳胶生产技术难点是:PP材料的分子量要控制在一个比较窄的范围内,目前国内的技术生产出的PP胶达不到要求。
极耳胶结构:极耳胶一般由三层材料热压在一起而构成,除凸版及昭和制造单层改性PP构成及腾森制造五层极耳胶以外。
一般极耳胶由中间骨架层及两表面改性PP层构成,两表面的改性PP材质相同。
极耳绝缘胶特性说明
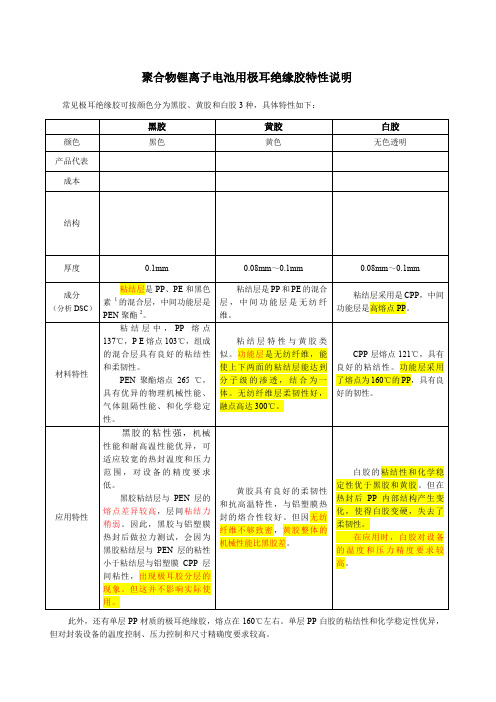
聚合物锂离子电池用极耳绝缘胶特性说明
常见极耳绝缘胶可按颜色分为黑胶、黄胶和白胶3种,具体特性如下:
此外,还有单层PP材质的极耳绝缘胶,熔点在160℃左右。
单层PP白胶的粘结性和化学稳定性优异,但对封装设备的温度控制、压力控制和尺寸精确度要求较高。
黑胶和黄胶对设备的精度要求相对较低,对于一般软性封头的封装设备,使用黑胶和黄胶较为适合。
使用时一定要选用匹配的铝塑膜,调好热封温度和压力,以封装不良和降低电解液渗透的风险。
注:
1 按供应商所提供的资料,黑色素的熔点是66℃,但实际测试熔点时,并未在此温度发现吸热峰。
分析认为是其含量过小,以测试时所使用仪器的精度未能测出。
2 PEN是聚萘二甲酸乙二醇酯的简称,其化学结构与PET相似,不同之处在于分子链中,PEN由刚性更大的萘环代替了PET中的苯环,使PEN比PET具有更高的物理机械性能、气体阻隔性能、化学稳定性及耐热、耐紫外线、耐辐射等性能。
锂离子电池铝壳腐蚀电位及影响因素的研究

锂离子电池铝壳腐蚀电位及影响因素的研究一、引言锂离子电池作为一种高性能、高安全性的电池,已经广泛应用于电动车、智能手机等领域。
然而,锂离子电池在使用过程中存在着铝壳腐蚀的问题,导致电池寿命缩短、性能下降等不良影响。
因此,研究锂离子电池铝壳腐蚀电位及其影响因素具有重要意义。
二、锂离子电池铝壳腐蚀机理锂离子电池的正极材料通常采用氧化物(如LiCoO2、LiMn2O4等)或磷酸盐(如LiFePO4)等化合物,负极材料则采用石墨或硅等材料。
正负极材料之间通过隔膜隔开,并浸泡在电解液中。
在充放电过程中,正负极材料之间的离子交换会引起电解液中水分解产生氢氧根离子和氢离子,其中氢氧根离子与铝壳反应生成Al(OH)4-,进而形成Al2O3保护层。
但当电池使用时间过长,电解液中的水分解产物逐渐增多,导致Al(OH)4-浓度升高,铝壳腐蚀速度加快,最终形成孔洞和腐蚀坑。
三、锂离子电池铝壳腐蚀电位的测定方法锂离子电池铝壳腐蚀电位是指在一定条件下,铝壳开始发生腐蚀的电位值。
通常采用静态浸泡法或动态极化法来测定。
静态浸泡法是将铝壳置于一定温度、pH值和氧分压下的模拟电解液中静置一段时间后,通过扫描电位仪等设备记录铝壳表面的极化曲线,并确定起始点对应的电位值;动态极化法则是在扫描一定范围内施加一个恒定的扫描速率来观察铝壳表面的极化曲线,并计算出起始点对应的电位值。
四、影响锂离子电池铝壳腐蚀电位的因素1. 电解液成分:不同类型、不同浓度的盐酸、硫酸等电解液会对铝壳腐蚀电位产生不同的影响。
2. 温度:温度升高会加速铝壳腐蚀速度,从而降低铝壳腐蚀电位。
3. pH值:pH值升高会使电解液中Al(OH)4-浓度降低,从而提高铝壳腐蚀电位。
4. 氧分压:氧分压升高会促进Al(OH)4-生成,加快铝壳的腐蚀速度,从而降低铝壳腐蚀电位。
五、锂离子电池铝壳防护方法为了延长锂离子电池的使用寿命和提高性能,需要采取有效的防护措施。
常见的防护方法包括:1. 采用复合材料或塑料外壳代替铝壳;2. 在铝壳表面涂覆一层保护性涂层(如聚合物、氧化物等);3. 优化电解液配方,降低Al(OH)4-浓度;4. 控制温度、pH值和氧分压等因素。
简析软包锂电池的极耳部分贴胶机构

简析软包锂电池的极耳部分贴胶机构锂电池电芯在制作时需要在极耳上焊接Tab lead,这样对极耳进行加长,方便后面的顶侧封将Sealant融化进行密封。
Tab lead焊接采用超声波进行焊接,在焊接完成后,极耳上会有焊点产生,而且由于极耳伸出高度位置不一定适合我们的要求,一般需要对极耳进行折弯,在这种情况下容易产生短路,所以需要对焊接的位置进行贴绝缘胶带,而且极耳的两面都需要粘贴上绝缘胶带(见图1)。
市面上目前主流的贴绝缘胶的方式有两种,现在我们就对这两种方式进行分析找出它们各自的优缺点,使我们在生产过程中找到更合适的贴绝缘胶方式。
1 贴胶机构简介由于需要对电芯的正极和负极两个极耳的正面和反面进行贴绝缘胶带,一共是4个贴胶绝缘胶带的动作,为了提高贴胶机构的空间利用率,一般采用两个工位进行贴胶:一个对正极正反两面进行贴绝缘胶带;另一个对负极正反两面进行贴绝缘胶带,也就是说需要一个对锂电池电芯极耳进行正反两面同时进行贴胶的机构。
贴胶分两组动作完成,即备绝缘胶带和贴绝缘胶带,备绝缘胶带是将两卷绝缘胶带切断为需要的长度并让其吸附在上下两组吸胶带的吸头上;贴绝缘胶带是将已经吸附在吸头上的两条绝缘胶带粘贴在极耳的正反两面上。
备绝缘胶带有两种方式:一种为送料式;另一种为拉料式,贴胶机构的区分主要集中在备胶方式上。
2 送料式备绝缘胶带送料式备绝缘胶带由以下机构组成:(1)绝缘胶带上料机构;(2)重力锤;(3)过辊;(4)断带感应器;(5)切断刀;(6)吸盘;(7)送胶带机构;(8)胶带压紧机构(压紧部分为铁氟龙材质,防止胶带粘附在压紧机构上);(9)吸盘上下机构;(10)吸盘驱动机构(见图2)。
送料式备绝缘胶带工作流程:送胶带机构将绝缘胶带送到指定位置(可以通过触摸屏进行设置,此位置决定了胶带长度),吸盘上下机构驱动吸盘下降,然后由胶带压紧机构将胶带头端压在吸盘上,此时送胶带机构再向回移动到起始点,并将胶带后端夹紧同时做向上提升的动作,使绝缘胶带背面完全贴紧吸盘,然后由吸盘将胶带吸附,此时胶带前段由吸盘和胶带压紧机构配合固定,后端由送胶带机构固定,由于重力锤的存在,使胶带形成一个绷紧的状态,此时切断刀在吸盘与胶带后端固定处之间将绝缘胶带切断,胶带被切断后,胶带压紧机构脱离吸盘,使吸盘吸附的是一段完整的定长的绝缘胶带,这样就完成了送料式备绝缘胶带的工作,后面吸盘上下机构将吸附了胶带的吸盘提升,吸盘位置驱动机构将吸盘移动到需要贴绝缘胶带的电芯处,吸盘上下机构再进行贴胶动作,完成贴胶动作后吸盘位置驱动机构回原位,这样就形成了一个完整的贴胶循环。
软包锂离子电池极耳结构设计及充电性能分析
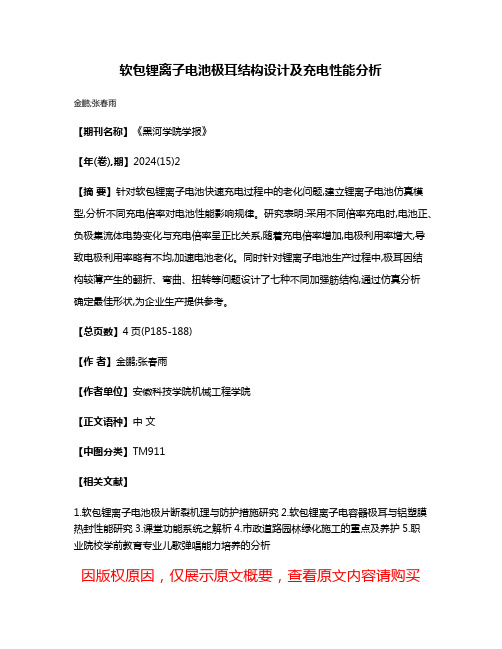
软包锂离子电池极耳结构设计及充电性能分析
金鹏;张春雨
【期刊名称】《黑河学院学报》
【年(卷),期】2024(15)2
【摘要】针对软包锂离子电池快速充电过程中的老化问题,建立锂离子电池仿真模型,分析不同充电倍率对电池性能影响规律。
研究表明:采用不同倍率充电时,电池正、负极集流体电势变化与充电倍率呈正比关系,随着充电倍率增加,电极利用率增大,导致电极利用率略有不均,加速电池老化。
同时针对锂离子电池生产过程中,极耳因结
构较薄产生的翻折、弯曲、扭转等问题设计了七种不同加强筋结构,通过仿真分析
确定最佳形状,为企业生产提供参考。
【总页数】4页(P185-188)
【作者】金鹏;张春雨
【作者单位】安徽科技学院机械工程学院
【正文语种】中文
【中图分类】TM911
【相关文献】
1.软包锂离子电池极片断裂机理与防护措施研究
2.软包锂离子电容器极耳与铝塑膜热封性能研究
3.课堂功能系统之解析
4.市政道路园林绿化施工的重点及养护
5.职
业院校学前教育专业儿歌弹唱能力培养的分析
因版权原因,仅展示原文概要,查看原文内容请购买。
锂离子电池腐蚀损伤机理和防护策略
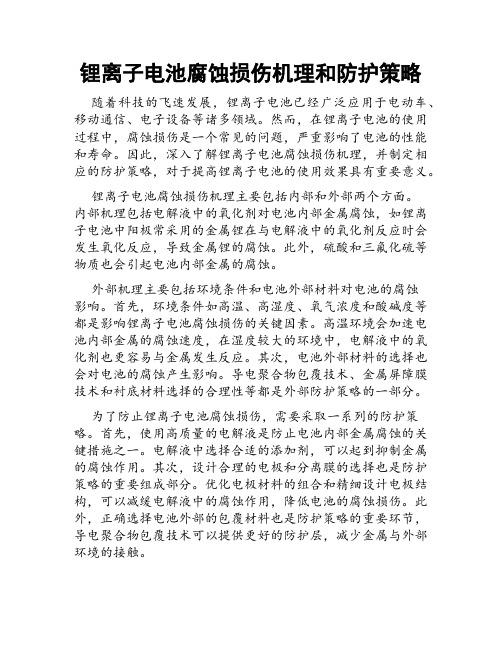
锂离子电池腐蚀损伤机理和防护策略随着科技的飞速发展,锂离子电池已经广泛应用于电动车、移动通信、电子设备等诸多领域。
然而,在锂离子电池的使用过程中,腐蚀损伤是一个常见的问题,严重影响了电池的性能和寿命。
因此,深入了解锂离子电池腐蚀损伤机理,并制定相应的防护策略,对于提高锂离子电池的使用效果具有重要意义。
锂离子电池腐蚀损伤机理主要包括内部和外部两个方面。
内部机理包括电解液中的氧化剂对电池内部金属腐蚀,如锂离子电池中阳极常采用的金属锂在与电解液中的氧化剂反应时会发生氧化反应,导致金属锂的腐蚀。
此外,硫酸和三氟化硫等物质也会引起电池内部金属的腐蚀。
外部机理主要包括环境条件和电池外部材料对电池的腐蚀影响。
首先,环境条件如高温、高湿度、氧气浓度和酸碱度等都是影响锂离子电池腐蚀损伤的关键因素。
高温环境会加速电池内部金属的腐蚀速度,在湿度较大的环境中,电解液中的氧化剂也更容易与金属发生反应。
其次,电池外部材料的选择也会对电池的腐蚀产生影响。
导电聚合物包覆技术、金属屏障膜技术和衬底材料选择的合理性等都是外部防护策略的一部分。
为了防止锂离子电池腐蚀损伤,需要采取一系列的防护策略。
首先,使用高质量的电解液是防止电池内部金属腐蚀的关键措施之一。
电解液中选择合适的添加剂,可以起到抑制金属的腐蚀作用。
其次,设计合理的电极和分离膜的选择也是防护策略的重要组成部分。
优化电极材料的组合和精细设计电极结构,可以减缓电解液中的腐蚀作用,降低电池的腐蚀损伤。
此外,正确选择电池外部的包覆材料也是防护策略的重要环节,导电聚合物包覆技术可以提供更好的防护层,减少金属与外部环境的接触。
除了以上的防护策略,正确的使用和储存方式也至关重要。
锂离子电池应存放在干燥、通风良好的环境中,避免高温和潮湿的环境。
同时,在使用过程中也要避免过度放电和充电,以减少电池内部金属的腐蚀。
综上所述,锂离子电池的腐蚀损伤机理涉及电池内部和外部两个方面,需要全方位的防护策略来保护电池的性能和寿命。
锂离子动力电池极耳介绍
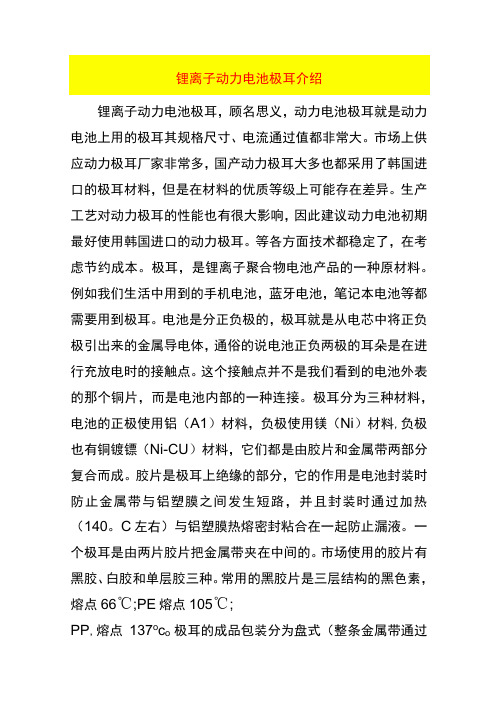
锂离子动力电池极耳,顾名思义,动力电池极耳就是动力电池上用的极耳其规格尺寸、电流通过值都非常大。
市场上供应动力极耳厂家非常多,国产动力极耳大多也都采用了韩国进口的极耳材料,但是在材料的优质等级上可能存在差异。
生产工艺对动力极耳的性能也有很大影响,因此建议动力电池初期最好使用韩国进口的动力极耳。
等各方面技术都稳定了,在考虑节约成本。
极耳,是锂离子聚合物电池产品的一种原材料。
例如我们生活中用到的手机电池,蓝牙电池,笔记本电池等都需要用到极耳。
电池是分正负极的,极耳就是从电芯中将正负极引出来的金属导电体,通俗的说电池正负两极的耳朵是在进行充放电时的接触点。
这个接触点并不是我们看到的电池外表的那个铜片,而是电池内部的一种连接。
极耳分为三种材料,电池的正极使用铝(A1)材料,负极使用镁(Ni)材料,负极也有铜镀镖(Ni-CU)材料,它们都是由胶片和金属带两部分复合而成。
胶片是极耳上绝缘的部分,它的作用是电池封装时防止金属带与铝塑膜之间发生短路,并且封装时通过加热(140。
C左右)与铝塑膜热熔密封粘合在一起防止漏液。
一个极耳是由两片胶片把金属带夹在中间的。
市场使用的胶片有黑胶、白胶和单层胶三种。
常用的黑胶片是三层结构的黑色素,熔点66℃;PE熔点105℃;PP,熔点137o c o极耳的成品包装分为盘式(整条金属带通过设备加上胶片后整条的卷绕成盘)和板式(金属带加上胶片后裁切成单个的,然后成排摆放用两片薄透明塑料片夹在中间)OT:极耳厚度,W:极耳宽度(胶片宽度),T1:胶片厚度,g:胶片错位值,t:金属带厚度,I:胶片高度,1:金属带毛刺,P:单个极耳长度(并不是指单个极耳是从两个胶片的顶端裁切,客户自己决定胶片两端的长度),M:极耳肩宽,d:金属带宽度。
极耳用规格命名的方式为:金属带厚度tX金属带宽度d—胶片高度IX胶片宽度W—单个极耳长度P例如0.1x2mm—4.2x5mm—30mm o另外动力极耳也可以做成圆角的。
聚合物锂离子电池用极耳绝缘胶特性说明
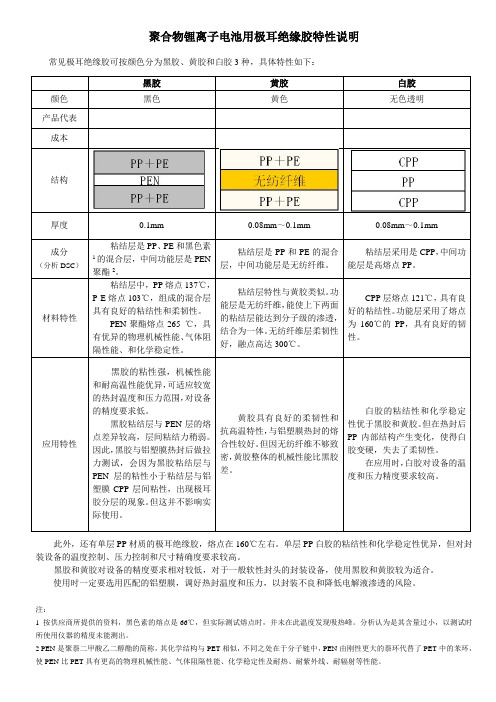
聚合物锂离子电池用极耳绝缘胶特性说明
常见极耳绝缘胶可按颜色分为黑胶、黄胶和白胶3种,具体特性如下:
此外,还有单层PP材质的极耳绝缘胶,熔点在160℃左右。
单层PP白胶的粘结性和化学稳定性优异,但对封装设备的温度控制、压力控制和尺寸精确度要求较高。
黑胶和黄胶对设备的精度要求相对较低,对于一般软性封头的封装设备,使用黑胶和黄胶较为适合。
使用时一定要选用匹配的铝塑膜,调好热封温度和压力,以封装不良和降低电解液渗透的风险。
注:
1 按供应商所提供的资料,黑色素的熔点是66℃,但实际测试熔点时,并未在此温度发现吸热峰。
分析认为是其含量过小,以测试时所使用仪器的精度未能测出。
2 PEN是聚萘二甲酸乙二醇酯的简称,其化学结构与PET相似,不同之处在于分子链中,PEN由刚性更大的萘环代替了PET中的苯环,使PEN比PET具有更高的物理机械性能、气体阻隔性能、化学稳定性及耐热、耐紫外线、耐辐射等性能。
- 1、下载文档前请自行甄别文档内容的完整性,平台不提供额外的编辑、内容补充、找答案等附加服务。
- 2、"仅部分预览"的文档,不可在线预览部分如存在完整性等问题,可反馈申请退款(可完整预览的文档不适用该条件!)。
- 3、如文档侵犯您的权益,请联系客服反馈,我们会尽快为您处理(人工客服工作时间:9:00-18:30)。
腐蚀研究电芯从开始到结束共有三次阻抗测试,包括:极片Hi-pot测试、Foil电阻测试和内阻(IMP)测试。
Hi-pot影响电芯的化成,内阻(IMP)影响电芯的自放电,它们只反应到电芯的电压、容量性能,可以通过现有的高精度设备将坏品挑出。
但Foil电阻坏品有发生腐蚀的可能性,一般需要一段时间最终在客户出表现出来,它的失效表现为外观Al被腐蚀破烂,变黑,电芯胀气,无法使用,可以说是最严重的坏品表现,是一件非常恐怖的事情!Foil电阻坏品指的是电芯Nitab(阳极)与包装铝箔Al layer短路,目前定义Ni tab 与Al layer 电阻低于1.0×200Mohm(非OEM产品)和OEM产品为低于2.0×200Mohm的为电阻坏品,使用万用表测量挑出以避免电芯在客户处发生腐蚀。
当然,电阻越大甚至无穷大,发生腐蚀的概率越低。
对于这两个标准的选择是基于对电芯进行On-hold模拟测试而定,大概客户反应的腐蚀坏品为4ppm,个别案例除外(指由于特殊原因导致电芯必然会发生腐蚀)。
我们知道控制这种电阻坏品的目的是防止包装铝箔的铝层发生腐蚀,下面就从腐蚀发生原因、腐蚀防止、电阻坏品防止几个方面入手介绍。
腐蚀原因引起电芯腐蚀必须具备两个短路的通道:一,离子短路通道,即包装铝箔铝层与阳极发生离子短路;二,电子短路通道,即包装铝箔铝层与阳极发生电子短路。
这样包装铝箔的铝层就与阳极形成一个短路的回路,阳极即为电芯负极,处于低电势的部分,一旦与铝接触会通过电导率较高的电解液引起电化学反应,导致铝层的不断被消耗。
空气中水分会进入电芯内部导致进一步反应产生大量气体。
这两种短路是电芯发生腐蚀的必要条件,两者缺一不可。
腐蚀防止我们知道离子短路和电子短路是发生腐蚀的必要条件,要防止腐蚀就必须弄清楚两种短路形成的原因。
我们已经知道了包装铝箔的结构,内部为绝缘PP,PP的一个作用就是绝缘,将电解液环境与铝层隔离,保护铝层,发生离子短路是由于PP发生破损致使电解液渗透将铝层与阳极导通,因此腐蚀均发生在PP破损部位。
电子短路必须是有导体在阳极和铝层(PP破损处)间能够导通电子或阳极通过Ni tab直接与铝层短路导通电子。
要防止腐蚀的发生就必须杜绝两种短路的存在。
在电芯的封装过程中,封边部位的PP受到热压后PP比较容易发生破损,所以会产生比较多的电阻坏品,因此只要发生电子短路,腐蚀必然发生,防止腐蚀,必须先从防止电子短路开始。
阳极通过Ni tab与包装铝箔铝层在顶封部位发生短路,PP绝缘胶失去保护作用,Ni tab与铝层接触,这种情况必然会发生腐蚀。
目前Ni tab与包装铝层发生短路主要有两种情况:第一,在顶封过程中两者直接短接:a.顶封封头槽位与包装铝箔厚度不匹配或封头变形损坏等导致Ni tab顶封时PP变形率过大,被挤压到严电芯长度方向,Ni tab与铝层导通;b.顶封夹具、Loading操作失误或顶边宽度设计不够,顶封时封头压偏在Ni tab上,使Tab顶部PP被挤压流走,发生短路;c.顶封封头槽位压在Ni tab上或过度压偏导致两者短路;d.顶封夹具调整不合理或Tab中心矩不合格(尤其焊接返修产品),在loading电芯时为Ni tab发生扭曲,导致两者在封装过程中短路;e.Tab上有毛刺或杂质刺穿Sealant和PP导致两者短路。
第二,在焊接PTC或Fuse过程中,折叠Ni tab两者直接发生短路:a.顶封后Nitab上Sealant没有外露或外露长度不够,导致在折叠后Ni tab直接与包装铝箔截面铝层发生短路;b.如2×0.5mm Ni tab 比较柔软,由于折叠方法问题导致Nitab与截面铝层导通(即使有外露Sealant保护);451730曾经由于此种原因在客户处发生大量腐蚀,缘由是由于加工商没有考虑到折叠后对截面的绝缘保护。
以上所列到的原因为实际过程中对腐蚀样品失效分析经验的总结,Ni tab一旦与包装铝箔铝层发生直接短路,电子直接导通,必然会发生腐蚀,毋庸置疑!在生产过程中必须注意对以上所列举的方面的控制,同时在进行腐蚀失效时也需要先从这几个方面入手。
其实除阳极通过Ni tab与铝层在顶封部位直接发生短路外,还有另外一种情况就是在电芯内部阳极通过电子导电物质与P P破损处裸露铝层短路。
电子导电物质一般为金属Partical、碳粉或导电剂物质,多发生P1工艺的Model上,因为它的阳极几乎直接暴露在PP破损的两个侧封边部位。
P2工艺电芯由于表面有隔离膜包裹住电芯,封边部位阳极没有与铝层接触的可能性,目前位置尚未发现因为电子导电物质引起腐蚀的案例。
M6S卷绕工艺电芯由阴极收尾,外面一层为阴极铝箔,隔离膜和阴极铝箔会阻止阳极与铝层接触,但M6S采用的是Overhung的设计方式,阳极要超出阴极1mm,当发生严重错位阳极膜片会在电芯底部或顶部伸出隔离膜而暴露,阳极膜片比较脆碳粉等导电物质易脱落引起短路,383450目前位置有一个电芯为此种短路案例。
刚才介绍了引起电阻坏品及发生腐蚀的诸多原因,引起电芯发生腐蚀最常见的直接因素便是顶封部位Ni tab与包装铝箔铝层发生短接,由于前面所指各种原因导致该部位绝缘胶变薄,不能完全隔断Nitab与包装铝箔铝层。
可以参考下面的示意图:以上为短接情况的示意图,我们在分析时需要进行切边观察,沿Tab方向切刮掉包装铝箔和Sealant胶,在高倍率放大镜下观察切边Ni tab和包装铝箔铝层的位置情况,下图a为切面观察无短路情况,图b为切面观察发生短路的情况。
可作为参考。
层发生短接。
图c所示Ni tab在铝箔上有明显的印痕,图d将Ni tab弯折后测量发生为短路。
图c 图d电子短路一旦形成必然会发生腐蚀,因此必须在各过程中控制严防电子短路的发生,工艺、夹具、操作方法规范可避免直接短路的发生,还需要控制电子导电物质的存在,注意顶封前的各工序对隔离膜、阴、阳极、Pocket、Tray、操作台面等partical的预防控制,目前在顶封lo ading电芯前采用吸尘方式裸电芯和Pocket进行控制。
注意卷绕工艺的膜片错位和膜片脱膜掉碳的控制检查。
电阻坏品防止任何电阻坏品都有发生腐蚀的潜在可能性,对电阻坏品规格的定义是经验上的总结,被Reject 的电芯需要进行On-hold(待潜在的腐蚀发生),不能正常出货,增加了成本控制和影响到产品的总体优率。
我们知道PP破损导致包装铝箔铝层发生裸露才会导致阳极通过电解液与其发生短路。
提高电阻优率可降低发生潜在腐蚀的可能性,也能极大地节约成本(ATL目前日产量近300K),因此必须控制电芯在Top sealing、Side sealing和Degassing三个工艺控制PP的意外受损,也可能需要从设计上进行改善。
目前使用的包装铝箔主要有两种:PFR-001-05和PFR-002-05,两种厚度不同的包装铝箔是因为PP厚度的不同,PFR-001-05 PP的厚度为40um,PFR-005-05的PP厚度为80um,PP越薄越容易发生破损产生电阻坏品,所以普遍来说使用薄Showa的Model电阻优率一般比厚Showa的要低些。
PP破损的原因主要归结以下几个方面(包括控制检查方法):1.温度过高,封装温度过高,封边Pocket内PP受热辐射影响易被烫伤,产生鼓泡,折边后发生破损。
目前对机器温度采用首件测量和On-line monitor的方式进行控制。
2.PP变形率过大,用错Stopper高度的封头或封头磨损、杂质等原因导致封装PP受过度挤压,变形率过大,PP胶堆积在电芯封边内部折边易发生破损。
目前采用平行度检查、监控的方式保证封头处于良好状态。
3.封头错位,封头沿宽度方向错位,封装热压时未重合部位直接烫伤PP。
目前定期检查封头错位情况。
4.隔离膜划伤,主要表现在P1 Model,该种工艺为叠片方式,隔离膜裸露在电芯两侧,热压封边周围PP受热辐射影响比较软,隔离膜伸到PP将其划伤,由以CD隔离膜和大电芯最最为严重,CD隔离膜萃取后变硬,大电芯Pocket中间部位易发生形变。
目前一些Model采用在裸电芯两侧贴短条或长条绿较(根据电芯实际情况和电解液渗透)阻止隔离膜外伸,灵活调整Bi-cell折叠方式,隔离膜比较长的一端放入深坑内,同时控制侧封的未封区宽度,避免隔离膜在封装过程中划伤pocket PP层。
5. 绿胶划伤,为防止P1Model隔离膜两侧外露划伤PP,在Bi-cell两端加贴了绿胶,但经常发生由于绿胶的松动而引起绿胶被封装在封边区域或绿胶边缘划伤PP,因此在贴绿胶工序必须贴紧绿胶,同时灵活地变更方式,绿胶端缘(收尾)不能在Bi-cell侧面,尽量上到电芯实体上。
6. Bi-cell错位,对于叠片工艺的P1Model。
Bi-cell一旦发生错位,不仅隔离膜可能损伤PP。
甚至集流体会严重地划破PP,因此必须在叠片工序控制Bi-cell的错位情况,尽量使用夹具限位。
7.未封区过小,不考虑切边后实际封装宽度的情况下,未封区(封装区域到电芯主体的距离)越大,PP受隔离膜、绿胶等损伤的机率越小。
根据切边宽度和有效封装宽度,将P1Model未封区宽度定义在1.0mm比较合适。
虽然M6S工艺和P2工艺的电芯两侧没有隔离膜外露,但也应有适当的未封区域,否侧会受到电芯实体的挤压而造成PP拉伸变薄,电阻会明显降低。
8.电解液影响,电解液是作为导体连接阳极和铝层造成电阻坏品,电解液越少,造成电阻坏品的机率和比例也会越低,电解液越多,电阻坏品也会相应的增加,曾经M6S 383450和P1 451730 等曾经出现过。
所以需要对各Model电解液的使用系数进行优化。
目前所用的系数不是最优化的条件,由以M6S Model最为严重。
9.Forming折烫边的影响,在Forming工序共有两种折边方式:单折和双折,电芯厚度比较薄一般低于3.2mm,为保证折边不超厚和有效封装宽度,一般采用双折边方式,其余情况下单折就可以满足正常要求。
单折边机器有切、折、烫功能,必须调整好机器加热块的距离,不可过度挤压电芯实体,以免造成封边部位PP的破损,需要对距离进行优化调节;采用双折边工艺的电芯采用的都是薄的包装铝箔,PP厚度只有40um,更加容易破损,所以必须优化调节好滚论的间隙和高度,防止实体封边受到过度挤压造成电阻坏品,对于双折边由于调节不宕,这种情况经常出现并且电阻优率非常低。
产生电阻坏品必是由于某处PP受损导致铝层裸露,众多原因可以归结为两种情况,一是PP被划伤,一是封边内堆积PP发生断裂破损。
两种情况可参考下面图片:这里介绍一种检查PP绝缘不良部位即破损部位的方法,采用电镀的方法。
具体操作方法为:①成型品或做成袋子形状,里面灌入硫酸铜20%水的液体;②6V的电源,阳极放入液体中,阴极与包装膜的铝层接触;③通电20分钟-60分钟;④根据铜的表面析出,可找到绝缘不良处。