氮化铝陶瓷基板覆铜实验方案
氧化铝陶瓷基板化学镀铜工艺优化

氧化铝陶瓷基板化学镀铜工艺优化发表时间:2018-11-08T15:45:19.937Z 来源:《建筑学研究前沿》2018年第19期作者:王平进[导读] 采用96%的氧化铝陶瓷基板,经500#和800#金相砂纸打磨以除去油污及杂质。
浙江新纳陶瓷新材有限公司浙江东阳 322118 摘要:随着微电子技术的迅猛发展,电子器件趋于集成化和多功能化,印刷电路板(也称电子基板)已成为一种不可或缺的电子部件。
陶瓷基板以其优良的导热性和气密性,广泛应用于功率电子、电子封装、混合微电子和多芯片模块等领域。
目前最常用的陶瓷基板材料是氧化铝,其具有与半导体硅相匹配的热膨胀系数、高热稳定性、化学稳定性和低介电常数,且价格便宜。
关键词:化学镀铜;氧化铝;陶瓷基板;沉积速度;微结构;导电性1实验氧化铝陶瓷基板上化学镀铜过程主要有以下步骤。
基板打磨:采用96%的氧化铝陶瓷基板,经500#和800#金相砂纸打磨以除去油污及杂质,并使表面获得一定的粗糙度,而后分别用水、丙酮、乙醇超声波清洗。
清洗:将基板放入浓度为1.25mol/L的氢氧化钠溶液中经50℃水浴加热10min,后用蒸馏水清洗。
粗化:将基板放入100mL/L浓H2SO4与1.8mol/LCrO3的溶液中经50℃水浴加热90min,后用蒸馏水超声清洗。
敏化:将基板放入由0.1mol/LSnCl2、100mL/LHCl和金属锡粒配成的溶液中,常温下敏化10min,后用蒸馏水超声清洗。
活化:配制0.06mol/L的AgNO3溶液,采用氨水滴定至澄清,将敏化后的基板放入常温下活化3~5min,后用蒸馏水超声清洗。
采用四种不同配比(分别以a、b、c、d表示)的镀液对氧化铝陶瓷基板进行化学镀铜,化学镀铜液配比见表1。
在50℃恒温水浴条件下,pH值为12.7,将氧化铝陶瓷基板放入化学镀铜液中,利用搅拌器鼓入空气施镀1h。
采用X射线衍射仪(丹东方圆,DX2700,Cu靶,工作电压35kV,工作电流20mA,扫描速度0.03(°)/min)对镀铜后的氧化铝陶瓷基板物相进行分析。
氮化铝陶瓷基板金属化及其应用

202010220微电子材料表面和散热基板之间存在极细微的凹凸不平的空隙,其在直接安装应用的时候空隙中均为空气,而空气的导热系数很小,会显著降低散热效果。
根据实践发现,电子元器件的温度每升高2℃,其可靠性和稳定性下降约10%,要想保证电子元器件的可靠正常运行,改善其散热环境至关重要。
目前市场上量产的氮化铝热导率普遍在170W/(m ·k )以上,比氧化铝高4~7倍。
再加上氮化铝优良的导热性、可靠的电绝缘性、较低的介电常数与介电损耗、无毒且与硅相匹配的热膨胀系数被认为是第三代半导体导热基板和电子封装的理想材料。
1氮化铝陶瓷的性质氮化铝陶瓷是相对完美的封装用电子材料,表1为氮化铝的性质。
表1氮化铝的性质2氮化铝陶瓷基板金属化的方法2.1薄膜法薄膜法一般是指用真空蒸镀、磁控溅射、离子镀等真空镀的手段在氮化铝陶瓷基板表面附着一层较薄的金属层。
用薄膜法制备的金属化基板一般为多层金属基板,目前市场上常见的基板以Ti 系统浆料为主,然后再在Ti 层上沉积Ag 、Ni 、Cu 等。
必要的时候,还可以通过电镀或化学镀的方法增加金属层的厚度,一般是通过以下步骤实现的。
(1)清洗氮化铝陶瓷板表面,在氮化铝陶瓷板表面镀上设定厚度的钛导电层。
(2)将表面镀钛的氮化铝陶瓷板作为阴极,并置于盛有酸性硫酸铜镀液的电解槽中,精铜为阳极,控制阴极电流密度和电镀时间获得相应厚度的铜镀层。
(3)将表面先后镀覆了钛导电层和铜镀层的氮化铝陶瓷板置于充满氩气的热处理炉中加热,当温度达到300~400℃时,保温25~30min ,钛导电层向氮化铝渗透形成过渡层。
(4)继续加热,当温度达到600~700℃时,保温10~15min ,并持续施加超声波使液态的单质铝振动流出,稳固TiN 冶金过渡层。
(4)进一步加热升温到800~900℃,并保温30~60min ,钛导电层向铜镀层渗透形成TiCu 冶金过渡层。
薄膜法制备的金属化基板线路精度高,适合对电路精度要求较高的电子器件封装。
氮化铝陶瓷基板烧结工艺
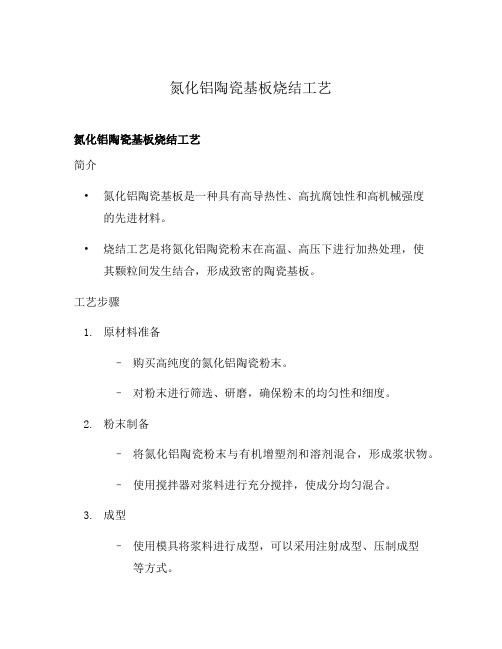
氮化铝陶瓷基板烧结工艺氮化铝陶瓷基板烧结工艺简介•氮化铝陶瓷基板是一种具有高导热性、高抗腐蚀性和高机械强度的先进材料。
•烧结工艺是将氮化铝陶瓷粉末在高温、高压下进行加热处理,使其颗粒间发生结合,形成致密的陶瓷基板。
工艺步骤1.原材料准备–购买高纯度的氮化铝陶瓷粉末。
–对粉末进行筛选、研磨,确保粉末的均匀性和细度。
2.粉末制备–将氮化铝陶瓷粉末与有机增塑剂和溶剂混合,形成浆状物。
–使用搅拌器对浆料进行充分搅拌,使成分均匀混合。
3.成型–使用模具将浆料进行成型,可以采用注射成型、压制成型等方式。
–根据需要,决定陶瓷基板的形状和尺寸。
4.干燥–将成型后的陶瓷基板进行自然干燥或采用烘干设备进行加热干燥。
–控制干燥温度和时间,确保基板内部水分蒸发完全。
5.烧结–将干燥后的陶瓷基板置于烧结设备中。
–升温至高温区,保持一段时间,使粉末颗粒间发生结合反应。
–快速冷却,降温至室温。
6.加工与测试–对烧结后的陶瓷基板进行加工,如打磨、光面处理等,以获得所需的平滑度和尺寸精度。
–对烧结基板进行物理和化学测试,如导热系数、抗腐蚀性、机械强度等,保证产品质量。
工艺优势•高导热性:氮化铝陶瓷基板具有较高的热导率,能够有效传导热量。
•高机械强度:经过烧结工艺处理后的陶瓷基板具有良好的机械性能,能够承受较大压力和冲击。
•高抗腐蚀性:氮化铝陶瓷基板具有优异的耐腐蚀性,能够在恶劣环境下长期稳定运行。
•尺寸精度高:采用烧结工艺进行制作,能够实现精确的尺寸控制和表面处理。
应用领域•电子行业:用于高功率LED封装、半导体器件散热等。
•光电子行业:作为光学元件载体和激光器散热基板。
•汽车工业:用于发动机散热系统和车载电子设备散热。
结论氮化铝陶瓷基板烧结工艺是一种重要的制备方法,可以得到高导热性、高机械强度和优异抗腐蚀性的陶瓷基板。
通过控制工艺步骤和优化工艺参数,可以实现高质量的氮化铝陶瓷基板制备,并在多个领域中得到广泛应用。
氮化铝陶瓷基板烧结工艺(续)工艺参数优化•升温速率:影响烧结过程中粉末颗粒的结合和表面形貌的形成。
氮化铝陶瓷基板生产制作流程和加工制造工艺

氮化铝陶瓷基板生产制作流程和加工制造工艺氮化铝陶瓷基板相对于氧化铝套基板而氧,机械强度和硬度增加,相应的导热率比氧化铝陶瓷基板更高。
氮化铝陶瓷基板生产制作难度增加,加工工艺也有所不同。
今天小编主要是讲述一下氮化铝陶瓷基板生产制作流程和加工制造工艺。
一,氮化铝陶瓷基板生产制作流程1,氮化铝陶瓷基板生产制作过程氮化铝陶瓷基板生产制作流程,大致和陶瓷基板的制作流程接近,需要做烧结工艺,厚膜工艺,薄膜工艺因此具的制作流程和细节有所不同。
氮化铝陶瓷基板制作流程详见文章“关于氧化铝陶瓷基板这个八个方面你知道几个?”2,氮化铝陶瓷基板研磨氮化铝陶瓷电路板的制作流程是非常复杂的,第一步就是氮化铝陶瓷电路板的表面处理,也叫作研磨,其作用是去除其表面的附着物以及平整度的改善。
众所周知,氮化铝陶瓷基板会比氧化铝陶瓷电路板的硬度高很多,遇到比较薄的板厚要求的时候,研磨就是一个非常难得事情了,要保证氮化铝陶瓷电路板不会碎裂,还要达到尺寸精度和表面粗糙度的要求,需要专业的人操作。
不同的研磨方式对氮化铝陶瓷电路板的平整度、生产率、成品率的影响都是很大的,而且后续的工序是没办法提高基材的几何形状的精度。
所以氮化铝陶瓷电路板的制作选用的都是离散磨料双面研磨,对于生产企业来讲整个工序的成本会提升很多,但是为了使客户得到比较完美的氮化铝陶瓷电路板。
另外研磨液是一种溶于水的研磨剂,能够很好的做到去油污,防锈,清洁和增光效果,所以可以让氮化铝陶瓷电路板超过原本的光泽。
然而如今国内市场上的一些氮化铝陶瓷电路板仍旧不够完美,例如产品的流痕问题,是困扰氮化铝陶瓷电路板加工行业的难题。
主要还是没有办法达到比较好的成本控制和生产工艺。
3,氮化铝陶瓷基板切割打孔金瑞欣特种电路采用是激光切割打孔,采用激光切割打孔的优点:●采用皮秒或者飞秒激光器,超短脉冲加工无热传导,适于任意有机&无机材料的高速切割与钻孔,小10μm的崩边和热影响区。
●采用单激光器双光路分光技术,双激光头加工,效率提升一倍。
AlN 陶瓷表面快速制备铜覆层激光熔覆温度场的模拟及工艺 参数对温度场的影响
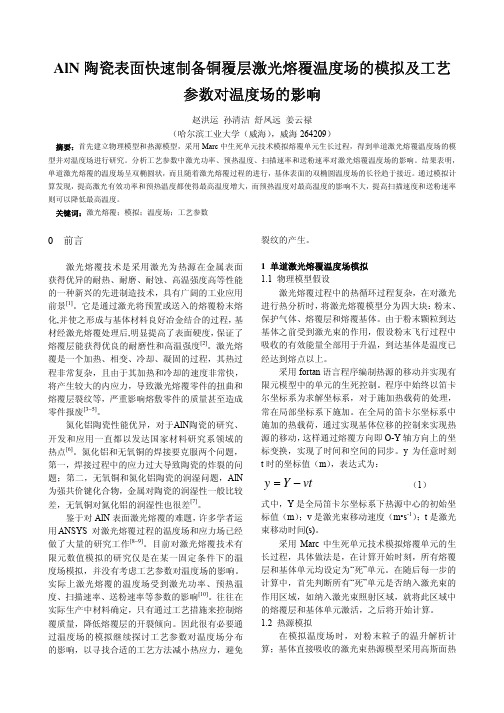
AlN陶瓷表面快速制备铜覆层激光熔覆温度场的模拟及工艺参数对温度场的影响赵洪运孙清洁舒凤远姜云禄(哈尔滨工业大学(威海),威海264209)摘要:首先建立物理模型和热源模型,采用Marc中生死单元技术模拟熔覆单元生长过程,得到单道激光熔覆温度场的模型并对温度场进行研究。
分析工艺参数中激光功率、预热温度、扫描速率和送粉速率对激光熔覆温度场的影响。
结果表明,单道激光熔覆的温度场呈双椭圆状,而且随着激光熔覆过程的进行,基体表面的双椭圆温度场的长径趋于接近。
通过模拟计算发现,提高激光有效功率和预热温度都使得最高温度增大,而预热温度对最高温度的影响不大,提高扫描速度和送粉速率则可以降低最高温度。
关键词:激光熔覆;模拟;温度场;工艺参数0 前言激光熔覆技术是采用激光为热源在金属表面获得优异的耐热、耐磨、耐蚀、高温强度高等性能的一种新兴的先进制造技术,具有广阔的工业应用前景[1]。
它是通过激光将预置或送入的熔覆粉末熔化,并使之形成与基体材料良好冶金结合的过程,基材经激光熔覆处理后,明显提高了表面硬度,保证了熔覆层能获得优良的耐磨性和高温强度[2]。
激光熔覆是一个加热、相变、冷却、凝固的过程,其热过程非常复杂,且由于其加热和冷却的速度非常快,将产生较大的内应力,导致激光熔覆零件的扭曲和熔覆层裂纹等,严重影响熔敷零件的质量甚至造成零件报废[3~5]。
氮化铝陶瓷性能优异,对于AlN陶瓷的研究、开发和应用一直都以发达国家材料研究系领域的热点[6]。
氮化铝和无氧铜的焊接要克服两个问题,第一,焊接过程中的应力过大导致陶瓷的炸裂的问题;第二,无氧铜和氮化铝陶瓷的润湿问题,AlN 为强共价键化合物,金属对陶瓷的润湿性一般比较差,无氧铜对氮化铝的润湿性也很差[7]。
鉴于对AlN表面激光熔覆的难题,许多学者运用ANSYS 对激光熔覆过程的温度场和应力场已经做了大量的研究工作[8~9]。
目前对激光熔覆技术有限元数值模拟的研究仅是在某一固定条件下的温度场模拟,并没有考虑工艺参数对温度场的影响。
陶瓷基覆铜板性能要求与标准

陶瓷基覆铜板性能要求与标准从前面论述可以看出,陶瓷基覆铜板是根据电力电子模块电路的要求进行了不同的功能设计,从而形成了许多品种和规格的系列产品。
这里主要介绍以Al2O3陶瓷-Cu板(100~600μm)进行直接键合的陶瓷基覆铜板,因为此种规格是目前生产规模最大,应用范围最广,应用效果最好的一种产品。
一、Al2O3-----DBC的制作Al2O3-DBC就是指采用Al2O3陶瓷片与铜板在高温和惰性气体中直接键合而成的陶瓷基覆铜板。
其制作流程为:这里所使用的Al2O3瓷片一般是指Al2O3含量96%,适用于薄膜电路或厚膜电路的电子陶瓷片经特殊加工处理而成。
二、Al2O3-DBC的制作的键合机理在高温下含氧量一定的气氛中,金属铜表面氧化形成一薄层Cu2O,温度高于低共熔点时,出现Cu-Cu2O 共晶液相,其中的Cu2O相与Al2O3陶瓷有着良好的亲和性,使界面能降低,共晶液相能很好地润湿铜和陶瓷。
同时液相中的Cu2O与Al2O3发生化学反应,形成CuAlO2:冷却后通过Cu-Al-O化学键,Cu2O与Al2O3陶瓷牢固键合在一起。
在Cu2O与金属接触的另一端,以Cu-O离子键将Cu2O与铜层紧密联接起来,但是这一层的键合力与Cu2O/Al2O3反应键合相比要小一些。
从拉脱试验中可以看出,当铜层拉离了瓷体,在陶瓷上留下粉红色岛状的Cu2O晶粒。
三、Al2O3-DBC覆铜板的性能要求1 铜导带和Al2O3陶瓷基片在高温适合的气氛中直接键合,具有较高的导热性。
热导率为:14~28W/m.K.2 DBC的热膨胀系数同于Al2O3基片(7.4x10-6/℃),与Si相近并和Si芯片相匹配,可以把大型Si芯片直接搭乘在铜导体电路上,省去了传统模块中用钼片等过渡层。
3 由于DBC制作主要以化学键合为主,所以键合强度十分高,拉脱强度大于50N/mm2,剥离强度大于9N/mm。
4 基板耐可焊接性好,使用温度高。
传统PCB一般在260℃ 60s左右,DBC成型温度在1000℃左右,在260℃可以多次焊接,-55~+88范围内长期使用具有优异的热可靠性。
氮化铝陶瓷及其表面金属化研究
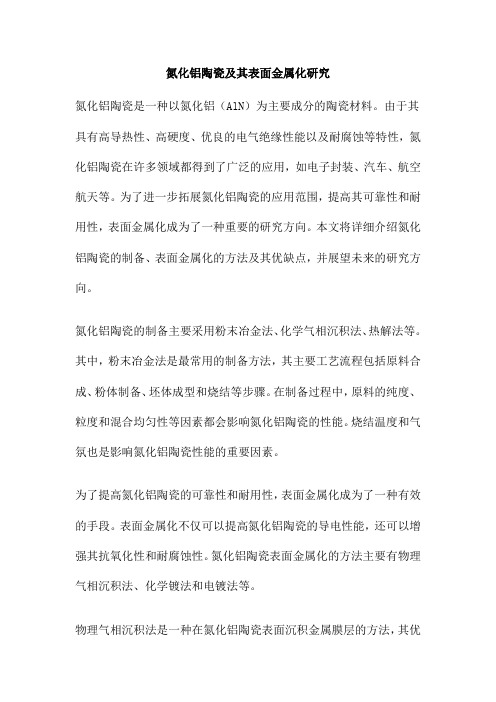
氮化铝陶瓷及其表面金属化研究氮化铝陶瓷是一种以氮化铝(AlN)为主要成分的陶瓷材料。
由于其具有高导热性、高硬度、优良的电气绝缘性能以及耐腐蚀等特性,氮化铝陶瓷在许多领域都得到了广泛的应用,如电子封装、汽车、航空航天等。
为了进一步拓展氮化铝陶瓷的应用范围,提高其可靠性和耐用性,表面金属化成为了一种重要的研究方向。
本文将详细介绍氮化铝陶瓷的制备、表面金属化的方法及其优缺点,并展望未来的研究方向。
氮化铝陶瓷的制备主要采用粉末冶金法、化学气相沉积法、热解法等。
其中,粉末冶金法是最常用的制备方法,其主要工艺流程包括原料合成、粉体制备、坯体成型和烧结等步骤。
在制备过程中,原料的纯度、粒度和混合均匀性等因素都会影响氮化铝陶瓷的性能。
烧结温度和气氛也是影响氮化铝陶瓷性能的重要因素。
为了提高氮化铝陶瓷的可靠性和耐用性,表面金属化成为了一种有效的手段。
表面金属化不仅可以提高氮化铝陶瓷的导电性能,还可以增强其抗氧化性和耐腐蚀性。
氮化铝陶瓷表面金属化的方法主要有物理气相沉积法、化学镀法和电镀法等。
物理气相沉积法是一种在氮化铝陶瓷表面沉积金属膜层的方法,其优点是附着力强、膜层致密,但生产效率较低。
化学镀和电镀法可以在氮化铝陶瓷表面沉积金属层,但需要对表面进行处理,以增加附着力。
在表面金属化过程中,金属种类、工艺参数和表面处理方式都会影响金属化层的性能。
通过对不同制备方法和表面金属化工艺的实验研究,我们发现,采用高纯度原料、优化烧结工艺和选择合适的表面金属是提高氮化铝陶瓷性能的关键。
在表面金属化方面,采用物理气相沉积法可以获得附着力强、致密的金属层,但生产效率较低;而化学镀和电镀法则具有较高的生产效率和较低的成本。
然而,这些方法都需要对表面进行处理,以增加附着力。
尽管氮化铝陶瓷及其表面金属化已经取得了显著的进展,但仍存在一些不足之处,如制备成本较高、金属层的导电性能和附着力有待进一步提高。
因此,未来的研究方向应包括:探索新型的制备方法和表面金属化工艺,以降低成本和提高性能;研究原料的优化配比和烧结气氛,以实现氮化铝陶瓷性能的进一步提高;开展表面金属化的改性研究,以增加金属层的导电性能和附着力;拓展氮化铝陶瓷及其表面金属化的应用领域,如新能源汽车、智能制造等领域。
氮化铝覆铜基板介电常数和热膨胀系数

氮化铝覆铜基板介电常数和热膨胀系数简介本文档将介绍氮化铝覆铜基板的介电常数和热膨胀系数,分析其在电子行业中的重要性以及相关应用。
1.氮化铝覆铜基板概述氮化铝覆铜基板是一种常用于电子器件制造的材料。
它由两个主要部分构成:铜基板和氮化铝薄膜。
铜基板提供了良好的导电性,而氮化铝薄膜具有良好的热传导性和绝缘性能。
2.氮化铝覆铜基板的介电常数介电常数是用来描述材料在电场中对电荷的响应能力的物理量。
氮化铝覆铜基板的介电常数是指材料在电场作用下的相对电容率。
氮化铝覆铜基板具有较低的介电常数,这使得它在高频率电子器件中具有重要的应用价值。
较低的介电常数能减小信号的传输损耗,提高信号的传输速度和质量。
3.氮化铝覆铜基板的热膨胀系数热膨胀系数是描述材料在温度变化下体积变化程度的物理量。
氮化铝覆铜基板的热膨胀系数较低,这意味着在温度变化时,其尺寸变化较小。
低热膨胀系数使得氮化铝覆铜基板在电子器件中能够更好地抵抗温度变化带来的应力和形变问题,提高电子器件的稳定性和可靠性。
4.氮化铝覆铜基板的应用氮化铝覆铜基板由于其优异的性能,在电子行业中有广泛的应用。
以下是一些典型的应用领域:4.1高频电路氮化铝覆铜基板的低介电常数能够减小信号的传输损耗,使其成为制造高频电路的理想材料。
高频电路通常要求信号传输速度快、质量高,氮化铝覆铜基板能够满足这些要求。
4.2微波射频器件氮化铝覆铜基板的低热膨胀系数使其在微波射频器件中广泛应用。
微波射频器件通常工作在高温和高频率环境中,氮化铝覆铜基板的优异性能使其能够稳定工作并抵抗温度变化引起的形变问题。
4.3L E D封装氮化铝覆铜基板的良好的热导性和绝缘性能使其成为L ED封装中常用的基板材料。
L ED封装要求基板能够有效散热,并提供良好的电绝缘性能,以保证L ED的稳定性和寿命。
4.4固态功率放大器氮化铝覆铜基板具有较高的热传导性能,适用于制造固态功率放大器。
固态功率放大器通常需要有效散热以保持正常工作温度,氮化铝覆铜基板能够提供良好的热管理解决方案。
- 1、下载文档前请自行甄别文档内容的完整性,平台不提供额外的编辑、内容补充、找答案等附加服务。
- 2、"仅部分预览"的文档,不可在线预览部分如存在完整性等问题,可反馈申请退款(可完整预览的文档不适用该条件!)。
- 3、如文档侵犯您的权益,请联系客服反馈,我们会尽快为您处理(人工客服工作时间:9:00-18:30)。
【2】氮化铝陶瓷直接覆铜技术
【3】铜-氮化铝陶瓷键合机理探究
【4】一种陶瓷覆铜技术(专利局文章)
实验阶段
敷接时将铜箔的氧化表面和陶瓷基板相对于管式炉中自然敷接,敷接气氛为纯氮,流量为50ml/min。,温度控制在1070摄氏度,保温30min。【1】
1.在氮化铝与铜箔结合体上加2kg的铁块【4】。
2.在纯氮气的烧结炉中,加热温度至1065摄氏度中保温45min,氮气流量为40ml/min.【4】
氮化铝陶瓷基板覆铜实验方案
方案
无添加物
有添加物
准备阶段
ALN基板:1.ALN基板在氧化和敷接之前要进行清,酸洗,丙酮和乙醇
2.空气条件下氧化的ALN基板(15*15mm),温度1100摄氏度,2小时【2】
铜箔:1.酸洗2.去离子水3.乙醇清洗4.烘干铜箔选取13*13*0.3MM。铜箔在敷接前采用高温预氧化的方式引入微量的氧(氧化在50ml/min的流动纯氮气下进行,1000摄氏度下保温30分钟)【1】【2】
ALN基板:粗糙表面15*15mm的基板,粗糙度在0.2-0.7之间.,在ALN表面涂抹三氧化二铝把它置于高温炉中,加热到1300摄氏度,30min。【4】
铜箔:13*13mm粗糙表面,粗糙度在0.2-0.7之间,在铜箔表面均匀涂抹氧化亚铜。1.5-2g/平方厘米。使之置于管式炉中,加温至1000摄氏度,30min。在加热过程中在含有0.3%体积的氧气的氮气下进行,氮气的流量控制在50ml/min【4】