提高球团矿抗压强度的生产实践
提高本钢球团厂生球质量的实践_王子鸣
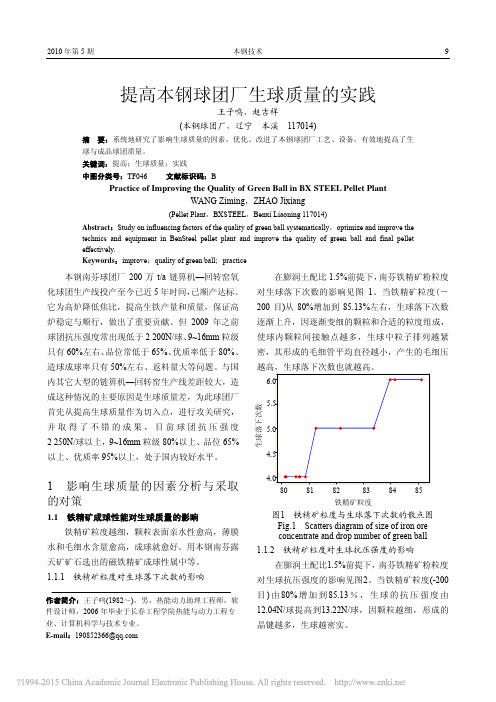
2010年第5期 本钢技术 9提高本钢球团厂生球质量的实践王子鸣,赵吉祥(本钢球团厂,辽宁 本溪 117014)摘 要:系统地研究了影响生球质量的因素,优化、改进了本钢球团厂工艺、设备,有效地提高了生球与成品球团质量。
关键词:提高;生球质量;实践 中图分类号:TF046 文献标识码:BPractice of Improving the Quality of Green Ball in BX STEEL Pellet PlantWANG Ziming ,ZHAO Jixiang(Pellet Plant ,BXSTEEL ,Benxi Liaoning 117014)Abstract :Study on influencing factors of the quality of green ball systematically ,optimize and improve the technics and equipment in BenSteel pellet plant and improve the quality of green ball and final pellet effectively.Keywords :improve ;quality of green ball ;practice本钢南芬球团厂200万t/a 链箅机—回转窑氧化球团生产线投产至今已近5年时间,已顺产达标。
它为高炉降低焦比,提高生铁产量和质量,保证高炉稳定与顺行,做出了重要贡献。
但2009年之前球团抗压强度常出现低于2 200N/球、9~16mm 粒级只有60%左右、品位常低于65%、优质率低于80%、造球成球率只有50%左右、返料量大等问题。
与国内其它大型的链箅机—回转窑生产线差距较大,造成这种情况的主要原因是生球质量差,为此球团厂首先从提高生球质量作为切入点,进行攻关研究,并取得了不错的成果,目前球团抗压强度 2 250N/球以上,9~16mm 粒级80%以上、品位65%以上、优质率95%以上,处于国内较好水平。
球团矿的制备和性能测定

球团矿的制备和性能测定一、国内外球团矿的发展球团矿是一种优良的高炉炼铁原料,我国的铁矿资源本适合生产球团矿,但是由于历史的原因,却走上了细精矿烧结的道路,上世纪80年代中期宝山钢铁公司的1号高炉投产,改变了我国传统的细精矿烧结工艺,其后随着钢铁工业快速的发展,国产精矿不能满足需求,进口粉矿逐年增加,目前就全国范围而言,细精矿在烧结配料中已经不占主导地位。
球团矿在我国高炉炉料中的比例逐年升高,进入21世纪,链篦机一回转窑工艺发展迅速,2007年球团矿的产量可以达到l亿吨左右,加上进口的球团矿大约1.3亿吨,在全国高炉炉料中的比重平均16%左右,在可以预见的将来,烧结矿依然是我国高炉的主要原料,球团矿必将持续发展。
各钢铁厂的情况不同和矿源不同决定了其不同的高炉炉料结构。
日本、韩国高炉以烧结矿为主, 因为其主要铁料是国际上购买的粉矿, 适宜生产烧结矿。
北美高炉以球团矿为主, 因为其矿源多为细精矿, 适宜生产球团矿。
欧盟由于环保要求, 烧结厂的生产和建设受到了严格的限制, 为了进一步改善高炉炼铁指标, 充分发挥球团矿在高炉炼铁中优越的冶金性能, 因而以球团矿为主。
欧美高炉球团矿使用比例一般都较高, 个别的高炉达100 %。
其中一部分高炉使用熔剂型球团矿, 如加拿大Algoma7 号高炉熔剂球团矿比例达99 % , 墨西哥AHMSA 公司Monclova 厂5 号高炉熔剂球团矿比例为93 % , 美国AKSteel 公司Ashland1KY厂Amanda 高炉熔剂球团矿比例为90 %以上; 另一部分高炉以酸性球团矿为主, 配比一般在70 %以上。
欧洲高炉中, 瑞典、英国和德国的部分高炉球团矿的比例很高。
亚洲国家的高炉一般以烧结矿为主, 高达70 %左右。
日本高炉炉料结构的特点是烧结矿比例高且一直比较平稳,而球团矿比例自1979 年以来一直在下降, 块矿比一直在上升。
高炉炉料中高碱度烧结矿比例维持在7113 %~7619 % , 用量一直比较平稳。
蒙库球团矿降硅生产实践

氧化硅的含量。
3. 2 提高膨润土质量生产实践表明, 球团矿膨润土配比每降低1% ,球团矿全铁含量提高0. 6%~0. 7% 。
球团矿生产厂家都把降低膨润土用量作为提高球团矿铁品位的重要技术措施。
膨润土是一种以蒙脱石为主要矿物成分的粘土一号线于2005 年7 月底投产, 二号线于2007 年10 月底投产。
在初期生产阶段由于一号线在设备、操作等多方面的影响因素, 球团矿质量满足不了高炉的需求, 特别是二氧化硅含量居高不下, 给高炉生产顺行带来极大影响。
为改善球团矿质量, 降低二氧化硅的含量, 在生产实践中通过提高铁精矿质量, 优化球团工艺操作, 球团矿质量有了明显改善。
岩, 亦称蒙脱石粘土岩, 主要化学成分是二氧化硅、投产初期生产状况球团厂投产初期, 设备事故较多, 回转窑结圈现象严重, 膨润土配比高达9% , 铁精粉在润磨机中的过磨量达到20%~30% 。
球团矿二氧化硅含量超过8% , 全铁在60% 以下, 球团矿抗压强度低, 粉末含量高, 粉末含量最高时球团矿中小于5mm 含量达到9% 以上, 不能满足炼铁高炉的生产需求。
2 三氧化二铝和水, 还含有铁、镁、钙、钠、钾等元素, N a2O 和 C aO 含量对膨润土的物理化学性质和工艺技术性能影响很大。
目前球团厂现用的膨润土属钙基膨润土。
钠基膨润土比钙基或镁基膨润土的物理化学性质和工艺技术性能更优越。
主要表现在: 吸水率和膨胀倍数大; 阳离子交换量高; 在水介质中分散性好, 胶质价高; 它的胶体悬浮液触变性、粘度、润滑性好, pH 值高; 热稳定性好; 有较高的可塑性和较强的粘结性; 热湿拉强度和干压强度高。
为了改善膨润土的质量,球团厂联合供应商对钙基膨润土进行钠化, 通过钠化, 膨润土性质及使用量得到了优化。
3. 3 生产工艺优化3. 3. 1 提高润磨机磨矿效率, 改善铁精粉表面性质球团厂刚投产时, 由于润磨机未投入使用, 严重影响了生球质量。
提高球团矿性能的试验
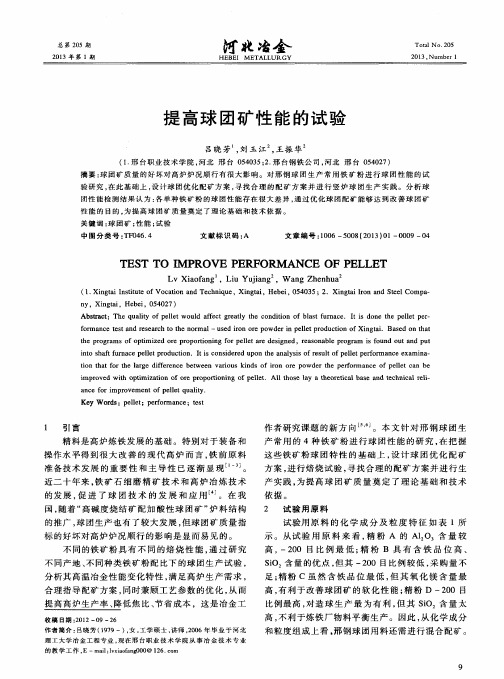
2 0 1 3年 第 1期
河 北 冶全
H EB EI M ETALL U R G Y
To t a l N0 . 2 0 5 2 0 1 3, Nu mb e r 1
提 高球 团矿 性 能 的试 验
吕晓 芳 , 刘 玉 江 , 王 振 华
( 1 . 邢 台职 业 技 术学 院 , 河北 邢台 0 5 4 0 3 5 ; 2 . 邢 台钢 铁 公 司 , 河北 邢台 0 5 4 0 2 7 )
a nc e f o r i m pr o v e me n t of p e l l e t qu a l i t y. Ke y W o r d s:pe l l e t ;pe r f o m a r n c e; t e s t
1
引 言
作 者研 究课 题 的新 方 向 ’ 。本 文 针 对 邢 钢 球 团 生 产 常 用 的 4种 铁 矿 粉进 行 球 团性 能 的研 究 , 在 把握 这 些铁 矿粉 球 团 特性 的基 础 上 , 设 计 球 团 优 化 配 矿 方案 , 进行 焙烧 试验 , 寻 找合 理 的配矿 方案 并进 行 生 产 实践 , 为 提高 球 团矿 质 量 奠 定 了理 论 基 础 和 技 术 依据。 2 试 验 用原 料 试 验用 原 料 的 化 学 成 分 及 粒 度 特 征 如 表 1所 示 。从 试 验 用 原 料 来 看 , 精粉 A的 A 1 o 含 量 较
he t pr o g r a ms o f o pt i mi z e d o r e pr o p or t i o n i n g f or p e l l e t a r e d e s i g ne d,r e a s o na b l e pr o g r a m i s f o un d ou t a nd pu t
哈密球团使用磁海精粉提高球团矿抗压强度的措施

类型 S j 0 2 T i 0 2 A L 2 0 3 C a o
组合样分析结果
M g 0 K 2在预 热 时 间 为 1 2分 钟 时, 当预 热温 度 为 9 5 0  ̄ C时, 预热球 的抗压强度为 6 8 9 N, 而当预热温度 为9 8 0 ℃时 , 预热球的抗压强度上升为 8 0 9 N。 在预 热温度 为9 8 0 ℃的条件下, 当预 热时间 为 1 0 mi n时,预热球 的抗压强度达 到 6 3 5 N。由表 4 . 2可知 :当预热温 度为 9 5 0 ℃,1 2 mi n ,焙烧温度 为 1 2 0 0 ℃, 焙 烧 时 间为 1 2 mi n ,焙 烧 球 的强度 为 2 9 3 2 N。 当预热 温度 为 9 8 0 ℃,1 2 mi n ,焙烧温度为 1 2 0 0 ℃ ,焙烧 时间为 1 2 mi n ,焙烧 球 的强度达到 3 7 0 3 N。但随着焙烧温 度的增大,焙烧球 强度 下
磁 铁 矿 是 矿 石 中最 主 要 铁 矿 物 ,含 量 占 3 0~ 9 0 % ,可 白 成 为一 种 铁 矿 石 。磁 铁 矿 结 晶程 度 以半 自形一 它 形 为 主 , 次 为 自形一半 自形 、它形 。 3 哈密球团厂使用纯磁海矿精粉的抗压情 况
哈密球团厂 自产磁海矿精粉,在生产 过程中遇到抗压强度 不稳定现象 ,持续 2 0天 以上维持在 2 2 0 0 N 以下 ,当用平 时多 种 原料搭配使用 时的窑尾温度 8 5 0 ℃以上 时,球团抗压强度急 剧 下滑 ,只有 1 2 0 0 . 1 3 0 0 N之 间,从单个球 团抗 压来看 ,球 团 内部存在层状 结构 ,可 以判 断出明显 的过烧现象 。
降。
富矿
l 2 . 3 g 0 2 3 2 6 0
提高八钢竖炉球团矿质量的实践

烧 结 球 团
32
Sn el ga d P l t ig i t rn n e l i n ez
第2 7卷 第 3 期 20 0 2年 5月
提 高 八 钢 竖 炉 球 团 矿 质 量 的 实 践
王 强 王永 林
( 疆钢铁公 司炼铁分公 司) 新
度 ,不 得 不配 加 较 多 的膨 润 土 作 为 补偿 ,反 过 来 又 影 响 了球 团矿 的 铁 品 位 ,并增 加 了生 产 成
本。为解 决这一问题 ,我 厂对 原料质量提出了
严格 的 要求 , 在 加 强 对 铁 精 矿 化 学 成 分 检 测 并 的 同 时 ,增 加 了磨 细 度 检 测 项 目,使 精 矿 品 位 由 19 年 的 6 .7 提 高 到 2 0 年 的 99 52% 01
导风墙 通 过 的 同 时 , 尚有 适 量 风 从 墙 外 通 过 , 增 强 了 以低 热值 煤 气 为 燃 料 的竖 炉 内 的 氧 化 性 气 氛 ,充分 利 用 磁 铁 矿 焙 烧 过 程 中 的 氧 化 放
热 ,提高 了焙烧 带 温 度 。而 且 ,适 当 提 高 冷 却
风压 力 ,使其 穿 透 能 力 增 强 ,既 有 利 于 炉 身 下
变更 ,蒙 脱 石 含 量 由 19 99年 6 .3 降 至 O4 %
5 .0 ,但 2 0 60 % 0 1年 又 上 升 到 了 5 .5 7 9 %。其
次 ,是 协 同钢 研 所 在 全 疆 范 围 内取 矿 化 验 ,发
现 了一 批 高质 量 矿 山 ,稳 定 了矿 源 ,为 进 一 步 提 高其 质 量 打下 了基 础 。
进厂 ,同时要求供货厂家提高质量 ,使膨润 土
提高竖炉球团生球质量生产实践
第19卷第1期2009年1月 安徽冶金科技职业学院学报Journal of Anhui V ocational C ollege of Metallurgy and T echnology V ol.19.N o.1Jan.2009提高竖炉球团生球质量生产实践黄龙炎,解珍健(马钢企管部 安徽马鞍山 243000)摘 要:总结了一烧结厂竖炉球团生产以来提高生球质量的生产实践,对影响生球质量的原因进行了分析,对生产异常情况等因素进行了探讨并提出解决对策,针对3#竖炉改造后球团产量的提高,提出了几点有利于造球质量稳定提高的建议。
关键词:造球;质量;提高中图分类号:TF124:TF554 文献标识码:B 文章编号:1672-9994(2009)01-0009-04收稿日期:2008-12-20作者简介:黄龙炎(1974-),男,马钢企管部,工程师。
马钢公司在结构调整阶段,为淘汰落后烧结工艺,利用部分存量资产进行了改造升级。
其中重要的一项举措是把马钢第一烧结厂由烧结生产工艺转产竖炉球团生产工艺。
至2001年开始,一烧结厂经过六年的发展,期间通过增添润磨工艺,多项设备技术改造等措施,现已形成年产240万t 球团矿生产规模。
该厂现有两座10m 2和一座16.2m 2竖炉生产线。
其工艺流程主要包括:风力输送膨润土,计算机全自动配料,烘干混匀,润磨处理,加水造球,生球筛分,干燥,高温焙烧,鼓风冷却,成品球筛分,产品直供2500m 3高炉。
工艺控制采用远程扩展P LC 电控系统,对配料、造球、竖炉焙烧及成品球系统进行逻辑连锁控制。
近几年来,一烧结厂通过“精心设计、精细管理、精确操作”,球团矿产、质量得到了大幅提高,主要经济技术指标已达到全国同类企业先进行列(见表1)。
表1 一烧结厂球团矿生产主要技术经济指标时间产量Π万t利用系数t.m -2.h -1合格率Π%TFe Π%膨润土单耗Πkg Πt10-16mmΠ%200281.21 6.6491.4661.703484.16200390.817.0399.5062.462585.762004142.837.4899.4662.541888.162005182.697.5699.8262.321988.622006202.807.9298.1262.391888.752007214.768.4398.7462.561688.352008220.368.6998.3662.881689.83 从表中可以看出,球团矿质量指标及主要化学成分逐年提高,特别是2008年的变化明显。
利用干燥技术提升含碳烧结球团的强度
利用干燥技术提升含碳烧结球团的强度【摘要】目前很多钢铁原料生产企业,都利用球团烘干,改进原料配比,利用粘结剂等措施来提升含碳烧结球团的强度。
经过大量的实验是数据对比分析,我们发现,钙基含碳球团在烘干温度为180℃,风速1.0 m/s时强度可以达到最佳效果,平均抗压强度为152.1 N,利用此法生产,有效的提升了含碳烧结球团矿的质量。
【关键词】热风烘干;含碳烧结球团;强度提升1 前言利用转底炉直接还原的技术在国内很多钢铁企业已经普遍应用,并且随着生产技术的不断革新,越来越受到更多冶金企业的关注。
这种工艺流程在处理钢铁企业的废弃物方面存在很大的优势,尤其是对含铅类物质的处理,更是有自己的独到之处。
在转底炉生产中含碳球团要经过运输、布料、还原、出料工艺流程,使得各方面性能指标达到最优,要改善含碳球团的强度主要控制好烘干以后环节,避免运输当中出现的破碎等问题,很多时候,烧结球团的强度不高是导致成材率低下的主要原因,所以提升烧结球团的强度是技术革新的关键所在。
2 实验2.1 原料中的粘结剂粘结剂:实验使用粘结剂为钙基含碳球团粘结剂,膨润土,沥青。
其中钙基含碳球团粘结剂主要成份为CaO,膨润土产自安徽省繁昌县,沥青来自某炼焦厂。
2.2 实验装置主要实验装置:Φ1000mm圆盘造球机一台,转速22.2r/min,倾斜角45.2°,YHKC-2型球团强度测定仪一台,自制烘干设备一套,如图1所示。
2.3 实验方法2.3.1 实验原料配比实验采用两种原料配比,见表1配方B是在配方A基础上用成球性较好的转炉泥代替成球性较差的机头灰。
钙基含碳球团粘结剂和膨润土加入量均为1.8%。
将两种不同粘结剂分别加入表2中两种配方的原料中,得到4种不同的造球原料A1,B1,A2,B2(其中A1表示原料配方A加1.8%膨润土,B1表示原料配方B加1.8%膨润土,A2表示原料配方A加1.8%钙基碳球团粘结剂,B2表示原料配方B加1.8%钙基含碳球团粘结剂)。
球团矿的制备及性能测试
实验2 球团矿的制备及性能测试一、球团矿的发展现状与趋势精料和合理的炉料结构一直是国内炼铁界努力探索的课题。
球团矿作为良好的高炉炉料,不仅具有品位高、强度好、易还原、粒度均匀等优点,而且酸性球团矿与高碱度烧结矿搭配,可以构成高炉合理的炉料结构,使得高炉达到增产节焦、提高经济效益的目的,因而近年来国内炼铁球团矿产量和用量大幅增加,不仅中小型高炉普遍使用,大型高炉如马钢2500M3高炉、昆钢2000 M3高炉、宝钢、攀钢等也加大了球团矿的配料比例。
大力发展球团矿已成为有关权威机构、学术会议以及生产厂家关注的焦点和共识,国内目前已形成一股球团矿“热”。
1、球团矿具有规则的形状、均匀的粒度、高的强度(抗压和抗磨),能进一步改善高炉的透气性和炉内煤气的均匀分布;球团矿FeO含量低,有较好的还原性(充分焙烧后,有发达的微孔)更有利于高炉内还原反应的进行。
因此,球团矿在我国高炉操作者的心目中称之为“顺气丸”,其冶金性能好,非其它熟料所能比。
2、国内大量的理论研究和生产实践表明,高碱度烧结矿与酸性炉料搭配有一个合适的配比。
大型高炉采用75% ~70%碱度为1.85左右的烧结矿与25% ~ 30%的酸性球团矿是合理的炉料结构。
当酸性球团配入比例为25% ~ 30%时,其在炉内软熔区间的最大压差值最小,也就是按此比例搭配效果最佳。
3、在上述合适的范围内,在高炉正常运行情况下,球团矿入炉配比的高低是由其质量决定的。
高质量的球团矿应具有的指标为:TFe≥65%; FeO≤1.0%; SiO2≤3.0%; S≤0.04%; 球团矿粒度8—16mm占95%以上;转鼓指数(ISO)≥96%,抗压强度≥2500N/个球。
目前,我国冶金企业生产的球团矿,特别是竖炉球团矿与高质量球团矿及进口球团矿相比,普遍存在着相当的差距。
纵观国内外先进高炉炼铁经验,在原料供应可能的情况下,合理的炉料结构发展趋势是:a)高炉少吃或不吃生料;b)增加高炉球团矿的用量;c)减少烧结矿的用量(即提高烧结矿的品位,应当相应提高烧结矿的碱度,否则烧结矿的强度、冶金性能将会有较大的下降。
提高球团矿产质量的综合技术措施
3 4
M i i g En i e i g n n g ne r n
第 1 O卷 第 4 期 21 0 2年 球 团 矿产 质量 的综 合 技术 措 施
席 玉 明
( 钢矿 业 分公 司峨 口铁矿 ,山西 代县 0 4 0 ) 太 3 2 7
指 标 ,见 表 3 。
是 SO 和 Al ,在球 团焙 烧 过 程 中烧 损 约 1 , iz z O。 0 所 以球 团 中加 入 膨 润 土 会 导 致 球 团 矿 TF e品位 的
下降 ,生 产实 践证 实 ,提 高 1 的 膨 润土 单 耗 ,球
表 3 膨 润 土 指 标
3 11 使 用复合 膨润 土 ,降低 膨润 土单耗 .. 膨 润 土 是 球 团 生 产 的 主 要 非 金 属 添 加 剂 ,在 成
21 0 2年 第 4期
席 玉 明 提 高球 团矿 产 质 量 的 综 合技 术 措 施
3 5
球 过程 中起 黏 结 作 用 ,可 以 提 高生 球 、预 热 球 强
摘 要 :峨 日铁 矿 球 团工 艺 为链 箅 机 一 回转 窑 一 环 冷 机 。通 过 优 化 工 艺 参 数 、 改 进 设 备 性 能 等 综 合 技 术
措 施 ,提 高 了球 团矿 的产 、质 量 。 关 键 词 :链 箅 机 一 回转 窑 一环 冷 机 ;产 、质 量 ;措 施 中 图分 类 号 :TF 0 6 6 4 . 文 献标 识 码 :B 文 章 编 号 :1 7 — 8 5 ( 0 2 4 0 4 0 6 1 5 0 2 1 )0 —0 3 — 4
团矿 TF e品位 下 降 0 6 ~0 6 。 . .5 在 膨 润 土 中添 加 有 机 成 分 ,有 机 成 分 分 子 链
- 1、下载文档前请自行甄别文档内容的完整性,平台不提供额外的编辑、内容补充、找答案等附加服务。
- 2、"仅部分预览"的文档,不可在线预览部分如存在完整性等问题,可反馈申请退款(可完整预览的文档不适用该条件!)。
- 3、如文档侵犯您的权益,请联系客服反馈,我们会尽快为您处理(人工客服工作时间:9:00-18:30)。
1 前言为改善高炉炉料结构和实现精料方针,必须提高高炉炉料中的球团矿配加量。
但球团矿的质量对高炉冶炼有着至关重要的影响。
尤其是近两年公司几座高炉都进行了扩容改造,新扩容的3#高炉已达到460 m3,因此对球团矿的质量要求也越来越高。
球团矿抗压强度是其主要的理化性能指标之一,对高炉冶炼是否顺行有着重要的影响。
国际公认的标准是:在海运和长途运输的情况下,球团矿的抗压强度要大于2 500 N/个;而直接用于高炉炼铁时,可适当低些,一般要求大于2 000 N/个。
另外,为了更好地体现球团矿优越的冶金性能,必须强调球团矿强度的均匀性。
按规定个数所测得的强度,不但其平均值要符合要求,而且所测试样中强度大于2 500 N/个的球所占的百分率要达到一定标准,通常链算机一回转窑工艺生产的成品球团矿应在90%~95%。
因此,必须提高成品球团矿抗压强度和合格率,以满足高炉生产的需要。
2 影响球团矿抗压强度的因素影响球团矿抗压强度的因素主要有原料和生球质量、热工参数和设备结构的制约。
其次,当环冷机内出现红球时,为保护成品输送皮带,被迫在三冷段内部打水进行冷却,也会对球团矿抗压强度造成影响。
3提高球团矿抗压强度的措施3.1提高生球质量指标生球质量指标对球团矿的抗压强度有直接的影响。
在造球工序主要控制生球以下几项指标:落下强度、湿球水分、粒度合格率。
从生产实践中生球水分和生球落下强度对比可知,生球水分和落下强度有一定联系:水分大时,生球落下强度有所上升;但生球水分过大,虽然塑性增强,且落下强度提高,但不利于链箅机过程的干燥及预热等,降低生球的爆裂温度。
实践证明,生球水分过大,势必延长干燥时间,湿球进入链算机干燥段后,由于球内外湿度相差大引起不均匀收缩严重,而使球团产生裂纹,干燥产生的裂纹可导致焙烧球团矿的强度降低67%~80%,。
此外,如果生球水分过大,干燥时间不足,当蒸发面移向内部后,由于内部水分的蒸发而形成的过剩蒸汽压,使生球发生爆裂产生粉末,影响链箅机的透气性且降低成品率。
同时,生球的粒度在很大程度上决定了造球机的生产率和生球落下强度。
粒度小,生产率高;粒度大,造球时间长,生产率低,落下强度就越低。
但粒度太小,抗压强度就变小,从而影响了链箅机的透气性。
因此,合理的生球粒度既是提高生球产量的需要,也是提高生球落下强度的需要。
生球粒度中8~16 mm粒级含量基本上随生球落下强度变化,成品球抗压强度也与生球强度有一定关系,生球强度越好,成品球抗压强度越好。
因此,保证生球质量是得到优质球团矿的前提。
3.1.1生球落下强度和粒度合格率低的原因造成生球落下强度和粒度合格率低的主要原因是:1)我厂球团生产所用精粉供货厂家达22家之多,各厂家精粉质量不一,而精粉料场场地狭窄,分点堆放困难,给配料工序带来了相当的困难,只能随进随吃,造成造球波动。
2)精粉理化性能指标低,粒度较粗,平均粒度一200目仅为57.12%,同时精粉中杂质较多,品位低,FeO含量高。
3)膨润土质量波动较大,进厂膨润土检测结果滞后,经常在造球工序反映出膨润土质量指标的变化。
4)由于产量的提高,原有润磨机能力已不能满足生产要求,新加一条旁通皮带过料,使造球原料粒度较粗,表面活化能降低,造成成球困难,生球落下强度降低。
5)造球盘倾角和转速不能及时调整满足原料结构的变化。
6)造球工的操作技术参差不齐,不能及时准确的判断。
3.1.2采取的主要措施1)优化原料结构,针对精粉厂家多的实际情况,新建一个精粉料场,对精粉进行分点堆放,天车分点抓料,优化配矿。
2)球团原料应具有一定的粒度和合适的粒度组成,适宜的水分,均匀而良好的化学成分,这都是生产球团矿的重要保证。
与烧结不同,球团矿的强度主要来自.Fe2O3的再结晶和固相固结。
因此,用于球团生产的铁精矿品位应尽可能高,而FeO含量则应尽可能低,以降低膨润土用量。
铁精矿要有一定的细度,这是保证造球过程顺利进行的基本条件。
一般情况下,粒度越细,矿粉的比表面积越大,颗粒表面间的分子作用力也越大,有利于成球。
在含有部分微绌颗粒的条件下,颗粒之间排列非常紧密,毛细管作用得到加强,所以,铁精矿中超细粒级(尤其是<10μm粒级)的存在,对造球非常重要。
因此,严把精粉验收质量关,提高精粉质量,为造球服务。
3)增加膨润土取样化验(主要化验吸蓝量、膨胀倍数、2 h吸水率、细度和水分)的次数,做到车车取样,对不合格膨润土拒收,避免由于膨润土质量波动造成生球落下强度降低。
4)加强理论学习,提高磨机工的操作技能和责任心。
同时,优化润磨机介质级配,使之更加趋于合理。
5)根据原料结构的变化,对造球盘倾角和转速做出了适当的调整。
6)通过培训提高造球工的操作技能,同时下发造球岗位工艺操作管理规定,如不符合要求,给予经济考核。
7)配加炼钢红泥。
炼钢红泥一200目粒级在80%,以上,经过充分混匀的红泥,具有良好的粘结性能,同时红泥中含铁在58%以上.有助于提高球团矿品位。
炼钢红泥的化学成分和粒度组成见表1。
从表l可看出,炼钢红泥粒度较细,其中<0.074 mm的比例达到83%,污泥固体物浓度在l 5%~20%时,静置2小时,无明显沉淀;含水35%~50%时,粘性大,脱水困难。
实验室和工业试验表明,炼钢污泥品位高,粒度细,粘性大,能有效地改善生球强度和粒度合格率。
3.1.3湿球水分大的原因造成湿球水分大的主要原因是:1)进厂原料水分大。
由于供货厂家为防止精粉在运输过程中流失,在精粉中喷水,使进厂精粉水分大。
2)随着产量的提高,烘干机能力已呈现不足趋势,不能有效达到造球所需适宜的原料水分要求。
3)造球工对“滴水成球,雾水长大,无水紧密”操作原则认识模糊,片面追求产量,开大水促使生球迅速长大,造成生球水分大。
3.1.4采取的主要措施1)新建一个精粉料场,进行分点堆放,先自然渗水。
2)将烘干机煤气烧嘴中焦炉煤气管道由原来的ø50 mm改为ø100 mm,加大焦炉煤气用量,提高烘干机系统风温。
3)加强造球工操作技能的培训,提高造球工的理论水平和操作水平。
3.2提高链箅机透气性链箅机是一种按逆流原理工作的热交换设备,保证链箅机内生球正常的干燥、预热的条件是箅床上的生球具有良好的透气性。
正常工况下,料层透气性好,料层阻力小,热废气穿透能力强,有利于生球的干燥、预热,提高入窑生球的抗压强度,有利于窑内的氧化焙烧。
3.2.1链箅机内料层透气性差的原因造成链箅机内料层透气性差的原因主要有:1)辊筛工未及时清理辊子上的粘料,使生球筛分效果变差,造成部分粉子进入链算机内。
2)链箅机工布料作业不规范,料层过厚,拦板刮料,料面不均匀,一影响生球干燥。
3)生球质量波动影响链算机热工参数的控制,造成干燥、预热过程中部分生球的破裂。
4)中控工对链箅机系统温度调整不适宜,造成生球破裂。
3.2.2采取的措施1)要求辊筛工每半小时清理一次辊筛粘料,保证筛分效果。
2)布料操作要求均匀平整,料层厚度控制在180~190 mm。
遇到溜料板粘料时,须及时清理,避免布料出现拉沟现象。
3)加强与造球岗位的联系,同时在造球岗位设立湿球质量记录台,发现生球质量变差,大块、粉子增多时要及时提醒造球工并通知中控室。
4)根据我们平时的观察,链箅机3#烟罩温度低于850℃,3#风箱温度低于350℃时,生球干燥变差,因此将3#烟罩温度确定在850℃以上,3#风箱温度确定在400℃以上。
3.3提高窑内氧化气氛,控制加温速度,改善焙烧效果Fe203再结晶连接是磁铁矿氧化球团同结的主要形式。
当磁铁矿球团在氧化气氛中焙烧时,氧化过程由球的表面沿同心球面向内推进,氧化温度达l 000℃时,约95%的磁铁矿氧化成新生的Fe203,并形成微晶键。
在最佳焙烧制度下,一方面残存的磁铁矿继续氧化,另一方面赤铁矿晶粒扩散增强,并产生再结晶和聚晶长大,颗粒之间的孔隙变圆,孔隙率下降,球体积收缩,球内各颗粒连接成一个致密的整体,因而使球的强度大大提高。
若在中性气氛或还原性气氛中焙烧时,Fe3O4再结晶速度慢,再结晶不完全,主要依靠形成硅酸盐(FeO一SiO2)、钙铁硅酸盐、铁酸钙等来固结,造成球团矿的抗压强度降低。
同时,球团的加温速度对其成品抗压强度有重要的影响。
3.3.1窑内氧化气氛不足的原因造成窑内氧化气氛不足的原因主要有:1)对氧化焙烧的认识不深刻,不能严格执行热工工艺制度和一次风、高炉煤气、焦炉煤气比例。
2)在调节链算机、回转窑温度时的方法不当,破坏炉内的氧化气氛。
3)高炉煤气、焦炉煤气压力、发热值波动,无法控制。
4)看火工忽视回热风对窑内氧化气氛的保证作用。
3.3.2采取的主要措施1)加强理论学习,提高职工的操作技能,同时,让看火工进主控室操作,在实际操作中以看火工为主。
在生产过程中出现异常情况,要及时分析原因,制定对策。
2)强调在氧化气氛下操作,看火工要经常观察窑内气氛,尤其在温度调整前后。
3)煤气压力长期低,热量不足,应请示调度后进行减产操作,确保球团矿能够氧化充分。
4)在日常操作中,强调二次风对窑内氧化气氛的补充作用,应该根据产量和温度合理调节。
3.3.3控制加温速度,改善焙烧效果加温速度过快时,外壳收缩严重,使孔隙封闭,一方面妨碍内层氧化,另一方面由于收缩应力的积累引起球表面形成小裂纹。
在焙烧的球团中时常会出现同心裂纹,它是导致球团强度下降的主要原因。
同心裂纹产生在氧化的外壳和未氧化的磁铁矿之间。
氧化发生在已氧化的外壳和未氧化的磁铁矿之问,并沿着同心圆向核心推进,当温度过高时,外壳致密,氧难以扩散进去,内部磁铁矿再结品,渣相熔融收缩离开外壳,是两种不同的物质问形成同心裂纹。
目前,生产中依靠提高链算机预热段温度和窑尾温度来控制加温速度,尽量减轻形成同心裂纹降低抗压强度.3.4提高环冷机布料厚度和一冷段温度经过焙烧的球团进入环冷机后发生二次氧化和再结晶过程,为保证这一过程,必须提高布料厚度和一冷段温度,生产中布料厚度控制在650~760 mm,一冷段温度控制在950~1 050℃之间。
3.5加强设备管理和技术改造1)加强点巡检管理,减少设备故障停机造成系统温度降低,使球团不能得到充分焙烧和氧化,从而降低球团抗压强度。
2)对窑头筒节长度和环冷机平料砣进行改造,减少红料的出现,避免直接打水造成球团激冷破碎。
4 效果分析通过不断摸索影响球团矿抗压强度的177I素,总结出了提高抗压强度的措施。
球团矿抗压强度变化情况表2。
5 结论1)南于原料和生球质量对球团矿的抗压强度影响较大,为保证生球指标满足生产需要,精粉一200目粒级一般>t60%,生球落下强度控制在5~8次/个,湿球水分≤8.5%,粒度合格率≥80%。
2)链箅机内透气性对球团矿抗压强度有很大的影响,为了保证透气性,链箅机布料平整,厚度(1 60±5)mm。