球团矿生产工艺
球团矿生产原理及工艺
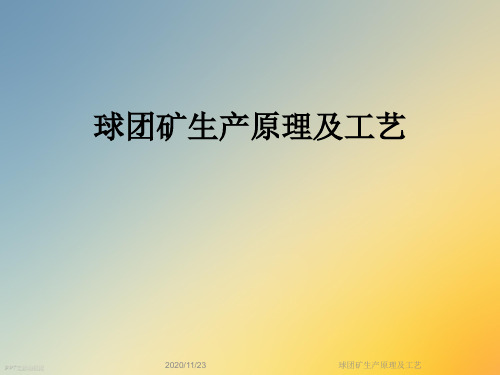
PPT文档演模板
球团矿生产原理及工艺
球团矿生产设备
n 原料准备处理设备
u 干燥机 u 混料机 u 润磨机
n 造球设备
u 圆盘造球机 u 圆筒造球机
n 干燥和焙烧设备
u 竖炉焙烧装置 u 环形焙烧装置 u 带式机焙烧装置 u 链箅机—回转窑焙烧装置
PPT文档演模板
球团矿生产原理及工艺
各种混合机
PPT文档演模板
PPT文档演模板
球团矿生产原理及工艺
SiO2含量与球团膨胀率的关系
PPT文档演模板
球团矿生产原理及工艺
碱度与球团膨胀率的关系
PPT文档演模板
球团矿生产原理及工艺
配加白云石对结圈发生比的影响
PPT文档演模板
球团矿生产原理及工艺
球团质量指标
PPT文档演模板
球团矿生产原理及工艺
各种条件的球矿生产原理及工艺
PPT文档演模板
2020/11/23
球团矿生产原理及工艺
工艺概述
n 概述
u 工艺概述:
球团矿生产是将细粒度的精矿粉在水的作用下,在造球设备中生成 含水7~11%的生球;在干燥预热设备中干燥并预热到900~1000℃; 在1150~1350℃的焙烧装置中进行高温焙烧;在冷却设备中冷却至 100~150℃。产品球团粒度在8~15mm,抗压强度在1500~2500N/ 个球。
分获得粒度8~16mm的生球,合适的落下强度和抗压强度。 F 布料:防止布料过程球的破碎 F 干燥:~400℃附近,防止产生裂纹和爆裂。 F 预热:→900~1100℃保证预热球强度,防止爆裂。 F 焙烧(均热):获得要求的强度 F 冷却:回收热量,方便运输。
PPT文档演模板
球团矿生产原理及工艺
球团矿工艺流程

球团矿生产工艺流程在球团矿的生产流程中,一般包括原料准备、配料、混合、造球、烘干和焙烧、冷却、成品和返矿处理等工序,如下图所示配料:原料配比采用酸性精粉+膨润土,配料按照1.05配比(料重/成品)。
其中包含水份挥发、返粉等烧损。
烘干机:经过配料后精粉通过烘干机脱去精粉矿水份,从而为润磨机进一步提高精粉细度创造条件。
润磨机:精粉经过润磨机钢球研磨,提高精粉细度8-10%(出料粒度要求小于250目的达到70%以上),同时将混合料进行较好的混合,为下一步的造球提供条件。
圆盘造球机:将皂土、红泥、铁精矿粉混合后,输入圆盘造球机上部的混合料仓内,均匀地向造球机布料,同时由水管供给雾状喷淋水,倾斜(倾角一般为40一50°)布置的圆盘造球机,由机械传动旋转,混合料加喷淋水在圆盘内滚动成球,球大小约10-25mm。
干燥和焙烧:在竖炉顶部烘干床(小水梁上的蓖板中部位置)对造好生球进行烘干,以脱去球内水份,使生球达到有效的强度,然后进入焙烧带进行培烧,温度约1100℃左右(一厂热电偶显示在850左右),生成成品球团矿。
冷却成品:成品球团矿在竖炉底部经过高压风机强制通风(高压风冷却热球后变为热空气,然后通过大水梁上的导风墙上升到烘干床对冷球进行烘干),达到球团矿有效冷却,减少对下道工序的烧损。
卸料:齿辊(内通水冷却)卸料到炉下料仓(仓壁装有冷却壁),再通过电磁振动给料机对料车给料,由卷扬卸料给运输车辆到高炉。
导风墙:竖炉炉膛内的导风墙是由耐火材料(盖板砖)构筑成的纵贯竖炉炉膛的中空墙,导风墙内有竖直风道,把与炉膛下部的热矿球进行热交换后的冷却风引导到炉口烘床下面以对生球进行有效烘干。
导风墙由其下部的大水梁进行支撑。
大水梁通水冷却。
水系统:水泵房(造球盘东)供水给造球盘、大小水梁、齿辊卸料器、料仓冷却壁。
小水梁、齿辊卸料器、料仓冷却壁的冷却水经凉水塔后,回水泵房进行循环。
大水梁采用汽水冷却,蒸汽到炉顶汽包,经凝汽器后上凉水塔回水泵房。
球团工艺简介及生产流程图

烧结厂球团工艺简介及生产流程图德晟金属制品有限公司烧结厂建设1座12m2竖炉,利用系数6。
3t/m2•h,年产酸性球团矿60万t。
车间组成及工艺流程1.1车间组成车间组成:配料室、烘干机室、润磨室、造球室、生筛室、转运站、焙烧室、带冷机通廊、成品缓冲仓、风机房、煤气加压站、软水站、高低压配电室等。
1.2工艺流程工艺流程图见付图1.2.1精矿接受与贮存竖炉生产主要原料为磁铁矿精粉,对铁精粉化学成分要求是进厂铁精粉化学成分精矿进料采用汽车输送,汽车将精矿粉卸到下沉式精矿堆场,经抓斗吊运至配料仓。
1.2.2膨润土接受与贮存竖炉对膨润土化学成分要求是:进厂膨润土化学指标袋装膨润土用汽车运入,储存在膨润土库,由库内设的电葫芦将袋装膨润土运至膨润土配料仓平台,由人工抖袋将膨润土卸到膨润土配料仓。
1.2.3配料系统配料矿槽采用单列配置,4个精矿配料仓,容积100m3,储量8.8h,三用一备;2个膨润土仓,膨润土仓为一用一备.配料室为地下结构。
采用自动重量配料,根据设定的给料量和铁精粉与膨润土的配比,自动调节给料量.铁精粉通过仓下2m圆盘给料机和配料皮带秤配料.膨润土通过螺旋给料机和螺旋秤配入皮带.圆盘给料机和螺旋给料机采用变频控制。
并且尽量做到铁精矿与膨润土两料流首尾重合。
在配料室膨润土落料点处和膨润土设抽风除尘,采用布袋除尘器,布袋除尘器采用反吹清灰方式。
设置铁精粉仓库和膨润土库。
铁精粉仓库能容纳约9天的用量,下沉式结构,铁精粉采用抓斗吊上料,设置2台10t抓斗吊。
膨润土库用来堆放袋装膨润土,膨润土设电葫芦环形轨道由电葫芦将袋装膨润土吊运至膨润土配料仓顶平台,人工抖袋卸料至膨润土配料仓。
1.2.4原料干燥系统精矿进厂水分为10。
5%左右,不能满足造球对精矿水分要求,因此设计中采用了干燥工艺,将精矿中水分部分脱除,以保证铁精矿水份满足造球工序的要求。
需干燥的湿精矿粉经配料胶带机运至干燥窑,物料干燥后经胶带机运至造球前料仓。
球团矿生产工艺[技巧]
![球团矿生产工艺[技巧]](https://img.taocdn.com/s3/m/1de1400458eef8c75fbfc77da26925c52cc591ca.png)
球团矿生产工艺1 球团矿生产迅速发展的原因(1)天然富矿日趋减少,大量贫矿被采用①铁矿石经细磨、选矿后的精矿粉,品位易于提高。
②过细精矿粉用于烧结生产会影响透气性,降低产量和质量。
③细磨精矿粉易于造球,粒度越细,成球率越高,球团矿强度也越高。
(2)球团法生产工艺的成熟①从单一处理铁精矿粉扩展到多种含铁原料。
②生产规模和操作也向大型化、机械化、自动化方向发展。
③技术经济指标显著提高。
④球团产品也已用于炼钢和直接还原炼铁等。
(3)球团矿具有良好的冶金性能粒度均匀、微气孔多、还原性好、强度高,有利于强化高炉冶炼。
2 球团矿生产方法及工艺流程目前世界上球团生产应用较为普通的方法有竖炉球团法、带式焙烧机球团法和链篦机-回转窑球团法。
竖炉球团法是最早发展起来的,曾一度发展很快。
但随着钢铁工业的发展,要求球团工艺不仅能处理磁铁矿,而且能处理赤铁矿、褐铁矿及土状赤铁矿等,另外高炉对球团矿的需求量不断增加,要求设备向大型化发展。
因此相继发展了带式焙烧机、链篦机-回转窑、环形焙烧炉等方法。
这些方法一直处于彼此相互竞争状态。
球团法按生产设备形式分,有竖炉焙烧、带式机焙烧、链篦机一回转窑焙烧及隧道窑、平地吹土球等多种。
根据球团的理化性能和焙烧工艺不同,球团成品有氧化球团、还原性球团(金属化球团)以及综合处理的氯化焙烧球团之分。
目前国内生产以氧化球团矿为主。
竖炉及带式机焙烧是生产氧化球团矿的主要方法。
图3-14是典型的我国球团矿生产工艺流程,与国外不同的是在混料后造球前(或配料后混料前)加有烘干设施,这是弥补精矿粉水分高而且不稳定的不足,一般烘干设施是将精矿粉水分控制到比最适宜造球水分低1%~2%。
由于我国精矿粉粒度过粗,比表面积小,所以在新建的球团厂的流程中又加了润磨机,在造球前混合料经润磨机加工,可使精矿粉的比表面积增加10 9/6~15%,有利于造球。
球团生产一般包括原料准备、配料、混合、造球、干燥和焙烧、冷却、成品和返矿处理等工序。
球团矿生产原理和工艺
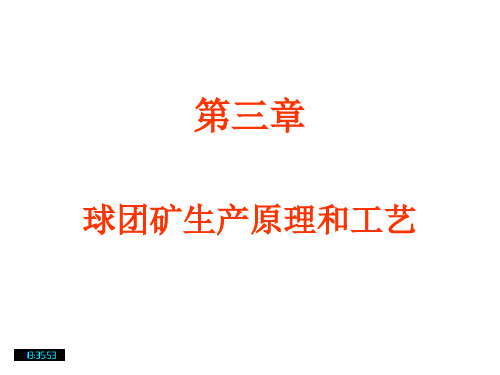
烧结与球团的区别
4)固结成块的机理不同: 烧结矿是靠液相固结的,为了保证烧结矿的强度, 要求产生一定数量的液相,因此混合料中必须有燃 料,为烧结过程提供热源。而球团矿主要是依靠矿 粉颗粒的高温再结晶固结的,不需要产生液相,热 量由焙烧炉内的燃料燃烧提供,混合料中不加燃料。
烧结与球团的区别
5)生产工艺不同: 烧结料的混合与造球是在混合机内同时进行的,成 球不完全,混合料中仍然含有相当数量未成球的小 颗粒。而球团矿生产工艺中必须有专门的造球工序 和设备,将全部混合料造成10~25mm的球,小于 10mm的小球要筛出重新造球。
• 经过一段时间的加热后。生球的内外温度趋于平 衡,此时生球的干燥主要受导湿现象的支配,内部 水分不断向表面迁移,表面水分不断汽化,直到表 面蒸汽压力与介质中的水气分压相等为止,至此干 燥过程结束。
生球的破裂温度
• 生球在干燥过程中随着水分的蒸发体积收缩。因干 燥过程是从表面向内部扩展的,所以内外体积收缩 的程度不同,表面层的体积收缩大于内部,于是表 面层受拉力,与拉力成45°角的方向上又受剪力, 内部则受压力。当生球表面所受拉力和剪应力超过 其抗拉强度和抗剪强度极限时,生球就要破裂。这 种生球的破裂现象,
生球焙烧固结成球团矿的原理
• 当生球中含有CaO,在强氧化性气氛和1300℃以 下焙烧时,CaO可与Fe2O3作用生成CaO·Fe2O3粘 结相。因为这种矿物的还原性和强度都比较好,所 以在渣相固结中它是一种较好的固结形式。
生球焙烧之前必须进行干燥
• 生球焙烧之前必须进行干燥处理,这对提高球团矿 的产量和质量都有十分重要的意义。未经干燥的生 球直接焙烧,在预热和点火时,由于加热过急,水 分蒸发过快,发生生球爆裂现象.一部分球团粉化, 恶化料层透气性,焙烧时间延长,球团质量下降, 废品率增加。所以生球干燥是整个球团矿生产过程 中非常重要的一环。应予充分重视。
球团矿生产工艺流程

球团矿生产工艺流程
《球团矿生产工艺流程》
球团矿生产工艺流程是指将球团矿从原料到成品的生产过程。
球团矿是一种铁矿石的加工产品,经过适当的处理后可用于制造铁制品,如钢铁。
首先,在球团矿的生产过程中,原料的选择非常重要。
通常使用的原料包括铁矿石、焦炭和石灰石。
这些原料经过混合和研磨后,形成了适合球团矿的原料混合物。
接下来,原料混合物被送入球团机进行球团化处理。
球团机会将原料混合物压制成颗粒状的球形颗粒,这些颗粒即为球团矿。
在这个过程中,通常会添加一些粘结剂,以便球团矿颗粒能够保持形状和坚固度。
然后,球团矿颗粒被送入烧结炉进行烧结处理。
在烧结炉中,球团矿颗粒经过高温烧结,使得颗粒间的结合更加牢固,同时去除了一部分水分和杂质。
最后,经过烧结处理的球团矿成为了成品球团,可以被用于制造铁制品。
成品球团通常会被送往高炉进行冶炼,将其中的铁提取出来,再进行进一步的加工。
整个球团矿生产工艺流程中,各个环节的精细操作和控制都至关重要,以确保成品球团的质量和生产效率。
同时,对于球团
矿的生产还需要考虑环保和资源利用的问题,采取合理的措施来实现可持续发展。
球团矿生产工艺流程
球团矿生产工艺流程球团矿是从铁矿石中提取铁的一种工艺流程,它能将铁矿石中的杂质和氧化物去除,使得铁矿石可以更好地被利用。
下面将介绍球团矿的生产工艺流程。
球团矿生产工艺流程主要包括破碎、筛分、湿制粉化、混合、调整湿度、造粒和烧结等几个步骤。
首先是破碎阶段。
铁矿石经过破碎设备破碎成适当的颗粒大小,这样方便后续处理。
接下来是筛分阶段。
通过筛分设备,将破碎后的铁矿石按照不同的粒度进行分离,得到符合要求的颗粒。
然后是湿制粉化阶段。
将分离后的铁矿石与适量的水混合,形成湿制粉。
湿制粉有助于球团矿的制备和后续工艺的进行。
混合阶段是将湿制粉与一定比例的结合剂和其他添加剂混合。
结合剂的作用是使湿制粉形成团聚力较强的颗粒,方便后续处理。
添加剂可以根据需要选择,常用的有石灰石、焦炭粉和石膏等。
为了保证湿制粉的湿度适宜,还需要调整湿度。
一般来说,湿制粉的湿度要保持在8%~12%左右,湿度过高或过低都会影响制球的效果。
接下来是造粒阶段。
将混合后的物料送入球团机,通过旋转和摩擦的作用,将物料制成球状颗粒。
此时,结合剂的作用发挥出来,使得颗粒有较强的粘结力。
最后是烧结阶段。
烧结是将球团矿加热到一定温度,使得颗粒内部发生化学反应,形成硬度和机械强度较高的球团。
通常,烧结温度在1200℃~1350℃之间。
整个球团矿生产工艺流程完成后,得到的球团矿可以作为高品质的铁矿石原料,供给冶金行业使用。
球团矿具有较好的堆与流动性,可以减少炉垫料的空隙,提高高炉产量和炉渣粘附力,是冶金行业不可或缺的重要物料。
总之,球团矿的生产工艺流程包括破碎、筛分、湿制粉化、混合、调整湿度、造粒和烧结等几个步骤。
通过这些步骤,可以将铁矿石中的杂质和氧化物去除,得到高品质的球团矿,提高铁矿石的利用率。
这对推动冶金行业的发展具有重要意义。
竖炉球团工艺流程
竖炉球团工艺流程引言竖炉球团工艺是一种常用于铁矿石烧结的冶金工艺,通过将铁矿石与其他辅助料料进行混合,并在竖直炉中进行还原、烧结等多个工序,最终得到球团矿。
本文将全面介绍竖炉球团工艺的流程及其各个环节。
工艺流程竖炉球团工艺主要分为原料制备、炉内反应、冷却、筛分、热处理等多个阶段。
下面详细介绍每个阶段的流程及其关键步骤。
1. 原料制备•原料准备:铁矿石、焦炭、石灰石等原料按一定的比例混合。
•粉煤喷吹:将适量的粉煤喷吹到混合料中,提高球团的强度。
•湿法制球:将混合料加入湿法制球机中进行制球工艺,使其成为一定粒度的湿球团。
2. 炉内反应•上料:将湿球团通过设备顶部装入竖直炉中。
•还原:在炉内加热过程中,焦炭发生氧化还原反应,将铁矿石中的氧化铁还原为金属铁,并释放出一定量的热量。
•固相反应:矿石中的氧化物与石灰石发生反应,生成熔融化合物,加快球团粒度的增长。
•烧结:炉内温度逐渐升高,湿球团中的水分被蒸发,颗粒逐渐结合形成球团矿。
3. 冷却•冷却:将高温的球团矿通过冷却设备,降低温度,使之逐渐冷却。
4. 筛分•粗筛分:对冷却后的球团矿进行初步筛分,分离出不同粒度的球状颗粒。
•细筛分:对粗筛分得到的球团矿进行细分,得到更加统一的颗粒粒度。
5. 热处理•烘干:将筛分后的球团矿送入烘干设备中,除去其表面的水分。
•煅烧:在高温下对球团矿进行煅烧处理,提高其机械强度和还原性能。
结论竖炉球团工艺流程是一种常用的铁矿石烧结工艺,通过一系列的工艺流程将原料转化为球团矿。
每个阶段的流程都具有其独特的作用,可以通过控制不同阶段的工艺参数来获得优质的球团矿产品。
在实际应用中,还可以根据不同的需求对工艺流程进行调整和改进,以提高球团矿的品质和产量。
本文对竖炉球团工艺的流程及其相关环节进行了全面、详细、完整且深入地探讨,希望对读者了解和应用该工艺有所帮助。
带式焙烧等高效球团矿生产方案(一)
带式焙烧等高效球团矿生产方案一、实施背景随着全球钢铁工业的快速发展,对铁矿石的需求量越来越大。
中国作为全球最大的钢铁生产国,对铁矿石的需求更加迫切。
在环保要求日益提高的背景下,高效、清洁的铁矿石生产工艺成为行业发展的必然趋势。
带式焙烧等高效球团矿生产方案作为一种新型的铁矿石生产工艺,具有提高产量、降低能耗、减少环境污染等优点,因此具有广阔的实施背景。
二、工作原理带式焙烧机是带式焙烧等高效球团矿生产方案的核心设备。
其主要工作原理是将铁精矿、熔剂和燃料混合后,通过高压成球机压制成球团,然后将球团矿输送至带式焙烧机进行焙烧。
在焙烧过程中,球团矿中的矿物发生物理化学变化,如晶格重构、分解、再结晶等,最终形成具有高活性、高密度、高强度的球团矿。
带式焙烧机通常分为干燥段、预热段、焙烧段和冷却段。
在干燥段,球团矿中的水分被蒸发;在预热段,球团矿被加热到焙烧温度;在焙烧段,球团矿中的矿物发生焙烧反应;在冷却段,焙烧后的球团矿被迅速冷却,以避免晶格破裂和过度氧化。
三、实施计划步骤1. 原料准备选择合适的铁精矿、熔剂和燃料,并进行混合。
在混合过程中,需加入适量的水以调节原料的成球性能。
混合后的原料通过高压成球机压制成球团矿,要求球团矿的形状、大小和强度一致。
2. 带式焙烧将球团矿送入带式焙烧机进行焙烧。
焙烧温度和焙烧时间是影响球团矿质量的关键因素。
根据具体工艺条件,需要对焙烧温度和焙烧时间进行精细调节。
3. 冷却和收集焙烧后的球团矿需要进行迅速冷却,以避免晶格破裂和过度氧化。
同时,需要将冷却后的球团矿收集起来,进行后续处理。
四、适用范围带式焙烧等高效球团矿生产方案适用于大型钢铁企业、中型钢铁企业和矿山的铁矿石生产。
该工艺具有高效、节能、环保等优点,因此在国内外得到了广泛应用。
此外,该工艺还可适用于其他具有类似物理化学性质的矿物的焙烧和活化处理,如锰矿、铬矿等。
五、创新要点1. 高压成球技术:通过高压成球机将原料混合物压制成球团矿,可提高球团矿的形状、大小和强度一致性,降低球团矿破损率和提高成球率。
2、球团矿生产工艺
2.2 造球作业
二、混合: 混合作业大都采用圆筒混合机或轮式混 合机的一次混合流程。国外有的厂采用 连续式混磨机。
2.2 造球作业
2.2.2 造球
圆盘造球机工艺 圆盘造球机是目前国 内外广泛使用的造球 设备。
2.2 造球作业
铁矿粉的成球过程
√铁矿粉加水造球过程可分为三个阶段,母球形成, 母球长大,生球密实。这3个阶段是靠加水润湿和机械 滚动作用力来完成的。
常用的添加剂有消石灰、石灰石和白云石等钙镁化合 物。
2.2 造球作业
2.2.1 配料与混合
一、配料 1、配料的目的:获得化学成分和物理性质稳 定,冶金性能符合高炉冶炼要求的球团矿,并 使混合料具有良好的成球性能和生球焙烧性能。 2、配料形式通常为集中配料。集中配料是把 各种原料全部集中到配料室,分别贮存在各种 配料槽内,然后根据配料比进行配料。 3、配料的方法为容量法和质量法,常用的为 质量配比法。也有采用 射线分析仪对混合料作 快速分析,按原料化学成分配料的方法。
烧结与球团的区别
1、矿粉粒度不同 富矿短缺,必须不断 扩大贫矿资源的利用,而选矿技术的进 步可经济地选出高品位细磨铁精矿,其 粒度从-200网目(小于0.074mm)进一 步减少到-325网目(小于0.044mm)。 这种过细精矿不益于烧结,透气性不好, 影响烧结矿产量和质量的提高,而用球 团方法处理却很适宜,因为过细精矿易 于成球,粒度愈细,成球性愈好,球团 强度愈高。
有关工艺流程见图
球团矿生产的工艺流程
2.1 球团原料及准备
2.1.1 含铁原料
一、铁矿石精矿 1、粒度:适合造球的精矿<0.044mm(-325目)
部分应占60%~85%,或<0.074mm(-200目) 部分应占>90%。
- 1、下载文档前请自行甄别文档内容的完整性,平台不提供额外的编辑、内容补充、找答案等附加服务。
- 2、"仅部分预览"的文档,不可在线预览部分如存在完整性等问题,可反馈申请退款(可完整预览的文档不适用该条件!)。
- 3、如文档侵犯您的权益,请联系客服反馈,我们会尽快为您处理(人工客服工作时间:9:00-18:30)。
起完成的,在造球过程中很难截然分开。√第一阶段 具有决定意义的是润湿,第二阶段除了润湿作用以外 ,机械作用也有着重要影响,而在第三阶段,机械作 用成为决定性因素。
造球加水原则:滴水成球;雾水长大;无水密实。
2020/5/26
王瑞祥
2.3 球团焙烧工艺 一、焙烧过程
焙烧设备:竖炉、带式焙烧机、链篦式-回转
窑三种。
焙烧过程分为干燥、预热、焙烧、均热和冷却
五个过程。
⑴干燥:200~600℃,主要反应:蒸发生球水
分。干燥过程中要预防裂纹和爆裂。
⑵预热:900~1000℃,水分蒸发完全。主要
反应:磁铁矿氧化为赤铁矿,碳酸盐分解,硫 化物和氧化分解以及固相反应 。
2020/5/26
2、水分:一般磁铁矿和赤铁矿适宜的水分为
7.5% ~10.5%。
3、化学成分:全铁含量波动<±0.5%,SiO2含
量波动<±0.3%。
2020/5/26
王瑞祥
2.1 球团原料及准备
二、其他含铁原料
包括:黄铁矿烧渣、轧钢皮、转炉炉尘、高炉
炉尘等。
原料进厂后需加工处理,主要有再磨、干燥、中和等
。
球团矿生产工艺流程框图
加水
焙烧设备: ①竖炉; ②链篦机-回转窑; ③带式焙烧机
↓
↑
原料准备 → 配料 → 混料 → 造球 → 焙烧
↓
成品球团矿 ←
产品处理 ←
↓
冷却 破碎 筛分
焙烧过程: 干燥
↓ 预热
↓ 焙烧
↓ 均热
↓ 冷却
2020/5/26
王瑞祥
烧结矿生产与球团矿生产的区别
烧结和球团都是粉矿造块的方法。但它们的生
2020/5/26
王瑞祥
温度继续升高,在高温
下保持一段时问,氧化 从球团矿表层向内部推 进,就一个颗粒而言, 氧化向中心扩展,直到 全部氧化成赤铁矿。在 高温下,赤铁矿微晶长 大并重新结晶,使颗粒 结合成牢固的整体(图 b)。
2020/5/26
王瑞祥
② Fe3O4的再结晶与晶粒长大
在缺乏氧气的地方温度达到一定的水平时,磁
2020/5/26
王瑞祥
竖炉工作原理图
球团竖炉是一种按逆流原则工作的热交换设 备。生球由布料机均匀地从炉口装入炉内并 以均匀的速度连续下降。用煤气或重油作燃 料,在燃烧室内充分燃烧。温度达到11501250℃的热气体从喷火口进入炉内,达到自 下而上与生球进行热交换。通过燃烧室进入 的空气量约为焙烧所需全部空气量的35% , 其余的空气从下部鼓入,使球团冷却的同时 空气被加热到高温,进入焙烧区域。
② Fe3O4再结晶
在,还加原热性到气90氛0℃中后焙,烧产赤生铁F矿e3O生4再球结时晶,使F球e2团O3将固还结原。成Fe3O4和FeO
③液相固结
用赤铁矿粉生产熔剂性球团矿时,氧化气氛下,当焙烧温度达到
600℃以后,就有铁酸钙等低熔点固相产物生成,温度升高到1300 ℃左右时,这些低熔点物质相继熔化,使矿粉颗粒润湿,在球团 冷团却时时,将则其出固现结2F起eO·来。SiO(2S或iOC2a含O量·较Fe多2O3或液用相赤固铁结矿。粉) 生产自熔性球
合机的一次混合流程。国外有的厂采用 连续式混磨机。
2020/5/26
王瑞祥
2.2 造球作业 2.2.2 造球
圆盘造球机工艺
圆盘造球机是目前国 内外广泛使用的造球 设备。
2020/5/26
王瑞祥
2.2 造球作业
铁矿粉的成球过程 √铁矿粉加水造球过程可分为三个阶段,母球形成,
母球长大,生球密实。这3个阶段是靠加水润湿和机械 滚动作用力来完成的。
2020/5/26
王瑞祥
㈡赤铁矿球团的焙烧固结方式:
① Fe2O3再结晶
较纯的赤铁精矿球团在氧化气氛中焙烧时,赤铁矿晶粒在900℃
开始再结晶,随着温度的升高,晶粒逐渐长大,球团强度将提高 。但这是一种简单的再结晶过程,比磁铁矿球团固结要困难。因 为与磁铁矿球团焙烧固结相比,赤铁矿在氧化气氛中不会氧化, 不能放热,不发生晶型转变,其原子的活动能力也比氧化新生成 的赤铁矿弱。赤铁矿球团的焙烧温度都控制在1300℃左右。
2020/5/26
王瑞祥
三种焙烧球团方法
①竖炉:一般为8~10m2优点是结构简单,热效率高,
缺点是温度控制难,局部温度易过高而易结块,料层 高易使球团破损,故单炉规模很难大型化,适合中小 企业。
②带式焙烧机:能调整加热焙烧制度,对原料适应性强
、生球在高温焙烧带停留时间较带式焙烧机长,有助 于获得高强度产品,生产的球团矿质量好和粒度均匀 。但因台车和箅条在高温运行,需要耐热钢制造。它 是大型球团厂的主要焙烧设备。缺点是投资费用大。
二、添加剂
目的:改善球团矿的化学成分,特别是其造渣成分,
提高球团矿的冶金性能,降低还原粉化率和还原膨胀 率等。
常用的添加剂有消石灰、石灰石和白云石等钙镁化合
物。
2020/5/26
ห้องสมุดไป่ตู้
王瑞祥
2.2 造球作业
2.2.1 配料与混合
一、配料 1、配料的目的:获得化学成分和物理性质稳
定,冶金性能符合高炉冶炼要求的球团矿,并 使混合料具有良好的成球性能和生球焙烧性能 。
2020/5/26
王瑞祥
⑷ 均热:温度略低于焙烧温度,保持一
段时间,使晶粒进一步长大,提高晶桥 强度,使球团组织均匀化,消除内部应 力。
⑸冷却:从1000℃以上冷却到运输皮带
可以承受的温度。冷却介质为空气。
球团矿强度变化 生球抗压强度:1-2kg/球 干燥后生球抗压强度:8-10 kg/球 焙烧后球团的抗压强度:>200kg/球
混合机内同时进行的,成球不完全,混合料中 仍然含有相当数量未成球的小颗粒。而球团矿 生产工艺中必须有专门的造球工序和设备,将 全部混合料造成10~25mm的球,小于10mm 的小球要筛出重新造球。
2020/5/26
王瑞祥
球团生产工艺概述
球团生产是使用不适宜烧结的精矿粉和其他
含铁粉料造块的一种方法。球团法是由瑞典的 于1913年取得国内专利的。但正式采用是在 1943年,美国开采一种低品位磁铁矿—铁隧石 ,精选出来的矿粉粒度很细,难以烧结,才开 始球团生产和用于高炉的试验。50年代中期开 始工业规模生产。由于各国天然富矿资源缺乏 ,必须扩大对贫矿资源的利用,正是球团工艺 为细磨精矿造块开拓了新路,而且球团矿粒度 均匀,还原性和强度好、微气孔多,故发展迅 速,全世界1980年初年产已达3亿t,其中北美 占一半以上。烧结和球团有各自的优点互为补 充,今天不少工厂为高炉提供烧结矿和球团矿 组成的综合炉料。
③链篦机-回转窑:优点是质量均匀、节能、生产能力
较大;缺点是易结圈、投资大。目前链箅机—回转窑 的球团矿占总产量的比例日益增多。
2020/5/26
王瑞祥
1、竖炉
竖炉的规格用炉口断
面积来表示。炉口断 面大部分呈矩形。我 国多数竖炉为4~ 8m2,炉口宽度不超 过 1.8m,长度为宽 度的3~3.25倍。一 座8m2竖炉的年产量 为12万t。
再磨可分为干磨和湿磨两种。
5.1.2 粘结剂与添加剂
一、粘结剂 球团生产使用的粘结剂有:
和膨水润泥土等Al。2(Si氧4O化10固)(O结H球)2团、常消用石膨灰润、土石、灰消石石、 灰两种。
2020/5/26
王瑞祥
2.1 球团原料及准备
膨润土的作用:能提高生球强度、调剂原料水分、稳
定造球作业,提高物料的成核率和降低生球长大速度 ,使生球粒度小而且均匀。同时膨润土还能够提高生 球的热稳定性,既提高了生球的爆裂温度和生球干燥 速度,缩短了干燥时间,又可提高干球强度和成品球 团矿的强度。
2020/5/26
王瑞祥
球团生产步骤
球团生产大致分三步: (1)将细磨精矿粉、熔剂(添加剂)、燃料(1%
~2%,有时也可不加)和黏结剂(如皂土等约 0.5%,有时也可不加)等原料进行配料与混合 ;
(2)在造球机上加适当的水,滚成10~15mm的
生球(即造球);
(3)生球在高温焙烧机上进行高温焙烧,焙烧
2020/5/26
王瑞祥
√球团矿焙烧的五个阶段
干燥、预热、 焙烧、
均热、冷却
2020/5/26
王瑞祥
二、球团的焙烧固结机理
√㈠磁铁矿球团的焙烧固结方式(磁铁精矿
是生产球团的主要原料)
①Fe2O3微晶键连接(晶桥连接)
磁铁矿氧化形成赤铁矿微晶键以及微晶长大和再结晶
。磁铁矿在200℃下便开始氧化,从颗粒的表层开始, 由接F触e处3O形4转成变“晶为桥Fe”2,O3新,生生的成F的e2FOe32微O3晶微具晶有在高相度邻的的迁颗移粒 能力,促使它们结合在一起,形成微晶键,又叫“晶桥 ”(图a)。当温度升到600℃时,只要氧化气氛充分, 新生的晶键已有定的强度,使球团矿一形成硬壳。
产工艺和固结成块的基本原理却有很大区别, 在高炉上冶炼的效果也有各自的特点。烧结与 球团的区别主要表现在以下几方面:
2020/5/26
王瑞祥
烧结与球团的区别 1、矿粉粒度不同 富矿短缺,必须不断
扩大贫矿资源的利用,而选矿技术的进 步可经济地选出高品位细磨铁精矿,其 粒度从-200网目(小于0.074mm)进一 步减少到-325网目(小于0.044mm)。 这种过细精矿不益于烧结,透气性不好 ,影响烧结矿产量和质量的提高,而用 球团方法处理却很适宜,因为过细精矿 易于成球,粒度愈细,成球性愈好,球 团强度愈高。
2020/5/26
王瑞祥
1、竖炉
干燥和预热过程中防爆
国外竖炉生球从上往下运动,与预热带上升的热废气
发生热交换进行干燥.无专门的干燥设备。生球下降 到离料面 120一150mm深度处,相当于经过了4—6分 钟的停留时间,大部分 已经干燥,并开始预热,磁铁 矿开始氧化。当炉料下降到500mm时, 便达到最佳焙 烧温度,l350 ℃左右。