工件表面裂纹机器视觉检测研究
基于机器视觉的桥梁裂缝检测技术
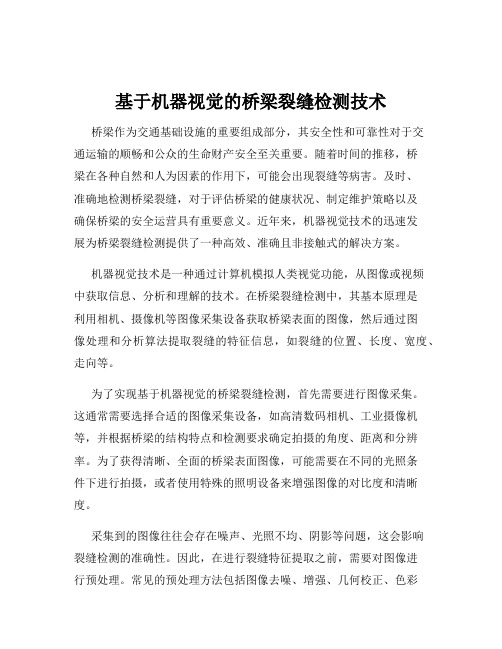
基于机器视觉的桥梁裂缝检测技术桥梁作为交通基础设施的重要组成部分,其安全性和可靠性对于交通运输的顺畅和公众的生命财产安全至关重要。
随着时间的推移,桥梁在各种自然和人为因素的作用下,可能会出现裂缝等病害。
及时、准确地检测桥梁裂缝,对于评估桥梁的健康状况、制定维护策略以及确保桥梁的安全运营具有重要意义。
近年来,机器视觉技术的迅速发展为桥梁裂缝检测提供了一种高效、准确且非接触式的解决方案。
机器视觉技术是一种通过计算机模拟人类视觉功能,从图像或视频中获取信息、分析和理解的技术。
在桥梁裂缝检测中,其基本原理是利用相机、摄像机等图像采集设备获取桥梁表面的图像,然后通过图像处理和分析算法提取裂缝的特征信息,如裂缝的位置、长度、宽度、走向等。
为了实现基于机器视觉的桥梁裂缝检测,首先需要进行图像采集。
这通常需要选择合适的图像采集设备,如高清数码相机、工业摄像机等,并根据桥梁的结构特点和检测要求确定拍摄的角度、距离和分辨率。
为了获得清晰、全面的桥梁表面图像,可能需要在不同的光照条件下进行拍摄,或者使用特殊的照明设备来增强图像的对比度和清晰度。
采集到的图像往往会存在噪声、光照不均、阴影等问题,这会影响裂缝检测的准确性。
因此,在进行裂缝特征提取之前,需要对图像进行预处理。
常见的预处理方法包括图像去噪、增强、几何校正、色彩平衡等。
通过这些处理,可以改善图像质量,突出裂缝的特征,为后续的检测工作奠定基础。
在裂缝特征提取阶段,算法的选择和设计至关重要。
目前,常用的裂缝特征提取算法包括基于边缘检测的算法、基于阈值分割的算法、基于形态学操作的算法以及基于深度学习的算法等。
基于边缘检测的算法通过检测图像中灰度值的突变来确定裂缝的边缘;基于阈值分割的算法则根据设定的灰度阈值将图像分为前景(裂缝)和背景;基于形态学操作的算法通过腐蚀、膨胀等运算来提取裂缝的形状和结构;基于深度学习的算法则利用深度神经网络自动学习裂缝的特征,具有较高的检测精度和泛化能力。
基于机器视觉的产品表面瑕疵检测算法

基于机器视觉的产品表面瑕疵检测算法随着工业生产的发展,产品质量的要求也越来越高。
而产品表面的瑕疵是一个常见的问题,对产品的外观质量和功能性都有很大的影响。
传统的人工检测方式费时费力,并且容易出现误判或漏检的情况。
因此,基于机器视觉的产品表面瑕疵检测算法应运而生,成为一种高效、准确的检测方法。
一、机器视觉技术在产品表面瑕疵检测中的应用机器视觉技术是一种模拟人眼的感知能力,并通过图像采集、处理和分析来实现对产品表面的检测。
在产品表面瑕疵检测中,机器视觉技术可以检测各种瑕疵,如划痕、凹陷、裂纹等,并根据瑕疵的程度和位置给出相应的判断结果。
二、机器视觉检测算法的基本原理机器视觉检测算法的基本原理是将产品表面的图像信息采集下来,并通过图像处理和分析来提取特征,进而判断是否存在瑕疵。
常见的机器视觉检测算法包括图像预处理、特征提取和分类器设计。
1. 图像预处理图像预处理是机器视觉检测算法的第一步,其目的是对采集到的图像进行增强和去噪。
常见的预处理技术包括灰度化、滤波、边缘检测等。
通过图像预处理,可以提高图像的质量,从而更好地提取特征和进行后续的分析。
2. 特征提取特征提取是机器视觉检测算法的核心步骤,其目的是从图像中提取出有用的信息,用于判断产品表面是否存在瑕疵。
常见的特征提取方法包括形态学运算、图像滤波、边缘检测以及纹理分析等。
通过合适的特征提取方法,可以有效地区分产品表面的瑕疵和正常部分。
3. 分类器设计分类器设计是机器视觉检测算法的最后一步,其目的是根据提取到的特征,对图像进行分类,判断产品表面是否存在瑕疵。
常见的分类器设计方法有支持向量机(SVM)、人工神经网络(ANN)和决策树等。
通过设计合适的分类器,可以实现对产品表面瑕疵的准确检测和分类。
三、机器视觉检测算法的优势基于机器视觉的产品表面瑕疵检测算法相比传统的人工检测方式具有许多优势。
1. 高效性机器视觉技术可以快速采集大量的图像信息,并通过算法进行处理和分析,从而实现对产品表面瑕疵的快速检测。
基于机器视觉的机械零件裂纹无损检测方法

基于机器视觉的机械零件裂纹无损检测方法摘要:一、引言1.背景介绍2.研究目的3.文章结构二、机器视觉技术概述1.定义与原理2.发展历程3.应用领域三、机械零件裂纹无损检测方法1.传统检测方法2.机器视觉检测方法a.图像处理技术b.特征提取与分类c.深度学习与神经网络四、机器视觉检测方法的优点与局限性1.优点a.非接触式检测b.高精度与高可靠性c.自动化与智能化2.局限性a.光照条件影响b.零件表面纹理影响c.检测范围与检测速度限制五、实例分析与应用1.某飞机零件裂纹检测2.某汽车发动机零件裂纹检测3.某电力设备零件裂纹检测六、未来发展趋势与展望1.深度学习与强化学习应用2.无人机与机器人检测技术3.跨领域融合与创新七、结论1.研究成果总结2.意义与价值3.后续研究方向正文:一、引言随着工业制造技术的不断发展,机械零件的可靠性与安全性在工程领域中显得尤为重要。
然而,在实际应用过程中,由于材料老化、疲劳累积等原因,零件会产生裂纹,严重影响其使用寿命和安全性。
为了确保工程安全,及时发现和检测零件裂纹至关重要。
近年来,基于机器视觉的检测方法逐渐成为无损检测领域的研究热点。
本文将介绍一种基于机器视觉的机械零件裂纹无损检测方法,并探讨其优点与局限性。
二、机器视觉技术概述1.定义与原理机器视觉是指通过计算机系统对图像进行处理、分析和理解,以实现对实际世界的感知和认知。
其基本原理是利用光学成像设备将实际场景转换为图像信号,然后通过计算机对图像进行预处理、特征提取和分类,最终实现对目标的检测、识别和定位。
2.发展历程机器视觉技术自20世纪50年代起开始发展,经历了从模拟电路到数字电路、从传统图像处理方法到现代图像处理方法、从单一学科研究到跨学科研究等阶段。
目前,机器视觉技术已广泛应用于工业自动化、医疗诊断、智能交通等领域。
3.应用领域机器视觉技术的应用领域包括工业检测、生物医学成像、无人驾驶、智能监控等。
在机械零件裂纹检测方面,机器视觉技术具有很高的实用价值。
基于机器视觉的工件表面粗糙度检测算法研究
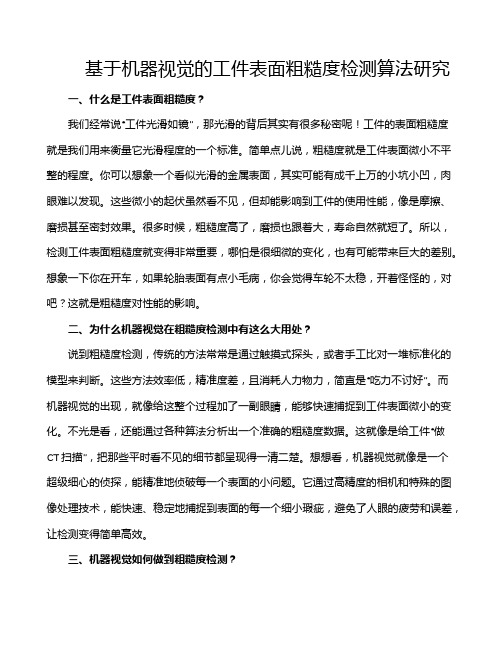
基于机器视觉的工件表面粗糙度检测算法研究一、什么是工件表面粗糙度?我们经常说“工件光滑如镜”,那光滑的背后其实有很多秘密呢!工件的表面粗糙度就是我们用来衡量它光滑程度的一个标准。
简单点儿说,粗糙度就是工件表面微小不平整的程度。
你可以想象一个看似光滑的金属表面,其实可能有成千上万的小坑小凹,肉眼难以发现。
这些微小的起伏虽然看不见,但却能影响到工件的使用性能,像是摩擦、磨损甚至密封效果。
很多时候,粗糙度高了,磨损也跟着大,寿命自然就短了。
所以,检测工件表面粗糙度就变得非常重要,哪怕是很细微的变化,也有可能带来巨大的差别。
想象一下你在开车,如果轮胎表面有点小毛病,你会觉得车轮不太稳,开着怪怪的,对吧?这就是粗糙度对性能的影响。
二、为什么机器视觉在粗糙度检测中有这么大用处?说到粗糙度检测,传统的方法常常是通过触摸式探头,或者手工比对一堆标准化的模型来判断。
这些方法效率低,精准度差,且消耗人力物力,简直是“吃力不讨好”。
而机器视觉的出现,就像给这整个过程加了一副眼睛,能够快速捕捉到工件表面微小的变化。
不光是看,还能通过各种算法分析出一个准确的粗糙度数据。
这就像是给工件“做CT扫描”,把那些平时看不见的细节都呈现得一清二楚。
想想看,机器视觉就像是一个超级细心的侦探,能精准地侦破每一个表面的小问题。
它通过高精度的相机和特殊的图像处理技术,能快速、稳定地捕捉到表面的每一个细小瑕疵,避免了人眼的疲劳和误差,让检测变得简单高效。
三、机器视觉如何做到粗糙度检测?说到机器视觉在粗糙度检测中的应用,先得提到图像的获取。
你看,机器视觉系统通过高清相机将工件表面拍得清清楚楚,然后通过图像处理技术,像是灰度处理、边缘检测、去噪声等等,去除掉一些不必要的干扰因素。
就进入了“核心环节”,这就是通过分析图像中那些微小的起伏、波动来计算粗糙度。
通过一些算法模型,机器可以将这些表面的起伏变化转换为数值,进而得出精确的粗糙度指标。
别看这些步骤有点复杂,其实它们就像是一部精密的机械手表,每个部件都在精确运作,确保检测结果的准确无误。
基于机器视觉的工件表面缺陷检测算法研究与应用

基于机器视觉的工件表面缺陷检测算法研究与应用随着工业发展的不断推进,工件表面缺陷的检测变得越来越重要。
其中,机器视觉技术的应用为工件缺陷检测提供了一种有效的手段。
本文将针对基于机器视觉的工件表面缺陷检测算法进行研究与应用,探讨其原理和优势。
一、机器视觉技术在工件表面缺陷检测中的应用机器视觉技术是一种利用计算机视觉系统对图像进行感知、分析和处理的技术。
在工件表面缺陷检测中,机器视觉技术可以通过图像采集、处理和分析,实现对工件表面缺陷的自动检测和分类。
二、工件表面缺陷检测的算法原理1. 图像采集与预处理在工件表面缺陷检测中,首先需要采集工件表面的图像数据。
通过合适的光源和相机等设备,获取高质量的图像。
然后,进行图像预处理,包括图像去噪、图像增强等处理,以提高后续算法的准确性和稳定性。
2. 特征提取与选择提取工件表面缺陷图像中的特征是缺陷检测的关键一步。
常用的特征包括纹理特征、形状特征、颜色特征等。
根据具体情况,选择适合的特征进行提取,并进行适当的降维处理,以减少特征的维度和冗余信息。
3. 缺陷检测与分类在特征提取后,利用机器学习算法对工件图像进行缺陷检测和分类。
常用的算法包括支持向量机(SVM)、卷积神经网络(CNN)等。
通过训练模型和测试样本,实现对工件缺陷的有效检测和分类。
三、基于机器视觉的工件表面缺陷检测算法的优势1. 高效性机器视觉技术可以实现对工件表面缺陷的自动检测和分类,大大提高了检测的效率。
相比于传统的人工检测方法,机器视觉算法可以在短时间内处理大量图像数据,提高了生产力和效益。
2. 准确性基于机器学习算法的工件缺陷检测可以通过大量的样本训练和测试,从而提高检测的准确性。
机器视觉算法可以自动识别和分析工件缺陷,避免了人眼视觉疲劳和主观判断的影响,减少了误检和漏检的问题。
3. 稳定性机器视觉算法可以稳定地运行在工业生产线上,实时地对工件进行检测。
相比于人工检测的系统,机器视觉算法可以克服环境变化对检测结果的影响,并且不受人为因素的干扰。
机器视觉表面缺陷检测综述

机器视觉表面缺陷检测综述摘要:随着科技的发展和工业生产的进步,表面缺陷的检测对于提高产品质量和生产效率变得越来越重要。
在传统的生产过程中,通常需要人工检查表面缺陷,但这种方式存在主观性高、效率低等问题。
机器视觉技术作为一种替代手工检测的方法,能够快速、准确地检测表面缺陷,并且具有自动化、高效率等优势。
本文综述了机器视觉表面缺陷检测的相关技术和方法,包括图像获取、特征提取、分类器设计等方面的内容,旨在为相关领域研究者提供参考和借鉴。
一、引言表面缺陷是指产品表面的瑕疵、污渍等不良状态,如裂纹、划痕、气泡等。
这些缺陷的存在可能会导致产品质量下降、市场竞争力降低甚至安全隐患。
在传统的生产过程中,通常采用人工检查的方式来判断产品表面缺陷,但这种方式存在主观性高、效率低等问题。
因此,有必要开发一种自动化、高效率的缺陷检测方法。
二、机器视觉表面缺陷检测技术1. 图像获取在机器视觉表面缺陷检测过程中,良好的图像获取是保证检测准确性的基础。
常用的图像获取方法包括CCD相机、高速相机、红外相机等。
选择适当的相机并设置合理的参数,可以获取清晰、高分辨率的图像。
2. 特征提取特征提取是机器视觉表面缺陷检测的关键步骤。
通过对图像进行特征提取,可以将表面缺陷与正常表面进行区分。
常用的特征提取方法包括灰度共生矩阵、小波变换等。
在特征提取过程中,需要选择适当的特征,并进行合适的预处理和选择。
3. 分类器设计分类器设计是机器视觉表面缺陷检测的核心任务。
常见的分类器包括支持向量机、神经网络、决策树等。
在选择分类器的过程中,需要考虑特征的表达能力、分类器计算复杂度等因素。
三、机器视觉表面缺陷检测方法1. 基于传统图像处理的方法基于传统图像处理的方法是机器视觉表面缺陷检测的最早应用之一。
该方法通过对图像进行预处理、滤波等操作,提取图像特征,并基于特征进行缺陷检测。
这种方法简单、易实现,但对于复杂的缺陷检测任务效果有限。
2. 基于深度学习的方法随着深度学习的发展,在机器视觉表面缺陷检测领域也得到了广泛应用。
自动化生产线上的机器视觉质量检测技术研究

自动化生产线上的机器视觉质量检测技术研究随着工业化的发展,自动化生产线已经成为许多行业的主流。
在这些生产线上,质量检测是至关重要的环节,它直接关系到产品的品质和生产效率。
传统的质量检测方法往往依赖于人工操作,效率低下且容易出现漏检和误检的情况。
为了解决这一问题,机器视觉技术被引入到了自动化生产线上,成为了一种重要的质量检测手段。
一、机器视觉技术在自动化生产线上的应用机器视觉技术是利用摄像头、传感器等设备,对产品进行图像采集和分析,以实现自动化质量检测的技术。
在自动化生产线上,机器视觉技术可以应用于以下几个方面:1. 缺陷检测:通过对产品表面图像的分析,检测产品表面的缺陷,如裂纹、划痕、气泡等,确保产品的完整性和质量。
2. 尺寸测量:利用机器视觉技术对产品的尺寸进行精确测量,确保产品符合规定的尺寸要求。
3. 外观检验:检测产品的外观质量,包括颜色、形状、纹理等,保证产品外观的一致性和美观度。
4. 拼装检测:对产品的组装过程进行监控和检测,确保各个零部件的正确拼装,避免因拼装不良导致的质量问题。
二、机器视觉质量检测技术的关键技术和挑战机器视觉质量检测技术虽然在自动化生产线上具有巨大的潜力,但也面临着一些关键技术和挑战:1. 图像处理算法:图像处理算法是机器视觉技术的核心,关乎着检测的准确性和效率。
如何设计高效的图像处理算法,对于提高质量检测的精度和速度至关重要。
2. 光照和环境干扰:生产现场的光照和环境条件可能会对图像采集和分析产生影响,如光照不均匀、环境噪声等,这对于质量检测的稳定性和可靠性提出了挑战。
3. 复杂产品检测:一些产品具有复杂的结构和表面特征,如电子元件、汽车零部件等,对于这些产品的质量检测需要更加复杂的算法和技术支持。
4. 实时性要求:在自动化生产线上,质量检测需要实时进行,对算法的实时性和响应速度提出了更高的要求。
三、机器视觉质量检测技术的发展趋势随着人工智能和深度学习技术的不断发展,机器视觉质量检测技术也在不断创新和进步。
基于机器视觉的电子元器件表面缺陷检测技术研究
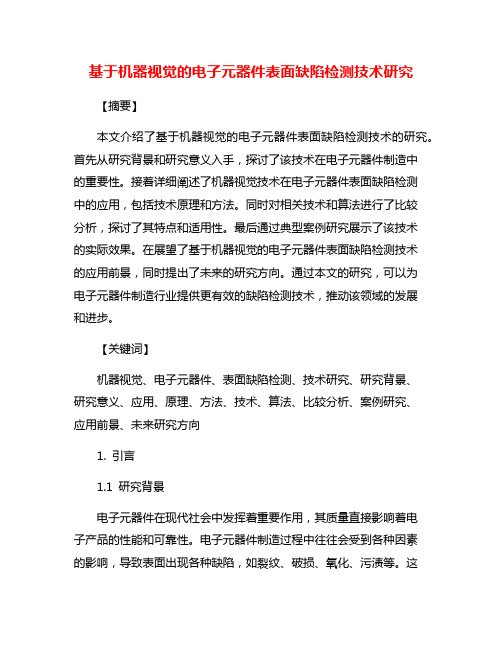
基于机器视觉的电子元器件表面缺陷检测技术研究【摘要】本文介绍了基于机器视觉的电子元器件表面缺陷检测技术的研究。
首先从研究背景和研究意义入手,探讨了该技术在电子元器件制造中的重要性。
接着详细阐述了机器视觉技术在电子元器件表面缺陷检测中的应用,包括技术原理和方法。
同时对相关技术和算法进行了比较分析,探讨了其特点和适用性。
最后通过典型案例研究展示了该技术的实际效果。
在展望了基于机器视觉的电子元器件表面缺陷检测技术的应用前景,同时提出了未来的研究方向。
通过本文的研究,可以为电子元器件制造行业提供更有效的缺陷检测技术,推动该领域的发展和进步。
【关键词】机器视觉、电子元器件、表面缺陷检测、技术研究、研究背景、研究意义、应用、原理、方法、技术、算法、比较分析、案例研究、应用前景、未来研究方向1. 引言1.1 研究背景电子元器件在现代社会中发挥着重要作用,其质量直接影响着电子产品的性能和可靠性。
电子元器件制造过程中往往会受到各种因素的影响,导致表面出现各种缺陷,如裂纹、破损、氧化、污渍等。
这些缺陷不仅影响了元器件的美观度,更可能影响其功能和寿命,甚至引发安全隐患。
传统的电子元器件表面缺陷检测方法大多依赖于人工目视检测,存在着效率低、易出错、主观性强等问题。
为了提高检测效率和准确性,近年来研究人员开始将机器视觉技术引入到电子元器件表面缺陷检测领域。
机器视觉技术通过使用数字相机、图像处理算法等工具,可以实现对电子元器件表面缺陷的自动检测和分析,大大提高了检测的准确性和效率。
基于机器视觉的电子元器件表面缺陷检测技术成为了当前热门研究领域之一。
通过结合机器视觉技术和深度学习算法,可以实现对电子元器件表面缺陷的自动识别和分类,为电子制造行业提供了一种全新的解决方案。
该技术的发展与应用将极大地推动电子元器件质量检测领域的进步,对提升电子产品的质量和市场竞争力具有重要意义。
1.2 研究意义电子元器件作为现代电子设备的核心部件,其表面缺陷问题一直是电子制造领域中的一个重要研究方向。
- 1、下载文档前请自行甄别文档内容的完整性,平台不提供额外的编辑、内容补充、找答案等附加服务。
- 2、"仅部分预览"的文档,不可在线预览部分如存在完整性等问题,可反馈申请退款(可完整预览的文档不适用该条件!)。
- 3、如文档侵犯您的权益,请联系客服反馈,我们会尽快为您处理(人工客服工作时间:9:00-18:30)。
圆形度和长宽比特征实现裂纹的存在判断。多个样本工件试验结果表明,该 类工件表面裂纹检测系统的稳定性、准确性均优于传统
的 人 工 检 测 ,很 好 地 完 成 了 裂 纹 检 测 任 务 。 关 键 词 :机器视觉;检 测 ;LabVIEW; 图像采集;小波算法
中 图 分 类 号 :TH878;TP391
第 38卷 第 9 期 2017年 9 月
白动化仪表 PROCESS AUTOMATION INSTRUMENTATION
V ol.38 No. 9 Sep. 2017
工件表面裂纹机器视觉检测研究
厉 荣 s 1 ,史 东 东 2
(1.上海工业自动化仪表研究院有限公司,上海200233;2.上海理工大学光电信息与计算机工程学院,上 海 200093)
提取裂纹有效区,将潜在的裂纹区域与背景部分区分开;调 用 MATLAB script节点对裂纹图像小波去噪,使裂纹部分变得清晰易辨;结
合 最 大 类 间 方 差 法 和 形 态 学 处 理 提 取 裂 纹 的 连 通 域 图 像 ,成 功 将 裂 纹 连 通 域 从 背 景 及 干 扰 粒 子 中 提 取 出 来 ;最 后 通 过 计 算 连 表面质量检测的重要部分,而表面质量的好坏又是影响工件整体质量的重要因素,因此工件表面 质量检测不可或缺。基于工件表面图像特征,结合机器视觉硬件,基 于 美 国 N I公 司 研 制 的 LabVIEW软 件 平 台 和 NI Vision视觉工具
包 ,研究了工件表面图像模板匹配、去噪、二次分割、裂纹识别的算法,设计了工件表面裂纹检测系统。采用基于灰度的模板匹配方法
文 献 标 志 码 :A
DOI:10.16086/j. cnki. issnlOOO -0380.201709020
Research on the Workpiece Surface Crack Detection Based on Machine Vision
LI Rongxuan1 , SHI Dongdong2 (1. Shanghai Institute of Process Automation Instrumentation Co. , Ltd. , Shanghai 200233, China ; 2. School of Opto Electronic Information and Computer Engineering, University of Shanghai for Science and Technology, Shanghai 200093, China)