超细纤维 简介
超细纤维的制造方法

超细纤维的制造方法超细纤维的制造方法超细纤维,又称超细旦.旦是纤维的纤度单位,一克重9000米长的丝为旦,蚕丝的纤度单位为旦.因为它比传统的纤维细,所以比一般纤维更具蓬松、柔软的触感,且能克服天然纤维的易皱、人造纤维不透气的缺点.此外,它还具有保暖、不发霉、无虫驻、质轻、防水等许多无可替代的优良特性.超细纤维的品种有超细旦粘胶丝、超细旦锦纶丝、超细旦涤纶丝、超细旦丙纶丝等等.超细长丝的制造方法超细长丝纺丝方法通常有:直接纺丝改良法;高分子相互并列纺丝法;剥离型复合纺丝法;多层型复合纺丝法等多种.超细代表型长丝的制造方法多采用剥离分割法.由于制造方法的不同,纤维的形状和性能也有差异,最终产品的性能也不同.直接纺丝改良法采用熔纺法纺制超细长丝的工艺条件如表1所示.现简单列举直接纺丝法制聚酯超细纤维的最佳纺丝条件如下表.表1 直接纺丝法制聚酯超细纤维的最佳纺丝条件与常规纺丝法比较,聚酯超细长丝的纺丝纺丝作如下改进:⑴适当降低聚合物黏度可通过降低聚合物分子量或提高纺丝温度来达到目的,这些措施可防止因液滴型挤出而断丝.⑵喷丝板上的喷丝孔应呈同心圆均匀排列,使丝条均匀冷却.⑶降低喷丝板下方的环境温度,使丝条迅速冷却,并在喷丝板下方20~70cm处集束、卷绕,以获得未拉伸丝.⑷使纤维经受4~6倍的后拉伸在特定的条件下可进行10~20倍的拉伸,但技术条件不稳定,而且范围较窄,故未获得应用.⑸通过高精度过滤以提高纺丝熔体的纯净度.⑹减少熔体的挤出量.高分子相互并列体纺丝法国际上的大公司日本东丽公司制作超细纤维用的就是高分子相互并列体纺丝法.以海岛型复合纤维的纺丝法,所得纤维截面为海组分的皮芯包围岛组分的芯层,溶解除去海组分后,即可得到岛组分的芯层.例如,以聚酯为岛组分、聚苯乙烯为海组分,制得超细聚酯纤维的纤度为,截面呈圆形,直径为μm.也可以整个复合丝的形态加工成织物,在后加工时除去海组分,在纤维间出现微孔隙而容易相互滑移,作人造革特别合适.此外,制造眼镜洁净布的超多岛技术、岛组分表面的凹凸化、岛组分异纤化混合排列、岛组分混合不同聚合物的技术等都已得到实际应用.剥离型复合纺丝法国际上的日本大公司钟纺与帝人公司制作超细纤维用的就是剥离型复合纺丝法.剥离型纺丝方法的关键是如何提高两组分的分割数,以达到超细化的要求.该方法可把两组分复合成米字型、中空型或层状型,纺丝技术的重点在于喷丝板.剥离型复合纤维可用化学药剂处理,使一组分收缩而剥出纤度为的单丝.单丝的剥离无需溶解除去特定成分,因而聚合物不受损失,通过剥离后可形成扁平形或楔形的纤维截面.聚酯与尼龙制成剥离型复合纤维后,用苯甲酸处理使尼龙组分收缩而剥离,所得聚酯纤维具有较好的染色牢度.复合纤维可用作防水织物、人造麂皮、仿真丝织物、眼镜洁净布等.多层型复合纤维的纺丝法国际上的日本大公司可乐丽公司制作超细纤维用的就是多层型复合纤维的纺丝法.多层型复合纤维的截面扁平,纵横向的弯曲刚性差别很大,薄的一方柔软,厚的一方硬挺.由聚酯和尼龙交互复合纤维,可在染色加工时进行剥离,纤度为~,剥离还可在制成织物后进行,还可在退浆精练工序中进行.超细短纤维的制造方法目前,国内外制造超细短纤维的方法有很多,纺丝法就开发了较多种,举几种具有代表性的方法供大家参考.喷射纺丝法或熔喷法该方法是从刀口状喷丝板端开出的一排细孔,熔融的聚合物从众多微小喷丝孔中吐出,再用热风吹散的方法.由于该方法采用吹散熔融聚合物的形式,因此主体是细纤维.但也适用于制造粗细不均匀的短纤维相互熔融粘着的薄片.将细纤维与粗纤维同时喷出制成混合物,可得到蓬松性和保湿性优良的薄片.从制造方法上可以知道该方法的缺点是纤维的分子取向低.闪蒸纺丝法将聚合物溶解于低沸点的的溶剂如液化气等中,加热、加压从喷丝板喷出,溶剂瞬间气化制造纤维的方法.聚合物呈网状喷射,纤维离散,但可得到的超细纤维.通过对喷丝板进行加工,还可形成分子取向的网状纤维,得到的片材结实、牢固.闪蒸纺丝法在非织造布方面的需求迅速增长,可用于装饰材料和信封等各种包装材料.聚合物混合法混合纤维将两种聚合物进行混合,经纺丝拉伸后,用溶解法除去量多的成分或基质成分制造短纤维的方法,得到长短、粗细不一致、有较大离散度的不均一纤维.其他方法⑴离心纺丝法与棉花糖同一原理生产细纤度纤维.⑵湍流成形法把高分子溶液投入呈湍流状的凝固剂中,而制得纤维.⑶爆发法在聚合物溶液或熔体中注入发泡剂或气体,使其剧烈膨胀而喷出的方法.⑷原纤化法把易原纤化的纤维或薄膜经打浆细化的方法.⑸表面溶解减量法用碱使聚酯等纤维溶解而细化的方法.。
超细纤维材料的发展前景
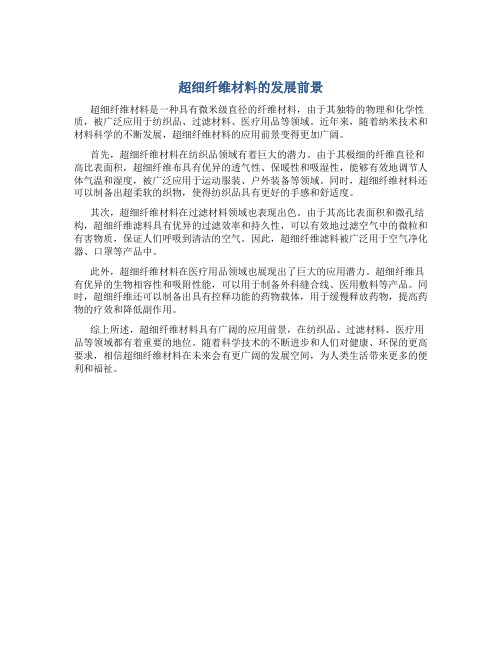
超细纤维材料的发展前景
超细纤维材料是一种具有微米级直径的纤维材料,由于其独特的物理和化学性质,被广泛应用于纺织品、过滤材料、医疗用品等领域。
近年来,随着纳米技术和材料科学的不断发展,超细纤维材料的应用前景变得更加广阔。
首先,超细纤维材料在纺织品领域有着巨大的潜力。
由于其极细的纤维直径和高比表面积,超细纤维布具有优异的透气性、保暖性和吸湿性,能够有效地调节人体气温和湿度,被广泛应用于运动服装、户外装备等领域。
同时,超细纤维材料还可以制备出超柔软的织物,使得纺织品具有更好的手感和舒适度。
其次,超细纤维材料在过滤材料领域也表现出色。
由于其高比表面积和微孔结构,超细纤维滤料具有优异的过滤效率和持久性,可以有效地过滤空气中的微粒和有害物质,保证人们呼吸到清洁的空气。
因此,超细纤维滤料被广泛用于空气净化器、口罩等产品中。
此外,超细纤维材料在医疗用品领域也展现出了巨大的应用潜力。
超细纤维具有优异的生物相容性和吸附性能,可以用于制备外科缝合线、医用敷料等产品。
同时,超细纤维还可以制备出具有控释功能的药物载体,用于缓慢释放药物,提高药物的疗效和降低副作用。
综上所述,超细纤维材料具有广阔的应用前景,在纺织品、过滤材料、医疗用品等领域都有着重要的地位。
随着科学技术的不断进步和人们对健康、环保的更高要求,相信超细纤维材料在未来会有更广阔的发展空间,为人类生活带来更多的便利和福祉。
微纤纤维介绍

微纤纤维介绍
微纤纤维,又称超细纤维。
一般把纤度0.3旦(直径5微米)以下的纤维称为超细纤维。
主要有涤纶/尼龙。
超细纤维纺织而成的面料具有柔软/顺滑/透气性良好/容易保养清洁的特性。
该纤维由美国杜邦公司发明,与传统化学纤维最大的不同处是,三角形结构/纤细的纤维,比圆形结构的纤维更透气,更加柔软,穿着更加舒服。
用微纤纤维制作的擦拭布可以吸附自身重量7倍的灰尘、颗粒、液体、油渍、污物。
可用清水或肥皂、清洁剂洗涤。
超细纤维有很强的吸水性。
普通纤维擦拭布也能起到擦拭物体表面作用,但擦拭效果不佳,仅能积压和推污物。
会有残留物留在被清洁物体的表面,也难以洗涤干净。
微纤纤维的优点:做成织物手感极为柔软,纤维细可增加层状结构,增大比表面积和毛细效应,使纤维内部反射光在表面分布更细腻,使之具有真丝般的高雅光泽,并有良好的吸湿散湿性。
强清洁力。
缺点:由于吸附性很强,所以超细纤维产品不能和其它物品混洗,否则会沾上很多毛和脏东西。
不能用熨斗熨超细纤维毛巾,不能接触60度以上的热水。
无尘布使用在很多行业,包括半导体装配、航空制造及维修、实验室、电子行业、电脑组装、光学仪器制造、液晶显示、精密仪器、光学产品、航空工业、及线路板生产线等;尤其适用于半导体工业、电子工业生产的10级-10000级净化厂房,很多精密五金制造行业大量使用无尘布。
超细纤维的制造方法
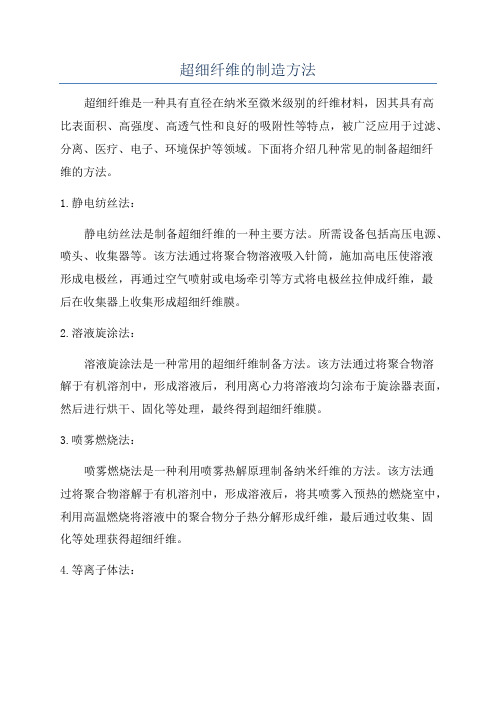
超细纤维的制造方法超细纤维是一种具有直径在纳米至微米级别的纤维材料,因其具有高比表面积、高强度、高透气性和良好的吸附性等特点,被广泛应用于过滤、分离、医疗、电子、环境保护等领域。
下面将介绍几种常见的制备超细纤维的方法。
1.静电纺丝法:静电纺丝法是制备超细纤维的一种主要方法。
所需设备包括高压电源、喷头、收集器等。
该方法通过将聚合物溶液吸入针筒,施加高电压使溶液形成电极丝,再通过空气喷射或电场牵引等方式将电极丝拉伸成纤维,最后在收集器上收集形成超细纤维膜。
2.溶液旋涂法:溶液旋涂法是一种常用的超细纤维制备方法。
该方法通过将聚合物溶解于有机溶剂中,形成溶液后,利用离心力将溶液均匀涂布于旋涂器表面,然后进行烘干、固化等处理,最终得到超细纤维膜。
3.喷雾燃烧法:喷雾燃烧法是一种利用喷雾热解原理制备纳米纤维的方法。
该方法通过将聚合物溶解于有机溶剂中,形成溶液后,将其喷雾入预热的燃烧室中,利用高温燃烧将溶液中的聚合物分子热分解形成纤维,最后通过收集、固化等处理获得超细纤维。
4.等离子体法:等离子体法是一种通过等离子体处理聚合物形成超细纤维的方法。
该方法通过利用高能等离子体对聚合物进行处理,将其分解为活性基团,然后将活性基团通过化学反应方式交联、重组形成纤维,最终得到超细纤维。
5.纳米纤维膜模板法:纳米纤维膜模板法是一种通过模板辅助制备超细纤维的方法。
该方法通过利用金属、陶瓷等材料制备纳米纤维膜模板,然后将聚合物溶液浸渍于模板表面,经过固化、去除模板等处理,得到超细纤维膜。
以上是一些常见的制备超细纤维的方法。
不同的制备方法适用于不同的材料和应用场景,可根据具体需求选择合适的制备方法。
此外,制备超细纤维还需要进行后续的表面改性、组装等处理,以提高其性能和应用价值。
【推荐下载】超细纤维是什么 超细纤维品牌推荐
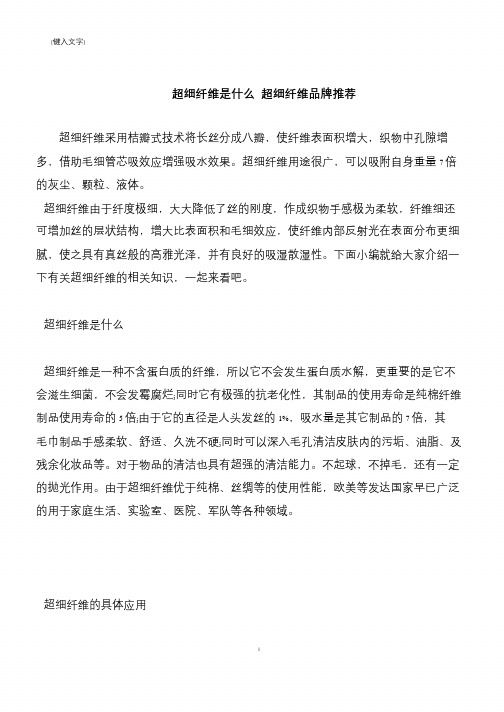
[键入文字]
超细纤维是什么超细纤维品牌推荐
超细纤维采用桔瓣式技术将长丝分成八瓣,使纤维表面积增大,织物中孔隙增多,借助毛细管芯吸效应增强吸水效果。
超细纤维用途很广,可以吸附自身重量7 倍的灰尘、颗粒、液体。
超细纤维由于纤度极细,大大降低了丝的刚度,作成织物手感极为柔软,纤维细还可增加丝的层状结构,增大比表面积和毛细效应,使纤维内部反射光在表面分布更细腻,使之具有真丝般的高雅光泽,并有良好的吸湿散湿性。
下面小编就给大家介绍一下有关超细纤维的相关知识,一起来看吧。
超细纤维是什么
超细纤维是一种不含蛋白质的纤维,所以它不会发生蛋白质水解,更重要的是它不会滋生细菌,不会发霉腐烂;同时它有极强的抗老化性,其制品的使用寿命是纯棉纤维制品使用寿命的5 倍;由于它的直径是人头发丝的1%,吸水量是其它制品的7 倍,其毛巾制品手感柔软、舒适、久洗不硬;同时可以深入毛孔清洁皮肤内的污垢、油脂、及残余化妆品等。
对于物品的清洁也具有超强的清洁能力。
不起球,不掉毛,还有一定的抛光作用。
由于超细纤维优于纯棉、丝绸等的使用性能,欧美等发达国家早已广泛的用于家庭生活、实验室、医院、军队等各种领域。
超细纤维的具体应用
1。
超细纤维
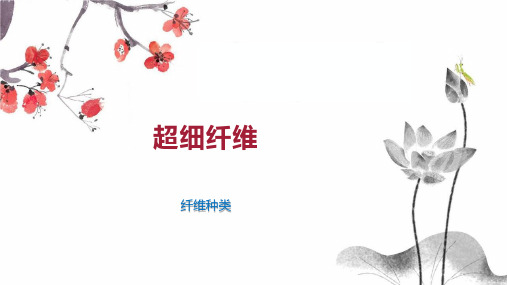
(二)抗皱性与耐磨性较好
超细纤维细度的下降使其绝对强力降低,但是,对于相同纱号而言,其纱截面的纤维根数比常规纱多,因而 纱的强度仍然比较高;同时,有利于对织物进行砂洗或起绒处理,从而制备仿天鹅绒、仿麂皮及桃皮绒等档次较 高的织物,而且具有较好的抗皱性和耐磨性。
制备方法
常规制备
纳米纤维的制 备
常规制备
(4)高密度防水透汽织物:由超细纤维织造的高密度织物,既有防水作用,又有透汽、透湿和轻便、易折 叠携带的性能。用超细纤维制作的滑雪、滑冰、游泳等运动服可减少阻力,有利于运动员创造良好成绩。
(5)洁净布和无尘衣料:超细纤维可以吸附自身质量7倍的灰尘、颗粒、液体。用超细纤维制成的洁净布具 有很强的清洁性能,除污既快又彻底,而且不掉毛,洗涤后可重复使用,在精密机械、光学仪器、微电子、无尘 室以及家庭等方面都得到了广泛的应用,也是无尘衣料的理想选择。
(2)仿桃皮绒织物:这是一种品质优良、风格独特的服装面料。采用超细纤维织成的仿桃皮绒织物,表面 有极短而手感很好的茸毛,犹如桃子表面的细短绒毛,手感柔软、细腻而温暖。用这种面料织造的高档时装、夹 克、T恤衫、内衣、裙裤等凉爽舒适,吸汗不贴身,富有青春美。
涤纶超细纤维概述

2.超细纤维的特点
超细纤维单丝纤度和单丝截面直径比任何天然纤维均小,而纤维越细,相同特数纱线的截面内纤维根数越多,纤维总表面积大。虽然单丝强力小,而纱的总强度较高;超细纤维的单丝抗弯硬挺度较低,加上多根单丝的结构,从而使超细纤维织物有优良的悬垂性、手感柔软;可以利用超细纤维形成很紧密的织物,从而使其功能性得到改善,防水、防风、透湿、绝热性提高,具有丝样外观,光泽柔和。纤维细度对织物表面覆盖性和织物美感有直接影响。由于超细纤维纤度细,单纤强力小,因而其织物易起绒、拉毛,可使织物表面形成纤细绒毛,同时较多的纤维根数,加强了表面遮盖,使手感柔软,因而有较好的毛绒效果,可作仿麂皮、桃皮绒等面料。超细纤维的单丝细度细,所纺成纱线内纤维总比表面积大,利于吸收水分,与常规织物相比,织物中的孔隙率高,有许多毛细管或毛细管系统,再利用材料本身的回潮率,使水分能迅速吸收转移、并扩散,从而可使面料有很好的导湿舒适性。
涤纶超细纤维概述
涤纶超细纤维是一种具有高品质、高性能、高技术含量、高附加值的新产品。它的单丝线密度比常规涤纶纤维低得多,这就赋予了它不同于常规涤纶纤维的优异的服用性能,如吸湿、透气、手感柔软、丰满、富有弹性、蓬松性和飘逸感等。涤纶超细纤维由于线密度比常规纤维低得多,故有异于常规纤维的染色特性,这主要表现在上染速率、上染量、染料提升性、颜色深度、匀染性、移染性、颜色鲜艳度以及染色牢度等和常规纤维有明显的区别。线密度低带来的表面积增加,首先引起染色时对染料吸附和解吸程度的增加,吸附程度的增加导致了上染速率的增加、湿牢度和耐光牢度的下降,其次是引起染色织物的色泽浓度降低。改善涤纶超细纤维及面料的染色性能,成为企业很感兴趣的话题。其实,超细纤维是近年来发展迅速的差别化纤维的一种,被称为新一代的合成纤维,是一种高品质、高技术的纺织原料,是化学纤维向高技术、高仿真化方向发展的新合纤的典型代表。 超细纤维,又称超细旦。(旦是纤维的纤度单位,一克重9000米长的丝为旦,蚕丝的纤度单位为1.1旦)。因为它比传统的纤维细,所以比一般纤维更具蓬松、柔软的触感,且能克服天然纤维的易皱、人造纤维不透气的缺点。此外,它还具有保暖、不发霉、无虫驻、质轻、防水等许多无可替代的优良特性。超细纤维的品种有超细旦粘胶丝、超细旦锦纶丝、超细旦涤纶丝、超细旦丙纶丝等等。
涤纶超细纤维概述

涤纶超细纤维概述涤纶超细纤维,也被称为超细涤纶纤维,是指直径在0.1-1.0微米之间的涤纶纤维。
它是一种人造纤维,由聚酯类原料制成。
涤纶超细纤维具有较高的比表面积和特殊的物理性能,被广泛应用于纺织、过滤、环境保护等领域。
本文将详细讨论涤纶超细纤维的制备方法、性能特点、应用领域和未来发展趋势。
涤纶超细纤维的制备方法主要包括湿法纺丝和干法纺丝两种。
湿法纺丝是将涤纶原料溶解在溶剂中形成聚合液,通过纺丝机将聚合液喷射成纤维,然后进行拉伸、固化、润湿和干燥等工序,最终得到超细纤维。
干法纺丝则是利用高速气流将聚合液喷射,并通过喷水和喷雾等方式迅速固化,形成超细纤维。
两种制备方法各有优势,湿法纺丝能制备出尺寸均匀、纤维形态良好的超细纤维,而干法纺丝具有高产率和较低的生产成本。
涤纶超细纤维的性能特点主要体现在以下几个方面。
首先,涤纶超细纤维具有较高的比表面积,能够提供更多的接触面积与物质进行反应和传递。
其次,涤纶超细纤维的孔隙结构较为均匀且分布密集,有利于气流和水流的流通,提高过滤效率。
此外,涤纶超细纤维具有优异的力学性能和化学稳定性,耐磨、耐高温、耐腐蚀等特点,适用于各种复杂环境下的应用。
涤纶超细纤维在多个领域具有广泛的应用。
首先,在纺织领域,涤纶超细纤维可以用于生产高性能纺织品,如运动服装、内衣、窗帘等。
其细密的纤维结构能够提供更好的柔软性和透气性,使得纺织品更加舒适。
其次,在过滤领域,涤纶超细纤维可以用于空气和水的过滤,如空气净化器、口罩、过滤器等。
由于其高比表面积和孔隙结构,涤纶超细纤维能够提供较高的过滤效率和寿命。
此外,在环境保护领域,涤纶超细纤维可以用于处理废水和废气,如污水处理、烟气脱硫等。
其细纤维的吸附效果和化学稳定性能使其成为优良的吸附材料。
未来,涤纶超细纤维的发展趋势将主要集中在以下几个方面。
首先,提高超细纤维的制备工艺和技术,制备更加均匀、一致的纤维。
其次,改善超细纤维的力学性能和抗菌性能,增加其在纺织和医疗领域的应用。
- 1、下载文档前请自行甄别文档内容的完整性,平台不提供额外的编辑、内容补充、找答案等附加服务。
- 2、"仅部分预览"的文档,不可在线预览部分如存在完整性等问题,可反馈申请退款(可完整预览的文档不适用该条件!)。
- 3、如文档侵犯您的权益,请联系客服反馈,我们会尽快为您处理(人工客服工作时间:9:00-18:30)。
超细纤维(南通大学纺织服装学院,南通桑烨琨0915012002)摘要超细纤维是近代开发法的一类高科技新型纤维.超细纤维虽然没有明确的定义,但是它具有普通纤维无法比拟的优点,可制成许多高性能和高附加价值的纺织品,因此近年来超细纤维的制造及其纺织,染整和服装加工都有了快速发展.关键词超细纤维定义制造发展超细纤维(ultra-fine fiber, micro-fiber),目前国际上尚未有统一的定义,美国PET委员会认为纤维纤度0.3~1.0dtex为超细纤维,AKZO公司认为超细纤维纤度的上限是0.3dtex,意大利则将0.5dtex以下的纤维称为超细纤维;我国纺织工业部化纤工业公司则对超细纤维作了以下定义:涤纶长丝0.5~1.3dtex;锦纶长丝0.5~1.7dtex;丙纶长丝0.5~2.2dtex;短纤维0.5~1.3dtex。
而日本化纤行业普遍将单丝线密度低于0.3dtex的纤维称为超细纤维,这个规定也逐渐被人们所接受。
目前世界上能够生产的最细的超细纤维已达到0.0001dtex。
目前多数合成纤维均可纺制成超细纤维,如聚酯、聚酰胺、聚丙烯腈、聚丙烯甚至聚四氟乙烯、玻璃纤维等。
现在产量最大的是聚酯和聚酰胺超细纤维。
1 超细纤维的发展历史20世纪40年代,受当时羊毛皮芯结构的启发,仿制出了双组分的复合粘胶纤维.该纤维具有三维卷曲,而且卷曲性能较稳定,故称为“永久卷曲粘胶纤维”[1].国外化纤公司在20世纪60年代开始对细旦和超细旦纤维的研究开发工作,杜邦公司在1964年就取得了用复合纺丝法生产超细纤维的专利,并以此作为发展超细纤维的起点.到20世纪70年代,剥离法和海岛法两种复合纺丝法制取0.1 dtex左右超细旦纤维的生产工艺实现了工业化,并取得了较好的经济效果.三菱人造丝公司采用直接纺丝法,制得纤度为0.06 dtex~0.1 dtex的超细旦腈纶[2].日本首批问世的商业化双组分共轭复合纤维结构十分简单,有“并列型”.“皮芯型”等。
随着生产技术水平的不断提高,所谓的多层复合纤维,即在1根单丝内有5个以上结构层的复合纤维研制成功,将其分离即可制得超细纤维.从80年代开始,纤维的产品开发向高品质化、高附加值化、新材料化方向进展,即进入了“高技术时代”,而所谓的“新合纤”技术正是这一时代最夺目的里程碑,超细纤维的技术正是在这种历史背景下日趋成熟的.我国起步较晚,20世纪80年代末着手对超细纤维的研究,1996年7月北京服装学院纺制成了纤维密度为0.05 dtex的超细长纤维[3],打破了发达国家单丝小于0.1 dtex的技术垄断.中国纺织大学也成功开发了世界领先水平的超细旦丙纶长丝及其制品.2超细纤维的类型及生产技术2.1 类型用复合纺丝技术制造的超细纤维可分为:剥离海-岛型和多层型超细纤维,此外还有随机纤维型.不同的生产技术,可制造出不同线、不同种类及用途的超细纤维。
剥离型超细纤维是将两种不相容、但粘度相近聚物,各自沿纺丝组件中预定的通道流过,并汇集复合,通过同一喷丝孔挤出而成形;丝条却、拉伸、织造过程中保持原有的截面形状,当加工成织物后,采用物理或化学处理方法使纺制的复合纤维中的各个组分相互剥离分割开来,成为超细纤维。
海-岛型超细纤维,又称基质原纤型纤维,它是由一种聚合物以极细的形式(原纤)包埋在另一聚合物(基质)之中形成的,又因分散相原纤在纤维截面中呈岛屿状态,因此又称为海-岛型纤维,海-岛型纤维有长丝和短丝两种。
长丝是原纤有规则地连续分布在基质中;短丝是原纤不连续地分布在基质中,其主轴与纤维轴一致。
多层型运用了两种不相溶的高聚物,纺丝前将高聚物熔体由一个静态分离器多层化,然后进行分离或剥离。
日本可乐丽公司开发了第一个多层型超细纤维工业产品,是把聚酯和聚酰胺-6纺制成具有椭圆形截面的多层结构复合纤维,然后在染色过程中微细化成长丝。
2.2生产技术利用不同的生产技术,可制造出不同线密度、不同种类及用途的超细纤维,它们的生产方法主要有直接纺丝法、复合纺丝法和共混纺丝法。
用复合纺丝技术制造的超细纤维可分为剥离型和海岛型(溶解型),前者通过机械处理或化学处理的方法,使纺出的常规线密度的复合纤维中的各个不同性能组分相互剥离分割开来;后者是使用溶剂将海岛型复合纤维中的海组分溶除,从而得到岛组分的超细纤维。
前者适合生产单丝线密度0.33~0.55dtex的长丝,后者则适合生产更细的纤维(0.0001~0.11dtex)纤维的线密度与其生产方法密切相关,表1列出了几种不同细度纤维的生产方法。
可以看出,生产技术的进步使纤维的不断细化成为现实,而纤维细化使纤维的性能发生了很多变化,人们利用纤维性能上的这些变化开发出了各种用途的新产品。
目前较为流行且实现工业化的超细纤维生产技术有:直接纺丝法、复合纺丝法和共混纺丝法,此外,还有静电纺丝法、熔喷法和闪蒸法等。
其中,后四种方法较适合生产短纤维型超细纤维。
2.2.1电纺丝法用电纺丝方法制备超细纤维早在20世纪30年代就申请了专利,但由于纺丝工艺很难稳定,生产效率很低,长期以来很少有人问津。
近年来随着纳米技术的发展,电纺丝技术受到高度的重视,因为它是目前获得纳米直径长纤维的唯一方法或少有的方法之一。
区别于传统纺丝,电纺丝是指聚合物溶液或熔体在外加电场作用下的纺丝工艺。
在电场力作用下,处于纺丝喷头的聚合物溶液或熔体液滴,克服自身的表面张力而形成带电细流,在喷射过程中细流分裂多次,经溶剂挥发或固化后形成超细纤维,最终被收集在接收屏上,形成非制造超细纤维膜或附加特殊装置,将超细纤维纺成纱线。
[4]可用于电纺丝法的高分子材料各种各样,几乎不受任何限制,如聚环氧乙烷(PEO)、聚丙交酯(PLA)、胶原、聚苯胺、聚苯乙烯,等等,甚至蚕的分泌物。
因此其应用研究范围很广,可制备多种生物降解性聚合物超细纤维。
由于这种纺丝技术发展得比较晚,总的说来,它的应用研究还处于起始阶段。
2.2.2复合纺丝剥离法这是一种较为经济、简单的生产方法。
它是用两种不相容而黏度相近的聚合物,通过特殊的纺丝组件制成具有两组分交替排布截面形状的复合纤维后,再通过机械法或化学法使两组分分离,制得超细纤维复合体。
如用聚对苯二甲醇乙二酯(PET)与聚己二酰二胺(锦纶66)经过纺丝、拉伸、定型等处理,制得具有橘瓣形截面形状的双组分纤维,在织造、染整等工序中逐步剥离为单丝线密度小于0.5 dtex的超细纤维。
复合纺丝剥离法的优点是:效率高,无聚合物损失;制得的超细纤维单丝线密度低,并具有混纤及异型纤维的特性。
缺点是纺丝组件构造复杂、加工难度高、设备投资大。
2.2.3超拉伸法以PET为例,聚酯是热塑性高聚物,在玻璃化温度Tg以上温度以很低的形变速率对其进行拉伸时,高聚物分子将产生缓慢流动而不取向。
超拉伸法即基于这一原理,就是使刚从喷丝孔喷出的聚酯纤维先在一定温度下进行超倍拉伸,得到低取向细纤维,再在一定条件下进行补充拉伸使之取向,得到具有一定强度的超细纤维。
这种方法的优点是:可用现有纺丝设备制低取向丝。
缺点是后拉伸工艺控制不稳定,设备产率低,难以适应大工业化生产。
2.2.4溶解法溶解法包含两种含义:一是通过化学方法除去复合纤维中的一个组分,使剩下的组分成为超细纤维包括皮芯和细纤连续分布型两种。
皮芯型是先制皮芯型复合纤维,然后除去皮组织,由芯构成超细纤维。
细纤连续型的复合丝由细纤和基质构成,细纤沿纤维轴连续均匀地分散于基质中,溶解除去基质,可得单丝线密度达0.01 dtex~0.2 dtex的超细长丝。
二是用化学法除去共混纤维中的基质,使分散于基质中的微纤形成单丝线密度为0.001 dtex~0.005 dtex的超细短纤维,用其制造的非制造布是合成革用的最佳基布材料。
溶解法的优点是:纺丝操作较简单,其中的细纤连续型超细纤维线密度低,且在一定范围内可调;溶解过程实施灵活性大,如果选择在织造过程后实施溶解,则可利用现有纺丝、印染设备,以缓解现有纺丝设备落后于超细纤维发展的矛盾。
缺点是高聚物损失量大,溶解产物回收困难,而排放又可能造成污染,且采用复合型原丝时需用特殊纺丝组件。
2.2.5闪蒸法闪蒸法是当聚合物溶液形成纤维时,溶剂瞬间汽化,脱离高聚物,高聚物被喷化成线密度达0.1 dtex~0.15 dtex的超细纤维。
例如将PET溶解在二氯甲烷与1,1,2-三氯乙烷或1,2,2-三氯乙烷的混合溶剂(两者质量比为4∶6~9∶1)中,制成浓度为5%~20%的纺丝原液,再在220℃~280℃,8 MPa条件下进行纺丝,纺丝原液从喷丝孔喷出,溶剂瞬间汽化,喷出的PET即成为超细纤维。
2.2.6常规熔融法常规熔融法是用单一组分的高聚物,通过特定的纺丝工艺,使纤维的单丝线密度降到1 dtex以下。
开发这些设备的基点是:以POY纺丝机或FDY牵伸机为基础,并对原料及部分设备有特殊要求。
常规熔融法的优点是:原料利用率高,纺丝设备简单,生产成本低。
缺点是:生产超低线密度纤维难度大,对原料及部分设备有特殊要求,但其制品仍能满足纺真丝及高密织物的要求。
3超细纤维性能超细纤维由于直径很小,因此其弯曲刚度很小,纤维手感特别柔软;超细纤维的比表面积很大,因此超细纤维织物的覆盖性、蓬松性和保暖性有明显提高,比表面积大纤维与灰尘或油污接触的次数更多,而且油污从纤维表面间缝隙渗透的机会更多,因此具有极强的清洁功能;将超细纤维制成超高密织物,纤维间的空隙介于水滴直径和水蒸汽微滴直径之间,因此超细织物具有防水透汽效果;超细纤维在微纤维之间具有许多微细的孔隙,形成毛细管构造,如果加工成可被水润湿的毛巾类织物,则具有高吸水性,洗过的头发用这种毛巾可很快将水份吸掉。
4 超细纤维的特点与应用细纤维的功能性应用超细纤维的最显著特点,是其单丝线密度大大于普通纤维最细可达0.0001dtex,单丝线密度的急剧降低,决定了超维有许多不同于常规纤维的特性,具有丝般柔、手感滑爽、光泽柔和、抗弯刚度小,易于弯曲;织物表面纤维细柔,悬垂性好,手感柔软。
由于纤维线密度很小,空隙多,形成微孔结构,微孔织物内空隙密而多,织物超高密、质轻、防水透湿性好。
由于纤维线密度很小,织物内空隙细而多,形成微孔结构,且表面拥有较多的茸毛,织物具有良好的排汗、导湿作用,保暖性、耐磨性好。
由于纤维间空隙多而密,可利用其毛细管作用,使织物获得极好的吸水、吸油性能,织物具有很高的清洁能力和去污能力,织物覆盖力强及服装生效果好等优点,其产品具有许多异乎寻常的性能,此在许多领域应用广泛。
其中最重要的应用领域是服装业,对于现代服,已经进入了一个以材质取胜的时代,采用新型维开发的面料可以极大提高服装的附加值。
关注科技纤维的发展,把握其特性,实现面料的科技新和高档化,成为纺织产品的突破口。