发动机油底壳冲压模具设计说明
油箱壳体冲压工艺与模具设计

油箱壳体冲压工艺与模具设计由于油箱的外观质量要求式样越来越受到客户的重视,所以在油箱模具生产过程中,首先对油箱外壳体的冲压工艺的制定必须要合理,油箱模具的质量更要保证,才能够满足客户的生产需求。
通常车油箱外壳体是由两片对称的冲压成形件焊接而成的,钢板厚度为0.8mm。
这两片对称的冲压成形件的拉伸工艺有两种:一种是单片式拉伸成形,另一种为两片式拉伸成形。
这两种冲压工艺方法各有其特点。
只有根据油箱的形状来选择使用哪种冲压工艺,才能做到既能保证油箱外壳体冲压件质量,又能保证油箱制造费用较为经济。
1冲压工艺方案在确定壳体冲压工艺方案时,考虑到生产与设备条件的实际情况,为了提高生产效率,充分有效地利用设备资源,油箱上下壳体的冲压拟采用组合冲模成形,即油箱上下壳体2个冲压件的每道冲压工序都使用一副组合冲模来完成,故壳体冲压工艺方案可采用拉深、整形冲孔、翻孔冲孔切边3道工序,由3副组合冲模完成。
首先将板料分别下料。
拉深件三维数字模型可通过Dynaform软件进行成形模拟分析。
2零件成形工艺分析上壳体顶部有个较大的翻边圆口,圆口周边有若干个小孔,凸缘边入口圆角很小。
为了满足拉深时板料的塑性变形要求,拉深凹模的入口圆角必须增大。
经查资料,凹模的入口圆角取R8mm,由下一道工序整形到零件所要求的R0.8mm;下壳体局部深度高低差异较大,且在凸缘边上有一条加强筋,下壳体拉深难度大于上壳体。
下壳体拉深凹模的入口圆角也增大到R8mm,由下一道工序整形到所要求的R0.8mm。
下壳体局部深度高低变化较大,拉深时凸缘上局部板料产生塑性变形后流入模腔的快慢要求不一致,必须在板料要求流入较慢的凸缘边上设置拉深筋,增大板料径向流动阻力。
零件圆角由R8mm 整形至R0.8mm时,凸缘上的板料还会产生塑性变形,所以下壳体凸缘边上的加强筋不能在第一次拉深时成形出来,应由下一道工序整形圆角R0.8mm时连同加强筋一起成形出来。
为了减少整形R8mm圆角时凸缘上的板料产生过大径向流动,避免造成在整形R0.8mm圆角的过程中受到成形凸缘边上加强筋的影响,经计算在下壳体第一次拉深时应多拉深2mm深度。
冲压模具设计方法与步骤

冲压模具设计方法与步骤冲压模具是制造行业中常用的一种模具,用于在金属板材上进行冲裁、压制、成形等工艺。
冲压模具的设计是冲压工艺的关键环节之一,合理的设计可以提高产品质量和生产效率。
以下是冲压模具设计的方法与步骤。
一、冲压模具设计方法1.分析产品要求:首先需要仔细分析产品要求,了解产品的形状、尺寸、材质等要求,以及要求的生产效率和成本等因素。
2.选择合适的材料:根据产品的要求选择合适的模具材料,常用的材料有合金工具钢、合金冷作工具钢等。
3.制定冲压工艺:根据产品要求,制定冲压工艺,包括冲剪顺序、成形方式、冲压力、冲头形状等因素。
4.设计模具结构:根据产品要求和冲压工艺,设计模具的结构,包括上模、下模、导向机构等部分。
5.进行模具布局:进行模具布局,合理安排模具零件的形状、位置和尺寸,以确保模具的强度和稳定性。
6.进行模具零件设计:根据模具布局,设计模具的零件,包括冲头、导柱、导套、导向板等部分。
7.进行模具装配:根据模具设计,进行模具的装配,确保各个零件之间的配合和精度。
8.进行模具调试:进行模具调试,调整模具的尺寸和位置,确保模具在冲压过程中的稳定性和精度。
9.进行模具试产:进行模具试产,对模具进行试模和试产,检验产品的质量和模具的性能。
10.进行模具改进:根据试产结果,对模具进行改进和优化,提高模具的性能和生产效率。
二、冲压模具设计步骤1.初步设计:根据产品要求,进行初步的模具设计,包括模具结构和布局。
2.详细设计:对初步设计的模具进行详细设计,包括各个零件的形状、尺寸和材料等。
3.模具制造:根据详细设计,进行模具的制造,包括加工模具零部件和进行模具装配。
4.模具调试:对制造完成的模具进行调试,调整模具的尺寸和位置,确保模具的性能和精度。
5.模具试产:进行模具的试模和试产,检验产品的质量和冲压工艺的可行性。
6.模具改进:根据试产结果,对模具进行改进和优化,提高模具的性能和生产效率。
7.模具验收:对改进后的模具进行验收,确保模具达到产品要求和生产效果。
冲压模具设计

冲压模具设计一、冲压模具设计的步骤1.确定需求:首先要明确冲压件的形状、尺寸和质量要求,以及加工工艺的要求,包括材料选材、工艺流程等。
2.分析冲压过程:了解冲压过程中的受力情况,确定冲压件的受力情况,考虑冲压件的结构和形状。
分析完成后,可以确定模具的结构和工作原理。
3.制定设计方案:设计方案是根据需求和分析决策,形成的模具设计的主要思路,包括模具的结构形式、材料选材、零件加工工艺等。
4.细化设计:在设计方案的基础上,进一步细化设计,包括每个零件的尺寸、形状和工艺要求,确保每个零件都符合设计要求。
5.制作样品:制作模具样品,进行试验和调试,验证设计方案的可行性,确定调整和改进方案。
6.定稿设计:根据试验结果,对设计方案进行调整和优化,形成最终的设计方案。
二、冲压模具设计的关键要点1.良好的受力结构:冲压模具在工作过程中要经受巨大的冲击力和挤压力,因此必须具备良好的受力结构,包括合理的分布受力、合理的受力传递和合理的受力集中。
2.优秀的耐磨材料:冲压模具的工作环境往往十分恶劣,耐磨材料可以大大延长模具的使用寿命,提高生产效率。
3.精密的加工工艺:冲压模具的加工精度直接影响到冲压件的质量,因此必须采用精密的加工工艺,确保模具的精密度和可靠性。
4.优化的结构设计:冲压模具的结构设计要尽可能简单,降低成本,提高生产效率。
同时也要考虑模具的易维护性,方便维修和更换零件。
5.可靠的试验与调试:为了保证冲压模具的质量和可靠性,必须进行全面的试验和调试,包括模具的运行测试、冲压件的检测评价等。
三、结语冲压模具设计是一个复杂而细致的工程,需要综合运用材料学、结构设计、机械加工、模具试验等多方面的知识。
只有具备扎实的理论基础和丰富的实践经验,才能设计出高质量的冲压模具。
希望以上内容对冲压模具设计有所帮助,能够指导相关行业的人士更好地进行冲压模具设计工作。
冲压模具设计是一个复杂的过程,需要设计人员深入且全面地了解冲压工艺、材料特性、机械结构、模具加工工艺等多方面知识,并且需要经验丰富的工程师进行设计。
冲压模具设计

冲压模具设计1. 引言冲压模具是指用于进行金属冲压工艺的模具,用于在金属工件上施加力量以将其形状改变。
冲压模具设计在制造业中扮演着重要的角色,它直接影响到产品的质量和生产效率。
本文将介绍冲压模具设计的基本概念、设计过程和一些常用的设计原则。
2. 冲压模具设计的基本概念2.1 冲压工艺冲压工艺是指将薄板金属材料经过剪切、冲孔、弯曲等工艺加工,以获得所需形状和尺寸的工件。
冲压工艺具有高效、精确和重复性好等特点,广泛应用于汽车制造、电子设备和机械制造等行业。
2.2 冲压模具冲压模具是用于进行冲压工艺的工具,通常由上模、下模和导向装置等部件组成。
上模和下模通过导向装置进行定位,形成模腔,金属材料在模腔中受力产生变形,从而得到所需形状的工件。
3. 冲压模具设计的过程冲压模具设计通常包括以下几个步骤:3.1 零件分析在进行冲压模具设计之前,需要对待加工的零件进行分析。
分析包括对零件的形状、材料和尺寸等方面进行研究,以确定合适的冲压工艺和模具结构。
3.2 模具结构设计根据零件的形状和要求,设计冲压模具的结构。
模具结构设计包括上模、下模、导向装置、顶出装置等部分的设计,以保证模具具有足够的刚度和稳定性。
3.3 模具零部件设计根据模具结构设计的结果,对各个零部件进行详细设计。
包括绘制各个零部件的草图、确定材料和尺寸,以及进行结构优化和强度计算等工作。
3.4 工艺路线设计根据零件的要求和工艺特点,设计出适合的工艺路线。
包括冲孔位置和尺寸、切削方式、顶出顺序等方面的确定。
3.5 模具制造和试模根据模具设计的结果,进行模具制造和试模工作。
包括制造各个零部件、装配模具、进行调试和试模等过程。
通过试模,检验模具的设计和制造是否符合要求,提出改进和优化的意见。
4. 冲压模具设计的常用原则4.1 简化结构冲压模具的结构尽量简化,以减少制造成本和提高生产效率。
避免使用复杂的零部件和工艺过程,尽量采用标准件或通用部件,方便制造和维护。
汽车冲压模具设计标准
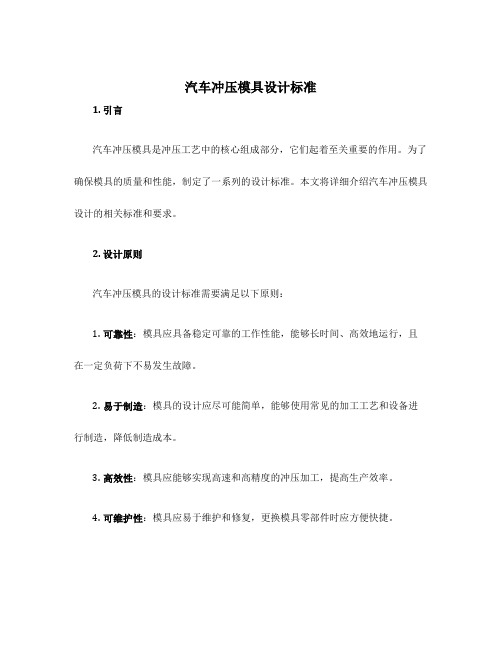
汽车冲压模具设计标准1. 引言汽车冲压模具是冲压工艺中的核心组成部分,它们起着至关重要的作用。
为了确保模具的质量和性能,制定了一系列的设计标准。
本文将详细介绍汽车冲压模具设计的相关标准和要求。
2. 设计原则汽车冲压模具的设计标准需要满足以下原则:1.可靠性:模具应具备稳定可靠的工作性能,能够长时间、高效地运行,且在一定负荷下不易发生故障。
2.易于制造:模具的设计应尽可能简单,能够使用常见的加工工艺和设备进行制造,降低制造成本。
3.高效性:模具应能够实现高速和高精度的冲压加工,提高生产效率。
4.可维护性:模具应易于维护和修复,更换模具零部件时应方便快捷。
3. 结构设计要求根据汽车冲压模具的不同类型和具体工艺要求,模具的结构设计需要满足以下要求:3.1 组合件结构汽车冲压模具通常由多个组合件组成,每个组合件都有特定的功能。
模具的组合件结构应满足以下要求:•简单可靠:组合件设计应尽可能简单,避免过多的连接点和复杂的结构,以提高稳定性和可靠性。
•便于组装和拆卸:组装和拆卸组合件时应方便快捷,避免使用过多的紧固件和工具,节约时间和人力成本。
•可互换性:组合件之间的连接应采用标准化的接口和紧固件,以实现模具部件的互换和共用。
3.2 材料选择汽车冲压模具的材料选择应满足以下要求:•硬度:模具材料应具有足够的硬度,以保证冲压过程中的切削和变形性能。
•耐磨性:模具材料应具有良好的耐磨性能,能够在长时间冲压加工中保持良好的表面质量。
•耐腐蚀性:模具材料应具有一定的抗腐蚀性能,能够应对冲压工艺中的润滑剂和金属氧化物的腐蚀。
•导热性:模具材料应具有良好的导热性能,以加速冲压工艺中的冷却和卸载过程。
3.3 寿命设计模具的寿命设计应考虑以下因素:•材料疲劳:模具在长时间使用过程中可能会发生疲劳损伤,设计时应考虑增加材料的强度和耐疲劳性能。
•应力集中:模具在冲压过程中会受到较大的应力,应避免应力集中,通过结构设计和材料选择来缓解应力分布。
冲压模具设计范文

冲压模具设计范文冲压模具是冲压加工中不可或缺的工具,具有很高的精度和稳定性要求。
冲压模具设计的好坏直接影响到产品的质量和生产效率。
本文将从冲压模具设计的原则、设计步骤和常见问题等方面进行详细介绍。
一、冲压模具设计的原则1.确定加工工艺:在进行模具设计之前,首先要确定产品的加工工艺,包括冲床选型、压力、速度等参数。
模具设计应按照产品加工工艺进行设计,确保模具能够满足产品的加工要求。
2.简洁实用:冲压模具的设计应尽量简洁实用,减少繁杂的结构,提高模具的使用寿命和生产效率。
避免设计过于复杂的零部件,降低制造成本和维修难度。
3.可靠稳定:冲压模具的设计应具有良好的刚性和稳定性,避免产生变形和磨损。
同时,模具应具备相对独立的操作性能,便于调整和维修。
4.提高生产效率:冲压模具设计应注重提高生产效率,包括降低换模时间、缩短生产周期和提高自动化程度等。
合理设计模具结构,优化工艺流程,能够有效提高生产效率和降低生产成本。
5.考虑产品质量:冲压模具设计应考虑产品的质量要求,包括尺寸公差、表面质量等。
通过优化模具结构和加工工艺,提高产品精度和稳定性。
二、冲压模具设计的步骤1.确定产品的加工工艺和技术要求。
包括冲床型号、压力、速度等参数,以及产品的尺寸公差、表面质量等要求。
2.制定模具设计方案。
根据产品的形状、尺寸和加工要求,确定冲压模具的结构类型和数量。
并进行模具结构设计和选材。
3.进行模具的构想和创意设计。
包括模具的整体结构、零件布局和工艺设计等。
根据产品的外观和形状,设计合理的冲压工艺流程。
4.进行模具的详细设计。
根据构想设计,制定模具的详细设计方案。
包括模具的各个零部件的结构设计、力学分析和零件图纸绘制等。
5.完成模具的加工和装配工作。
根据设计方案,进行模具的材料采购、零部件加工和装配工作。
保证模具的质量和精度要求。
6.进行模具的调试和试产。
将模具安装在冲床上,并进行调试和试产。
保证模具的稳定性和生产效果。
三、冲压模具设计的常见问题在进行冲压模具设计时,常见的问题包括:1.材料选择不当:冲压模具的材料选择应根据模具的具体工作情况进行选择。
冲压模具设计

冲压模具设计1. 引言冲压模具是指在冲压加工过程中用于将金属材料加工成所需形状的专用模具。
冲压加工具有高效率、高精度、低材料消耗等优点,是广泛应用于汽车、家电、航空航天等制造行业的关键工艺。
冲压模具的设计是冲压加工过程中不可或缺的一环,在模具设计过程中需要考虑多个因素,包括材料的选择、模具结构的设计、加工工艺的确定等。
2. 冲压模具的基本概念和工作原理冲压模具主要由上模、下模和导向系统组成。
上模与下模配合后形成一个封闭的腔体,腔体中通过金属材料进行冲压加工,使其变形成所需要的形状。
冲压模具的工作原理是通过将上模与下模进行闭合,并施加一定的压力,使金属材料产生弹性变形或塑性变形,从而得到目标形状。
3. 冲压模具的设计步骤冲压模具的设计过程可以分为以下几个步骤:3.1 确定产品形状和尺寸在冲压模具设计之前,首先需要明确产品的形状和尺寸要求。
这可以从产品的图纸和技术要求中获取,也可以通过与产品设计师的沟通来确认。
3.2 材料选择根据产品的特性和工艺要求,选择适合的材料作为冲压模具的材料。
常见的冲压模具材料包括合金工具钢、高速钢等,具体选择需要综合考虑材料的强度、耐磨性、导热性等因素。
3.3 模具结构设计根据产品形状和尺寸要求,设计模具的结构。
模具一般分为上模和下模,根据需要还可以增加一些辅助结构,如导向柱、导向套等。
模具的结构设计需要考虑到产品的加工过程和模具的使用寿命,确保模具具有足够的强度和刚度。
3.4 模具零件设计根据模具的结构设计,对各个零部件进行详细设计。
主要包括上模、下模、导向柱、导向套、导向销等部件。
在设计过程中,需要考虑到各个零件的功能需求,如导向柱的导向精度、导向套的磨损等。
3.5 加工工艺确定根据产品的加工要求和模具的结构特点,确定模具的加工工艺。
主要包括不同零件的加工顺序、加工方法、加工设备的选择等。
加工工艺的确定需要综合考虑加工效率、加工精度和加工成本等因素。
4. 冲压模具设计的注意事项在冲压模具设计过程中,需要注意以下几个方面:•结构合理性:冲压模具的结构应尽可能简洁,确保模具的强度和刚度满足要求;同时要尽量避免零部件的干涉和冲突,以提高模具的稳定性和寿命。
毕业设计论文油箱内侧板冲压工艺及模具设计(含全套cad图纸)

ly is provided the product the 3D data model by the need square of
product molding tool, again the product 3D data model been provided according to
3.模具设计原则 13
3.1 模具设计的基本作用 ............................................................................................13 3.2 模具设计的基本内容................................................................................................17 3.3 冲模设计的技术关键................................................................................................17
4.2 成形模 ...........................................................................................................................22 4.2.1 压力机的选择.................................................................................................22 4.2.2 成形模设计关键 ............................................................................................23 4.2.2 总体设计 ..........................................................................................................29 4.2.3 模具结构材料选择........................................................................................30
- 1、下载文档前请自行甄别文档内容的完整性,平台不提供额外的编辑、内容补充、找答案等附加服务。
- 2、"仅部分预览"的文档,不可在线预览部分如存在完整性等问题,可反馈申请退款(可完整预览的文档不适用该条件!)。
- 3、如文档侵犯您的权益,请联系客服反馈,我们会尽快为您处理(人工客服工作时间:9:00-18:30)。
发动机油底壳冲压模具设计
摘要 汽车发动机油底壳冲压模具属于大中型模具,在实际的模具设计生产中存在一定的
难点,如形状不规则,需要对压力中心进行确定;整体形状复杂,一次拉深对模具、设备的要求相对较高,但多次拉深又易引起拉裂、破损等现象。 首先利用UG对发动机油底壳进行三维实体造型,其属于具有台阶状的复杂盒形件,两侧拉深深度不一,径向拉应力沿盒形件周边分布极为不均匀,在落差的地方产生较大的附加应力,易引起材料堆积或破裂。所以设计关键在于确定拉深次数,以保证油底壳的成形;确定压力中心,以保证设备的安全工作。确定采用单工序模的工艺方案,分别为:落料模、拉深模、冲孔模。 落料模的设计着重于合理安排毛坯的排样和压力机的选择,以及凸、凹模等工作零件的设计确定。拉深模着重于工艺力的计算,并根据工艺力选择了双动拉深压力机,对凸、凹模等也做了设计。冲孔模与落料模同属冲裁模,其原理基本一致。冲孔模着重于法兰边上的25个小孔分布较为密集,因此冲孔凸模的采用过盈配合的固定方式,凹模选择最小壁厚。针对上述三副模具的凸、凹模和其他主要工作零件的服役性能要求,选择合适的材料以及合理的热处理方式,以提高其使用性能,延长使用寿命。最终通过AutoCAD绘制出每一副模具的具体结构。
关键词:油底壳 落料 拉深 冲孔 模具设计 Design of Stamping Die in Oil Sump of Engine Abstract The stamping die of the oil sump of engine belongs to the large and medium molds,
there are many difficulties in the actual design and production, such as an irregularly shaped, you need to calculate the center of the pressure; The whole shape are complex,it is a relatively high requirement of the die if drawing once ,but it is easy to be tension crack and damage after drawing many times. Frist of all, draw a stereogram of the oil sump of the engine by UG, then we can analysis technological parameter of the oil sump of the engine, the depth of drawing in both sides is different, the distribution of the radial tensile stress along the periphery of the rectangular box is extremely non-uniform, it is likely to be a great additional stress in the gap, and cause the accumulation of materials or rupture. So the key of the design is to determine the number of drawing ,in order to ensure the forming of oil sump; to determine the center of the pressure, to make sure the safety of the equipment. On this basis, we adopt the process program of single die definite which are blanking, drawing and perforating respectively. The most important of the die of blanking is to arrange the layout of blank reasonably and select the pressing machine and design the working parts such as convex die and concave die. The most important of the die of drawing is to figure out the force of technology, and select the press machine of double action drawing rely on the force of technology. Besides, we also design the convex die and concave die. The perforating and blanking die belongs to the blanking die, the basic principle of them is consistent. The most important of the perforating die is that the distribution of the 25 small holes in the flange is very concentrated. Therefore we choose the interference fit to fix the convex die of perforating and select the minimum wall thickness of the concave die. At the same time, according the working performance requirement of the convex、concave die and other major working parts, we choose the reasonable materials and the best way to heat treatment, in order to improve its performance and extend the service life. Finally draw out each mould of concrete structures through the AutoCAD.
Key words:oil sump blanking drawing perforating mould design目录 第一章 绪论 ...................................................... 0 1.1概述 ................................................................. 0 1.2冲压成形基本问题 ..................................................... 0 1.2.1冲压与冷冲模的概念 ............................................. 0 1.2.2冲压工序的分类 ................................................. 1 1.2.3冲模的分类 ..................................................... 1 1.3冲压行业的现状 ....................................................... 2 1.3.1冲压行业产品结构现状 ........................................... 2 1.3.2冲压行业技术结构现状 ........................................... 2 1.3.3冲压模具行业配套材料、标准件结构现状 ........................... 3 1.3.4冲压模具行业产业组织结构现状 ................................... 3 1.4冲压行业的发展方向 ................................................... 3 1.4.1模具CAD/CAE/CAM正向集成化、三维化、智能化和网络化方向发展 ..... 4 1.4.2快速经济制模技术 ............................................... 4 1.4.3模具材料及表面处理技术发展迅速 ................................. 4 1.4.4模具工业创新理念和先进生产管理模式 ............................. 5 1.5设计的主要特点及意义 ................................................. 5 第二章 发动机油底壳的工艺分析及工艺方案确定 ...................... 6
2.1 发动机油底壳结构分析及成形工艺方案确定 .............................. 6 2.2发动机油底壳成形工艺方案的确定 ....................................... 7 2.2.1发动机油底壳拉深的特点 ......................................... 7 2.2.2拉深次数的确定 ................................................. 8 2.2.3冲压模具压力中心的确定 ......................................... 9 2.2.4工艺方案的确定 ................................................ 10 第三章 发动机油底壳落料模的设计 ................................. 11