石油脱硫技术经验
石油加工中的脱硫技术

石油加工中的脱硫技术脱硫技术在石油加工中起着重要的作用。
随着环境保护意识的增强,减少二氧化硫排放已成为石油行业的重要任务。
本文将探讨石油加工中常用的脱硫技术,并分析其原理和应用。
一、湿法脱硫技术湿法脱硫技术是目前石油加工中广泛应用的一种方法。
在湿法脱硫中,通过将石油中含有的硫化物与一种溶剂反应,使硫化物转化为可溶性的形式并从石油中移除。
这种技术可以同时去除硫和氮等杂质。
湿法脱硫技术中最常用的方法是氧化脱硫。
在这种方法中,石油经过一系列的处理,使其酸性增加,然后通过与空气中的氧气反应,将硫化物氧化为硫酸盐。
最后,硫酸盐与水反应形成硫酸,从而实现脱硫的目的。
二、干法脱硫技术干法脱硫技术是另一种在石油加工中使用的脱硫方法。
与湿法脱硫不同,干法脱硫不需要使用溶剂,而是通过物理化学反应直接去除石油中的硫化物。
干法脱硫技术中,最常用的方法是选择性吸附。
在这种方法中,石油经过特殊的吸附剂,硫化物会被吸附剂选择性地吸附,从而实现脱硫的目的。
这种方法能够高效地去除硫化物,并且不会引入额外的溶剂,因此在石油加工中得到了广泛应用。
三、生物脱硫技术生物脱硫技术是一种新兴的脱硫方法,其原理是利用特定微生物对硫化物进行降解。
这种方法具有环保、经济和高效的特点,在石油加工中越来越受到关注。
生物脱硫技术中,最常用的方法是利用硫氧化细菌进行脱硫。
这些细菌能够通过代谢过程将硫化物转化为硫酸盐,并从石油中除去。
利用生物脱硫技术不仅可以减少二氧化硫的排放,还可以降低工艺过程中的能耗和废物产生。
四、新兴脱硫技术除了传统的湿法脱硫、干法脱硫和生物脱硫技术,还有一些新兴的脱硫技术在石油加工中逐渐兴起。
这些技术包括离子液体脱硫、高温煤气脱硫以及催化剂脱硫等。
离子液体脱硫技术是利用特殊的离子液体作为溶剂,将硫化物溶解并从石油中去除。
这种方法具有高效率和可再生性的特点,被认为是一种可持续发展的脱硫技术。
高温煤气脱硫技术是将石油加工中产生的高温煤气与一种脱硫剂反应,使硫化物转化为硫酸盐并从煤气中去除。
齐鲁石化炼油厂脱硫技术
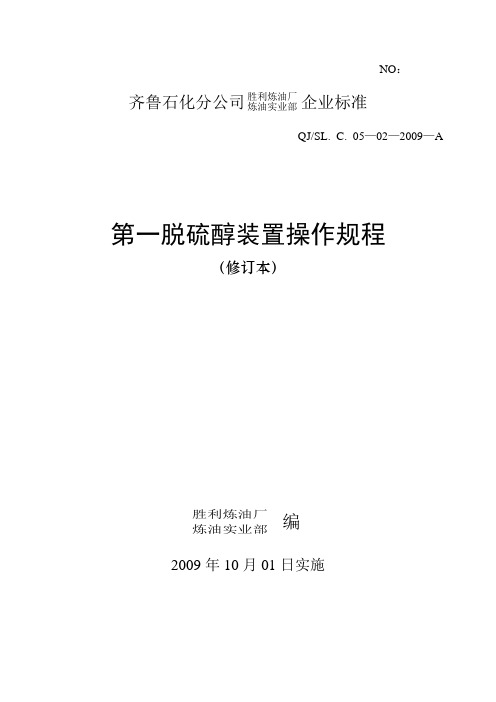
NO :齐鲁石化分公司 企业标准QJ/SL. C. 05—02—2009—A第一脱硫醇装置操作规程(修订本)编2009年10月01日实施胜利炼油厂炼油实业部 胜利炼油厂 炼油实业部质量管理体系文件审批表单位:编号:目录第一部分工艺手册汽油无碱脱臭装置生产工艺手册第一章基本知识 (1)第一节轻质油产品脱硫醇的意义 (1)第二节脱硫醇工艺的发展 (1)第三节Merox法脱硫醇工艺原理 (1)第四节基本概念 (2)第二章装置概况 (5)第一节工艺流程概述 (5)第二节装置设备明细 (8)第三节主要设备结构介绍 (10)第四节原料、产品及化工原料性质及要求 (11)第五节工艺、质量、技术经济指标 (12)液态烃脱硫醇装置工艺手册第一章基本知识 (15)第一节轻质油产品脱硫醇的意义 (15)第二节脱硫醇工艺的发展 (15)第三节Merox法脱硫醇工艺原理 (15)第四节基本概念及计算 (16)第二章装置概况 (18)第一节工艺流程说明 (18)第二节设计基础数据 (20)第三节装置设备 (21)第四节原材料性质、工艺操作指标及产品质量指标 (22)第五节化验分析项目及分析方法 (23)生产管理制度及安全知识 (26)第一节公司关于安全生产的部分禁令和规定 (26)第二节有关安全规定 (27)两脱装置“三废”排放量及环境保护措施 (29)第二部分岗位操作法第一章汽油脱硫醇岗位 (31)第一节岗位操作法 (31)第二节工艺参数分析 (32)第三节不正常现象及事故处理 (34)第二章液态烃脱硫醇岗位 (40)第一节岗位操作法 (40)第二节不正常现象及事故处理 (46)液态烃装置工艺技术卡片 (54)汽油碚硫醇装置工艺技术卡片 (55)第三部分开、停工方案第一节汽油碚硫醇装置开工方案 (56)第二节汽油碚硫醇装置停工方案 (64)第三节液态烃碚硫醇装置开工方案 (68)第三节液态烃碚硫醇装置停工方案 (74)工艺手册岗位操作法开、停工方案汽油无碱脱臭装置生产工艺手册第一章 基本知识第一节 轻质油产品脱硫醇的意义石油产品的硫醇是气味恶臭难嗅的有机化合物之一,空气中含l×l0-8g /L 的低分子量硫醇,人们即可嗅出。
炼油化工中气体脱硫技术探分析

炼油化工中气体脱硫技术探分析目前,由于我国经济在飞速发展,炼油化工厂也在加快发展。
炼油化工生产过程中,气体脱硫技术的不断完善和发展,促进炼油化工企业的进步。
对气体脱硫技术措施进行优化,使其达到更高的标准,满足炼油化工企业生产的需要。
有必要研究炼油化工中气体脱硫的技术措施,达到环境保护的效果,而且有效地防止设备的腐蚀,提高炼油化工生产的经济效益。
标签:炼油化工;气体;脱硫技术引言工业生产是产生空气污染的主要原因,特别是炼油化工生产中的含硫气体对空气和环境有严重的污染,甚至会危害人们的身体健康,因此要解决炼油化工的含硫气体污染问题。
在炼油化工生产中采用气体脱硫技术可以有效地去除炼油化工中的硫化氢,起到保护环境和提高炼油化工经济效益的目的。
1目前脱硫技术概述炼油过程中的脱硫技术一直是国内炼油厂家和相关研究院所的研究重点,随着国内国际对于汽油、柴油的技术指标的提高,对汽油等油品种的脱硫技术研究比较主要有以下几个方面:(一)FCC汽油加氢脱硫技术采用传统的进行脱硫转化时,轻烃汽油馏分经常容易被饱和,导致石油中的烯烃很容易被饱和,导致汽油中的辛烷降低。
Mobil公司的OCTGAIN技术,能控制其中的硫含量的同时,还能够控制辛烷值。
(二)溶剂萃取脱硫技术该技术是利用萃取溶剂,通常用甘醇类和砜类溶剂作萃取剂,通过萃取,将硫化物转化到高沸点溶剂中,再经过蒸馏的方式将汽油分离,最后将萃取溶剂与硫化物分离,抽提出来的硫化物,主要是苯并噻吩和甲基苯并噻吩,这些硫化物可以作为化工产品的原料或中间产物使用,从而减少了环境污染。
(三)催化裂化脱硫技术Grace公司提出的直接减少催化裂化汽油硫含量的新催化技术,称为GSR技术。
目前应用的技术,是在第一代技术的基础上添加了含有锐钛矿型结构的TiO2组元而制得,主要组分为TiO2/Al2O3。
该技术的应用,可使汽油馏分中的硫含量降低20%~30%。
2炼油化工中气体脱硫技术措施2.1化学脱硫剂脱硫工艺技术措施的应用结合炼油化工生产的实际情况,选择最佳的化学脱硫剂,应用脱硫塔设备,结合再生塔,对脱硫剂进行再生利用,降低脱硫工艺的成本,满足炼油化工生产节能降耗的技术要求。
石油脱硫工艺流程

石油脱硫工艺流程概述石油脱硫是一项重要的工艺,旨在降低石油中含硫化合物的浓度,以提高石油的质量和环境可接受性。
本文将详细介绍石油脱硫的工艺流程以及相关的技术细节。
工艺流程石油脱硫通常包括以下几个主要步骤:1. 预处理在石油脱硫之前,通常需要对原油进行预处理。
这一步骤的目的是去除石油中的杂质和水分,以减少对后续脱硫工艺的影响。
•原油在进入预处理阶段时,首先通过沉淀和过滤来去除悬浮颗粒物和固体杂质。
•接下来,原油需要被加热以分离其中的水分。
常用的方法是在加热过程中注入蒸汽或使用加热器。
•最后,通过第三次沉淀将油中的水分进一步去除。
2. 硫化物转化在预处理之后,石油进入硫化物转化阶段。
这一步骤旨在将硫化物转化为易于去除的形式。
•首先,将催化剂注入到石油中,以加速硫化物的转化过程。
常用的催化剂包括氢化铝和钠。
•在加热的条件下,硫化物会与催化剂发生反应,生成硫化物的易于去除的形式,如硫化钠。
•这一转化过程需要在高压和高温环境下进行,以提高反应速率和转化效率。
3. 吸收剂处理硫化物转化后,石油进入吸收剂处理阶段。
这一步骤旨在去除石油中的硫化物。
•吸收剂通常选择具有高选择性和吸附能力的物质,如碱性溶液、氨水或酸性氧化物。
•石油与吸收剂接触,硫化物以化学反应的形式被吸附到吸收剂表面。
•重新加热吸收剂,使其继续可用于后续的硫化物吸附。
4. 再生吸收剂处理后,石油中的硫化物被成功去除。
然而,吸收剂中的硫化物达到一定浓度后,需要进行再生。
•再生通常通过多级加热和蒸馏来实现。
首先,将吸收剂加热至高温,以驱除其中的硫化物。
•接下来,通过蒸馏将硫化物从冷却的吸收剂中分离出来。
•结果是得到一种含高浓度硫化物的流体,常被称为“硫化剂废液”。
技术细节石油脱硫工艺中的一些关键技术细节包括以下几点:1. 选择适当的催化剂催化剂的选择对于脱硫工艺的效果至关重要。
不同类型的原油和硫化物需要使用不同的催化剂。
2. 控制温度和压力温度和压力对于脱硫工艺的效果有着重要影响。
石油化工厂里的工艺-催化汽油选择性加氢脱硫醇技术

催化汽油选择性加氢脱硫醇技术(RSDS技术)
催化汽油加氢脱硫醇装置的主要目的是拖出催化汽油中的硫含量,目前我国大部分地区汽油执行国三标准,硫含量要求小于150ppm,烯烃含量不大于30%,苯含量小于1%。
在汽油加氢脱硫的过程中,烯烃极易饱和,辛烷值损失较大,针对这一问题,石科院开发了RSDS技术。
本技术的关键是将催化汽油轻重组分进行分离,重组分进行加氢脱硫,轻组分碱洗脱硫。
采取轻重组分分离的理论基础是,轻组分中烯烃含量高,可达到50%以上,通过直接碱洗,辛烷值几乎不损失。
而重组分中烯烃大多是环烯烃,经过加氢后变为环烷烃,辛烷值几乎不损失,导致重组分加氢辛烷值损失的是C7以上单烯烃和双烯烃饱和,但以上两种物质所占比例较小,正常情况下重组分加氢后辛烷值损失在1.5以内。
RSDS技术的另一个优点是设立了两个反应器,第一个反应器在低温高空速下操作,目的是将二烯烃饱和成单烯烃,防止在高温反应条件下二烯烃聚合生胶,可以延长装置运转周期。
60万吨汽油选择性加氢
P7202E7204E7204E7207。
石油脱硫技术
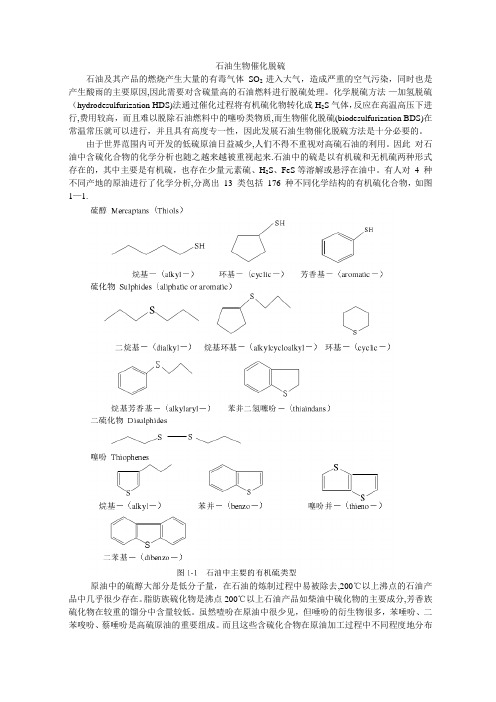
石油生物催化脱硫石油及其产品的燃烧产生大量的有毒气体SO2进入大气,造成严重的空气污染,同时也是产生酸雨的主要原因,因此需要对含硫量高的石油燃料进行脱硫处理。
化学脱硫方法-—加氢脱硫(hydrodesulfurization HDS)法通过催化过程将有机硫化物转化成H2S气体,反应在高温高压下进行,费用较高,而且难以脱除石油燃料中的噻吩类物质,而生物催化脱硫(biodesulfurization BDS)在常温常压就可以进行,并且具有高度专一性,因此发展石油生物催化脱硫方法是十分必要的。
由于世界范围内可开发的低硫原油日益减少,人们不得不重视对高硫石油的利用。
因此对石油中含硫化合物的化学分析也随之越来越被重视起来.石油中的硫是以有机硫和无机硫两种形式存在的,其中主要是有机硫,也存在少量元素硫、H2S、FeS等溶解或悬浮在油中。
有人对4 种不同产地的原油进行了化学分析,分离出13 类包括176 种不同化学结构的有机硫化合物,如图1—1.原油中的硫醇大部分是低分子量,在石油的炼制过程中易被除去,200℃以上沸点的石油产品中几乎很少存在。
脂肪族硫化物是沸点200℃以上石油产品如柴油中硫化物的主要成分,芳香族硫化物在较重的馏分中含量较低。
虽然喳吩在原油中很少见,但唾吩的衍生物很多,苯唾吩、二苯唆吩、蔡唾吩是高硫原油的重要组成。
而且这些含硫化合物在原油加工过程中不同程度地分布于各馏分油中。
在流化床催化裂化(Fluldeaatlyti.。
arkce,Fcc)汽油中,唆吩和各种取代唆吩是主要的含硫化合物,其中苯并唾吩(BeZnohtiophene,BTH)占30%。
催化柴油馏分中的含硫化合物主要是BHT和二苯并唆吩(Dibenzothi0Phene,DBT)及各种烷基取代物.随着唾吩类含硫化合物的环数的增加,多环唾吩因空间位阻效应使加氢脱硫催化剂反应活性迅速降低。
从炼油角度来看,非活性硫的化合物一般比活性硫的化合物更难脱除,而原油中的硫大部分都是以硫醚类和噻吩类硫的形态存在于沸点较高的石油馏分中,这是含硫原油加工过程中所面临的主要问题。
dds催化剂脱硫新技术及工业应用
dds催化剂脱硫新技术及工业应用DDS催化剂脱硫新技术及工业应用随着环保要求的不断提高,石油炼制和化工行业对硫含量的控制越来越严格。
传统的脱硫技术主要包括吸附法、氧化法、生物法等,但这些方法存在处理效果不理想、成本较高、副产物处理困难等问题。
因此,开发新型高效、低成本的脱硫技术成为了当前的研究热点。
DDS催化剂脱硫新技术应运而生,其在工业应用中取得了显著的成果。
一、DDS催化剂脱硫新技术简介DDS催化剂脱硫新技术是一种基于催化剂的湿式氧化脱硫技术,其核心是利用催化剂将硫化物转化为二氧化硫和水,从而实现脱硫的目的。
DDS催化剂具有高活性、高选择性和高稳定性等优点,能够在短时间内实现高效的脱硫效果。
此外,DDS催化剂还具有较好的抗硫中毒能力,能够在较宽的温度和压力范围内稳定工作。
二、DDS催化剂脱硫新技术的原理DDS催化剂脱硫新技术的基本原理是在一定的温度和压力条件下,利用催化剂将硫化物氧化为二氧化硫和水。
在这个过程中,催化剂起到了催化作用,降低了反应的活化能,提高了反应速率。
同时,催化剂还能够选择性地将硫化物转化为二氧化硫,避免了其他副反应的发生。
三、DDS催化剂脱硫新技术的优势1. 高效:DDS催化剂具有较高的催化活性,能够在短时间内实现高效的脱硫效果。
与传统的脱硫技术相比,DDS催化剂脱硫新技术的处理效率更高,能够满足严格的环保要求。
2. 低成本:DDS催化剂具有较高的选择性和稳定性,能够在较宽的温度和压力范围内稳定工作。
这使得DDS催化剂脱硫新技术在实际应用中具有较低的运行成本,有利于降低企业的生产成本。
3. 环保:DDS催化剂脱硫新技术产生的副产物主要是水和二氧化碳,对环境无污染。
此外,DDS 催化剂还具有较好的抗硫中毒能力,能够减少硫资源的浪费。
4. 安全:DDS催化剂脱硫新技术采用湿式氧化法进行脱硫,避免了高温、高压等危险条件,具有较高的安全性。
四、DDS催化剂脱硫新技术的工业应用近年来,DDS催化剂脱硫新技术在石油炼制和化工行业的工业应用中取得了显著的成果。
氨法脱硫技术装备在石油炼制过程中的应用研究
氨法脱硫技术装备在石油炼制过程中的应用研究氨法脱硫技术是一种常用的烟气脱硫技术,广泛应用于石油炼制过程中。
该技术通过在烟气中喷入氨水,使氨水与烟气中的二氧化硫反应生成氨硫水溶液,从而达到脱硫的目的。
本文将介绍氨法脱硫技术装备在石油炼制过程中的应用研究。
首先,氨法脱硫技术在石油炼制过程中的应用主要包括石油炼厂的脱硫装置和炼油炉的脱硫装置。
石油炼厂的脱硫装置一般采用脱硫塔,烟气通过脱硫塔时与喷入的氨水反应,生成氨硫水溶液。
而炼油炉的脱硫装置主要包括炉顶脱硫和废气烟囱脱硫两种方式。
炉顶脱硫是通过在炉顶处喷入氨水,使氨水与燃烧产生的二氧化硫反应,达到脱硫的目的。
废气烟囱脱硫是在废气烟囱中喷入氨水,将二氧化硫转化为硫酸气态化合物,达到脱硫的目的。
其次,氨法脱硫技术装备的研究主要包括脱硫塔结构和喷射装置的优化。
脱硫塔结构的优化可以通过改变塔床的形状和粒径,提高氨水与烟气的接触效果,增加反应的有效面积,提高脱硫效率。
喷射装置的优化可以通过改变喷射位置和角度,使氨水均匀喷洒到烟气中,提高反应的均匀性,减少反应的死角,提高脱硫效率。
此外,还可以根据石油炼制过程中的实际情况,对氨水的喷射量和浓度进行调整,以达到最佳脱硫效果。
最后,氨法脱硫技术装备在石油炼制过程中的应用研究还包括脱硫效果的评价和增效方法的研究。
脱硫效果的评价可以通过测量烟气中二氧化硫的浓度,计算脱硫效率和脱硫速度,从而评估脱硫装置的性能。
增效方法的研究可以通过改变反应条件,如温度、压力和氨溶液的浓度,以及添加助剂等方式,提高脱硫效果。
总之,氨法脱硫技术装备在石油炼制过程中的应用研究包括脱硫装置和喷射装置的优化,脱硫效果的评价和增效方法的研究等方面。
这些研究可以提高脱硫装置的性能,实现对石油炼制过程中产生的二氧化硫的有效脱除,保护环境,减少大气污染。
同时,这些研究也为石油炼厂提供了参考,以确保其脱硫装置的正常运行和高效脱硫。
石油加工中的脱硫脱氮工艺技术
石油加工中的脱硫脱氮工艺技术在石油加工中,脱硫脱氮工艺技术扮演着至关重要的角色。
随着环境保护意识的增强,对燃料的污染物排放要求也越来越严格,特别是对硫和氮的排放控制。
为了满足这些要求,石油加工行业积极探索和应用各种脱硫脱氮工艺技术,以减少环境污染,改善空气质量。
一、脱硫技术1.吸收法吸收法是最常见的脱硫技术之一。
其原理是利用吸收剂,如氨水、碱溶液等,在气相和液相之间进行气体吸收和气液反应。
这种方法能有效地从燃料中去除硫化物,减少二氧化硫的排放。
常用的吸收法脱硫工艺有胺法和碱吸收法。
2.氧化法氧化法是通过氧化剂氧化硫化物,使其转化为更易于去除的氧化产物。
常用的氧化法包括氧化吸附法和氧化催化法。
其中,氧化吸附法利用氧化剂将硫化物氧化成二氧化硫,并通过吸附剂吸附去除。
氧化催化法则是在催化剂的作用下,将硫化物氧化成二氧化硫,然后通过吸附剂进行去除。
二、脱氮技术1.选择性催化还原法选择性催化还原法是目前最常用的脱氮技术。
该技术利用催化剂将氮氧化物还原成氮气,从而达到脱氮的目的。
常用的催化剂有铈铁、钴钼等。
选择性催化还原法具有脱氮效率高、能耗低等优点。
2.吸附法吸附法是利用吸附剂从燃料中吸附氮氧化物,然后再进行再生或者处理。
吸附剂通常选择活性炭、分子筛等材料。
该方法具有简单易行、处理效果稳定等优点,但需要定期更换吸附剂。
三、脱硫脱氮技术的应用脱硫脱氮技术已广泛应用于石油加工领域,特别是在石油炼制、天然气加工和燃煤电厂等领域。
这些技术的应用不仅可以降低环境污染,减少大气二氧化硫和氮氧化物的排放,还能够改善空气质量,保护生态环境。
在石油炼制过程中,通过脱硫脱氮技术可以有效地去除原油中的硫和氮杂质,提高燃油质量,减少污染物排放。
在天然气加工过程中,脱硫脱氮技术可以提高天然气质量,保护管道设备的使用寿命。
在燃煤电厂中,使用脱硫脱氮技术可以降低燃料中的硫和氮含量,减少燃煤产生的大气污染物。
综上所述,脱硫脱氮工艺技术在石油加工中的重要性不言而喻。
石油油品脱硫技术综述
存 在 着 催 化 剂投 资 大 、 制 备 条 件 苛 刻 、 常 压 下利 用需 氧菌 、厌 氧 菌 除去 石 油含
硫 杂 环化 合 物 中 结 合 硫 。早 在 1 4 8年 资较 少 , 催 化 加氢 难 以脱 除 的苯 并噻 9 对
美 国就 有 了生 物脱 硫 的专 利 ,但 一 直没 吩 类化 合 物有 较 高 的脱 硫 效 率 , 一 项 是
进 行 处 理 ,可 除 去 硫 醇 。金 属 螯 合 剂 是 对重 组分 中的聚芳烃 硫杂 环不起作 用 法 和 酸 性 催 化 剂 法 都 能 使 有 机 硫 化 物 () s存在会 毒害脱 硫系统 的催化 剂 。 4
料 油深 度 脱 硫 的 有效 方 法 。 氧 化脱 硫
氧 化 脱 硫 (O ) 为 近 年 来 发 展 O S 作
存 在 的 问 题 :()加 氢 脱 硫 反 应 热 量 。美 国 E C公 司不 仅 成 功 多放 术 生 产 的 由于 柴 油 中 的 二 甲基 二 苯
并 噻 吩 结 构 稳 定 不 易 加 氢 脱 硫 .为 了 的 操 作 温 度 通 常 为 2 0~ 4 0。 7 2 C.较 再 生 了生 物 脱硫 催 化 剂 并 在 降低 催 化 使 油 品 中的硫 含 量 降 到 1 9 9.需 要 0 / 高 的 操 作 温 度 可 降 低 产 品 中 的 硫 含 剂 生产 成 本 的 同 时也 延 长 了催 化 剂 的寿 更 高 的反 应 压 力 和 更 低 的 空 速 这 无 量 , 但 是 会 缩 短 催 化 剂 寿 命 , 提 高 命 。此 外 该 公 司 又 分 离 得 到 了玫 鸿 球 疑 增 加 了 加 氢 技 术 的 投 资 费 用 和 生 产 成 本 费 用 。 () 汽 油 加 氢 脱 硫 的 操 菌 的 细 菌 ,该 细 菌 能 够 使 C 2 -S键 断裂 成 本 。 而 氧 化 脱 硫 技 术 不 仅 可 以 满 足
- 1、下载文档前请自行甄别文档内容的完整性,平台不提供额外的编辑、内容补充、找答案等附加服务。
- 2、"仅部分预览"的文档,不可在线预览部分如存在完整性等问题,可反馈申请退款(可完整预览的文档不适用该条件!)。
- 3、如文档侵犯您的权益,请联系客服反馈,我们会尽快为您处理(人工客服工作时间:9:00-18:30)。
矿产资源开发利用方案编写内容要求及审查大纲
矿产资源开发利用方案编写内容要求及《矿产资源开发利用方案》审查大纲一、概述
㈠矿区位置、隶属关系和企业性质。
如为改扩建矿山, 应说明矿山现状、
特点及存在的主要问题。
㈡编制依据
(1简述项目前期工作进展情况及与有关方面对项目的意向性协议情况。
(2 列出开发利用方案编制所依据的主要基础性资料的名称。
如经储量管理部门认定的矿区地质勘探报告、选矿试验报告、加工利用试验报告、工程地质初评资料、矿区水文资料和供水资料等。
对改、扩建矿山应有生产实际资料, 如矿山总平面现状图、矿床开拓系统图、采场现状图和主要采选设备清单等。
二、矿产品需求现状和预测
㈠该矿产在国内需求情况和市场供应情况
1、矿产品现状及加工利用趋向。
2、国内近、远期的需求量及主要销向预测。
㈡产品价格分析
1、国内矿产品价格现状。
2、矿产品价格稳定性及变化趋势。
三、矿产资源概况
㈠矿区总体概况
1、矿区总体规划情况。
2、矿区矿产资源概况。
3、该设计与矿区总体开发的关系。
㈡该设计项目的资源概况
1、矿床地质及构造特征。
2、矿床开采技术条件及水文地质条件。