液化石油气深度脱硫技术探讨
石油加工中的脱硫技术

石油加工中的脱硫技术脱硫技术在石油加工中起着重要的作用。
随着环境保护意识的增强,减少二氧化硫排放已成为石油行业的重要任务。
本文将探讨石油加工中常用的脱硫技术,并分析其原理和应用。
一、湿法脱硫技术湿法脱硫技术是目前石油加工中广泛应用的一种方法。
在湿法脱硫中,通过将石油中含有的硫化物与一种溶剂反应,使硫化物转化为可溶性的形式并从石油中移除。
这种技术可以同时去除硫和氮等杂质。
湿法脱硫技术中最常用的方法是氧化脱硫。
在这种方法中,石油经过一系列的处理,使其酸性增加,然后通过与空气中的氧气反应,将硫化物氧化为硫酸盐。
最后,硫酸盐与水反应形成硫酸,从而实现脱硫的目的。
二、干法脱硫技术干法脱硫技术是另一种在石油加工中使用的脱硫方法。
与湿法脱硫不同,干法脱硫不需要使用溶剂,而是通过物理化学反应直接去除石油中的硫化物。
干法脱硫技术中,最常用的方法是选择性吸附。
在这种方法中,石油经过特殊的吸附剂,硫化物会被吸附剂选择性地吸附,从而实现脱硫的目的。
这种方法能够高效地去除硫化物,并且不会引入额外的溶剂,因此在石油加工中得到了广泛应用。
三、生物脱硫技术生物脱硫技术是一种新兴的脱硫方法,其原理是利用特定微生物对硫化物进行降解。
这种方法具有环保、经济和高效的特点,在石油加工中越来越受到关注。
生物脱硫技术中,最常用的方法是利用硫氧化细菌进行脱硫。
这些细菌能够通过代谢过程将硫化物转化为硫酸盐,并从石油中除去。
利用生物脱硫技术不仅可以减少二氧化硫的排放,还可以降低工艺过程中的能耗和废物产生。
四、新兴脱硫技术除了传统的湿法脱硫、干法脱硫和生物脱硫技术,还有一些新兴的脱硫技术在石油加工中逐渐兴起。
这些技术包括离子液体脱硫、高温煤气脱硫以及催化剂脱硫等。
离子液体脱硫技术是利用特殊的离子液体作为溶剂,将硫化物溶解并从石油中去除。
这种方法具有高效率和可再生性的特点,被认为是一种可持续发展的脱硫技术。
高温煤气脱硫技术是将石油加工中产生的高温煤气与一种脱硫剂反应,使硫化物转化为硫酸盐并从煤气中去除。
TS-1型液化石油气常温精脱硫剂的性能研究

随着我国进口高硫含量原油量的增加,从原油中分离出的液化石油气中硫化物含量、结构和分布都有较大变化,传统的液化气脱硫工艺,往往达不到精脱硫要求,脱后液化石油气硫化物含量仍偏高,铜片腐蚀严重超标,影响产品质量和生产系统安全以及造成很大的环境污染。
液化石油气的脱硫方法和技术有很多种,包括:干法脱硫,湿法脱硫,膜分离脱硫,生物脱硫,电子束照射法及微波法脱硫等。
各种脱硫方法都有各自的特点、优点和缺陷,但在液化石油气的脱硫中,需要找到脱硫效果最好,工艺简单,脱硫成本较低的方法。
目前有很多研究报道了液化石油气的脱硫方法及技术或者脱硫剂的研究。
杨云平[1]介绍了HB5-l、HB5-3(DS-1)精脱硫剂在液化气中的工业应用情况。
结果表明,该脱硫剂脱硫效果很好,使液化气的铜片腐蚀从3级降至l级,总硫明显下降。
开发和合成新型的脱硫剂是目前对液化石油气脱硫的工作重点。
本文应用湖北省化学研究所开发出的TS-1型转化吸收精脱硫剂进行实验研究。
该脱硫剂以大孔结构为主,兼顾大量发达的微孔,并添加有助催化剂和活性促进剂。
TS-1型精脱硫剂在常温液相条件下对COS、硫醇有极强的转化吸收能力,同时对H2S、元素硫又具有优良的脱除性能,成本却有大幅降低,T S-1型精脱硫剂物化性能见表1。
表1TS-1型精脱硫剂物化性能1.实验部分1.1试验流程液化石油气原料以试验需求量的H2S、C OS、元素硫和甲硫醇等硫化物与液化石油气(经WK-2D总硫分析仪检验总硫小于0.01mg/m3)按一定比例混合均匀后配制而得。
原料经减压阀进入反应器,反应后尾液经过汽化器后,再经流量计、燃烧器、碱液吸收装置后放空。
在脱硫反应器前后均有取样点,以检测硫化物含量、种类和铜片腐蚀情况。
1.2试验条件试验原料所用液化石油气中丙烷、丁烷体积含量≥96%,戊烷及戊烷以上组分体积含量≤2%,O2<5mg/m3,H2O≤1000mg/m3,H2S、元素硫、COS、甲硫醇按实验要求配入。
液化石油气脱硫工艺概述
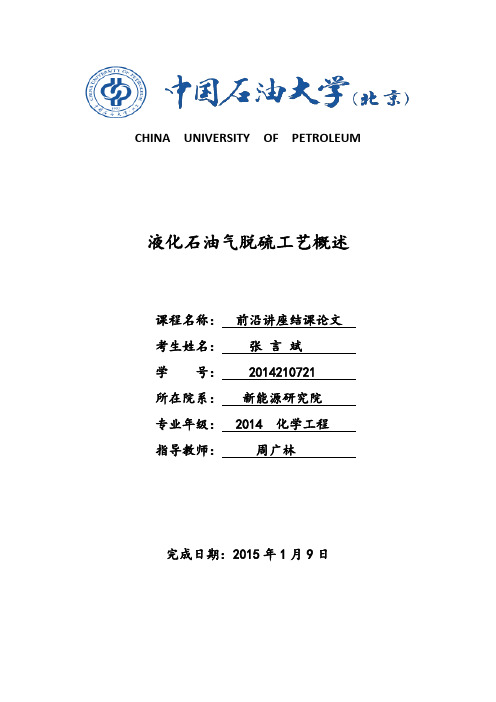
CHINA UNIVERSITY OF PETROLEUM 液化石油气脱硫工艺概述课程名称:前沿讲座结课论文考生姓名:张言斌学号: 2014210721 所在院系:新能源研究院专业年级: 2014 化学工程指导教师:周广林完成日期:2015年1月9日前沿讲座结课论文摘要液化石油气的杂质中除含有H2S和CO2等酸性组成外,还含有硫醇、硫醚、二甲基二硫醚、CS2等有机硫,这些硫的存在会对下游产品加工、环境保护和设备防腐蚀等方面造成非常不利的影响。
因此,液化石油气的脱硫及其硫化物的检测是液化石油气生产与检测中的重要环节。
脱除硫化物的方法和技术日渐发展和成熟,液化石油气脱硫的方法很多,在工业上应用的主要有湿法和干法两大类[1],近年来又发展了液膜脱硫技术,分子筛吸附脱硫,ThiolexSM技术,催化氧化-吸附结合法,等离子体法,生物脱硫法[2],电子束照射法和微波法等[3]。
关键词:液化石油气;含硫物;脱硫工艺;液化石油气主要来源于炼油厂催化裂化、延迟焦化、常减压、加氢裂化、连续重整等装置,其主要组分是C3和C4烃及少量C2和C5烃类,还含有硫化氢(质量浓度约0.01%~4%)、硫醇(质量浓度约1~9000mgS/Nm3)、硫醚(质量浓度0~100mgS/Nm3),COS 等硫化物。
常减压、加氢裂化、连续重整装置的液化气因烯烃含量少,大部分是丙烷、丁烷等饱和烃。
如果作为民用液化气,则精制后的总硫质量浓度满足不大于343 mgS/Nm3产品质量标准即可;如果作为下游装置的化工原料,如生产丙烷、正丁烷、异丁烷等,则总硫质量浓度通常控制在100 mgS/Nm3以下,越低越好;催化裂化、焦化装置产的液化气因含有高附加值的丙烯、异丁烯,为满足气体分离装置分离丙烯、丙烷和C4,必须将精制液化气总硫质量浓度脱除至小于100 mgS/Nm3以下[4]。
由以上产品的质量标准可以看出,液化石油气的脱硫是液化石油气净化精制工艺中极为重要的步骤,液化石油气的脱硫工艺也成了研究、探索、优化的重点。
液化气脱硫技术交流28页PPT

▪
30、意志是一个强壮的盲人,倚靠在明眼的跛子肩上。——叔本华
谢谢!
28
液化气脱硫技术交流
51、没有哪个社会可以制订一部永远 适用的 宪法, 甚至一 条永远 适用的 法律。 ——杰 斐逊 52、法律源于人的自卫本能。——英 格索尔
53、人们通常会发现,法律就是这样 一种的 网,触 犯法律 的人, 小的可 以穿网 而过, 大的可 以破网 而出, 只有中 等的才 会坠入 网中。 ——申 斯通 54、法律就是法律它是一座雄伟的大 夏,庇 护着我 们大家 ;它的 每一块 砖石都 垒在另 一块砖 石上。 —·伯顿
▪
26、要使整个人生都过得舒适、愉快,这是不可能的,因为人类必须具备一种能应付逆境的态度。——卢梭
▪
27、只有把抱怨环境的心情,化为上进的力量,才是成功的保证。——罗曼·罗兰
▪
28、知之者不如好之者,好之者不如乐之者。——孔子
▪
29、勇猛、大胆和坚定的决心能够抵得上武器的精良。——达·芬奇
干气与液化气系统脱硫工艺的探讨
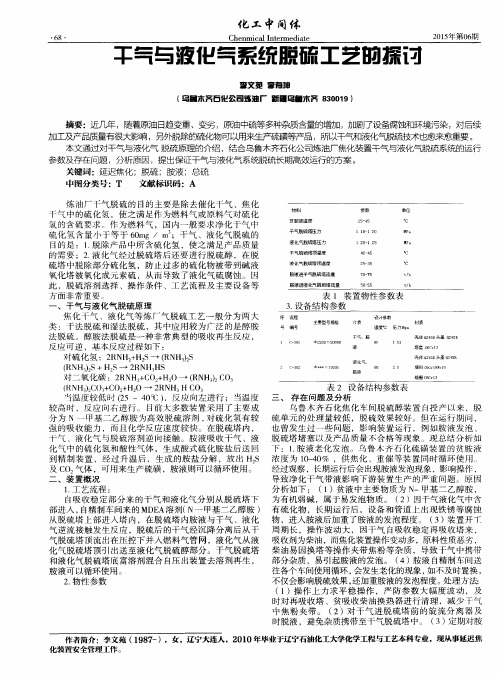
表 2 设备结构参数表 三、 存在 问题及分析 乌鲁 木齐石化焦 化车间脱硫 醇装 置 自投 产以来 ,脱 硫 单元 的处 理量较低 ,脱 硫效果较好 。但在运行 期问 , 也 曾发生过 一些 问题 ,影 响装置运行 ,例如胺 液发泡 、 脱硫 塔堵塞 以及产 品质量 不合格等现 象。现总结分 析如 下 :1 . 胺液 老化发泡 。乌鲁 小齐石 化硫磺装 置 的贫 胺液 浓度为 1 0 — 4 0 % ,供 焦化 、重催 等装 置同时循 环使用 。 经过观察 ,长期运行后会 出现胺液发泡现象 , 影 响操作 , 导致净化干气 带液影 响下游装置生产 的严重 问题 。原因 分析如下 : ( 1 )贫液 中主要物质为 N 一甲基 二乙醇胺 , 为有机弱碱 ,属于易发泡物质。 ( 2 )因干气液化气 中含 有硫化物 ,长 期运行后 ,设备 和管道 上出现铁锈等 腐蚀 物 ,进入胺 液后加 重了胺 液的发泡程度 。 ( 3 )装置开 T 周期长 ,操作 波动大 ,因干气 自吸 收稳定再 吸收塔来 , 吸收剂为柴油 ,而焦化装置操作变动多 ,原料性质恶劣 , 柴油易 因换塔 等操作 夹带焦粉等 杂质 ,导致干气 中携带 部分杂质 ,易引起胺 液的发泡。 ( 4 )胺液 自精制车间送 往各个车间使用循环 , 会发生老化 的现象 , 如不及时置换 , 不仅会影响脱硫效果 , 还加重胺 液的发泡程度。 处理方法 ( 1 )操 作上 力求 平稳操 作 ,严 防参数 大幅 度波 动 ,及 时对再 吸收塔 、贫 吸收柴油换热器 进行清理 ,减少 下气 中焦 粉 夹带 。 ( 2 )对 干气 进脱 硫塔 前 的旋流 分离 器 及 时脱液 ,避免杂质携带至干气脱硫塔 中。 ( 3) 定期对胺
化 工 中 间体
・
68 ・
2 0 1 5 年第0 6 期
环保型液化气深度脱硫LDS技术的开发与应用

11 液 化 气 脱 硫 醇 的 主 要 问 题 分 析 液化气 碱 洗 脱 硫 醇 过 程 一 般 包 括 碱 洗 抽 提、
收 稿 日 期 :20180507。 作者简介:胡雪生,博士,高级工程师,从 事 轻 烃 加 工 技 术 研 究
与开发工作。 通 讯 联 系 人 :高 飞 ,Email:gaofei@petrochina.com.cn。 基金项目:中国石 油 天 然 气 股 份 有 限 公 司 合 同 项 目 (2013B
中国石油石油化工研究院在深入研究常规液化 气 脱硫 醇工 艺 存 在 问 题 的 基 础 上 ,将 超 重 力 分 离 技 术 与碱 洗脱 硫 醇 技 术 相 结 合,开 发 了 以 超 重 力 法 循 环碱液再生为核心工艺的环保型液化气深度脱硫成 套技术(简称 LDS技术)[8]。该技术于2014年12月 在中国石油某石化公司0.30 Mt?a液化气脱硫醇装 置 首 次 工 业 应 用 成 功 。 截 至 2018 年 5 月 ,该 技 术 共 在7家石化企业实现工业应用或推广。本文主要介 绍 LDS技术的开发过程及工业应用情况。
23050302)。
12
石 油 炼 制 与 化 工 2018年 第49卷
Hale Waihona Puke 碱液再生、二硫化物分 离 3 个 步 骤,分 别 涉 及 到 如
下化学反应:
RSH+NaOH 幑幐NaSR+H2O
(1)
4NaSR+O2+2H2O →2RSSR+4NaOH (2)
反应(1)发生在 碱 洗 抽 提 阶 段,为 酸 碱 中 和 快
关 键 词 :液 化 气 脱 硫 醇 碱 渣 超 重 力
精制液化 气可 广 泛应用 于生产 高 附 加 值 产 品。目前,液 化 气 精 制 一 般 采 用 “胺 洗 法 ”脱 硫 化 氢和“碱洗 法”脱 硫 醇 相 结 合,其 中 “胺 洗 法”脱 硫 化氢的工 艺 较 为 成 熟,而 “碱 洗 法”脱 硫 醇 则 是 实 现 液 化 气 深 度 脱 硫 的 关 键。 美 国 UOP 公 司 开 发 的 Merox工艺是经典的液化气 或 轻石 脑油 碱洗 脱 硫 醇 技 术 ,已 工 业 应 用 近60 年 ,被 称 为 第 一 代 碱 洗 脱硫醇技术。美国 MeriChem 公司于1974年推出 的纤维膜脱硫醇工艺采用纤维膜接触器取 代 Mer ox工艺中的抽 提 塔,并 且 使 用 溶 剂 油 反 抽 提 替 代 二硫化物的重力沉 降 分 离,提 高 了 硫 醇 脱 除 效 率, 被称为第 二 代 碱 洗 脱 硫 醇 技 术。 目 前,这 两 种 工 艺是世界上 主 要 的 液 化 气 脱 硫 醇 工 艺,占 90% 以 上 ,但 共 同 的 缺 点 是 对 液 化 气 深 度 脱 硫 的 同 时 无 法 避免碱 渣 的 大 量 排 放[13]。一 般 地,对 于 一 套 0.30 Mt?a液 化 气 脱 硫 醇 装 置 ,如 果 控 制 产 品 液 化 气 的 硫 质量分数不大于10 g?g,采用传统 Merox工艺时产 生 的 碱 渣 量 在 800t?a以 上 ,采 用 纤 维 膜 脱 硫 醇 工 艺 时产生的碱渣量在300t?a以上。
液化气铜片腐蚀原因及脱硫技术研究现状
液化气铜片腐蚀原因及脱硫技术研究现状X刘海燕(西南石油大学化学化工学院,四川成都 610500) 摘 要:含硫液化气对环境、人体及下游化工生产等均会造成不良影响,如何高效经济地实现液化气脱硫是石化公司亟待解决的问题。
本文针对目前许多液化气铜片腐蚀不合格的现象,对液化气产生铜片腐蚀的原因进行了分析,在此基础之上,详细介绍了国内外常用的脱硫技术的使用条件、优缺点等,同时介绍了纤维膜脱硫法、络合脱除法、硫醇无碱转化组合技术等液化气脱硫新技术。
关键词:液化气;铜片腐蚀;脱硫;硫化氢 中图分类号:T E980.1 文献标识码:A 文章编号:1006—7981(2012)05—0090—02 随着石油化工业的发展,液化气作为一种新型燃料和化工原料,已经受到人们的高度重视。
用液化气作为燃料,由于其无炭渣、无烟尘、热值高,使用操作方便,已经广泛进入到人们的生活领域。
在化工生产方面,液化气经分离可以得到丁二烯、丁烯、丙烯、乙烯等,它们是生产合成纤维、合成塑料、合成橡胶以及生产染料、炸药、医药等产品的重要原料。
此外,液化气还可用于切割金属,用于工业窑炉焙烧和农产品烘烤等。
液化气中含硫,燃烧生成的二氧化硫是造成环境污染的主要原因,同时它也是产生酸雨的罪魁祸首。
二氧化硫对人体的肺部产生强烈的刺激作用,损伤肺部组织;二氧化硫能降低酶的活性,从而极大地影响蛋白质以及碳水化合物的代谢,损害肝脏功能。
此外,液化气中的硫化物还将进入到下游化工产品中,从而影响下游装置的安全生产。
含硫液化气对环境、人体及下游化工生产等均会造成不良影响,因此研究液化气脱硫技术具有重要意义。
铜片腐蚀是国家石化产品标准(GB 11174-1997)中液化气的一项非常重要的质量检测指标,目的是尽可能减小液化气在运输、储存以及使用过程中对铜部件的腐蚀。
国家石化产品标准中要求铜片腐蚀≤1级。
1 液化气铜片腐蚀不合格的影响因素要减小液化气对铜片的腐蚀,需要研究分析铜片腐蚀不合格的影响因素[1,2]:在常温常压条件下,单质硫能够与铜片直接发生反应,生成黑色的Cu2S,液化气中单质硫含量在0.5~1Lg/g 时,铜片腐蚀检验不合格。
双氧水给液化石油气脱硫反应-概述说明以及解释
双氧水给液化石油气脱硫反应-概述说明以及解释1.引言1.1 概述概述部分的内容可以参考如下:引言部分是对整篇文章的开篇介绍,目的是引起读者的兴趣并提供一些背景信息。
本文将详细讨论使用双氧水进行液化石油气脱硫反应的相关内容。
液化石油气脱硫是指从液化石油气中去除硫化物化合物的过程,目的是减少对环境和人体健康的影响。
硫化物化合物是液化石油气中普遍存在的污染物之一,它们在燃烧过程中会产生二氧化硫等有害物质,对大气和环境产生负面影响。
因此,液化石油气脱硫技术的研究和应用具有重要的理论和实际意义。
在液化石油气脱硫技术中,双氧水作为一种重要的催化剂和氧化剂得到了广泛的应用。
双氧水具有优异的氧化性能和催化活性,可以有效地将硫化物化合物转化为无毒的硫酸盐化合物。
因此,本文将重点讨论双氧水在液化石油气脱硫反应中的应用和作用机理。
本文的结构如下:首先,我们将介绍双氧水的性质和应用,包括其化学性质、反应特点以及在其他领域的应用情况。
接着,我们将探讨液化石油气脱硫的背景和需求,包括液化石油气中硫化物化合物的来源和对环境的影响。
最后,我们将总结双氧水在液化石油气脱硫中的作用,评估其优势和局限性,并展望未来可能的研究方向。
通过对双氧水在液化石油气脱硫反应中的研究和应用进行系统的总结和分析,有助于更好地理解和推动该领域的发展。
双氧水在液化石油气脱硫中具有潜在的应用前景,但也面临一些挑战和限制。
通过深入研究这一领域,我们可以进一步优化反应条件、提高脱硫效率,并为环境保护和可持续发展做出贡献。
1.2文章结构文章结构部分包括对整篇文章的组织和分章节的介绍。
在这篇文章中,我们将按照以下结构进行叙述:1. 引言1.1 概述:介绍液化石油气脱硫的背景和意义,同时提及双氧水在脱硫反应中的重要作用。
1.2 文章结构:简要说明本文的章节组织和内容安排,引导读者对整篇文章的概况有所了解。
1.3 目的:阐明本文的研究目的和意义,概括研究效果和观点的目标。
石油炼化企业烟气脱硫技术研究综述
石油炼化企业烟气脱硫技术研究综述石油炼化企业作为目前国民经济发展的主要支柱之一,其产生的废气排放一直是环境保护的重点关注对象。
烟气中的二氧化硫是其中的主要有害组分之一,对环境和人体健康都有着严重的危害。
石油炼化企业烟气脱硫技术一直备受关注和重视。
本文将对石油炼化企业烟气脱硫技术进行综述,介绍目前主流的烟气脱硫技术及其优缺点,并展望未来的发展方向。
一、烟气脱硫技术简介烟气脱硫技术是指通过一系列工艺手段将燃煤、燃油等燃料中的二氧化硫(SO2)转化成可容易吸收或易于分离的化合物,以减少其排放浓度的技术。
目前主流的烟气脱硫技术主要包括湿法脱硫和干法脱硫两大类。
湿法脱硫技术是利用吸收剂溶液(如石灰石浆液、石灰乳、碱液等)对烟气进行喷淋或浸润的方式,利用物理和化学吸收将二氧化硫吸附、转化为硫酸根离子,并通过沉淀或吸附等方式使其从烟气中剥离出来。
干法脱硫技术主要是指利用气固反应或气液反应的方式将烟气中的二氧化硫转化为易于分离的化合物,并进行除尘后将化合物和粉尘一并收集处理。
二、湿法脱硫技术1.石灰石法脱硫石灰石法脱硫是目前应用最广泛的湿法烟气脱硫技术之一。
其主要过程是将石灰石(CaCO3)与水混合成石灰石浆液,在吸收塔内与烟气进行接触,二氧化硫和氢氧化钙发生化学反应生成硫化钙。
化学反应方程式如下:CaCO3 + SO2 + 1/2 O2 + H2O → CaSO4·2H2O + CO2此反应生成的硫化钙会析出在吸收塔液体循环系统中形成硫石,随后通过沉淀和其他方式将其分离出来。
石灰石法脱硫技术具有工艺成熟、处理能力大、除硫效率高等优点,但同时也存在石灰石的消耗、废水处理等问题。
2.海水法脱硫此反应生成的硫酸钠会溶解在海水中,形成含硫酸钠的氯化钠溶液,在一系列处理后可将硫酸钠从溶液中结晶出来。
海水法脱硫技术相对于石灰石法脱硫具有更低的成本和更简化的工艺流程,但同时也存在对海水资源的开采和废水处理的问题。
宁夏交流-液化气脱硫(PPT)
17
二、宁夏石化液化气深度脱硫技术改造方案
6、新增或利旧改造设备表
序
名称
数量
备注
号
(台/具)
1
超重机
1
新增
2
碱液闪蒸罐
1
利旧
3
碱液缓冲罐
1
利旧改造
4
分液罐
1
新增
5
待生碱液过滤器2Fra bibliotek新增6
液体捕集器
1
新增
7
待生碱液泵
2
新增
8
循环碱液泵
2
新增
9
再生碱液泵
2
新增或核算利旧再
生碱液泵P-705
总工程费用768万元
创新了反应产物与原料的分离过程。由液液沉降分离变化为强制气提分 离,分离率由80%提高到98%,碱液中二硫化物残留量极少,反抽提进入液化 气的含量极低;
分离效率对比图
二 硫 化 物 分 离 率 wt %
(时间/月)
沉降罐
超重力机
6
一、液化气深度脱硫技术工业应用进展
创新点-3
集成优化了纤维膜抽提脱硫-超重力法碱液循环再生工艺。液化气脱后含硫 比改造前降低50%,碱液氧化再生突破了常规气液传质极限和二硫化物平衡溶 解度限制,新碱消耗和碱渣减少90%。
➢ 超重力法碱液循环再生技术的领先优势是:一步低成本地实现了液化气深度脱硫(5ppm)、
碱渣零排放和产品质量升级(MTBE硫含量20ppm)三重目标。
工艺流程和工业装置:
30万吨/年液化气脱硫醇 -超重力碱液再生装置
液化气脱硫醇-循环 碱液再生流程
新增部分
3
一、液化气深度脱硫技术工业应用进展
- 1、下载文档前请自行甄别文档内容的完整性,平台不提供额外的编辑、内容补充、找答案等附加服务。
- 2、"仅部分预览"的文档,不可在线预览部分如存在完整性等问题,可反馈申请退款(可完整预览的文档不适用该条件!)。
- 3、如文档侵犯您的权益,请联系客服反馈,我们会尽快为您处理(人工客服工作时间:9:00-18:30)。
2010年11月 炼油技术与工程 PETROLEUM REFINERY ENGINEERING 第40卷第1 1期
液化石油气深度脱硫技术探讨 孟庆飞郝天臻 中国石油化工股份有限公司沧州分公司(河北省沧州市061000)
摘要:为了解决MTBE产品总硫高的问题,在分析液化石油气中硫化物的形态、分布规律、现有脱硫精制技术 现状后,得出造成液化石油气精制后总硫偏高的原因是现有工艺的不足,用GL助溶法组合工艺精制液化石油气, 使产品MTBE总硫降低到50 txg/g。通过采用组合工艺,降低了液化石油气总硫含量,解决了MTBE总硫高的问题。
关键词:液化石油气深度脱硫脱硫醇COS MTBE 1 深度脱硫的必要性 炼油厂液化石油气主要来源于催化裂化和延 迟焦化装置,其中催化裂化液化石油气是生产丙 烯和MTBE的主要原料。近年来,随着对资源综 合利用不断加深的要求,焦化液化石油气也被作 为生产丙烯和MTBE的原料。在生产MTBE的过 程中,与甲醇一样,硫醇与异丁烯也能发生醚化反 应,同时还可能发生自醚化反应;再加上MTBE对 硫化物有比烃更高的溶解性,在MTBE与醚后碳四 蒸馏分离时,碳四原料中的硫化物几乎全部被产 品MTBE所富集。由于焦化液化石油气中异丁烯 含量较低,若液化石油气脱硫精制不彻底,将造成 产品MTBE的硫含量高得惊人。某企业生产 MTBE的原料为催化裂化和焦化液化石油气各占 一半,液化石油气精制后总硫浓度不大于343 mg/m ,但产品MTBE的硫质量分数却高达 3 mg/g。由于MTBE具有硫化物的溶解特性、分 子结构的不稳定性和自身溶于水等原因,从产品 MTBE中脱硫是相当困难的。鉴于以上原因,液 化石油气深度脱硫是非常必要的。 2硫化物分布规律及深度脱硫的可行性 正常情况下,精制前液化石油气中主要含有 H,S、甲硫醇、乙硫醇、少量COS和CS:、甲硫醚等 含硫化合物;吸收稳定操作不正常时,也会夹带微 量丙硫醇、丁硫醇和噻吩。 尽管液化石油气中各硫化物的含量差别很 大,但分布具有一定的规律性。其中H s含量最 高,至少能占到总硫含量的90%或更高。H S质 量分数低的可在几百个 gig,高的可达几万个 txg/g。影响H s含量的因素主要有原料和操作 两方面,原料的硫含量越高,液化石油气的H S 含量就越高。操作时稳定塔操作压力越高、不凝 气排放量越少,液化石油气中的H:S含量就越 高;另外,压缩富气是否注氨、注水对H S含量影 响也非常大。脱除H,S后,硫醇硫含量最高,占 到全部有机硫的90%左右。而羰基硫和甲硫醚 等的质量分数总共不超过10%。表1列出了催 化裂化液化石油气精制前所含硫化物的形态及分 布。焦化液化石油气的硫含量更高,其有机硫质 量浓度一般在2 000~4 000 rag/m ,约为催化裂 化液化石油气的10倍 。 表1 精制前硫化物的形态及分布 Table 1 Speciation and distribution of sulphide be ̄re LPG refining
从表1硫化物的分布规律看,液化石油气中 硫化物主要为H:S和硫醇,一般企业都有液化石 油气脱H S和硫醇的措施。在脱H:S和硫醇的 过程中,COS也可部分被脱除。理论上讲,催化裂
收稿13期:2010—08—24。 作者简介:盂庆飞,工程师,毕业于抚顺石油学院辽阳分院有 机化工系化工工艺专业,获学士学位。在中国石油化工股份 有限公司沧州分公司从事技术管理工作。联系电话:0317— 3551792.E-mail:mengqfl973@yahoo.COIl1.cn 第11期 孟庆飞等.液化石油气深度脱硫技术探讨 化液化石油气硫质量分数可以降到5 g/g以下, 焦化液化石油气硫质量分数也可以降到30 g/g 以下。可见,通过完善液化石油气脱H S和脱硫 醇措施、改进操作,液化石油气精制后总硫质量分 数可控制到10 g/g以下,实现产品MTBE的总 硫质量分数在50 g/g左右是可能的。 3脱硫技术的现状与不足 目前,液化石油气脱硫精制一般包括胺吸收 脱}I’s、预碱洗脱H s、抽提氧化脱硫醇,极少配 套脱羰基硫。大多数企业液化石油气精制后总硫 含量远高于理论值;尤其是焦化液化石油气硫浓 度能降低到343 mg/rfl 以下的较少,极个别的有 600~800 mg/m 。精制后工业液化石油气中的硫 化物组成,其主要成分为二硫化物。针对液化石 油气脱硫的现状与不足分析如下。 3.1胺吸收脱H,S技术 脱H s普遍采用醇胺水溶液化学吸附工艺。 根据原料的性质、酸性气含量和C含量与s含量 比值的不同,选择合适的醇胺功能配方溶剂、灵活 调整吸收塔板数和负荷,进一步降低能耗是该技 术未来努力的方向。大部分企业都能将H S浓 度控制在20 mr//TI 以下;但也有不少企业受落后 的总硫指标的影响,并不严格控制脱后硫化氢的 含量 。一些过去加工低硫原油的企业甚至没 有胺吸收脱H,s装置,给后续的脱硫醇和丙烯精 制带来极大的困难,而且也会造成精制后液化石 油气铜片腐蚀不合格。因此,脱后H s浓度控制 在10 mg/13"1 以下比较理想,太高会加重后续精制 的负荷,使碱渣排放量增加;太低会使能耗增加。 另外,引起溶剂降解的原因分析不清,功能成 分和有害物的分析化验方法不健全,降解及夹带 造成的溶剂消耗高是普遍存在的现象,并时常对 脱硫醇操作形成冲击。 3.2预碱洗脱H,S技术 液化石油气预碱洗脱H S技术一般与脱硫 醇技术组合在一起,是用液体NaOH进一步降低 液化石油气中的H:s含量。理论上能将H:s完 全脱除,一方面避免H,S在脱硫醇段与NaOH反 应,降低循环的溶剂量及碱液浓度,缩短脱硫醇溶 剂的使用寿命;另一方面避免Na,S溶剂再生时发 生下列生成元素硫的反应,造成液化石油气精制 后铜片腐蚀不合格。 2Na2S+2H20+O2—— 2S十4NaOH 2NaHS+NaHSO3 3S+3NaOH 从设计到生产未给予预碱洗足够重视。设计 没有明确的控制参数,生产没有明确的预碱洗操 作控制指标。 首先,碱液与液化石油气接触不充分是预碱 洗普遍存在的问题。目前,卧罐一般采用文氏管 混合,立罐一般采用液化石油气鼓泡混合。由于 液化石油气与碱液的密度差较大,很难保证H:s 和碱液的接触效果。加之间断换碱,没有明确的 控制指标,所以,不能保证预碱洗后H S质量分 数低于0.1 g/g。 其次,不重视预碱洗的沉降分离。胺吸收脱 H,S携带溶剂的问题本应在预碱洗段解决,但却 经常造成后续脱硫醇段的操作困难。富集了高浓 度H2S的胺液和预碱洗碱液集中进人脱硫醇段, 造成的冲击比没有预碱洗更为严重。 此外,有的学者提出采用固体碱代替液体碱 进行预碱洗,以减少排渣。但因其效率低、投资 高,不节能减排,故不具有工业推广价值。 3.3脱硫醇技术 Merox抽提氧化法是液化石油气最广泛采用 的脱硫醇技术,其依据的原理是硫醇的弱酸性和 硫醇负离子易被氧化生成二硫化合物,反应方程 式如下: RSH+NaOH RSNa+H2O 2RSNa+1/202+H20——}RSSR+2NaOH 首先由强碱(NaOH)与硫醇反应生成硫醇钠, 硫醇钠溶于碱液从液化石油气中脱除;溶于碱液中 的硫醇钠部分形成硫醇负离子,硫醇负离子在催化 剂的作用下被空气氧化为二硫化物,二硫化物为油 状,从碱液中脱出,使NaOH得到再生l2 J。 Merox抽提氧化法再生一般都采用散堆填料 塔,抽提采用静态混合器、填料塔和纤维膜接触器 等。由于液化石油气黏度小、与碱液的密度差较 大,所以剂烃两相充分接触较困难。填料塔易沟 流,造成铜片腐蚀不合格。纤维膜接触器优点是 剂烃两相无需强混合就可实现充分接触,避免了 油品带剂和需要较大的沉降分离设备。但是纤维 膜容易被结垢污染,同时不适合高硫负荷下的抽 提反应。碱吸收原料和再生空气中的CO 形成 碳酸钠,碳酸钠溶解度较低,极易结晶析出l3]。 某厂汽油脱硫醇纤维膜设备,使用前两年效果良 一18一 炼油技术与工程 2010年第40卷 好,到第三年失效,检修发现纤维膜上结有大量污 垢。使用纤维膜接触器时,剂烃比小且是顺流接 触,并且纤维对碱液有较强的吸附性,造成硫醇钠 溶解困难,脱硫效果变差。 液化石油气脱硫醇装置存在的问题为脱后总 硫含量较高、铜片腐蚀不合格和排渣量大等,精制 后液化石油气中含有较多的二硫化物,实质问题 是抽提和再生效果差,其中再生效果差是核心问 题。液化石油气脱硫醇反应的难点在再生,再生 不好会导致循环溶剂中硫醇钠的浓度偏高,一方 面制约了抽提脱硫醇精制的深度,另一方面又提 高了催化剂、碱对二硫化物的增溶作用,使循环溶 剂携带较高的二硫化物,这两方面都导致液化石 油气精制后总硫含量偏高。 另外,传统工艺再生催化剂溶于溶剂,与溶 剂循环于抽提和再生,在进行抽提反应时,溶解 氧在催化剂作用下使部分硫醇钠转化成二硫化 物-4]。尽管有些企业采用了严格的二级反抽提 措施,但由于以上原因,精制后二硫化物含量依 然很高。 有的学者推出无碱固定床直接转化脱硫醇工 艺和液化石油气脱硫醇后固定床补充精制等技 术。前者因投资高、精制后液化石油气总硫含量 高,不具推广价值;后者因液化石油气脱硫醇工艺 完全能够确保液化石油气的精制质量,必要性 不大。 3.4脱羰基硫技术 在常温、无水、无碱性催化剂存在时,COS呈 中性,无腐蚀性,且COS占总硫含量指标甚微,一 般没有专门考虑脱除羰基硫的问题。一些企业液 化石油气的羰基硫含量较高,要实现深度脱硫,羰 基硫也将成为影响因素。 4 GL助溶法液化石油气深度脱硫 根据液化石油气所含硫化物的形态和分布特 点,在分析现有脱硫工艺技术存在不足的基础上, 提出了液化石油气深度脱硫组合技术,并同时深 切关注了节能减排和经济效益等因素,主要措施 可概括为功能强化、设施简化和节能减排三方面 的内容。其核心是GL助溶法强化脱硫醇技术。 4.1 加入专用功能强化助剂 功能强化助剂的加入,提高了抽提能力和再 生活性。某企业在传统工艺装置上采用功能强化 助剂,一级抽提就将焦化液化石油气的总硫浓度 降低到100 mg/m。以下。功能强化助剂同时增加 羰基硫在溶剂和碱液中的溶解度,促进羰基硫的 水解和脱除,获得更高的脱硫深度。 oH— COS+H,0—_-+H。S+CO,
4.2实现常温再生 通过强化再生,实现了常温再生,简化了流程 和控制,降低了投资和操作费用。通过高效再生 催化剂、改善剂风混合效果、再生塔增加反抽提油 等措施,实现三相}昆合氧化再生,增强了再生反应 推动力,强化了再生效果,降低了循环溶剂中硫醇 的浓度,减少了二硫化物的夹带量。 4.3消除再生的副反应 采用固定床催化剂技术减弱溶解氧的影响, 消除抽提反应时发生的再生副反应。通过固定床 催化剂技术,减少或避免了抽提反应时硫醇钠在 催化剂存在时的氧化反应,减少生成二硫化物。 4.4选用静态混合器 选用静态混合器与筛板塔或纤维膜科学组 合,作为溶剂和液化石油气的接触设备。充分利 用静态混合器投资小、混合效果好,萃取塔逆流多 级接触反应推动力大和纤维膜具有的接触充分且 分离效果好等优势的组合,在提高脱硫醇深度的同 时,降低剂烃比,减少水洗水消耗,实现节能减排。 4.5 改善预碱洗剂烃接触方式和时间 改善预碱洗剂烃接触方式和时间,提高处理 效果,将胺吸收脱H S后残余的H s和CO:尽可 能脱除,制定明确的预碱洗精制控制指标;同时改 善预碱洗过程的沉降分离效果,严格限制预碱洗 带碱渣,以保护脱硫醇溶剂的使用寿命,减少 排渣。 4.6对氧化风实施除CO 预净化 采取这一措施后,可进一步延长脱硫醇溶剂 的使用寿命,减少排渣。