【半导体抛光】硅片腐蚀和抛光工艺的化学原理
硅片双面抛光粗抛原理

硅片双面抛光粗抛原理在半导体制造过程中,硅片抛光是一个至关重要的步骤。
其中,硅片双面抛光粗抛是整个抛光过程中的首要步骤。
本文将详细介绍硅片双面抛光粗抛的原理和过程。
硅片双面抛光粗抛是将硅片两面进行粗糙度的消除,以达到平整度和光滑度的要求。
该过程是通过使用专用的抛光机器和抛光液来实现的。
硅片被固定在抛光机器的夹具上,保持稳定。
然后,在硅片的两面涂上一层抛光液,抛光液中含有磨料颗粒。
这些磨料颗粒可以有效地去除硅片表面的不平坦部分。
接下来,抛光机器启动,夹具开始旋转,硅片也随之旋转。
同时,抛光机器中的抛光头也开始运动。
抛光头上覆盖有抛光布,抛光布上也含有磨料颗粒。
当抛光头与硅片接触时,磨料颗粒会与硅片表面的不平坦部分发生摩擦,从而使硅片表面变得更加平整。
在整个抛光过程中,硅片会不断地旋转,并且抛光机器会自动调整抛光头的位置,以保持抛光的均匀性。
通过不断地抛光和旋转,硅片的两面逐渐变得平整和光滑。
完成双面抛光粗抛后,硅片将被取下并进行后续的抛光工艺。
这个过程是非常重要的,因为它直接影响到硅片的质量和性能。
总结起来,硅片双面抛光粗抛是半导体制造过程中不可或缺的一步。
通过使用专用的抛光机器和抛光液,可以将硅片表面的不平坦部分去除,使其变得更加平整和光滑。
这个过程在整个半导体制造过程中起到了至关重要的作用,确保最终产品的质量和性能。
为了更好地理解硅片双面抛光粗抛原理,我们可以想象一下一个工匠在打磨一个雕塑的过程。
他会使用磨料和工具,不断地打磨雕塑的表面,直到达到理想的效果。
同样地,硅片双面抛光粗抛也是一个精细的工艺过程,需要仔细操作和控制,以确保最终产品的质量。
硅片双面抛光粗抛这一步骤的成功与否,直接影响到整个半导体制造过程的顺利进行。
因此,工程师们在设计抛光机器和抛光液时,需要考虑各种因素,以确保最佳的抛光效果。
通过本文的介绍,希望读者能更加了解硅片双面抛光粗抛的原理和过程。
这个步骤的重要性不可小觑,它直接关系到半导体产品的质量和性能。
硅片酸蚀刻充氮气的原理
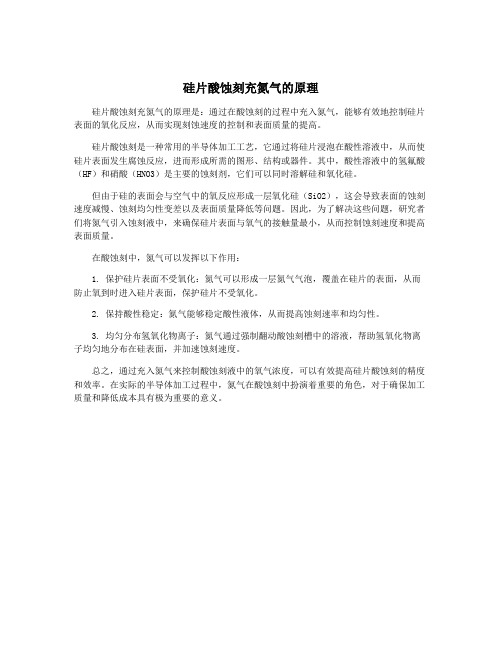
硅片酸蚀刻充氮气的原理
硅片酸蚀刻充氮气的原理是:通过在酸蚀刻的过程中充入氮气,能够有效地控制硅片表面的氧化反应,从而实现刻蚀速度的控制和表面质量的提高。
硅片酸蚀刻是一种常用的半导体加工工艺,它通过将硅片浸泡在酸性溶液中,从而使硅片表面发生腐蚀反应,进而形成所需的图形、结构或器件。
其中,酸性溶液中的氢氟酸(HF)和硝酸(HNO3)是主要的蚀刻剂,它们可以同时溶解硅和氧化硅。
但由于硅的表面会与空气中的氧反应形成一层氧化硅(SiO2),这会导致表面的蚀刻速度减慢、蚀刻均匀性变差以及表面质量降低等问题。
因此,为了解决这些问题,研究者们将氮气引入蚀刻液中,来确保硅片表面与氧气的接触量最小,从而控制蚀刻速度和提高表面质量。
在酸蚀刻中,氮气可以发挥以下作用:
1. 保护硅片表面不受氧化:氮气可以形成一层氮气气泡,覆盖在硅片的表面,从而防止氧到时进入硅片表面,保护硅片不受氧化。
2. 保持酸性稳定:氮气能够稳定酸性液体,从而提高蚀刻速率和均匀性。
3. 均匀分布氢氧化物离子:氮气通过强制翻动酸蚀刻槽中的溶液,帮助氢氧化物离子均匀地分布在硅表面,并加速蚀刻速度。
总之,通过充入氮气来控制酸蚀刻液中的氧气浓度,可以有效提高硅片酸蚀刻的精度和效率。
在实际的半导体加工过程中,氮气在酸蚀刻中扮演着重要的角色,对于确保加工质量和降低成本具有极为重要的意义。
硅片酸蚀刻氮气的原理

硅片酸蚀刻氮气的原理硅片是电子器件制造过程中的常用材料之一,蚀刻是一种重要的工艺步骤,通过蚀刻可以将不需要的硅片表层材料去除,从而实现制造所需的图形和结构。
酸蚀刻是其中一种常见的蚀刻方式,通过将硅片浸泡在酸溶液中,使酸与硅反应,从而发生蚀刻。
在普通的酸蚀刻过程中,常使用的酸是盐酸(HCl)或硝酸(HNO3)等。
这些酸对硅材料具有较高的腐蚀作用,但同时也容易引起一些问题,例如表面损伤、杂质沉积等。
为了避免这些问题,氮气蚀刻在一些情况下被选择代替传统的酸蚀刻。
氮气是一种无色无味的常温常压气体,它具有氧化性质。
氮气的氧化性是指在一些物质中,它能够与其他物质发生氧化反应,从而引起蚀刻。
氮气蚀刻的基本原理是将氮气溶解在酸溶液中,形成一个含氮气的酸性环境。
在这个环境中,氮气与硅表面发生氧化反应,从而发生蚀刻。
具体来说,氮气被溶解在酸溶液中后,会分解成氮氧化物,例如一氧化氮和二氧化氮等。
这些氮氧化物会与水反应生成一些氧化剂,例如亚硝酸离子(NO2-)和硝酸离子(NO3-)。
这些氧化剂具有较强的氧化性质,能够与硅表面的材料发生反应,从而引起蚀刻。
硅的蚀刻过程可以通过一系列的化学反应来描述。
首先,氧化剂与硅发生反应,生成硅氮酸(silicic acid)和一些气体产物。
这些产物会在硅与氧化剂相互作用的过程中被移除,从而实现了蚀刻。
在氮气蚀刻中,硅氮酸中的氮氧化物起到了氧化剂的作用。
与传统的盐酸或硝酸蚀刻相比,氮气蚀刻具有一些优点。
首先,氮气是一种安全、环保的气体,不会对操作人员和环境造成危害。
其次,氮气蚀刻不会导致表面损伤和杂质沉积等问题,可以实现高质量的蚀刻。
此外,氮气蚀刻还可以用于一些对激光辐照等传统蚀刻方法不适用的材料。
总之,硅片酸蚀刻氮气利用氮气的氧化性质,在酸溶液中形成含氮气的酸性环境,使氮气与硅表面发生反应,从而实现蚀刻。
这种蚀刻方法具有安全、高质量等优点,适用于一些特殊材料的蚀刻需求。
硅片的腐蚀

实验三 硅片的腐蚀一、实验目的1.掌握Si 单晶片的位错侵蚀方法和位错密度的计算方法2.了解腐蚀Si 单晶位错原理,正确使用金相显微镜,二、实验原理位错是晶体的线缺陷,它标志着晶体结构的完整程度,它对半导体材料的电学性能有很大影响,通常制造器件要求位错密度要低,或是无位错晶体,而且还要求晶体位错分布均匀,位错高低直接影响晶体做器件的质量。
测量单位体积内位错的方法有X 射线法,电子显微镜法和铜缀饰红外投射法等,但这些方法设备昂贵,工艺复杂,所以生产上很少采用。
目前生产上广泛使用的是腐蚀金相法(腐蚀坑法)。
它是将样品进行化学腐蚀,然后用金相显微镜测定样品表面上出现的腐蚀坑数目。
因为每一腐蚀坑代表与被测表面相交的一条位错线的露头处,所以位错密度是指单位被测表面积上相交的位错线(坑)的个数。
N D = Sn (1) N D 为位错密度,单位个数/厘米2 ,n 是位错线的(坑)的个数,S 是面积。
为什么在晶体表面位错露头的地方,经化学腐蚀后会出现腐蚀坑呢?这是因为在位错线的地方,原子排列不规则,存在差应力场,使该处的原子具有较高的能量和较大的应力,当我们用某种化学腐蚀剂腐蚀晶体时,有位错处的腐蚀速度大于完整晶体的腐蚀速度,这样经过一定时间腐蚀后,就会在位错线和样品表面的相交处显示出凹的蚀坑,由于晶体具有各向异性,因此在不同的结晶面腐蚀速度不同,在不同晶面上其蚀坑形状亦不同。
如图1所示,在(111)面上经腐蚀出现正三角形腐蚀坑,在(100)面上出现正四边形腐蚀坑,在(110)面上为矩形腐蚀坑。
图2.1-1位错蚀坑的形状用金相显微镜观测位错密度是一种近似的方法,因为位错在晶体中的分布是不规则的,有些位错并不一定在被观测的面形成蚀坑,有些位错非常临近,几个临近的位错只形成一个蚀坑,所以蚀坑与位错并不是一一对应的,它只能近似地反应出晶体中的位错密度大小。
三、实验仪器和化学药品金相显微镜、天平、塑料烧杯、镊子、量桶、硝酸、氢氟酸,自配铬酸溶液、乙醇等。
硅的cmp抛光技术

硅的cmp抛光技术
硅的CMP抛光技术,全称为化学机械抛光技术,是半导体晶片表面加工的
关键技术之一。
这种技术利用化学腐蚀和机械力对加工过程中的硅晶圆或其它衬底材料进行平坦化处理。
CMP设备包括抛光、清洗、传送三大模块,
其作业过程中,抛光头将晶圆待抛光面压抵在粗糙的抛光垫上,借助抛光液腐蚀、微粒摩擦、抛光垫摩擦等耦合实现全局平坦化。
此外,单晶硅片制造过程和前半制程中也需要多次用到化学机械抛光技术。
与先前普遍使用的机械抛光相比,化学机械抛光能使硅片表面变得更加平坦,并且还具有加工成本低及加工方法简单的优势,因而成为目前最为普遍的半导体材料表面平整技术。
由于目前集成电路元件普遍采用多层立体布线,集成电路制造的前道工艺环节需要进行多层循环。
在此过程中,需要通过CMP工艺实现晶圆表面的平
坦化。
集成电路制造是CMP设备应用的最主要的场景,重复使用在薄膜沉
积后、光刻环节之前。
以上信息仅供参考,如有需要,建议查阅CMP技术相关论文或咨询专业人士。
硅片酸蚀刻氮气的原理

硅片酸蚀刻氮气的原理
硅片酸蚀刻是半导体工艺中的一项重要步骤,也是制备微电子器件的关键技术之一。
氮气在硅片酸蚀刻过程中起到了重要的作用,下面我们来了解一下它的原理。
硅片酸蚀刻是利用酸性溶液对硅片表面进行腐蚀,从而实现对硅片表面形貌和结构的精细控制。
酸性溶液中的氢离子可以与硅表面的氧原子形成化学键,从而使硅表面发生腐蚀。
但是,酸性溶液中的氢离子对硅表面的反应速率较慢,而且会产生大量的氢气,容易形成气泡,影响腐蚀质量。
氮气在硅片酸蚀刻过程中被用来代替水,起到了抑制氢气生成的作用。
具体地说,氮气可以和酸性溶液中的氢离子反应生成氮氧化物,而不会产生氢气。
氮氧化物可以较快地与硅表面反应,促进酸性溶液对硅表面的腐蚀。
此外,氮气还可以形成一个氮气垫,抵消硅表面的静电作用,保证硅表面的均匀腐蚀。
所以,硅片酸蚀刻中添加氮气可以有效地抑制氢气的产生,提高腐蚀质量和均匀性。
同时,氮气还可以促进酸性溶液对硅表面的腐蚀反应,加速刻蚀速率。
这些都是氮气在硅片酸蚀刻过程中起到的重要作用。
- 1 -。
硅片腐蚀工作步骤及工作事项

硅片腐蚀㈠、目的和原理:利用氢氧化钠对多晶硅腐蚀作用,去除硅片在多线切割锯切片时产生的表面损伤层,同时利用氢氧化钠对硅腐蚀的各向异性,争取表面较低反射率较低的表面织构。
解释:①现有多晶硅片是由长方体晶锭在多线切割锯切成一片片多晶硅方片。
由于切片是钢丝在金刚砂溶液作用下多次往返削切成硅片,金刚砂硬度很高,会在硅片表面带来一定的机械损伤。
如果损伤不去除,会影响太阳电池的填充因子。
②氢氧化钠俗称烧碱,是在国民经济生产中大量应用化工产品。
由电解食盐水而得,价格比较便宜,每500克6元。
化学反应方程式为:↑+↑+=+222222H Cl NaOH O H NaCl 电解。
分析纯氢氧化锂、氢氧化钾也可以与硅起反应,但价格较贵。
如氢氧化锂每500克23元,用于镉-镍电池电解液中。
↑+=++23222a 2H SiO N O H NaOH Si 加热③碱性腐蚀优点是反应生成物无毒,不污染空气和环境。
不像HF-HNO 3酸性系统会生成有毒的NO x 气体污染大气。
另外,碱性系统与硅反应,基本处于受控状态。
有利于大面积硅片的腐蚀,可以保证一定的平行度。
㈡、步骤:面产生出部分反射率较低的织构表面。
如果含有[100]晶向的晶粒,就可以长出金字塔体状的绒面。
第五步是通过盐酸中和残余的氢氧化钠,化学反应方程式为:O H NaCl NaOH HCl 2+=+。
第七步氢氟酸络合掉硅片表面的二氧化硅层,化学反应方程式为:O H SiF H HF SiO 26222][6+=+。
2. 我们就粗抛作过实验,投入50片硅片:a . 在20%NaOH 溶液中,温度为80℃,反应了10分钟,硅片厚度平均去掉了32μm 。
b . 在15%NaOH 溶液中,温度为80℃,反应了10分钟,硅片厚度平均去掉了25μm (此数据来源于小片实验)。
硅片粗抛是放热反应且反应激烈,反应速度与温度上升有点正反馈的态势:温度高,浓度高反应就会更激烈。
新硅片由于表面粗糙,表面积大一些反应也会激烈一些。
半导体CMP工艺介绍

半导体CMP工艺介绍半导体CMP工艺的基本原理是将硅片或其他基底材料放置在旋转的抛光盘上,其中涂有一层精细研磨颗粒的抛光材料。
通过施加垂直于硅片表面的压力和旋转抛光盘,在化学溶液的作用下,研磨颗粒将不均匀的材料移除,从而使表面平整化。
此外,化学溶液中添加的缓冲剂和表面活性剂等物质还可以起到控制反应速率和表面质量的作用。
CMP工艺的应用主要包括以下几个方面:1.平坦化:在半导体制造的各个步骤中,不可避免地会产生不均匀的层厚度和表面高度差。
通过CMP工艺,可以将这些不均匀物质去除,实现表面的平整化。
平坦化可以提高电子器件的性能,减少漏电流和损耗,并且提高芯片的可靠性。
2.边缘控制:在制造微小结构的芯片中,边缘效应是一个很重要的因素。
通过CMP工艺,在边缘处可以实现材料的去除,从而改善边缘效应,并提高芯片的性能。
3.材料移除:在半导体器件的制造过程中,常常会有需要移除的材料层,例如氧化物、金属等。
通过选择合适的抛光材料和化学溶液,可以对这些材料进行高效、精确的去除。
4.纳米级平整化:随着科技的发展,芯片的制造尺寸不断减小,对表面平整度和光洁度的要求也越来越高。
CMP工艺可以实现纳米级别的平整化,使得芯片表面具有非常高的质量。
除了以上的应用之外,半导体CMP工艺还被广泛应用于高深度微细加工、背隙法制备硅为基的太阳能电池、数据存储器件等领域。
虽然CMP工艺在半导体制造过程中起到了重要作用,但是在实际应用中也存在一些挑战。
例如,选择合适的抛光材料和化学溶液,控制好抛光时间和压力等参数都需要精确的掌握。
此外,还需要解决杂质污染和热效应等问题,以确保芯片的质量和稳定性。
总之,半导体CMP工艺是一种重要的半导体后期加工技术,能够在半导体制造过程中实现表面的平整化和材料的去除。
它在半导体行业中的应用已经非常广泛,并且随着芯片制造尺寸的不断缩小和技术的不断进步,CMP工艺的发展和应用还具有很大的潜力。
- 1、下载文档前请自行甄别文档内容的完整性,平台不提供额外的编辑、内容补充、找答案等附加服务。
- 2、"仅部分预览"的文档,不可在线预览部分如存在完整性等问题,可反馈申请退款(可完整预览的文档不适用该条件!)。
- 3、如文档侵犯您的权益,请联系客服反馈,我们会尽快为您处理(人工客服工作时间:9:00-18:30)。
在半导体材料硅的表面清洁处理,硅片机械加工后表面损伤层的去除、直接键合硅片的减薄、硅中缺陷的化学腐蚀等方面要用到硅的化学腐蚀过程。
下面讨论硅片腐蚀工艺的化学原理和抛光工艺的化学原理。
一、硅片腐蚀工艺的化学原理
硅表面的化学腐蚀一般采用湿法腐蚀,硅表面腐蚀形成随机分布的微小原电池,腐蚀电流较大,一般超过100A/cm2,但是出于对腐蚀液高纯度和减少可能金属离子污染的要求,目前主要使用氢氟酸(HF),硝酸(HNO3)混合的酸性腐蚀液,以及氢氧化钾(KOH)或氢氧化钠(NaOH)等碱性腐蚀液。
现在主要用的是HNO3-HF 腐蚀液和NaOH 腐蚀液。
下面分别介绍这两种腐蚀液的腐蚀化学原理和基本规律。
1.HNO3-HF 腐蚀液及腐蚀原理
通常情况下,硅的腐蚀液包括氧化剂(如HNO3)和络合剂(如HF)两部分。
其配置为:浓度为70%的HNO3和浓度为50%的HF 以体积比10~2:1,有关的化学反应如下:
3Si+4HNO3=3SiO2↓+2H2O+4NO↑
硅被氧化后形成一层致密的二氧化硅薄膜,不溶于水和硝酸,但能溶于氢氟酸,这样腐蚀过程连续不断地进行。
有关的化学反应如下:
SiO2+6HF=H2[SiF6]+2H2O
1
2.NaOH 腐蚀液
在氢氧化钠化学腐蚀时,采用10%~30%的氢氧化钠水溶液,温度为80~90℃,将硅片浸入腐蚀液中,腐蚀的化学方程式为
Si+H2O+2 NaOH =Na2SiO3+2H2↑
对于太阳电池所用的硅片化学腐蚀,从成本控制,环境保护和操作方便等因素出发,一般用氢氧化钠腐蚀液腐蚀深度要超过硅片机械损伤层的厚度,约为20~30um。
二、抛光工艺的化学原理
抛光分为两种:机械抛光和化学抛光,机械抛光速度慢,成本高,而且容易产生有晶体缺陷的表面。
现在一般采用化学-机械抛光工艺,例如铜离子抛光、铬离子抛光和二氧化硅-氢氧化钠抛光等。
1. 铜离子抛光
铜离子抛光液由氯化铜、氟化铵和水,一般以质量比60:26:1000 组成,调节PH=5.8 左右,或者以质量比80:102.8:1000,其反应原理如下:
Si+2CuCl2+6NH4F=(NH4)2[SiF6]+4NH4Cl+2Cu
铜离子抛光一般在酸性(pH 为5~6)条件下进行,当pH﹥7 时,反应终止,这是因为pH=7 时铜离子与氨分子生成了稳定的络合物-铜氨络离子,这时铜离子大大减
2
少,抛光作用停止了。
抛光反应速度很快,为防止发生腐蚀,取片时不能在表面残留抛光液,应立即进行水抛,也可以在取片前进行稀硝酸漂洗,可以再洗一次,防止铜离子污染。
2.铬离子抛光铬离子抛光液由三氧化二铬、重铬酸铵和水一般以质量比1:3:100 组成,其反应原理如下:
3Si+2Cr2O72-+28H+=3Si4++4Cr3++14H2O
三氧化二铬不溶于水,对硅表面进行研磨,重铬酸铵能不断地对硅表面进行氧化腐蚀,与三氧化二铬的机械研磨作用相结合,进行抛光。
3.二氧化硅-氢氧化钠抛光法二氧化硅-氢氧化钠抛光配置方法有三种:
(1)将三氯氢硅或四氯化硅液体用氮气携带通入到氢氧化钠溶液中,产生的沉淀在母液中静置,然后把上面的悬浮液轻轻倒出,并调节pH 值为9.5~11。
其反应如下:
SiCl4+4NaOH=SiO2↓+4NaCl+2H2O
SiHCl3+3NaOH=SiO2↓+3NaCl+H2O +H2↑
(2)也可以利用制备多晶硅的尾气或硅外延生长时的废气生产二氧化硅微粒。
反应如下:
SiCl4+4H2O=H2SiO3↓+4HCl
3
H2SiO3=SiO2+H2O
(3)用工业二氧化硅粉和水以质量比为150:1000 配置,并用氢氧化钠调节pH 值为9.5~11。
抛光液的pH 值为9.5~11 范围内,pH 值过低,抛光很慢,PH 值过高产生较强的腐蚀作用,硅片表面出现腐蚀坑。
4。