化学镀镍的常见故障及解决办法
镀镍问题与解决方案
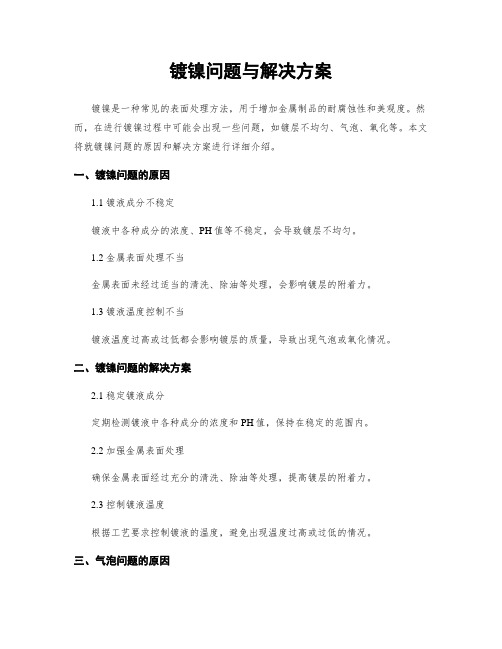
镀镍问题与解决方案镀镍是一种常见的表面处理方法,用于增加金属制品的耐腐蚀性和美观度。
然而,在进行镀镍过程中可能会出现一些问题,如镀层不均匀、气泡、氧化等。
本文将就镀镍问题的原因和解决方案进行详细介绍。
一、镀镍问题的原因1.1 镀液成分不稳定镀液中各种成分的浓度、PH值等不稳定,会导致镀层不均匀。
1.2 金属表面处理不当金属表面未经过适当的清洗、除油等处理,会影响镀层的附着力。
1.3 镀液温度控制不当镀液温度过高或过低都会影响镀层的质量,导致出现气泡或氧化情况。
二、镀镍问题的解决方案2.1 稳定镀液成分定期检测镀液中各种成分的浓度和PH值,保持在稳定的范围内。
2.2 加强金属表面处理确保金属表面经过充分的清洗、除油等处理,提高镀层的附着力。
2.3 控制镀液温度根据工艺要求控制镀液的温度,避免出现温度过高或过低的情况。
三、气泡问题的原因3.1 镀液中含有杂质镀液中可能存在杂质,导致镀层表面出现气泡。
3.2 镀液搅拌不均匀镀液搅拌不均匀会造成气泡在镀液中无法释放。
3.3 镀液中气体过多镀液中气体过多也会导致气泡问题的出现。
四、气泡问题的解决方案4.1 滤除镀液中的杂质定期对镀液进行过滤,去除其中的杂质,减少气泡问题的发生。
4.2 加强镀液搅拌确保镀液搅拌均匀,使气泡能够顺利释放。
4.3 控制镀液中气体含量适当控制镀液中气体的含量,避免气体过多导致气泡问题。
五、氧化问题的原因5.1 镀液中含氧量过高镀液中含氧量过高会导致镀层表面氧化。
5.2 镀层附着力不足镀层附着力不足会导致镀层表面容易氧化。
5.3 镀液中含有氧化物镀液中可能存在氧化物,会导致镀层表面出现氧化情况。
六、氧化问题的解决方案6.1 控制镀液中氧含量通过适当的方法控制镀液中氧含量,避免出现过高的情况。
6.2 提高镀层附着力加强金属表面处理,提高镀层的附着力,减少氧化问题的发生。
6.3 定期清洗镀液定期清洗镀液中的氧化物,保持镀液的清洁度,减少氧化问题的发生。
化学镀镍问题及对策

化学镍故障与对策
状况 镀液分解 浴液的混浊 析出速度过快 析出速度过慢
无析出反应 析出皮膜粗糙
原因
pH 值过高
镀浴负荷过大 过多活化钯带入 镀液局部过热 亚磷酸镍的生成
pH 值偏高 镀液温度偏高 镀液不平衡 pH 值偏低
镀液温度偏低 镀液不平衡 金属或有机污染
镀液老化 pH 值偏低
镀液温度偏低 前处理不良
避免发生 分批逐次添加并修正 补充量 Nhomakorabea光泽不良
发生斑点
针孔 peeling
pH 值偏高 负载过小 pH 偏高 镀浴浓度过低 重金属混入 镀液老化 後水洗及乾燥不充份 pH 偏高 前处理不良 镀浴浓度过高 前处理不良 素材表面不良 前处理不良(脱脂不 良) 工件中途吊起 单次药液补充过量
式调整 以稀硫酸降低 pH 值 修正负载比例 以稀硫酸降低 pH 值 镀液调整 重新建浴 重新建浴 加强水洗及热水洗 以稀硫酸降低 pH 值 改善前处理 补充蒸发水份 改善前处理 检查素材表面 改善前处理
前处理不良 有不溶解物带入 氢氧化镍生成
改善对策
pH 值测量应在补充添加
彻底搅拌後进行
修正负载比例
加强水洗
充份搅拌并注意温控 镍浓度及 pH 值确认在 正常操作范围,降低液 温至 20 ~40℃後添加 适量建浴液充份搅拌 添加稀硫酸降低 pH 值 温度控制在 84~92℃ 分析添加镀液组成 以稀释 2 倍氨水调整 pH 值 温度控制在 84~92℃ 分析添加镀液组成 假镀去除金属,以活性 碳去除有机污染 重新建浴 以稀释 2 倍氨水调整 pH 值 改善浴温控制 脱脂、酸活化、活化钯 等要确认条件 加强前处理 加强过滤 注意 pH 控制及搅拌方
手把手教你化学镀镍的常见故障及解决办法

手把手教你化学镀镍的常见故障及解决办法(1)沉积速度慢(这点也是平台上最多朋友咨询的)造成这种现象的原因与解决方法:镀液pH值过低:测pH值调整,并控制pH在下限值。
虽然pH 值较高能提高沉速,但会影响镀液稳定性。
镀液温度过低:要求温度达到规范时下槽进行施镀。
新开缸第一批工件下槽时,温度应达到上限,反应开始后,正常施镀时,温度在下限为好。
溶液主成分浓度低:分析调整,如还原剂不足时,添加还原补充液;镍离子浓度偏低时,添加镍盐补充液。
对于上规模的化学镀镍,设自动分析、补给装置是必要的,可以延长连续工作时间(由30h延至56h)和镍循环周期(由6周延至11周)。
亚磷酸根过多:弃掉部分镀液。
装载量太低:增加受镀面积至1dm2/L。
稳定剂浓度偏重:倾倒部分,少量多次加浓缩液。
(2)镀液分解(镀液呈翻腾状,出现镍粉)造成这种现象的原因与解决方法:温度过高或局部过热:搅拌下加入温去离子水。
次亚磷酸钠大多:冲稀补加其它成分。
镀液的pH值过高:调整pH值至规范值。
机械杂质:过滤除去。
装载量过高:降至1dm2/L槽壁或设备上有沉淀物:滤出镀液,退镀清洗(用3HNO3溶液)。
操作温度下补加液料大多:搅拌下少量多次添加。
稳定剂带出损失:添加少量稳定剂。
催化物质带入镀液:加强镀前清洗。
镀层剥离碎片:过滤镀液。
(3)镀层结合力差或起泡造成这种现象的原因与解决方法:镀前处理不良:提高工作表面的质量,加工完成后应清除工件上所有的焊接飞溅物和焊渣。
工件表面的粗糙度应达到与精饰要求相当的粗糙义,如碳钢工件表面粗糙度Ra<>温度波动太大:控制温度在较小的范围波动。
下槽温度太低:适当提高下槽温度。
清洗不良:改进清洗工序。
金属离子污染:用大面积废件镀而除去。
有机杂质污染:活化炭1-2g/L 处理。
热处理不当:调整热处理时间和温度。
(4)镀层粗糙造成这种现象的原因与解决方法:镀液浓度过高:适当冲稀镀液。
镀液的pH值过高:降低pH值至规范值。
镀镍问题与解决方案

镀镍问题与解决方案引言概述:镀镍是一种常见的金属表面处理方法,它可以提高金属的耐腐蚀性、硬度和外观。
然而,在镀镍过程中,我们常常会遇到一些问题,如镀层不均匀、气泡、缺陷等。
为了解决这些问题,我们需要采取一些有效的解决方案。
正文内容:1. 镀层不均匀问题:1.1 控制电流密度:调整电流密度可以使镀层均匀。
在镀层不均匀的区域增加电流密度,而在均匀的区域减少电流密度。
1.2 改善搅拌条件:通过改善搅拌条件,如增加搅拌桨的数量或改变搅拌桨的位置,可以使电解液均匀分布,从而获得均匀的镀层。
2. 气泡问题:2.1 降低电流密度:气泡往往是由于过高的电流密度造成的。
降低电流密度可以减少气泡的产生。
2.2 提高搅拌效果:通过增加搅拌桨的转速或改变搅拌桨的形状,可以提高搅拌效果,将气泡从电解液中排出。
3. 缺陷问题:3.1 清洗金属表面:在镀镍之前,彻底清洗金属表面是非常重要的。
通过去除污垢、油脂和氧化物,可以减少缺陷的产生。
3.2 控制镀液温度:镀液温度对镀层质量有很大影响。
在适宜的温度范围内进行镀镍,可以减少缺陷的发生。
3.3 选择合适的镀液配方:不同的金属需要不同的镀液配方。
选择合适的镀液配方可以提高镀层的质量,减少缺陷的产生。
4. 防止镀层剥落问题:4.1 提高镀层附着力:通过在金属表面进行预处理,如机械打磨、化学处理等,可以增加镀层的附着力,防止镀层剥落。
4.2 控制镀液pH值:镀液的pH值对镀层的附着力有重要影响。
在适宜的pH范围内进行镀镍,可以提高镀层的附着力。
5. 提高镀层质量问题:5.1 优化镀液配方:通过调整镀液配方中的各种成分的比例,可以提高镀层的质量。
5.2 控制镀液温度和时间:镀液的温度和镀液时间对镀层质量有很大影响。
在适宜的温度和时间范围内进行镀镍,可以获得高质量的镀层。
总结:通过控制电流密度、改善搅拌条件、降低电流密度、提高搅拌效果、清洗金属表面、控制镀液温度、选择合适的镀液配方、提高镀层附着力、控制镀液pH值、优化镀液配方、控制镀液温度和时间等方法,可以解决镀镍过程中的一些常见问题,提高镀层的质量和均匀性,从而满足不同应用领域的需求。
镀镍问题与解决方案
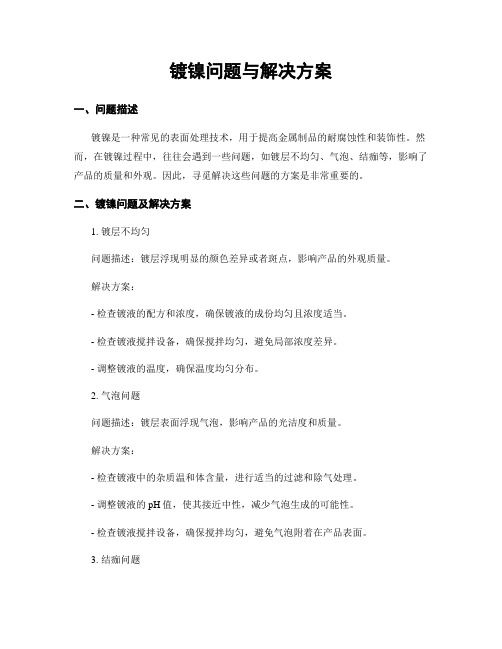
镀镍问题与解决方案一、问题描述镀镍是一种常见的表面处理技术,用于提高金属制品的耐腐蚀性和装饰性。
然而,在镀镍过程中,往往会遇到一些问题,如镀层不均匀、气泡、结痂等,影响了产品的质量和外观。
因此,寻觅解决这些问题的方案是非常重要的。
二、镀镍问题及解决方案1. 镀层不均匀问题描述:镀层浮现明显的颜色差异或者斑点,影响产品的外观质量。
解决方案:- 检查镀液的配方和浓度,确保镀液的成份均匀且浓度适当。
- 检查镀液搅拌设备,确保搅拌均匀,避免局部浓度差异。
- 调整镀液的温度,确保温度均匀分布。
2. 气泡问题问题描述:镀层表面浮现气泡,影响产品的光洁度和质量。
解决方案:- 检查镀液中的杂质温和体含量,进行适当的过滤和除气处理。
- 调整镀液的pH值,使其接近中性,减少气泡生成的可能性。
- 检查镀液搅拌设备,确保搅拌均匀,避免气泡附着在产品表面。
3. 结痂问题问题描述:镀层表面浮现结痂,影响产品的光洁度和质量。
解决方案:- 检查镀液中的杂质和沉淀物,进行适当的过滤和清理。
- 调整镀液的温度和浓度,确保镀液的流动性和均匀性。
- 检查镀液搅拌设备,确保搅拌均匀,避免结痂形成。
4. 镀层附着力问题问题描述:镀层容易剥落或者脱落,附着力不够坚固。
解决方案:- 检查基材表面的清洁度和粗糙度,确保基材表面适合镀镍。
- 使用适当的预处理方法,如酸洗、电解抛光等,提高基材与镀层的结合力。
- 调整镀液的成份和工艺参数,提高镀层的附着力。
5. 镀层厚度不足或者过厚问题问题描述:镀层厚度不符合要求,影响产品的功能和外观。
解决方案:- 调整镀液的成份和工艺参数,控制镀层的沉积速率,使其达到预定的厚度。
- 使用合适的检测设备,如X射线荧光仪、电子显微镜等,对镀层厚度进行准确测量和控制。
6. 环境污染问题问题描述:镀液中的有害物质对环境造成污染。
解决方案:- 使用环保型的镀液和镀液添加剂,减少有害物质的使用和排放。
- 定期清洁和维护镀液处理设备,确保废液的处理符合环保要求。
镀镍问题与解决方案
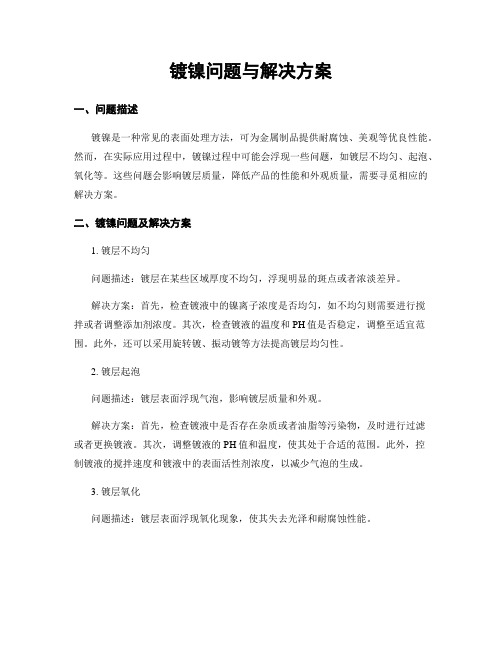
镀镍问题与解决方案一、问题描述镀镍是一种常见的表面处理方法,可为金属制品提供耐腐蚀、美观等优良性能。
然而,在实际应用过程中,镀镍过程中可能会浮现一些问题,如镀层不均匀、起泡、氧化等。
这些问题会影响镀层质量,降低产品的性能和外观质量,需要寻觅相应的解决方案。
二、镀镍问题及解决方案1. 镀层不均匀问题描述:镀层在某些区域厚度不均匀,浮现明显的斑点或者浓淡差异。
解决方案:首先,检查镀液中的镍离子浓度是否均匀,如不均匀则需要进行搅拌或者调整添加剂浓度。
其次,检查镀液的温度和PH值是否稳定,调整至适宜范围。
此外,还可以采用旋转镀、振动镀等方法提高镀层均匀性。
2. 镀层起泡问题描述:镀层表面浮现气泡,影响镀层质量和外观。
解决方案:首先,检查镀液中是否存在杂质或者油脂等污染物,及时进行过滤或者更换镀液。
其次,调整镀液的PH值和温度,使其处于合适的范围。
此外,控制镀液的搅拌速度和镀液中的表面活性剂浓度,以减少气泡的生成。
3. 镀层氧化问题描述:镀层表面浮现氧化现象,使其失去光泽和耐腐蚀性能。
解决方案:首先,检查镀液中的氧气含量,如过高则需要采取相应的措施减少氧气进入。
其次,加强镀液的过滤和除杂工作,减少镀液中的杂质对镀层的影响。
此外,可以采用添加剂或者改变镀液成份的方法,提高镀层的耐氧化性能。
4. 镀层粘附力不强问题描述:镀层与基材之间的粘附力不强,容易剥离或者脱落。
解决方案:首先,检查基材表面的清洁度和粗糙度,确保其符合镀层的要求。
其次,采用预处理方法,如酸洗、机械打磨等,增加基材与镀层之间的结合力。
此外,还可以调整镀液中的添加剂浓度和镀液的温度,以提高镀层的粘附力。
5. 镀层色差问题描述:镀层表面浮现色差,影响产品的外观质量。
解决方案:首先,检查镀液中的金属离子浓度和PH值是否稳定,调整至适宜范围。
其次,控制镀液的温度和搅拌速度,以保持镀层的一致性。
此外,可以采用添加剂或者改变镀液成份的方法,调整镀层的颜色。
镀镍问题与解决方案
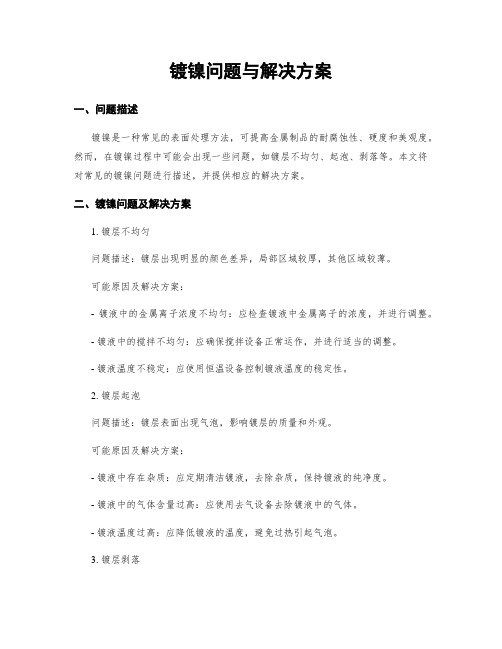
镀镍问题与解决方案一、问题描述镀镍是一种常见的表面处理方法,可提高金属制品的耐腐蚀性、硬度和美观度。
然而,在镀镍过程中可能会出现一些问题,如镀层不均匀、起泡、剥落等。
本文将对常见的镀镍问题进行描述,并提供相应的解决方案。
二、镀镍问题及解决方案1. 镀层不均匀问题描述:镀层出现明显的颜色差异,局部区域较厚,其他区域较薄。
可能原因及解决方案:- 镀液中的金属离子浓度不均匀:应检查镀液中金属离子的浓度,并进行调整。
- 镀液中的搅拌不均匀:应确保搅拌设备正常运作,并进行适当的调整。
- 镀液温度不稳定:应使用恒温设备控制镀液温度的稳定性。
2. 镀层起泡问题描述:镀层表面出现气泡,影响镀层的质量和外观。
可能原因及解决方案:- 镀液中存在杂质:应定期清洁镀液,去除杂质,保持镀液的纯净度。
- 镀液中的气体含量过高:应使用去气设备去除镀液中的气体。
- 镀液温度过高:应降低镀液的温度,避免过热引起气泡。
3. 镀层剥落问题描述:镀层与基材之间出现剥离现象,降低了镀层的附着力。
可能原因及解决方案:- 基材表面未经过充分处理:应确保基材表面清洁,去除油污和氧化物,增加镀层与基材的附着力。
- 镀液中的添加剂使用不当:应根据镀液的特性选择合适的添加剂,并按照规定的比例使用。
- 镀液中的酸碱度不适宜:应调整镀液的酸碱度,使其处于适宜的范围内。
4. 镀层颜色不符合要求问题描述:镀层的颜色与预期不符,无法满足客户的需求。
可能原因及解决方案:- 镀液中的添加剂使用不当:应根据所需颜色选择合适的添加剂,并按照规定的比例使用。
- 镀液中的金属离子浓度不适宜:应调整镀液中金属离子的浓度,以达到所需颜色。
- 镀液温度过高或过低:应控制镀液的温度,使其处于适宜的范围内。
5. 镀层出现氧化现象问题描述:镀层表面出现氧化物,影响镀层的质量和外观。
可能原因及解决方案:- 镀液中的氧含量过高:应使用除氧设备去除镀液中的氧气。
- 镀液中的添加剂使用不当:应根据镀液的特性选择合适的添加剂,并按照规定的比例使用。
镀镍问题与解决方案

镀镍问题与解决方案一、问题描述镀镍是一种常见的表面处理方法,用于提高金属制品的耐腐蚀性和装饰性。
然而,在镀镍过程中,可能会出现一些问题,如镀层不均匀、气泡、孔洞等。
这些问题会影响产品的质量和外观,因此需要找到相应的解决方案。
二、镀镍问题及解决方案1. 镀层不均匀问题描述:镀层在部分区域厚度不均匀,出现明显的颜色差异。
解决方案:- 检查电流密度:确保电流在整个镀镍过程中均匀分布,可以通过调整电流密度来解决问题。
- 检查镀液浓度:镀液浓度不均匀可能导致镀层不均匀,应确保镀液浓度均匀。
- 检查搅拌装置:搅拌装置的运行状况会影响镀液的流动性,进而影响镀层的均匀性,应确保搅拌装置正常运转。
2. 气泡问题问题描述:镀层表面出现气泡,影响镀层的光洁度和质量。
解决方案:- 检查镀液温度:镀液温度过高可能导致气泡产生,应控制镀液温度在适宜范围内。
- 检查镀液中的杂质:镀液中的杂质会促使气泡的形成,应定期清理镀液中的杂质。
- 检查镀液搅拌:充分搅拌镀液可以减少气泡的产生。
3. 孔洞问题问题描述:镀层表面出现孔洞,影响镀层的紧密性和耐腐蚀性。
解决方案:- 检查镀液成分:镀液成分不当可能导致孔洞的产生,应调整镀液成分以提高镀层的质量。
- 检查镀液pH值:镀液pH值过高或过低都会导致孔洞的产生,应保持镀液pH值在适宜范围内。
- 检查镀液搅拌:充分搅拌镀液可以减少孔洞的产生。
4. 其他问题除了上述常见的问题,镀镍过程中还可能出现其他问题,如黑斑、脱落等。
针对不同问题,可以采取以下解决方案:- 检查镀液中的杂质:杂质可能导致黑斑或脱落,应定期清理镀液中的杂质。
- 检查镀液温度和时间:温度和时间的控制可能影响镀层的质量,应确保镀液温度和时间在适宜范围内。
- 检查镀液pH值:pH值的不当可能导致镀层问题,应保持镀液pH值在适宜范围内。
三、总结镀镍过程中可能出现的问题包括镀层不均匀、气泡、孔洞等,这些问题会影响产品的质量和外观。
针对不同问题,可以采取相应的解决方案,如调整电流密度、镀液浓度、镀液温度和时间,清理镀液中的杂质等。
- 1、下载文档前请自行甄别文档内容的完整性,平台不提供额外的编辑、内容补充、找答案等附加服务。
- 2、"仅部分预览"的文档,不可在线预览部分如存在完整性等问题,可反馈申请退款(可完整预览的文档不适用该条件!)。
- 3、如文档侵犯您的权益,请联系客服反馈,我们会尽快为您处理(人工客服工作时间:9:00-18:30)。
化学镀镍的常见故障及解决办法:
(1)沉速低
镀液pH值过低:测pH值调整,并控制pH在下限值。
虽然pH值较高能提高沉速,但会影响镀液稳定性。
镀液温度过低:要求温度达到规范时下槽进行施镀。
新开缸第一批工件下槽时,温度应达到上限,反应开始后,正常施镀时,温度在下限为好。
溶液主成分浓度低:分析调整,如还原剂不足时,添加还原补充液;镍离子浓度偏低时,添加镍盐补充液。
对于上规模的化学镀镍,设自动分析、补给装置是必要的,可以延长连续工作时间(由30h延至56h)和镍循环周期(由6周延至11周)。
亚磷酸根过多:弃掉部分镀液。
装载量太低:增加受镀面积至1dm2/L。
稳定剂浓度偏重:倾倒部分,少量多次加浓缩液。
(2)镀液分解(镀液呈翻腾状,出现镍粉)
温度过高或局部过热:搅拌下加入温去离子水。
次亚磷酸钠大多:冲稀补加其它成分。
镀液的pH值过高:调整pH值至规范值。
机械杂质:过滤除去。
装载量过高:降至1dm2/L
槽壁或设备上有沉淀物:滤出镀液,退镀清洗(用3HNO3溶液)。
操作温度下补加液料大多:搅拌下少量多次添加。
稳定剂带出损失:添加少量稳定剂。
催化物质带入镀液:加强镀前清洗。
镀层剥离碎片:过滤镀液。
(3)镀层结合力差或起泡
镀前处理不良:提高工作表面的质量,加工完成后应清除工件上所有的焊接飞溅物和焊渣。
工件表面的粗糙度应达到与精饰要求相当的粗糙义,如碳钢工件表面粗糙度Ra<1.75μm时,很难获得有良好附着力的镀层;对于严重锈蚀的非加工表面,可用角向磨光机打磨,最好采用喷砂或喷丸处理;工件镀前适当的活化处理可以提高镀层的附着力。
如合金钢、钛合金可用含氟化物的盐酸活化后,与碳钢件混装施镀;高级合金钢和铅基合金预镀化学镍;碳钢活化时注意脱碳。
温度波动太大:控制温度在较小的范围波动。
下槽温度太低:适当提高下槽温度。
清洗不良:改进清洗工序。
金属离子污染:用大面积废件镀而除去。
有机杂质污染:活化炭1-2g/L 处理。
热处理不当:调整热处理时间和温度。
(4)镀层粗糙
镀液浓度过高:适当冲稀镀液。
镀液的pH值过高:降低pH值至规范值。
机械杂质:过滤除去。
亚磷酸盐过高:弃掉部分镀液。
加药方法不对:不可直接加固体药品或用镀液溶解药品。
清洗不够,带入污染:加强清洗。
络合剂浓度偏低:补充络合剂。
工艺用水污染:使用去离子水或蒸馏水。
(5)镀层不完整(漏镀)
前处理不当、镀件局部钝化或油污、清洗水不干净等:加强前处理,更换清洗水。
装挂不对有气袋:改进装挂方法、抖动工件、变换位置等。
十二烷基硫酸钠污染:活性炭吸附。
金属离子污染:除去(见上述),过滤。
底金属影响:镀前闪镀镍。
稳定剂过量:弃去部分镀液。
(6)镀层针孔(通常镀层厚度达10μm以上是无孔)
工件前处理不当和酸洗后停留时间过长:提高工件表面加工质量,酸洗后应在30s内进入镀液。
pH值过高:降低pH值。
镀液组份变质和老化:报废镀液。
悬浮不溶物:过滤除去。
装载量过大:减至1dm2/ L,降低pH值。
金属离子污染:除去。
对于含pb、cd、Zn、Sn等元素的基材,在施镀镍前,最好电镀1~5μm 的镍打底,以阻止有害元素进入镀液。
搅拌不充分:摆动工作。
有机杂质污染:活性炭处理。
(7)镀液不沉积镍
稳定剂浓度过高:弃去部分镀镍。
表面未活化:改进镀前处理工艺。
表面非催化:镀前表面催化处理
镀液pH值、温度过低:调整之。
金属离子污染:加1~2g/L活性炭过滤,通电处理。
(8)pH值变化快
前处理溶液带入:改进清洗工序。
装载量太大:减少受镀面积。
pH值出范围:调pH至最佳范围。
(9)镍离子消耗过快
槽壁和设备镀上镍:处理方法同(2)--⑥
载量太大:减少装载量。
液分解:滤去镀液分析调整或报废。
补充硫酸镍不及时:补加主盐。
(10)镀层光亮度下降、发黑或不均匀
镀液过度浓缩(水份蒸发超过30):补水
镀液老化(使用寿命达6周期):报废旧液。
络合剂用错或络合剂、稳定剂变质:无法恢复镀液性能时只能将镀液报废。
施镀条件不当,如pH值或温度过高,溶液搅拌和工件阴极移动不良等:调低pH值至规定值的下限,当镀液寿命超过2周期时,pH值控制在4.2为好。
但pH=3.5---4.0之间也能得到光亮的镀层;良好的镀液搅拌系统工程和工件移动以及低温施镀都有利于提高镀层光亮度。
并控制镀液流速<0.3m/s避免造成漏镀。
有机杂质污染:处理方法同(3)---⑥。
前处理不充分:加强前处理。
(11)镀层有麻点
工件表面光洁度较低:尽量提高工件的表面质量。
在施镀时调整pH值:施镀时不调pH值。
镀液不稳定和镀液中悬浮颗粒较多:加强过滤,补充一定的稳定剂。
工件摆放位置不当:工件较重要的表面朝下或竖直成90o,并将工件预热到70oC以上施镀,可改善工件向上的光洁度。
(12)镀层厚度不均匀(可以看到镀液中气泡的析出量较正常情况下要多)
由于工件几何形状影响工件表面上的氢气逸出不易,有妨碍氢气顺利排出的部位可能造成镀层较薄:最好采用滚镀法。
对于较大的工件也应尽可能性在施镀过程中移动、镀液搅拌、降温等,以利于氢气的排出,提高镀层厚度的均匀性。
工件材质不同:不同材料的化学镀镍速度是不同的,所以不同材质的工件一起施镀时,必须分别测量不同材质工件的镀层厚度。
(13)镀层表面化有大量"花斑",局部有暗色条纹或斑块状沉积物(用10倍放大镜观察)前处理清洗不良,工件表面粘附了某些杂质:更换洗净剂,镀层恢复了均匀的光亮表面。
(14)镀液中毒(工件上的析氢量较正常情况下多,且沉积速度很慢)
稳定剂过量:通电处理。
(工件作阴极,不锈钢件阳极,Dk=0.6~1.0A/dm2电解1~5min;将镀液置于80oC保温24h;如镀液还不行,最好将镀液储存起来,分批与新镀液混合使用。
缓蚀剂污染镀液:酸洗液中缓蚀剂的加入要慎重,要防止微量缓蚀剂带入镀槽中。
(15)镀槽不沉积镀层
镀液中产生一些固体颗粒:将镀液打入备用槽,再用30(wt)HNO3在40OC下清洗(不能冷洗),钝化镀槽5h,然后用水洗净硝酸,再用干净棉纱擦洗镀槽上附着物。
用清水清洗干净。
镀槽的防镀效果不好:为了防止镀槽上沉积镀层,必须采取相应的防镀方法。
据称,采用阳极保护法时,以工件作为阴极和参比电极效果好。
在75~85OC的镀液中维持不锈钢镀槽相对施镀的工件的参比电位为+350~550mv时,镀槽有良好的钝化性能。
此时的阳极电流密度为20~90mA/m2。
当机械杂质进入镀槽或镀槽上有镀层产生时,其维钝电流将有所上升,但很快将下降至正常水平。
这样防镀效果好,并且可以提高镀速10~20,而且对镀层质量无显著影响。
加热管功率与其表面积之比不当:同样功率的加热管,应作得尽量长一些,管子粗一些,缩小加热管,应作得尽量长一些,管子粗一些,缩小加热管功率与其表面积之比。
施镀设备及挂具用硝酸清洗不够:每次开缸前用硝酸浸泡镀槽、加热管、挂具、滚筒等,即使没有发现镍镀层也应这样做。
(16)镀液混浊
主盐、还原剂浓度超过上限:调整溶液。
络合剂浓度低:补充络合剂。
pH值过高:降低镀液pH值。
(17)槽液不环保,不能通过SGS认证测试,污染环境,废液处理成本高
使用环保的化学镀镍液,如环保化学镀镍光亮剂、环保化学镀镍稳定剂等,这样不但增加产品的质量和稳定性,而且镀液环保,废液易处理排放,成本底。