ANSYS优化设计
ANSYS优化设计设计优化技术

ANSYS优化设计设计优化技术ANSYS优化设计是一种基于计算机仿真和数值分析的设计优化方法。
它利用ANSYS软件平台上的多物理场问题求解器和优化算法,对设计进行高效、全面的优化。
通过不断迭代求解和更新设计参数,最终达到设计性能的最优化。
ANSYS优化设计涵盖了多个领域的设计问题,例如结构优化、流体优化、电磁优化等。
在结构优化中,可以通过调整材料属性、几何形状和连接方式等设计参数,使结构在承受最大载荷的同时,尽可能地减少重量和成本。
在流体优化中,可以通过调整流体流动的速度、方向和阻力等设计参数,使流体系统的效率和性能得到最大化。
在电磁优化中,可以通过调整电磁场的分布和强度等设计参数,实现电磁设备的最佳性能。
ANSYS优化设计的核心是优化算法。
ANSYS提供了多种优化算法,包括遗传算法、进化算法、粒子群算法等。
这些算法可以根据设计问题的特点和约束条件选择合适的优化策略,并通过不断地试验和调整设计参数,逐步优化设计方案。
优化设计的目标通常是在一定的约束条件下,使设计满足最大化性能、最小化成本或达到特定的指标要求。
使用ANSYS进行优化设计需要以下几个步骤。
首先,确定优化目标和约束条件。
这包括定义设计的性能要求、约束条件、可变参数范围等。
其次,建立数学模型。
将设计问题转化为数学方程组,并确定相关参数之间的关系。
然后,选择合适的优化算法。
根据设计问题的特点和约束条件,选择合适的优化算法进行求解。
最后,进行多次迭代求解。
根据优化算法的要求,通过不断地更新设计参数,逐步接近最优解。
ANSYS优化设计具有以下优势。
首先,通过仿真和数值分析,可以提前发现并解决设计中的问题,减少试错成本。
其次,可以在多个设计方案中比较和选择最优解,提高设计性能。
第三,使用计算机仿真和优化算法,可以大大缩短设计周期,提高设计效率。
最后,ANSYS提供了丰富的优化设计工具和资源,使设计工程师可以更好地应用和掌握优化设计技术。
总之,ANSYS优化设计是一种基于计算机仿真和数值分析的设计优化方法。
第五章ANSYS优化设计
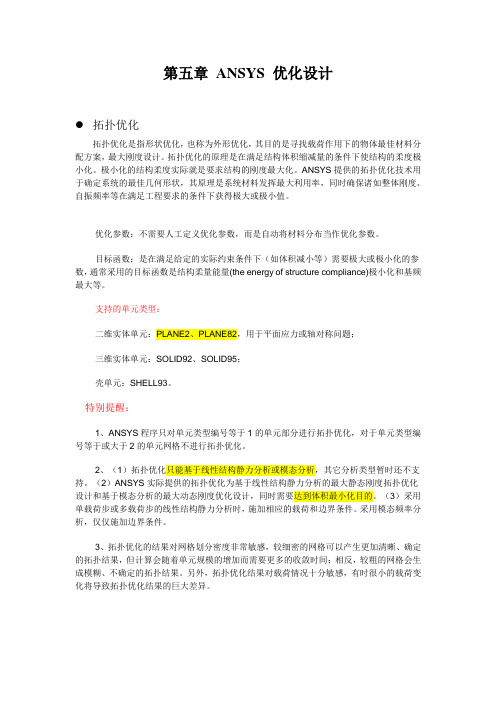
第五章ANSYS 优化设计拓扑优化拓扑优化是指形状优化,也称为外形优化,其目的是寻找载荷作用下的物体最佳材料分配方案,最大刚度设计。
拓扑优化的原理是在满足结构体积缩减量的条件下使结构的柔度极小化。
极小化的结构柔度实际就是要求结构的刚度最大化。
ANSYS提供的拓扑优化技术用于确定系统的最佳几何形状,其原理是系统材料发挥最大利用率,同时确保诸如整体刚度、自振频率等在满足工程要求的条件下获得极大或极小值。
优化参数:不需要人工定义优化参数,而是自动将材料分布当作优化参数。
目标函数:是在满足给定的实际约束条件下(如体积减小等)需要极大或极小化的参数,通常采用的目标函数是结构柔量能量(the energy of structure compliance)极小化和基频最大等。
支持的单元类型:二维实体单元:PLANE2、PLANE82,用于平面应力或轴对称问题;三维实体单元:SOLID92、SOLID95;壳单元:SHELL93。
特别提醒:1、ANSYS程序只对单元类型编号等于1的单元部分进行拓扑优化,对于单元类型编号等于或大于2的单元网格不进行拓扑优化。
2、(1)拓扑优化只能基于线性结构静力分析或模态分析,其它分析类型暂时还不支持。
(2)ANSYS实际提供的拓扑优化为基于线性结构静力分析的最大静态刚度拓扑优化设计和基于模态分析的最大动态刚度优化设计,同时需要达到体积最小化目的。
(3)采用单载荷步或多载荷步的线性结构静力分析时,施加相应的载荷和边界条件。
采用模态频率分析,仅仅施加边界条件。
3、拓扑优化的结果对网格划分密度非常敏感,较细密的网格可以产生更加清晰、确定的拓扑结果,但计算会随着单元规模的增加而需要更多的收敛时间;相反,较粗的网格会生成模糊、不确定的拓扑结果。
另外,拓扑优化结果对载荷情况十分敏感,有时很小的载荷变化将导致拓扑优化结果的巨大差异。
优化设计1. 简介举例:如何在原材料消耗最少情况下,使水杯的容积最大。
ANSYS优化设计_练习
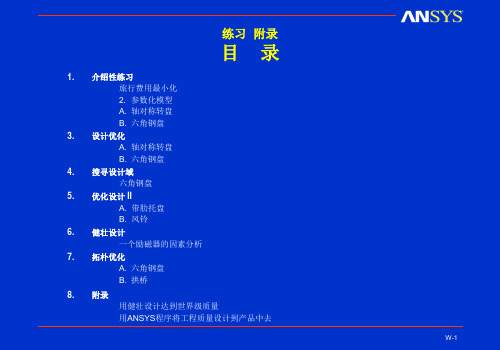
• NPT = 10 • X,Y,Z = hub_ro+xmid, ymid, 0
• [OK] 5. 将活动坐标系转到全局柱坐标系。这将允许我们创建一个样条曲线并指定 qhub and qrim.为其端部斜率: – Utility Menu > WorkPlane > Change Active CS to > Global Cylindrical
练习 附录
目
1. 介绍性练习 旅行费用最小化 2. 参数化模型 A. 轴对称转盘 B. 六角钢盘
录
3.
设计优化 A. 轴对称转盘 B. 六角钢盘
搜寻设计域 六角钢盘 优化设计 II A. 带肋托盘 B. 风铃 健壮设计 一个励磁器的因素分析 拓朴优化 A. 六角钢盘 B. 拱桥 附录 用健壮设计达到世界级质量 用ANSYS程序将工程质量设计到产品中去
– (Design Opt >) -Design Sets- List… • 选择 Best Set,然后 [OK] – (Design Opt >) -Design Sets- List…
• 选择 ALL Sets,然后 [OK]
W-6
1. 介绍性练习 旅行费用最小化
12. 画出速度对旅行费用曲线: – (Design Opt >) -Design Sets- Graphs/Tables…
E = 30e6 psi r = 7.2e-4 lb-s2/in4 n = 0.3
1.6 qhub xmid ymid qrim
基于ANSYS的结构优化设计方法

ωL 1
≤ω1
≤ωU1
( 12 )
因此 ,不但要对结构进行静力分析 ,还要进行模态分析
并判断其一阶固有频率是否满足式 ( 12) 。利用 ANSYS经过
44次迭代 ,得到较理想的结果 。优化过程如表 4所示 。
(下转第 150页 )
四川建筑 第 29 卷 3 期 200 9. 0 6
147
·工 程 结 构 ·
【关键词 】 结构优化 ; 桁架系统 ; 动力优化
【中图分类号 】 TU311. 41 【文献标识码 】 B
在钢结构工程中 ,钢材的用量是非常巨大的 ,这其中不 免会存在材料安全储备太高 ,过于浪费的情况 。如何在保证 结构安全的情况下 ,减少钢材用量 ,降低成本 ,这正是本文研 究的意义所在 。结构优化设计是在满足各种规范或某些特 定要求的条件下 ,使结构的某种指标 (如重量 、造价 、刚度或 频率等 )达到最佳的设计方法 。该方法最早应用在航空工程 中 ,随着计算机的快速发展 ,很快推广到机械 、土木 、水利等 工程领域 。它的出现使设计者从被动的分析 、校核进入主动 的设计 ,这是结构设计上的一次飞跃 [1 ] 。ANSYS作为大型 工程计算软件 ,其模拟分析功能非常强大 ,掌握并使用 AN2 SYS对结构进行模拟 、计算 、优化 ,对提高材料利用率 、减少 成本 ,是很有效的 。
265
341
466
306
59. 2 41. 9 26. 1 0. 01 0. 20 0. 29 0. 17 31. 6 262
264
341
464
296
59. 2 41. 9 26. 1 0. 01 0. 08 0. 28 0. 17 31. 6 262
264
利用ansysAPDL进行优化设计的例子

利用ansys APDL 进行优化设计的例子一、问题描述:约束条件;1.总应力不超过"max2, 梁的变形不超过8m*3, 梁的高度不超过hm^x目标函数:使梁的重量最小二、分析文件的APDL语句及注释:(可把该文件拷贝到一个文本文件,作为ansys的分析文件。
)!第一步,初始化ANSYS系统环境FINISH/CLEAR/filename,BeamOpt!第二步,定义参数化设计变量B=1.4 !初始化宽度H=3.8 !初始化高度!第三步,利用参数创建有限元模型/PREP7 !进入前处理ET,1,BEAM3 !定义单元类型为BEAM3AREA=B*H !梁的截面积ETABLE,SMAX_I,NMISC,1 !每个单元I 节点处应力的最大值ETABLE,SMAX_J,NMISC,3 !每个单元J 节点处应力的最大值!绕Z 轴的转动惯量FILLE,1,2EGEN,10,1,-1 FINISH !第四步,执行求解 /SOLUANTYPE,STATICD,1,UX,0,,11,10,UYSFBEAM,ALL,1,PRES,20 !施加压力(单位长度上的负荷) =20SOLVEFINISH!第五步,进入后处理并创建状态变量与目标变量 /POST1SET,,,,!对单元表求和 *GET,VOLUME,SSUM,,ITEM,VOLU ! 得到总的体积ESORT,ETAB,SMAX_I,,1!按照单元SMAX_I 的绝对值大小排序 *GET,SMAXI,SORT,,MAX!参数 SMAXI=SMAX_I 中的最大值 ESORT,ETAB,SMAX_J,,1!按照单元SMAX_J 的绝对值大小排序 *GET,SMAXJ,SORT,,MAX !参数 SMAXJ=SMAX_J 中的最大值R,1,AREA,IZZ,H !定义单元实常数,以设计变量表示 MP,EX,1,30E6 MP,PRXY,1,0.3N,1!创建节点1 N,11,120!创建节点11NSORT,U,Y !以Uy 为基准对节点排序 *GET,DMAX,SORT,,MAX !参数DMAX=最大位移ETABLE,VOLU,VOLU !VOLU=每个单元的体积SSUMSMAX=SMAXI>SMAXJ !找到最大的应力FINISH三、优化过程的菜单方式实现1、1、读入分析文件进行分析:2、进入。
基于ANSYS的车架结构优化设计
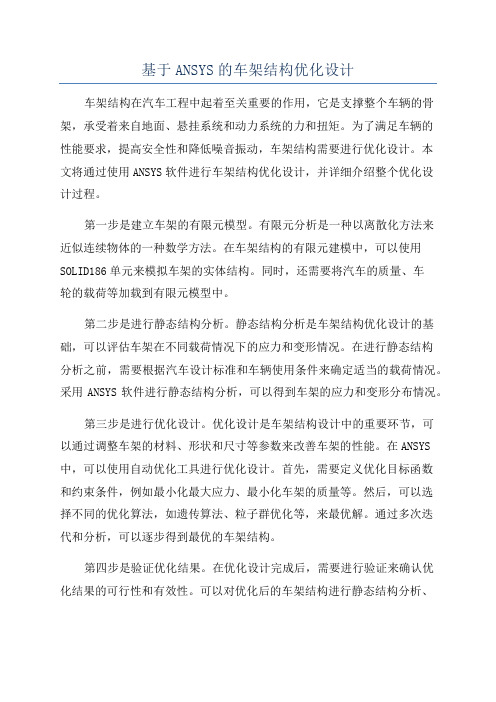
基于ANSYS的车架结构优化设计车架结构在汽车工程中起着至关重要的作用,它是支撑整个车辆的骨架,承受着来自地面、悬挂系统和动力系统的力和扭矩。
为了满足车辆的性能要求,提高安全性和降低噪音振动,车架结构需要进行优化设计。
本文将通过使用ANSYS软件进行车架结构优化设计,并详细介绍整个优化设计过程。
第一步是建立车架的有限元模型。
有限元分析是一种以离散化方法来近似连续物体的一种数学方法。
在车架结构的有限元建模中,可以使用SOLID186单元来模拟车架的实体结构。
同时,还需要将汽车的质量、车轮的载荷等加载到有限元模型中。
第二步是进行静态结构分析。
静态结构分析是车架结构优化设计的基础,可以评估车架在不同载荷情况下的应力和变形情况。
在进行静态结构分析之前,需要根据汽车设计标准和车辆使用条件来确定适当的载荷情况。
采用ANSYS软件进行静态结构分析,可以得到车架的应力和变形分布情况。
第三步是进行优化设计。
优化设计是车架结构设计中的重要环节,可以通过调整车架的材料、形状和尺寸等参数来改善车架的性能。
在ANSYS 中,可以使用自动优化工具进行优化设计。
首先,需要定义优化目标函数和约束条件,例如最小化最大应力、最小化车架的质量等。
然后,可以选择不同的优化算法,如遗传算法、粒子群优化等,来最优解。
通过多次迭代和分析,可以逐步得到最优的车架结构。
第四步是验证优化结果。
在优化设计完成后,需要进行验证来确认优化结果的可行性和有效性。
可以对优化后的车架结构进行静态结构分析、模态分析和疲劳寿命分析等,来评估车架的性能和可靠性。
如果结果满足要求,就可以进行后续的制造和测试。
总之,基于ANSYS的车架结构优化设计可以帮助工程师更好地理解和改善车架的性能。
通过使用ANSYS软件进行有限元建模、静态结构分析、优化设计和验证,可以得到最优的车架结构,提高汽车的性能和安全性。
同时,车架结构优化设计还可以减少材料的使用和降低成本,对环境也有积极的意义。
基于ANSYS workbench的汽车传动轴有限元分析和优化设计
基于ANSYS workbench的汽车传动轴有限元分析和优化设计使用ANSYS Workbench进行汽车传动轴的有限元分析和优化设计是一种常见的方法。
以下是基于ANSYS Workbench的汽车传动轴有限元分析和优化设计的一般步骤:1.创建几何模型:使用CAD软件创建传动轴的几何模型,并将其导入到ANSYS Workbench中。
确保几何模型准确、完整,并符合设计要求。
2.网格划分:对传动轴几何模型进行网格划分,将其划分为离散的单元。
选择合适的网格划分方法和单元类型,以确保模型的准确性和计算效率。
3.材料属性定义:定义传动轴所使用的材料的力学性质,如弹性模量、泊松比、密度等。
确保选择适当的材料模型,以准确模拟材料的行为。
4.载荷和约束定义:定义施加在传动轴上的载荷,如扭矩、轴向力等。
同时,定义约束条件,如固定轴承端点、自由转动等。
5.设置分析类型和求解器:根据实际情况选择适当的分析类型,如静态、动态、模态等。
配置求解器设置,选择合适的求解器类型和参数。
6.进行有限元分析:运行有限元分析,计算传动轴的应力、变形和振动等。
根据分析结果,评估传动轴的性能和强度。
7.优化设计:根据有限元分析的结果,对传动轴的结构进行优化设计。
通过调整传动轴的几何形状、材料或其他参数,以提高其性能。
8.重新进行有限元分析:对优化后的设计进行再次有限元分析,以验证优化结果。
如果需要,可以多次进行重复优化和分析的步骤。
9.结果评估和优化验证:评估优化结果的有效性,并验证传动轴在实际工况下的性能。
根据需求进行修正和改进。
请注意,基于ANSYS Workbench的有限元分析和优化设计需要一定的专业知识和技能。
基于ANSYS的风扇设计与优化
基于ANSYS的风扇设计与优化一、引言风扇是一种常见的动力工具,广泛应用于家用电器、车辆、建筑等领域。
良好的风扇设计和优化可以提高工作效率和节能性能,为各行各业带来巨大的经济和环境收益。
本文将介绍基于ANSYS的风扇设计与优化的方法和实践,力图提供一个全面的指导。
二、风扇设计的基本原理1.风扇的工作理论风扇是通过旋转叶片产生气流,利用气流的动能对周围空气进行运动的装置。
其工作原理是将旋转动能转化为风速和压力。
风扇的关键参数包括风量、风速和静压。
2.风扇的主要构件风扇由电机、叶轮和外壳组成。
电机提供动力,叶轮是产生气流的关键部分,外壳起到引导气流的作用。
三、基于ANSYS的风扇设计与优化实践1.建立风扇模型首先,在ANSYS软件中,我们需要建立一个风扇的三维模型。
可以使用CAD 模型导入、参数化建模等方法。
接下来,通过划分网格,提高模型的精度和计算效率。
2.流体动力学模拟在建立了风扇模型后,通过ANSYS的流体动力学(CFD)模块进行模拟分析。
CFD模块可以模拟风扇在不同工况下的气流特性,如风速、风量和静压等。
通过调整叶片的形状和数量,可以改变风扇的气流性能。
3.模拟结果分析根据CFD模拟的结果,可以对风扇的气流性能进行评估和分析。
比如,可以通过观察叶轮上的压力分布、流线图和速度云图等来判断风扇的工作效果。
同时,也可以对比不同设计方案的性能差异,选择最佳的风扇设计方案。
4.优化设计根据模拟结果的分析,我们可以进一步优化风扇的设计。
比如,可以通过调整叶片的形状和数量来改变风扇的工作效率和噪声水平。
还可以通过优化叶轮和外壳之间的匹配关系,减少内部的漏风和压力损失。
5.验证与改进进行优化设计后,需要对改进后的风扇进行验证。
可以通过建立物理原型并进行实验测试来验证CFD模拟的准确性。
如果实验结果与模拟结果一致,说明优化设计是可行的。
如果存在差异,则需要对模型进行进一步改进和优化。
四、风扇设计与优化的挑战与展望1.挑战风扇设计与优化面临着诸多挑战。
基于ANSYS的机械结构强度计算及优化设计
基于ANSYS的机械结构强度计算及优化设计随着科技的不断发展,机械结构在各行各业中扮演着至关重要的角色。
为确保机械结构的安全性和可靠性,强度计算和优化设计成为了不可忽视的环节。
本文将介绍如何利用ANSYS软件进行机械结构的强度计算及优化设计,旨在提升产品的质量和性能。
1. 强度计算的基本原理强度计算是指通过数学方法和有限元分析等技术手段,预测机械结构在特定工况下的受力状态和应力分布,以评估其承载能力和强度情况。
ANSYS作为一款强大的有限元分析软件,提供了丰富的分析工具和模拟功能,可以高效准确地进行机械结构的强度计算。
2. 剖析ANSYS软件的应用ANSYS软件支持用户对机械结构模型进行网格划分、材料属性定义、加载条件设置等操作,并可以对结构进行静力、动力、热力学等方面的强度计算。
在进行强度计算之前,用户需要先建立准确的模型,并进行网格划分。
通过选择各个部件的材料属性和相应的加载条件,可以模拟出真实工况下机械结构的受力状态。
3. 强度计算结果的分析在进行强度计算后,ANSYS能够生成大量的数据和图形,如应力云图、位移变形图、应力分布图等。
通过这些图形和数据,用户可以直观地了解机械结构的受力情况,进而分析结构的强度和刚度情况。
根据实际需求,用户可以对强度计算结果进行进一步的优化设计。
4. 优化设计的思路和方法机械结构的优化设计是通过对结构形状、材料和参数等方面的调整,以达到优化目标的一种方法。
在进行优化设计时,考虑到机械结构的复杂性和多变性,我们可以采用基于ANSYS软件的仿真和优化技术。
通过设置设计变量、约束条件和优化目标,可以对机械结构进行参数优化和拓扑优化,从而改善结构的性能。
5. 优化设计案例分析以一个机械零部件的优化设计为例,首先在ANSYS中建立机械结构的有限元模型并进行强度计算。
然后,设定设计变量和约束条件,以降低结构的重量和提高承载能力为优化目标,利用优化算法进行设计迭代。
通过多次迭代计算和评估,最终获得一个满足设计要求的优化结构。
利用ANSYS进行优化设计时的几种优化算法
利用ANSYS进行优化设计时的几种优化算法优化技术理解计算机程序的算法总是很有用的,尤其是在优化设计中。
在这一部分中,将提供对下列方法的说明:零阶方法,一阶方法,随机搜索法,等步长搜索法,乘子计算法和最优梯度法。
(更多的细节参见ANSYS Theory Reference 第20章。
)零阶方法零阶方法之所以称为零阶方法是由于它只用到因变量而不用到它的偏导数。
在零阶方法中有两个重要的概念:目标函数和状态变量的逼近方法,由约束的优化问题转换为非约束的优化问题。
逼近方法:本方法中,程序用曲线拟合来建立目标函数和设计变量之间的关系。
这是通过用几个设计变量序列计算目标函数然后求得各数据点间最小平方实现的。
该结果曲线(或平面)叫做逼近。
每次优化循环生成一个新的数据点,目标函数就完成一次更新。
实际上是逼近被求解最小值而并非目标函数。
状态变量也是同样处理的。
每个状态变量都生成一个逼近并在每次循环后更新。
用户可以控制优化近似的逼近曲线。
可以指定线性拟合,平方拟合或平方差拟合。
缺省情况下,用平方差拟合目标函数,用平方拟合状态变量。
用下列方法实现该控制功能:Command: OPEQNGUI: Main Menu>Design Opt>Method/ToolOPEQN同样可以控制设计数据点在形成逼近时如何加权;见ANSYS Theory Referenc e。
转换为非约束问题状态变量和设计变量的数值范围约束了设计,优化问题就成为约束的优化问题。
ANS YS程序将其转化为非约束问题,因为后者的最小化方法比前者更有效率。
转换是通过对目标函数逼近加罚函数的方法计入所加约束的。
搜索非约束目标函数的逼近是在每次迭代中用Sequential Unconstrained Minimization Technique(SUMT) 实现的。
收敛检查在每次循环结束时都要进行收敛检查。
当当前的,前面的或最佳设计是合理的而且满足下列条件之一时,问题就是收敛的:& #61548; 目标函数值由最佳合理设计到当前设计的变化应小于目标函数允差。
- 1、下载文档前请自行甄别文档内容的完整性,平台不提供额外的编辑、内容补充、找答案等附加服务。
- 2、"仅部分预览"的文档,不可在线预览部分如存在完整性等问题,可反馈申请退款(可完整预览的文档不适用该条件!)。
- 3、如文档侵犯您的权益,请联系客服反馈,我们会尽快为您处理(人工客服工作时间:9:00-18:30)。
x1 x2 X= . =[x1,x2…x3] T : xn
(7-1)
式(7-1)的意义在于表示了“设计空间”的概念,即以n个设计变量 为坐标轴组成的实空间。这个设计空间成为n纬欧氏空间,用Rn表 示。
2001年6月1日 7-3
当n=2,如例7-2中悬臂梁,则有: x1 d X= = x2 l 此时,设计空间是以x1,x2为坐标轴的平面,平面上任一点的 坐标对应着一个二维设计变量。 X=[x1x2]T代表了一个设计方案。 当n=3时,例如7-1中贮料箱,由三个设计变量组成一个3维设计空 间,空间内任一点的坐标对应着一个三维设计变量X=[x1x2x3]T。同 样,向量X代表了一个设计方案。 依此类推,当n>3时,其n个设计变量x1,x2,…xn组成的空间成为超 越空间。 设计空间是所有设计方案的集合,表示为: XRn
(7-2)
2001年6月1日
7-4
2.目标函数
优化设计是要在多种因素下寻求使人最满意、最 适宜的一组参数。这里的“最满意”是针对某一特定 目标而言的。根据特定目标建立起来的、以设计变量 为自变量的、一个可计算的函数称为目标函数,它是 设计方案评价的标准。 优化设计的过程实际上是寻求目标函数最小值或 最大值的过程。因为求目标函数的最大值可转换为求 负的最小值,故目标函数统一描述为: minF (X)=F (x1,x2,…xn) (7-3)
2001年6月1日
7-9
(2)性能约束 又称性态约束,是由某种设计性能或指标推导出来的一种约 束条件。属于这类设计约束的如零件的工作应力、应变的限制; 对震动频率、震幅的限制;对传动效率、温升、噪声、输出扭矩 波动最大值等的限制;对运动学参数如位移、速度、转速、加速 度的限制等。这类约束条件,一般可以根据设计规范中的设计公 式或通过物理学和力学的基本分析导出的约束函数来表示。如例 7-2中,悬臂梁设计弯曲强度条件Pl/(0.1d3 )<=[б ],扭转强度条件 M/(0.2d³ )<=[τ ] ,刚度条件Pl3 /(3EJ)<=[ƒ]。已知 [б ] = 100N/mm2 ,[τ ] =75/Nmm2 ,[ƒ]=0.1mm,E=7.03*104 N/mm², 可导出性能约束条件为: g5 (X) =g5 (d, l) = (d3/l) -1000>=0 g6 (X) =g6 (d, l) = d3 -6666.6>=0 g7(X) =g7 (d, l) = (d4/l3) –9.65>=0
2001年6月1日
7-6
F(x1)
a)
图 7.2 目标函数与设计变量之间的关系及等值线 a)曲线 b)曲面
b)
2001年6月1日
7-7
3 .约束条件
在实际问题中,设计变量不能任意选择,必须满足某些 规定的功能和其它要求。为产生一个可接受的设计而对设计 变量取值施加的种种限制称为约束条件。约束条件一般表示 为设计变量的不等式约束和等式约束函数形式: g i(X)= g i (x1,x2,…xn)>=0 或 g i(X)= g i (x1,x2,…xn)<=0 (i=1,2,…m) (7-4) h j(X)=h j(x1,x2,…xn)=0 (j=1,2,…,p<n)
和等式约束条件数目。 式中m,p分别表示施加与该项设计的不等式约束条件数目
20能约束两种。 (1)边界约束 又称区域约束,表示设计变量的物理限制和取值范围。如例71中贮料箱设计,可得边界约束条件为: g1 (x) = g1 (l, w, h) = w-1.6>=0 g2 (x) = g2 (l, w, h) = l>0 g3(x) = g3 (l w, h) = h>0 再如例7-2中悬臂梁设计,可得边界约束条件为: g1 (x) = g1 (d, l) = d-20>=0 g2 (x) = g2 (d, l) = 100-d>=0 g3 (x) = g3 (d, l) = l-50>=0 g4 (x) = g4 (d, l) = 150-l>=0
2001年6月1日
7-1
例7-2 设计一圆形截面悬臂梁(见图7.1)。该悬臂梁自由端作用 有集中载荷P=10000N;扭矩M=10N.m;悬臂伸出长度的允许取 值范围为50mm ≤ L ≤ 150mm,直径的允许取值范围为20mm ≤ d ≤ 100mm。要求在满足强度、刚度条件下,体积最小。其设计变 量是棒料直径d和悬臂长度 L 。
2001年6月1日
7-5
目标函数与设计变量之间的关系可以用几何图形 形象地表示出来。例如,单变量时,目标函数是二维 平面上的一条曲线(图7.2a);双变量时,目标函数是 三维空间的一个曲面(图7.2b)。曲面上具有相同目标 函数值的点构成了曲线,该曲线称为等值线(或等高 线)。如 图7.2b所示,在等值线a上的所有点,其目标 函数值均为15,在等值线c上的各点(设计点),目 标函数值均为25等等。将其投影到设计空间是一族 近似的共心椭圆,他们共同的中心点就是最优点(图 7.2b 中的P点)。因此形象地说,优化设计就是近似 地求出这些共心椭圆的中心。若有n个设计变量时,目 标函数是n+1维空间中的超曲面,难于用平面图形表示。 例7-1中贮料箱优化设计的目标函数可表示为: minF(X) F(X)=F(l,w,h)=2 ( l h+w h)+l w (X=[l,w,h]T)
P
d
M
L
图7.1 悬臂梁
2001年6月1日 7-2
机械设计常用的设计变量有:几何外形尺寸(如长、宽、高、 厚等);材料性质;速度、加速度、效率、温度等。机械优化设 计时,作为设计变量的基本参数,一般是一些相互独立的参数, 它们的取值都是实数。根据设计要求,大多数设计变量被认为是 有界连续变量,称为连续量。但在一些情况下,有的设计变量取 值是跳跃式的量,例如齿轮的齿数、模数,丝杠的直径和螺距等, 凡属这种跳跃式的量称为离散量。对于离散变量,在优化设计过 常常把它视为连续量,在求得一个是实用的最优方案。 一项设计,若有n个设计变量x1,x2,…xn,可以按一定次序排 列,用n维列向量来表示,即:
§7.1
基本概念和术语
优化设计要解决的关键问题:一是建立设计数学模型,即优化设计 问题的目标函数、约束条件和设计变量;二是选择适用的优化方法。 1 .设计变量 设计中,可以用一组对设计性能指标有影响的基本参数来表示某 个设计方案。设计问题的性质不同,则表示该设计的参数也不同。 对一项具体的机械设计来说,有些基本参数可以根据工艺、安装和 使用要求预先确定,而另一些则需要在设计过程中进行选择。那些 需要在设计过程中进行选择的基本参数被称为设计变量。 例7-1: 设计一开口矩形贮料箱,容积为2.4m³ ,宽度不小于1.6m, 要求用料最省。显然,这项简单设计的设计变量是矩形贮料箱的长l、 宽 w 、高 h 。