发电厂A引风机叶片断裂原因分析报告
锅炉引风机叶片断裂原因分析及解决措施初探

锅炉引风机叶片断裂原因分析及解决措施初探作者:刘建新来源:《科技风》2017年第11期摘要:在火电中,引风机是非常重要的一种设备,位于锅炉中的送引风系统,通常被安装在烟道的除尘器与烟囱之间的位置,起到从炉膛中吸出烟气并排入烟囱的作用。
一直以来,很多电厂中会出现300MW锅炉引风机叶片断裂的事故,这些事故一直都是相关领域的技术人员研究的重点,电厂在社会建设中是不可缺少的一部分,这种事故会让电厂的生产受到严重的影响,影响电力的生产和输送,对社会生产和人们的生活造成影响。
本文对300MW锅炉引风机叶片断裂的原因进行详细的分析,并提出解决的措施,希望能够为我国火电的发展提供借鉴。
关键词:300MW锅炉;引风机;叶片断裂我国大多数的火电产生烟气中,含尘量非常大,引风机在火电中应用范围非常广,引风机中叶片转动的速度很快,因此很容易造成磨损。
烟气中的含尘量也是让叶片不断损坏的原因。
长期处于高温、高尘的工作环境,颗粒带有严重的腐蚀性,引风机中由于不断流动的灰粒,叶片的腐蚀和磨损都是不可避免的,这其中带来的隐患也是非常严重,300MW锅炉引风机叶片断裂就是本文要研究的重点。
一、300MW锅炉引风机叶片断裂原因(一)空气动力学分析以空气动力学的角度进行分析,300MW锅炉引风机叶片结构在运行中,要承受巨大的风压,而受到风压冲击最大的部位,就是迎风侧面,这一位置有些地方是焊接而成,在整个引风机中算是比较脆弱的位置,风压对其产生的压力本来就非常大,而不断吸引的烟气中,含有大量的飞灰及烟尘,这就导致这些焊接处是最容易受到磨损的地方。
在引风机的运行中,叶片时刻处于高速旋转状态,而烟气则是由于叶片的高速旋转被吸引过来,因此叶片的迎风面要时刻受到烟气持续的高速冲刷下,迎风面的焊接处会不断受到严重的磨损,叶片上的迎风侧钢板会随之张开,这样就会产生非常大的引力。
叶片的迎风面,始终承受着非常巨大的向外压力,这样的压力作用下,叶片非常容易被撕裂。
627MW超临界重油锅炉引风机叶片断裂原因分析与防范措施

627MW超临界重油锅炉引风机叶片断裂原因分析与防范措施Analysis and preventive measures of ID Fan blade fractureof 627mw supercritical heavy oil boilerZhou Junqiang1 Liu Chonggang2 Xiang Baolu2摘要:本文针对沙特延布三期引风机叶片断裂造成机组跳闸,设备损坏的实际案例,对引风机叶片断裂的危害及原因进行了具体的分析,并提出具有针对性的处理措施。
关键词:引风机叶片断裂分析处理措施Abstract: In this paper, In view of the actual case of unit trip and equipment damage caused by the ID Fan blade fracture of Saudi Arabia Yanbu III power plant, The damage and reason of ID Fan blade fracture are analyzed concretely, and the corresponding treatment measures are put forward.Key words: ID Fan blade Fracture analyzed treatment01引言引风机是发电厂的主要辅助设备之一,它的安全稳定运行对电厂影响极大。
引风机叶片裂纹给机组安全稳定运行带来隐患,断裂会造成引风机设备损坏,导致机组降负荷或者跳闸,是必须遏止的。
沙特延布三期引风机主要设计参数如表一所示表一:引风机主要设计参数和国内引风机动调一般采用双级动调、转速745RPM相比,延布引风机特殊之处在于采用单级动调,风机转速在1190RPM,即为长叶片、高转速风机,烟道设计流速燃用重油时为18m/s,燃用天然气时为20 m/s。
电站增压风机叶片断裂失效分析

电站增压风机叶片断裂失效分析摘要:现如今,社会经济不断进步,我国各行各业的科学技术也在不停的进步当中,本文主要叙述电站增压风机叶片断裂失效分析。
关键词:试验;讨论;分析;前言某电厂型号为RAF28-15-1的增压风机1只叶片断裂,经更换新叶片,在运行不足一星期后再次断裂。
叶片材料为15MnV,叶片与叶柄依靠螺栓连接,介质为烟气,进口处介质温度为126℃,进口处介质密度为0.9038kg/m3,风机转速为985r/min。
一、试验结果1.1断口宏观检查新、旧叶片均断裂于叶片根部向上约150mm处,断口形貌类似,均为厚壁侧平坦断口加薄壁侧较粗糙的撕裂断口,平坦区域和撕裂区域约各占一半。
对新断口在平坦区域仔细观察可见明显的疲劳纹路及疲劳源(图1),裂源表面镀层厚度为1.1~1.2mm,裂源处镀层发现微小裂纹且延伸进入基体;在疲劳源处叶片镀层表面还发现较多密集的颗粒状附着物。
图1:断口裂源处形貌1.2 新叶片断口扫描电镜分析从裂源处取样清洗后扫描电镜检查,裂源处叶片外表面有两层覆盖,第一层(内层)和叶片基体结合较好,断裂由第一层表面向内扩展,能谱成分分析结果除氧外主要是Cr、Ni、Al、Si、Fe、Co和Mn。
而外层呈层状,且较疏松,能谱成分分析结果有较高的O、Al、Si,还有较多的S、K、Ca等元素。
在表面金属喷镀层(内层)内有较多的夹杂,经能谱成分测定为Cr、Fe、Ni、Si的氧化物。
断裂扩展区有较密集的疲劳条带(图2)。
对裂源的外表面堆积物能谱测定,结果和断裂面边缘能谱成分基本相同,除主要成分为O、Al、Si外,还有较多的S、Cl、K和Ca等元素。
图2:扩展区的疲劳条带1.3 元素成分分析用化学方法对新、旧叶片的各元素含量进行精确分析,结果表明,旧叶片符合GB713-86中对15MnVg的元素含量规定的范围,但新叶片与15MnVg不符,没有V元素,Si含量也明显偏低,与GB713-86中16Mng的元素含量范围基本相符。
风力发电机组叶片裂纹的分析与预控措施
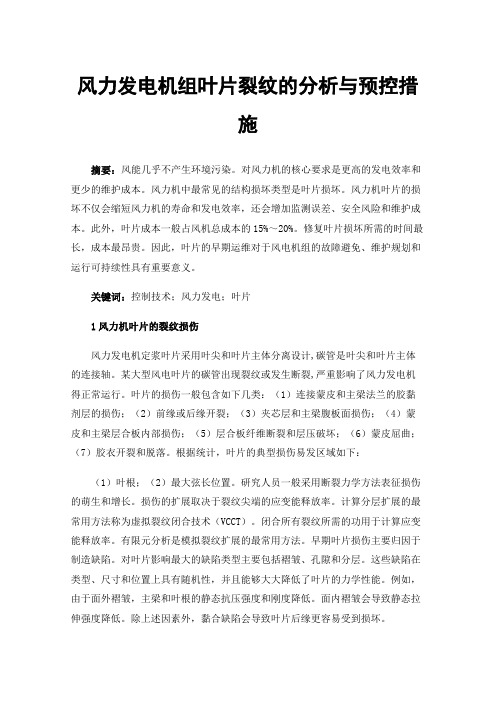
风力发电机组叶片裂纹的分析与预控措施摘要:风能几乎不产生环境污染。
对风力机的核心要求是更高的发电效率和更少的维护成本。
风力机中最常见的结构损坏类型是叶片损坏。
风力机叶片的损坏不仅会缩短风力机的寿命和发电效率,还会增加监测误差、安全风险和维护成本。
此外,叶片成本一般占风机总成本的15%~20%。
修复叶片损坏所需的时间最长,成本最昂贵。
因此,叶片的早期运维对于风电机组的故障避免、维护规划和运行可持续性具有重要意义。
关键词:控制技术;风力发电;叶片1风力机叶片的裂纹损伤风力发电机定浆叶片采用叶尖和叶片主体分离设计,碳管是叶尖和叶片主体的连接轴。
某大型风电叶片的碳管出现裂纹或发生断裂,严重影响了风力发电机得正常运行。
叶片的损伤一般包含如下几类:(1)连接蒙皮和主梁法兰的胶黏剂层的损伤;(2)前缘或后缘开裂;(3)夹芯层和主梁腹板面损伤;(4)蒙皮和主梁层合板内部损伤;(5)层合板纤维断裂和层压破坏;(6)蒙皮屈曲;(7)胶衣开裂和脱落。
根据统计,叶片的典型损伤易发区域如下:(1)叶根;(2)最大弦长位置。
研究人员一般采用断裂力学方法表征损伤的萌生和增长。
损伤的扩展取决于裂纹尖端的应变能释放率。
计算分层扩展的最常用方法称为虚拟裂纹闭合技术(VCCT)。
闭合所有裂纹所需的功用于计算应变能释放率。
有限元分析是模拟裂纹扩展的最常用方法。
早期叶片损伤主要归因于制造缺陷。
对叶片影响最大的缺陷类型主要包括褶皱、孔隙和分层。
这些缺陷在类型、尺寸和位置上具有随机性,并且能够大大降低了叶片的力学性能。
例如,由于面外褶皱,主梁和叶根的静态抗压强度和刚度降低。
面内褶皱会导致静态拉伸强度降低。
除上述因素外,黏合缺陷会导致叶片后缘更容易受到损坏。
除制造缺陷,降水和碎片同样是导致叶片损伤的重要原因。
雨水、冰雹、烟雾和含沙风容易导致前缘侵蚀。
不均匀的积冰会导致旋转不平衡,进而导致发局部损伤甚至失效。
此外,水如果通过预先存在的裂缝、表面缺陷或螺栓接头进入叶片,可能会导致叶片树脂和芯材性能显著下降,并且导致叶片重量增加和力学性能退化。
风电机组变桨连接螺栓断裂原因分析及预防措施

风电机组变桨连接螺栓断裂原因分析及预防措施摘要风力发电机叶片是一个纤维增强复合材料制成的薄壳结构。
叶片工作时,根部承受着复杂的剪切、挤压、弯扭载荷组合作用,应力状态复杂易产生结构失效,所以叶片根部连接必须具有足够的强度、刚度、局部稳定性、胶接强度和疲劳断裂强度。
一旦叶根部位出现连接失效问题,叶片与风力机转子轮毂分离,发电机无法正常工作,甚至导致灾难性的质量和安全事故。
因此,对风机叶片连接螺栓状态进行监测成为了必要的手段,某公司针对风电机组变桨连接螺栓断裂情况,对叶片连接螺栓断裂进行了原因分析,并提出预防及监测措施,以确保机组安全稳定运行。
关键词:变桨连接螺栓;疲劳断裂;预紧力0引言风电叶片是风力发电机组捕获风能的核心部件,其工况复杂、工作载荷很大,设计上要求达到安全运行二十年的使用寿命要求。
叶片在运转过程中,同时承受着气动力、重力及离心力等复杂载荷的作用,其中叶片根部连接成为叶片设计中最关键的部分(如图1)。
由于叶根的载荷最大,而且应力状态复杂,承受着复杂的剪切、挤压、弯扭载荷作用,所以叶根连接必须具有足够的机械强度与弯扭刚度。
叶根的受力方式也极为复杂,同时承受拉伸、压缩、扭转及剪切等复杂应力的作用。
叶片根部连接螺栓断裂而导致风电机组运行事故是一种常见的故障模式。
图 1 叶片与轮毂链接示意图1叶片根部连接螺栓断裂的主要故障及根源分析目前,叶根与轮毂链接的的方式主要由三种:“T型螺栓”连接方式,螺栓套筒预埋连接方式,金属制根部连接件连接方式。
在正常工作状态中,叶片叶根螺栓连接是紧连接,承受着交变载荷。
“T 型螺栓”连接( 包含双头螺栓及横向螺母) ,也称“IKEA” 连接,是风机叶片最广泛的螺栓连接结构之一,本文重点考虑“T型螺栓”连接方式。
在叶片根部断面沿叶根节圆均匀分布多组高强度螺栓组,每组螺栓由双头螺杆和交叉螺母组成,叶片根端有两组均匀分布且互相对应螺栓孔和螺母孔,交叉螺母安装在径向螺母孔中,双头螺杆安装在轴向螺栓孔中,双头螺杆一端与交叉螺母连接,另一端伸出断面与主机轮毂连接,从而将叶片与主机联为一体(如图2)。
风电场风力发电机组叶片失效断裂分析

风电场风力发电机组叶片失效断裂分析作者:惠鹏郭永刚鞠伟来源:《科技创新导报》2017年第33期摘要:风力发电系统大多都布置在环境恶劣的条件下,通过将自然风产生的动能转化为电能进行工作。
由于自然风具有强烈的随机性,常常发生风速、风向剧变的情况,因此要求风电场中的风力发电机必须能够承受较大的载荷。
而随着风力发电规模和技术的不断发展,风机叶片变得越来越大,这无形中增加了叶片损坏的概率。
本文通过对机组叶片的结构和受力情况进行介绍,对风电场风力发电机组叶片的断裂监测和预防进行了分析。
关键词:风电机组叶片断裂结构受力监测中图分类号:TM614 文献标识码:A 文章编号:1674-098X(2017)11(c)-0080-02随着经济和社会的不断发展,能源问题成为制约人类发展的关键问题。
石化资源由于其污染性、不可再生性等特点已经无法满足社会发展的需求。
这种情况下,风能成为一种重要的绿色替代能源,并因此受到了更多的研究和关注。
通过风力发电机组将风产生的动能转化为电能,不仅有效降低了污染废料的排放,还改善了电力结构。
随着装机容量的快速增加,风力发电设备和技术的发展非常迅速。
其中,叶片是风电场风力发电机组的重要组成部件,直接影响到发电机的性能、效率、质量和经济效益。
叶片会随着机组容量的增大而快速增加,越大的风机叶片会无形中增加叶片损坏的概率。
而且在风机的运行过程中会使叶片受到恶劣自然环境的影响,使叶片出现共振现象。
叶片共振是风力发电机组叶片失效断裂的重要原因之一。
本文通过对机组叶片的结构和受力情况进行介绍,对风电场风力发电机组叶片的断裂监测和预防进行了分析。
1 机组叶片的基本结构和特性1.1 材料由于风力发电机组都是布置在环境恶劣的条件下,因此,风力发电机的叶片材料选择要十分慎重,要综合考虑叶片的重量、强度和化学性能,这样才能有效降低叶片的断裂概率。
选择的材料应具有较大的强度和比模量、良好的减震性和破损安全性,以及耐疲劳性。
火电厂轴流增压风机叶片断裂原因及其解决方案探究

火电厂轴流增压风机叶片断裂原因及其解决方案探究摘要:针对增压风机叶片断裂问题,采用材质性能检测、热态性能试验、数值计算等方法,探究叶片断裂的原因。
数据结果表明,风机性能与其所在的管道系统不匹配是叶片断裂的主要原因,同时风机叶片的加工存在一定的质量问题,风机长时间受到交变应力的作用从而产生疲劳断裂。
鉴于此,提出风机改造方案并进行改造,此后增压风机安全稳定运行一年多,振动数值较小。
可见,改造取得明显效果,对类似问题的解决具有很好的借鉴意义。
关键词:轴流式风机;增压风机;叶片断裂;大型轴流增压风机是火电厂脱硫烟风系统的重要辅助设备之一,其运行状况对火电厂的安全经济运行至关重要,如增压风机发生安全故障,严重时可导致整台机组跳停。
增压风机和引风机叶片承受离心力和高温烟气中固体颗粒的冲蚀,工作环境比较恶劣。
如果风机本身性能达不到设计要求、叶片加工质量存在问题或者风机运行在失速区域,叶片就极易发生断裂现象。
1 设备概况及事故过程1.1 设备概况。
锅炉额定工况蒸汽压力为13.7 MPa,锅炉最大连续蒸发量不小于670 t/h。
脱硫系统增压风机是型号为RTF28-15-1的静调轴流风机(由动调轴流风机改进而来),风机设计转速为990 r/min。
1.2 事故过程机组进行超低排放改造前,增压风机运行稳定,未出现叶片断裂的事故。
超低排放改造后,增压风机叶片开始出现断裂现象,每次断裂前表盘振动数据均无明显异常。
风机正常运行过程中振动突然增大,振速超过7 mm/s,立即停机检查,发现叶片断裂。
初步判断振动增大时叶片已经发生断裂,且通过检查推测断裂首先发生在一个叶片上,随后将其他叶片扫射损坏,同时对机壳、调节门撑筋产生不同程度的损坏,叶片断口在距离叶盘200 mm左右位置,如图1所示。
图1 叶片断裂现场示意图2 风机与管网系统匹配性分析根据上文叶片断裂现象和相关经验可初步得出以下判断:超低排放改造后,烟风管网系统和脱硫系统阻力增加,增压风机出力增加,风机与烟风管网系统的匹配性发生变化。
轴流风机叶片断裂的原因以及系统对风机性能影响分析

科技风2016年4月上轴流风机叶片断裂的原因以及系统对风机性能影响分析徐俊浙江亿利达风机股份有限公司浙江台州318056摘要:随着现代经济社会的不断发展,机械研究和机械使用在多个领域中都发挥着不可替代的优势,本文就轴流风机叶片出现断裂的原因加以分析,并对这种断裂导致的系统对风机性能造成的影响进行分析,制定出可以运用的措施,保证轴流风机能够实现安全运行。
关键词:轴流风机;叶片断裂;风机性能影响目前轴流风机系统内部选择的风机一般控制风量为80000m3/h,风压控制在2300Pa左右,其配套电机功率控制在110kW左右。
在对其进行检测时发现部分叶片出现了不同程度的裂缝,对这些裂缝出现的原因进行分析,并对系统对风机性能造成的影响加以概括。
一、裂缝原因分析(一)叶片结构风机轮毂的直径在700mm左右,单台风机轮毂上的叶片数量为14片,叶片的尺寸控制为260mm,叶尖弦长度为210mm左右,叶根厚度控制为19mm,叶片选择的是焊接的结构,叶身则是由两块厚度规格为2mm的钢板沿着周边实现焊接,叶片内部上下两端则使用加强筋来进行焊接,下端则是由叶身钢板和加强筋焊接在厚度为22mm的钢板兰盘之上,控制焊接区长度为100mm。
[1]14片叶片使用6只螺栓将其与风机轮毂实现连接。
(二)叶片断裂原因探讨1.叶片制造从风机制造以及叶片强度来分析,叶片焊缝的总负载要超过设计载荷,不会诱发强度断裂的现象。
叶片材料的硬度和金相组织相对正常。
但是,从金相和端口结果来分析,由于叶片叶身属于中空薄钢板和刚性较大的法兰盘之上,这种焊接属于单面角焊,叶片焊接内侧边缘可能出现焊瘤以及焊透等缺陷,导致内部边缘应力出现严重集中现象。
[2]使用常规性的表面PT探伤无法检查出焊缝存在的缺陷,超声波探伤以及磁粉探伤又因为叶片结构的影响难以顺利进行。
裂纹全部都是由内缘缺陷位置开始逐渐向四周扩散的疲劳断裂裂缝,所以,叶片结构以及焊接裂缝则是风机叶片出现断裂的主要原因。
- 1、下载文档前请自行甄别文档内容的完整性,平台不提供额外的编辑、内容补充、找答案等附加服务。
- 2、"仅部分预览"的文档,不可在线预览部分如存在完整性等问题,可反馈申请退款(可完整预览的文档不适用该条件!)。
- 3、如文档侵犯您的权益,请联系客服反馈,我们会尽快为您处理(人工客服工作时间:9:00-18:30)。
发电厂A引风机叶片断裂原因分析报告
某发电有限公司5号机组A引风机于2012年12月2日在运行过程中发生叶
片断裂失效,两片叶片断裂脱离风机主轴。为查明断裂发生原因,对断裂叶片进
行了相关分析。
1. 断口宏观检查及微观分析
A引风机共有两片叶片断裂,其中一片断裂发生在叶片圆柱形根部,其根部
断面存在因交变应力长期作用产生的疲劳贝纹线,应为断裂起始点,该处的
断裂引起了其他部件的破坏。对该叶片根部断面进行取样,清洗后观察其宏
观形貌(见图1)。从断面的裂纹扩展宏观形态可以确定,断裂属于疲劳断裂特
性。疲劳源位于断口边缘(因断裂后发生碰撞,疲劳源区已严重变形),呈斜坡
状,能明显观察到裂纹扩展过程中形成的疲劳贝纹线。裂纹疲劳扩展到一定尺寸
后在外力作用下扩展,直至开裂。
图1 断口疲劳断裂宏观形貌
2. 光谱检验
对叶片根部进行处理后,在德国进口的SPECTRO TEST便携式光谱仪上进行
材质检验,结果见表1。
疲劳源区
疲劳贝纹线
瞬断区
表1 光谱检验结果
元素 C Si Mn Cr
含量/% 0.44 0.255 0.69 1.10
GB/T 17107-1997 0.37~0.44 0.17~0.37 0.50~0.80 0.80~1.10
光谱检验结果符合GB/T 17107对40Cr的成分要求。
3. 冲击试验
依据GB/T 229-2007 要求,在叶片根部沿轴向和径向切取摆锤试验标准样
品,采用JB-300C 型摆锤冲击试验机测试材料的冲击性能,检验结果见表2 。
表2 冲击试验结果
检验项目
编号
径向AKU/J 径向AKV/J 轴向AKU/J 轴向AKV/J
1 75.2 46.5 46.4 24.5
2 88.8 70.8 35.3 35.4
3 92.2 57.8 40.2 34.8
GB/T 17107-1997 ≥39 - - -
材料冲击试验结果无异常。
4. 拉伸试验
按照GB/T 228-2002在叶片根部截取3个拉伸试样,在深圳三思生产的
CMT5105电子万能试验机上检验齿轮材料的抗拉强度,结果见表3。
表3 拉伸试验结果
检验项目
编号
抗拉强度Rm/MPa 下屈服强度Rel/ MPa 断后伸长率A/%
1 775 567 15
2 789 553 15
3 786 587 16
GB/T 17107 ≥735 ≥540 ≥15
拉伸试验结果无异常。
5. 金相检验
在断口疲劳源区截取纵向面作观察面,同时沿轴向在远离断口一段距离处取
样,经镶嵌、粗磨、细磨、抛光后,采用2%的硝酸酒精进行腐蚀,在Carl Zeiss
Axio Obsever 倒置式研究级金相显微镜观察试样的显微组织。
疲劳源区取样的金相组织,靠近表面处存在3处体积较大(每处直径约
100um)的脆性非金属夹杂物;而且存在方向性的夹杂物,走向与疲劳源面的走
向基本一致。表面存在渗氮层,基体组织为回火索氏体,靠近心部区域的回火索
氏体上有针状分布的铁素体存在,组织无异常。
沿轴向远离断口处取样金相组织,表面存在渗氮层,基体组织为回火索氏体,
靠近心部区域的回火索氏体上有针状分布的铁素体存在,组织无异常。
6. 显微硬度检验
在试样金相观察面沿表面至中心方向分别测试各区域的显微硬度,试验所用
仪器为日本岛津生产的HMV-2T显微硬度计,所得结果见表4。
表4 显微硬度检验结果(HV0.2)
检验区域
试样
渗氮层 基体(表面)→ 基体(心部)
疲劳源区取样 645 639 270 278 268 242 245
远离断口处取样 651 641 276 273 275 250 249
表面渗氮层显微硬度较高,基体心部因为存在铁素体显微硬度略有下降。硬
度无异常。
7. 断裂原因分析
此次引风机叶片根部失效形式为疲劳断裂,疲劳源位于根部表面。从检验结
果看,根部材料靠近表面处存在体积较大的脆性非金属夹杂物。疲劳断裂对表面
缺陷非常敏感,在叶片高速转动时,受振动冲击的影响,脆性非金属夹杂物处易
于萌发原始微裂纹,进而扩展成为疲劳源。根部材料还存在与疲劳源面走向一致
的非金属夹杂物,表明微裂纹是沿着夹杂物方向扩展而发展成疲劳源。在交变应
力作用下,裂纹逐渐扩展到一定尺寸,由缓慢扩展发展成为快速扩展,最终导致
叶片根部形成过载断裂失效。
该引风机叶片根部发生断裂的主要原因是由于近表面处非金属夹杂物的存
在促使疲劳源的形成,进而在交变载荷作用下产生疲劳断裂。