基于切削力的刀具状态在线监控
切削过程健康状态监测与评估研究

制這.材料切削过程健康状态监测与评估研究口邢诺贝口刘福军口周超口胡德金口许黎明上海交通大学机械与动力工程学院上海200240摘要:加工稳定性是影响机床加工精度与效率的重要因素。
为了实现对生产线设备不同加工工艺过程的健康状态进行智能监测,对切削过程健康状态的监测与评估进行了研究。
基于快速傅里叶变换,确认机床加工失稳时信号在频域具有能量转移特性。
考虑加工失稳时信号变化的复杂性,提出一种基于s变换与奇异值分解的特征提取方法,通过奇异值e实时跟踪机床当前的加工状态。
通过对切削数据的积累和学习统计,设定不同工艺过程的稳定阈值线,实现切削过程健康状态的实时监测。
试验表明,所提出的方法能够有效应用于切削过程健康状态的监测与评估。
关键词:切削状态监测评估中图分类号:TG506文献标志码:A文章编号:1000-4998(2021)04-0043-04Abstracr:Machining stability is an Xiiportant factor affecting the machining accuacy and eficnncy of the machine tool.In order te realize the intelligent monitoring of the health status of dXferent machining processesof the equipment in the production line$the monitoring and evvluation of the health status of cutting process was studied.Based on the fast Fourier transform,it is confirmed that the signal has eneray transfer thaeatteeistitsin theteequentzdomain when themathiningisunstabie.Consideeingthetompieiitzotsignai changes when machining is unstable,a feature extraction method based on S—transform and singular vdue deoomposition waspeoposed toteaok theou e ntmaohiningstateotthemaohinetooiin eeaitimetheough singueaevaeueenteopz.Theough theattumueation,eeaeningand statistitsottu t ingdata,thestabieitztheeshoedline of dXferent technolooical processes was set to realize real-tine monitoring of health status of cutting peote s.Testsshowthatthepeoposed method tan beeettiveezappeied tothemonitoeingand evaeuation o<the heaith statuso<tu t ingpeote s.Keyworrt:Cutting Statut Monitoring Evaluation1研究背景制造业是支撑我国经济高速增长的重要产业之一,是提升我国综合国力及科技竞争力的重要基础,尤其是大型关键设备的生产制造技术,对国家整体装备制造水平的提升有重要影响。
具备高适应性的高速铣削刀具磨损状态监测系统

Ab s t r a c t :To e n h a n c e t h e a d a p t a b i l i t y o f t o o l c o n d i t i o n mo n i t o r i n g( TCM ) s y s t e m ,a n n o v e l a n d i n t e l l i —
v a l u e wi t h n o n e e d o f t h e p r e — d e s i g n e d” t e a c h i n g ”o r” t r a i n i n g”p h a s e .A u t o ma t i c s e n s o r y f e a t u r e s e l e c — t i o n me t h o d i s u s e d t o a i d t h e s y s t e ma t i c d e s i g n o f TCM ,a n d t o s u p p r e s s i n t e r f e r e n c e i n t r o d u c e d b y c h a n g e s o f c u t t i n g p a r a me t e r .Fo r c e a n d a c o u s t i c e mi s s i o n s e n s o r s a r e u s e d i n h i g h s p e e d mi l l i n g o p e r a —
数控机床刀具磨、破损状态监测方法的探讨

测 方 法的 基 本 原 理 、优 缺 点和 应 用 范 围的基 础 上 结合 自身的研 究指 出合 理 的 多信 号 融 合 监 测 是 目前 在 线 监 测研 究 的 发展 方
的情境和监控效果存在较大差异 , 所 以对 刀具磨 、 破损状 态 的监测技 术进行分类和研究具有现实意义.
2 国 内外 刀 具磨 、 破 损 状 态 监测 技 术
光学法主要包括光导纤维法等 ,它的工作原理通 常是 基于刀具磨损后磨损 区相对未磨损区具有更强 的光 反射 能 力, 且传 感器检测 的光 通量随着磨损 区域 的增 大而增大 , 从 而识别刀具 的磨损程度 ,光学法理论上具有可靠性高 的优 点, 缺点是其监测结果 受到刀刃的清 洁状 态 、 切削热 引起 的
1 数控机床刀具磨、 破 损 状 态 监 测 的意 义
刀具 既是金 属切 削类机 床 的重要 工作 原件 又属 于耗 材, 在切削过程 中不可避免的出现磨 、 破损现象. 一方面为保 证工件 的表面质量及尺寸精度 ,目前企业一般 是按 刀具 的 平均 寿命作 为更换 刀具 的标 准 ,以减少刀具破 损带来的各 种损 失 , 但 这种做法往往导致 刀具使用 寿命 偏低. 而且频繁 地更 换刀具还会 带来加工成本的提高 ,机床辅助时 间的增 加 以及生产效率 的降低 . 另一方面如果 刀具 的磨 、 破 损未能
图像 与刀具磨 、 破损程度间的关 系 , 达到刀具状 态监 测的 目 的. 南京航空航天大学的杨吟飞基于窗 口跟踪的办法获取 了
Байду номын сангаас
高速铣削加工中刀具监测系统研究

带有修正 系统 的磨损监测结果分别如 图4 、5示 。
1 00 0
80 0
j 60 四 0 罂
40 0
20 0
0
1
2
3
4
5
6
7
8
频带 ( ) 量 图 b能
图4 带有 修正系统的磨损监钡 结果 4
小波神 经网络是基于小波变换而构成的神经 网络 模型 ,即用非线性 小波基 取代通 常的神经元非线性激 励 函数 ( S m i 如 i o g d函数 ) ,把 小波 变换 与神 经 网络
1 铣 刀磨损 与工 件表 面精 度的联 系
铣刀在初期磨 合与正常磨合 时期 ,因为刀具 引起 的表面加工质量变化不大 ,但是在 急剧磨损 阶段 ,工 件的表 面加工质量也跟着急剧下降 。在正常磨损 与急 剧磨损混合期 ,表征刀具磨损 的信号较弱 ,容易淹没
有机地结合起来 ,充分继 承了两者 的优点 。小波神经 网络 主要分为输入层 、隐含层和输出层 ,它是将神经 网络隐结点 的 s函数用小 波函数来代替 ,相应 的输入 层 到隐含层 的权值及隐含层的阈值分别 由小波函数的 尺度伸缩 因子 和时 间平移 因子所代替 。
收 稿 日期 :2 1 — 5— 4 0 1 0 0
高 速 铣 削加 工 中刀 具监 测 系统 研 究
郭贵 中 ,毛新华
(.新 乡学 院 ,河南新 乡 4 30 ;2 1 503 .河 南科技 学院 ,河 南新 乡 430 ) 50 3
摘要 :在铣 削加工中 ,在 刀具 急剧磨损 的初级 阶段 ,表征 刀具磨损 的信号较弱 ,而此 时工件精度 已早 有 明显变 化。小 波神经网络虽能有效处理各种频段信号 ,但对较 弱信号还 是存 在漏检现 象。开发针对 高速铣削 的刀具 在线监测 系统 ,通过 监测工件表面精度的变化 ,及时修正小波变换参数 ,提高了监测微 弱信 号的能力 ,有效 降低 了刀具监测 的漏检 、误报率 。
浅谈数控机床刀具磨损的监测方法

浅谈数控机床刀具磨损的监测方法摘要:数控机床刀具磨损情况的监测对于降低因刀具的破损而带来的经济损失,提高其在数控机床中的利用率起着非常重要的作用。
通过回顾国内外各种关于刀具磨损情况的监测技术与方法研究,大概有以下方法,针对振动监测法、切削力监测法、功率性监测、及基于动态树理论的刀具磨损检测等,分析它们的优势与特点,可以了解到基于动态树理论的刀具而研究磨损监测技术手段是其未来发展的趋势。
关键词:数控机床;刀具磨损;监测方法前言刀具的磨损状态在目前我国的各种机械加工中已成为一种常见的情况,刀具磨损以及它的磨损状态直接地影响到了机械加工的准确性、精度和企业的经济效益,降低其刀具加工的费用,对于提高企业的社会经济效益很有利。
近几年来,随着我国先进的技术如 cims、 cnc 、 fms 机床的广泛应用,极大地改善了机械加工精度与生产设备的加工效率。
操纵人机已经从原先的单独或者两台开始进行操纵,变成现在可以同时运行和操纵多个设备。
如此,数控机床系统就能够实现自动地监视各种刀具的运转和工作状态,及时掌握正在运行中所需要使用刀具的磨损情况,从而根据各种刀具的断裂程度、刀具寿命、磨损量等各种刀具的故障情况实时地监测各种刀具的运转和工作状态的变化,并且当各种刀具的磨损量已经超过预先设置的磨损程度时发出信号和报警,就会因此变得尤其重要。
一、刀具磨损的监测方法刀具检测状态的检查技术通常包括传感器信号采集、信号处理及状态特征提取和状态辨认器三个组成部分。
刀具运行状态检测传感器系统中的传感器主要是为了接收到在切削工作过程中产生的切削机械信号,例如切削能力、功率、音频发射、震荡、振动、电流等。
1.刀具状态的振动监测法当工件在切削的过程中,工件和磨损后的刀具刃部侧面发生摩擦,产生不同速度和频率的振动,振动信号已经被认为是一种检测刀具的磨损和破坏敏感性较高的技术。
振动的特征检测和处理方法主要分为两种:一种就是把振幅区域划分为几个单独的振幅区域,不断地通过使用计算机电脑和数字化计算机对这些振幅区域的位置进行记录、分析,就已经可以准确检测得出一把刀具在使用后的每一个刀面上受到磨损的严重性程度;二是把振幅划分为高低两个组成部分,在切削过程中分别计算出两个组成部分的振幅。
刀具状态检测方法
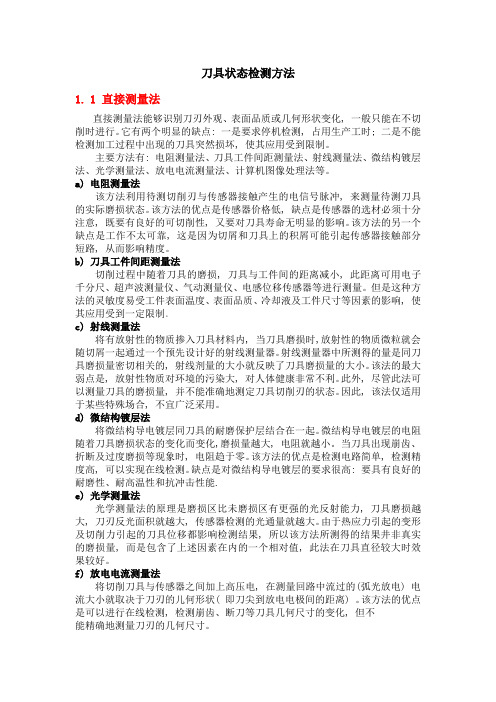
刀具状态检测方法1.1直接测量法直接测量法能够识别刀刃外观、表面品质或几何形状变化, 一般只能在不切削时进行。
它有两个明显的缺点: 一是要求停机检测, 占用生产工时; 二是不能检测加工过程中出现的刀具突然损坏, 使其应用受到限制。
主要方法有: 电阻测量法、刀具工件间距测量法、射线测量法、微结构镀层法、光学测量法、放电电流测量法、计算机图像处理法等。
a)电阻测量法该方法利用待测切削刃与传感器接触产生的电信号脉冲, 来测量待测刀具的实际磨损状态。
该方法的优点是传感器价格低, 缺点是传感器的选材必须十分注意, 既要有良好的可切削性, 又要对刀具寿命无明显的影响。
该方法的另一个缺点是工作不太可靠, 这是因为切屑和刀具上的积屑可能引起传感器接触部分短路, 从而影响精度。
b) 刀具工件间距测量法切削过程中随着刀具的磨损, 刀具与工件间的距离减小, 此距离可用电子千分尺、超声波测量仪、气动测量仪、电感位移传感器等进行测量。
但是这种方法的灵敏度易受工件表面温度、表面品质、冷却液及工件尺寸等因素的影响, 使其应用受到一定限制。
c) 射线测量法将有放射性的物质掺入刀具材料内, 当刀具磨损时,放射性的物质微粒就会随切屑一起通过一个预先设计好的射线测量器。
射线测量器中所测得的量是同刀具磨损量密切相关的, 射线剂量的大小就反映了刀具磨损量的大小。
该法的最大弱点是, 放射性物质对环境的污染大, 对人体健康非常不利。
此外, 尽管此法可以测量刀具的磨损量, 并不能准确地测定刀具切削刃的状态。
因此, 该法仅适用于某些特殊场合, 不宜广泛采用。
d) 微结构镀层法将微结构导电镀层同刀具的耐磨保护层结合在一起。
微结构导电镀层的电阻随着刀具磨损状态的变化而变化,磨损量越大, 电阻就越小。
当刀具出现崩齿、折断及过度磨损等现象时, 电阻趋于零。
该方法的优点是检测电路简单, 检测精度高, 可以实现在线检测。
缺点是对微结构导电镀层的要求很高: 要具有良好的耐磨性、耐高温性和抗冲击性能.e) 光学测量法光学测量法的原理是磨损区比未磨损区有更强的光反射能力, 刀具磨损越大, 刀刃反光面积就越大, 传感器检测的光通量就越大。
基于计算智能算法的铣刀状态监测

中图分类号 : TH1 4 6
文献标识码 : A
程中刀具的两种状 态量切削力和振 动信号 以及加工参数通
1 引言
要提高加工系统的 自动化 和智 能化水 平 , 须开 发有 必 效的和鲁棒性强的刀具状 态监测系统 , 以避免机床 、 刀具和 工件的损坏 。但是 , 在加 工过程 中 , 由于机 床动态 特性 、 刀 具材料 以及切削条件 的影 响 , 工系 统具有较 强 的非 线性 加
Ke r :o lwe ; a a f so wa ee a k g e o o s t n; v lt n u a e wo k; e e i n u a e wo k; e ywo ds t o a d t u in; v lt p c a e d c mp ii wa ee e r ln t r g n t e ln t r g r o c r n tcwa ee e r e wo k e i v l t u a n t r n l
Vo . 0, . 2 0 1 3 No 2, 0 8
文 章 编 号 :0 710 (0 80 —1 20 10 ~3 X 2 0 ) 20 4 —5
基 于计 算 智 能算 法 的铣 刀 状 态 监 测 ‘
En ilW e r M o t rn s d o m pu a i n l dM l a nio i g Ba e n Co t to a I t li e l o ihm s n e lg ntA g rt
郑金 兴. 张铭钧 . 孟庆鑫
ZI N Jnx g Z N n jn ME GQigxn l G i i . HA G Mi ̄ u . N n -i E -n
( 尔 滨 工 程 大 学 机 电 学 院 , 龙 江 哈 尔 滨 10 0 ) 哈 黑 50 1
金属切削中的切削力测量与分析方法综述
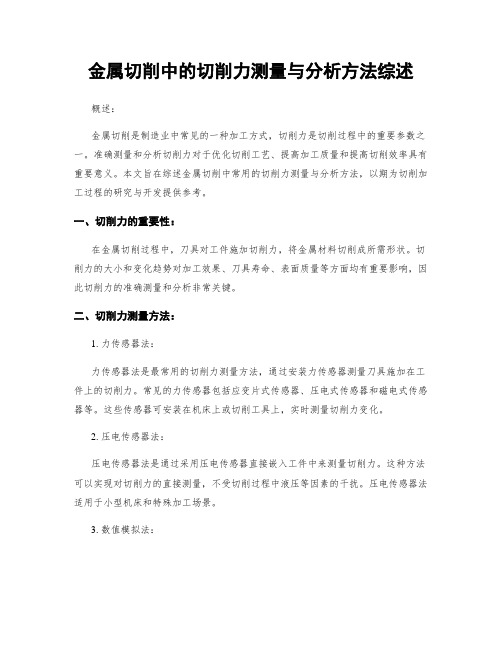
金属切削中的切削力测量与分析方法综述概述:金属切削是制造业中常见的一种加工方式,切削力是切削过程中的重要参数之一。
准确测量和分析切削力对于优化切削工艺、提高加工质量和提高切削效率具有重要意义。
本文旨在综述金属切削中常用的切削力测量与分析方法,以期为切削加工过程的研究与开发提供参考。
一、切削力的重要性:在金属切削过程中,刀具对工件施加切削力,将金属材料切削成所需形状。
切削力的大小和变化趋势对加工效果、刀具寿命、表面质量等方面均有重要影响,因此切削力的准确测量和分析非常关键。
二、切削力测量方法:1. 力传感器法:力传感器法是最常用的切削力测量方法,通过安装力传感器测量刀具施加在工件上的切削力。
常见的力传感器包括应变片式传感器、压电式传感器和磁电式传感器等。
这些传感器可安装在机床上或切削工具上,实时测量切削力变化。
2. 压电传感器法:压电传感器法是通过采用压电传感器直接嵌入工件中来测量切削力。
这种方法可以实现对切削力的直接测量,不受切削过程中液压等因素的干扰。
压电传感器法适用于小型机床和特殊加工场景。
3. 数值模拟法:数值模拟法是通过建立切削过程的力学模型,并通过计算机仿真来估计切削力。
这种方法可以预测不同切削条件下的切削力,并帮助优化切削工艺。
数值模拟法需要准确的材料力学参数和边界条件数据。
三、切削力分析方法:1. 力信号时域分析:力信号时域分析是对切削力信号进行时间序列分析,提取力信号的振幅、频率、周期和波形等信息。
这种方法能够揭示切削力的变化规律和切削过程中的动态特性。
2. 功率谱分析:功率谱分析是对切削力信号进行频谱分析,将力信号在频域上进行研究。
通过功率谱分析,可以确定切削过程中主要频率成分的强度和相位关系,从而了解切削过程中的振动和噪声特性。
3. 统计分析方法:统计分析方法基于大量实验数据的统计学原理,对切削力进行统计处理。
通过统计分析,可以确定切削力的平均值、方差、标准差和相关系数等参数,揭示不同因素对切削力的影响程度。
- 1、下载文档前请自行甄别文档内容的完整性,平台不提供额外的编辑、内容补充、找答案等附加服务。
- 2、"仅部分预览"的文档,不可在线预览部分如存在完整性等问题,可反馈申请退款(可完整预览的文档不适用该条件!)。
- 3、如文档侵犯您的权益,请联系客服反馈,我们会尽快为您处理(人工客服工作时间:9:00-18:30)。
基于刀具状态的切削力模型研究 (常州铁道高等职业技术学校、常州昌成铁路机械厂 江苏 常州 213011) 张宝金 摘 要:建立适用于变工况加工的切削力模型,将切削力信号用于切削过程监控。建立基于切削参数(切削速度、进给量、切削深度)与刀具状态(主要考虑后刀面磨损量)的切削力模型,通过试验值与模型的预测值之间的比较,进一步验证模型的准确性。 关键词:切削力;刀具状态监控;金属切削;模型 1 引言 目前,加工中心(MC)、柔性制造单元(FMC)、柔性制造系统(FMS)及
计算机集成制造系统(CIMS)逐渐成为现代机械制造业的主流,为实现制造系统的高度自动化提供了先决条件。自动化生产的实现,依赖于加工过程中切削刀具状态的自动监控,国内外学者在切削力模型方面进行了大量的研究工作。其中,切削力法被认为是一种具有实际应用前景的监控方法[1]。但以往基于切削力信号的研究大多是通过单因素试验[2]确定特定情况下切削力的阈值,从而对刀具状态进行识别。这类方法存在监控阈值难以确定以及监控参数特征信息不能适应切削参数的变化即监控的柔性差等问题,仅适用于不改变或较少改变切削参数的刚性加工生产线。随着计算机技术的发展,建立可适应变工况加工的刀具状态监控系统十分必要。 影响切削力的因素有很多,其中切削用量三要素:切削速度、进给量、切削深度对切削力的影响最为显着[3]。本文以外圆车削为例,建立了基于切削参数(切削速度、进给量、切削深度)与刀具状态(主要考虑后刀面磨损量)的切削力简化模型,并通过试验值与模型的预测值之间的比较,进一步验证模型的准确性。
2 切削试验系统及方案 (1)试验装置
本试验在一台型号为CA6140的普通车床上进行,切削力信号由Kistler测力仪(传感器)检测,测出的力信号经电荷放大器放大、经过数据采集卡后可直接将信号传送到计算机。再用Kistler测力仪的配套软件Dynoware对测得的力信号进行分析和处理。试验系统组成如图1-1 所示。试验中刀面磨损状况及磨损值随时刻进行测量,使用Keyence的VH-8000系列数码显微镜对车刀后刀面的磨损状况拍照,通过测量软件测量车刀后刀面的磨损量以及刀具的破损情况。 (2) 试验方案 切削力试验分为三部分进行:使用新刀片(磨损量为零)进行切削试验;使用不同状态的刀片(变化的磨损量)进行切削试验;使用不同状态的刀片(变化的磨损量)验证已建立的刀具磨损状态下的切削力模型。 采用正交试验法安排试验,使用L9(43)正交表,为三因素、三水平试验。 具体试验正交表如表1: 表1试验计划 3 基于刀具状态的切削力模型 (1)切削力模型的简化 由于切削力经典理论模型过于繁琐的局限,难以在实际生产进行有效应用。因此,研究人员常常通过大量试验,由测力仪得到切削力后,将所得数据进行数学方法处理,即可得到切削力的试验模型。如采用指数模型计算切削力,在金属切削加工中得到广泛的应用。常用的指数模型形式如下 :
xxFxFxFxyyFyFxFyzzFzFzFFnyxpFxFnyxpFyFnyxpFzzKvfaCFKvfaCFKvfaCF 和[4]的研究表明主切削力能更准确的反映刀具磨损的程度,并建立了切削参数、后刀面磨损量与主切削力Fz的模型。式(1)切削力简化模型如下: zyxpvfakF
(2) 式中:F为切削力(N);pa为车削深度(mm);f为进给量(mm/r);v为车削速度(m/min);k、x、y、z分别为待定系数和指数,需要通过试验建立回归方程确定。 (2)基于刀具状态的切削力模型 在实际的生产过程中,切削用量为已知量,刀具的磨损量未知。参考已
试验 号 试验因素(切削三要素) 试验结果记录 切削速度 Fx(N) Fy(N) Fz
(N)
主轴转速r/min 线速度m/ min 进给
量mm/ r
切削深
度mm
1 320 60 2 500 95 3 710 135 4 320 60 5 500 95 6 710 135 7 320 60 8 500 95 9 710 135 刀具后刀面磨损量VB(㎜)
(1) 建立的切削力模型,考虑到刀具磨损量的与切削用量之间的相互影响,建立一个以刀具的磨损量和切削三要素为自变量、切削力Fz为因变量的函数方程(即切削力模型)。 在原有切削力模型的基础上引入VB因素,试验数据表明,当VB≤, 切削力上升较平缓;当VB在附近, 切削力上升较陡峭;当VB≥, 切削力上升有趋于平缓。因此,VB=是一个突变点,对切削力模型有重大影响。切削力模型如下: zyxpwVvfakFB)(30.11
(3) 式中:F为切削力(N);pa为车削深度(mm);f为进给量(mm/r);v为车削速度(m/min);k、x、y、z分别为待定系数和指数,需要通过试验建立回归方程确定。 4 试验结果与讨论 (1)正交试验数据的处理 切削试验获得刀具处于不同状态的切削力信号,选择具有代表性的VB=0㎜、VB=㎜、VB=㎜等三组试验处理结果(见表2~表4)。 表2 试验结果一 表3 试验结果二 表4 试验结果三
在相同的切削用量,不同的切削刀具后刀面磨损量下,切削力随磨损量变化而变化。变化有增大的趋势,但并不完全对应,在初始阶段上升较快,随后又缓缓上升, 至VB=时上升较突然,然后又开始缓升。 (2) 基于刀具状态的切削力模型拟合 对式(3)两边同时取对数,可得: vzfyaxwkFpVBlnlnln)ln(lnln30.11
顺序 组别 第一组 磨损量VB(mm) 0 切削用量 切削力 主轴转切削速进给切削深Fx Fy Fz
1-320 60 1-500 95 1-710 135 1-320 60 1-500 95 1-710 135 1-320 60 1-500 95 1-710 135
顺序组别 第二组 磨损量VB(mm) 切削用量 切削力 主轴转切削速进给切削深Fx Fy Fz
2-320 60 2-500 95 2-710 135 2-320 60 2-500 95 2-710 135 2-320 60 2-500 95 2-710 135
顺 序 号
组别 第三组 磨损量VB(mm) 切削用量 切削力 主轴转速速/min 切削速度m/min 进给量 mm/r
切削深
度 Fx (N) Fy (N) Fz (N)
3-1 320 60 3-2 500 95 3-3 710 135 3-4 320 60 3-5 500 95 3-6 710 135 3-7 320 60
3-8 500 95 3-9 710 135 (4) 则切削力的对数同切削用量及磨损量的对数关系就变成为线性关系,成为多元线性回归方程。 利用表2中的数据,拟合出基于切削用量和刀具状态的切削力模型如下: 198.0534.0616.088.030.11)(58.137VfaFPVzB
(5) 式中已含有后刀面磨损量。刀具磨损量作为切削力模型的参数,更能反映出切削用量和刀具后刀面磨损量与切削力的的内在关系,为切削刀具状态的检测打下了坚定基础。 (3) 基于刀具状态的切削力模型检验 表5中试验值Fzs用于模型拟合,预测值Fzc用式(5)计算出的切削力Fz值。显然,预测值与试验值的相对误差很小,多数在-5%~5%之间,最大不超过10%,相对误差平均为,显示出该回归模型具有较好的拟合度。切削力Fz、预测值Fzc与试验值Fzs符合程度较高,能比较准确地反映切削力Fz与切削用量和刀具后刀面磨损量的内在联系,各切削用量指数客观地体现
各因素在切削力模型中的作用或影响,特别是后刀面磨损量作为切削力模型的重要参数,建立起刀具后刀面磨损量VB与主切削力Fz的模型,确立了后刀面磨损量与切削力Fz的内在关系,探索出磨损量影响切削力的内在规律;为建立基于切削力模型的刀具状态检测做好准备。 表5 试验数据及预测值 序号 切削用量 刀具磨损试验值Fzs 预测值Fzc Fzs/Fzc 相对误差
切削进给背
1 60 0 2 60 3 60 4 60 5 60 6 60 7 60 8 95 0 9 95 10 95 11 95 12 95 13 95 14 95 15 135 0 16 135 17 135 18 135 19 135 20 135 21 135 Fz平均值及平均误差
5 结论
建立了基于切削参数和刀具状态的车削力简化模型, 通过对试验值与模型的预测值进行比较,验证模型的准确性。 基于多因素试验建立的模型可适应变工况的加工,模型的试验验证成功为建立可适应变工况加工的刀具状态监控系统提供了一种较准确的监控方法,同时为多传感器信号耦合(切削力、切削功率、声发射等)提供了基础。 以外圆车削试验建立的力模型为基础,可以尝试为其他常见的加工过程如铣削加工、钻削加工等建立类似的力模型,以解决变工况加工的刀具状态监控问题。 参考文献 [1] Dimla E. Dimla Snr. Sensor signals for tool-wear monitoring in metal cutting operations—a review of methods [J].International