刀具状态检测方法.
对刀仪使用方法

对刀仪使用方法随着的广泛使用,许多用户也开始使用刀具装置;它不仅可以检测刀具的磨损情况,而且可实现自动补偿通过修改刀补值实现,极大的提高了加工效率和精度;另外,同时使用其刀具破损检测功能与刀具寿命管理功能,还可以实现自动寻找同组刀具的功能,节约了刀具检查和更换的时间;但由于用户对原理不是很了解,使用时容易产生误区,有时补偿后的精度反而不如补偿前,这就使用户产生了迷惑,限制了测量装置的广泛使用;本文以英国" tar get="_blank" class="keylink">雷尼绍公司TS27 R测头的安装调试为例,就如何更好的使用刀具测量装置做一详细介绍,供读者参考借鉴;刀具测量的基本原理是利用系统的跳步功能G31:在程序中指令“G31 Zx x x Fx x x”与GO1的动作相同;但此时如果SKIP信号由“0”变为“1”时,Z轴将停止运动,再用宏程序控制坐标轴后退,然后再次碰触量块,反复测量并运算后得出刀具的实际长度和直径,最后修改系统宏变量从而达到修改刀补值的目的;刀具测量装置的使用主要包括三个步骤:安装和接线;标定;测量;1 安装和接线刀具侧量装置通常包括测头和信号转换装置硬件及相关的测量程序软件包;测头TS27R 安装在工作台上,并尽量远离加工区域,外部应加防护装置,使用前先将防护装置打开并将刀具用风吹干净用M代码控制气动元件可实现自动,确保刀具表面无杂物,测量完成后关闭防护;测头安装完成后,首先要调整测头接触面的平行度和直线度;将一只百分表或千分表DT I吸在头上,表头打在量块圆形或方形的上表面;用手轮控制X轴沿量块表面来回移动,观察表针变化,同时调整测头上的调节螺钉,使X向的直线度保证在0.010mm,调整好后紧固螺钉;再控制Y轴沿量块表面来回移动,同时调整测头上的调节螺钉,使Y向的直线度也保证在0.010mm,调整好后紧固螺钉;转换装置MI 8-4用35mm标准导轨安装在电气柜里;需要注意的是,给转换装置提供DC 24V的稳压电源最好是单独的,尽量不要和电磁阀或中间继电器共用电源,如果必须共用,就要考虑信号的抗干扰能力,否则可能会影响测量结果;安装结束后,按照图1三菱系统或图2系统正确接线;图1 测量装置接线原理图三菱64M系统图2 测量装置接线原理图-0i-M系统2 测头的标定为了确定测头在坐标系中的坐标位置,需要对测头进行标定;以下情况进行测量前,都必须首先进行测头的标定:①首次使用前;②更换新量块后;③怀疑量块扭曲或测头安装松动;④意外碰撞后;测头的标定步骤如下手动标定:1 量块Z向坐标值的确定执行返回参考点的操作,确认机床参考点;再选择一把标准刀具已知该刀具精确的长度和直径,如检棒,手动使刀具运行到距离量块上表面10mm的地方起始位置,选择MDI方式,执行如下程序:G65 P9851 K:代表标定循环,输入所选标准刀具的精确长度,结束后就建立了量块的Z向坐标值;2 量块X,Y向坐标值的确定以圆形量块为例在系统变量530中设定“1”沿X轴方向测量,手动使标准刀具移动到距离量块中心表面约10mm的地方,执行程序:G65 P9852 ;S:标准刀具直径,需输入精确值;K:表示标定循环,输入量块的理论尺寸理论尺寸2.7mm〕,结束后就建立了量块在X方向的中心位置循环结束后,主轴返回距离量块表面10mm的初始位置,准备进行下一次Y向的测量循环;修改方向变量530=2,再次执行G65 ,则可建立Y向的位置以及量块的尺寸;循环结束后主轴返回初始位置;标定的坐标值和量块的尺寸被存储到宏变量中断电保持型,以便在以后的测量宏程序中使用;以上是手动标定量块位置的方法;还可以通过一些专用的标定程序自动标定;限于篇幅,这里不再赘述,详细的资料参见RENISHAW的手册介绍;3 刀具的测量标定完成后,就确定了量块的尺寸及其在机床坐标系中的位置,这时才可进行刀具测量;1 手动刀具长度测量09851用于测量旋转或非旋转的刀具的有效切削长度;使用方法:手动使切削刀具定位到距离量块上表面10mm的地方,运行以下程序:G65 P9851 S80. T8S80:被测刀具的理论切削直径,T8:刀具长度偏置号8〕;图3 刀具长度测量图4 刀具直径测量2 手动刀具直径测量09852测量切削刀具的有效切削直径沿X或Y方向;使用方法:手动使切削刀具定位到距离量块上表面10mm的地方,运行以下程序:G65 P9852 S80. D8. S80.:切削刀具直径,D80.:刀具半径的偏置号码;机床运动步骤如下见图4:刀具以程序指定的速度沿X向或Y向快速运动→使刀具的侧面和量块的侧面产生一定距离Rr→然后Z轴向下运动,使刀具侧面和量块侧面在同样的高度→刀具以指定速度逼近量块→碰上量块后停止并后退一定距离→再减速逼近量块→碰上后再次停止并后退一定距离→然后刀具再运行到量块的另外一边180°方向→用同样的步骤进行测量;最后得出刀具的实际切削直径,同时自动修改其补偿值;下次加工时,就可以使用新的刀具半径补偿值了;3 自动刀具长度和直径测量09853测量旋转的切削刀具或不旋转的有效切削长度和直径,也可用于刀具破损检测;注意:测量前,首先应在对应的刀具偏置表中设定理论的刀具长度和半径值;编程格式:G65 P9853 Bb TtDd Ss;:代表选择项目输入参数的定义,B按以下设定:B=1,仅测量长度缺省设定;B=2,仅测量直径;B=3,长度和直径都测量;D:要更新的刀具半径偏置号码仅用于旋转刀具测量;如欲同时测量刀具长度和直径,则指令B=3,执行程序:G65 P9853 B3 .T1. D20.S30;机床运行步骤如下见图5:从刀库中选择刀具T1A→快速移动X和y轴→使刀具位于量块的上方B→快速向下移动到逼近位置并调用T1的刀具补偿值→慢速移动到净空位置距离量块上表面10mm的地方→测量刀具长度旋转或非旋转,与09851的步骤一样→测量刀具半径旋转或非旋转,与09852的步骤一样→退回起始点;图5 刀具长度和直径自动测量注意:如果未使用Ss,则必须在刀具补偿页面输入刀具半径的理论尺寸;4 刀具破损检测09853使用方法:执行如下编程格式的程序,当检测到刀具的实际长度或半径的破损值已经超出设定范围时,会产生刀具破损报警或提示信息,用户可根据实际情况进行处理;编程格式:G65 P9853 B1. T1. H0. 5 D8. .R3 .Z-4. M30. 10. 01其中:Hh中的h为刀具破损允许差值,如定义,即检查刀具损耗与偏置值是否在±0.5m m之内;Mm中的m为PLC的输入信号地址,当检测到刀具破损时,该信号将变为“1”,无破损时则为“0”;此时的“M”代表宏变量,不同于一般的M代码,请使用者注意区分;当定义M30时,则当检测到刀具破损时,宏变量2030即2000+M将变为“1”,此时不会出现报警,但可以在零件程序中检查2030的状态,同时在PLC中处理该信号去报警或者去寻找同样的刀具见例2,后者需要系统具备刀具寿命管理的功能;例1:破损刀具处理方法1——仅提示报警M06 T1 选择T1刀具G65 P9853 B1. T1. 检测刀具是否破损,如超差则会出现刀具破损报警M06 T2 选择下一把刀进行加工在上例中,只有破损超出0.5mm时才会产生“BROKEN TOOL”服警;当不适合使用报警信息的时候,可以使用标志位提示在PLC中处理;例2:破损刀具处理方法2——选择同组同样的刀具继续加工M06 T1 选择T1刀具…… 加工G65 P9853 B1. T1. H0.5 M30 检测刀具是否破损,如超差则会出现刀具破损报警IF 2030 EQ1 GOTO N 如果标志位为1,则跳转到N段去,否则继续M06 T2 选择下一把刀进行加工N 重新开始循环 N:去寻找同组刀具与破损刀具相同的刀具的程序段4 结语刀具测量的过程比较简单,但首次使用前的调整和标定非常重要,用户一定要非常重视;当改变测头的安装位置后、测量精度经常有误差、怀疑测头松动、更换新量块或意外碰撞后,都必须重新进行标定;为了防止意外碰撞,可定期的检查SKIP信号是否灵敏;这可在系统的自诊断画面上看到:人为使测头动作,SKIP信号应该有0→1→0→1的变化;另外还应注意电缆的走线,尽量与动力线分开,并单独给转换装置提供DC24V电源;由于系统的不同,所使用的测量程序也不尽相同,但测量原理都是一样的;用户在使用前一定要明确机床所用的系统类型,再去购买专用的测头和测量程序软件;。
10-11机械制造自动化技术-检测过程自动化

5
▲ 检测方法 ——直接测量与间接测量 ——接触测量和非接触测量
——在线测量和离线测量
直接测量:测量时,直接从测量器具上读出被测几 何量的大小值 ,测量过程迅速,应用广泛。 间接测量 :被测几何量无法直接测量时,首先测出与 被测几何量有关的其他几何量,然后,通过一定的 数学关系式进行计算来求得被测几何量的尺寸值 。
18
磨床的专用自动检测装置
图中机床、执行机构与测量装置构成一个闭环系统。在 机床加工工件的同时,自动测量头对工件进行测量,将测得 的工件尺寸变化量经信号转换放大器,转换成相应的电信号
并经过放大后返回机床控制系统,控制机床的执行机构,从
而控制加工过程(如刀具补偿、停车等)。
图 6-4 磨削加工中自动测量原理方框图
2.在线检测
分为工序间检测与最终工序检测。
工序间检测可实现加工精度的在线检测及实时补偿。 (可在后续加工工序中进行补偿,以保证此产品的尺 寸精度)。
最终工序检测对已加工完成的产品进行检测,找出误 差产生的原因,调整加工过程。(以保证下一个产品 的尺寸精度)
15
工件尺寸、形状的在线测量是机械加工中很重要的功能。 工件的工件的尺寸和形状误差分为:
有关机床、产品及加工过程的信息。 ——自适应控制:指加工系统能自动适应客观条件的变化而进行 相应的自我调节。
29
▲实现在线检测的方法——一种可采用在机床上安装自动检 测装置;另一种可采用在自动线中设置自动检测工位的方法。
自动化单机——可在机床上安装自动尺寸检测装置与自动补偿装置。
可组成自动线——也具有自动检测与补偿功能。
7
在线测量:在加工过程或加工系统运行过程中对被
测对象进行检测。通常还得对测得数据进行分析处 理,再反馈控制系统调整加工过程,可实现自动化 测量。 离线测量:在被测对象加工后脱离加工系统在进行
自动切割机刀具破损检测方法

自动切割机刀具破损检测方法孙敏;杨云龙【摘要】文章介绍了自动切割机的刀具破损的检测原理,并进行了方法设计.对实验得到的数据分析后,结合统计学方法,使用引进的几个基本统计量,进行了算法设计,得到了一套针对有效的自动切割机的刀具破损检测方法.【期刊名称】《电子工业专用设备》【年(卷),期】2010(039)012【总页数】4页(P35-38)【关键词】自动切割机;刀具破损检测;基本统计量【作者】孙敏;杨云龙【作者单位】中国电子科技集团公司第四十五研究所,北京,101601;中国电子科技集团公司第四十五研究所,北京,101601【正文语种】中文【中图分类】TN247自动切割机即针对为划切对象的自动砂轮划片设备。
砂轮划片机是以强力磨削为划切原理,空气静压电主轴为执行元件,以30000~60000 r/min的转速磨削晶圆的划切区域,同时承载着晶圆的工作台以一定的速度沿刀具与晶圆接触点的划切线方向呈直线运动,将每一个具有独立电气的芯片分裂出来。
工作原理如图1所示。
方形扁平无引脚封装(Quad Flat No-Lead Package)是一种焊盘尺寸小、体积小、以塑料作为密封材料的新兴的表面贴装芯片封装技术。
正是因为划切对象特殊性,使得自动切割机和传统的砂轮划片机有一些不同。
基板为塑料材质,本身在制作过程中就对通道平行度控制的不是很高,并且在划切过程中划切通道可能会变形。
因此传统的对准模式不适合切割机,需要频繁对准导致速度慢,准确度不高。
本项目针对这些特点为划切定制出一台针对性强的划片设备。
图1 原理示意图对于自动切割机来说,刀具破损检测功能是必不可少的。
首先芯片底部为延展性强的金属,使得刀片磨损量过大。
其次切割对效率要求很高,人为监控必定降低切割效率,达不到自动切割的要求。
这些特点就使得刀具破损检测在自动切割机中成为必要功能之一。
1 光纤检测原理与方法BBD(Blade Breakage Detection)即刀具破损检测。
基于小波-神经网络纹理图像识别的刀具状态监测

b s n s a i a d d ’ mi e r ewo k i d v s d t e s t a eu e u t gt o ig o i i l a e o tt y a c n u a n t r s e ie , yse c n b s d i c ti l a s al d cn n l h m n n o d n sn -
( . 家庄职 业技 术学 院 机 电系 , 家庄 1石 石 北 师范大 学 电子 系, 家庄 0 o 3 ) 石 5 0 1 摘要 : 绍 了一种 采集旋 转工件 图像 的 光 学监 测 系统 , 出通 过 二 维 小波 分 析 工件 纹 理 图像 , 取 纹 理 介 提 提 特征 , 计 了基 于动 态和 静 态神 经 网络 的 刀具 状 态识 别 系统 , 系统 可用 于 自动 化 加 工 中刀具诊 断 , 设 该 仿 真证 明 了有效 性 。 关键 词 : 刀具状 态监 测 ; 图像 处理 ; 理分析 ; 经 网络 纹 神 中图分类 号 : G 5 T 6 文献标 识码 : A 0 0 8 ; . 京理 工 大 学 电子 工 程 系 , 京 10 8 ; . 50 l 2 北 北 0 0 1 3 河
( . hJZ u n oai a T c n l y Istt,S iah ag0 0 8 ,C ia . e a meto lc o i 1 S i h a g V ct n l eh oo ntue hj z un 5 0 hn ;2 D p r n fEet nc a o g i i 1 t r E g er g B in stt o eh o g , e ig10 8 , hn ) ni ei , e igI tu f c nly B in 0 0 C ia n n j ni e T o j 1
CNC机床加工中的刀具磨损检测与修复技术改进与应用
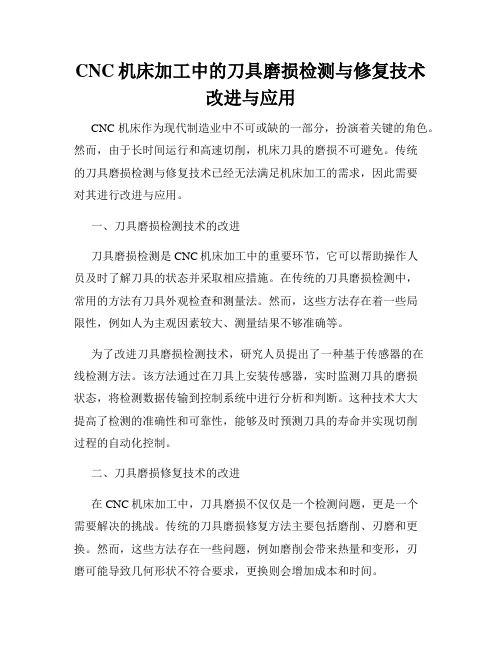
CNC机床加工中的刀具磨损检测与修复技术改进与应用CNC机床作为现代制造业中不可或缺的一部分,扮演着关键的角色。
然而,由于长时间运行和高速切削,机床刀具的磨损不可避免。
传统的刀具磨损检测与修复技术已经无法满足机床加工的需求,因此需要对其进行改进与应用。
一、刀具磨损检测技术的改进刀具磨损检测是CNC机床加工中的重要环节,它可以帮助操作人员及时了解刀具的状态并采取相应措施。
在传统的刀具磨损检测中,常用的方法有刀具外观检查和测量法。
然而,这些方法存在着一些局限性,例如人为主观因素较大、测量结果不够准确等。
为了改进刀具磨损检测技术,研究人员提出了一种基于传感器的在线检测方法。
该方法通过在刀具上安装传感器,实时监测刀具的磨损状态,将检测数据传输到控制系统中进行分析和判断。
这种技术大大提高了检测的准确性和可靠性,能够及时预测刀具的寿命并实现切削过程的自动化控制。
二、刀具磨损修复技术的改进在CNC机床加工中,刀具磨损不仅仅是一个检测问题,更是一个需要解决的挑战。
传统的刀具磨损修复方法主要包括磨削、刃磨和更换。
然而,这些方法存在一些问题,例如磨削会带来热量和变形,刃磨可能导致几何形状不符合要求,更换则会增加成本和时间。
为了改进刀具磨损修复技术,研究人员提出了一种基于涂层修复的方法。
该方法通过在刀具表面涂覆一层特殊的涂层材料,提高刀具的抗磨性和耐热性。
这种涂层修复技术不仅可以延长刀具的使用寿命,还可以减少因修复而带来的误差和变形。
三、刀具磨损检测与修复技术的应用刀具磨损检测与修复技术的改进对CNC机床加工具有重要意义,可以提高加工质量和效率。
该技术的应用涉及到各个领域,包括航空航天、汽车制造、电子设备等。
以航空航天为例,航空发动机的制造过程需要大量切削加工操作,而刀具磨损会严重影响发动机的性能和寿命。
因此,采用刀具磨损检测与修复技术可以实时监测刀具状态、预测寿命并进行修复,从而提高发动机的加工质量和可靠性。
四、总结CNC机床加工中的刀具磨损检测与修复技术的改进与应用,对于提高加工质量和效率具有重要意义。
浅谈刀具磨损的小波检测

引 言
刀具 磨 损 的检 测 方 法通 常 可分 为 直 接 测 量法 和 间 接 测量 法 两 类 。直 接 测 量 法就 是 直接 测 量 刀具 后 刀面 磨损 带 中 间部 分 的 平 均磨 损 量 ;而 间接 测 量法 则 是 通过 测 量 与 刀具 磨 损 有 关 的 物 理量 (如 切 削 力 、声 发 射等 ),并 根据 它们 与 刀具 磨 损 之 间 的 对 应 关 系 来 判 别 刀具 磨 损 情 况 。 常 用 的 一种 间接测 量 法 是选 取 切 削 分 力 的 比值 和 该 比值 的 变 化作 为 判 别 刀具 磨
力 仪 :瑞 士 KI TL S ER 公 司 9 5 Al型 压 电 27
晶体测 力仪 ,采用 5 0 型 电荷放 大器,采 06 样频率为 l 0 。 HZ 0 图 la 所示 为 试 验 测得 的 刀具 磨 损 时
的 一 个 切 削 力 信 号 , 由于 背 景噪 声较 大 ,
因此 切 削 力 的 变化 曲线 较 平滑 。采 用 小 波 变换 则可 将 切 削 力的 变 化 从 背景 噪 声 中检 测出来 。设 N( 是一 个方差为 s 的 白噪 声, x) z 它实际上是一种 L p指数 为 一0. 一 (>0 的 i 5 ee )
随机分 布 ,其 小波 变换的平 均功率 为 E 1 f w (, )= Y / ,它随着尺度的增大而 8 Xl s s 迅 速 减小 ,这 也 是 小 波 变 换 的 另一 优 点 。
v-16 m/ 8 mm f O.mm/ .5 二 ,a =3 Байду номын сангаас , = 2 r ;测
关 键 词 :刀具 磨损 ;小波检 测
一
LiP 指数 也越小 ;当 刀具折 断时 ,切削 力 信号 会 发 生 突 变 ,此 时 对应 的 L iP 指 数 a =0;Li P指数越接近于 l,则说 明切 削力 越平 稳 , 刀具 的磨 损 程 度也 越 轻 。 由此 可 知 ,通过 LiP指数 对切 削 力信号 变化 程 度 的描 述 ,可 以 真实 反 映 刀具 磨 损 状 态 。 基 于上 述分 析 ,本文 将 刀具 磨 损 分 为 5 种 状 态 ,每 一 种状 态 对 应于 某 一 范 围 的 切 削 力 信号 Li P指数 ( 见表 1) ,这样就在 刀具磨 损 与 Li P指数 a之 间建立 了直接联 系 ,实 际检 测时 通过计 算切 削力 信号 的 Li 指 数 ,根 P
刀盘刀具检查作业指导书(更改)【范本模板】

刀盘刀具检查作业指导书1、目的·规范操作程序,指导现场施工;·确保刀盘、刀具检查作业的安全;·确保刀盘、刀具检查作业的质量,提高检查作业的速度;2、适用范围本指导书适用于北京地下直径线隧道工程所采用的Φ11.97m泥水加压平衡式盾构.3、刀具更换安全、质量、环境保护、文明施工管理要求(1)刀具检查必须实行土木和机电工程师值班制度;(2)刀具检查机具使用按照相关机具操作规程进行;(3)刀具检查作业中的安全,做到自防、互防和联防;(4)刀具检查所使用的废弃物应该统一回收,避免造成环境污染。
4、编制依据(1)本项目工程概况;(2)本项目工程地质、水文地质情况;(3)用于本项目的泥水气压平衡盾构机技术资料;(4)国家盾构掘进施工相关规范;(5)国家和相关行业技术规范;(6)以往盾构施工技术经验;5、 刀盘、刀具结构原理概述 5.1、刀盘的结构刀盘结构由8块辐条及8块幅板所组成,上面安装切刀和刮刀。
刀盘的中心部分做成半个小锥体,有较大的开口,便于泥渣进入开挖室内.安装在刀盘外缘的周边保护刀可以用来校准盾构的开挖直径. 仿形刀安装在刀盘的外缘上,它是通过一个液压油缸来动作的。
5.2、刀具的形式与数量名称结示意图构数量名称结示意图构数量刮刀280 边刮刀16中心刀12 保护刀166、刀具检查开仓前注意事项(1)到达停机位置前,观察掘进速度、推力、转速、压力的变化。
(2)必须由值班工程师或土木总工确认准备的停机位置,后才能停机。
(3)按照人行气闸文件中的相关章节,使工作人员适应开挖室内的压力条件,以便在压缩空气下进行工作,如果常压开仓,进入停止加压。
(4)对隧道开挖面和水位,予以严密监视。
(5)必须提供压缩空气设备,并且这些设备必须是完好可用的。
(6)只有当设备处于怠速备用状态下,方可进行维护工作;(7)气闸室作为应急室使用,必须保证所有人员随时可以进入.门锁不得被管路、缆线或其它材料堵塞.(8)所有人员均必需佩戴安全用具,并且必须将其固定到专用的固定点上,特别是在对刀盘作业过程中.(9)开挖室内具备新鲜的气源。
复合地层中盾构刀具磨损的检测方法

复合地层中盾构刀具磨损的检测方法(总12页)-CAL-FENGHAI.-(YICAI)-Company One1-CAL-本页仅作为文档封面,使用请直接删除复合地层中盾构刀具磨损的检测方法研究张厚美(广州市盾建地下工程有限公司,广州,510030)摘要:刀具磨损严重是盾构在复合地层中施工遇到的最大难题之一,刀具磨损检测技术是盾构施工的一个重要研究课题。
本文结合实际工程对运用掘进参数检测刀具磨损的方法进行了探索研究。
介绍了刀具失效的常用判断方法、运用掘进参数检测滚刀失效的原理、滚刀磨损或失效的判断方法以及工程应用实例。
初步研究结果表明,掘进参数的计算原理是正确的,方法是可行的;计算值和实际值变化趋势是一致的;刀具磨损情况检测结果与实际换刀情况是相吻合的。
经常进行刀具检查,尽早更换磨损或失效的刀具是正确的选择。
主题词:盾构,刀具磨损,复合地层,检测模型,切削力,掘进参数Study on the method of estimating cutter wear of shield in mix-facegroundZhang Hou-meiGuangzhou Municipal Dunjian Underground Construction Eng. CO.,Ltd.,Guangzhou 510030,ChinaAbstract:One of the most difficult problem of shield tunnelingin mix-face ground is the severe wear of cutters.How to estimate the cutter wear in mix-face ground is an important task for shield tunneling. The method estimating the cutter wear by analyzing the tunneling parameters is presented in this paper. General approaches for estimating the cutter wear ,the principle of estimating thecutter wear and an engineering example are also introduced.A comparison is made between the calculating parameters and the performance of shield in the field.Tt is shown that the method estimating the cutter wear is feasible, the estimation results are reasonable and in accordant with the case of cutters change.Examining the cutters regularly and changing the worn cutters in good time is necessary for shield tunnelling.Key words:shield,cutter wear, mix-face ground , estimating method, cutting force,tunneling parameter引言随着盾构机制造技术的发展,盾构机的适应地层范围越来越广,盾构技术不仅在比较均匀、单一的土层中得到广泛应用,也在各种软硬交替的复合地层中得到了应用。
- 1、下载文档前请自行甄别文档内容的完整性,平台不提供额外的编辑、内容补充、找答案等附加服务。
- 2、"仅部分预览"的文档,不可在线预览部分如存在完整性等问题,可反馈申请退款(可完整预览的文档不适用该条件!)。
- 3、如文档侵犯您的权益,请联系客服反馈,我们会尽快为您处理(人工客服工作时间:9:00-18:30)。
刀具状态检测方法
1. 1 直接测量法
直接测量法能够识别刀刃外观、表面品质或几何形状变化, 一般只能在不切
削时进行。
它有两个明显的缺点: 一是要求停机检测, 占用生产工时; 二是不能
检测加工过程中出现的刀具突然损坏, 使其应用受到限制。
主要方法有: 电阻测量法、刀具工件间距测量法、射线测量法、微结构镀层法、光学测量法、放电电流测量法、计算机图像处理法等。
a 电阻测量法
该方法利用待测切削刃与传感器接触产生的电信号脉冲, 来测量待测刀具的实际磨损状态。
该方法的优点是传感器价格低, 缺点是传感器的选材必须十分注意, 既要有良好的可切削性, 又要对刀具寿命无明显的影响。
该方法的另一个缺点是工作不太可靠, 这是因为切屑和刀具上的积屑可能引起传感器接触部分短路, 从而影响精度。
b 刀具工件间距测量法
切削过程中随着刀具的磨损, 刀具与工件间的距离减小, 此距离可用电子千分尺、超声波测量仪、气动测量仪、电感位移传感器等进行测量。
但是这种方法的
灵敏度易受工件表面温度、表面品质、冷却液及工件尺寸等因素的影响, 使其应用受到一定限制。
c 射线测量法
将有放射性的物质掺入刀具材料内, 当刀具磨损时, 放射性的物质微粒就会随切屑一起通过一个预先设计好的射线测量器。
射线测量器中所测得的量是同刀具磨损量密切相关的, 射线剂量的大小就反映了刀具磨损量的大小。
该法的最大弱点是, 放射性物质对环境的污染大, 对人体健康非常不利。
此外, 尽管此法可以测量刀具的磨损量, 并不能准确地测定刀具切削刃的状态。
因此, 该法仅适用于
某些特殊场合, 不宜广泛采用。
d 微结构镀层法
将微结构导电镀层同刀具的耐磨保护层结合在一起。
微结构导电镀层的电阻随着刀具磨损状态的变化而变化, 磨损量越大, 电阻就越小。
当刀具出现崩齿、折断及过度磨损等现象时, 电阻趋于零。
该方法的优点是检测电路简单, 检测精度高, 可以实现在线检测。
缺点是对微结构导电镀层的要求很高: 要具有良好的耐磨性、耐高温性和抗冲击性能.
e 光学测量法
光学测量法的原理是磨损区比未磨损区有更强的光反射能力, 刀具磨损越大, 刀刃反光面积就越大, 传感器检测的光通量就越大。
由于热应力引起的变形及切削力引起的刀具位移都影响检测结果, 所以该方法所测得的结果井非真实的磨损量, 而是包含了上述因素在内的一个相对值, 此法在刀具直径较大时效果较好。
f 放电电流测量法
将切削刀具与传感器之间加上高压电, 在测量回路中流过的(弧光放电电流大小就取决于刀刃的儿何形状( 即刀尖到放电电极间的距离。
该方法的优点是可以进行在线检测, 检测崩齿、断刀等刀具几何尺寸的变化, 但不
能精确地测量刀刃的几何尺寸。
g 计算机图像处理法
计算机图像处理法是一种快捷、无接触、无磨损的检测力法, 它可以精确地检测每个刀刃上不同形式的磨损状态。
这种检测系统通常由CCD 摄像机、光源和计算机构成。
但由于光学设备对环境的要求很高, 而实际生产中刀具的工作环境非常恶劣( 如冷却介质、切屑等, 故该方法目前仅适用于实验室自动检测。
1. 2 间接测量法
间接测量法是利用刀其磨损或将要破损时的状态对不同的工作参数的影响效果, 测量反映刀具磨损、破损的各种影响程度的参量, 能在刀具切削时检测, 不影响切削加工过程, 其不足之处在于检测到的各种过程信号中含有大量的干扰因素。
尽管如此, 随着信号分析处理技术、模式识别技术的发展, 这一方法已成为一种主流方法, 并取得了很好的效果。
主要方法有: 切削力检测法、声发射检测法、功率信号检测法、振动信号检测法、切削温度测量法、电流信号测量法、热电压测量法、工件表面粗糙度测量
a 切削力检测法
刀具在切削过程中, 切削力的增长速率与刀具磨损速率成线性关系。
在正常磨损过程中, 切削力的增长速率保持恒量; 当切削力增长速率变大时, 刀具的磨损速率也将变大, 表明刀具开始进入剧烈的磨损阶段。
以此为依据可以对刀具的磨损进行监测。
利用测力传感器, 可以测量切削力的变化。
随着刀具磨损的加剧, 切削力也会产生相应的变化, 从而可以间接地检测到刀具的磨损状态。
该法的优点是具有较好的抗干扰能力和较高的识别精度, 可以实现在线检测。
缺点是传感器的安装需要对机床作些改动, 不易被用户接受。
b 声发射检测法
此法通过分析切削过程中产生的振动信号来间接地测量刀具的磨损状态。
其原理是材料在切削过程中, 形成切屑, 同时发出一种断裂波, 这种波除了同工件材料本身的性质有关外, 其频率范围及幅值还同刀具的磨损状态密切相关。
声发射信号直接来源于切削加工点, 与刀具破损相关程度高, 受切削条件变化影响小, 能预报刀具破损。
声发射监控技术具有灵敏度高、响应速度快、使用和安装方便且不干涉切削加工过程等优点, 受到了极大程度地重视与
开发, 有较广阔的应用前景
c 功率信号检测法
该检测法是工业生产中应用潜力很大的方法。
利用切削加工时机床主运动电
动机的功率信号监控刀具的状态, 当刀具在加工过程中发生磨损破损或其它失效时, 会引起驱动电动机的功率发生变化, 从而可判断刀具状态的化。
在使用该法时, 通常是把功率传感器串接到机床的驱动电路中去, 可以测量主轴的功耗, 也可以测量进给系统的功耗, 或者两者同时测量。
该方法具有信号检测方便, 可以避免切削环境中切屑、油、烟、振动等因素的干扰, 易于安装。
d 振动信号检测法
振动信号被认为是对刀具磨损, 破损敏感度较高的一种, 它与切削力、切削
系统本身的动态性密切相关, 检测振动加速度是目前较常采用的一种监测方法, 在振动工程中使用更为普遍, 它具有传感器安装方便, 测量信号易于引出, 测试仪器简单等特点。
e 切削温度测量法
切削热是金属切削过程中的一种重要现象, 刀具的磨损或破损会导致切削温度急剧升高。
用热电偶作为传感元件, 把热电偶嵌入刀具中测量切削温度, 可以实现刀具状态的在线监测, 但这种方法的发展前途不大。
f 电流信号测量法
该方法简称MCSA ( m otor current signal ana lys is,利用感应电动机的定子电流作为信号分析的切入点, 研究其特征与故障的对应关系。
其基本原理是: 随着刀具磨损的增大, 切削力矩增大, 机床所消耗的功率增大或电流上升, 故可实现在线地监测刀具磨损。
M CSA 具有测试便利、信息集成度高、传动路径直接、信号提取方便、不受加工环境的影响、价格低、易于移植等特点, 在机床这种传动系统封闭、一般传
感器比较困难安装的场合, 应该是一种值得探索的方法。
g 热电压测量法
热电压测量法利用热电效应原理, 即两种不同导体的接触点在受热时, 将在两导体的另一端之间产生一个电压, 这个电压的大小取决于导体的电特性及接触点与自由端之间的温度差。
当刀具和加工工件是由不同的材料构成时, 在刀具与工件之间就可以产生一个与切削温度相关的热电压。
这个电压就可以作为刀具磨损量的一个度量, 因为随着刀具磨损量的增大, 热电压也随之增大。
该方法的优点是价格便宜, 精度较高, 使用简便, 特别适用于高速加工区, 缺点是对传感器材料及精度要求高, 只能进行间隔式检测。
h 工件表面粗糙度测量法
随着刀具磨损或破损的不断发生, 工件的表面粗糙度呈增大趋势, 据此可间接评价刀具的磨损或破损状态。
其测量方法有两类: 一类是采用划针式静态接触测量, 可直接得出表面粗糙度的评价参数Ra 或Rz, 该方法仅适用于静态测量; 另一类是采用非接触式光学反射测量, 得出的是工件表面粗糙度的相对值。
这种方法测试效率高, 不会损伤工件表面品质, 但受加工过程中切削液、切屑、材质、振动等因素的影响, 因此尚未达到实用水平。