检测刀具磨损和破损的方法
自动切割机刀具破损检测方法

自动切割机刀具破损检测方法1.视觉检测法视觉检测法是一种高效、准确的刀具破损检测方法。
通过安装摄像头和光源,实时拍摄刀具工作时的图像,并通过专用软件进行图像处理和分析,识别和判断刀具是否破损。
使用这种方法,可以检测到刀具的缺口、断刃、磨损、变形等破损情况,并及时发出警报,以便及时更换损坏的刀具。
2.声音检测法刀具在工作时会发出特定的声音,当刀具破损时,其声音会发生变化。
利用这一特点,可以通过声音检测来判断刀具是否破损。
通过安装专用的声音传感器或麦克风,接收刀具工作时发出的声音,并通过信号处理和分析,判断刀具的破损情况。
比如,可以检测到刀具的异响、偏声、共振等信号,这些都可能是刀具破损的表现,从而及时发出报警信号。
3.动态力学检测法刀具在工作时会产生一定的力学响应,当刀具破损时,其力学响应会发生变化。
利用这一原理,可以通过安装力传感器或加速度传感器,测量刀具工作时的力学响应,并通过信号处理和分析,判断刀具的破损情况。
比如,可以检测到刀具的振动幅度、频率、相位等参数,这些都可能是刀具破损的表现,从而及时发出报警信号。
4.温度检测法刀具在工作时会产生一定的热量,当刀具破损时,其热量分布会发生变化。
利用这一原理,可以通过安装红外线温度传感器,测量刀具工作时的温度分布,并通过信号处理和分析,判断刀具的破损情况。
比如,可以检测到刀具的局部过热、散热不均等现象,这些都可能是刀具破损的表现,从而及时发出报警信号。
综上所述,自动切割机刀具破损检测方法包括视觉检测法、声音检测法、动态力学检测法和温度检测法等。
以上方法各有优势和适用场景,可以根据具体的生产需求选择相应的方法进行刀具破损检测,以保障生产效率和产品质量。
机床刀具磨损检测方法
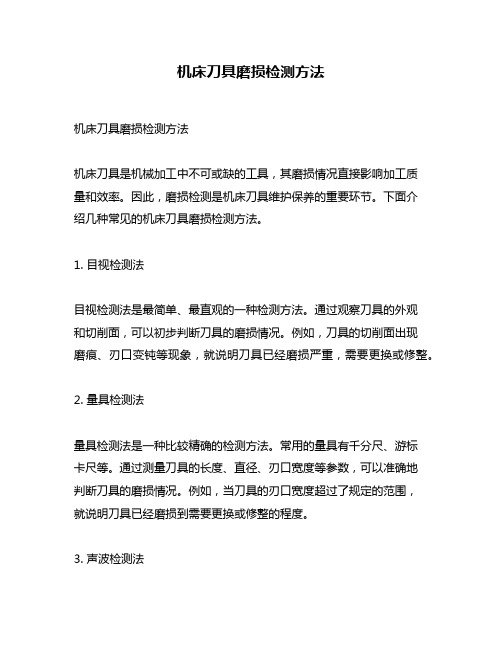
机床刀具磨损检测方法机床刀具磨损检测方法机床刀具是机械加工中不可或缺的工具,其磨损情况直接影响加工质量和效率。
因此,磨损检测是机床刀具维护保养的重要环节。
下面介绍几种常见的机床刀具磨损检测方法。
1. 目视检测法目视检测法是最简单、最直观的一种检测方法。
通过观察刀具的外观和切削面,可以初步判断刀具的磨损情况。
例如,刀具的切削面出现磨痕、刃口变钝等现象,就说明刀具已经磨损严重,需要更换或修整。
2. 量具检测法量具检测法是一种比较精确的检测方法。
常用的量具有千分尺、游标卡尺等。
通过测量刀具的长度、直径、刃口宽度等参数,可以准确地判断刀具的磨损情况。
例如,当刀具的刃口宽度超过了规定的范围,就说明刀具已经磨损到需要更换或修整的程度。
3. 声波检测法声波检测法是一种非接触式的检测方法。
通过检测刀具在切削过程中产生的声波信号,可以判断刀具的磨损情况。
当刀具磨损严重时,切削时产生的声波信号会发生变化,可以通过分析信号的频率、振幅等参数来判断刀具的磨损情况。
4. 热成像检测法热成像检测法是一种基于红外线技术的检测方法。
通过拍摄刀具在切削过程中产生的热像,可以判断刀具的磨损情况。
当刀具磨损严重时,切削时产生的热量会增加,从而在热像上表现为明显的热点。
通过分析热像的颜色、亮度等参数,可以准确地判断刀具的磨损情况。
总之,机床刀具磨损检测是机床维护保养的重要环节,不同的检测方法各有优缺点,可以根据具体情况选择合适的方法进行检测。
在实际应用中,可以结合多种检测方法,以提高检测的准确性和可靠性。
刀具破损的检测方法
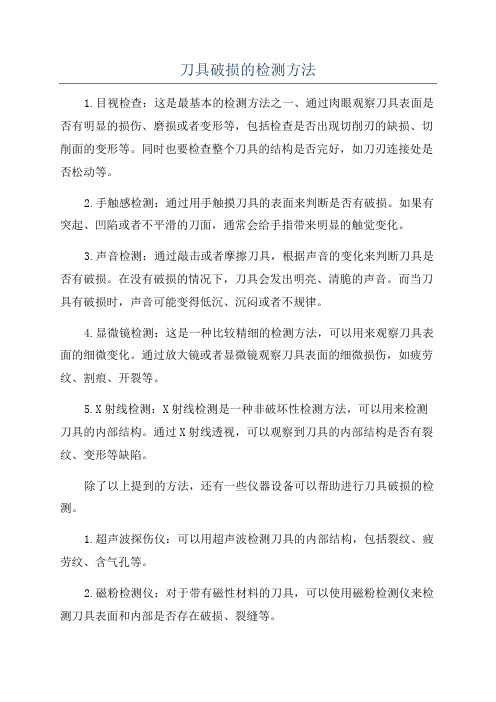
刀具破损的检测方法
1.目视检查:这是最基本的检测方法之一、通过肉眼观察刀具表面是否有明显的损伤、磨损或者变形等,包括检查是否出现切削刃的缺损、切削面的变形等。
同时也要检查整个刀具的结构是否完好,如刀刃连接处是否松动等。
2.手触感检测:通过用手触摸刀具的表面来判断是否有破损。
如果有突起、凹陷或者不平滑的刀面,通常会给手指带来明显的触觉变化。
3.声音检测:通过敲击或者摩擦刀具,根据声音的变化来判断刀具是否有破损。
在没有破损的情况下,刀具会发出明亮、清脆的声音。
而当刀具有破损时,声音可能变得低沉、沉闷或者不规律。
4.显微镜检测:这是一种比较精细的检测方法,可以用来观察刀具表面的细微变化。
通过放大镜或者显微镜观察刀具表面的细微损伤,如疲劳纹、割痕、开裂等。
5.X射线检测:X射线检测是一种非破坏性检测方法,可以用来检测刀具的内部结构。
通过X射线透视,可以观察到刀具的内部结构是否有裂纹、变形等缺陷。
除了以上提到的方法,还有一些仪器设备可以帮助进行刀具破损的检测。
1.超声波探伤仪:可以用超声波检测刀具的内部结构,包括裂纹、疲劳纹、含气孔等。
2.磁粉检测仪:对于带有磁性材料的刀具,可以使用磁粉检测仪来检测刀具表面和内部是否存在破损、裂缝等。
3.红外热像仪:可以利用热辐射检测方法来观察刀具表面的温度分布,以判断刀具是否存在热变形、烧损等。
总之,刀具破损的检测方法多种多样,可以选择适合的方法来进行检测。
在使用刀具之前,进行破损检测可以保证刀具的安全和使用效果。
刀具检测范本

刀具检测范本
刀具检测范本
为了确保刀具的质量和安全使用,我们对刀具进行了严格的检测。
以下是我们的刀具检测范本。
一、外观检测
1. 检查刀具的表面是否有变形、裂缝、锈蚀等缺陷。
2. 检查刀具的刀刃是否锋利,是否有缺口或不均匀的刀刃。
3. 检查刀具的把手是否牢固,是否有松动或裂纹。
二、尺寸检测
1. 使用测量工具测量刀具的整体长度,宽度和厚度。
2. 使用测量工具测量刀刃的长度,角度和厚度。
三、硬度检测
1. 使用硬度测定仪对刀具进行硬度测试,确保刀具具有足够的硬度来保持其切削性能。
四、材料检测
1. 使用化学分析仪器对刀具的材料成分进行分析,确保刀具材料符合标准要求。
五、功能检测
1. 对于具有特殊功能的刀具,例如多功能刀或电动刀,我们会对其功能进行验证,确保其正常工作。
2. 对于刀具的开启和关闭机制,我们会进行多次操作测试,确
保其灵活可靠。
六、安全性检测
1. 检查刀具是否具有安全保护措施,例如安全锁和刀套等。
2. 对于锋利的刀具,我们会检查其防护措施,例如刀刃的鞘套或收纳盒。
以上是我们对刀具进行的一般检测范本,具体的检测内容和方法可能因刀具类型和用途的不同而有所差异。
我们将根据需要制定相应的检测计划,并确保刀具的质量和安全性能达到标准要求。
检测数控铣床中刀具的磨损问题

检测数控铣床中刀具的磨损问题
数控铣床是现代制造业中广泛使用的一种机床,它能够高效地完成各种复杂零件的加工任务。
而其中刀具的磨损问题则是影响加工质量和效率的重要因素之一。
刀具磨损是指在使用过程中,刀具表面逐渐失去原有的尺寸和形状,导致其性能下降,甚至无法继续使用。
这种磨损现象主要是由于切削力、温度、润滑等因素引起的。
在实际生产中,如何及时检测刀具的磨损情况,是保证加工质量和效率的关键。
以下是一些常见的检测方法:
1. 目视检测法
这是最简单、最直观的检测方法。
操作人员可以通过肉眼观察刀具表面的变化,来判断其是否需要更换。
但这种方法只适用于表面磨损较为明显的情况,对于内部磨损或微小磨损则无法发现。
2. 测量法
这种方法需要使用专业的测量工具,如卡尺、显微镜等。
通过对刀具尺寸和形状进行精确测量,可以得出其磨损程度。
但这种方法操作较为繁琐,需要一定的技术水平和经验。
3. 振动信号分析法
这种方法利用数控铣床本身所产生的振动信号,通过信号处理技术来分析刀具的磨损程度。
这种方法不仅能够检测表面磨损,还能够发现内部磨损和微小磨损,具有较高的精度和可靠性。
除了以上几种方法外,还存在一些基于图像处理、声学信号等技术的检测方法。
这些方法在不同场景下都有其适用性和局限性,具体选择应根据实际情况而定。
总的来说,及时检测数控铣床中刀具的磨损问题,是保证加工质量和效率的重要措施。
通过选择合适的检测方法,并根据检测结果及时更换刀具,可以有效地减少生产过程中的故障和损失,提高生产效益。
刀具磨损检验方法
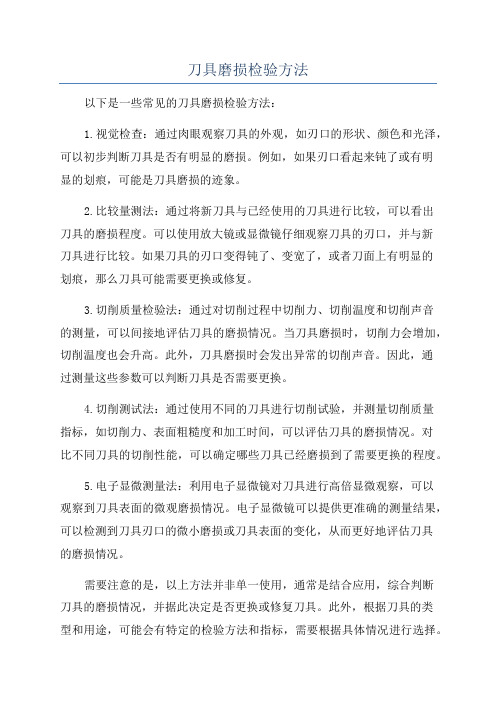
刀具磨损检验方法以下是一些常见的刀具磨损检验方法:1.视觉检查:通过肉眼观察刀具的外观,如刃口的形状、颜色和光泽,可以初步判断刀具是否有明显的磨损。
例如,如果刃口看起来钝了或有明显的划痕,可能是刀具磨损的迹象。
2.比较量测法:通过将新刀具与已经使用的刀具进行比较,可以看出刀具的磨损程度。
可以使用放大镜或显微镜仔细观察刀具的刃口,并与新刀具进行比较。
如果刀具的刃口变得钝了、变宽了,或者刀面上有明显的划痕,那么刀具可能需要更换或修复。
3.切削质量检验法:通过对切削过程中切削力、切削温度和切削声音的测量,可以间接地评估刀具的磨损情况。
当刀具磨损时,切削力会增加,切削温度也会升高。
此外,刀具磨损时会发出异常的切削声音。
因此,通过测量这些参数可以判断刀具是否需要更换。
4.切削测试法:通过使用不同的刀具进行切削试验,并测量切削质量指标,如切削力、表面粗糙度和加工时间,可以评估刀具的磨损情况。
对比不同刀具的切削性能,可以确定哪些刀具已经磨损到了需要更换的程度。
5.电子显微测量法:利用电子显微镜对刀具进行高倍显微观察,可以观察到刀具表面的微观磨损情况。
电子显微镜可以提供更准确的测量结果,可以检测到刀具刃口的微小磨损或刀具表面的变化,从而更好地评估刀具的磨损情况。
需要注意的是,以上方法并非单一使用,通常是结合应用,综合判断刀具的磨损情况,并据此决定是否更换或修复刀具。
此外,根据刀具的类型和用途,可能会有特定的检验方法和指标,需要根据具体情况进行选择。
刀具磨损检验的目的是保证刀具的切削质量和切削效率,确保产品的质量和生产效率的提高。
通过正确使用检验方法,可以及时发现刀具的磨损情况,及时采取措施维护和更换刀具,以确保刀具的正常运行。
同时,还可以通过分析和总结刀具磨损情况,来改进切削工艺和刀具维护方式,以提高刀具寿命和生产效率。
检测刀具磨损和破损的方法
检测刀具磨损和破损的方法单台机床的加工,对刀具磨损和破损的监测,凭工人的经验,尚能进行正常的生产,而对FMS、CIMS、无人化工厂,必须解决刀具磨损与破损的在线实时监测及控制问题。
因为及时确定刀具磨损和破损的程度并进行在线实时控制,是提高生产过程自动化程度及保证产品质量,避免损坏机床、刀具、工件的关键要素之一。
监测原理监测参量的选取监测原理监测原理框图监测刀具磨损和破损的方法很多,可分为直接测量法和间接测量法两大类。
直接测量法主要有:光学法、接触电阻法、放射性法等。
间接测量法主要有:切削力或功率测量法,刀具和工件测量法,温度测量法,振动分析法,AE法,电机电流或功率测量法等。
比较现有的刀具磨损和破损的监测方法,各有优缺点,我们选取声发射(AE)和电机电流信号作为监测参量。
这是因为AE信号能避开机加工中噪声影响最严重的低频区,受振动和声频噪声影响小,在感兴趣区信噪比较高,便于对信号进行处理。
响应速度快,灵敏度高;但重负荷时,易受干扰。
而电机电流信号易于提取,能适应所有的机加工过程,对正常的切削加工没有影响,但易受干扰,时间响应慢,轻负荷时,灵敏度低。
这样,同时选AE和电机电流为监测信号,就能利用这2个监测量的各自长处,互补不足,拓宽监测范围,提高监测精度和判别成功率。
切削过程中,当刀具发生磨损和破损时,切削力相应发生变化,切削力的变化引起电机输出转矩发生变化,进而导致电机电流发生相应的变化,电流法正是通过监测电机电流的变化,实现间接在线实时判断刀具的磨损和破损。
AE 是材料或结构受外力或内力作用产生变形或断裂时,以弹性波形的形式释放出应变能的现象。
它具有幅值低,频率范围宽的特点。
试验及频谱分析发现:正常切削产生的AE信号主要是工件材料的塑性变形,其功率谱分布,100kHz以下数值很大,100kHz 以上较小。
当刀具磨损和破损时,100kHz以上频率成分的AE信号要比正常切削时大得多,特别是100-300kHz 之间的频率成分更大些。
刀具磨损监测方法综述
刀具磨损监测方法综述导言:随着工业生产的不断发展,刀具在各类机械加工过程中扮演着重要的角色。
然而,由于长期使用和磨损,刀具会渐渐失去其优秀的切削性能。
因此,为了保证刀具的高效工作和延长其使用寿命,刀具磨损的监测成为了研究的焦点之一、本文将对刀具磨损监测方法进行综述,包括传统的触摸式测量方法和基于传感器的非接触式测量方法。
一、触摸式测量方法1.外形尺寸法该方法基于刀具磨损后外形的变化来进行判断,常用于一些尺寸较大的刀具监测。
通过测量刀具的长度、直径或角度变化,并与初始尺寸进行对比,就能够间接评估刀具的磨损程度。
这种方法的优点是简单易行,成本低廉,但其缺点是只能进行间接评估,无法精确测量刀具磨损的准确数值。
2.触摸探测法该方法通过将测量仪器与刀具进行接触,测量刀具表面的高度变化来确定刀具的磨损程度。
其中,最常见的方法是使用光电探测器对刀具的轮廓进行扫描,通过测量探测器的位移来计算刀具的磨损量。
这种方法具有较高的精度,可以实时监测刀具的磨损情况。
但缺点是由于测量过程中需要与刀具表面接触,可能会对刀具本身造成额外的磨损。
另外,由于测量仪器的复杂性,该方法的设备成本较高。
二、非接触式测量方法1.声发射法该方法通过检测刀具表面的声音信号来判断刀具的磨损程度。
刀具磨损会导致切削过程中产生较大的振动和噪声,这些声音可以被传感器捕捉到,并转化为电信号进行分析。
通过对声波信号的频域和时域分析,可以确定刀具的磨损情况以及可能存在的异常情况。
这种方法的优点是无需接触,对刀具的磨损进行实时监测。
但是,由于刀具的声音在噪声环境中容易受到干扰,因此对该方法的信号处理和分析要求较高。
2.热成像法该方法通过红外热成像仪对刀具的表面温度分布进行观测和分析,以判断刀具的磨损情况。
刀具磨损会导致切削过程中大量的热量变化,这些变化将反映在刀具表面的温度分布中。
通过热成像仪的高精度传感器,可以实时获取刀具的温度分布,并通过图像处理和分析来评估刀具的磨损程度。
刀具的检验方法、检验要点和检验工具
刀具的检验方法、检验要点和检验工具
所谓的刀具,是指机械制造中用于切削加工的工具,又称切削工具。
在机械制造的过程中,刀具的缺失、破损、磨损或选刀错误,都可能导致机床停机或造成代价不菲的工件报废。
由于许多加工都建立在刀具寿命的基础之上,这时,我们就需要对刀具的加工状态进行检测,从而保证机器的正常运转。
刀具检测的方法
现有的刀具检测的方法多种多样,而每一种检测方法使用的情形各不相同,其中有两种主要的刀具检测的方法,它们分别是直接测量法与间接测量法。
直接测量法是对刀刃外观、表面品质以及几何形状的变化进行刀具检测,一般只能在不切削时进行;间接测量法是利用刀具磨损或将要磨损时的状态对不同的工作参数完成刀具检测,是目前主要使用的检测方法。
同时,刀具检测的发展也可根据使用的测头分为接触式和非接触式两种检测。
接触式刀具检测的测头通过探针与刀具或工件接触而获取数据。
非接触式刀具检测的测头则是利用光束(通常是激光束)从刀具或工件表面反射到一个接收器中来获取数据。
刀具检测的主要工具——三坐标测量仪。
常用的刀具磨损检测方法比较
常用的刀具磨损检测方法比较刀具磨损是刀具使用过程中不可避免的问题,定期检测和维护刀具磨损可以保证其正常工作并延长使用寿命。
常用的刀具磨损检测方法有很多种,下面将对其中几种常用的方法进行比较。
1.目测法目测法是最简单也是最直观的一种刀具磨损检测方法。
只需通过肉眼观察刀具的外观和刀刃状况来判断刀具是否需要磨损。
这种方法优点是简单易行,无需任何专用设备和仪器,缺点是只能判断刀具的整体状况,无法提供具体的磨损程度信息。
2.测量法测量法通过测量刀具的几何参数来判断刀具的磨损情况。
常用的几个参数包括刀具直径、刀具长度、刀具刀刃的角度等。
通过测量这些参数的变化来判断刀具是否磨损。
这种方法优点是可以提供较为精确的刀具磨损程度信息,缺点是需要专用设备和仪器,操作比较繁琐。
3.接触法接触法是通过判断刀具与工件之间的接触情况来判断刀具的磨损情况。
常用的方法包括观察切削力的变化、观察切屑形态等。
通过分析接触情况可以判断刀具是否磨损,并且可以提供刀具磨损程度的定量指标。
这种方法优点是可以在实际工作中直接观察磨损情况,缺点是受到工艺条件的限制,可能无法应用于一些特殊工况。
4.声音法综上所述,不同的刀具磨损检测方法有各自的优点和适用场景。
目测法简单易行,适合于简单的刀具磨损情况判断;测量法可以提供较为精确的定量指标,适用于复杂的磨损情况判断;接触法可以在实际工作中进行检测,但受到工艺条件限制;声音法简单易行,但只能提供定性指标。
在实际应用中,可以根据具体情况选择合适的检测方法或结合多种方法进行磨损检测。
- 1、下载文档前请自行甄别文档内容的完整性,平台不提供额外的编辑、内容补充、找答案等附加服务。
- 2、"仅部分预览"的文档,不可在线预览部分如存在完整性等问题,可反馈申请退款(可完整预览的文档不适用该条件!)。
- 3、如文档侵犯您的权益,请联系客服反馈,我们会尽快为您处理(人工客服工作时间:9:00-18:30)。
检测刀具磨损和破损的方法
单台机床的加工,对刀具磨损和破损的监测,凭工人的经验,尚能进行正常的生产,而对FMS、CIMS、无人化工厂,必须解决刀
具磨损与破损的在线实时监测及控制问题。
因为及时确定刀具磨损和破损的程度并进行在线实时控制,是提高生产过程自动化程
度及保证产品质量,避免损坏机床、刀具、工件的关键要素之一。
监测原理监测参量的选取监测原理监测原理框图监测刀具磨损和破损的方法很多,可分为直接测量法和间接测量法两大类。
直接测量法主要有:光学法、接触电阻法、放射性法等。
间接测量法主要有:切削力或功率测量法,刀具和工件测量法,温度测
量法,振动分析法,AE法,电机电流或功率测量法等。
比较现有的刀具磨损和破损的监测方法,各有优缺点,我们选取声发射(AE)和电机电流信号作为监测参量。
这是因为AE信
号能避开机加工中噪声影响最严重的低频区,受振动和声频噪声影响小,在感兴趣区信噪比较高,便于对信号进行处理。
响应速
度快,灵敏度高;但重负荷时,易受干扰。
而电机电流信号易于提取,能适应所有的机加工过程,对正常的切削加工没有影响,
但易受干扰,时间响应慢,轻负荷时,灵敏度低。
这样,同时选AE和电机电流为监测信号,就能利用这2个监测量的各自长处,互
补不足,拓宽监测范围,提高监测精度和判别成功率。
切削过程中,当刀具发生磨损和破损时,切削力相应发生变化,切削力的变化引起电机输出转矩发生变化,进而导致电机电
流发生相应的变化,电流法正是通过监测电机电流的变化,实现间接在线实时判断刀具的磨损和破损。
AE 是材料或结构受外力或
内力作用产生变形或断裂时,以弹性波形的形式释放出应变能的现象。
它具有幅值低,频率范围宽的特点。
试验及频谱分析发现
:正常切削产生的AE信号主要是工件材料的塑性变形,其功率谱分布,100kHz以下数值很大,100kHz 以上较小。
当刀具磨损和破损时,100kHz以上频率成分的AE信号要比正常切削时大得多,特别是100-300kHz 之间的频率成分更大些。
为此,应通过带通滤波器,监测100-300kHz频率成分AE信号的变化,对刀具磨损和破损进行监测。
利用AE、电机电流信号综合对刀具磨损和破损进行判别的原理是:轻负荷区,依靠AE包络信号,用阈值的方法进行判别;在
中负荷区,这时电机电流和AE信号都起作用,用两者结合的方法进行判别,提高判别的成功率,具体方法是:如果AE信号超过AE
阈值,则置延时常数为ds(d的数值依赖于系统构成),如果在ds时间内,电流信号也超过电流信号的阈值,则判刀具极限磨损或
破损。
如果在ds时间内,电流信号未超过电流信号的阈值,则不报警,由延时常数继续监测。
这种以AE
为先导,AE信号和电机电
流信号进行“与”的判别模式,既利用了AE信号具有实时、灵敏的特点,又考虑了电机电流信号具有滞后的性质,具有较强的抗
干扰能力,提高了判别成功率。
在大负荷区,则以电机电流信号为主,AE信号为辅进行判别。
下图为监测系统的线路框图。
中间一路为电网电压监测线路,通过对电源的波动进行监测,消除由于电网电压波动对监测的影响,提高系统的抗干扰能力。
图中虚线部分为自动减去首切电流线路,目的是自动减去首切电流,以电流的变动量为判别量,提高电流信号监测的灵敏度。