钢的纯净度评测及其控制
转炉生产GCr15轴承钢的纯净度分析
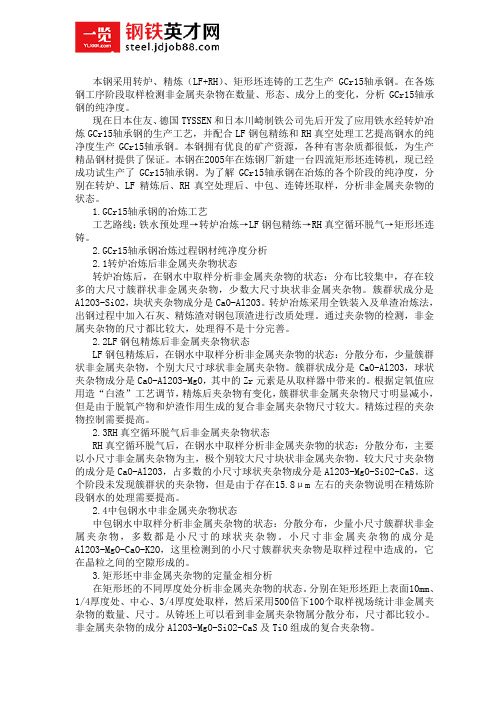
本钢采用转炉、精炼(LF+RH)、矩形坯连铸的工艺生产GCr15轴承钢。
在各炼钢工序阶段取样检测非金属夹杂物在数量、形态、成分上的变化,分析GCr15轴承钢的纯净度。
现在日本住友、德国TYSSEN和日本川崎制铁公司先后开发了应用铁水经转炉冶炼GCr15轴承钢的生产工艺,并配合LF钢包精练和RH真空处理工艺提高钢水的纯净度生产GCr15轴承钢。
本钢拥有优良的矿产资源,各种有害杂质都很低,为生产精品钢材提供了保证。
本钢在2005年在炼钢厂新建一台四流矩形坯连铸机,现已经成功试生产了GCr15轴承钢。
为了解GCr15轴承钢在冶炼的各个阶段的纯净度,分别在转炉、LF精炼后、RH真空处理后、中包、连铸坯取样,分析非金属夹杂物的状态。
1.GCr15轴承钢的冶炼工艺工艺路线:铁水预处理→转炉冶炼→LF钢包精练→RH真空循环脱气→矩形坯连铸。
2.GCr15轴承钢冶炼过程钢材纯净度分析2.1转炉冶炼后非金属夹杂物状态转炉冶炼后,在钢水中取样分析非金属夹杂物的状态:分布比较集中,存在较多的大尺寸簇群状非金属夹杂物,少数大尺寸块状非金属夹杂物。
簇群状成分是Al2O3-SiO2,块状夹杂物成分是CaO-Al2O3。
转炉冶炼采用全铁装入及单渣冶炼法,出钢过程中加入石灰、精炼渣对钢包顶渣进行改质处理。
通过夹杂物的检测,非金属夹杂物的尺寸都比较大,处理得不是十分完善。
2.2LF钢包精炼后非金属夹杂物状态LF钢包精炼后,在钢水中取样分析非金属夹杂物的状态:分散分布,少量簇群状非金属夹杂物,个别大尺寸球状非金属夹杂物。
簇群状成分是CaO-Al2O3,球状夹杂物成分是CaO-Al2O3-MgO,其中的Zr元素是从取样器中带来的。
根据定氧值应用造“白渣”工艺调节,精炼后夹杂物有变化,簇群状非金属夹杂物尺寸明显减小,但是由于脱氧产物和炉渣作用生成的复合非金属夹杂物尺寸较大。
精炼过程的夹杂物控制需要提高。
2.3RH真空循环脱气后非金属夹杂物状态RH真空循环脱气后,在钢水中取样分析非金属夹杂物的状态:分散分布,主要以小尺寸非金属夹杂物为主,极个别较大尺寸块状非金属夹杂物。
钢的纯净度的评价方法

钢的纯净度的评价方法薛正良, 李正邦, 张家雯(钢铁研究总院冶金工艺研究所,北京 100081)摘 要:根据实验研究结果分析了用于评价非金属夹杂物数量、类型、形貌和尺寸分布的各种方法的特点及其相互关系,指出用不同冶炼工艺生产的氧含量相近的钢有可能具有完全不同的非金属夹杂物类型和尺寸分布。
用图像分析仪检测金相试样中非金属夹杂物的尺寸分布并不能反映钢中非金属夹杂物的真实状况。
关键词:非金属夹杂物;化学分析;标准图谱;图像分析仪;电解萃取法一般而言,钢的纯净度主要指与非金属夹杂物的数量、类型、形貌、尺寸及分布等有关的信息。
目前工业生产和科研工作中常用的评价方法有化学分析法、标准图谱比较法,图像分析仪分析法、电解萃取分析法。
各种评价方法都从某一个侧面反映了钢中非金属夹杂物的数量或其它属性,同时各种方法都存在局限性。
本文对以上各种评价方法及其它们之间的相互关系进行了比较和分析。
1 非金属夹杂物数量的评价方法1.1 化学分析法化学分析法主要是通过检测钢中非金属夹杂物形成元素氧和硫的含量来估计非金属夹杂物的数量。
室温下钢中的氧几乎全部以氧化物夹杂的形式存在,因此钢中全氧含量可以代表氧化物夹杂的数量。
但化学分析法并不能反映钢中非金属夹杂物的类型、形貌、尺寸大小和尺寸分布。
用不同工艺冶炼的钢,即使其氧含量基本相同,仍有可能具有完全不同的氧化物夹杂类型和尺寸分布。
1.2 标准图谱比较法国际标准化组织(ISO)、美国材料试验协会(ASTM)和我国国家标准GB10561-89将高倍金相夹杂物分为4类[4],即A类(硫化物类)、B类(氧化铝类)、C类(硅酸盐类)和D类(球状或点状氧化物类)。
标准评级图谱的图片直径80 mm,相当于被检金相试样上直径0.8 mm的视场放大100倍后的尺寸。
A、B、C和D类夹杂物按其厚度或直径不同又分为细系和粗系两个系列,每个系列按夹杂物沿钢材轧制方向的长度分成5个级别,JK法分为1~5级、ASTM法分为0.5~2.5级,后者用于评定高纯度钢。
钢洁净度的评定和控制二

A C D钢公司 " # $ 7 2 / : &’ $ 0 2 K" # $ 0 2 K : &’ $ 8 2 / 0 / / 7 克利夫兰厂 美国 . / / 7 " # $ 6 1 2 / : &’ $ 6 2 /" # $ @ 2 6 : &’ $ 6 2 8 0 内陆钢公司 # $ ( 2 0 : &’ $ 1 2 6" # $ 6 2 @ : &’ $ 0 2 @ 0 / / 8 美国 . " @号 ; $ " -
? @ & BA> &含量对中间包内钢水总氧含量 # $ % & ’ 的影响 ) ! 1 " 策+ 为了减少 ? 采取了如下对 @ &和 A> &的污染 *
& B( % A> ’ ( A> & B1 % 7 8 ’ C7 8 1 (
钢洁净度的评定和控制 二.
OQ P O
从根本上降低补吹频率 4 ; $ "采用副枪 : 采用高效的机械挡渣设备 : 如挡渣球 浮在钢 水和炉渣界面之间 . 有助于减少出钢带入钢包的 : 渣 量约7 钢. 也 可 采 用 一 些 传 感 器9 出 钢 < = > ? : 后: 钢包厚渣层引起了大量渣携带问题 9 例如 : 美 国内陆钢公司第 @ ; $ "车间标准钢种通过机械扒 渣 使钢包炉 渣层厚度低于 @ A &" . 8 B B90 / / 7年 A C D钢 公 司 克 力 夫 兰 厂 最 后 钢 包 渣 平 均 厚 度 为 厂低碳铝镇 ! 1 B B: A C D钢 公 司 印 第 安 那 E F G H I G 静钢钢包渣层厚 / 高强度低合金钢钢包渣 ! B B: 层厚 0 要求增碳条件的钢种渣层厚 7 1 B B:
钢水纯净度控制

• (8)钢种微细夹杂物去除 钢种微细夹杂物去除
• 大颗粒夹杂(>50µm)去除, 大颗粒夹杂( )去除, 术; • 小颗粒夹杂(<50µm)去除: 小颗粒夹杂( )去除: 采用中间包控流技
• •
-中间包钙质过滤器 -中间包电磁旋转
• • • • •
(9)防止浇注过程下渣和卷渣 防止浇注过程下渣和卷渣 — 加入示踪剂追踪铸坯中夹杂物来源; 加入示踪剂追踪铸坯中夹杂物来源; — 结晶器渣中示踪剂变化; 结晶器渣中示踪剂变化; — 铸坯中夹杂物来源,初步估算外来夹杂 铸坯中夹杂物来源, 物占41.6%二次氧化占 39%,脱氧产物为 物占 二次氧化占 , 20%
中间包冶金的最新技术
◆ H型中间包 ◆ 离心流中间包 ◆中间包吹氩 ◆去夹杂的陶瓷过滤器 ◆电磁流控制
• (4)钢包高FeO渣子是氧的储存器。浇 注过程中钢包表面渣子可能会凝结在 钢包内壁上,浇完后倒渣不净,附着 在包壁上的高FeO渣子与下一炉钢水 相接触,渣中氧就要释放出来,氧化 合金元素(如硅、锰),严重时会导致钢 水成分出格。 • 因此,为了发挥炉外精炼的效果, 提高铸坯的质量,控制钢水成分的稳 定性,在出钢时必须进行挡渣操作。
• (5)中间包控流装置 中间包控流装置
• 中间包不是简单的过渡容器,而是一个冶 金反应 中间包不是简单的过渡容器, 容器, 容器,作为钢水进入结晶器之前进一步净化钢水 • 中间包促进夹杂物上浮其方法: 中间包促进夹杂物上浮其方法:
• • • •
1)增加钢水在中间包平均停留时间t: )增加钢水在中间包平均停留时间 : t=w/(a×b×ρ×v) = ( × × × ) 中间包向大容量深熔池方向发展。 中间包向大容量深熔池方向发展。 2)改变钢水在中间包流动路径和方向, )改变钢水在中间包流动路径和方向, 促进 • 夹杂物上浮。 夹杂物上浮。
钢水纯净度控制PPT课件

连铸坯质量控制
优化连铸工艺参数,减少 铸坯内部缺陷;采用电磁 搅拌等技术,改善铸坯质 量。
04
夹杂物形态控制与变性处理
夹杂物分类及来源
夹杂物分类
根据夹杂物的性质、形态和来源,可分为内生夹杂物和外来 夹杂物两大类。内生夹杂物是在钢液凝固过程中由于溶解度 降低、偏析等原因析出的,而外来夹杂物则是由于原料不纯 、炉衬侵蚀等原因引入的。
电炉冶炼工艺
优化供电制度,提高电效率;采用泡沫渣 技术,减少钢液吸气。
炉外精炼工艺
采用真空处理、吹氩搅拌等技术,进一步 去除钢中夹杂物和气体。
二次精炼技术
钢包精炼
在钢包内对钢液进行加热 、搅拌、真空处理等操作 ,提高钢液纯净度。
中间包冶金
在中间包内采用过滤器、 加热器等设备,对钢液进 行净化处理。
高锰硫比可以控制硫化物的形态。
02
精炼处理
采用真空脱气、炉外精炼等技术手段,可以进一步降低钢液中的气体和
杂质含量,提高钢液的纯净度。例如,通过真空脱气处理可以降低钢液
中的氢含量,减少白点等缺陷的产生。
03
过滤技术
在钢液凝固前,采用过滤技术可以去除钢液中的大尺寸夹杂物,提高铸
坯的质量。常用的过滤技术包括陶瓷过滤器、金属网过滤器等。
影响因素及危害
影响因素
炼钢原料、冶炼工艺、炉渣性能、耐火材料、钢包处理等都是影响钢水纯净度的 重要因素。
危害
非金属夹杂物和有害元素的存在会降低钢的力学性能、耐蚀性能和加工性能,严 重影响钢材的使用寿命和安全性。如:降低钢的韧性、塑性和疲劳强度;造成应 力集中,促进钢的脆化;影响钢的耐蚀性和耐磨性等。
钢水纯净度控制ppt课件
汇报人:文小库
连铸钢水质量纯净度控制ppm战略(蔡开科)

C
鱼雷罐+喷CaC2
D 铁水罐喷石灰+Mg粉
E
铁水罐CaC2+Mg粉
F 铁水罐喷石灰+Mg粉
G
KR法
H
铁水罐喷镁粉
I
铁水罐喂包芯镁线
脱硫后 [S]/ppm
15 11 15 10.5 10 30 10 20 30
铁水罐 [S]/ppm
22 21 25 10.5 10 30 10 30 30
回硫 ppm
≤900;
70年代
≤800;
80年代
≤600;
90年代
≤100;
2000年后 ≤50。
纯净度是个相对概念,钢中的有害杂质元素降到什么样的 水平决定于钢种和产品的用途。
本文简要评述钢中五大有害元素在炼钢-精炼-连铸过程中 的去除及达到水平。
1. 钢中硫
1.1 钢中硫含量的要求
硫的主要危害:钢中[S]>0.015%时,连铸
碱度一定,渣中(FeO)太高, LP反而下降 ,渣稀会冲刷炉衬。
因此,在BOF渣R=3.0,(FeO)=20%, LP可 达150。
(2)较低的熔池温度
钢中[P]和渣中(MgO)含量的关系
(3)熔池搅拌动力学
在BOF中,LP仅为70~90,在顶底复吹转 炉,增加了熔池搅拌动能,加速了钢水与乳 化渣滴之间脱P反应,故LP比顶吹提高了 35~40%。
对于生产超低硫钢(<30ppm),二次精炼脱硫方法有
出钢渣洗脱硫 钢包渣/金搅拌脱硫 喷石灰粉脱硫 真空室脱硫等 喂钙线脱硫
其[S]含量演变如表所示。
S<30ppm钢水脱硫
工艺 [S]开,ppm [S]终,ppm 脱硫率,% [N]终,ppm
X52MS管线钢纯净度的控制
X52MS管线钢纯净度的控制吾塔;李立民;张浩;卜志胜【摘要】文章介绍了采用铁水脱硫预处理、复吹转炉、LF和RH双联精炼、板坯连铸工艺试制开发X52MS管线钢的过程.LF使用CaO-Al2O3-CaF2-SiO2-MgO 渣系,平均渣量控制在10kg/t,平均脱硫率达到82.4%,最高脱硫率为89.6%,熔炼成品钢水终点硫质量分数小于15×10-6,[C]≤0.055%,[N]≤0.0040%,T[O]≤20×10-6,[H]≤1.5×10-6,提高钢水纯净度的同时缩短了LF精炼时间.【期刊名称】《新疆钢铁》【年(卷),期】2018(000)003【总页数】5页(P13-17)【关键词】超低硫钢;LF精炼;纯净度【作者】吾塔;李立民;张浩;卜志胜【作者单位】宝钢集团八钢公司制造管理部;新疆八一钢铁股份有限公司;新疆八一钢铁股份有限公司;新疆八一钢铁股份有限公司【正文语种】中文【中图分类】TF762+.81 前言硫化氢 (H2S)是石油和天然气中腐蚀能力最强的有害介质,抗硫化氢腐蚀管线钢主要用来制造输送酸性石油和天然气管道,主要是在原油和天然气未脱硫的情况下使用,该类管道多属于支线管道,通常采用X65以下牌号的管线钢制造。
抗硫化氢腐蚀管线钢是石油天然气用钢中技术要求最高、生产难度最大的一类管线钢。
对钢水纯净度、硫含量、连铸坯的中心偏析以及轧制中的控轧、控冷提出了极高的要求[1]。
根据对国家石油、天然气需求分析,八钢公司试验开发了X52MS管线钢,对管线钢生产中脱硫、脱磷、脱氮、脱氢、夹杂物等工艺控制进行了研究。
确定了工艺控制关键点,通过工艺优化控制提高X52MS管线钢的纯净度及板坯较低的中心偏析。
2X52MS管线钢生产工艺生产工艺:铁水脱硫预处理-顶底复吹转炉冶炼-LF精炼-RH真空处理-板坯连铸。
生产X52MS管线钢采用铁水深脱硫预处理、转炉冶炼,LF精炼和RH真空精炼双联生产工艺。
钢铁厂:钢材质量检验标准及检验方法
钢铁厂:钢材质量检验标准及检验方法1. 引言在钢铁厂生产过程中,钢材质量的检验是至关重要的一环。
合格的钢材质量是确保产品性能和安全的基础,同时也是提高客户满意度的关键因素。
本文将介绍钢铁厂常用的钢材质量检验标准及检验方法,以及在实际操作中应注意的事项。
2. 钢材质量检验标准钢材质量检验标准是评估钢材质量的重要依据,一般包括以下方面:- 物理性能:包括强度、硬度、韧性等指标;- 化学成分:检测钢材中的主要元素含量;- 尺寸和外观:检查钢材的长度、宽度、厚度等尺寸,并评估外观质量;- 表面质量:检验钢材表面的缺陷、氧化程度等。
常见的钢材质量检验标准有国家标准、行业标准和企业标准等。
钢铁厂应根据具体产品和客户要求,选择适用的标准进行检验。
3. 钢材质量检验方法钢材质量检验方法一般包括以下几方面:- 物理性能测试:使用万能试验机等设备进行拉伸、冲击、硬度等相关测试;- 化学成分分析:通过光谱仪、分析天平等设备检测钢材的化学成分;- 尺寸和外观检验:使用卡尺、显微镜等工具对钢材的尺寸和外观进行检测;- 表面质量检验:通过目测、照相等方式评估钢材表面的质量。
在进行钢材质量检验时,应严格按照标准和方法进行操作,确保检验的准确性和可靠性。
4. 检验过程注意事项在进行钢材质量检验时,需要注意以下事项:- 检验设备和仪器的校准:定期对使用的检测设备和仪器进行校准,以确保测试结果的准确性;- 检验环境的控制:在适宜的温湿度条件下进行检验,避免外部环境对测试结果的影响;- 检验人员的培训和技能:确保检验人员具备必要的专业知识和操作技能,避免误操作和测试错误;- 检验记录的保存:及时记录和保存检验结果,以备后续参考和追溯。
5. 结论钢材质量的检验是钢铁厂生产过程中的关键环节。
通过采用适用的标准和方法,并注意检验过程中的操作要点,可以有效确保钢材质量。
钢铁厂应通过持续改进和培训,提高质量检验的水平和能力,为客户提供优质的钢材产品。
钢的纯净度评测及其控制
钢的纯净度估测及其控制<The Evaluation Methods and Control of Steel Cleanliness>1.引言随着社会发展和科技进步, 对钢质量, 尤其对它的纯净度(cleanliness)要求越来越高. 除了要降低钢中非金属氧化物夹杂物(non-metallic oxide inclusions)的含量, 控制其尺寸、形貌和成分外, 就洁净钢(clean steel)而言, 还要求控制其硫(S)、磷(P)、氢(H)、氮(N), 甚至碳(C), 并且要尽可能减少钢中金属杂质元素(metallic impurity elements), 诸如: 砷(AS)、锡(Sn) 、锑(Sb)、硒(Se)、铜(Cu)、锌(Zn)、铅(Pb)、镉(Cd)、碲(Te)、铋(Bi)等.不同钢种因其不同的应用场合和条件,对上述要求也各不相同。
例下表所示:表1 对不同钢种典型的纯净度要求(Typical steel cleanliness requirements for various steel grades)钢中的金属杂质元素(metallic impurity elements)通常被视为残余元素(trace elements).由于它们在炼钢和精炼过程很难去除,所以在钢中不断累积,成为废钢供应的一大问题。
鉴于钢中如存在超量的残余金属元素,会造成晶间偏析(intergranular segregation)、有害析出物和其它一些问题。
目前,在钢的生产过程中为了克服钢中残余元素造成的危害,尤其是电炉炼钢,通常采用严格控制废钢的种类和用量。
近年来世界各国普遍采用高炉铁水、直接还原铁、海绵铁、碳化铁或其它相对纯的铁来替代废钢,旨在降低钢中残余元素含量。
从钢中残余元素角度讨论钢纯净度问题近年来已有不少相关研究的报道和论文发表。
我们今天主要讨论钢厂普遍存在,大家又十分关注并想得到解决的问题:〈低碳铝镇静钢氧化物夹杂对其纯净度的影响〉。
轴承钢的纯净度和均匀度
轴承钢的纯净度和均匀度
轴承钢的纯净度和均匀度对其机械性能和寿命具有至关重要的影响。
纯净度是指钢中非金属杂质的含量,如氧化物、硫化物和氮化物等。
这些杂质会降低钢的韧性、疲劳强度和耐腐蚀性。
因此,提高轴承钢的纯净度是提高其机械性能和延长其使用寿命的重要途径。
为了获得高纯净度的轴承钢,需要采用先进的冶炼和轧制技术。
例如,电渣重熔技术和真空熔炼技术可以有效地去除钢中的非金属杂质。
同时,采用高精度轧制技术可以确保钢的晶粒大小和组织结构均匀,从而提高其机械性能。
除了纯净度外,轴承钢的均匀度也非常重要。
均匀度是指钢的化学成分、组织结构和机械性能在各个方向上的均匀分布。
为了获得高均匀度的轴承钢,需要采用先进的冶炼和轧制工艺,并严格控制钢的化学成分和显微组织。
总之,轴承钢的纯净度和均匀度对其机械性能和寿命具有重要影响。
为了获得高纯净度和高均匀度的轴承钢,需要采用先进的冶炼和轧制技术,并严格控制其化学成分和显微组织。
这将有助于提高轴承的性能和延长其使用寿命。
- 1、下载文档前请自行甄别文档内容的完整性,平台不提供额外的编辑、内容补充、找答案等附加服务。
- 2、"仅部分预览"的文档,不可在线预览部分如存在完整性等问题,可反馈申请退款(可完整预览的文档不适用该条件!)。
- 3、如文档侵犯您的权益,请联系客服反馈,我们会尽快为您处理(人工客服工作时间:9:00-18:30)。
钢的纯净度估测及其控制<The Evaluation Methods and Control of Steel Cleanliness>1.引言随着社会发展和科技进步, 对钢质量, 尤其对它的纯净度(cleanliness)要求越来越高. 除了要降低钢中非金属氧化物夹杂物(non-metallic oxide inclusions)的含量, 控制其尺寸、形貌和成分外, 就洁净钢(clean steel)而言, 还要求控制其硫(S)、磷(P)、氢(H)、氮(N), 甚至碳(C), 并且要尽可能减少钢中金属杂质元素(metallic impurity elements), 诸如: 砷(AS)、锡(Sn) 、锑(Sb)、硒(Se)、铜(Cu)、锌(Zn)、铅(Pb)、镉(Cd)、碲(Te)、铋(Bi)等.不同钢种因其不同的应用场合和条件,对上述要求也各不相同。
例下表所示:表1 对不同钢种典型的纯净度要求(Typical steel cleanliness requirements for various steel grades)钢中的金属杂质元素(metallic impurity elements)通常被视为残余元素(trace elements).由于它们在炼钢和精炼过程很难去除,所以在钢中不断累积,成为废钢供应的一大问题。
鉴于钢中如存在超量的残余金属元素,会造成晶间偏析(intergranular segregation)、有害析出物和其它一些问题。
目前,在钢的生产过程中为了克服钢中残余元素造成的危害,尤其是电炉炼钢,通常采用严格控制废钢的种类和用量。
近年来世界各国普遍采用高炉铁水、直接还原铁、海绵铁、碳化铁或其它相对纯的铁来替代废钢,旨在降低钢中残余元素含量。
从钢中残余元素角度讨论钢纯净度问题近年来已有不少相关研究的报道和论文发表。
我们今天主要讨论钢厂普遍存在,大家又十分关注并想得到解决的问题:〈低碳铝镇静钢氧化物夹杂对其纯净度的影响〉。
钢中夹杂物会使产品产生很多不同类型的缺陷。
例如:低碳铝镇静钢(LCAKS)生产易拉罐时,由于不适量夹杂物的存在而缺乏成形性(formability)致使产生有裂纹的折边(cracked flanges)和用于生产其它制品时出现的疲劳寿命(fatigue life)等问题。
钢的成形性和疲劳寿命很大程度上是受它所含的硫化物(sulfides)和氧化物(oxides)夹杂物的影响。
微裂纹缺陷(sliver defects)往往以线状沿钢板表面平行于轧制方向存在。
它用于汽车板时会造成浅表的不完整(cosmetic imperfections)和成形性问题。
据美国内陆钢铁公司(Inland Steel CO.)、国家钢铁公司(National Steel Co.)和日本川崎钢铁公司(Kawasaki Steel Co.)等研究结果认为,它们通常含有来自脱氧产物中的三氧化二铝或者来自由卷入的结晶器保护渣所形成的复杂非金属夹杂物(complex non-metallic inclusions)。
就钢的纯净度而言,除了考虑夹杂物的含量外,很大程度上取决于夹杂物的尺寸分布、形貌和它的成分,其中尤以钢中夹杂物的尺寸分布特别重要。
因为大型宏观夹杂物(macro-inclusions)对钢的机械性质(mechanical properties)最为有害。
有人统计得到:1Kg典型的低碳铝镇静钢中含有107-108个夹杂物,其中只有400个80-130µm;10个130-200µm和少于1个200-270 µm的夹杂物。
显而易见,通常在钢中要检测到特大的夹杂物也是并不容易的。
从夹杂物的数量而言,小型夹杂物远超过大形夹杂物。
但是大型夹杂物所占总的体积分数(total volume fraction)可能是较大的。
有时候在整炉钢中造成灾难性缺陷(catastrophic defect)的正是由于单个大型夹杂物所致。
因此,就清洁钢而言,不仅只是控制钢中夹杂物的平均含量,而且要避免对产品造成致命危害的大于临界尺寸的有害夹杂物的存在。
基于这一目的,在表1中列出了对钢中最大夹杂物尺寸限制的要求。
夹杂物尺寸分布的重要性在下图1中作了进一步阐述。
图1测得钢包和中间包中>30µm夹杂物含量分别为1.61ppm 和0.58ppm。
因此,尽管中间包钢水中的总氧含量和总夹杂物含量略高于它们在钢包中的含量。
但中间包中钢比钢包中的钢更纯净了。
钢中非金属夹杂物的来源有:1)脱氧的产物(Deoxidation products)。
在低碳铝镇静钢中的主要内生夹杂物(Indigenous inclusions)是三氧化铝。
它是脱氧剂(例如:铝)和钢中溶解氧(dissolved oxygen)化学反应形成的。
当在高含氧量的条件下,三氧化二铝呈树枝状,如图2(a)和(b)所示;或可能是由图2(c)中的这些较小夹杂物颗粒经碰撞所形成的。
图22)二次氧化的产物(Reoxidation products)。
例在下述情况下形成的三氧化铝。
当:10)残留在钢中的铝被FeO、MnO、SiO2和熔渣及耐火材料中的氧化物氧化形成;20)铝暴露在大气中,被空气中的氧所氧化形成。
3)卷渣(slag entrapment)。
当冶金熔剂(metallurgical fluxes)被卷入钢中。
尤其发生在炼钢、精炼和连铸过程中。
这种条件下形成的夹杂物通常呈球形(spherical inclusions),如图2(d)所示。
4) 外来夹杂物(Exogenous inclusions)。
这类夹杂物主要来自钢包和中间包等的残渣、污物、灰尘和垃圾;破碎的耐火砖;硅酸盐包衬材料的侵蚀物。
它的特点是颗粒大且呈不规则形状(Irregular shaped)。
它可能成为三氧化二铝异类物质形核的核心;也可能成为图2(c)中所示夹杂物的颗粒中心。
5)化学反应的产物(Products of chemical reaction)。
例如当不正确的钙处理(Calcium treatment)进行夹杂物变性(Inclusion modification)所产生的氧化物。
确认钢中夹杂物的来源并不是很容易的事。
例如含有CaO的夹杂物也可能是由卷渣造成的。
钢纯净度控制可以通过生产全过程中各个环节得以实现。
诸如:炼钢原材料的选择和处理;炼钢过程中的合理用氧,避免过吹和重吹;冶炼过程中的正确监控,实现终点碳和温度的最佳控制;炉外精炼方法的合理选择和最佳工艺匹配;合理选用耐火材料尽量减少因受钢渣侵蚀而造成外来夹杂;合理的中间包形状、合适的容量和深度、最佳的流场和温度场;采用全程保护浇铸;应用较强吸收钢中夹杂物能力的冶金熔剂(钢包调渣剂、中间包覆盖剂和结晶器保护渣)等。
尽管如此,钢中不可避免地存在氧化物(Oxides);硫化物(Sulfides);硫氧化合物(Oxysulfides);氮化物(Nitrides)和碳氮化合物(Carbonitrides)等。
然而,为了提供生产清洁钢(Clean steel)的有价值信息,核心问题是钢中三氧化二铝夹杂物的控制和对钢纯净度评测方法现状的了解。
2.钢纯净度评测方法为了研究和控制钢的纯净度,关键的问题是要有正确评测方法。
夹杂物的数量、尺寸分布、形状和成分应该在钢生产的全过程都要测定。
测定的方法有直接法(direct method)和间接法(indirect)。
前者准确但昂贵;后者快而经济,但准确性没有前者高。
2.1.直接法有几种评测钢纯净度的方法。
现将其总结和比较在]下表2。
表2 直接法评测钢纯净度的比较(Comparison of direct methods for evaluating steel cleanliness)2.1.1.固态钢中夹杂物的二维检测法有几种常规的固态钢中夹杂物二维检测法。
1)金相显微镜观测法(Metallographic Microscope Observation)。
在这种常规的方法中,通过钢样试片用光学显微镜(Optical Microscope)检测并凭眼观测定量。
当采用具有复杂形状的夹杂物(Complex shaped inclusions)检测时,就会发生问题。
例图2(a)照片所示的夹杂物是由可能被错误地解释为一些较小夹杂物形成的簇状的单个夹杂物来显示的。
此外,用此法测定小型夹杂物太耗时,而大型夹杂物并不多见。
2)图像分析法(Image analysis)。
它比用眼观测的金相显微镜法有了改进。
它采用高速计算机(High-speed computer),由视频扫描显微镜图像(Video-scanned microscope image)来识别灰色基体上的黑白区域。
此法能比金相显微镜法容易地检测较大范围和较多数量的夹杂物。
然而,由于试样上的擦伤(scratches)、蚀坑(pitting)和非金属斑点而造成检测误差。
3)硫印(Sulfur print)。
这种常规而经济的宏观照相法,通过对试样的硫酸酸洗,就能检测宏观夹杂和裂。
/ 4)扫描电子显微镜法(Scanning Electron Microscopy)。
此法能容易地检测到被测试样的三维形貌和每一个夹杂物的成分。
例如图2(b)就是用电子探针显微分析仪(Electron Probe Micro Analyzer)测得的成分。
为了找到暴露的夹杂物,试样加工的工作量很大。
5)光学发射光谱法(带有脉冲识别分析功能)。
此法分析熔解在钢水中的元素。
Ovako钢铁公司改进了这种方法后,可以在取样后1min 内检测钢的总氧量、微观夹杂物尺寸分布和化学成分。
6)激光显微探针质谱仪(Laser Microprobe Mass Spectrometry)。
由于夹杂物确定的化学状态,当单个夹杂物被脉冲激光束(Pulsed laser beam)照射后,超过它离子化门槛值(threshold value)时的最低激光强度,选择为特征光谱图(characteristic spectrum patterns)。
根据参考样比较得到的结果,在激光现微探针质谱仪测定的光谱峰值是与化学元素有关的。
7)X-射线光电子光谱法(X-rays Photoelectron Spectroscopy)。
此法应用X射线可描述大于10µm单个夹杂物的化学状态。
7)俄歇电子光谱法(Auger Electron Spectroscopy)。
此法可采用电子束来描述靠近平板式试样表面附近小范围内的化学成分。
2.1.2.固态钢中夹杂物的三维检测法有几种方法可直接用三维法测固态钢中的夹杂物。
1)常规超声波扫描法(Conventional Ultrasonic Scanning)这种非破坏性方法(Non-destructive method)能检测凝固了的钢中大于20µm夹杂物的数量和成分。